 |
 |
 |
 |
 |
 |
 |
 |
 |
 |
 |
 |
 |
 |
 |
 |
 |
 |
 |
 |
 |
 |
 |
 |
 |
 |
 |
 |
 |
 |
 |
 |
 |
 |
 |
 |
 |
 |
 |
 |
 |
 |
 |
 |
 |
 |
 |
 |
 |
 |
 |
 |
 |
 |
 |
 |
 |
|
|
|
|
|
|
|
|
|
|
|
|
|
|
|
|
|
|
|
|
|
|
|
|
|
|
|
|
|
|
|
|
|
|
|
|
|
|
|
|
|
|
|
|
|
|
|
|
|
|
|
|
|
|
|
|
|
|
|
|
|
|
|
|
|
|
|
|
|
With a 330 mm (13") swing and admitting 635 mm (25") between centres, the Harrison VS330TR was a small, very well specified toolroom-quality lathe constructed to International Precision Lathe Standards ISO R1708 and BS 4656 (UK) and DIN 8605 (Germany). For export markets it was also listed as the Model AA, and replaced the previous variable-speed drive Harrison lathe, a re-badged Colchester Chipmaster. The VS330's main feature was a quiet-running mechanical variable-speed drive unit that, in combination with gears and an "inverted chain" drive in the headstock, gave three separate overlapping speed ranges which equated to: 35 to 180 rpm, 180 rpm to 500 rpm and 500 to 3000 rpm. A 2.2 kW (3 hp) 1000 rpm totally-enclosed, fan-cooled motor was bolted, in the usual Harrison fashion, to an adjustable plate fastened to the back of the bed behind the headstock with (in a very compact arrangement) one variable-speed drive pulley fitted to the motor's shaft and the other to the input shaft of the headstock. The 110-volt electrical-control equipment was neatly built into a single compartment on the left-hand end of the stand, access being through a door protected by a mechanically interlocked isolator switch. The lathe was not fitted with a clutch, but relied instead upon direct on-line starting through forward and reverse contactors with an 'emergency stop' available though both a button mounted on the headstock and a full-length foot bar between the cabinet feet; the main spindle stop, start, forward and reverse control was by a safety-gated lever fastened to the right-hand face of the apron and working a long control rod set below and parallel to the leadscrew and powershaft. With no gearlevers to set, or belts to move - and hence no mechanical indication of the spindle speed - some form of speed readout was required; unfortunately, instead of being a large, clear unit angled so that the operator could read it without hesitation, this was a to-small, insignificant affair tucked away in the top right hand corner of the headstock's front face. With the speeds divided into three ranges and assisted by the special chain drive the headstock contributed to the unusually quiet running of the machine - the makers claiming a maximum noise level of just 80 DBA. The 38 mm (1.5") bore headstock spindle was fitted with a No. 4-D1 Camlock nose and a No. 5 Morse taper - which was normally sleeved down to No. 3 Morse for between-centre use - and ran in "Gamet" precision taper roller bearings produced by one of the companies in the parent 600 group. Although a high-speed lathe intended for industrial use the designers were content to rely on a system of splash lubrication of the headstock gears from a sump in the base of the casting. Following modern practice in being constructed from a rigid, one-piece casting that held a supply of lubricant in the base, the screwcutting gearbox was, like the headstock, lubricated by a simple splash system. All gears were induction hardened with the threading and feed ranges selected by three levers and an 8-position dial; a total of 39 metric, 35 English, 18 Module and 18 Diametrical pitches could be achieved by moving the control levers and either rearranging the standard changewheel set - or employing some of the extra non-metallic (hence quiet-running) gears supplied with the machine in order for it to achieve its full threading range. Power feeds varied from 0.03 to 1 mm (0.001 to 0.040") per revolution of the spindle per revolution in the English; selecting power feeds automatically disengaged the leadscrew drive and both that and the power-feed shaft were fitted with torque-limiting clutches to protect the gearbox. A thread-dial indicator was supplied as standard. Constructed along traditional Harrison lines, the carriage featured a full-length cross slide and a top slide that swivelled through 360 degrees; both the saddle-to-bed fitting, and the cross slide were fitted with proper taper-key gib strips that allowed very fine control over their free movement and, as standard, the compound slide feed screws were fitted with dual-reading English/metric micrometer dials. The cross-feed screw nut was equipped with the same type of simple but effective "wedge" anti-backlash adjustment employed for many years on all larger Harrison (and Colchester) lathes. The double-wall, cast-iron apron was of a straightforward but efficient design with a push/pull button to select the power sliding or surfacing feeds (the surfacing feed was one-half the sliding rate) with a separate flick-up-and-down lever (that retained its easy movement even under the heaviest cuts) to engage and disengage them. The hand-traverse handwheel could be disengaged when power feeds were selected and a hand-operated plunger pump drew oil from a sump in the base of the apron and lubricated not only the bearings and gears, but could also the saddle and cross slide ways. Strongly built, the tailstock carried a 42 mm diameter (1.65") spindle with 110 mm (4.3") of travel and a No. 3 Morse taper. The spindle was engraved with ruler marks in either inch or metric graduations (and sometimes both) with a micrometer dial fitted as standard. The straight bed (there was no option of a gap) was induction hardened and fastened to a heavy-gauge sheet-metal stand fitted as standard not only with the usual splash back, but (unusually for a modern Harrison) a locking tool cupboard as well. The machine weighed approximately 1410 lbs (640 kg) and was 73 inches (1845 mm) long and 40 inches (1040 mm) wide, including the very deep splash back that was designed to allow the fitting of a hydraulic copy (tracer) attachment..
|
|
|
|
|
|
|
|
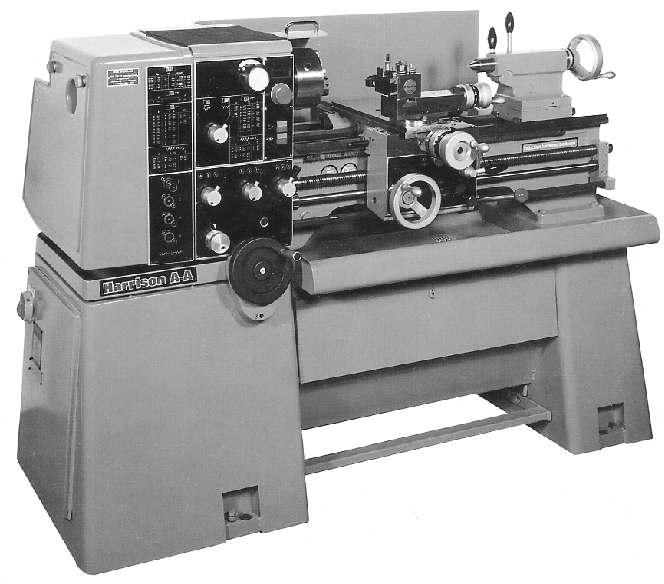 |
|
|
|
|
|
|
The 330 mm (13") swing by 635 mm (25") between centres Harrison AA was a small, very well specified toolroom-quality lathe constructed to International Precision Lathe Standards ISO R1708 and BS 4656 (UK) and DIN 8605 (Germany); it replaced the previous small variable-speed drive Harrison lathe, the 10-AA, that had been a re-badged Colchester Chipmaster.
|
|
|
|
|
|
|
|
|
|
|
|
|
|
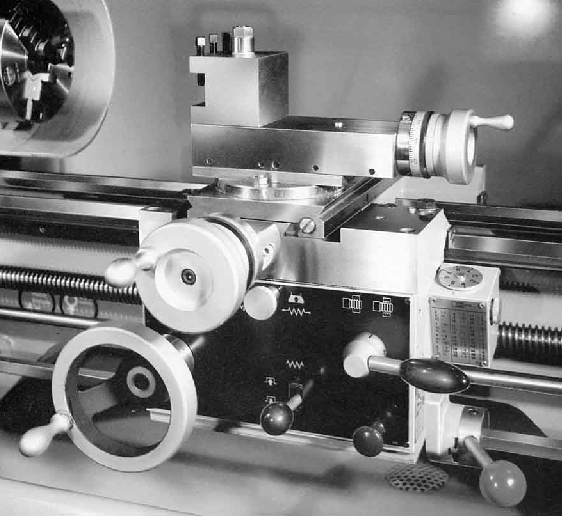 |
|
|
|
|
|
|
The carriage was constructed along traditional Harrison lines with a full-length cross slide and a top slide that swivelled through 360 degrees; both the saddle-to-bed fitting, and the cross slide were fitted with proper taper-key gib strips that allowed very fine control over their free movement and, as standard, the compound slide feed screws were fitted with dual-reading English/metric micrometer dials. The cross-feed screw nut was equipped with the same type of effective anti-backlash adjustment employed for many years on all the larger Harrison (and Colchester) lathes.
|
|
|
|
|
|
|
|
|
|
|
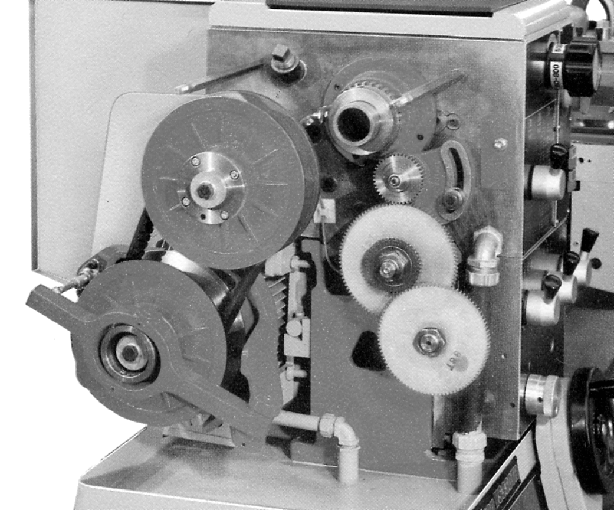 |
|
|
|
|
|
|
A 2.2 kW (3 hp) 1000 rpm totally-enclosed, fan-cooled motor was bolted, in the usual Harrison fashion, to a simply-engineered adjustable plate fastened to the back of the bed behind the headstock with (in a very compact arrangement) one variable-speed drive pulley fitted to the motor's shaft and the other to the input shaft of the headstock. The intermediate drive gears to the feeds and screwcutting gearbox were in a quiet-running, non-metallic material which required no lubrication.
|
|
|
|
|
|
|
|
|
|
|
|
|
|
|
|
|
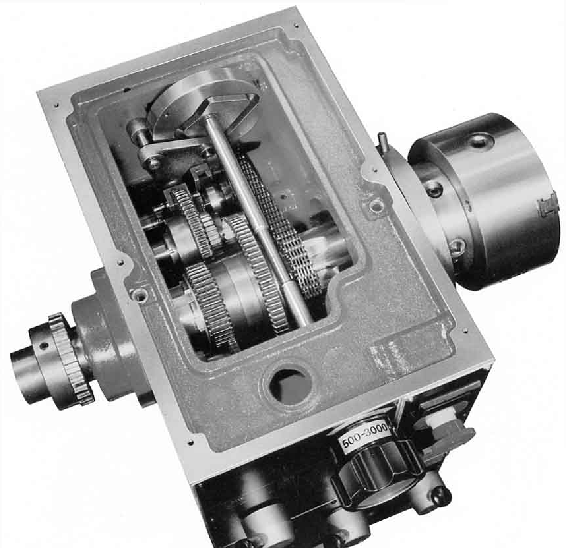 |
|
|
|
|
|
|
Gears, together with an "inverted chain" drive in the headstock and in combination with a quiet-running mechanical variable-speed drive unit, gave three separate overlapping speed ranges which equated to: 35 to 180 rpm, 180 rpm to 500 rpm and 500 to 3000 rpm.
|
|
|
|
|
|
|
|
|
|
|
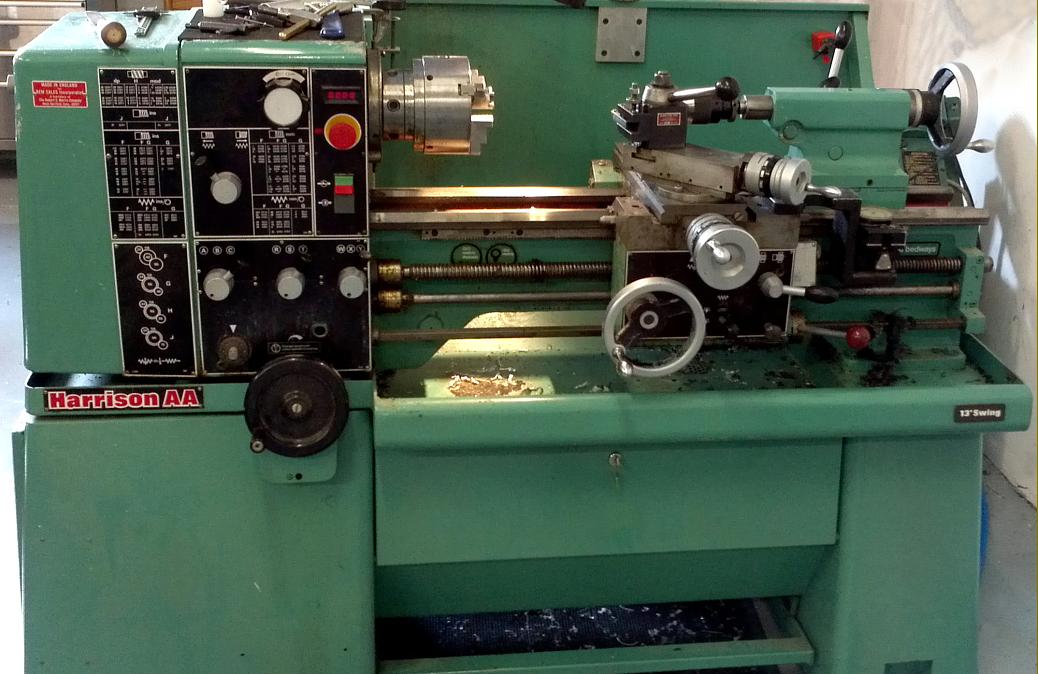 |
|
|
|
|
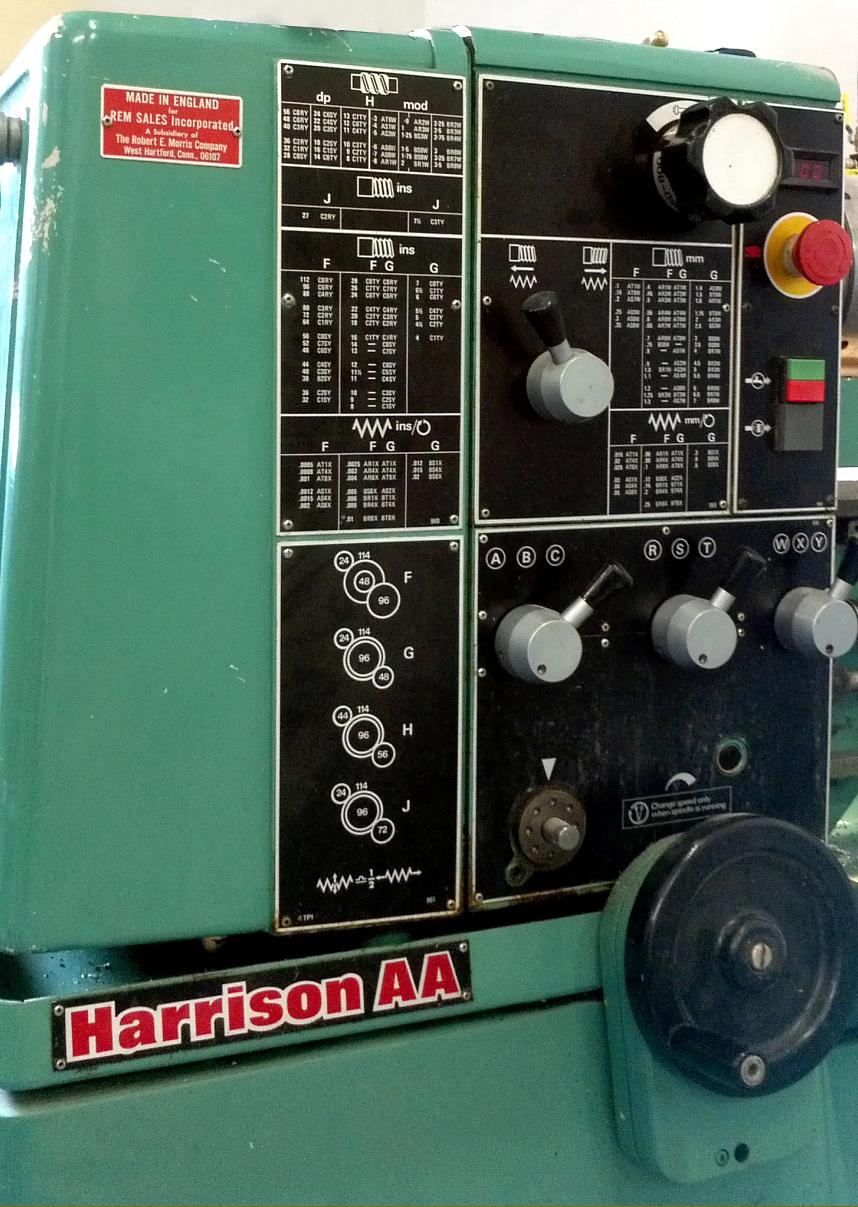 |
|
|
|
|
|
|
|
|
|
|
|
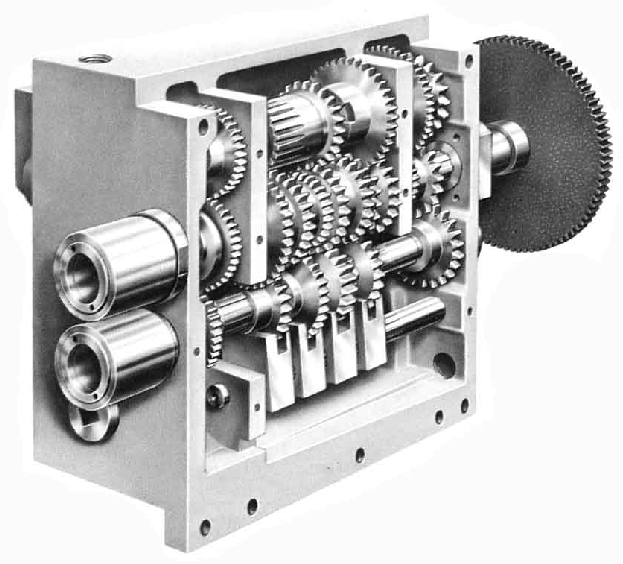 |
|
|
|
|
|
|
The screwcutting gearbox followed modern practice in being constructed from a totally enclosed, one-piece casting that held a supply of lubricant in the base from where it was distributed by splash. The gears were all induction hardened with the threading and feed ranges selected by three levers and an 8-position dial; a total of 39 metric, 35 English, 18 Module and 18 Diametrical pitches could be achieved by moving the control levers and either rearranging the standard changewheel set - or employing some of the extra non-metallic (hence quiet-running) gears which were supplied with the machine in order for it to achieve its full threading range.
|
|
|
|
|
|
|
|
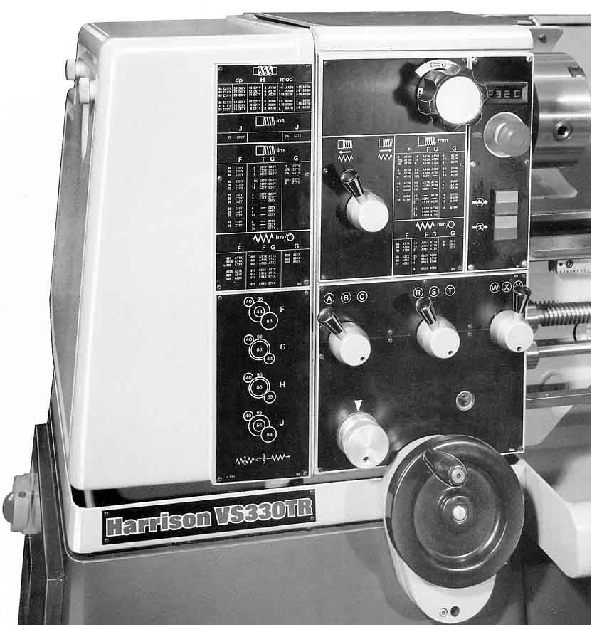 |
|
|
|
|
|
|
With no gearlevers to set, or belts to move - and hence no mechanical indication of the spindle speed - some form of digital speed readout was required; unfortunately, instead of being a large, clear unit angled so that the operator could read it without hesitation, it was a rather tiny, insignificant affair tucked away in the top right hand corner of the headstock's front face.
|
|
|
|
|
|
|
|
|
|
|
|
|
|
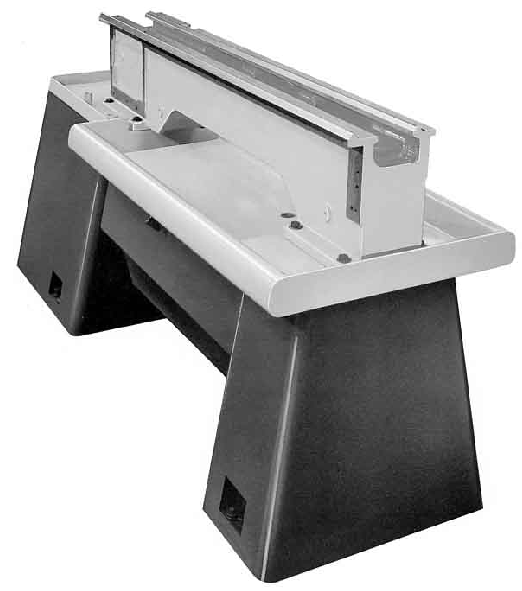 |
|
|
|
|
|
|
The straight bed (there was no option of a gap) was induction hardened and fastened to a heavy-gauge sheet-metal stand which was fitted not only with the usual splash back, but a locking tool cupboard as well.
|
|
|
|
|
|
|
|
|
|
|
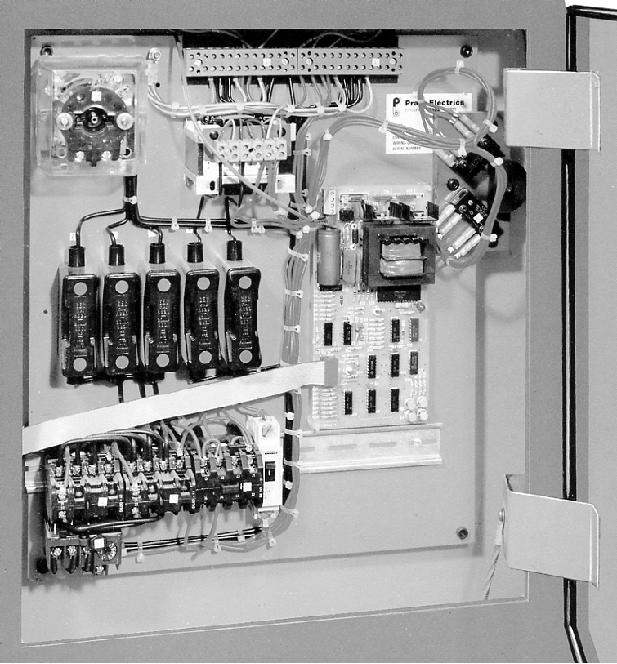 |
|
|
|
|
|
|
The 110-volt electrical control equipment was neatly built into a single compartment on the left-hand end of the stand, access being through a door protected by a mechanically interlocked isolator switch. The lathe was not fitted with a clutch, but relied instead upon direct on-line starting through forward and reverse contactors with 'emergency stop' available though a button mounted on the headstock and a full-length foot bar between the cabinet feet; the main spindle stop, start, forward and reverse control was by a gated lever fastened to the right-hand face of the apron.
|
|
|
|
|
|
|
|
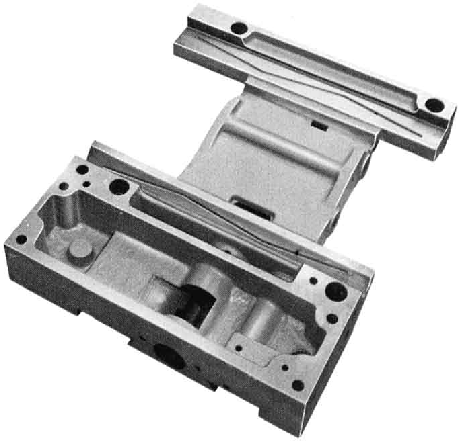 |
|
|
|
|
|
|
The pumped oil supply from the apron was distributed to long grooves in the V ways of the saddle.
|
|
|
|
|
|
|
|
|
|
|
|
|
|
|
|
|
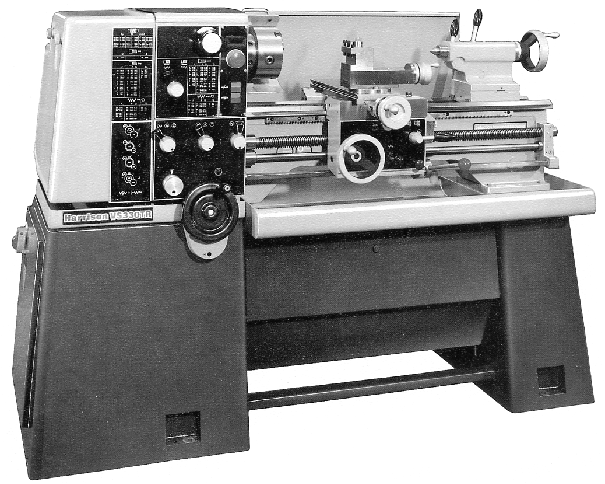 |
|
|
|
|
|
|
330 mm (13") swing by 635 mm (25") between centres Harrison VS330TR
|
|
|
|
|
|
|
|
|
|
|
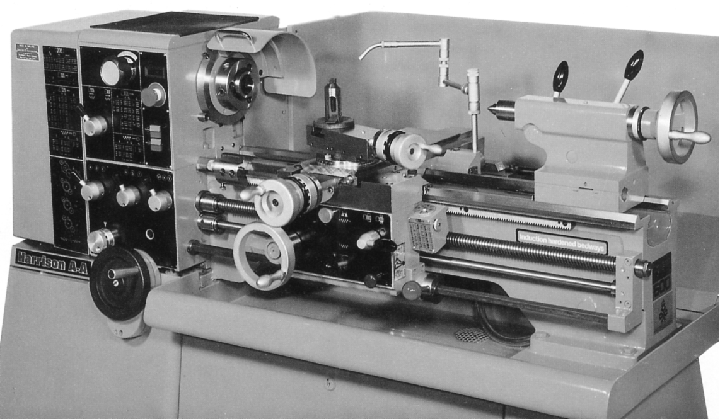 |
|
|
|
|
|
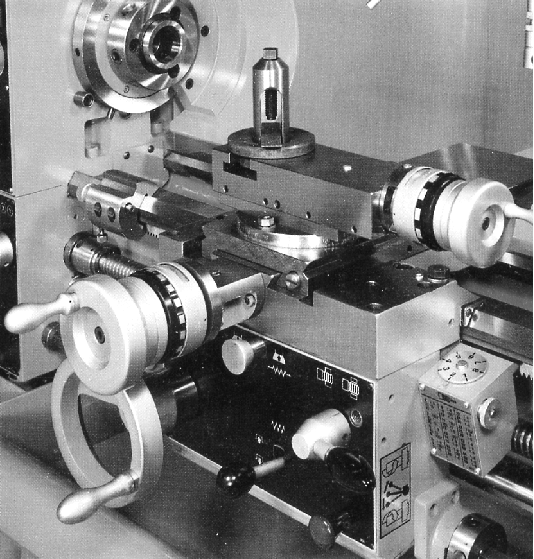 |
|
|
|
|
|
|
|
|
|
|
|
|
The carriage was constructed along traditional Harrison lines with a full-length cross slide and a top slide that swivelled through 360 degrees; both the saddle-to-bed fitting, and the cross slide were fitted with proper taper-key gib strips that allowed very fine control over their free movement and, as standard, the compound slide feed screws were fitted with dual-reading English/metric micrometer dials. The cross-feed screw nut was equipped with the same type of effective anti-backlash adjustment employed for many years on all he larger Harrison (and Colchester) lathes.
|
|
|
|
|
|
|
|
|
|
|
|
|
|
|
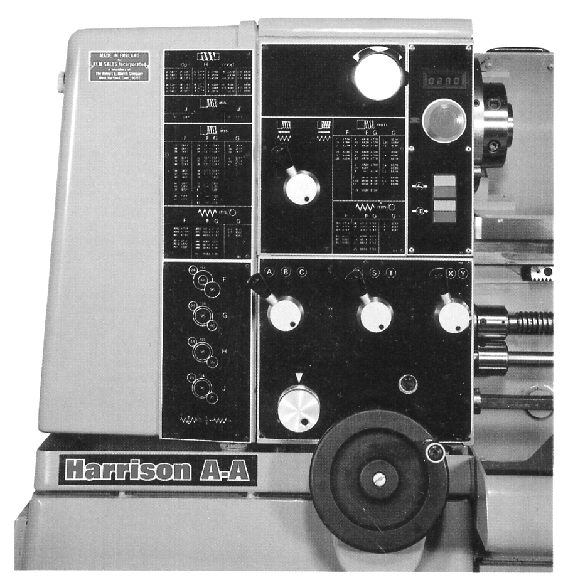 |
|
|
|
|
|
|
With no gearlevers to set, or belts to move - and hence no mechanical indication of the spindle speed - some form of digital speed readout was required; unfortunately, instead of being a large, clear unit angled so that the operator could read it without hesitation, it was a rather tiny, insignificant affair tucked away in the top right hand corner of the headstock's front face.
|
|
|
|
|
|
|
|
|
|
|
|
|
|
|
|
|
|
|