 |
 |
 |
 |
 |
 |
 |
 |
 |
 |
 |
 |
 |
 |
 |
 |
 |
 |
 |
 |
 |
 |
 |
 |
 |
 |
 |
 |
 |
 |
 |
 |
 |
 |
 |
 |
 |
 |
 |
 |
 |
 |
 |
 |
 |
 |
 |
 |
 |
 |
 |
 |
 |
 |
 |
 |
 |
 |
 |
 |
 |
 |
 |
 |
 |
 |
 |
 |
 |
 |
 |
 |
 |
 |
 |
 |
 |
 |
 |
 |
 |
 |
 |
 |
|
|
|
|
|
|
|
|
|
|
|
|
|
|
|
|
|
|
|
|
|
|
|
|
|
|
|
|
|
|
|
|
|
|
|
|
|
|
|
|
|
|
|
|
|
|
|
|
|
|
|
|
|
|
|
|
|
|
|
|
|
|
|
|
|
|
|
|
|
|
|
|
|
|
|
|
|
|
|
|
|
|
|
|
|
|
|
E-MAIL Tony@lathes.co.uk Home Machine Tool Archive Machine-tools for Sale & Wanted Machine Tool Manuals Machine Tool Catalogues Belts Books Accessories
Emco Maximat Standard & Compact Mk. 2 & Mk. 3 Lathe Models M-3100 MQ-3000 M-3000 & 4000 & 4100
An Instruction Manual and a Parts Manual are available for these lathes A Operation and Parts Manual is available for the Compact 5
Emco Home Page Emco Unimat & DB200 & SL1000 lathes Emco Unimat 1
Emco Unimat 3 and 4 Emco Compact 5 Emco Compact 5CNC and Compact 5PC Unimat PC and "Basic" Emcomat & Maximat 7 Emco Compact 8
Emcomat 8.4 & 8.6 Emco Maximat V8 Emco Compact 10 Emco Maximat V10/V10P Emco Super 11 Emco Maximat V13 Very Early Emco TD55 lathe
1950s Mk. 1 "Maximat Standard" and "Compact" Universal Machine Tool
1960s Mk. 2 Maximat "Standard" Model 3000 Universal Machine Tool
Emco Milling Machines Emco V10 Switch Replacement
The text below is repeated from the early Maximat Page:
By 1962 (having run through 4 versions of the original Maximat) the angular-styled Mk. 3 "Series 3000" was in production and being sold in three versions. The best was the MQ-3100, with a full screwcutting and feeds gearbox and equipped with two headstock-motor units - so it was always ready for vertical milling and drilling. A cheaper version, the cheaper M-3100, was mechanically identical - and with two headstocks - but with changewheels for screwcutting. The entry-level model, the M-3000, came with changewheels and only one headstock that had to be shared between lathe and milling column. Unchanged at 9/16" bore and with a No. 2 Morse taper centre the spindle nose was hardened and carried either a 1.125" or M27 spindle nose. However, on the better-specified lathes supplied with a non-sliding quill assembly in the lathe headstock (i.e. the "Maximat Compact" with a powered milling head in place) there was more room in the casting and they were equipped with a larger assembly carrying either a 1.5" x 8 t.p.i or M39 x 4 metric nose, a No. 3 Morse taper and a 20 mm (3/4") bore with an adaptor fitting to accept ordinary draw-in L20 collets. In all cases the spindle now ran in a Class 7, double-row roller bearing at the front and two Class 7 angular-contact (ball) bearings at the rear while the overhung pulley that drove the spindle ran on two angular-contact ball bearings. However, variations on this theme have been discovered, and it is entirely possible that not only were lathes originally supplied with a vertical-milling head (MQ-3100 and M3100) fitted with a "lathe" headstock that lacked the sliding quill mechanism, but the headstock supplied for milling was altered to accept collets similar to the ER type, which had a much better grip on milling cutters. With the new headstock, spindle speeds dropped in number from seven to six and, with a 1725 rpm, 0.5 hp 1-phase (or 3-phase) motor, these were: 125, 210, 370, 620, 1100 and 1900 rpm. Alternatively, a slower single or three-phase 0.5 hp, 1120 r.p.m. motor could be ordered to give: 80, 140, 250, 420, 720 and 1250 r.p.m. Again, variations from the catalogue specification have been found in production machines with some examples using a 1/2 h.p. split-phase, single-phase motor (fitted with a 560 mf start capacitor and a 40 mf run capacitor) on both the lathe and milling head. Of the two speed ranges, the slower 80 to 1250 rpm would have been the better for both screwcutting and large-diameter turning - if still nearly 100% too fast on the bottom speed for comfort and safety. However, in later versions of the Maximat (the much better known V10 and V10P Models) things were considerably improved with the employment of an all-geared headstock driven as standard by a 2-speed motor - in addition to being fitted with the 4 or 6-speed all-geared milling head from, respectively, the U2 and FB2 vertical milling machines. Fitted with 2 T-slots arranged to run at a right-angle to the bed ways the robust 10" x 4.75" cross slide was adapted from that on the Mk. 2 and retained the feature whereby the top slide could be slid backwards and forwards in the slots and bolted down in any position - this part of the design continuing unaltered on the V10 series in later years. Able to generate 24 threads and feeds, the Norton-type screwcutting gearbox featured the standard controls of a sliding tumbler lever on the front, a three-position lever on the top and a push/pull knob sticking out of the end cover to select either screwcutting or fine feeds for sliding and surfacing. As an indication of the quality of the lathe, the screwcutting gearbox was fitted throughout with ball bearings and the leadscrew (0.75" x 8 t.p.i Acme form) was both hardened and ground and could be adjusted so that it was tensioned between its angular-contact ball bearing fitted support brackets. Although models equipped with screwcutting by changewheels had an entirely adequate range of fine feeds, Emco persisted in fitted a modified version of the original belt-drive 2-speed feeds' gearbox. Based on designs as commonly employed from the late 1800s until the 1920s, the new box held an expensive ratio-lowering worm-and-wheel assembly with a pair of bevel gears to turn the drive through 90-degrees. Just before sales of the entirely new V10 range began a Mk. 4 version was introduced as the two-model 4000-Series - again, a machine rare in the UK but one that met with some success in the USA when sold through the Edelstall Corporation. Modifications over the Series 3000 appear to have been few (though the headstock was modified to take a No. 3 Morse taper) with the Model 4100 having a screwcutting gearbox and the 4000 screwcutting with changewheels - both models being supplied with two headstocks as standard. All-metric versions - gearbox, leadscrew and compound slide rest screws and micrometer collars - were given a suffix M, as in 4100-M. Additional features offered as extras on these later-model machines included a choice of a single-speed 1120 or 1725 r.p.m. motor (U.S.A. specification) - that gave top speeds of 2250 and 3400 r.p.m respectively - and more sophisticated SCR electronic variable-speed control of the spindle from 0 to 35000 rpm and with instant reverse. A useful variable-speed electric motor and gearbox unit was also available to drive the carriage and so allow the optimum sliding speed to be obtained for virtually any job. One problem that users of the Maximat Standard and Compact lathes report, is the propensity for swarf to find its way into the screwcutting gearbox (hence the plastic shield on the lathe shown below), through the gap between the end face of the headstock and the tumble-reverse lever and into the motor. While other lathes also suffer from these problems, the Maximat shown on this page seems particularly prone to them. However, shielding these parts is easy enough and well worth considering. Should any reader be able to provide high-resolution pictures of a clean Emco Maximat, the writer would be pleased to hear from you..
|
|
|
|
|
|
|
|
|
|
|
|
|
|
|
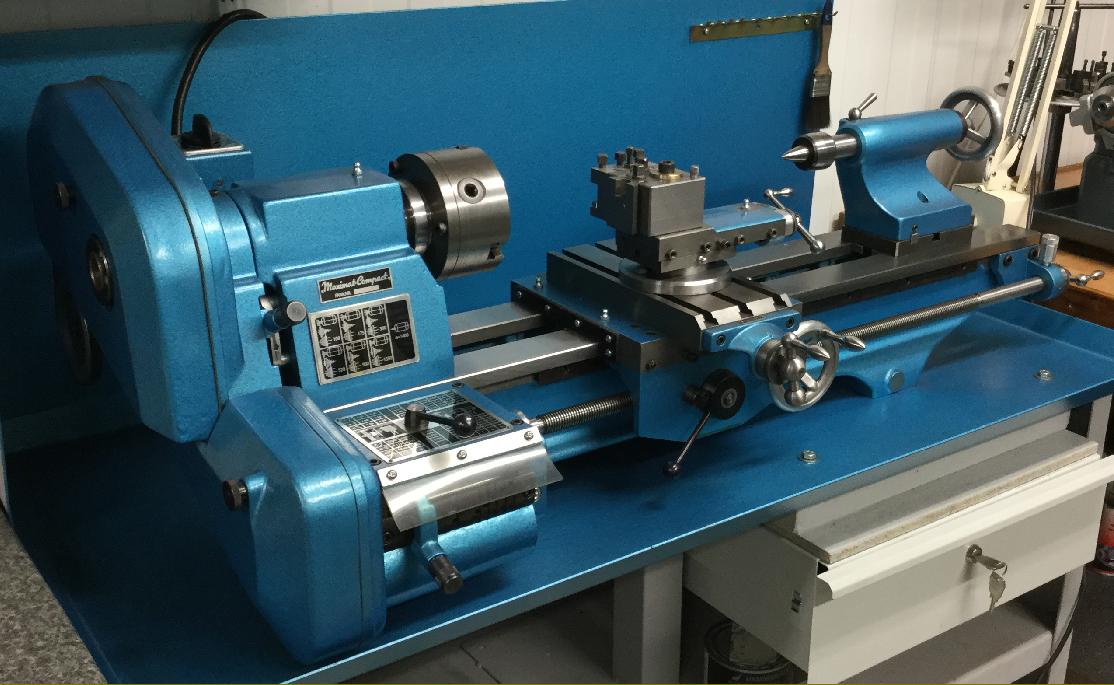 |
|
|
|
|
|
|
|
|
|
|
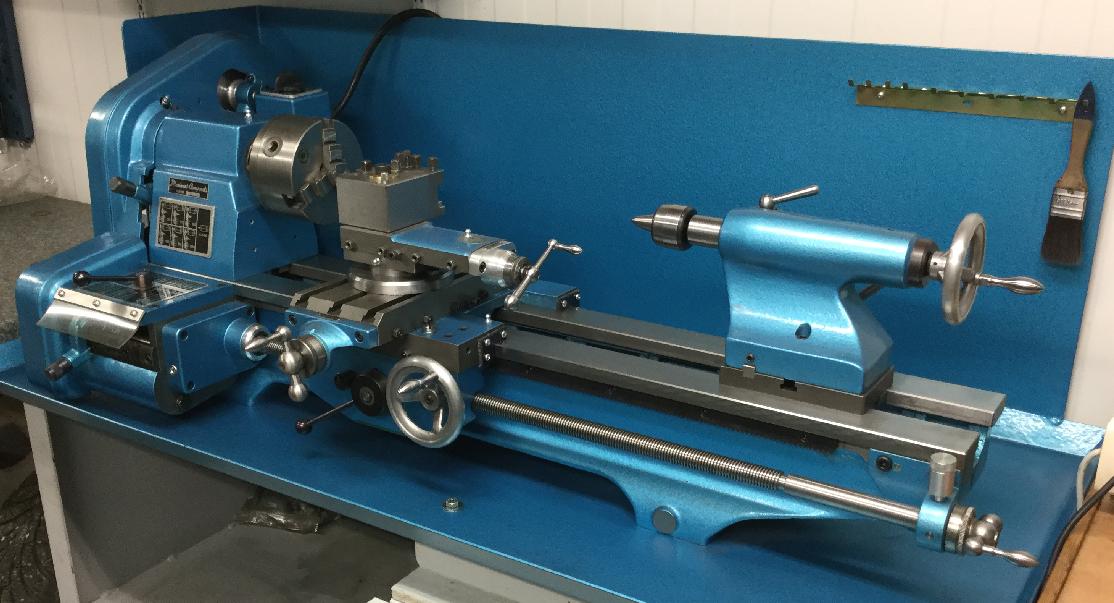 |
|
|
|
|
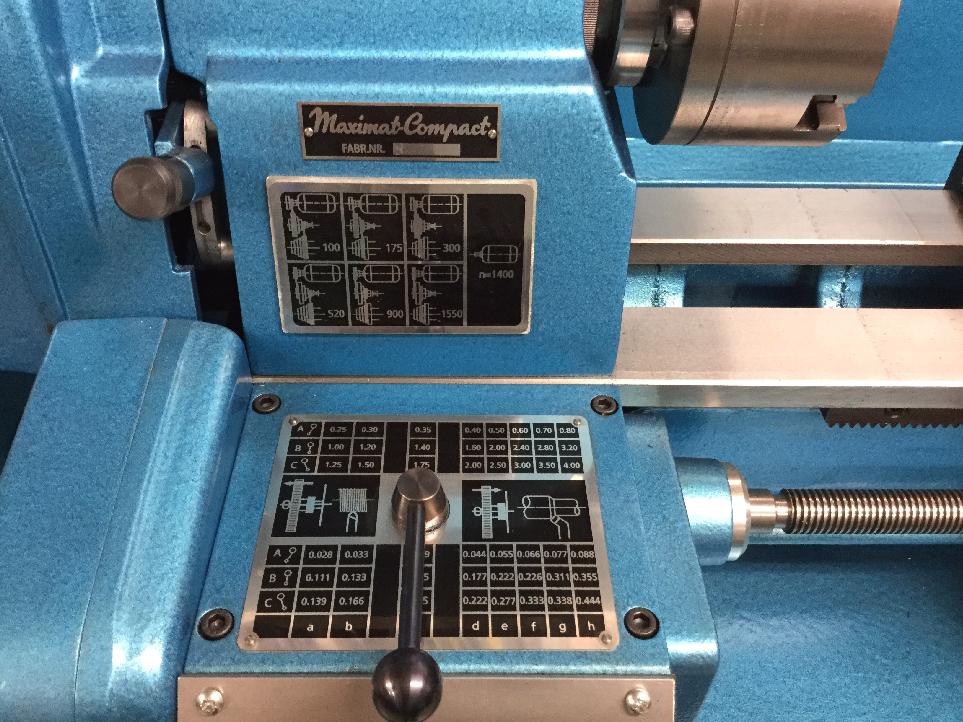 |
|
|
|
|
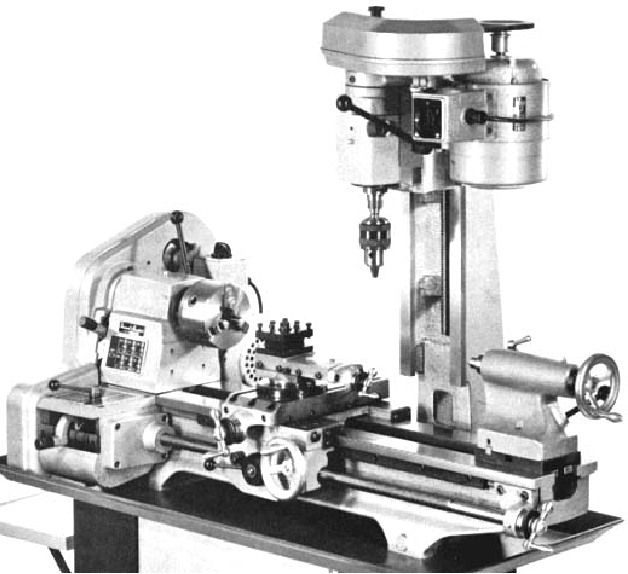 |
|
|
|
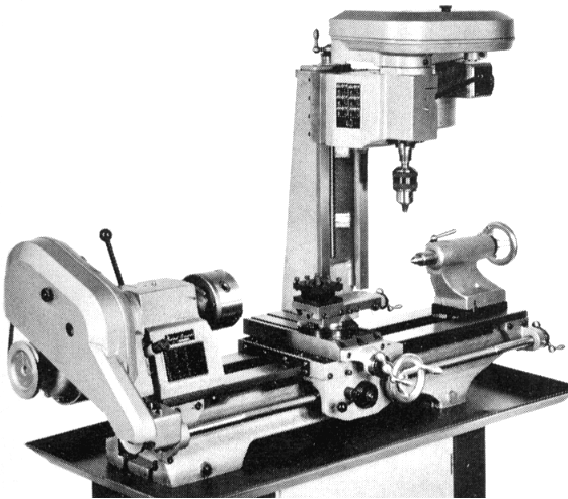 |
|
|
|
|
|
|
M-3100 - still with two motor units but with changewheels instead of a screwcutting gearbox.
|
|
|
|
|
|
|
|
|
|
|
|
|
|
Maximat MQ-3100 - the best specified of the range fitted with a screwcutting gearbox and two headstock motor units so that the machine was always ready for vertical milling and drilling.
|
|
|
|
|
|
|
|
|
|
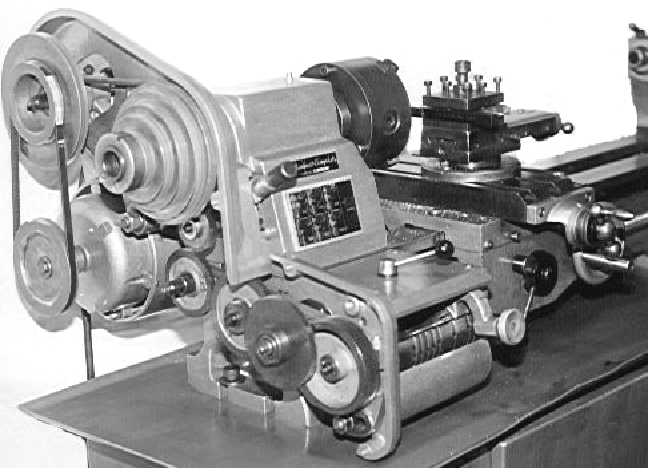 |
|
|
|
|
|
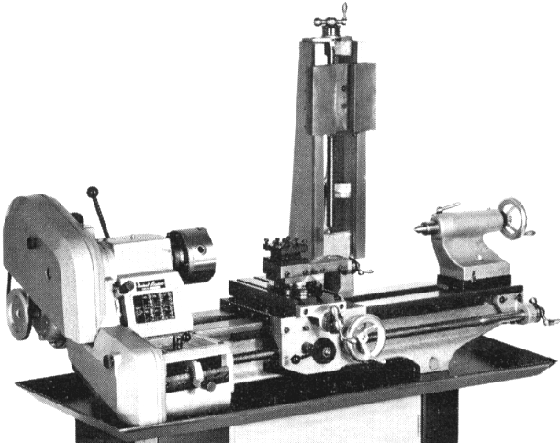 |
|
|
|
|
|
|
|
|
|
|
A clear picture showing the disposition of the belt-drive system - and gear drive to the screwcutting gearbox.
|
|
|
|
|
|
|
|
|
|
|
|
MQ-3000 - with a screwcutting gearbox but only one motor headstock unit.
|
|
|
|
|
|
|
|
|
|
|
|
|
|
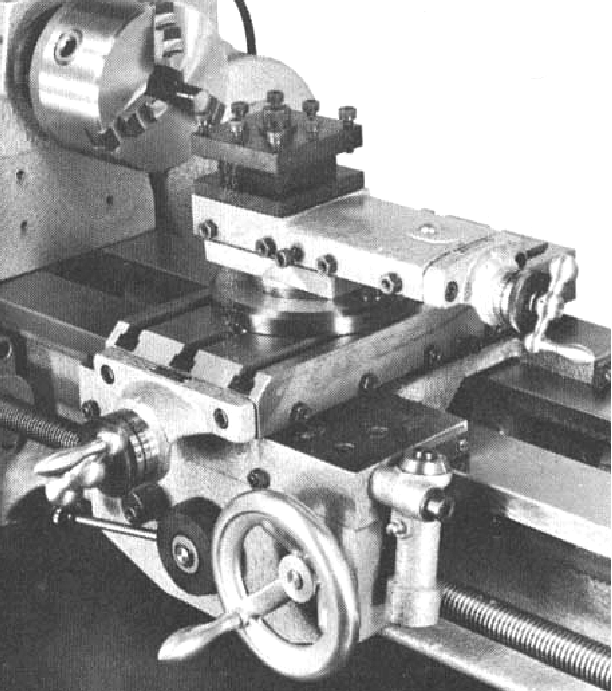 |
|
|
|
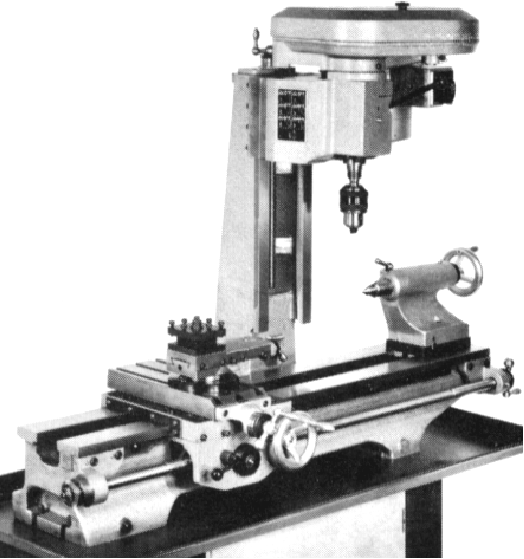 |
|
|
|
|
|
|
M-3000 - the basic unit with one headstock unit to share between the lathe and milling column and changewheels for screwcutting.
|
|
|
|
|
|
|
|
|
|
|
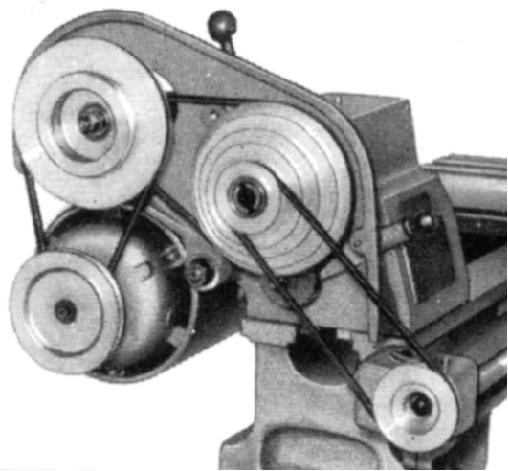 |
|
|
|
|
|
|
|
Used on the Mk. 1, Mk. 2 and Mk. 3 Maximat lathes the 10" x 4.75" cross slide had, for the first time on an Emco lathe, T slots arranged to run at right-angles to the bed ways instead of in the same direction. The top-slide mounting was also completely redesigned in a manner which enabled it to be slid backwards and forwards in the two outer slots and bolted down in any position.
|
|
|
|
|
|
|
|
|
|
|
|
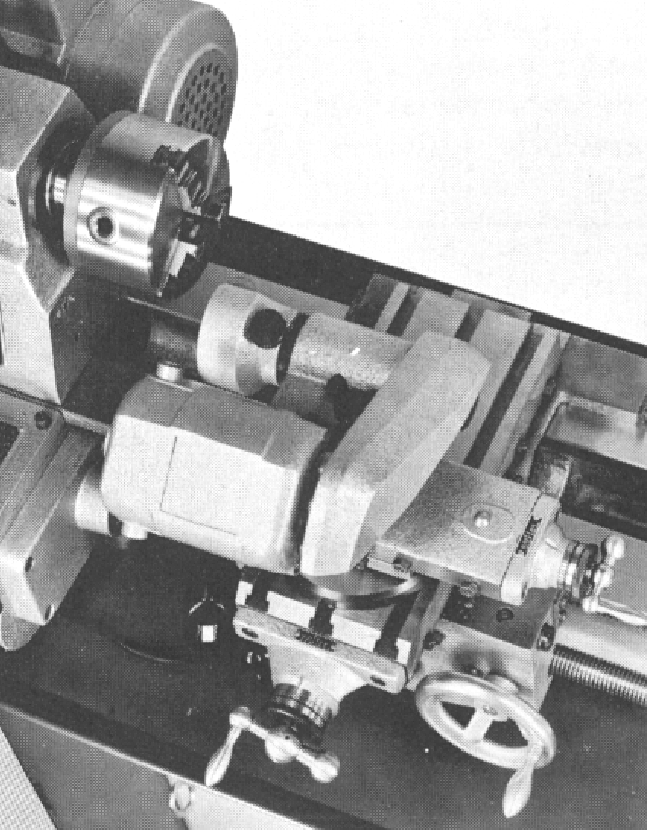 |
|
|
|
|
|
|
|
Based on designs as commonly employed from the late 1800s until the 1920s the belt-drive incorporated a box on the end of the leadscrew that held a ratio-lowering worm-and-wheel assembly with a pair of bevel gears to turn the drive taken through 90-degrees.
|
|
|
|
|
|
|
|
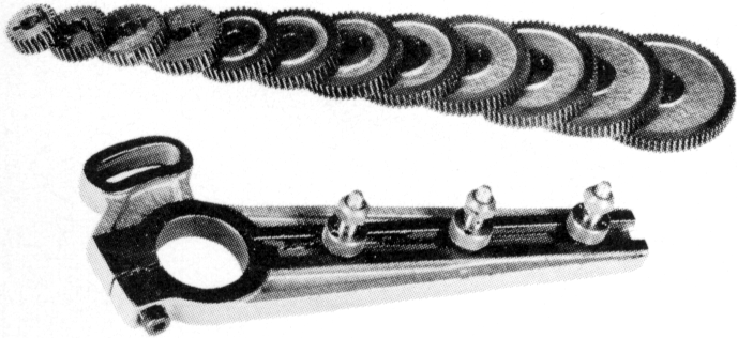 |
|
|
|
|
|
|
Accessory banjo (quadrant arm) and screwcutting changewheel set (Part MQ-3120) which allowed the screwcutting gearbox to generate almost any pitch of thread.
|
|
|
|
|
|
|
|
|
|
|
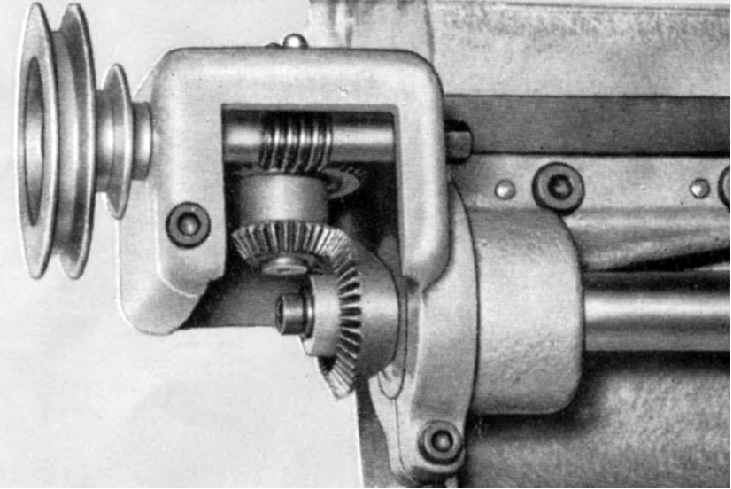 |
|
|
|
|
|
A toolpost grinder was, naturally, on the accessories list. Three speeds were available: 2500, 5000 and 10,000 rpm.
|
|
|
|
|
|
|
|
|
|
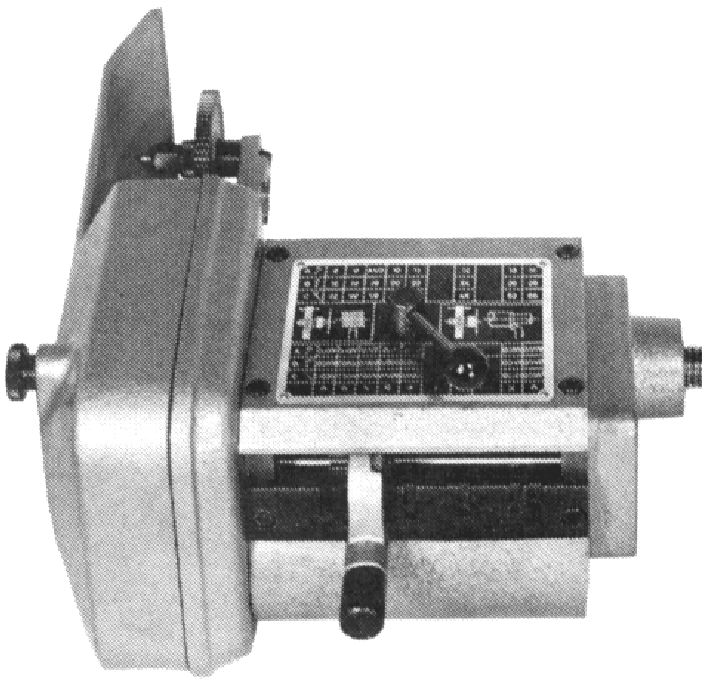 |
|
|
|
|
|
|
|
|
Norton-type screwcutting gearbox. Sliding lever on the front, three-position lever on the top and a push/pull knob sticking out of the end cover to select the 24 screwcutting or sliding-and-surfacing fine feeds. As an indication of the quality of the lathe, the screwcutting gearbox was fitted throughout with ball bearings and the leadscrew (0.75" x 8 tpi Acme form) was both hardened and ground and ran in angular-contact ball bearings.
|
|
|
|
|
|
|
|
|
|
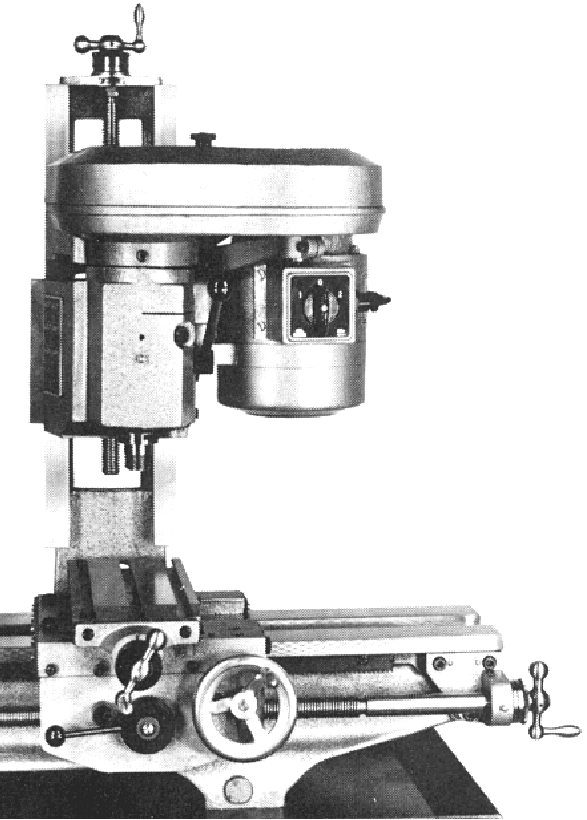 |
|
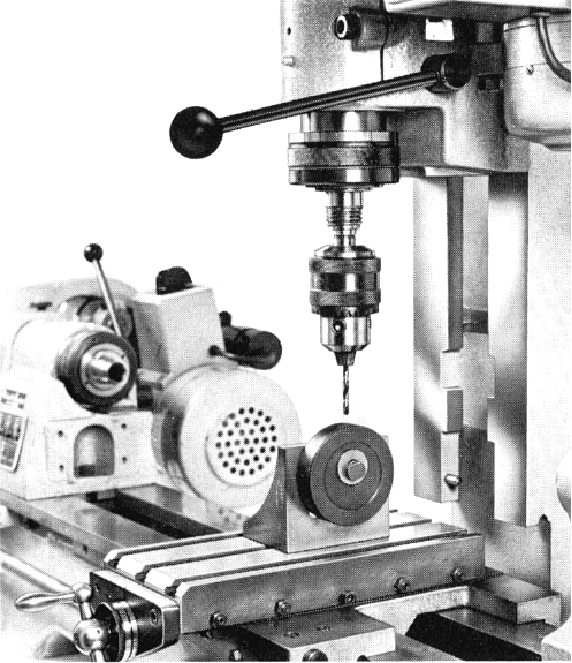 |
|
|
|
|
|
|
The quick-feed drill quill in use - typical of the type of job which can, on occasion, make a well-designed combination machine so useful to have in the workshop. Notice that the vertical column is really just a modified section of the standard lathe bed.
|
|
|
|
|
|
|
|
|
|
|
|
|
|
With the vertical milling and drilling head raised, and the top slide replaced, the machine could be used as a centre lathe without further alteration. Note the switch, built onto the body of the electric motor. The quill travel was 1.5625 inches and the maximum distance between the spindle nose and cross slide 12 inches - the assembly could drill a hole in the middle of a circle 11.8125 inches in diameter.
|
|
|
|
|
|
|
|
|
|
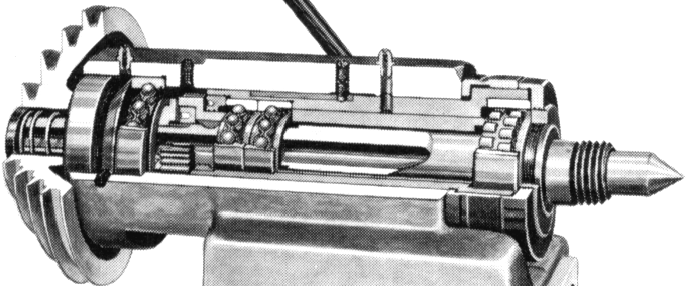 |
|
|
|
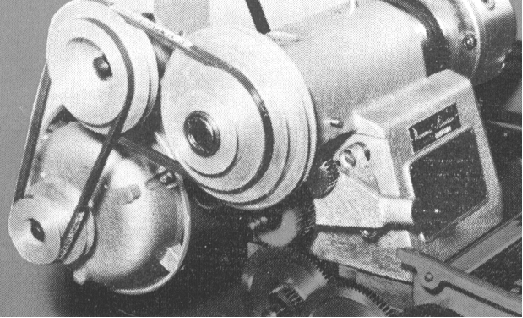 |
|
|
|
|
|
|
|
A section through the headstock showing the sliding spindle, outboard drive pulley and bearing layout.
|
|
|
|
|
|
|
|
|
|
|
|
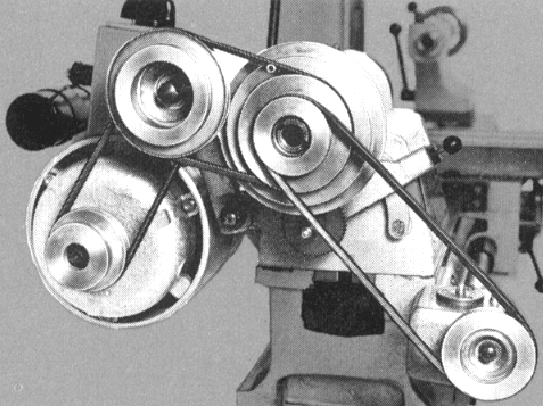 |
|
|
|
|
|
|
|
Lathe set with changewheels for screwcutting and showing the outboard headstock drive and jockey pulleys.
|
|
|
|
|
|
|
|
|
|
|
 |
|
|
|
|
|
|
|
On the non-gearbox model, with the changewheels disengaged, the fine feed was arranged through a belt drive to a two-speed gearbox on the end of the leadscrew.
|
|
|
|
|
|
|
|
|
|
|
|
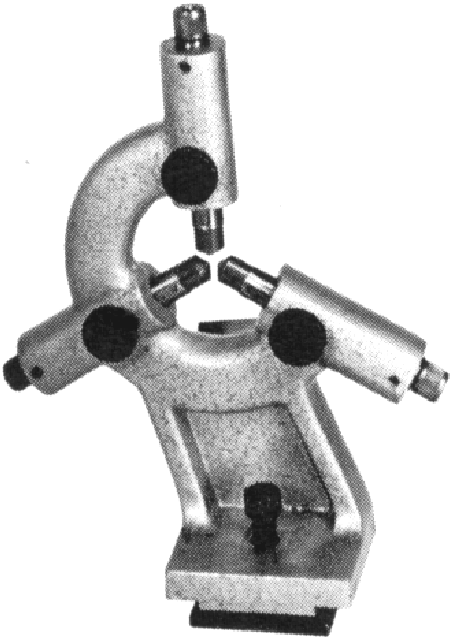 |
|
|
|
|
|
|
|
Later versions (this is an M300 Series) had an altered drive line ...
|
|
|
|
|
|
|
|
|
|
|
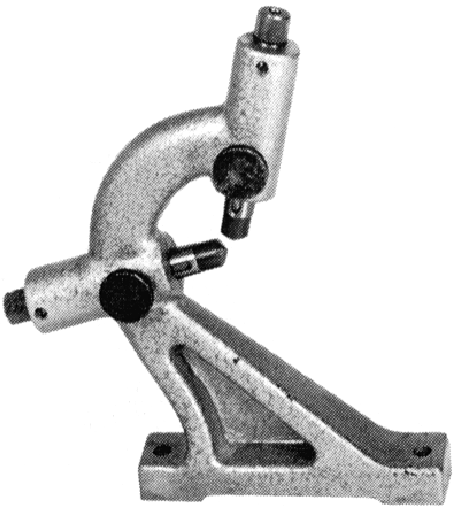 |
|
|
|
|
|
|
|
|
|
|
|
|
|
A distinctive design of fixed steady ...
|
|
|
|
|
|
|
|
|
|
|
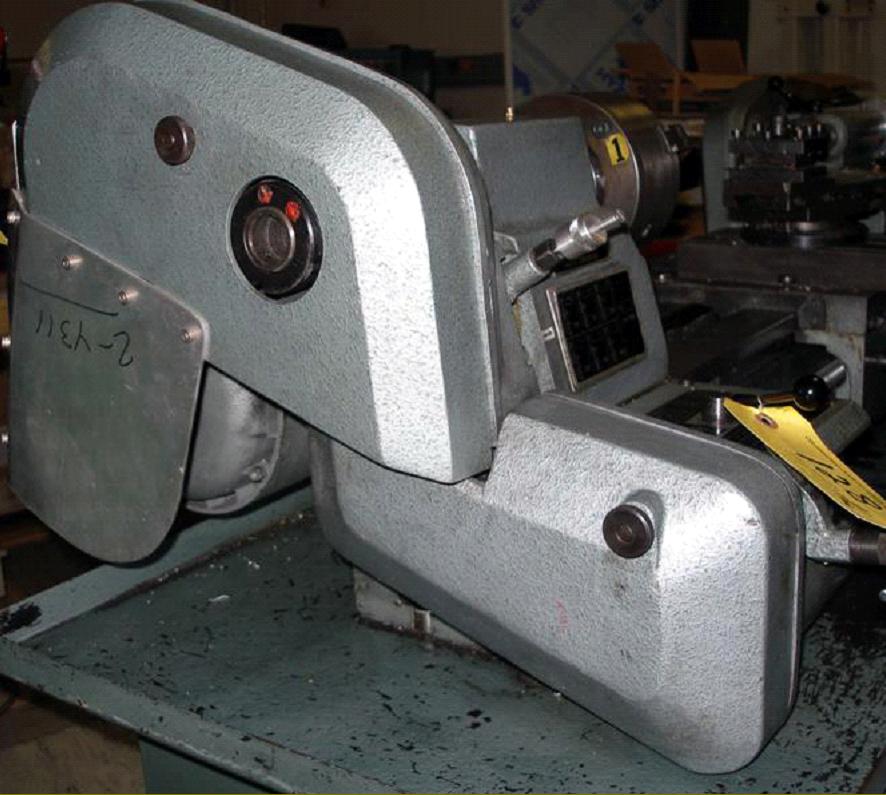 |
|
|
|
|
|
|
|
|
|
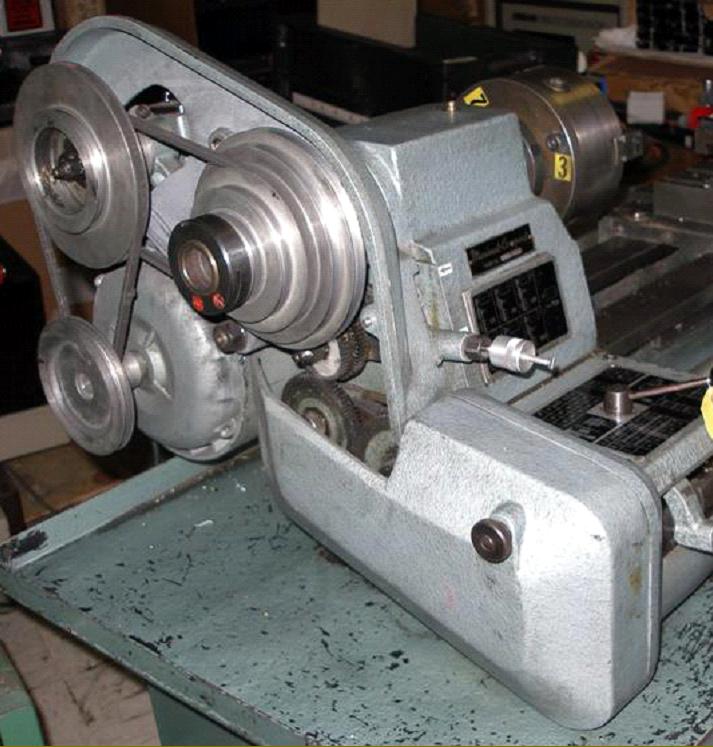 |
|
|
|
|
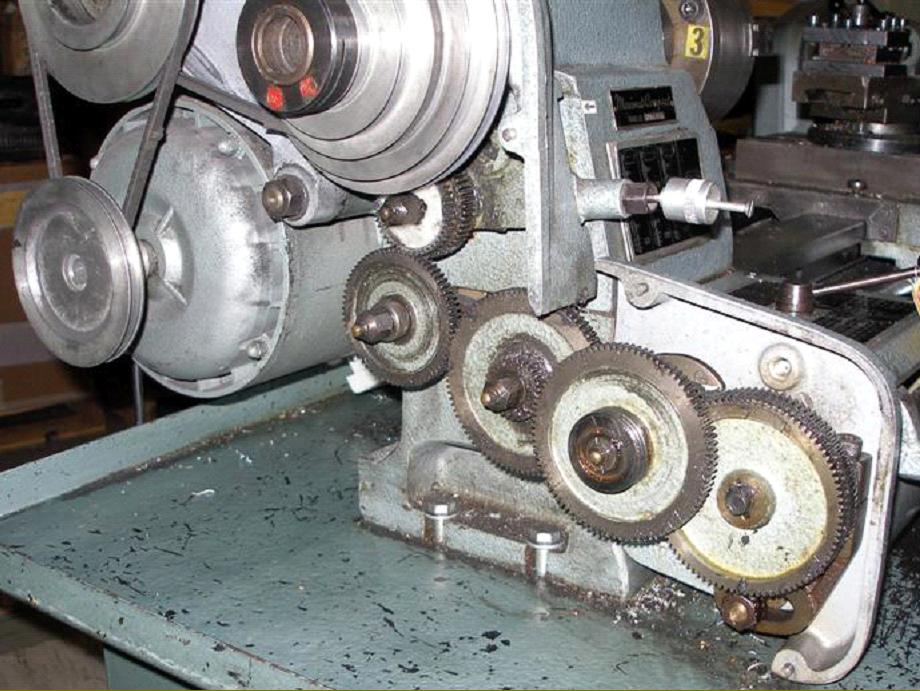 |
|
|
|
|
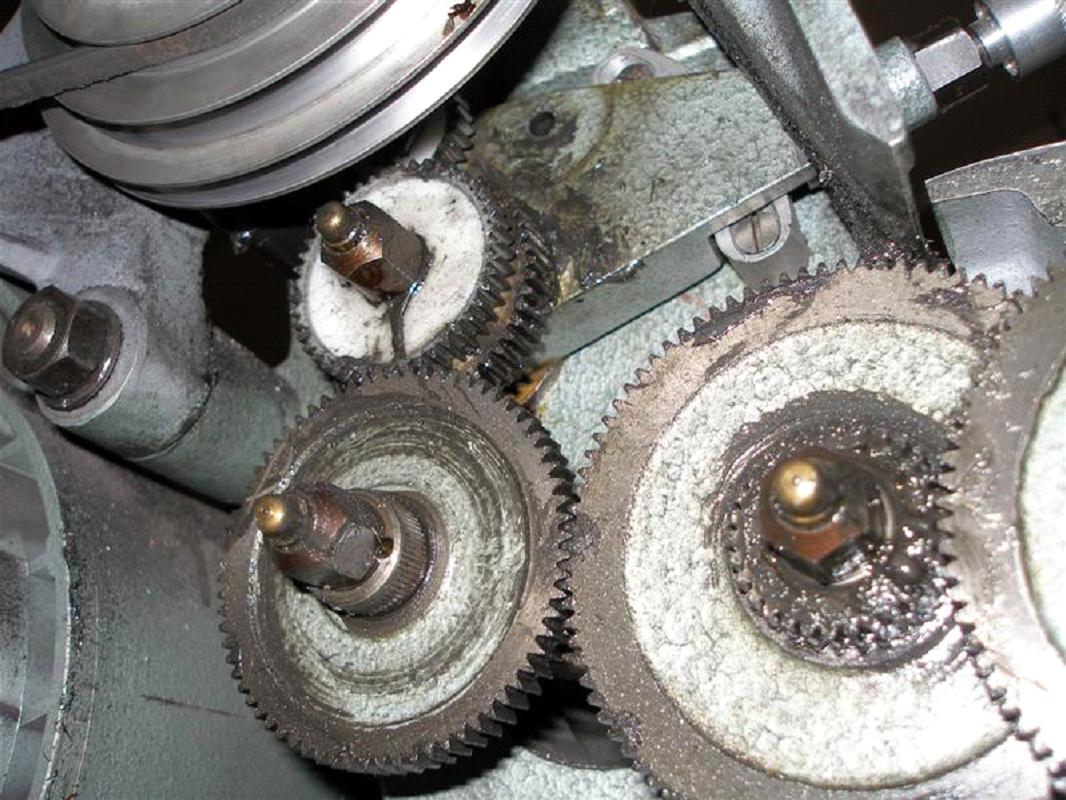 |
|
|
|
|
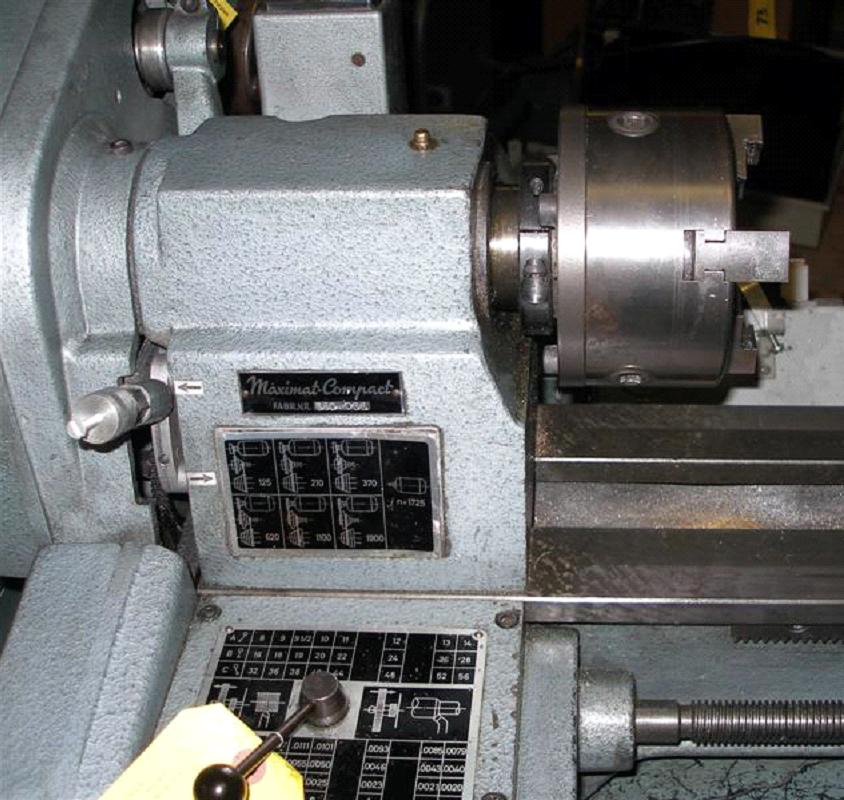 |
|
|
|
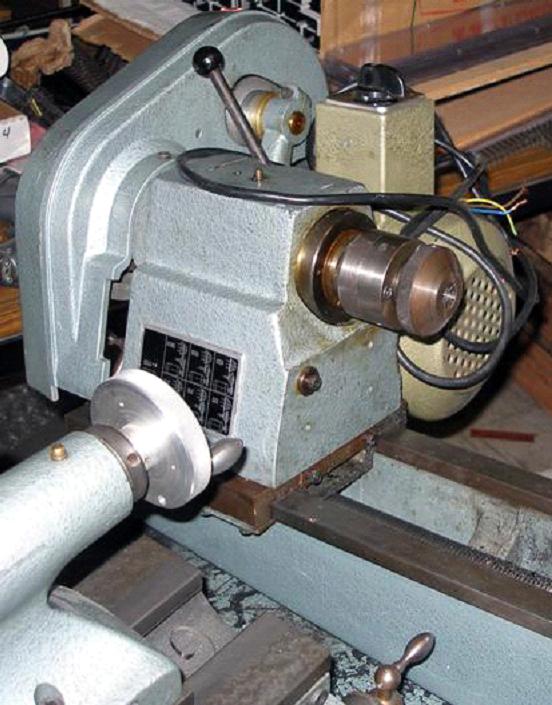 |
|
|
|
|
|
|
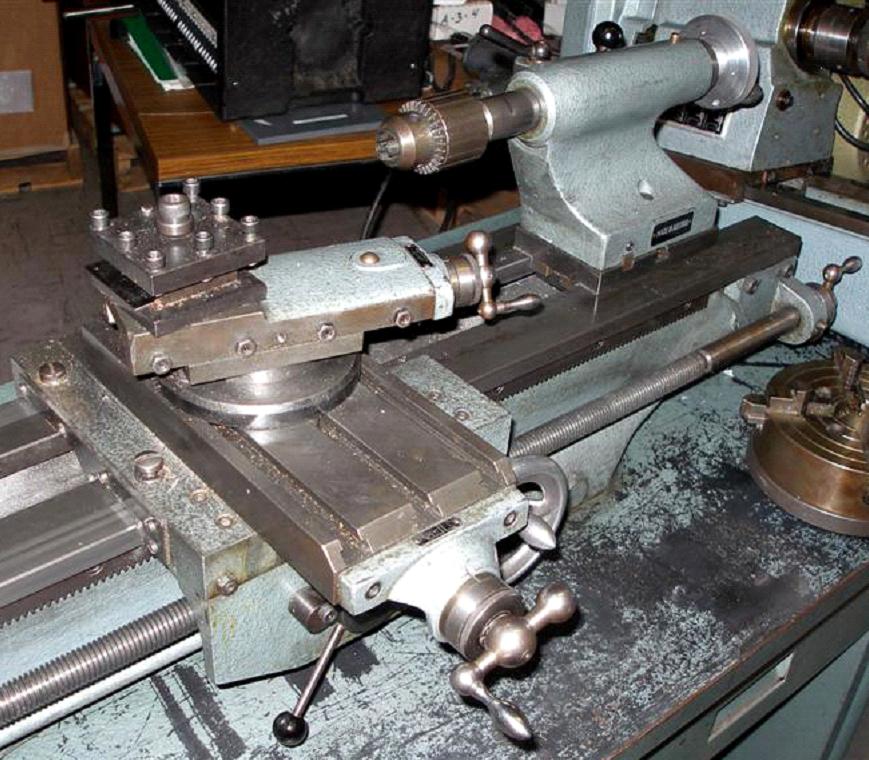 |
|
|
|
|
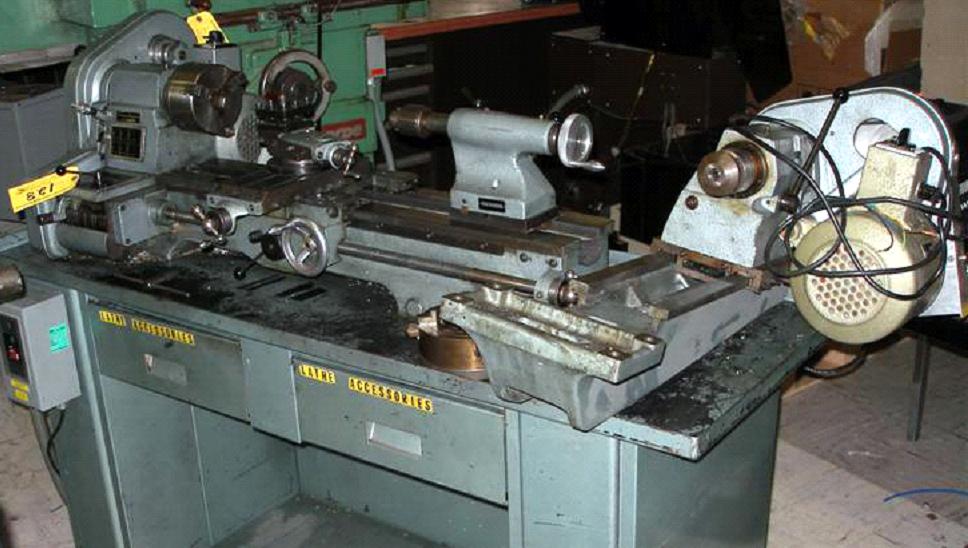 |
|
|
|
|
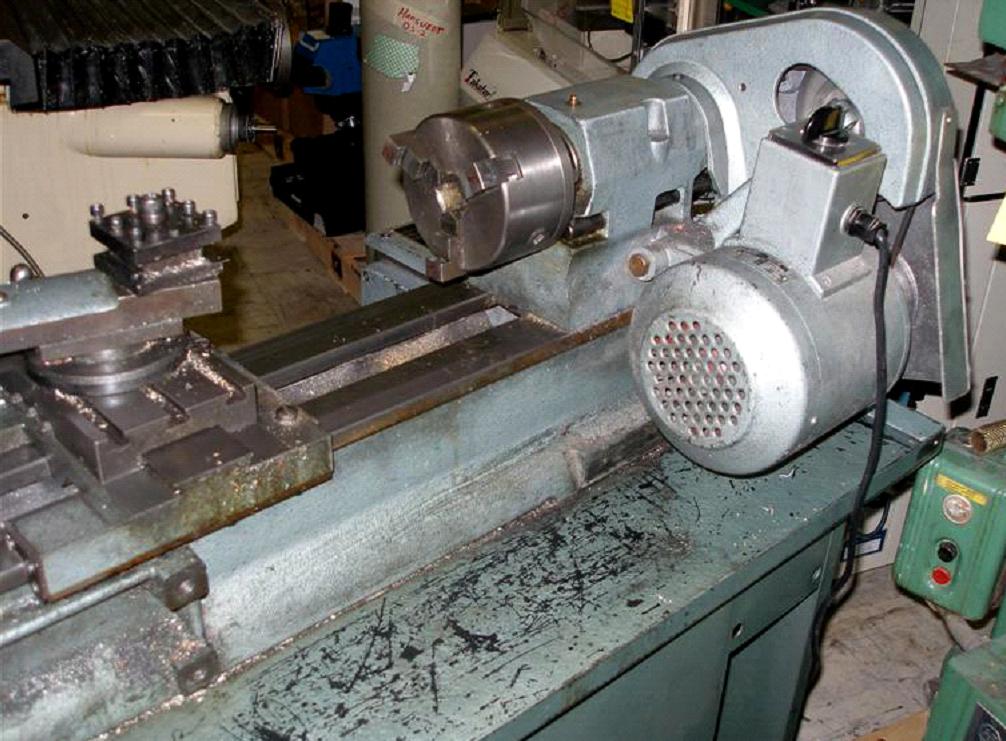 |
|
|
|
|
|
|
|
|
|
|
|
|
|