 |
 |
 |
 |
 |
 |
 |
 |
 |
 |
 |
 |
 |
 |
 |
 |
 |
 |
 |
 |
 |
 |
 |
 |
 |
 |
 |
 |
 |
 |
 |
 |
 |
 |
 |
 |
 |
 |
 |
 |
 |
 |
 |
 |
|
|
|
|
|
|
|
|
|
|
|
|
|
|
|
|
|
|
|
|
|
|
|
|
|
|
|
|
|
|
|
|
|
|
|
|
|
|
|
|
|
|
|
|
|
|
|
|
|
|
|
|
|
|
|
|
In the early 1950s, the Colchester company of England introduced three new lathes, the Student, Triumph and Mascot - and while the "Student" name was new, the other two were much older with "Mascot" dating back to around 1914. All were styled to closely resemble each other with a common and easily-used control system - but few interchangeable parts. The lathes were assembled in what was, at that time (and until the early 1960s) Europe's largest plant devoted to the manufacture of lathes. The factory had two 300 feet-long moving-floors and a system of "flow-line" production based on automotive practice that aimed to produce a consistently high standard of quality and accuracy to "American toolroom limits of accuracy". However, like all production process, hidden factors contrived to make some lathes more accurate than others, a fact that Colchester turned to advantage by offering a special model, distinguished by black micrometer feed-screw dials, to an improved "toolroom" standard of accuracy - however, these lathes were not specially built but just those that inspectors had classified as the most accurate of a batch . Although the new design had its origins in earlier Colchester models, and had very similar-looking geared headstocks and apron controls, each of the new models was individually engineered and constructed for a particular class of work; whilst the Student and Master became immensely popular during the next two decades in both commercial and training workshops the 8.5" centre height Mascot (the largest Colchester then made and sold in the United States as the "Mammoth") was designed for serious industrial use and was very heavily constructed. Two between-centres capacities of 54" or 78" were available that weighed, respectively 4620 and 5160 lbs - making them twice as heavy as the machine immediately below it in size the 7.5" centre height Triumph. The 127/8" wide V-way bed of the Mascot had distinctive "elliptical" cross ribbing and was manufactured from a casting that had been allowed to age for at least 6 months before being machined and finish ground. It could be supplied either straight or with a gap that, when removed, allowed a piece of material up to 29 inches in diameter and 9.25" thick on the special 25-inch diameter faceplate. Induction hardening was an optional extra, though this specification was standard on export lathes for the USA labelled "Clausing"; two between-centres capacities were available, either 54" or 78" between centres, both with heavy cast-iron plinths underneath both headstock and tailstock. Although the specification laid down in the sales literature was quite unambiguous, the factory would build a batch of machines to any specification the customer wished and the author has seen, over the years, examples which combine almost as many variations of the previous differences as could be imagined. However, one unvarying feature was that, on gap bed lathes, the carriage traverse handwheel was positioned on the right-hand side of the apron and a T-slotted saddle was fitted whilst on straight bed machines the handle was always on the left and the saddle top was plain - the latter specification described in the catalogues as "Dominion" and usually involving a screwcutting gearbox with English-only threading. Although a useful feature, a lathe with a gap bed can suffer one or two problems: if the gap is removed for a large-diameter turning job and not immediately replaced for ordinary turning, the bed (especially on unhardened models) will suffer excessive wear as the saddle is unsupported when the turning tool reaches the chuck-end of the workpiece. When replaced the gap can cause inaccurate turning as the saddle runs over it; the cause is usually dirt between the mating surfaces or uneven tightening. Before refitting make sure that the whole of the gap section is scrupulously clean, insert the screws, bring the saddle over the piece to roughly align it then lightly tighten the screws a little at a time. Final alignment can be made with a few blows in the right direction from a hide-faced mallet before tightening the four Allen screws fully and evenly. One tip, from a Colchester technician, is to strike the lathe bed near the gap as the bolts are tightened to help bed the gap in. Always store the gap piece in a safe place - or it will disappear, like so many before it, to that mysterious, impossible-to-find, gap-bed heaven.. Continued below:
|
|
|
|
|
|
|
|
 |
|
|
|
|
|
|
Early 1950s 8.5" centre height Colchester Mascot with dual English/metric screwcutting gearbox, T-slotted saddle and a detachable-gap in the bed.
|
|
|
|
|
|
|
|
|
|
|
|
Continued: The 3.125" bore headstock spindle was machined from a heat-treated, high tensile steel forging and ran in a pair of "Gamet Super High Precision" low-angle, double-row cylindrical taper roller bearings at the front and a single, automatically adjusted, taper roller bearing at the rear. It carried a hardened American L2 (long-taper) nose, a popular and very effective design that consisted of a large screwed ring, captive on the headstock spindle, with a matching thread and keyed taper in the chuck backplate. Unfortunately, the various sizes of this fitting are easily confused by the inexperienced and legion are the number of chucks and backplates that have been bought in error. If you look carefully the size is (usually) stamped somewhere on these spindle fittings but, if not, do your homework, and use a ruler. The range of spindle speeds differed slightly according to the year of manufacture; early models were restricted to a maximum of 600 rpm with a range that consisted of: 37, 56, 87, 125, 180, 270,415 and 600 rpm whilst, soon after production started, two-speed motors were offered that gave a much-improved range of: 28, 42, 55, 65, 84, 94, 130, 135, 187, 202, 270, 311, 405, 450, 622 and 900 rpm. If the lathe was going to be used exclusively for larger jobs a special slow-speed model was also available that gave a range from 24 to 410 rpm. Originally a 5 hp single-speed motor was specified but, because this must have proved underpowered for the really heavy work the lathe was capable of (and possibly to increase electrical reliability) this was changed to a 7.5 hp from an unspecified date. Other options offered were a 2-speed 4hp /8hp unit and, to special order, single-phase or DC motors. To control the spindle a vertically disposed rod protruded from right-hand side of the headstock's front face; it combined the functions of an electrical stop/start switch and, because it was linked to a pair of automotive-like shoes that operated against the inside of the (headstock-mounted) 4-step V pulley, a brake lever as well. Mounted concentrically with the lever's pivot point was an (optional-extra) electrical reversing switch and the standard switch also included a safety "no-volt" release. Although a Matrix multi-disc clutch (combined with a brake) should have been a standard fitting on a machine of this class it was relegated to the options list - but also available for retrofitting when the curses of operators not involved in piece work reached the ears of the accountants cowering in their offices remote from the stench of cutting oil. The headstock gears of these lathes were never entirely silent, even when new, and a "noisy" headstock can almost be expected as they age; the worst offender is usually the most-used speed, often that immediately below the highest. In an attempt to quieten the headstock some owners resort to using a thick oil instead of the thin hydraulic lubricant specified by the makers; the heavier oil will defeat the spiral oil-return grove built into the bearing cover plate on the left-hand end of the spindle - and appear to be almost 'sucked out' as the machine runs. Small leaks from the headstock are almost a feature of these lathes and, providing the oil is kept topped up, should result in no harm; the time to worry is when the lubricant stops coming out - the reservoir will be empty. Continued below:
|
|
|
|
|
|
|
|
|
|
|
|
|
|
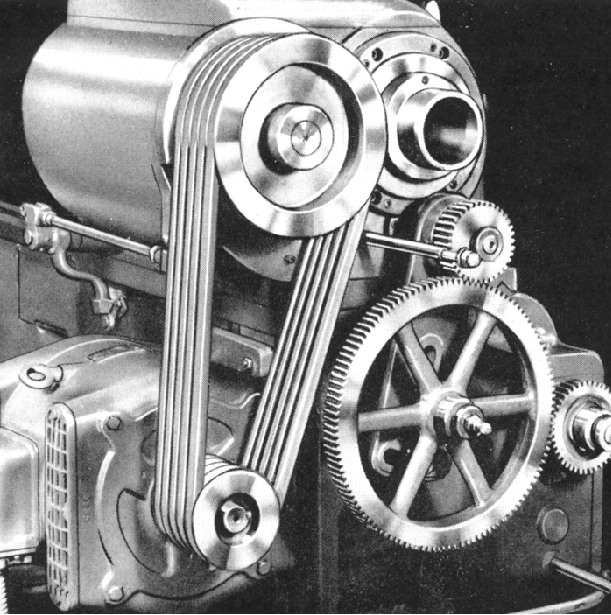 |
|
|
|
|
|
|
|
|
Mascot drive system. The 5 hp fan-cooled single speed or 4/8 hp 2-speed motor was bolted to the back of the bed and drove into the headstock through 5 V belts. A brake was built into the headstock pulley but, at extra cost, this could be exchanged for a clutch.
|
|
|
|
|
|
|
|
|
|
|
|
|
|
Continued: The lathes appears to have been offered as standard with a screwcutting gearbox that could produce both English and metric threads just by just lifting or lowering a lever; a cheaper model, called "Dominion" in the Colchester tradition, was also available with an English-threads only set-up, no gap in the bed and without T slots in the top surface of the saddle. The dual gearbox gave 36 English threads from 4 to 60 tpi and 11 metric from 0.5 mm to 6 mm pitch; the gearbox fitted to the Dominion models (it had 5 instead of 4 rows on the selector plate and was marked with the Dominion name) gave 45 threads from 4 to 112 tpi, including 11.5 tpi and 23 tpi. On dual-gearbox model threads were changed from English to metric by a short horizontal lever just above the screw-cutting chart whilst on the English-threads only version the same lever was used to disengage the leadscrew drive. The apron was double walled, but open at the bottom, so precluding any chance of the gears being run in oil; the power-feed controls followed standard Colchester practice of the day being concentrated into a single lever that slid along the lower edge of the apron and was lifted into one of two slots to engage either power sliding or surfacing. Lifting the lever automatically locked the engagement whilst stopping the feed merely required the lever to be pressed downwards; unfortunately, the heavier the load on the feed the greater the effort required to disengage it, but at least it was a positive action and did not require a knob to be unscrewed in order to release a clutch. All Mascots had a cleverly-designed safety over-load ball-bearing "clutch" built into the powershaft feed to protect the apron gears; the leadscrew drive could be disengaged and was only intended to be used for screwcutting. The set-over tailstock had a 2" diameter, No. 4 Morse taper barrel with 6.5" of travel that self-ejected its centre; it was graduated in 1/8" (or 1 mm) increments and clamped by a proper "close-down fitting. Standard equipment supplied with the lathe was fairly sparse: a triangular plate-type toolholder, Two No. 4 Morse taper centres and a centre sleeve-down bush for the headstock spindle, a thread-dial indicator built into a short leadscrew cover on the left-hand face of the apron, travelling steady, spanners, oil can, an accuracy and inspection chart and a combined instruction and parts book. Listed with the USA Clausing version (but not with the British) was an extra changewheel that provided power feed at half the usual rate. A large number of accessories was listed although some, like faceplates and decent toolholders ,should really have been part of the standard specification; amongst the items listed were: 3 and 4-jaw chucks, 16 and 25-inch faceplates, a drive plate, coolant equipment, a 6-inch capacity 3-point fixed steady, taper-turning attachment, headstock clutch by Matrix, spindle collet fittings with a maximum through capacity of 2", a 4-way automatic-indexing turret to replace the standard compound slide rest and a special 4-way automatic-indexing slide complete with its own compound slide rest; Gamet super-precision rotating centre, induction-hardened bedways, reversing switch, 1-phase or DC motors, an adapter backplate to mount customers existing chucks and faceplates, low-volt lighting, additional changewheels to cut special and metric threads, chromium-plated control levers and handwheels and, to guild the lilly, instead of the ordinary machine-tool grey special single or two-tone paint finishes were available to the customer's specification. By the mid 1960s the Mascot was looking distinctly old fashioned in comparison with the rest of the range for, unlike the Student and Master, it had not been given an up-to-date appearance nor a higher speed range. Colchester solved the problem by introducing the Mascot 1600 a machine with a radically modern appearance and a 1600 rpm top speed. The design of the new lathe not only revitalised Colchester's reputation but also managed to make the competition look distinctly old-fashioned and out of touch; so successful was it that it formed the basis for Colchester's new "corporate" look that lasted from the late 1960 until the end of the 1980s..
|
|
|
|
|
|
|
|
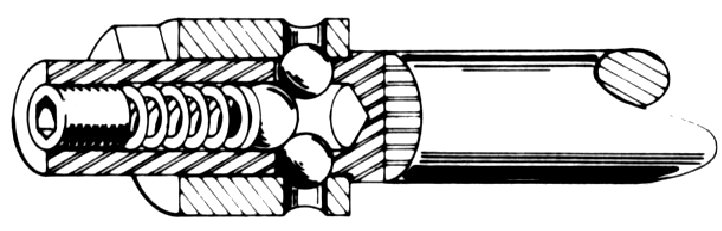 |
|
|
|
|
|
|
|
|
|
The simple but ingeniously-contrived safety spring-loaded ball-bearing "clutch" built into the junction of the powershaft rod with its gearbox connection. The same design of overload protection was also used on some contemporary and later lathes by the Harrison Company
|
|
|
|
|
|
|
|
|
|
|
|
|
|
|
|
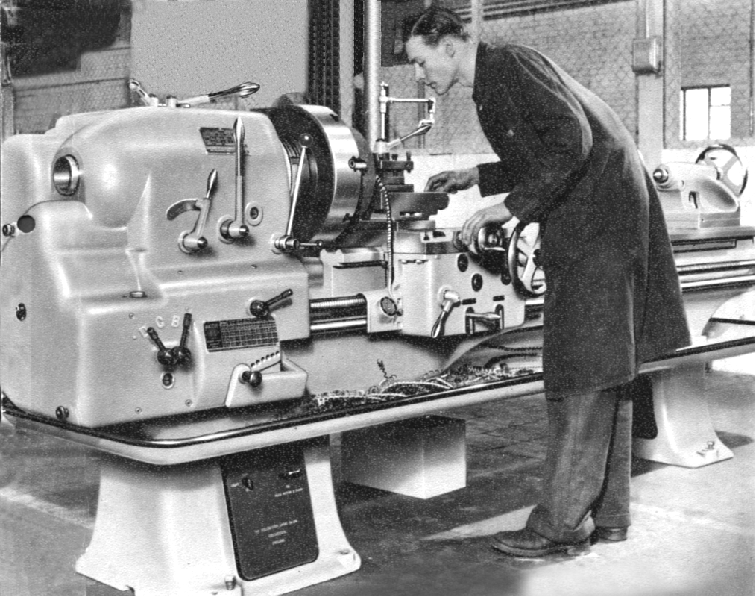 |
|
|
|
|
|
|
1950s to mid 1960s Colchester 8.5" centre height "Mascot" Model shown mounting a 16" diameter 4-jaw chuck
|
|
|
|
|
|
|
|
|
|
|
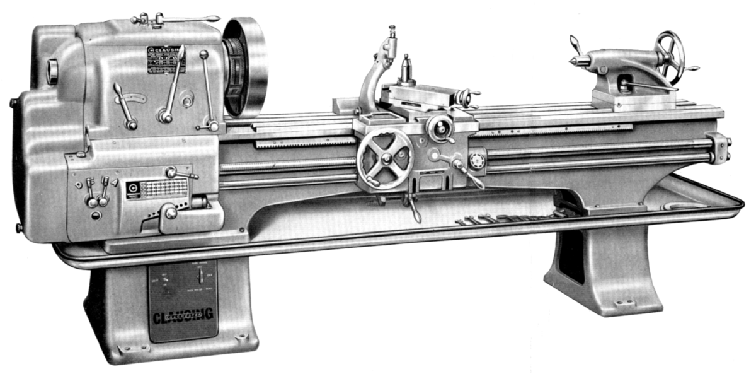 |
|
|
|
|
|
|
Mascot long-bed 78" between-centres model
|
|
|
|
|
|
|
|
|
|
|
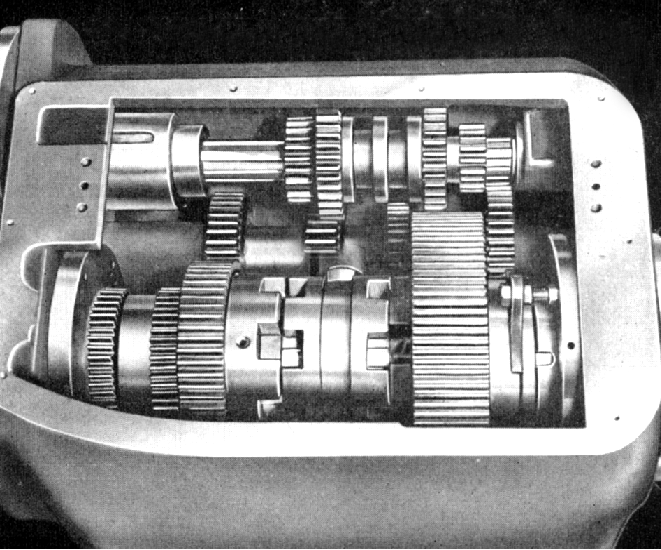 |
|
|
|
|
|
|
|
|
|
The gears inside the 8.5" centre height Mascot headstock were of considerably heavier construction than those used in the 7.5" Triumph
|
|
|
|
|
|
|
|
|
|
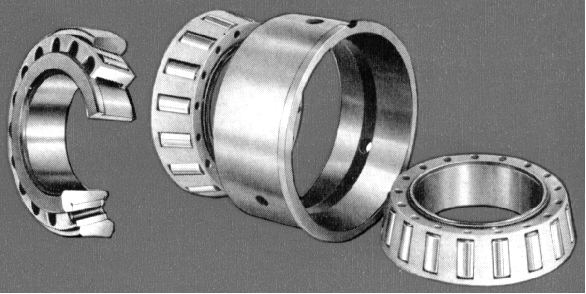 |
|
|
|
|
|
|
Special "Super-precision" Gamet" bearings made by a sister company in the 600 Group - owners of the Colchester Brand name.
|
|
|
|
|
|
|
|
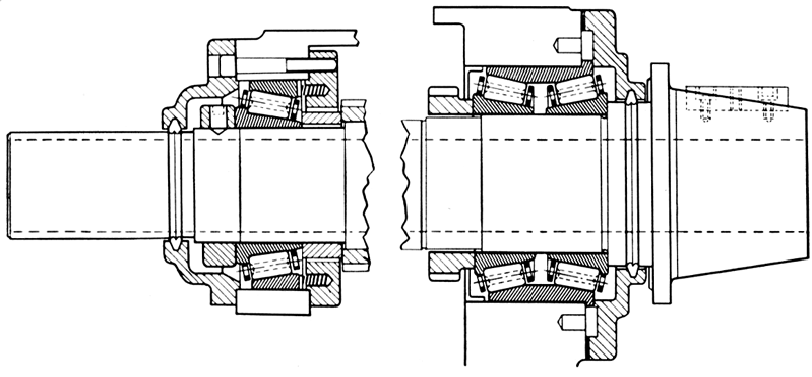 |
|
|
|
|
|
|
Section through the headstock spindle and its bearings
|
|
|
|
|
|
|
|
|
|
|
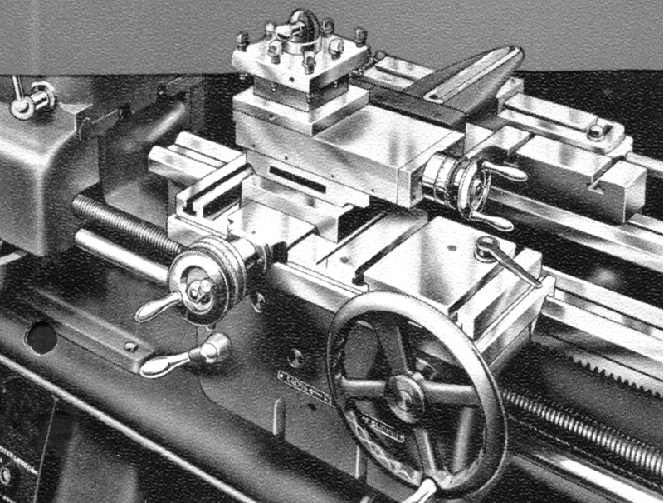 |
|
|
|
|
|
|
The gap-bed Mascot models had, like other Colchester with the same specification, a T-slotted saddle.
|
|
|
|
|
|
|
|
|
|
|
|
|
|
|
|
|
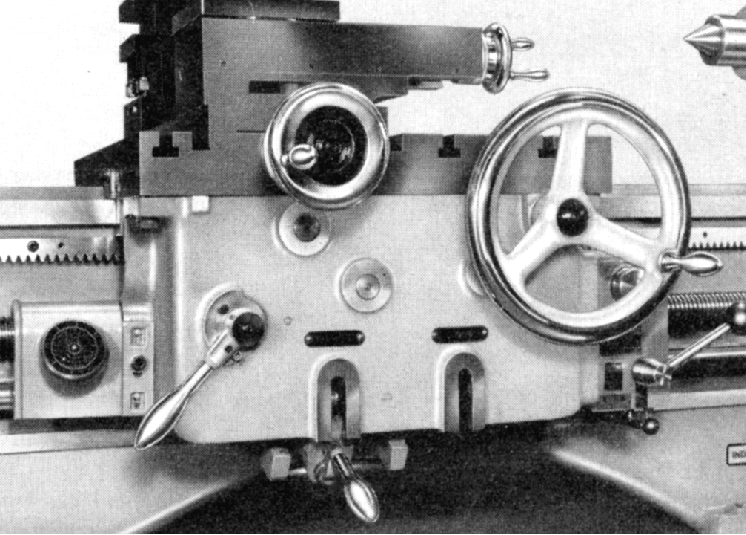 |
|
|
|
|
|
|
Mascot Apron with the original type of the Colchester sliding arm that both selected and engaged the power sliding and surfacing feeds.
|
|
|
|
|
|
|
|
|
|
|
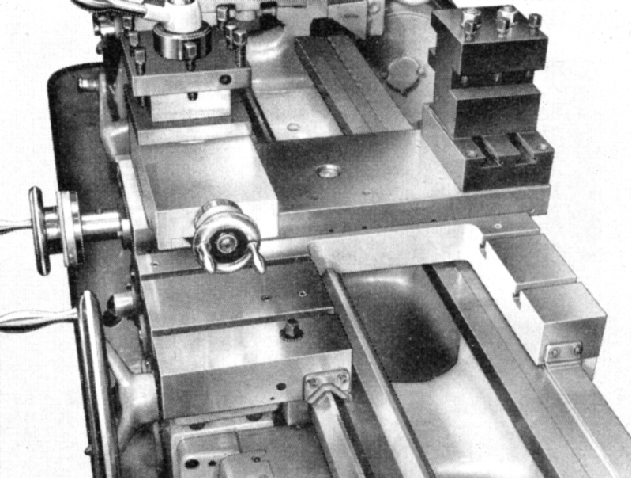 |
|
|
|
|
|
|
The standard cross slide had a plain top and the rear toolpost was fitted to a T-slotted mounting block.
|
|
|
|
|
|
|
|
|
|
|
 |
|
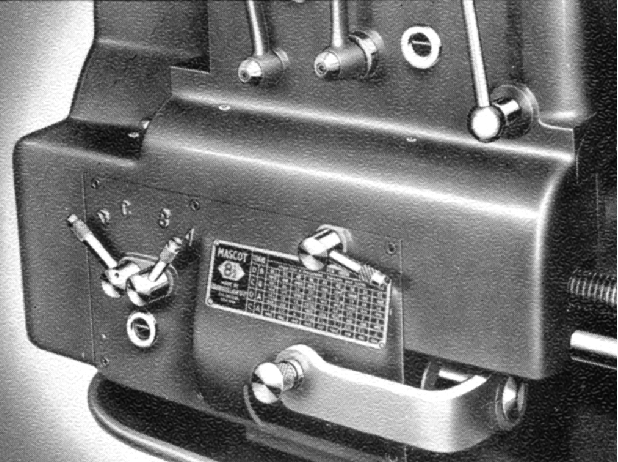 |
|
|
|
|
|
|
|
|
|
English-threads-only Screwcutting gearbox
|
|
|
|
|
|
|
|
|
|
Mascot bed - hardening was an option of the home model but standard on the USA-market Clausing version.
|
|
|
|
|
|
|
|
|
|
|
|
|
|
|
|
|
|
|