 |
 |
 |
 |
 |
 |
 |
 |
 |
 |
 |
 |
 |
 |
 |
 |
 |
 |
 |
 |
 |
 |
 |
 |
 |
 |
 |
 |
 |
 |
 |
 |
 |
 |
 |
 |
 |
 |
 |
 |
|
|
|
|
|
|
|
|
|
|
|
|
|
|
|
|
|
|
|
|
|
|
|
|
|
|
|
|
|
|
|
|
|
|
|
|
|
|
|
|
|
|
|
|
|
|
|
|
|
|
|
|
|
|
|
|
|
Manufactured by W. H. Nichols & Sons of Waltham, Massachusetts( the spiritual home of many early American precision machine tools) the Nichols "Hand Milling Machine", as it was termed in advertising literature, was a robust, beautifully-built tool intended for "volume production of small parts at low cost." The machine was available in a range of models: Standard, Production, Heavy-duty Production, Tool Room, Duplex, Twin-mill and Semi-automatic. The "Standard" was the basic machine and fitted with a table 20 inches long by 6.75 inches wide with 10 inches of longitudinal travel operated by a lever-feed; the 7 inches of cross feed and 13 inches of vertical travel were generous for a small miller and both driven by screw feeds. The "Production" was identical in construction and specification to the Standard, with the sole exception of a lever-operated traverse feed, while the "Tool Room" (see lower down this page and here) was supplied with a table 10 inches longer than standard - with an extra 9 inches of travel - and equipped with both lever and screw-feed to the longitudinal movement. The "Duplex" was fitted with two independent spindles and available in two models: one had the spindles facing each other on a single axis while on the other they were parallel, one above the other, and able to be adjusted so that they could be brought to within 3.75" - or moved until 14.375" apart. The "Semi-automatic" was a standard machine but equipped with a pneumatic longitudinal feed which could be arranged for simple cycle jobs where the table could be rapidly advanced from its start position, slowed to a rate suitable for the cut to take place and then returned at high speed to repeat the process; the "Heavy-Duty Production" was a late edition to catalog and featured a longer table, strengthened castings and the ability to cut more metal in a given time than the standard production model. The final machine in the range, the "Twin-mill", was a very special, automatically-controlled machine which employed two independent heads mounted one at each side of the table. Although the stand, main body, knee and table were of conventional design, the Nichols employed (for a horizontal miller) an unusual arrangement whereby the entire head assembly, counterbalanced by the weight of the motor and complete with main spindle and overarm, could be moved up and down over a distance of 4.5 inches. The movement, on hand-scraped dovetail slides, was under the sensitive control of a long lever acting through rack-and-pinion gearing while a cleverly-engineered sliding pivot between motor and head allowed the belt to remain at a constant tension no matter what the position of the head. The drive system was simple, but superbly engineered, with the input pulley overhung on the end of the main spindle and driven directly from an electric motor fitted with a speed-reducing gearbox. The standard drive used a pair of one-piece, 5-step, cast-iron pulleys which, because alternative sizes were available to increase the top speed to as much as 5000 rpm (and the bottom speed to as low as 50 rpm,) were held to their shafts by a split, tapered bush retained by three set screws this making removal and replacement a relatively painless operation. The substantial iron pulleys were (claimed the makers), heavy enough to produce something of a flywheel effect and so smooth out the drive. Continued below:
|
|
|
|
|
|
|
|
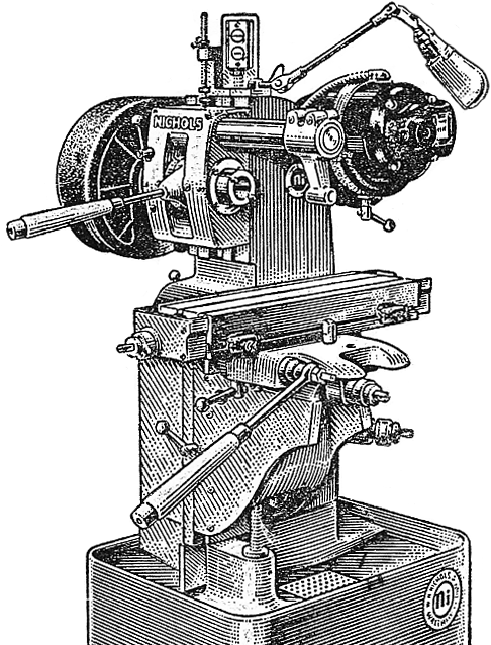 |
|
|
|
|
|
|
The Nichols "Standard" model with screw elevation of the knee and cross travel but lever feed to the table's longitudinal travel.
|
|
|
|
|
|
|
|
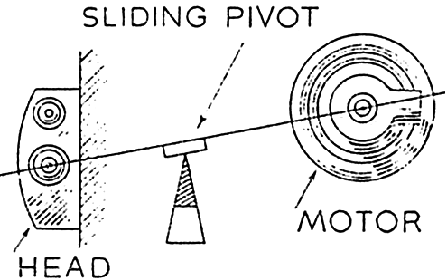 |
|
|
|
|
|
|
Belt tension was kept constant by the use of a cleverly-designed sliding pivot between the motor and main spindle.
|
|
|
|
|
|
|
|
|
Continued: Ruggedly constructed and accurately built the main spindle had a hardened nose (ground inside and out) a 1-inch bore and a 40 MMS taper - the assembly was guaranteed to run within 0.00015" of true. Speeds varied widely with age and model; early Standard versions, which all ran on taper-roller bearings, appear to have had four speeds driven from a 1 hp 3-phase motor (fitted with a gearbox on its output shaft to give a 300 rpm output,) of 100, 200, 600 and 1200 rpm. Later models were offered with five speeds and a choice either Timken taper-roller or ball bearings - the former with speeds of 100, 175, 365, 700 and 1350 rpm from a 1 hp motor, or 200, 350, 730, 1400 and 2700 rpm from a 1.5 hp motor with its gearbox modified to produce an output speed of 780 rpm. The high-speed ball-bearing model had the 1.5 hp motor as standard - but with a 900 rpm output - and spindle speeds of 250, 440, 910, 1750 and 3380 rpm; there was also the option of lifting the maximum speed to either 4000 or 5000 rpm by using special "pick-off" pulleys and fitting a stronger belt and pulley guard. It was also possible to change the speed range of an individual machine by fitting a different ratio gearbox to the motor - they were all interchangeable - but the makers cautioned against allowing the standard 5-step V pulley be run in excess of 1350 rpm and instead recommended the use of a safer two-part pulley. The absolute safe maximum speed for the taper-roller bearing models was set at 2750 rpm. At the opposite end of the scale, special pulley sets were available to bring the bottom speed down to 50 rpm - a modification which again required the use of a different belt and pulley guard. Two types of vertical head were available: the simpler of the two was mounted on the spindle head by a T-slotted ring adaptor and driven by a splined shaft inserted into the horizontal spindle taper. The unit was geared (up) to run at a ratio of 5 : 4 in comparison with the horizontal speeds, but was limited to a maximum of 2000 rpm; this meant taking care not to let the horizontal spindle speed exceed 1500 rpm - especially if the miller had been modified with a faster-output motor gearbox or high-speed pulley set when the marked speeds would not have been those achieved in practice. Driven from its own motor, and mounted on the end of the round overarm, the better of the two heads was similar in appearance and design to the those auxiliary types made by Halco, Tree and the Kearney & Trecker "Midgetmill" and "Speedmill" types. To see how these various attachments were arranged, and the range of their capabilities, click here. Supplied with each new Nichols miller was an electric motor and push-button starter, a machine light, an 8 gallon coolant tank (the pump and motor were extra), depth stop for the head, table stops, a hardened 1-inch diameter arbor with draw-in bolt, a belt guard and the necessary drive belts and wrenches. A typical Nichols weighted around 1175 lbs..
|
|
|
|
|
|
|
|
|
|
|
|
|
|
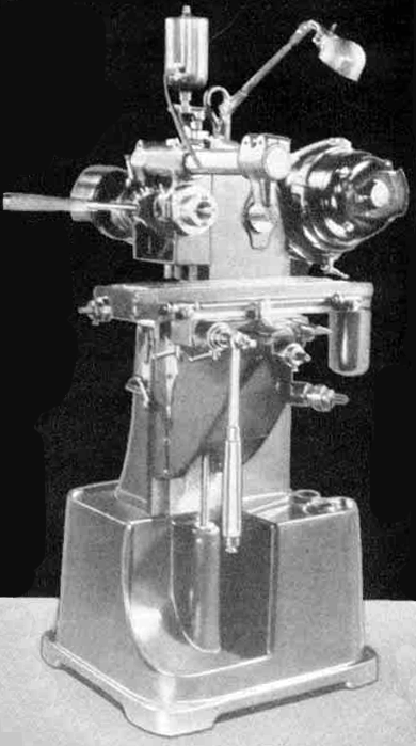 |
|
|
|
|
|
|
"Standard" version of the Nichols hand Milling Machine
|
|
|
|
|
|
|
|
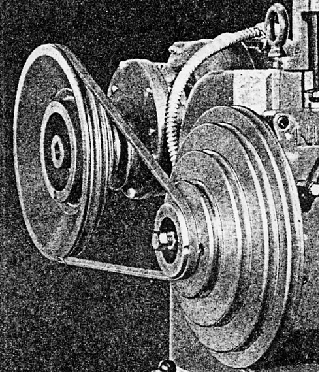 |
|
|
|
|
|
|
Overhung on the main spindle, the input drive pulley was driven directly from an electric motor fitted with a speed-reducing gearbox. The standard drive used a pair of one-piece, 5-step, cast-iron pulleys which, because alternative sizes were available to increase the top speed to as much as 5000 rpm (and the bottom speed to as low as 50 rpm,) were held to their shafts by a split, tapered bush retained by three set screws this making removal and replacement a relatively painless operation.
|
|
|
|
|
|
|
|
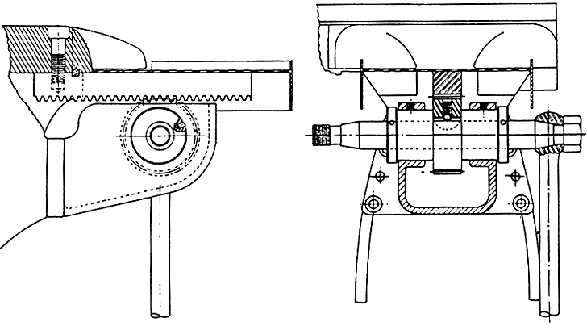 |
|
|
|
|
|
The simple but well-supported rack feed as fitted to the Standard, Production and Duplex models
|
|
|
|
|
|
|
|
|
|
|
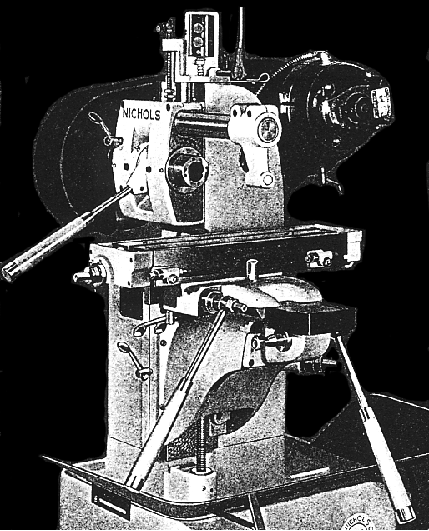 |
|
|
|
|
|
|
|
|
|
Production Model with all the table movements controlled by levers.
|
|
|
|
|
|
|
|
|
|
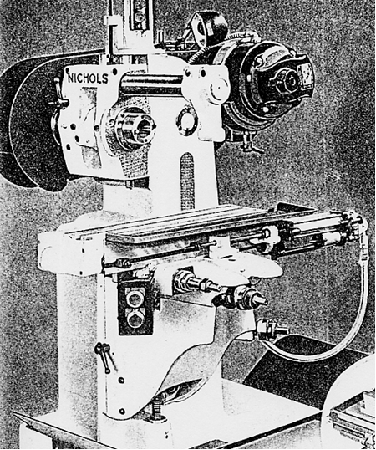 |
|
|
|
|
|
|
Semi-automatic model with pneumatic table feed.
|
|
|
|
|
|
|
|
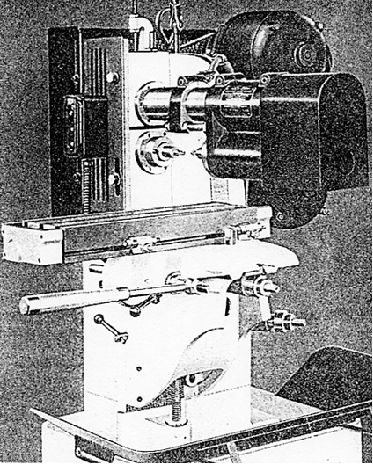 |
|
|
|
|
|
|
Duplex miller with a second electrically- driven opposed spindle.
|
|
|
|
|
|
|
|
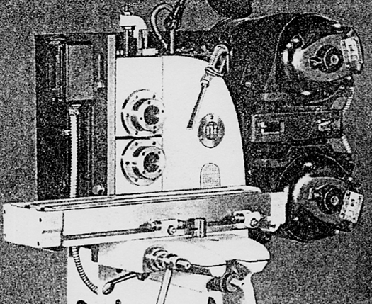 |
|
|
|
|
|
|
Duplex miller with a second spindle, parallel to the first and adjustable in position relative to it.
|
|
|
|
|
|
|
|
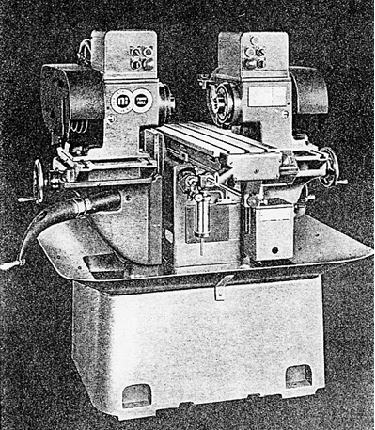 |
|
|
|
|
|
|
Special model with twin heads, each independently controlled.
|
|
|
|
|
|
|
|
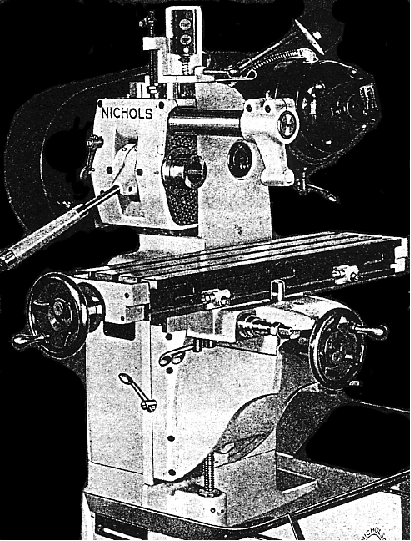 |
|
|
|
|
|
|
Toolroom Model with screw feed to every movement of the longer-than-standard table.
|
|
|
|
|
|
|
|
|
|
|
|
|
|
|
|