 |
 |
 |
 |
 |
 |
 |
 |
 |
 |
 |
 |
 |
 |
 |
 |
 |
 |
 |
 |
 |
 |
 |
 |
 |
 |
 |
 |
 |
 |
 |
 |
 |
 |
 |
 |
 |
 |
 |
 |
 |
 |
 |
 |
 |
 |
 |
 |
 |
 |
 |
 |
 |
 |
 |
 |
 |
 |
 |
 |
 |
 |
 |
 |
 |
 |
 |
|
|
|
|
|
|
|
|
|
|
|
|
|
|
|
email: tony@lathes.co.uk Home Machine Tool Archive Machine-tools Sale & Wanted Machine Tool Manuals Catalogues Belts Books Accessories
LORCH LATHES Newer Accessories More information about Lorch Lathes is contained in various Manuals, Parts Lists and well-illustrated Sales & Technical Specification Brochures and can be purchased on-line here
NOTE: Lorch lathes were advertised using Roman numerals - but are also found stamped using decimal notation e.g. the AV1-K might be found stamped A 6 K and the AV11-K as A 7 K Larger lathes branded Lorch, Schmidt & Co.
LAS Precision Screwcutting and LAS, AV1-K, AV11-K, LLRGN, AVRG, BVIRG, LLRN, AVR & BVIR Lathes
Lorch LAS Photographic Essay
Sliding Headstock Screwcutting BVIPK
Lorch LL "tall-feet" Clockmakers' Lathe
Precision Plain Lathes: LLS, LLV,LLK
Precision 50 mm Lorch KD50
Toolmakers' Screwcutting Lathe AVI-L
Screwcutting Type AB Precision Screwcutting Lathe BL27LZ
Precision Screwcutting Lathe B30LZS
Toolmakers' Miniature Lathes: LA, LAN, LLN & LLPN Plain and Screwcutting with Leadscrew
Lorch lathes--Newer Accessories
Lorch lathes--Older Accessories
Larger Screwcutting Lathes D27 & BIIZ
Lorch Dividing Apparatus for Watchmakers' Lathes
Lorch COLLETS
Lorch Watchmakers' Lathes
Lorch "Triumph" Watchmakers' Lathe
Lorch Junior Watchmaker's Lathe Lorch Lathe Restoration Lorch Lathe Restoration - 2
Early Lorch Model A Lathes - circa 1885 to 1920
Lorch Milling Machines
Lorch Manufacturing Programme Circa 1950
The accessories illustrated on the following pages were available for Lorch precision lathes Models A, B and C until the mid 1970s. Only the more interesting examples are shown; there was also a wide selection of other devices, of a rather more mundane nature - as well as variations on the items shown; for example, compound slide rests could be purchased with either screw or lever feeds, or combinations thereof..
|
|
|
|
|
|
|
|
|
|
|
|
|
|
|
|
|
|
|
|
|
|
|
|
|
|
|
|
|
|
|
|
|
|
|
|
|
|
|
|
|
|
|
|
|
|
|
|
|
|
|
|
|
|
|
|
|
|
|
|
|
|
|
|
|
|
|
|
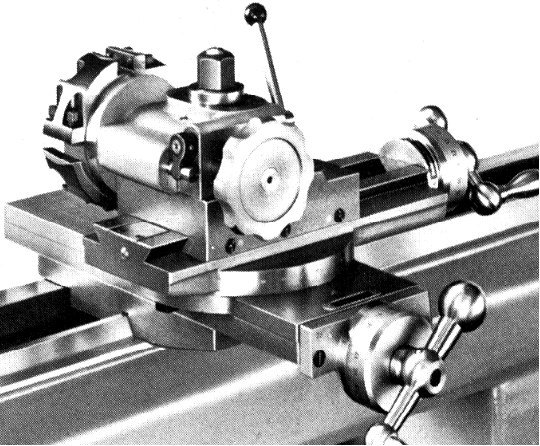 |
|
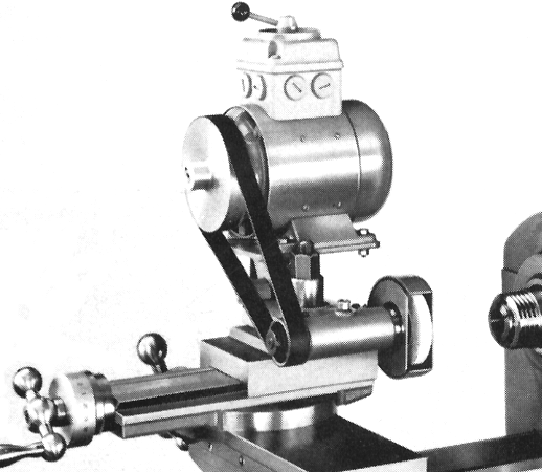 |
|
|
|
|
|
Four-way Revolving Toolholder - fitted with a horizontal swivel axis - with tool clamping parallel or at right-angles to the axis. Designed to be mounted on either screw or lever-feed compound slides.
|
|
|
|
|
|
|
|
|
|
|
|
|
Tool-post Grinding Attachment - a 0.5 hp 2,800 rpm 3-phase motor drove a 80 mm diameter grinding wheel supported on adjustable plain bearings.
|
|
|
|
|
|
|
|
|
|
|
|
|
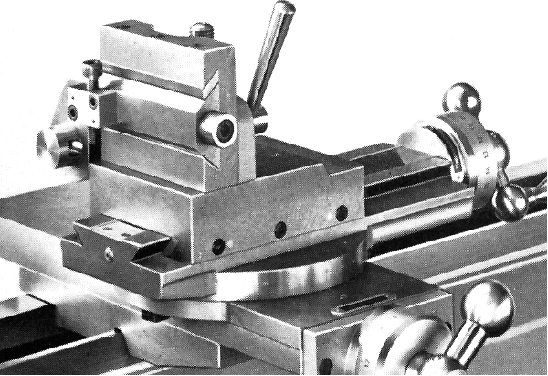 |
|
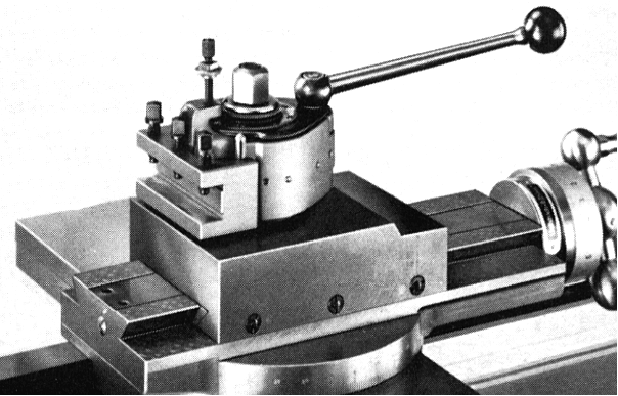 |
|
|
|
|
|
|
Adjusting Slide - for setting the tools square to the direction of feed, particularly on the fine-turning slide rest when facing or turning steep tapers.
|
|
|
|
|
|
|
|
|
Multifix Quick Change Clamping Head - this famous (and very expensive) Swiss-made toolholder could only be mounted on a slide rest having increased height (note the step-up on the slide casting). The hardened and ground serrations of a Multifix allow the toolholders to be gripped at various angles with the highest repeating accuracy. If you find one of these units at reasonable price (they were made in various sizes) - buy it.
|
|
|
|
|
|
|
|
|
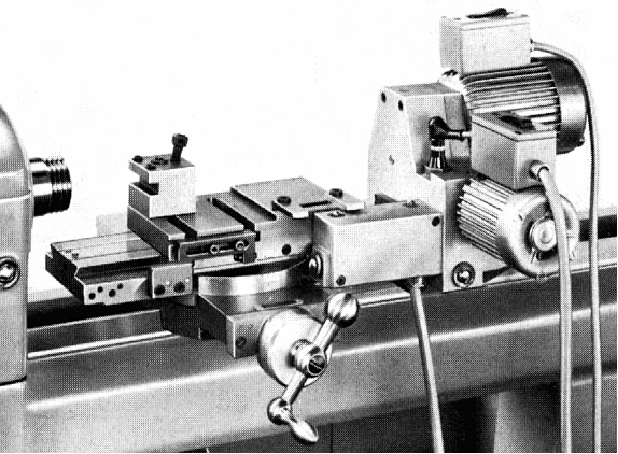 |
|
|
|
|
Fine-turning Slide rest - with a semi-automatic work cycle: the unit would advance rapidly, switch to fine feed and withdraw rapidly. Six individual rates of feed were available from either 23 to 207 mm/min or 46 to 414 mm/min. Two motors were fitted, each responsible for either fine or rapid feeds. Adjustable automatic knock-off stops were fitted. The maximum travel on fine feed was 170 mm and on rapid feed 150 mm.
|
|
|
|
|
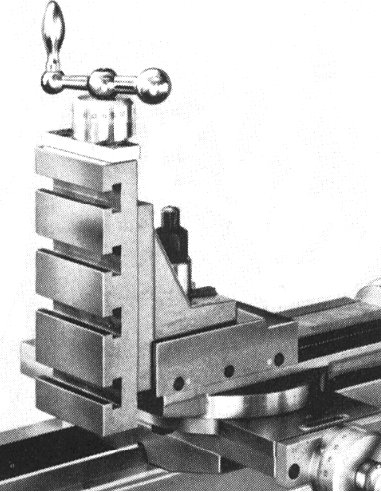 |
|
|
|
 |
|
|
|
|
|
Treble Lever-operated Compound Slide - this had two lever-operated longitudinal slides (with 6 adjustable stops) as well as a traverse slide movement.
|
|
|
|
|
|
|
|
|
Vertical Support - what other makers would call a vertical milling slide was, on the Lorch, designed to mount a variety of beautifully made accessories designed to expand the lathe's versatility
|
|
|
|
|
|
|
|
|
|
|
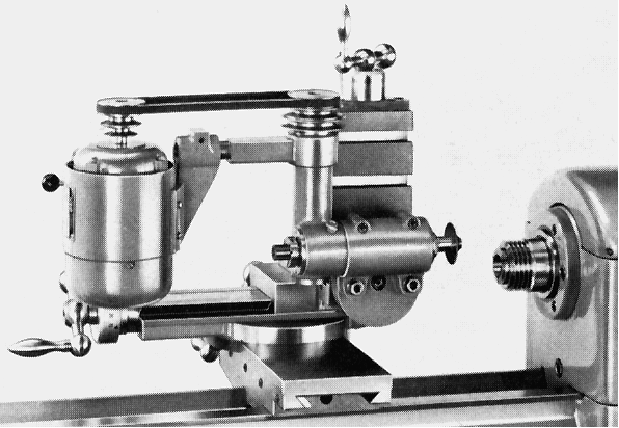 |
|
|
|
|
Universal Milling Attachment - for installation on the Vertical Support. Drive to the spindle was by a 0.4 hp 2,800 rpm 3-phase motor via a three-step V pulley and worm drive. The whole assembly could be swivelled on its graduated base plate from horizontal to vertical. 10mm collets and various other spindle fittings were available. The Spindle speeds were: 170, 235, 320, 380, 500 and 670 rpm.
|
|
|
|
|
|
|
|
|
|
|
|
|
|
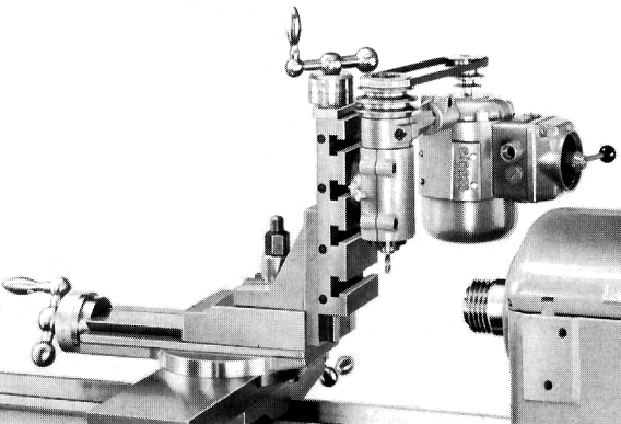 |
|
|
|
|
Universal Milling Attachment High-Speed Version - another view of the Milling Spindle showing the integral switch mounted on the motor. This version, being designed for much higher speeds, omitted the worm drive and was driven directly from the motor. The spindle speeds were: 1350, 1885 and 2540 rpm.
|
|
|
|
|
|
|
|
|
|
 |
|
|
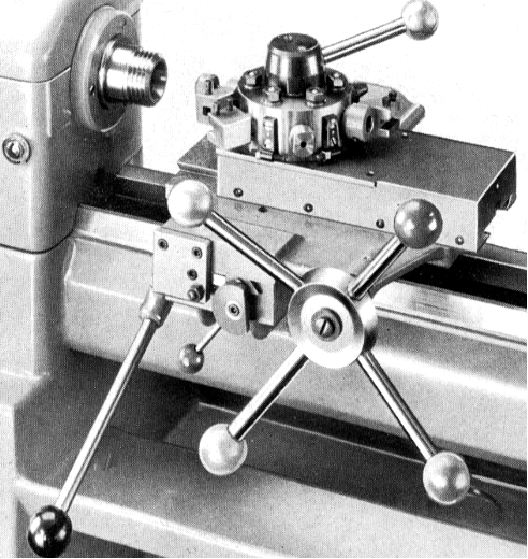 |
|
|
|
|
|
|
|
|
|
|
Dividing Plate - for mounting on the headstock spindle nose with an indexing lever. 24 dividing circles were provided giving divisions of: 24, 54, 74, 96, 102, 116, 124, 132, 138, 156, 228, 360, 10, 50, 60, 70, 85, 95, 110, 125, 135, 168, 300 and 400
|
|
|
|
|
|
|
|
|
|
|
|
|
|
|
|
Turret Compound Slide for Type B lathe - with longitudinal and transverse movement of the 6-tool turret head controlled by hand lever and capstan handle. Automatic indexing stops were fitted to both slide movements. The toolholder bore diameter was 20 mm
|
|
|
|
|
|
|
|
|
|
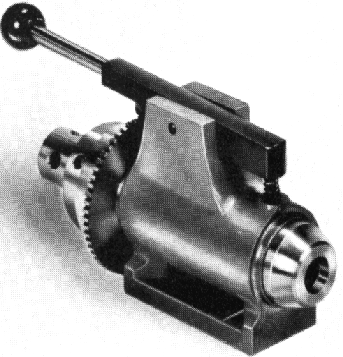 |
|
|
 |
|
|
|
|
|
|
|
|
|
|
Left - Dividing Head - for use on the vertical support. With a 60 division dividing plate (gear) and provision for use of Size 20 collets. Alternative dividing plates were also available.
|
|
|
|
|
|
|
|
|
|
|
|
Above - Small Turret Slide - for small, high-precision turned parts and drilling operations. Available for the Lorch Type A and other makes with a 100 mm centre height.
|
|
|
|
|
|
|
|
|
|
|
|
|
|
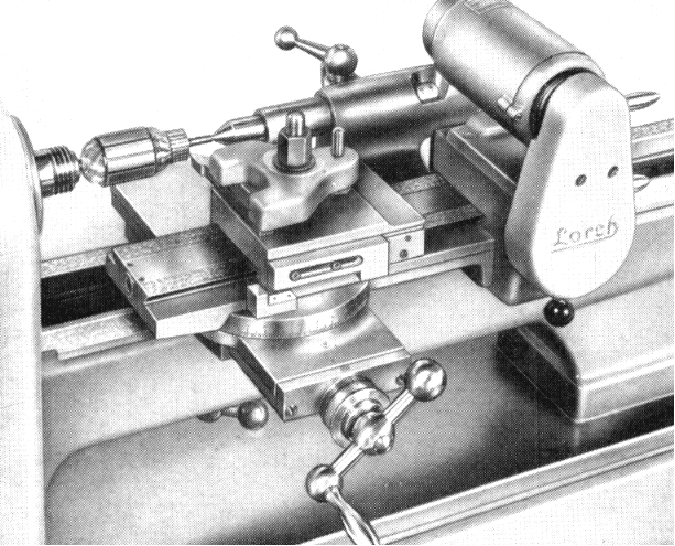 |
|
|
|
|
|
|
A rare fitting - the Motorised Cross Slide
|
|
|
|
|
|
|
|
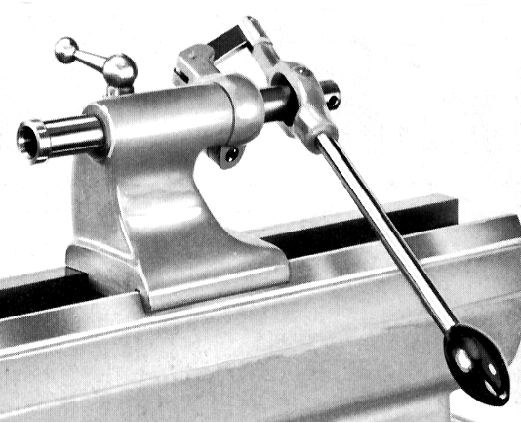 |
|
|
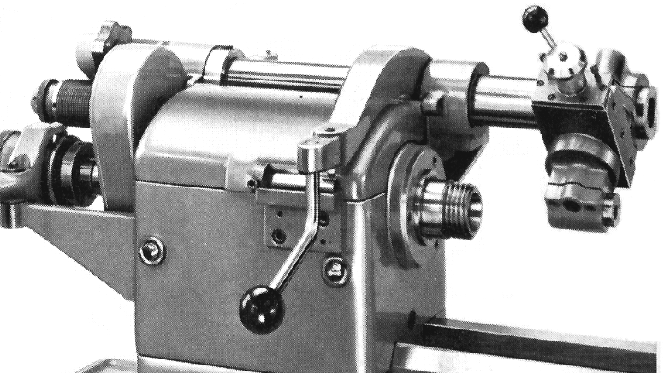 |
|
|
|
|
|
Thread Chasing Attachment - designed for use on the plain lathe and capable of producing very accurate external and internal threads with a maximum length of 50 mm. Unlike a conventional screwcutting lathe the Lorch (and many similar precision lathes) relied on a system of threaded "hobs", with precision-ground threads, which served as masters whose profile could be transferred to the workpiece. The master thread was mounted at the left-hand end of the headstock and its movement transmitted by a sliding bar mounted in brackets clamped to the upper rear edge of the headstock casting. A thread-cutting tool, held in an adjustable holder at the other end of the bar, completed the set up.
|
|
|
|
|
|
|
|
|
|
|
|
Drilling Tailstock - with a lever-operated spindle and provision for 20mm collets and 3 Morse taper spindle inserts. The operating lever was adjustable to any position from horizontal to vertical. A lever-operated tailstock is infinitely preferable for drilling operations, mirroring the operation of a vertical drill press in its action and allowing great sensitivity of control - especially with small diameter drills.
|
|
|
|
|
|
|
|
|
|
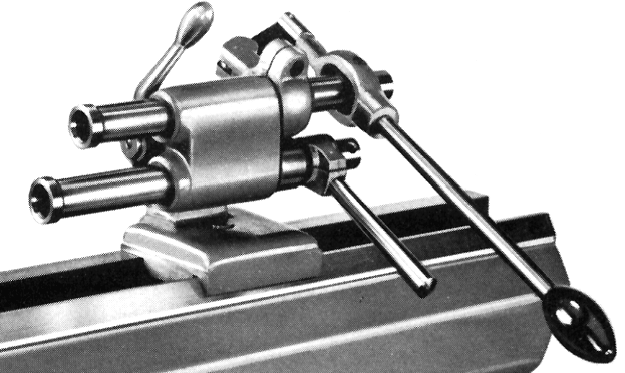 |
|
|
|
|
|
|
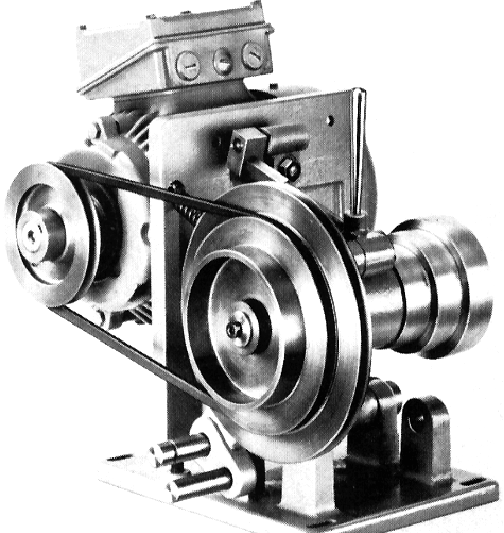 |
|
|
|
|
|
|
|
Double Drilling Tailstock This unit was fitted with two-way swivelling spindles each able to mount 20 mm collets or 3 Morse taper inserts. Each barrel could be swung into position by releasing a single lever which then simultaneously locked the new position. This unit was especially useful for drilling/reaming and drilling/tapping operations, etc.
|
|
|
|
|
|
|
|
|
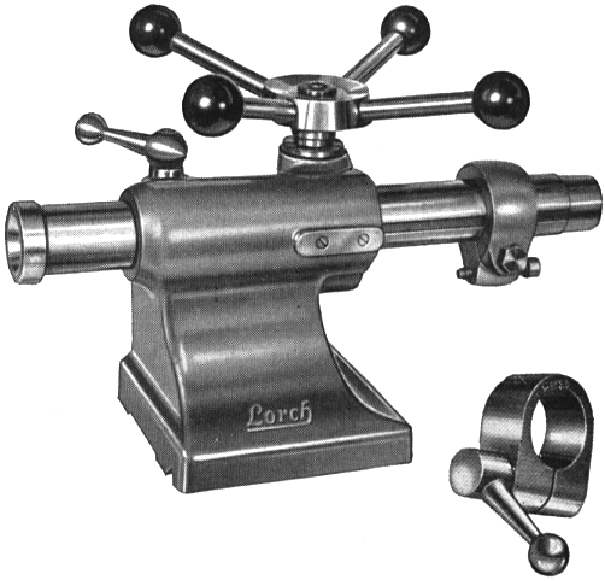 |
|
|
|
|
|
|
|
|
|
|
Motor Drive Unit for Bench Lathes - this countershaft unit was designed to be positioned underneath the workbench. The base plate was provided with a hinge and an eccentric belt-tensioning device.
|
|
|
|
|
|
|
|
|
|
|
|
|
Capstan lever operated Drilling Tailstock - this tailstock was fitted with an especially robust spindle for heavy-duty work and deep-hole drilling. The spindle could mount headstock type collets of 20, 27 and 30 mm shank diameter - or Morse tapers. Accurate depth drilling was aided by a stop-ring fitted with an adjusting screw. This accessory was made for the Type A and B lathes only.
|
|
|
|
|
|
|
|
|
|
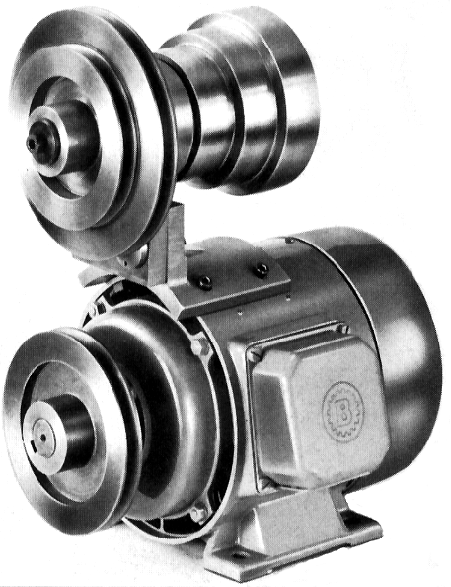 |
|
|
|
|
|
|
|
Motor Drive Unit for Bench Lathes - this countershaft unit was designed to be positioned behind the lathe. The bracket carrying the pulley bearings was bolted directly to the casing of the 1,400 rpm motor. Two speed ranges were offered: a single-speed motor gave 6 speeds between 375 and 2,100 whilst the optional two-speed 1,400/2,800 rpm motor provided 12 spindle speeds spanning 375 to 4,200 rpm
|
|
|
|
|
|
|
|
|
|
|
|
|
|
|
|
|
|
E-MAIL Tony@lathes.co.uk Home Machine Tool Archive Machine Tools For Sale & Wanted Machine Tool Manuals Machine Tool Catalogues
LORCH LATHES Newer Accessories More information about Lorch Lathes is contained in various Manuals, Parts Lists and well-illustrated Sales & Technical Specification Brochures and can be purchased on-line here
Larger lathes branded Lorch, Schmidt & Co.
LAS Precision Screwcutting and LAS, AV1-K, AV11-K, LLRGN, AVRG, BVIRG, LLRN, AVR & BVIR Lathes
Lorch LAS Photographic Essay
Sliding Headstock Screwcutting BVIPK
Lorch LL "tall-feet" Clockmakers' Lathe
Precision Plain Lathes: LLS, LLV,LLK
Precision 50 mm Lorch KD50
Toolmakers' Screwcutting Lathe AVI-L
Screwcutting Type AB Precision Screwcutting Lathe BL27LZ
Precision Screwcutting Lathe B30LZS
Toolmakers' Miniature Lathes: LA, LAN, LLN & LLPN Plain and Screwcutting with Leadscrew
Lorch lathes--Newer Accessories
Lorch lathes--Older Accessories
Larger Screwcutting Lathes D27 & BIIZ
Lorch Dividing Apparatus for Watchmakers' Lathes
Lorch COLLETS
Lorch Watchmakers' Lathes
Lorch "Triumph" Watchmakers' Lathe
Lorch Junior Watchmaker's Lathe Lorch Lathe Restoration Lorch Lathe Restoration - 2
Early Lorch Model A Lathes - circa 1885 to 1920
Lorch Milling Machines
Lorch Manufacturing Programme Circa 1950
Lorch LAS Photographic Essay
Lorch Manufacturing Programme Circa 1950
|
|
|
|