 |
 |
 |
 |
 |
 |
 |
 |
 |
 |
 |
 |
 |
 |
 |
 |
 |
 |
 |
 |
 |
 |
 |
 |
 |
 |
 |
 |
 |
 |
 |
 |
 |
 |
 |
 |
 |
 |
 |
 |
 |
 |
 |
 |
 |
 |
 |
 |
 |
 |
 |
|
|
|
|
|
|
|
|
|
|
|
|
|
|
|
|
|
|
|
|
|
|
|
|
|
|
|
|
|
|
|
|
|
|
|
|
|
|
|
|
|
|
|
|
|
|
|
|
|
|
|
|
|
|
|
|
|
|
|
|
|
|
|
Used by the famous American mail-order company "Sears, Roebuck & Co." (and Simpson-Sears Limited of Canada) the lathe models "Craftsman", "Companion" and "Dunlap" were also employed to brand a very wide range of power and hand tools. Although the company had offered a range of lathes from the late 1800s, it was in 1932 that their most famous machine became available, a 9" swing model manufactured by the Atlas Company. This machine, regularly updated year by year in line with changes to the Atlas range, was replaced in 1936 by a much heavier 12" model based on the Atlas F10. It seems surprising that Atlas built a 12" model for Sears, yet restricted their own machine to a 10" swing, especially as it would be the early 1960s before they increased the capacity of their own lathe to match. The introduction of the large Atlas clone was followed, in 1937, by a version of the same company's 6" lathe. This latter machine was marketed in an almost unchanged form until the late 1960s, when a redesigned Mk. 2 model was introduced and Atlas also began selling direct to the public; these machines are featured on other pages. It can be difficult to separate the wood-turning lathes offered by Sears, Roebuck into the products of Atlas and the Double A Company - the latter of Lansing, Michigan and owned at one time by the huge Brown & Sharp Corporation. However, it appears that, until the 1939 season, the metal and some wood-turning lathes were by Atlas, with the cheaper wood lathes produced by Double A and a number of smaller suppliers including the original Clausing company. In 1936 the first, very simple V-bed "AA" metal-turning lathe was introduced (illustrated immediately below) using the brand name that Sears reserved for their cheaper products: "Companion". Even the earliest models can be clearly recognised as having features belonging to the better-known post-war AA "Model 109" and later Craftsman "Model 80" lathes. These more highly-developed versions included proper leadscrew clasp nuts, an epicyclic "backgear" assembly built into the headstock pulley and graduations on the cross-feed screw; however, the headstock spindle and bearings were always of marginal strength and durability, and remained a weak point throughout the model's life. Some AA 109s were branded as Simpson, for sale by the Canadian mail-order store of the same name; in the 1970s Sears-Roebuck bought out Simpson and renamed the company Simpson-Sears and later just Sears - by which name the firm continues to market the Craftsman brand. Another branding occasionally found on the 109 and Model 80 is "Courlan" - lathes with this marking having been found in Australia and South Africa although one report has the Company based in Jersey City, USA. Should any reader have a Courlan-branded lathe the writer would be interested to know. Principle maker of chucks fitted to AA (and Craftsman) lathes were by Dexter (a company still in business in 2010) and its just possible that the AA may have been marketed in Europe branded "Dexter" - though nothing certain is known about this arrangement. All the lathes illustrated on this page are products of the Double A Company (many people use the shorthand "AA") a regular supplier to Sears of other equipment, whose earliest lathes appear to have been wood-turning machines offered with a range of accessories that allowed them to undertake light-duty metal turning. As a point of interest, the official designation was to be found on the company's transfers badges: Double A Products Co. / Manchester, Michigan 48158 / A division of Brown & Sharpe Mfg . Co Numbers affixed to these cheaper Craftsman lathes included: 109.0701, 109.0702, 109.0703, 109.2046, 109.2053, 109.2062, 109.2063, 109.2064, 109.2082, 109.2127, 109.2128 with some having an additional zero at the end. Continued below:
|
|
|
|
|
|
|
|
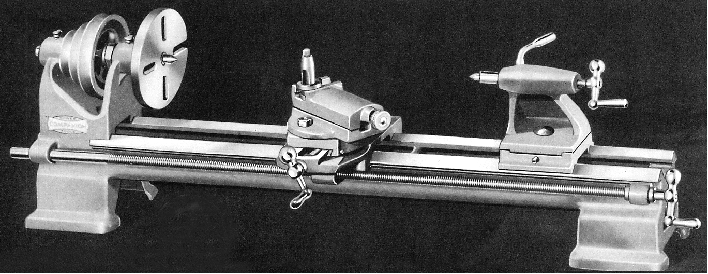 |
|
|
|
|
|
|
Continued: Late 1936 and the first of the V-bed AA metal-turning lathes appears as the simple, plain-turning, 6-inch by 28-inch "Companion" model (Catalog Number 99 P 2021) listed as: "metal working, model maker's lathe". The 1/2" x 24 t.p.i headstock spindle ran in plain bronze bushes - the front was adjustable - and carried a 3-step V belt pulley. Unfortunately, in its first form, the machine was not as heavily built nor as well specified as it might have been; the front of the headstock casting was open and the front bearing given the minimum of support; both the headstock and tailstock were provided with a non-standard form of taper that was close to, but did not match, the standard O Morse - a size adequate for genuine miniature lathes, but hopeless for anything with a swing of greater than 3 inches. There were no graduations on the micrometer feed dials and no quick-feed rack drive fitted to the carriage, instead it was hand driven along the length of the twin V-way bed by a leadscrew and "full" nut - but at least the slide rest was a proper compound unit. For decades, most small lathes have been arranged so that carriage and tailstock run on different ways, or different parts of the same way, to ensure that the tailstock does not have to run over the bed worn away by the saddle and spoil its height alignment. Unfortunately, on all 109s, in the interests of economy, the ways were shared. Notice that the lathe has no apron on the carriage, the leadscrew nut is fastened to the underside of the saddle front, a simple design used by many other makers, such as Portass of Sheffield. However, despite these simple arrangements, it is as well to bear in mind that the machine sold at a very competitive price and (devoid of almost all equipment) was listed at just $10.95 when even a decent-quality 1/4 hp motor from the Craftsman catalog was US$11.70. For the money this represented a remarkable achievement of production economics. Throughout its production life (1936--1940) the lathe was offered with only a very limited range of accessories: a 4-jaw chuck at $3.10, 0 Morse centres at 45c, a jack-shaft drive pulley system for $2.45 (that gave a speed range more suitable for metal turning) and standard or "improved" pairs of adjustable motor rails at 50c. Continued below:
|
|
|
|
|
|
|
|
|
|
|
|
|
|
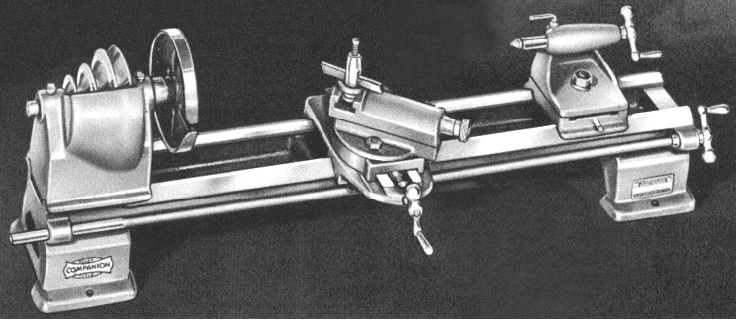 |
|
|
|
|
|
|
Continued: By late 1937 the lathe had been given an enclosed front to the headstock casting that both protected the operator's hands from the drive and provided a very much better supported spindle - though there was no back wall to the assembly and both the left and right-hand sides were of rather slender proportions. For once a maker was refreshingly honest about its products limitations, stating that the lathe was: "Well suited to the model maker or man who wants to do light metal work. Not quite the accuracy and precision of the larger machines, but plenty close enough for most work." To put the lather into perspective, although the price had now risen to $14.50 the nearest competitor in the Craftsman range, the newly-introduced and very well specified 6-inch Atlas clone, was $42.50 - a price that included a neat, built-on all-V-belt countershaft unit - but not a motor or set of screwcutting changewheels. In order to offer a dedicated armature-turning model, "Sherman Clark Mfg. Co. of Jackson Michigan (USA)" offered a special version with longitudinal feed by power and hand lever and, if your 109 is so equipped, the writer would be interested to hear from you. The 109 model survived in the catalogs until 1940 when it was replaced by a more highly developed and useful version.. Continued below:
|
|
|
|
|
|
|
|
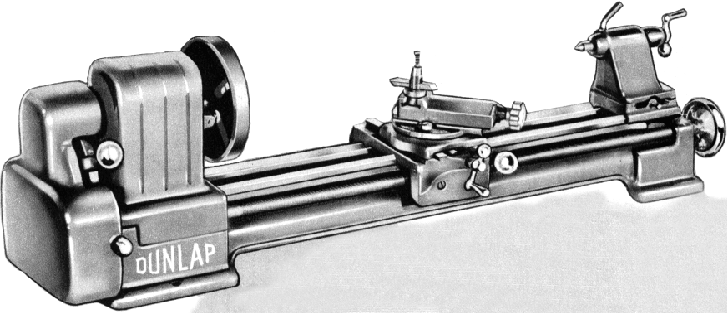 |
|
|
|
|
|
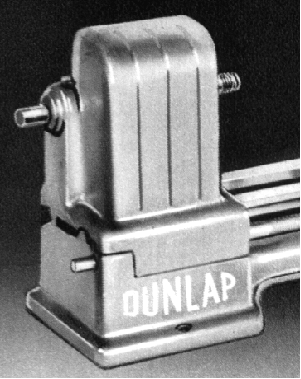 |
|
|
|
|
|
|
Above: badged as a Dunlap the new-for-1941-season 109 with screwcutting and backgear. It was also available (left) bereft of these fitting as the "Standard Model" 109.2046. Because the lathe was offered as a modular system it was possible to buy the ordinary model and then add features as finances allowed.
|
|
|
|
|
|
|
|
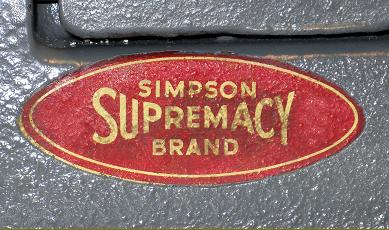 |
|
|
|
|
|
|
Badge used on the AA lathe distributed through the Canadian Simpson Company
|
|
|
|
|
|
|
|
|
|
|
|
|
|
|
Continued: Marketed by Sears the new-for-1941-version of the AA109 6" x 18" at first carried the name "Dunlap", a name always used for the company's less-expensive models. By now the lathe had begun to grow up and also been given the contemporary "streamline" treatment and, for the fist time, was fitted with an apron that carried a leadscrew half-nut the operating lever for which snapped into position through the operation of a spring-loaded ball detent. Although this mechanism gave a positive action, there was no compensating pad on top of the leadscrew to absorb the upward thrust. The new lathe was a model of mechanical simplicity and economical production with the saddle, apron and the cross-feed screw end bracket cast as one piece - as illustrated lower down the page. The lathe was initially marketed as just a single model with a capacity between centres of 18 inches (identification numbers included 109.07801 and 109.0702 with a hand-cranked leadscrew to drive the carriage (but no screwcutting), the 109.0703 with both screwcutting and backgear and later, advertised for just a single selling season (from November 1945) as a short-bed version with models that included the 109.2062 and 109.20630. However, regardless of specification, all versions were of very similar appearance and the simple models always available with a range of extras to turn them into more effective machines; these items included a 5 : 1 ratio epicyclic backgear ($3.95) built into the 4-step headstock pulley and a complete screwcutting set ($9.65) consisting of changewheels (these are the same as used on the Craftsman/Atlas 618), mounting bracket, inner and outer guards, a 0.5" by 16 t.p.i. Acme-form leadscrew and a proper tumble-reverse mechanism that allowed the spindle turn freely or engage the changewheels to produce left or right-handed threads to choice. An interesting detail concerns the beds: those with shorter ones, whether badged as Dunlap or (later) Craftsman, had a gap between the top of the two V-ways of 2.50 inches while two specific variants, the longer 109.0702 and 109.073 models had beds that were narrower, with a V-to-V spacing of 2.125". Interestingly, although the "manuals" for this series mentions the 109.07** types, they fail to give separate parts numbers for either the bed or any of the other important items associated with it - the saddle, headstock casting and tailstock, etc. Should you come across a dedicated "manual" for the 109.07** versions, the writer would be very interested to hear from you. Whilst the improvements to both rigidity and specification were welcome all versions of the new model were still of limited usefulness for serious work as they retained the No. 0 Morse centres, had un-graduated micrometer dials and were not supplied with a speed-reducing countershaft unit. In recent years the inherent weakness of the headstock assembly (and flexibility of the whole machine) has been displayed by a number of scrap machines appearing less their main spindle. These were probably broken when the owner, an impatient beginner, "bore down" on the cross-feed to "compensate" for a dull, off-centre tool bit. Those more experienced user would have recognised the "wiggly" feeling as the tool got under the work - the precursor, of course, to something snapping. However, when new, the machines remained good value with the better specified of the two priced at $31.95 - something of a bargain when the 6" Atlas was $67.50 and the 12" Deluxe $135. When driven directly from an electric motor 8 speeds from 580 to 2040 RPM were available - and threads from 8 to 96 t.p.i could be cut. However, because the lathe's bottom speed was so high, success in this department would have meant either specifying the optional epicyclic backgear assembly, which was built into the headstock belt pulley and reduced the bottom speed to a more useful (but still not ideal) 116 rpm, or looking through the Sears catalog in the hope of being able to adapt one of the speed-reducing "Jack-shaft" (countershaft) units made for the wood-lathe range. That the lathe was not offered with one of these as even an option was a strange omission, for, in earlier years, just such a unit had been listed as an accessory along with other metal-turning accessories. When the Sears, Roebuck catalog reappeared after WW2, in 1948, the 6" lathe was marketed under a new model number "99 TM 2063" and, labelled "Craftsman Model 80"; apart from a shorter bed it looked identical to its last appearance in 1943 when it was labelled a "Dunlap". The 2063 version of the Model 80 lasted for just one year and in 1949 the Catalog number became 99 AM 2127 (Model 109.21270) and the familiar three-rib headstock cover was replaced by an "engine-turned" decorative plate with other numerous styling changes to give it a more "up-to-date" appearance. No mechanical improvements were made to the lathe which now had a deliberately styled "consumer look", and was offered, as before, in basic form without motor or chuck. The headstock spindle carried a three-step V pulley - whilst supplied with the lathe was a four-step pulley to be used on the customer's own motor. Although fitted with a planetary-type backgear assembly built into the face of the headstock pulley, tumble reverse and screwcutting there was no countershaft arrangement and, if directly driven by the recommended 1750 rpm motor, the bottom speed of 120 rpm would have made screwcutting very difficult - though no doubt serious users might have found a slower or variable-speed motor and fitted smaller pulleys on its shaft or built a speed-reducing countershaft to get round the problem. Obviously aware of the limitations imposed by this arrangement, the Company offered later versions with the option of a double-step pulley on the motor and a proper countershaft assembly, thus doubling the number of speeds and giving, according to the handbook, a range from 55 to 465 rpm in backgear and from 380 to 3050 in direct drive - a very much more satisfactory arrangement. The (frankly weak and inadequate) headstock spindle ran in bronze bearings and carried a nose thread of 0.5" x 20 t.p.i. To the inexperienced eye this would have appeared a little lathe of attractive design but, in reality, it was a bottom-of-the-range model and intended only for very light-duty work. Although with experience, care and the use of light cuts satisfactory work could be accomplished, new owners, once exposed to the practicalities of using the machine, must have been quickly irritated by its general lack of rigidity, the tiny 0-Morse taper centres, the absence of a proper handwheel handle on the leadscrew end, the penny-pinching failure to fit graduated dials on the feed screws and, on early or standard late versions, a bottom speed that was far too fast. In truth, if you want to do real work, don't buy a 109, find something else…. Besides lathes, the Double A Company also manufactured many items for Sears including bench grinders, wet grinders, sanders, bench saws and a builders' saw. Production of lathes appears to have stopped in about 1965 and, unfortunately, parts and drawings are no longer available. Although the two models are very different, confusion has arisen in the past between the "Craftsman 80" and another lathe sold be Sears, the Craftsman 6" - a machine actually made by the Atlas Company. The Craftsman 80 was in quite a different league to the Atlas version and cost, in the mid 1950s, as little as $48.50 in comparison to the $160 of its much better built and specified bother..
|
|
|
|
|
|
|
|
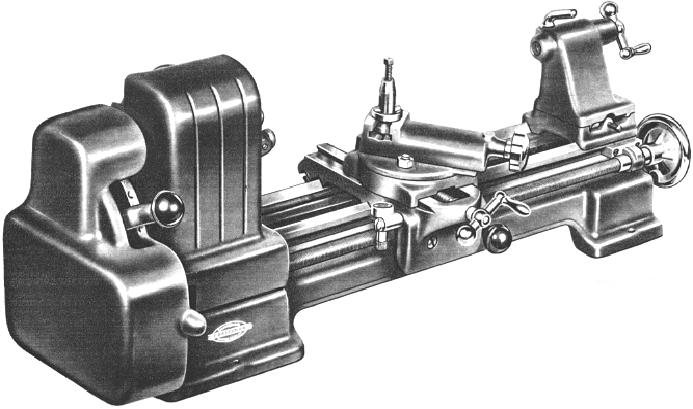 |
|
|
|
|
|
|
Listed for just the 1948 selling season, the Double A Company's Model 109-2063 was identical, apart from a shorter bed and a bolt-on bracket to carry the tailstock end of the leadscrew, to its last appearance in wartime 1943.
|
|
|
|
|
|
|
|
|
|
|
|
|
|
|
|
|
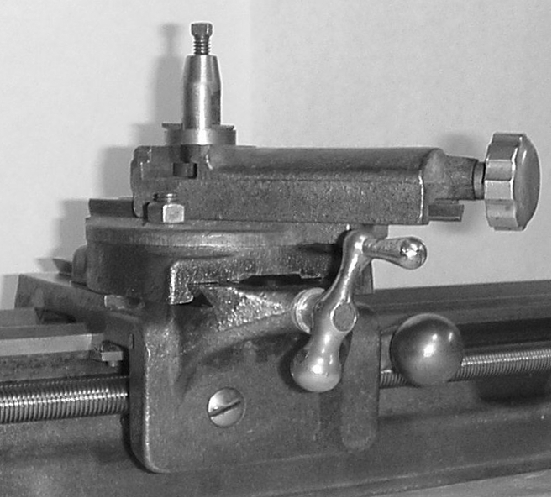 |
|
|
|
|
|
|
Economical casting. The saddle on the 1941 109-series was cast complete with an apron and cross-feed screw end bracket.
|
|
|
|
|
|
|
|
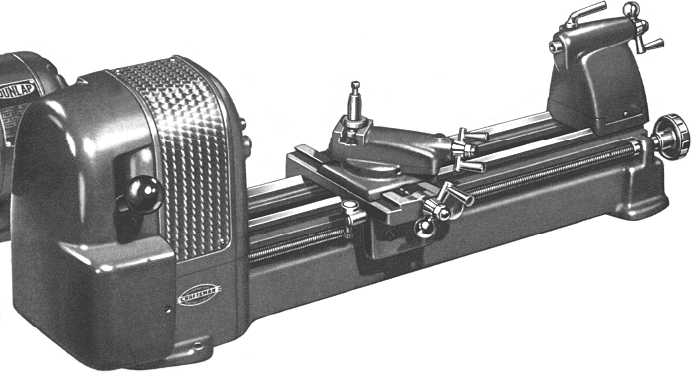 |
|
|
|
|
|
|
1949 6" x 12" Craftsman Model 80 - usually catalogued as the 109-21270
|
|
|
|
|
|
|
|
|
|
|
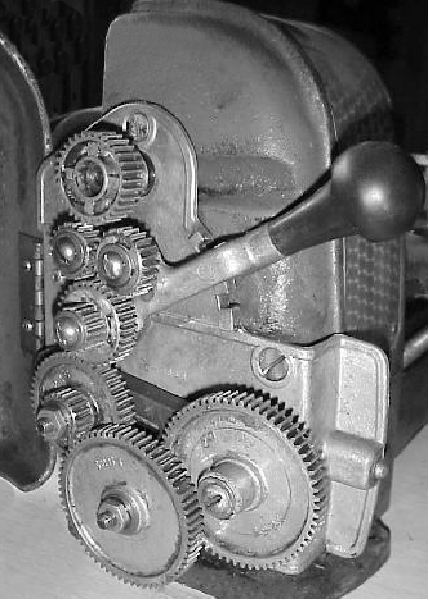 |
|
|
|
|
|
|
|
|
|
Craftsman 80 (Model 109.21270) screwcutting changewheels and tumble reverse mechanism. Note how use was made of the inner-guard cover to provide an indent location for the tumble reverse selector lever - a method also used on the English Murad lathe of the 1940s.
|
|
|
|
|
|
|
|
|
|
|
|
|
|
|
|
 |
|
|
|
|
|
|
The 3-inch centre height by 19.25" between centres Model 109.21280 was the last machine in the AA series and listed until the late 1960s. It had a distinctly "square" appearance to the headstock, looked rather different to the earlier variants and, because of the styling, is sometimes confused with the later Atlas Mk. 2 6-inch (also produced in a Craftsman version). The headstock spindle ran in plain bearing and carried a 5 : 1 ratio epicyclic slow-speed "backgear" arrangement inside the 3-step headstock pulley that gave a total of 6 speeds; the headstock pulley was driven directly from the motor, with no intermediate countershaft. In comparison with earlier versions the lathe featured numerous small improvements, including a No. 1 Morse taper tailstock and No. 2 Morse headstock spindle, and further details can be found here. If you own a 109.21280 the writer would be interested to hear from you.
**It has long been assumed that Simpson, the Canadian department store and mail order firm was bought out by Sears. However, Simpson were an independent firm and carried numerous AA products including the early AA-109 lathe. Until Simpson and Sears entered into a partnership in 1952, one might presumes that AA Engineering had an exclusive relationship with Sears in the US, but was free to supply foreign firms where Sears had no market presence. Simpson, a powerful firm and not a mere satellite of the great Sears, Roebuck empire, was thus able to sell AA products through its own supply system. Emerging in good order from the depression of the 1930s - and despite materials restrictions and significant loss of employees during WW2 - it expanded during the conflict and immediately after allowing it to swallow Smallman and Ingram of London Ontario and R.H. Department Store, the largest retailer in Regina Saskatchewan. It also managed to build a new mail-order centre in Vancouver, British Columbia, and renovate many of its outlets. It is not known when Simpson first sold an AA Products lathe, but the rare 'Simpson Supremacy' lathe was identical to the Dunlap 109 model introduced in 1943 and then reintroduced in December 1945 by Sears. After WW2, Sears, sought expansion into Canada - though it could not simply steamroller the 'Dominion' firm Simpson. Hence, in 1951, Sears initiated discussions about an association with Simpson welcoming the capital for expansion and access to Sears' procurement and distribution mechanism. Accordingly, in 1952, a deal was reached whereby Sears assumed control of Simpson's mail-order business comprising 390 fixed distribution installations. Concurrently, the two firms would jointly own and operate department stores known as Simpson-Sears. During the 1950s and 1960s Simpson continued to run its own stores in the five urban zones where it already had a presence (and also opened new outlets) while outside these areas new Simpson-Sears stores began to appeared. In 1978 the great Hudson's Bay Company acquired the Simpson chain and, in 1991, the last Simpson store became 'The Bay'. During the course of this the Simpson-Sears stores became US-operated Sears operations under that name.
|
|
|
|
|
|
|
|
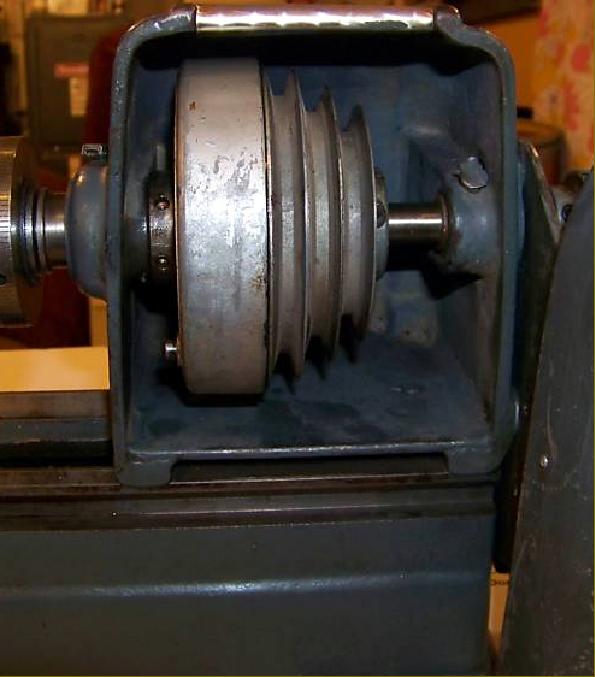 |
|
|
|
|
|
|
Headstock epicyclic gear housing on the 109 Not as common on other makes as one might expect - especially given the transformation it can make to a lathe's capabilities - the compact epicyclic (or planetary) backgear assembly fitted to some AA-manufactured, Craftsman-branded machines gave a range of slow speeds that allowed screwcutting and the facing of large diameters to be undertaken with a greater chance of success. Consisting of three main elements, the mechanism comprised: a gear attached to a 3-step pulley, a carrier with 3 planet pinions and an annulus gear. The 3-step pulley, together with its attached "sun" gear, was free to rotate on the headstock spindle. Opposite was a large gear cut on the inside surface of a short cylinder so that its teeth faced inwards (an annulus gear): this assembly was also free to rotate on the spindle. The "sun" gear on the 3-step pulley engaged simultaneously with 3 "planet" gears (called pinions because they meshed with a larger gear) mounted on studs attached to a carrier plate that was both keyed (permanently) to the spindle and locked (temporarily, by a sliding block) to the annulus gear. Because the carrier was both keyed to the shaft and locked to the annulus gear, non of the gears could rotate and turning the pulley caused the spindle to rotate - so giving a direct drive. For any epicyclic gearing to work, one of the three gears sets has to be held stationary so that one of the other gear sets can act independently as an input and the third set independently as an output. In the case of the 109 lathe it was the annulus gear that was prevented from rotating (by a 2-position indented pin passing through the front face of the headstock into its face) and the carrier assembly that had to be released so that it could turn independently. The carrier had six slots cut in its periphery into which a block, sliding in a slot cut in the face of the annulus gear, could engaged and so lock them together. The block was clamped in place by a bolt and slackening this let the block slide out of engagement and allowed the carrier and its planet pinions to rotate. With this new arrangement set, turning the pulley caused the "sun" drive gear to rotate the planet pinions, mesh with the annulus gear and so reduce the drive ratio. When you see the mechanism in action, its function is obvious - though tortuous to explain. Another AA epicyclic backgear assembly, with the annulus gear held stationary by a clamp, can be seen in pictures of the company's last lathe, the 109.21290. Those of you interested in automobile engineering might recall the automatic transmission systems made by Ford and Borg-Warner that also incorporated an epicyclic system. However, these gearboxes were rather different and, instead of the usual two speeds generated, these boxes had three using a gearset called the "Ravigneaux " - after the French engineer and inventor Pol Ravigneaux. The patented Ravigneaux system was ingenious and used two sun gears in combination with a single planet carrying two sets of planetary gears. An useful summing up of AA109 production and models has been composed by the contributor "aoresteen" on the hobby-machinist.com site. He writes: Generation I lathes 109.0701 Released 1938 Bed Vee to Vee 2.125" Spindle Nose size: 1/2" x 24 t.p.i. Plain 4-step spindle pulley and branded: "Companion" 109.0702 Released 1941 Bed Vee to Vee 2.125" Spindle Nose size: 1/2" x 24 t.p.i. Plain 4-Step spindle pulley and branded: "Dunlap" 109.0703 Released 1941 Bed Vee to Vee 2.125" Spindle Nose Size: 1/2" x 24 t.p.i. Planetary backgear pulley and branded: "Dunlap" Note 1: The 109.0702 is the same lathe as the 109.0703 except that the 109.0703 has thread cutting gears. The 109.0702 came without the gears but Craftsman sold a upgrade kit (Cat No. 99 PT 2083) that would convert the 109.0702 in a 109.0703 model. Generation 2 lathes 109.20630 Released 1945 Bed Vee to Vee 2.50" Spindle Nose size: 1/2" x 20 t.p.i. Planetary backgear pulley and branded: "Craftsman" 109.21270 Released 1949 Bed Vee to Vee 2.50" Spindle Nose size: 1/2" x 20 t.p.i. Planetary backgear pulley and branded: "Craftsman" 109.21270 (Bronze/Gold Color) Released 1960 Bed Vee to Vee 2.50" Spindle Nose size: 1/2" x 20 t.p.i. Planetary backgear pulley and branded: "Craftsman" Note 2: The 109.21270 (Bronze/Gold Color) model is exactly the same as the original grey model. For the last 3 years of it's life (1960,1961,1962) it was sold in the Bronze/Gold color. Generation 3 lathes 109.21280 Released 1965ish ("Mid-1960s") Bed Vee & Square Step Size ??. Spindle Nose size: unknown - Planetary backgear pulley and branded: "Craftsman"
|
|
|
|
|
|
|
|
|
|
|
|
|
|
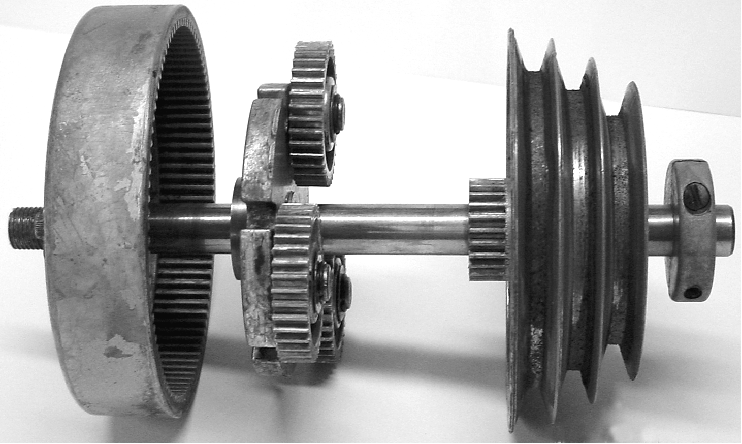 |
|
|
|
|
|
The whole of the compact epicyclic gear assembly. On the left the annulus gear, free to rotate on the spindle: in the middle the carrier plate keyed to the spindle with its 3 "planet" pinions: on the right, and also free to spin on the headstock spindle, the 3-step pulley with its attached "sun" gear.
|
|
|
|
|
|
|
|
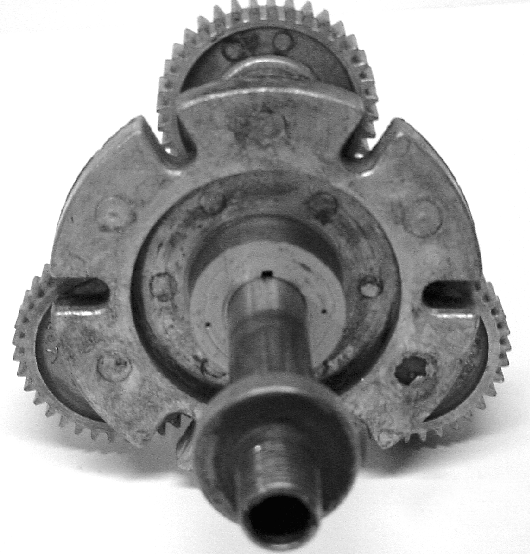 |
|
|
|
|
|
|
The carrier plate with 6 slots in its periphery to accept the sliding block that locked it to the annulus gear CONTINUED HERE
|
|
|
|
|
|
|
|
|
|
|
|
|
|
|
|