 |
 |
 |
 |
 |
 |
 |
 |
 |
 |
 |
 |
 |
 |
 |
 |
 |
 |
 |
 |
|
|
|
|
|
|
|
|
|
|
|
|
|
|
|
|
|
|
|
|
|
|
|
|
|
|
|
|
|
|
|
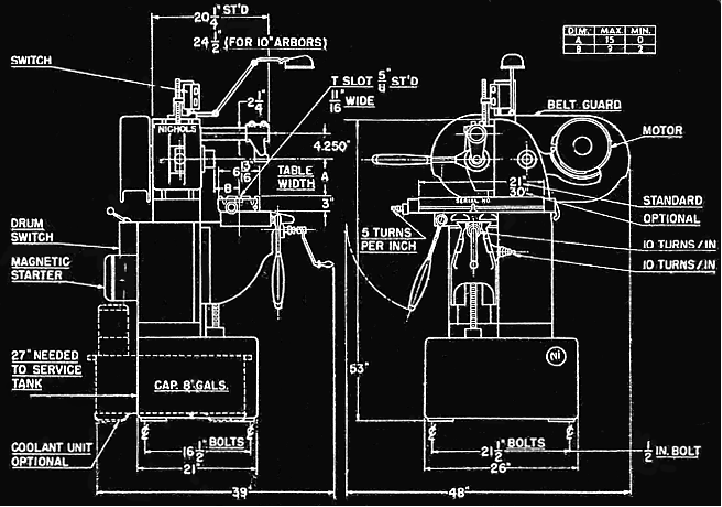 |
|
|
|
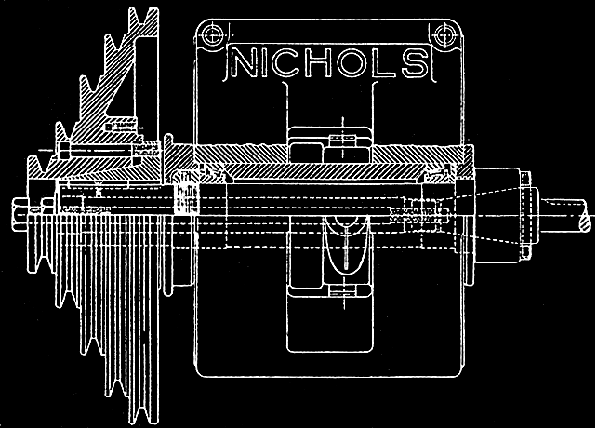 |
|
|
|
|
|
|
Section through the main spindle and overhung cast-iron drive pulley
|
|
|
|
|
|
|
|
|
|
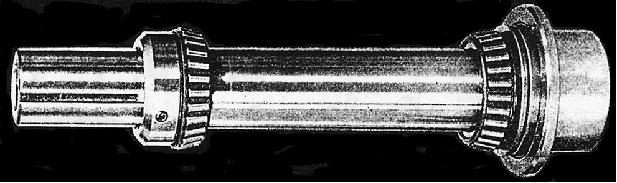 |
|
|
|
|
|
|
Ruggedly built, the main spindle had a 1-inch bore, a hardened and ground nose and a 40 MMS taper. The standard models ran on taper-roller bearings while the high-speed version, which could attain 5000 rpm, used pre-loaded ball races.
|
|
|
|
|
|
|
|
|
|
|
|
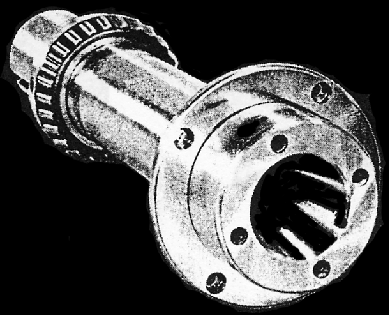 |
|
|
|
|
|
|
The spindle nose was provided with four holes tapped 5/16" x 18 t.p.i. Cap screws were fitted to diametrically opposed holes to act as driving lugs for arbors whilst a notch was also cut in the mouth of the spindle to act as a means of positively driving collets or other fittings. A radial hole was also provided to carry a pin that engaged with the bayonet locks on short, quickly-interchangeable boring bars - these allowing the operator to rough out and finish at one setting.
|
|
|
|
|
|
|
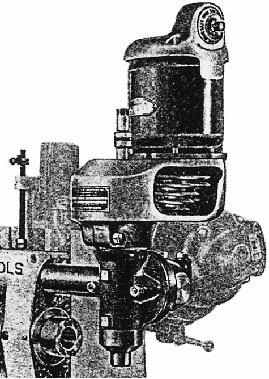 |
|
|
|
|
The more complex of the two optional vertical heads was driven from its own motor and mounted on the end of the round overarm; it was similar in appearance and design to the auxiliary heads made by Halco, Tree and the Kearney & Trecker "Midgetmill" and "Speedmill" units. To see how these units were arranged, and the range of their capabilities, click here.
|
|
|
|
|
|
|
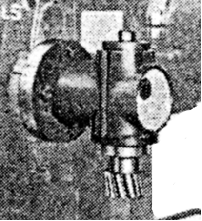 |
|
|
|
|
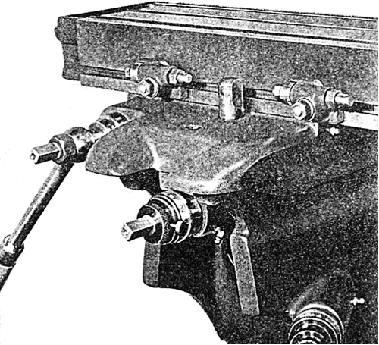 |
|
|
|
|
|
The table was fitted, as standard, with two micrometer stops
|
|
|
|
|
|
|
|
|
|
|
|
|
|