 |
 |
 |
 |
 |
 |
 |
 |
 |
 |
 |
 |
 |
 |
 |
 |
 |
 |
 |
 |
 |
 |
 |
 |
 |
 |
 |
 |
 |
 |
 |
|
|
|
|
|
|
|
|
|
|
|
|
|
|
|
|
|
|
|
|
|
|
|
|
|
|
|
|
|
|
|
|
|
|
|
|
|
|
|
|
|
|
|
|
|
200 Series Apart from one or two design features (and the late-model aprons on Mk. 3a 100 Series machines) the 200 lathes had, almost nothing in common with the 100 Series, being a new design, of greater capacity based on an entirely fresh set of much heavier and more rigid castings. Paul Clausing has started work on what was described in internal literature as the "1-inch collet capacity lathe" in January 1941, but the pressures of war-time production delayed further work until the conflict was over and the first lathe was not ready for shipment until March 31, 1949. Besides its greater capacity, the most radical change centred on the drive system; all the spindle-speed changes were made before the drive belt reached an 'overhung' pulley on the left-hand side of the headstock spindle. This system - of a pulley on the left-hand end of the headstock - had been used before, but only, I believe, on various light-duty wood and wood-cum-metal lathes and to commit such a design to production on a mainstream, medium-duty centre lathe was a bold move. In the event the designer's courage paid off, and countless other makers - Emco, Myford 254, Scintilla, Wabeco, etc. - successfully copied or adapted the principle. As an aside, it's interesting to consider the extraordinary lengths that some makers of small lathes went to over the years in order to provide a finely-engineered, mid-headstock bearing pulley system - when they could have achieved comparable results with a much simpler and cheaper (though some would argue aesthetically inferior) overhung system. The swing over the bed of the 200 Series was a true 12.75 inches, over the saddle wings 12.25 inches and over the cross slide 7.5 inches; three bed lengths were available giving 24, 36 and 48 inches between centres. Forged, hardened and ground, the spindle had a generous 13/8" bore and 1-inch collet capacity, ran on Timken taper-roller bearings and was fitted with the excellent 'long taper-key drive' nose in an L-00 size fitting that gave both a very rigid assembly and absolute security when running in reverse; the taper bore was finish ground in place after being mounted in its own bearings. Because the headstock spindle was now driven by either one or two V belts from its extreme left-hand end, the headstock could be made in the form of a rigid, open-top box and lubricated from an oil sump within its base - ensuring that the backgears and leadscrew reversing mechanism had a much better chance of survival than before - especially when used for extended periods. Backgear could be selected almost instantly by pulling on a large handwheel fastened to the end of the spindle and throwing over one lever positioned towards the top left of the headstock face. Continued below:
|
|
|
|
|
|
|
|
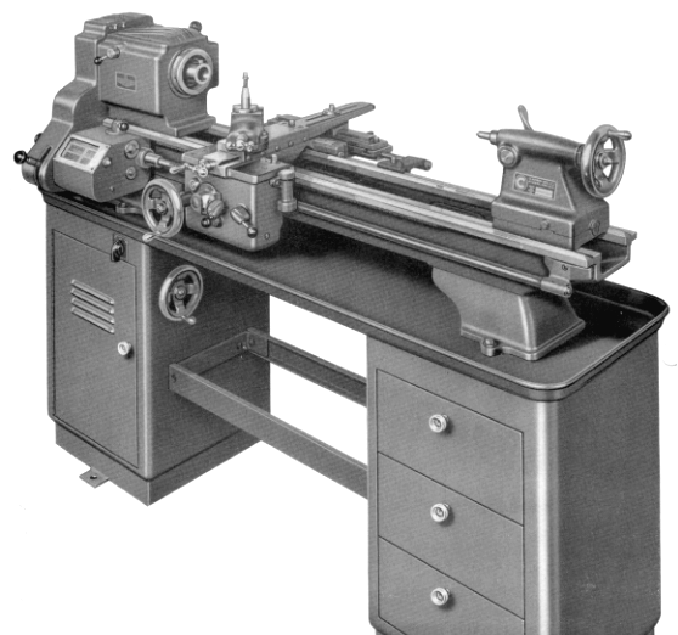 |
|
|
|
|
|
|
Continued: Two drive systems were offered, a conventional 4-step V belt countershaft (which gave a total of 8 speeds from 50 to 1300 rpm) and an infinitely-variable mechanical type that employed expanding and contracting pulleys and produced a usefully-superior speed range of 30 to 1400 rpm. A 1760 rpm 1/3 hp motor was recommended for the ordinary-countershaft lathe - and for the variable-speed machine a 1760 rpm 1/2 hp unit. With a double-wall and an oil sump in the base, the apron carried an all-new (and subsequently much-copied) easy-to-use and positive-action power-feed control system. A centrally-located lever was moved upwards for power sliding and downwards, through a protective spring-loaded central position, for power surfacing. There was no need to screw in a clutch or gear to engage the feed and, more importantly, it could be instantly disengaged with a flick of the lever - a vast improvement on the previous design. As the compound slide had already been modified on the last of the 100 Series lathes, the Mk. 3a, this design was continued for the 200 - even to the inadequately-small micrometer dials.Not only a new design - completely sealed, running on ball races and lubricated by splash from an oil supply retained within its base - the screwcutting gearbox was also operated in an almost entirely different manner To change the thread or feed rate (of which there were still 48) a selector handle was moved until a red marker, under a transparent cover, was opposite the required figure on the chart. A second "engage" handle was then moved to an automatically determined position and the gear selection was locked. Continued below:
|
|
|
|
|
|
|
|
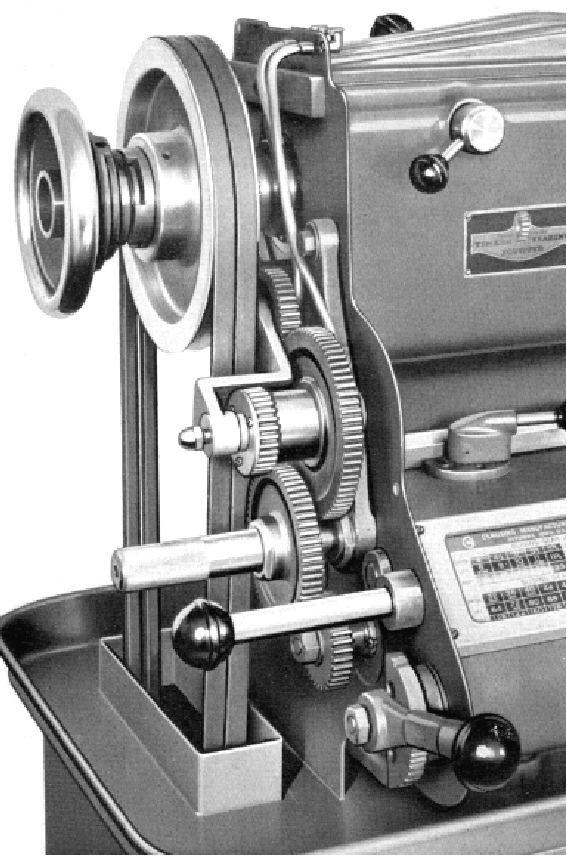 |
|
|
|
|
|
|
Continued: Tensioned between taper roller bearings the leadscrew was well supported and, as all longitudinal play was eliminated, a more immediate response to the power feed control lever was possible. As a finishing touch, the gears and pins that carried the drive from headstock to gearbox were provided with lubricant from pipes connected to two oil caps mounted on top of the headstock. Three different maker's stands were available; the cheapest was a steel bench, with either a wooden or chip-tray top that could hold only the ordinary 8-speed V-belt drive system. There were no cupboards or doors and the right-hand side of the column had to be left open for access to change speeds. The lathe fitted to this stand - and the one supplied for mounting on the customers own bench - had a final drive to the headstock spindle by a single "B" section V belt. A rather better stand was the steel 'semi-cabinet', fitted with a door to the (larger) left-side column and able to accommodate either of the two drive systems. When mounted on this, or the other superior stand, the final drive from both kinds of countershaft was by twin "A" section V belts. The best mounting available for the lathe was the 'full-cabinet'; this had the same left-hand column mounting for the drive with the addition of three rail-supported drawers in the right-hand column. Although a well-engineered lathe, with a generous work-holding ability, the Clausing 200 Series (like many other "light" 12-inch lathes) did not have the sheer mass or industrial 'presence' of, say, a Colchester Student or Master of similar capacity - to say nothing of the fully-geared headstock, optional detachable gap bed, dual metric/inch screwcutting gearbox and 3 hp motor offered on the (very much more expensive and less compact) English machine..
|
|
|
|
|
|
|
|
|
|
|
|
|
|
|
|
|
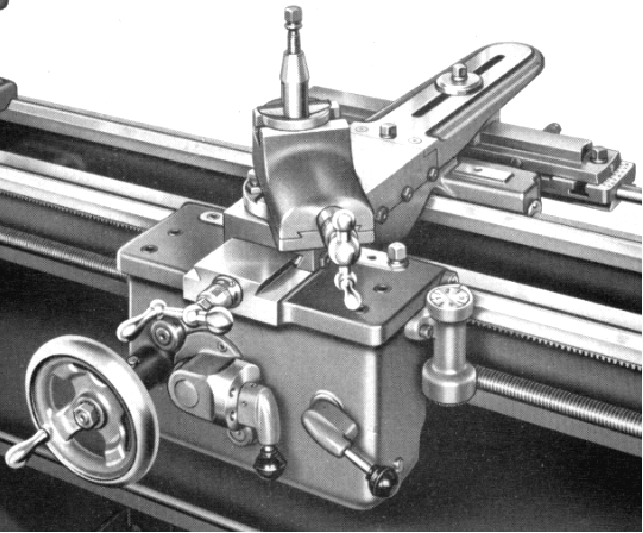 |
|
|
|
|
|
|
The stronger apron of the 200 Series lathe, with its distinctive boss mounted power-feeds selector, also found its way on to some of the last of the Series 100 machines
|
|
|
|
|
|
|
|
|
|
|
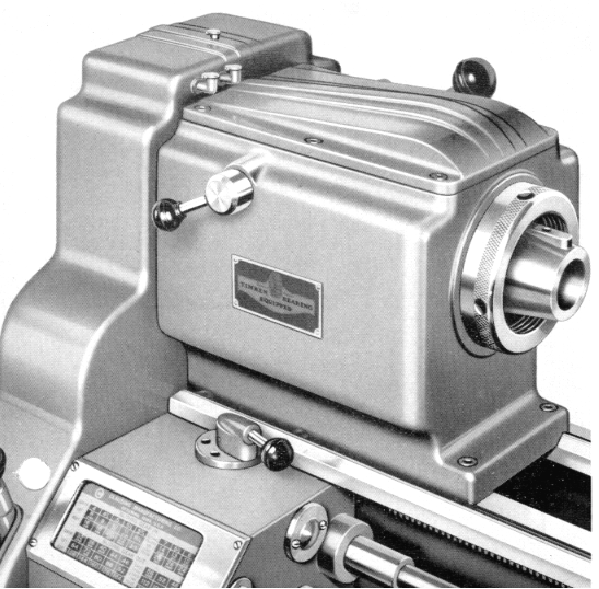 |
|
|
|
|
|
|
A significant improvement in the headstock cantered around the spindle nose that, instead of a thread, was fitted with the much superior and far safer American L00 long-taper fitting.
|
|
|
|
|
|
|
|
|
|
|
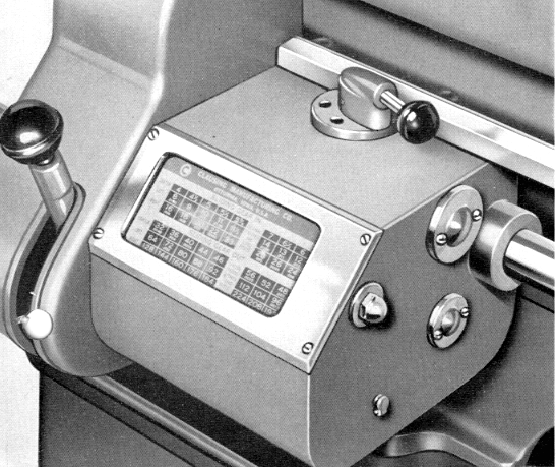 |
|
|
|
|
|
|
The oil-bath screwcutting gearbox was further improved and also made an enclosed unit so preventing the ingress of dirt and chipping.
|
|
|
|
|
|
|
|
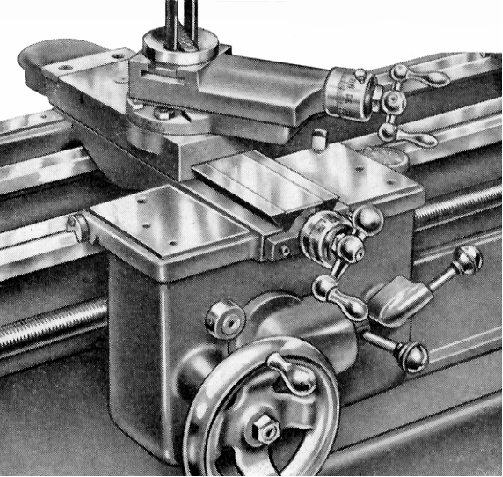 |
|
|
|
|
|
|
|
|
|
Distinctive apron controls of the 12" Clausing 6300/5400 lathe. A single, central, lever controlled the power sliding and surfacing selection.
|
|
|
|
|
|
|
|
|
|
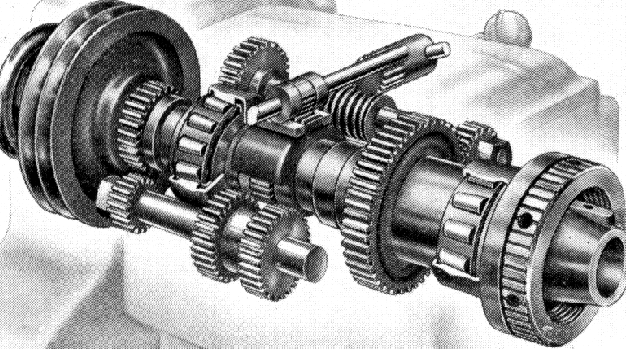 |
|
|
|
|
|
|
Clausing Model 6300 Timken taper-bearing headstock with outboard twin V-belt drive and L00 spindle nose fitting
|
|
|
|
|
|
|
|
|
|
|
|
|
|
|
|
|
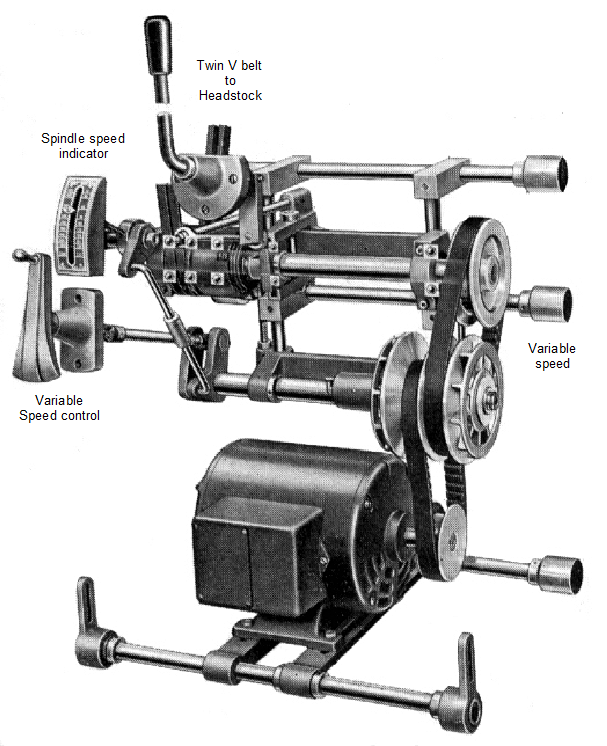 |
|
|
|
|
|
|
Optional variable-speed drive unit fitted with clutch and brake control
|
|
|
|
|
|
|
|
|
|
|
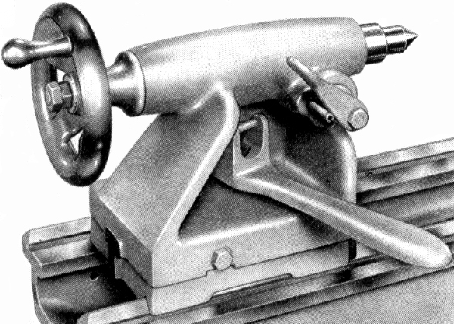 |
|
|
|
|
|
|
The tailstock was fitted with a 3 Morse centre with tang knock-out and very substantial clamps for both base and barrel.
|
|
|
|
|
|
|
|
|
|
|
|
|
|
|
|
|
|