 |
 |
 |
 |
 |
 |
 |
 |
 |
 |
 |
 |
 |
 |
 |
 |
 |
 |
 |
 |
 |
 |
 |
 |
 |
 |
 |
 |
 |
 |
 |
 |
 |
 |
 |
 |
 |
 |
 |
 |
 |
 |
 |
 |
 |
 |
 |
 |
 |
 |
 |
|
|
|
|
|
|
|
|
|
|
|
|
|
|
|
|
|
|
|
|
|
|
|
|
|
|
|
|
|
|
|
|
|
|
|
|
|
|
|
|
|
|
|
|
|
|
|
|
|
|
|
|
|
|
|
|
|
|
|
|
|
|
|
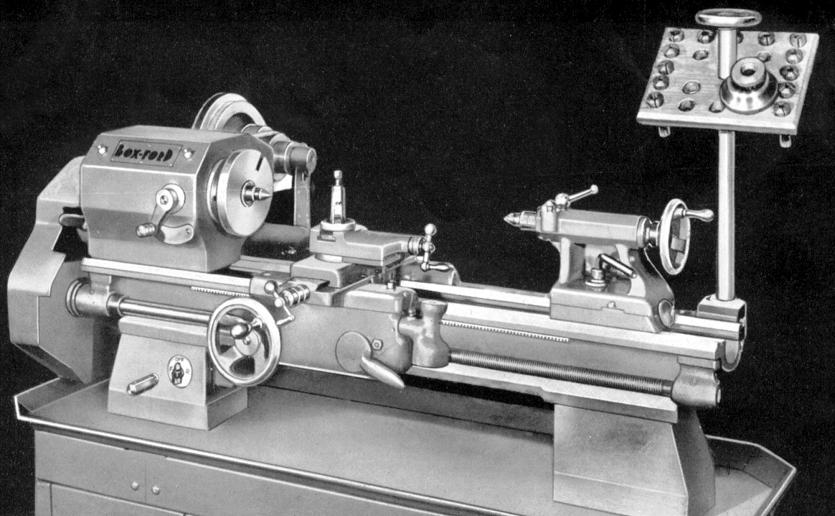 |
|
|
|
|
|
|
Above: the earliest known publicity photograph of a Boxford, this 1948 Model C had 3-step flat belt drive to the headstock, no headstock or countershaft belt-run guards, a tailstock held to the bed by a simple vertical bolt through the clamp plate and the electrical switch on the headstock-end bed foot. The countershaft was of the integral type, fastened to the back of the lathe and mounted on slider rails with a push/pull quick-action "screw" - the hexagon head of which can be seen protruding through the front of the bed foot. The collet tray clamped to the bed at the headstock end held not only the collets but the draw tube, spindle insert adaptor and thread protector. On the very first examples the lathe was fastened to the stand by two in-line bolts that passed upwards into the aluminium bed feet. The next version, as shown immediately below, used three bolts with two being set across the bed and passing through a flange on the inner face of the foot - with the other on the foot's centre line. The final type, and found on most machines, was a simpler arrangement of two bolts - one at the front and the other at the rear of each foot. For a complete description of all Boxford lathes go to the Boxford home page
|
|
|
|
|
|
|
|
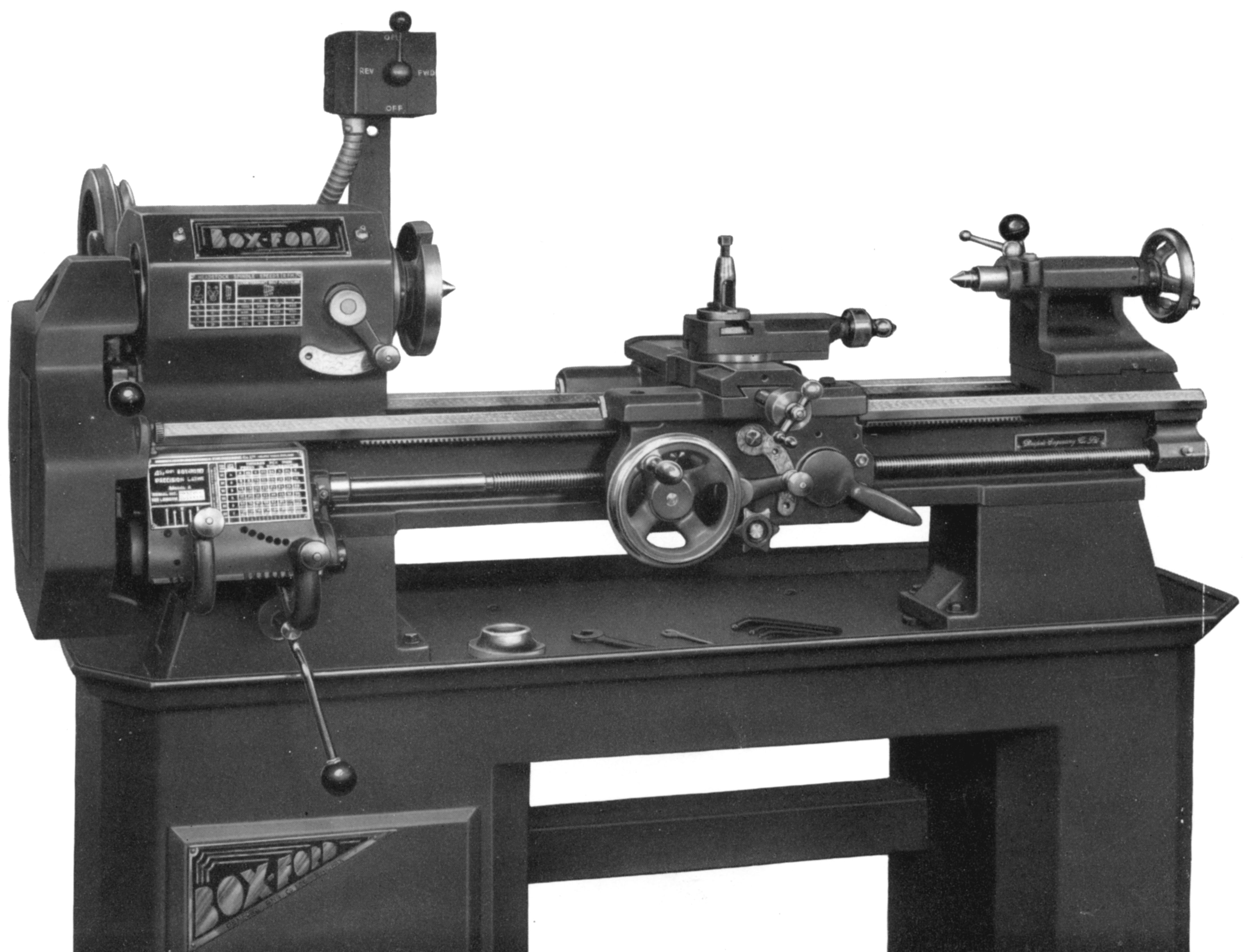 |
|
|
|
|
|
|
Circa 1952/3 Model A with screwcutting gearbox and power cross feed. The early form of quick-lock countershaft with its front-mounted handle was still in use and the belt run from the countershaft remained unguarded.
|
|
|
|
|
|
|
|
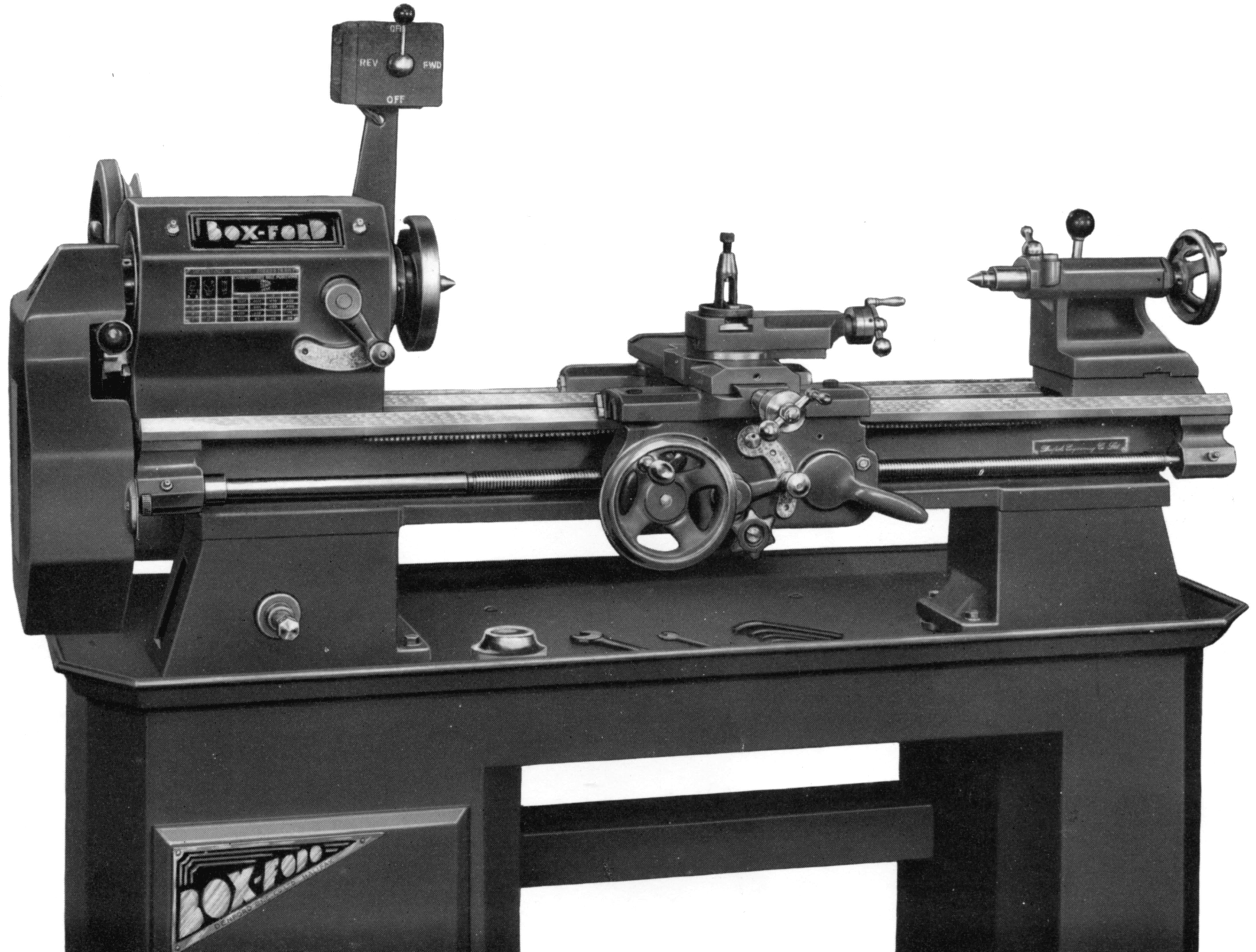 |
|
|
|
|
|
Circa 1952/3 Model B with screwcutting by changewheels and power cross feed.
|
|
|
|
|
|
|
|
|
|
|
|
|
|
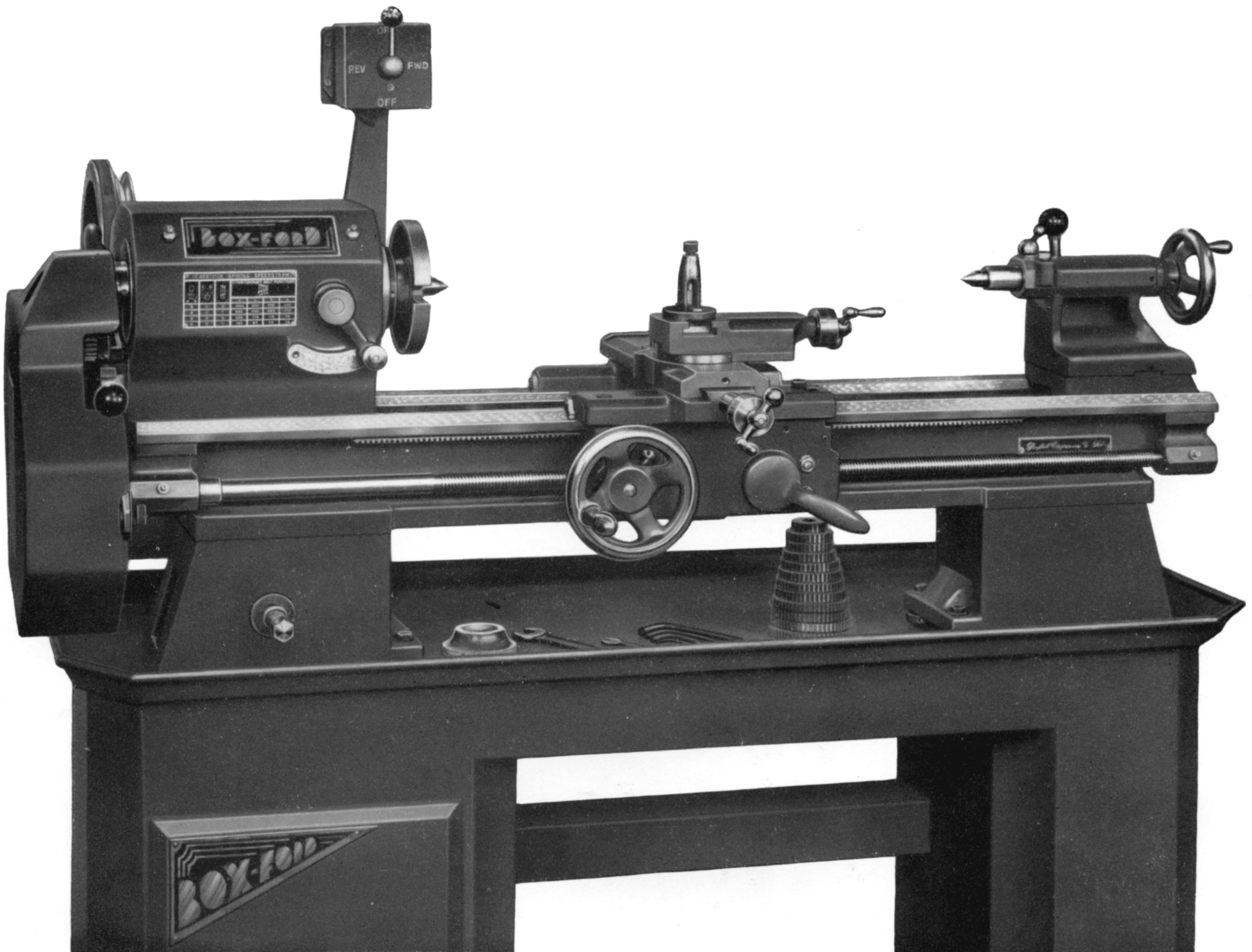 |
|
|
|
|
|
|
Circa 1952/3 Model C with screwcutting by changewheels and hand cross feed
|
|
|
|
|
|
|
|
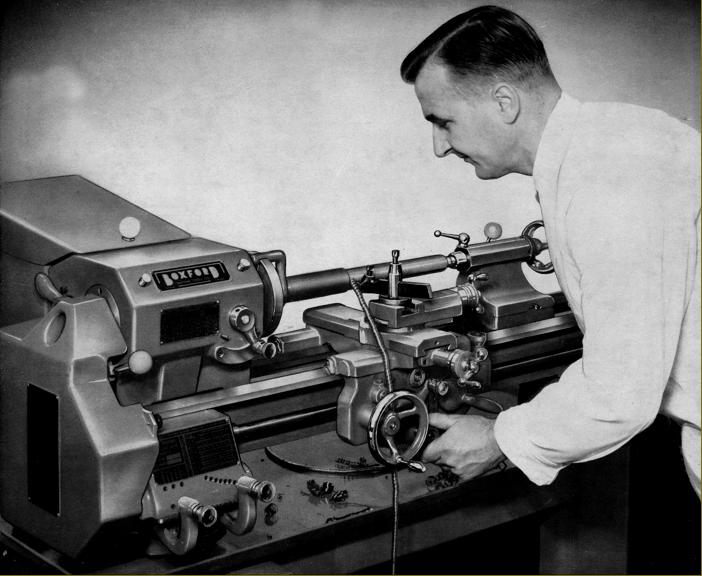 |
|
|
|
|
|
Later Boxford Model A with screwcutting gearbox and power cross feed. By the early 1950s the belt runs were completely guarded, the tailstock had a captive locking handle working though a cam and the electrical switch had been moved from the bed foot to a more convenient and safer position on a bracket bolted to the headstock.
|
|
|
|
|
|
|
|
|
|
|
|
|
|
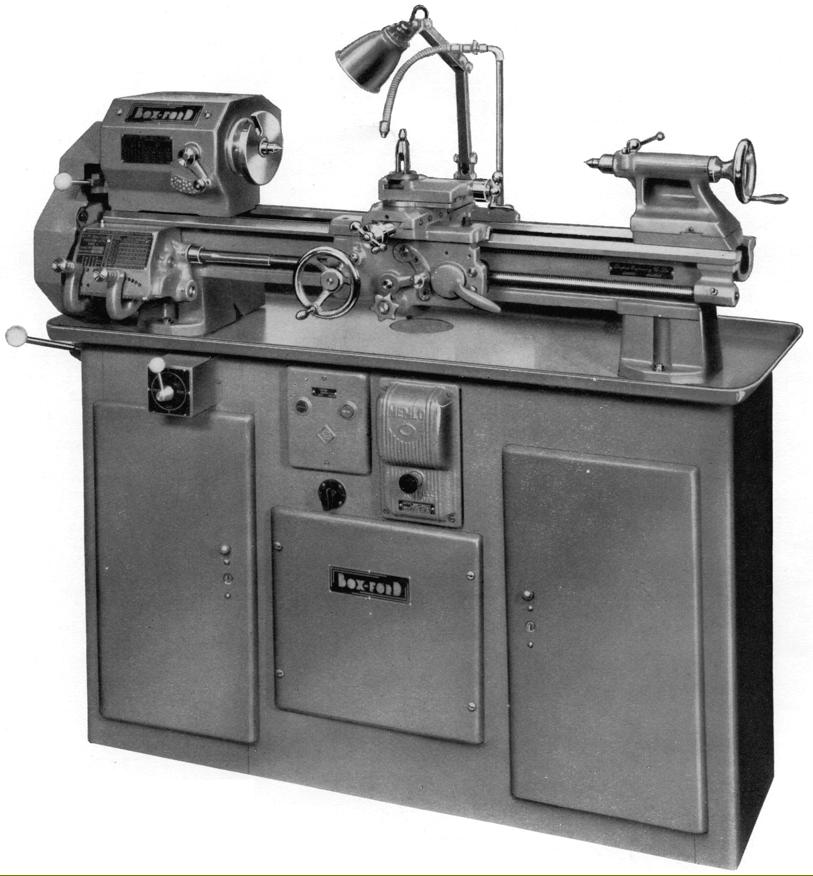 |
|
|
|
|
|
First version of the Underdrive lathe - in this case a Mk. 1 Model AUD with screwcutting gearbox and power sliding and surfacing feeds (note the countershaft belt-tensioning lever protruding through the left-hand face of the stand). While rear-drive lathes had 6, 8 or 16 spindle speeds all the under-drive machines, with the exception of the variable-speed VSL, were limited to 10. With some variations, because of special orders or educational and training use, the usual range on the back-drive type was 30 to 1250 rpm whilst the Mk. 1 and Mk. 2 Underdrive types of all models (CUD, BUD and AUD) generally ran at 40, 66, 105, 165 and 270 r.p.m. in backgear and 210, 340, 540, 850 and 1400 r.p.m in open belt drive. However, on the latter machines (at extra cost) the factory could provide a more powerful motor and a "high-speed" pulley set that increased the maximum to just over 2000 r.p.m. - but at the sacrifice of increasing the bottom speed to such an extent that it was difficult for beginners to cut threads.
|
|
|
|
|
|
|
|
|
|
|
 |
|
|
|
|
|
|
Underdrive stand as used on the AUD, BUD, CUD and TUD models
|
|
|
|
|
|
|
|
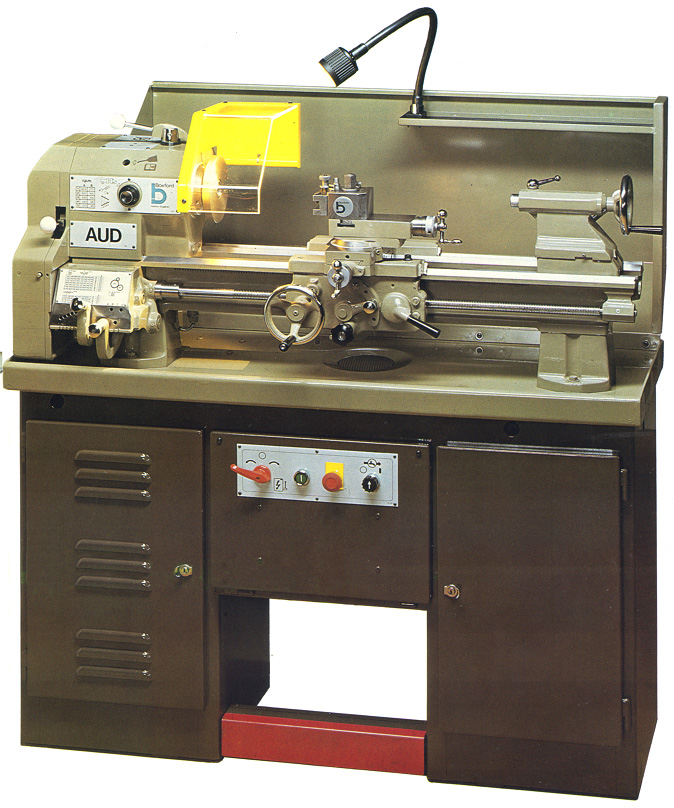 |
|
|
|
|
|
Some confusion surrounds exactly when the final version of the Underdrive, the Mk. 3, was put on the market. The official release date was May 1976, but machines have been found that pre-date this, for example: AUD III-33777 with a bed casting dated 1974 and with year also correctly corresponding to the Serial Number list. These lathes were distinguished by a more modern-looking stand complete with a neat splash-back, standard-fit low-voltage halogen light unit and a rather elegant grey and brown finish. However, the designation Mk. 3 was never acknowledged in the advertising literature, though it was used in the spares department to identify the particular models. During October and November 1981 the colour scheme was changed, temporarily, to green - a shade that can be replicated by ordering "Reseda Green B.S. Standard RAL6011".
|
|
|
|
|
|
|
|
|
|
|
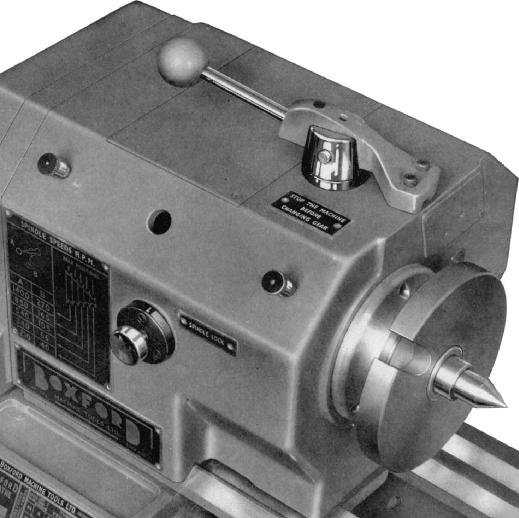 |
|
|
|
|
|
|
|
|
Mk. 2 headstock with a single lever to engage and disengage backgear. For safety the lever could be locked down into its two positions with Allen screws - and was also connected to a micro-switch that cut power if the handle was moved while the spindle was turning. Moving the lever slides the lathe "Bull Wheel" along the spindle to either engage or disengage it with the 4-step V-pulley while simultaneously moving the other gears into and out of mesh (to understand how backgear systems work see the article Lathe Backgear). Before using the backgears, look through the hole drilled in the sloping face on the front of the headstock and turn the chuck by hand until an oil nipple appears. Using a lever-action oil can with a plastic spout, apply no more than three pumps of oil to lubricate the pulley-to-spindle bearing. Find and oil the other headstock nipples as well. If you are unsure about how the mechanism works, removing the small rectangular plate on top of the headstock (its secured by four Allen screws) will allow you to peer in and see what happens when the lever is moved. In addition, it's easy enough to take off the sheet-metal cover at the back of the headstock to give an even clearer view. As the label on the headstock says (if it's not been prised off by a former schoolboy operator) do not move the lever if the lathe is running; if you do, you'll smash the gears.
|
|
|
|
|
|
|
|
|
|
|
|
|
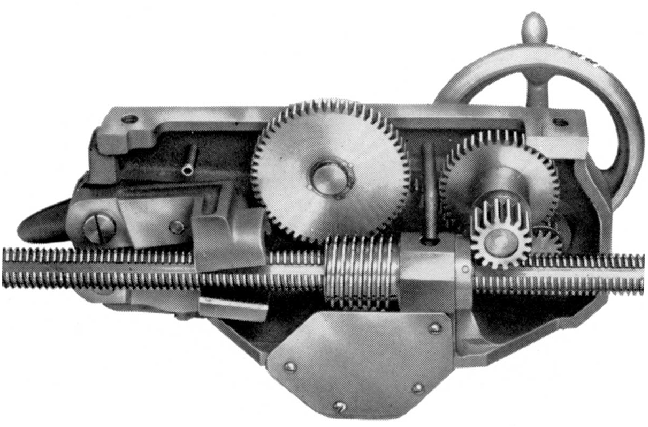 |
|
|
|
|
|
Virtually unchanged since it's introduction in the early 1930s on the South Bend 9-inch, the power-feed apron has proved capable of a long, trouble-free life
|
|
|
|
|
|
|
|
|
|
|
|
|
|
|
|
|
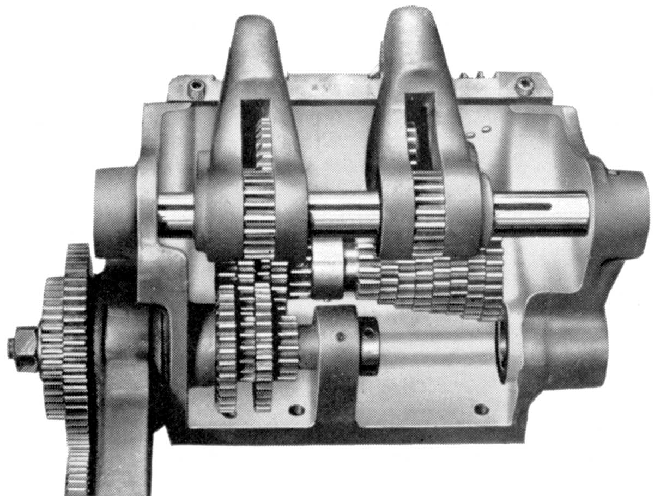 |
|
|
|
|
|
Another reliable component unaltered from first to last the screwcutting gearbox proved reliable - despite a lack of hardened gears and a reliance upon the operator applying an oil can occasionally as there was no oil-bath lubrication.
|
|
|
|
|
|
|
|
|
|
|
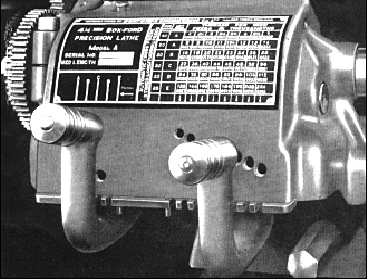 |
|
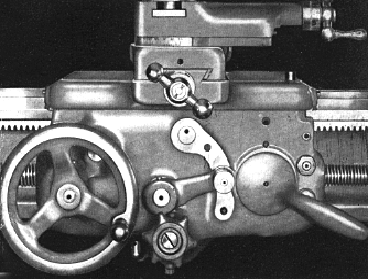 |
|
|
|
|
|
|
|
|
Models A and AUD Screwcutting gearbox. This version produced inch-pitch threads; the metric gearbox had the position of the tumbler locating holes reversed left to right.
|
|
Models A, AUD, B and BUD Power cross feed apron . Besides power cross feed this apron provided a finer range of longitudinal feeds than the Model C all-changewheel model - the reduction through the apron's gear train meaning that the feed rate slowed by a factor of 0.3.
|
|
|
|
|
|
|
|
|
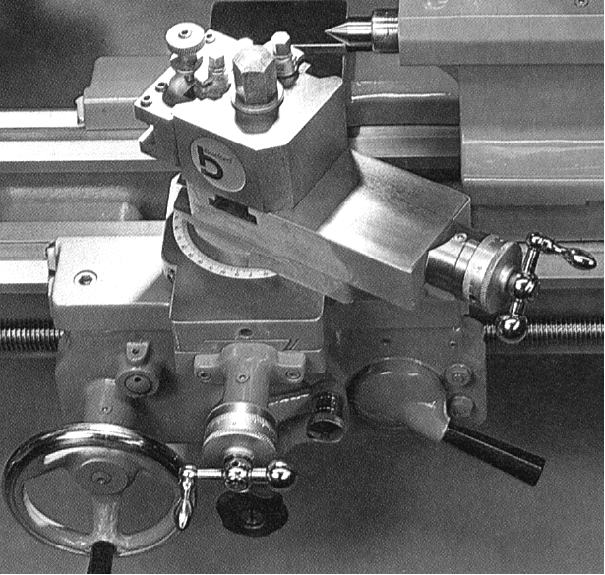 |
|
|
|
|
|
Boxford Mk 2 (5" centre height) compound slide rest assembly. Later Boxfords had the top slide travel extended by 3/8" with the swivelling graduations inscribed on a plastic ring inserted into the cross slide. Although fitted as standard on these lathes the useful Dickson quick-set tool holder could be deleted and a cheaper "American" or clog-heel toolpost chosen instead.
|
|
|
|
|
|
|
|
|
|
|
|
|
|