 |
 |
 |
 |
 |
 |
 |
 |
 |
 |
 |
 |
 |
 |
 |
 |
 |
 |
 |
 |
 |
 |
 |
 |
 |
 |
 |
 |
 |
 |
 |
 |
 |
 |
 |
 |
 |
 |
 |
 |
 |
 |
 |
 |
 |
 |
 |
 |
 |
 |
 |
 |
 |
 |
 |
 |
 |
 |
 |
 |
 |
 |
 |
 |
 |
 |
 |
 |
 |
 |
|
|
|
|
|
|
|
|
|
|
|
|
|
|
|
|
|
|
|
|
|
|
|
|
|
|
|
|
|
|
|
|
|
|
|
|
|
|
|
|
|
|
|
|
|
|
|
|
|
|
|
|
|
|
|
|
|
|
|
|
|
|
|
|
|
|
|
|
|
|
|
|
|
|
|
|
|
|
|
|
|
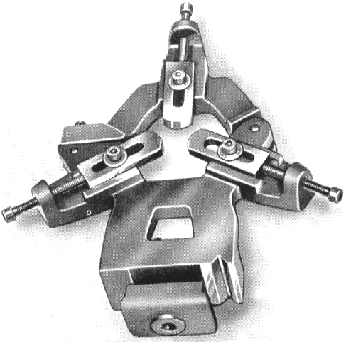 |
|
|
|
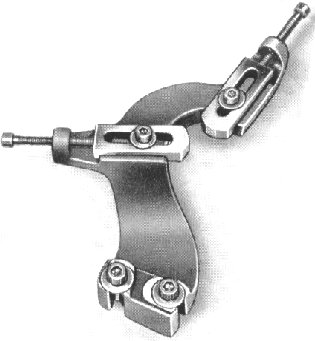 |
|
|
|
|
|
|
|
|
|
|
|
|
|
|
|
|
|
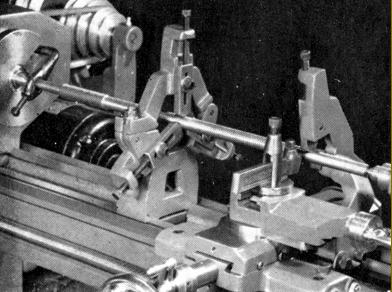 |
|
|
|
|
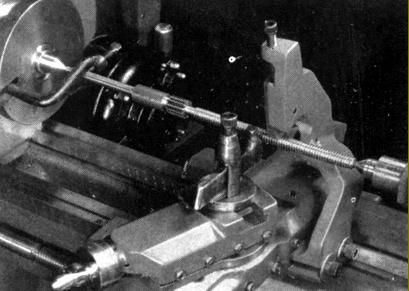 |
|
|
|
|
|
|
|
|
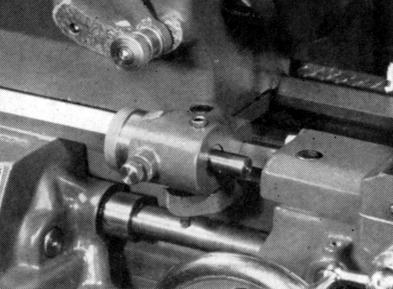 |
|
|
|
|
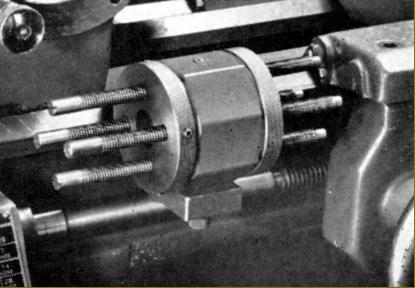 |
|
|
|
|
|
|
|
4-position rotating Multi-stop
|
|
|
|
|
|
|
Micrometer-stop for saddle traverse
|
|
|
|
|
|
|
|
|
|
|
|
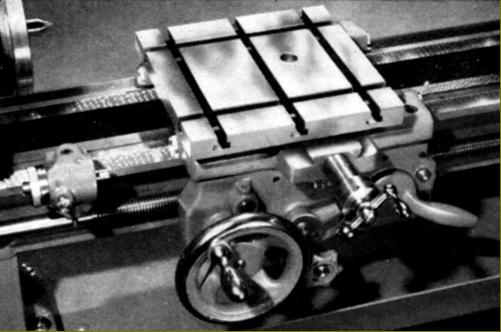 |
|
|
|
|
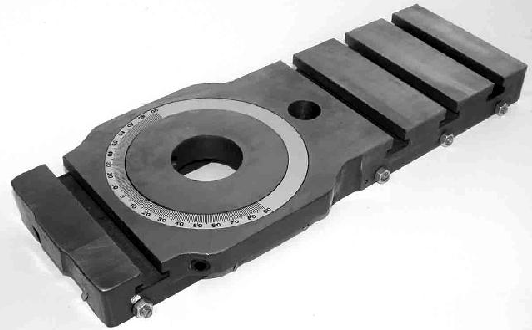 |
|
|
|
|
|
|
Boring TableT slotted cross slide and boring table. Some cross slides had only one T slot to the rear, others had three or even four. The boring table, always a comparatively expensive option, simply slid into position in place of the cross slide; today, it is a rare to find one with a used machine. New T-slotted slides are available, email for details.
|
|
|
|
|
|
|
|
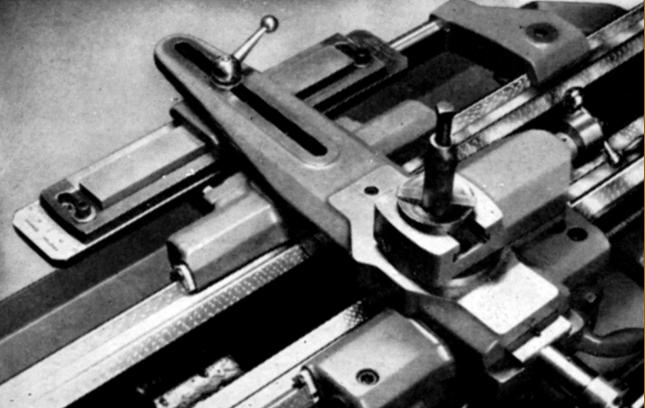 |
|
|
|
|
|
|
|
|
|
|
|
|
|
|
|
|
|
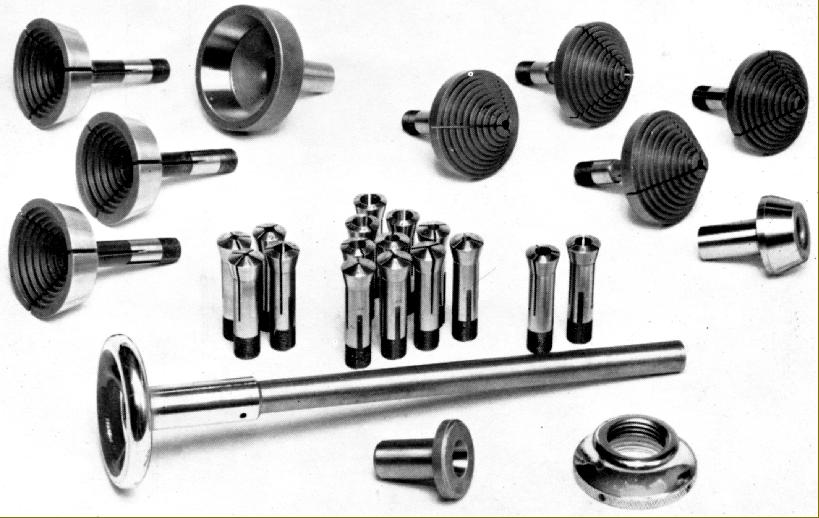 |
|
|
|
|
|
|
|
|
|
Draw-in collet attachment: Handwheel and hollow draw bar, tapered closing sleeve and spindle-nose thread protector. If you need to make one, here is the data: the draw tube is 3/4 inch OD and the bore at the collet end 19/32 (0.594) inch diameter. At the collet end it is tapped with a 26 t.p.i right-hand 60-degree (American) V thread, for a length of 3/4 inch. The maximum diameter of the (female) thread is 0.645 inch, i.e. the depth of thread is (0.645 - 0.594)/2 = 0.0256 inches.
|
|
|
|
|
|
|
|
|
|
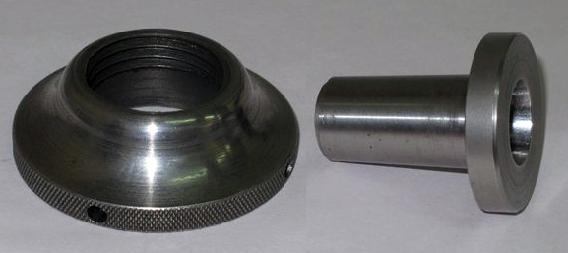 |
|
|
|
|
|
|
|
|
|
Collet nose adapter and protector as used on South Bend 9-inch lathes and early models of the Boxford. Later Boxford versions of the cap had a slightly different exterior profile and were chrome plated
|
|
|
|
|
|
|
|
|
|
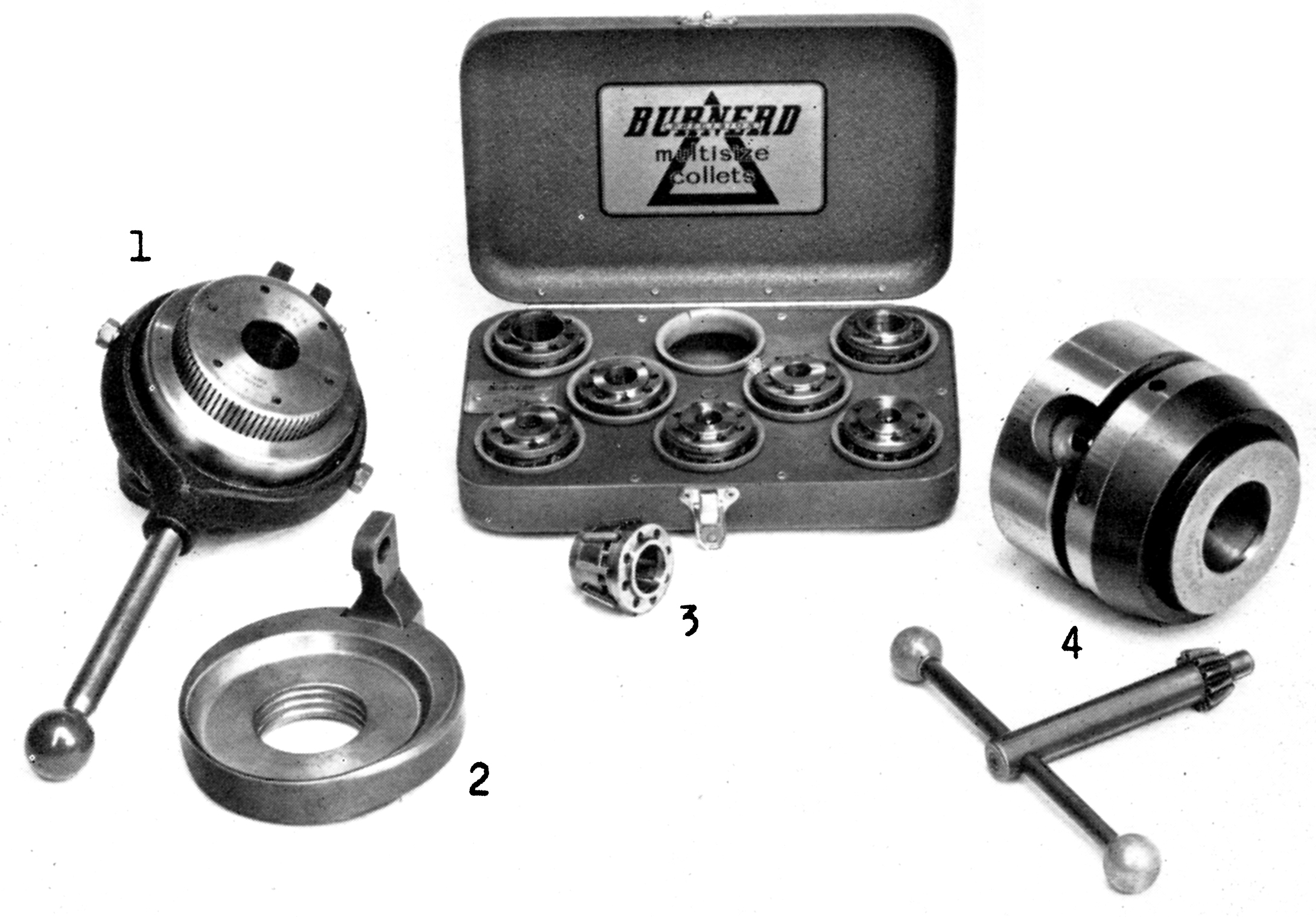 |
|
|
|
|
|
|
|
|
|
A wonderfully useful, if rare and originally expensive fitting, a Burnerd Multi-size collet chuck set. Two chucks were available, the No.1 was a lever-action type (that used Part No.2 as a backing plate to form the fulcrum point for the lever), and No. 4, a slower-to-use, key-operated type. Both chucks used "spring" collets (3) that could be adjusted over a small range of size (covering both inch and metric bar-stock metric) by screwing in or out a ring on the chuck's face
|
|
|
|
|
|
|
|
|
|
|
|
|
|
|
|
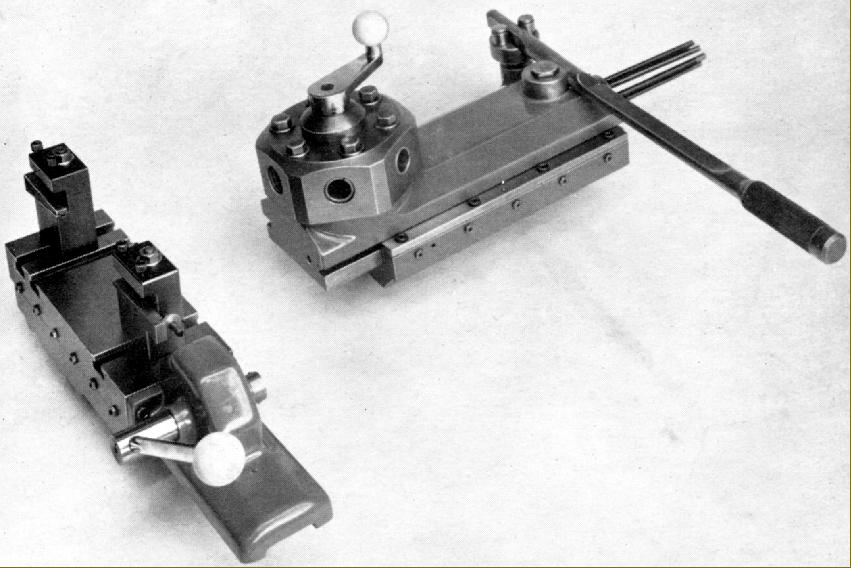 |
|
|
|
|
|
|
|
|
|
Boxford production capstan unit and lever-operated cut-off slide
|
|
|
|
|
|
|
|
|
|
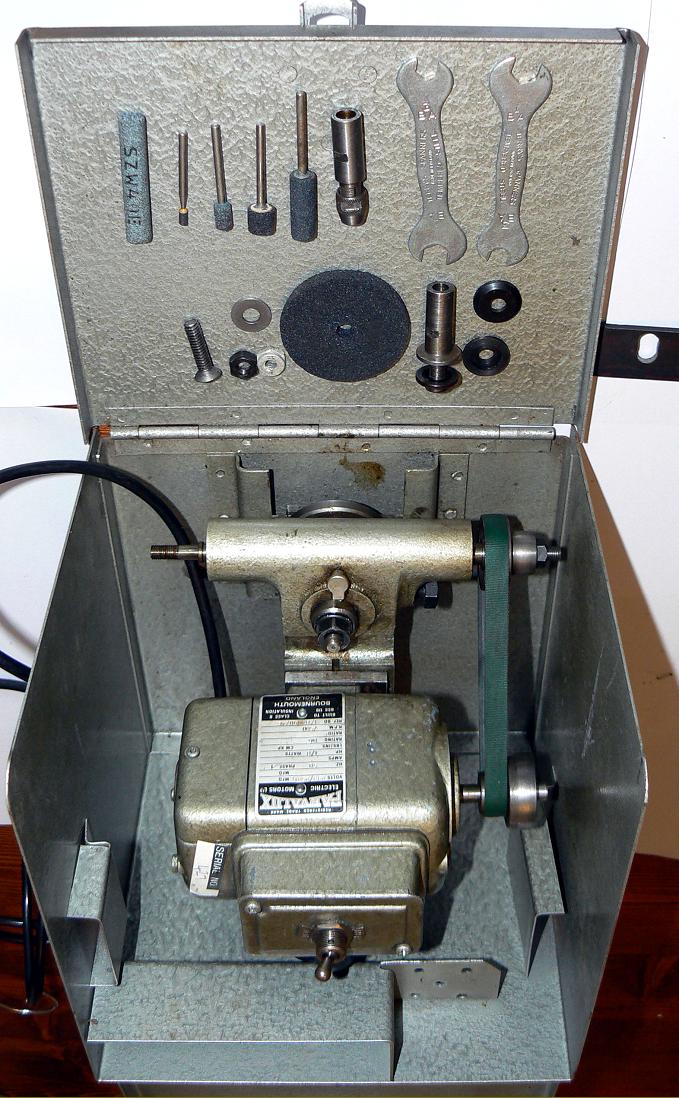 |
|
|
|
|
|
|
A late-model example of the expensive-when-new "Little Giant" toolpost grinder> Now a sought-after accessory, it was supplied, complete with accessories, in a particularly neat fitted metal case. Although normally mounted in the toolpost of Boxford lathe - and all the other South Bend Clones - the grinder can, by just changing the T-bolt, also be fitted to a variety of small lathes from 3 to 5-inch centre height. Although intended for the micro finishing of particularly accurate parts, it also comes into its own when a modification has to be made to a part so hard that it cannot be turned. The mechanical parts of Boxford unit appear to have been made by the American company Dumore (whose identical model, the Series 14, was called the "Tom Thumb") though the round-body motor fitted was always of English manufacture. Dumore are still going and can provide a wide range of accessories inkling extension spindles for internal grinding While earlier models had a round motor and usually an all-over silver finish, later models - some of which had a base painted brown - had a "square" English-made Parvalux rectangular motor in a light-green "Hammerite finish. On this version the spindle thread was changed to a Whitworth-form 1/4" x 32 t.p.i.
|
|
|
|
|
|
|
|
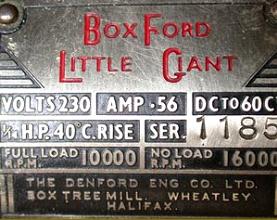 |
|
|
|
|
|
|
|
|
|
|
|
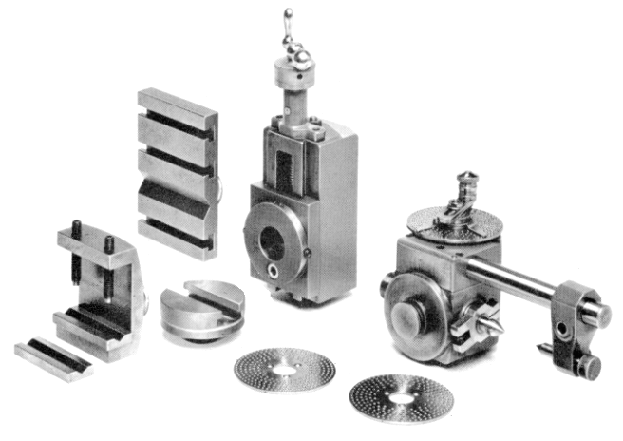 |
|
|
|
|
|
Boxford milling and dividing attachment. This cleverly designed, beautifully made but very expensive (and difficult-to-find) assembly features completely interchangeable components. The T slotted table, vice and dividing unit all have a mounting spigot identical to that used on the top slide - and so can be fitted either to the milling column, or used independently on the cross slide. The 40: 1 ratio dividing head (supplied with either two or three plates) was a direct fit on the milling slide using the inverted come mounting. The spindle passed through the main casting and had, at one end, a No. 1 Morse taper centre and a drive plate - this allowed work to be turned between centres with the second centre held by the drop bracket sliding along the overarm. At the other end of the spindle was 1.125" x 8 t.p.i. thread intended to mount chucks or other threaded fittings. The maximum diameter of work ble to be held between centres was 80 mm (3") and the maximum length 90 mm (3.5") Additional pictures lower down the page.
|
|
|
|
|
|
|
|
|
|
|
|
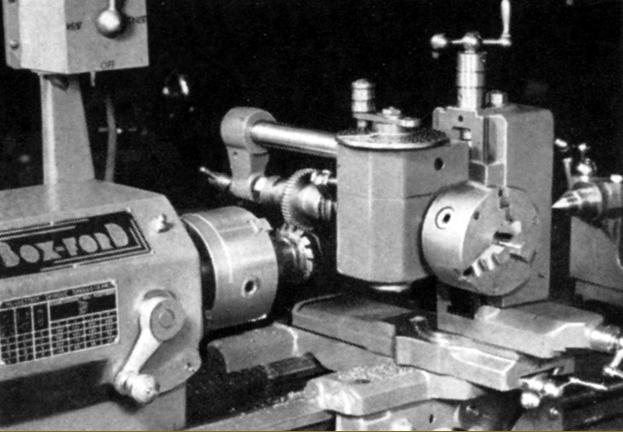 |
|
|
|
|
|
|
|
|
|
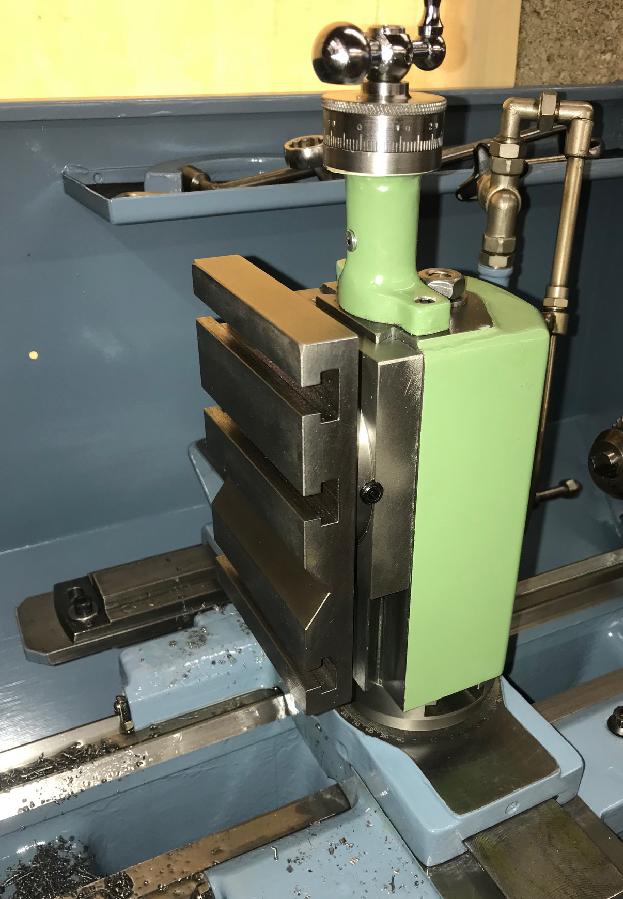 |
|
|
|
|
|
|
Boxford slide with attached T-slotted table mounted on a late-model VSL
|
|
|
|
|
|
|
|
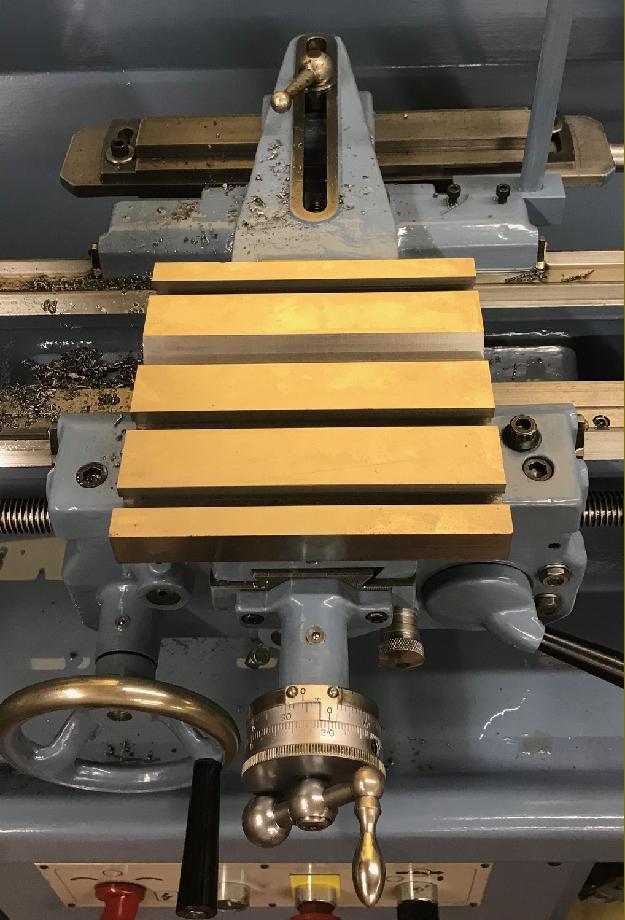 |
|
|
|
|
|
|
The T-slotted table from the slide could also, most usefully, be mounted in place of the top slide
|
|
|
|
|
|
|
|
|
|
|
|
|
|
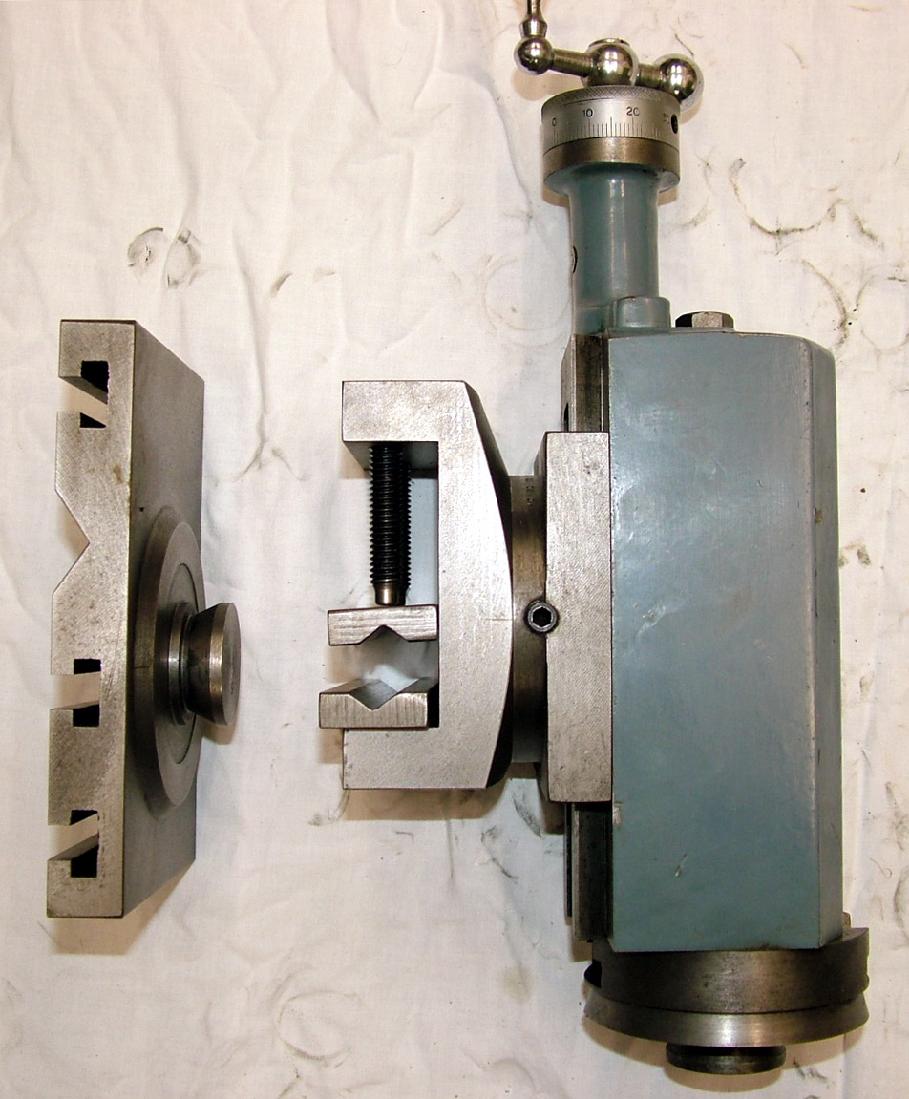 |
|
|
|
|
|
|
Boxford milling and dividing attachment. This cleverly designed, beautifully made but very expensive (and difficult-to-find) assembly featured completely interchangeable components. The T slotted table, vice and dividing unit all had a mounting spigot identical to that used on the top slide - and so could be fitted to either the milling column, or used independently on the cross slide.
|
|
|
|
|
|
|
|
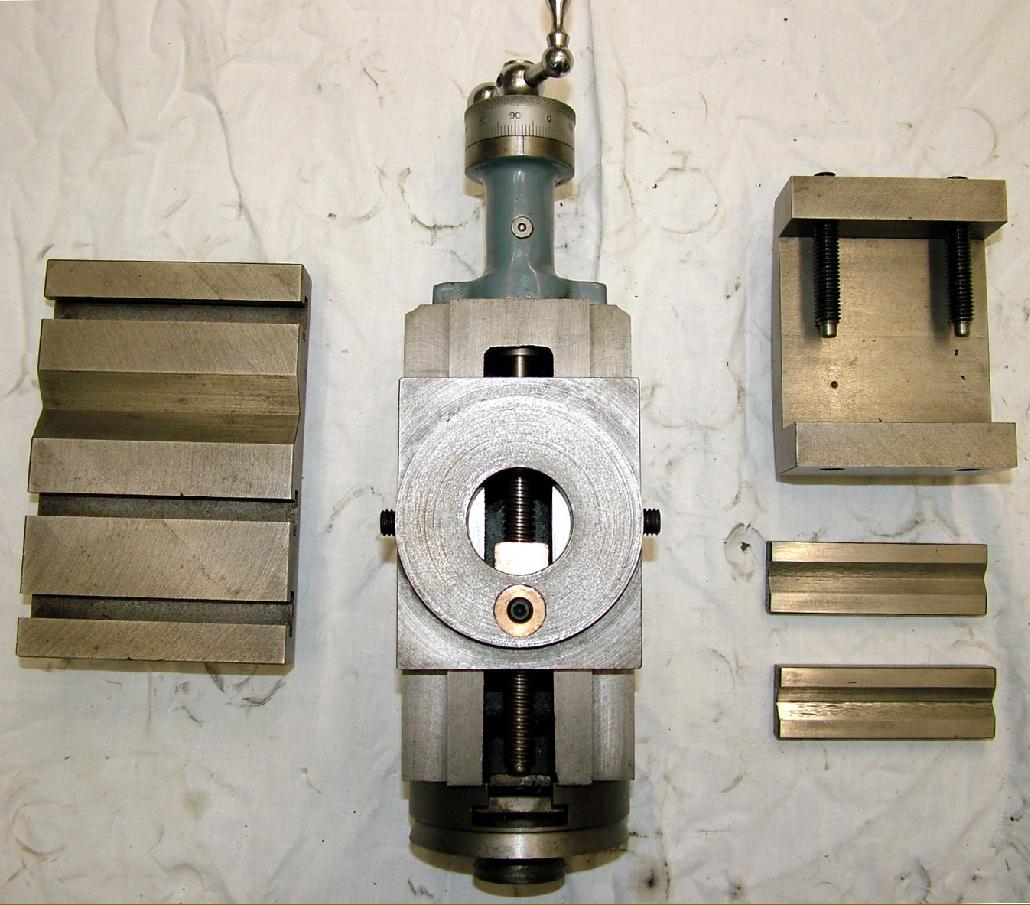 |
|
|
|
|
|
 |
|
|
|
|
|
|
|
|
|
|
|
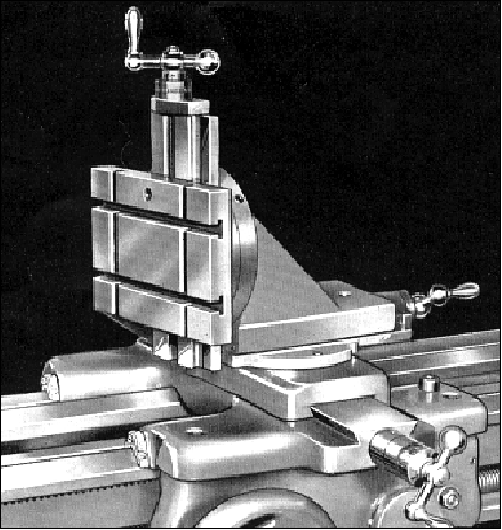 |
|
|
|
|
Produced in very limited numbers - the ultra-rare and very useful "compound" milling slide
|
|
|
|
|
|
|
|
|
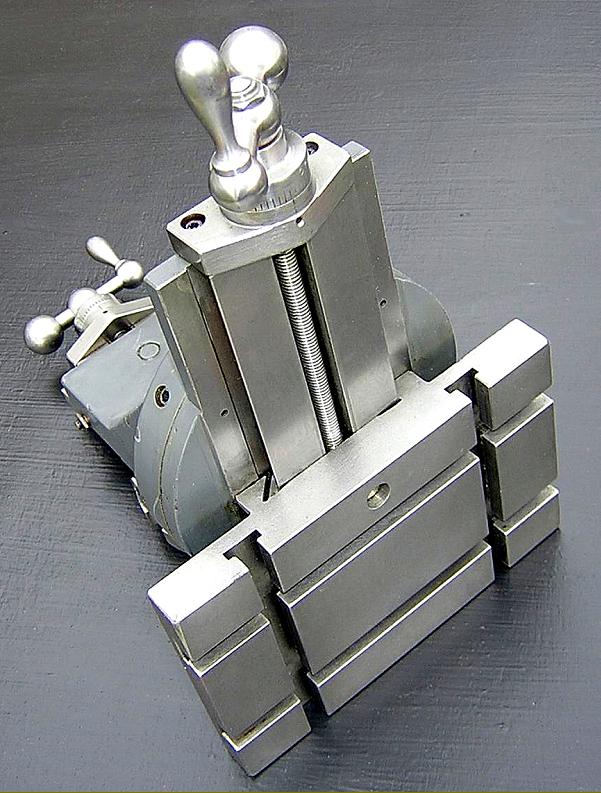 |
|
|
|
|
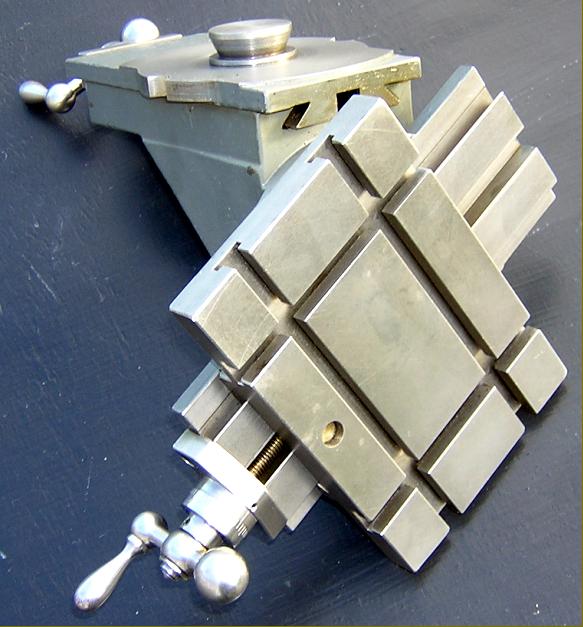 |
|
|
|
|
|
|
|
|
Very hard to find - though very useful to own - the Boxford Compound milling slide mounted in place of the top slide. With 360° of swivel on the base and something like 270° on the T-slotted slide before it contacted the bed, it was possible to arrange even awkward jobs satisfactorily.
|
|
|
|
|
|
|
|
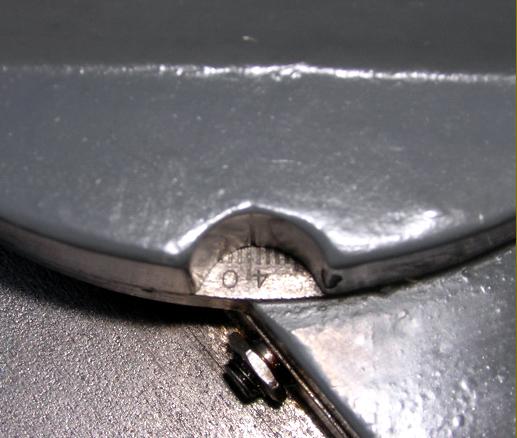 |
|
|
|
|
|
|
|
|
|
|
|
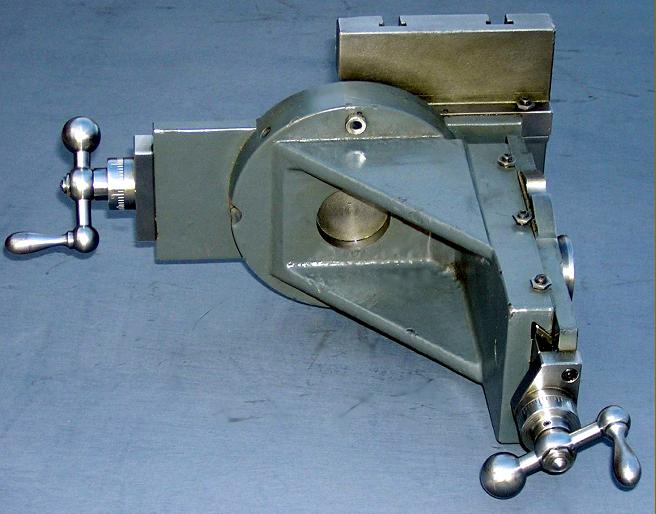 |
|
|
|
|
|
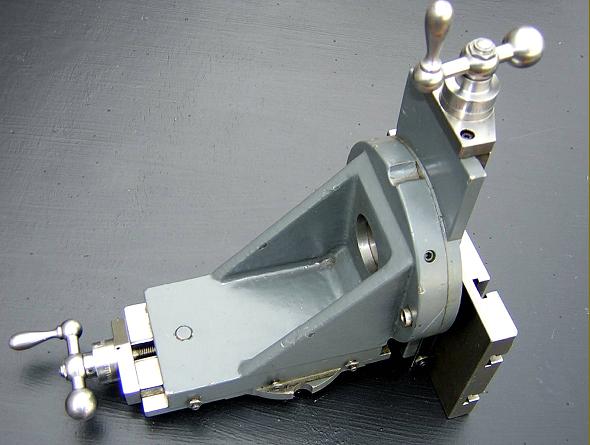 |
|
|
|
|
|
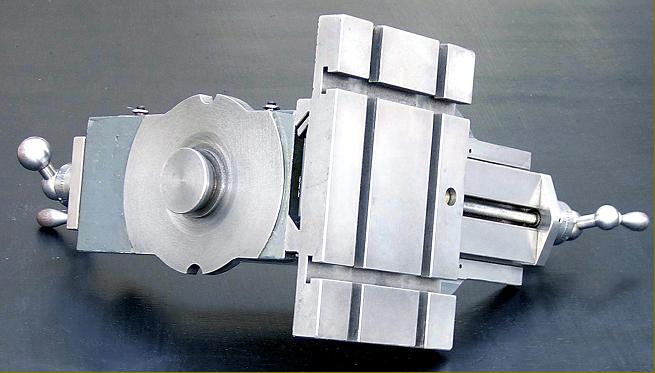 |
|
|
|
|
|
|
|
|
|
|
|
|
|