 |
 |
 |
 |
 |
 |
 |
 |
 |
 |
 |
 |
 |
 |
 |
 |
 |
 |
 |
 |
 |
 |
 |
 |
 |
|
|
|
|
|
|
|
|
|
|
|
|
|
|
|
|
|
|
|
|
|
|
|
|
|
|
|
|
|
|
|
|
|
|
|
|
|
|
|
After some forty years of steady development - though retaining the same basic design as earlier models - by the late 1940s W & B borers had their drive from the main motor by Vee belts, the motion passing through a self-compensating, multi-plate clutch that turned in ball and roller bearings lubricated by an oil bath Built as a complete unit, with hydraulic oil supply pipes, a distributor unit and valve chest, the speed-change gearbox had shafts that ran in ball and roller bearings and gears in a heat-treated, nickel chrome steel with their tooth profiles - and the shaft splines - being ground finished. Twelve speeds, in geometrical progression were usually provided, selected from a direct-reading dial engraved with changes made by hydraulic action. If two gears had stopped tooth-to-tooth - and so prevented engagement of a selected speed - a patented "gear-rocking" mechanism came into operation and partially rotated the gears until engagement was effected. Safety ensured by the change control being interlocked with the brake to prevent selection of a speed change when the clutch was engaged. As many jobs were extraordinarily heavy, to being them to a halt a powerful hydraulically operated, internal expanding brake by Lockheed, self-compensating for wear, was fitted. Like the speed-change gearbox, that for feeds was also formed as a complete unit with shafts that ran in ball and roller bearings and gears made from heat-treated, nickel-chrome steel with their tooth profiles - and the shaft splines - being ground finished. The twelve feeds - hydraulically selected by sliding dog clutches of alloy steel in combination with a free wheel - were selected by a rotating dial and operated in vertical, horizontal and angular directions. Engagement of the reversible feeds was by a hardened, positive clutch with a shear pin fitted to prevent damage from overloading. Fitted with "rapids" to the tool slides as part of the standard specification, drive for this function came from a separate gearbox, driven by its own motor and protected by a safety overload clutch. The drive passed through a hydraulically operated, self-adjusting, wet-plate clutch, the controls being interlocked to prevent the simultaneous engagement of two feed rates. The rapid drive was interlocked with the feeds and controlled - as it would have been on a milling machine - by a spring-loaded, combined feed and rapid-power traverse lever (releasing hand pressure on the lever disengaged the rapid feed). Continued below:
|
|
|
|
|
|
|
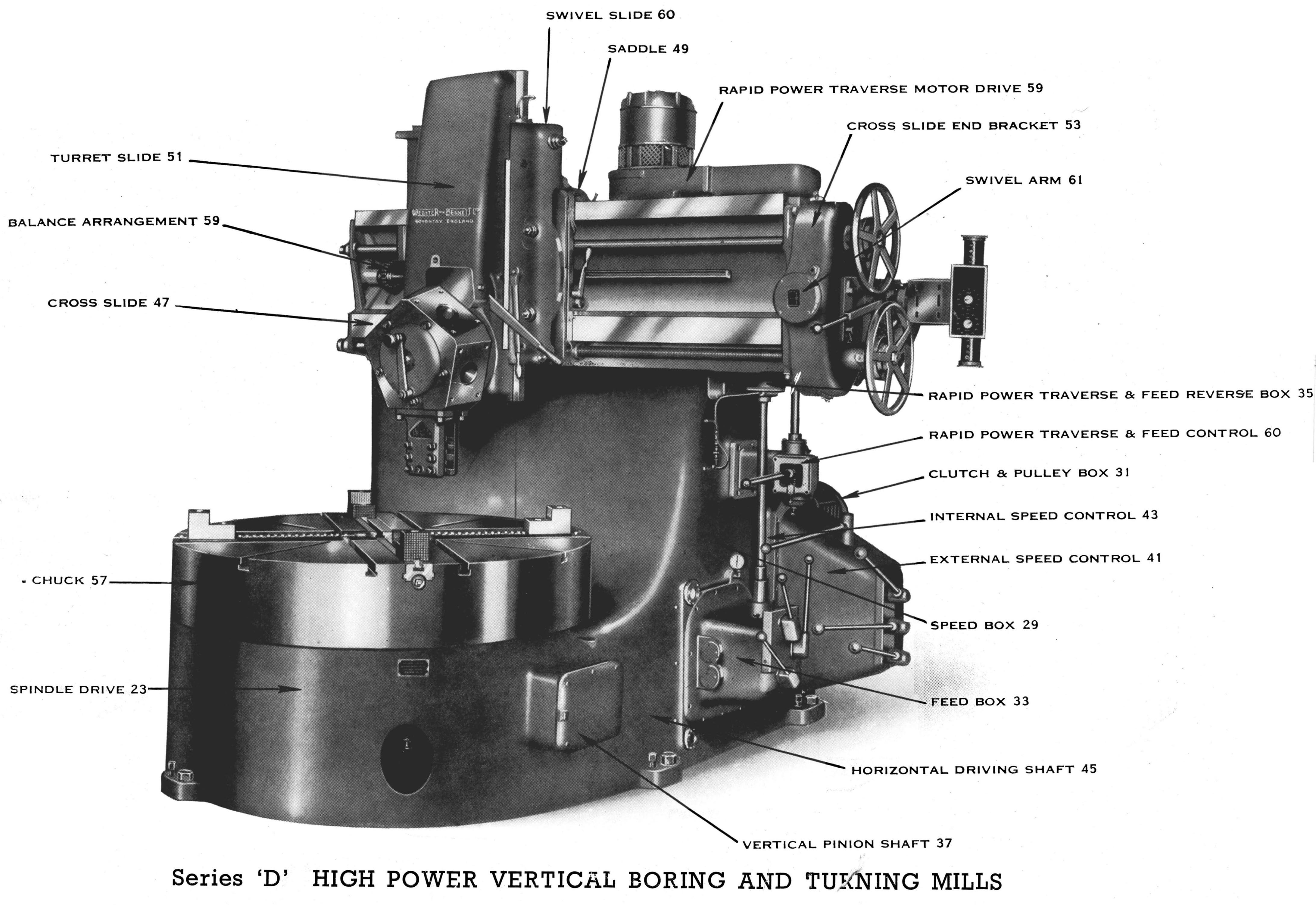 |
|
|
|
|
|
|
|
|
Continued: Built into the clutch and pulley box was a gear pump that supplied hydraulic pressure, two circuits being generated, one of low-pressure for bearing lubrication the other for control of the drive through clutch and brake, speed and feed changes and the rapid power traverse. Individual pressure gauges were fitted to each circuit as were (built into the main column) filters on the suction side of the pump and pressure regulators. The result of hydraulic control being employed was that finger-tip pressure alone was sufficient to start and stop the machine - and operate all other hydraulic functions. Instead of being termed a table or faceplate, the circular work-holding unit was, because of its function, termed by the makers as a "chuck" - this being spigoted, bolted and dowelled to a hollow spindle that ran in precision roller bearings. While the smallest model had its large diameter spindle in a Meehanite cast iron that ran in taper roller bearings to carry both radial and the considerable vertical loads, larger models in the 48-inch, 60-inch and 72-inch sizes had a forged steel spindle supported in parallel roller bearings for radial loads with thrust taken by a large diameter, pressure lubricated plain bearing of the Vee or flat type - the choice depending upon the speed range and class of work for which the machine was intended. If the customer insisted, the makers offered (at extra cost) to equip the larger models with an all-taper-roller bearing assembly. Drive to the chuck was transmitted through a hardened and ground pinion and -depending upon the particular model and its duty - a single-helical gear in a high-tensile steel that was mounted either as a lining to the inside wall or externally on a central boss. Two types of manually operated chucks were offered: an independent 4-jaw and a self-centring 3-jaw. Both came in a range of sizes, had bodies (and all other fittings) in a hardened and ground steel and each was equipped with T-slots for the mounting of special fixtures. When a machine was intended for continuous or batch production, hydraulic clamping of the jaws could be fitted, power being supplied by a separate motor-driven pump unit. A considerable number of extra-cost options was offered by the makers including electrically operated vertical and horizontal feed trips, a ram (slotting) head designed to deal with tall work-pieces when the main operation consisted of machining deep bores into which the ordinary turret head would not fit. Interchangeable with the turret head, the slotting head could be supplied either as standard on a new machine, or as an optional extra. Coolant equipment was an extra, this coming with a tall guard made in detachable flat sections that surrounded the table. Normally indexed by hand, the turret could also be electrically operated, a push button on the control panel being the only necessary control. While the fitting was available for all models, it was especially useful on the larger 'E.H.' models when the elevating way was raised and so putting the turret beyond the operator's reach. Another useful addition on the EH range was power clamping of the cross rail's vertical position, this being achieved by hydraulically operated toggles. In order to ensure that the clamps were automatically released before the lifting motor could start (and re-applied after it has stopped), the mechanism was interlocked with it by a solenoid valve and pressure switch controlled by a set of common push buttons. When a machine was intended for continuous or batch production, hydraulic clamping of the jaws could be fitted, power being supplied by a separate motor-driven pump unit. A separate control panel was provided for the installation with settings provided for clamping pressure and the selection of internal or external gripping. An essential safety measure was an interlock that prevented the machine from starting until the chuck pressure was applied - the chuck controller only able to be moved when the main motor clutch was disengaged. In addition, should the hydraulic pressure fail, the machine would stop automatically. If taper turning was required a complete (and rather complex) gearbox installation was available to make this possible. A number of special items to help with difficult machining operations was also listed amongst which was an attachment for the manufacture of piston rings from thin-walled cast iron tubing, jaw-equipped jigs and the necessary boring bars to work on axel boxes, profile copying attachments in both standard and electronically controlled forms, and a screwcutting gearbox. Webster & Bennett Models D, DH, M and EH continued on Page 2
|
|
|
|
|
|
|
|
|
|
|
|
|
|
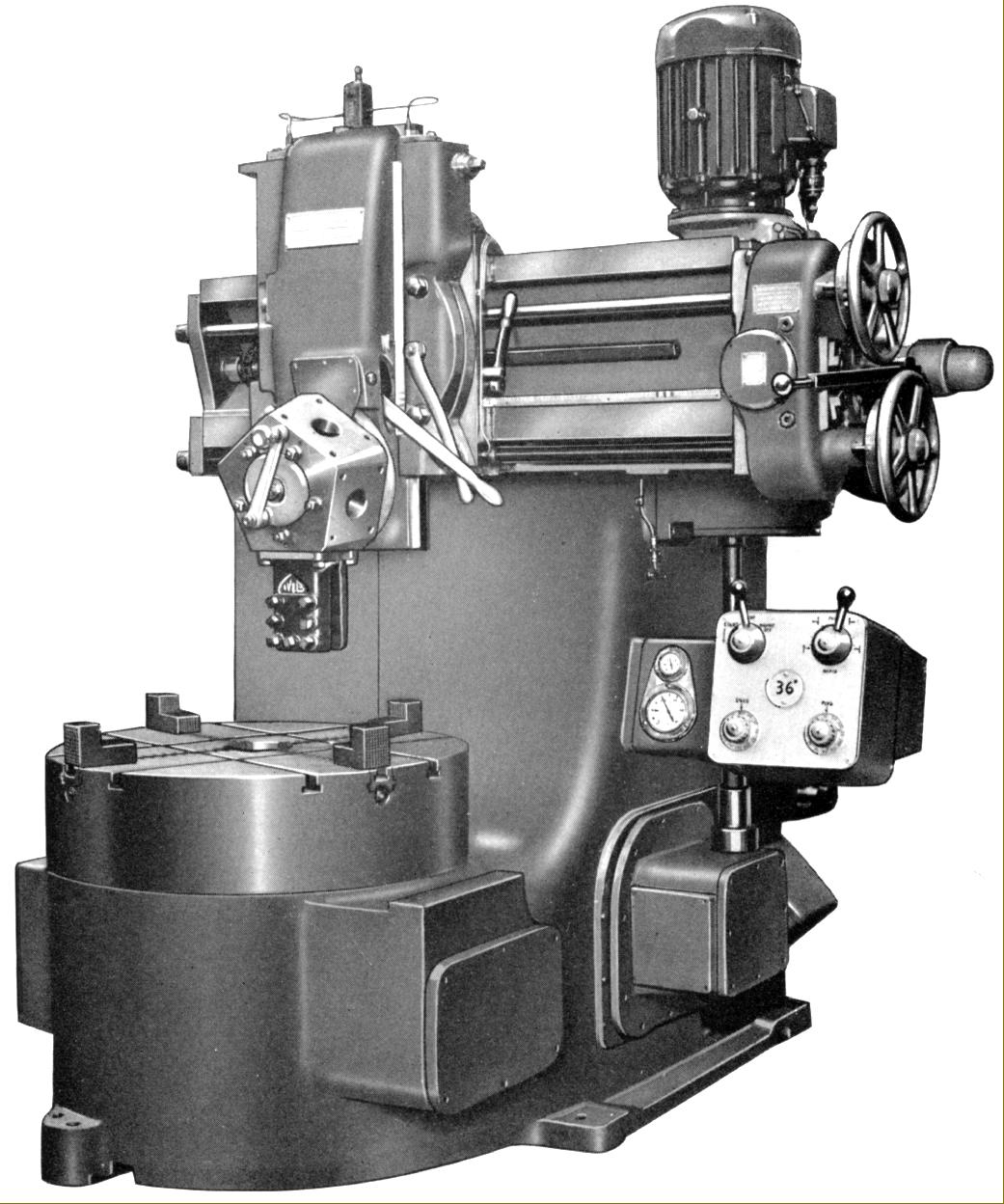 |
|
|
|
|
|
|
|
|
Standard 30-inch Series 2 Model DH Single, as built from the 1950s, fitted with an independent 4-jaw chuck
|
|
|
|
|
|
|
|
|
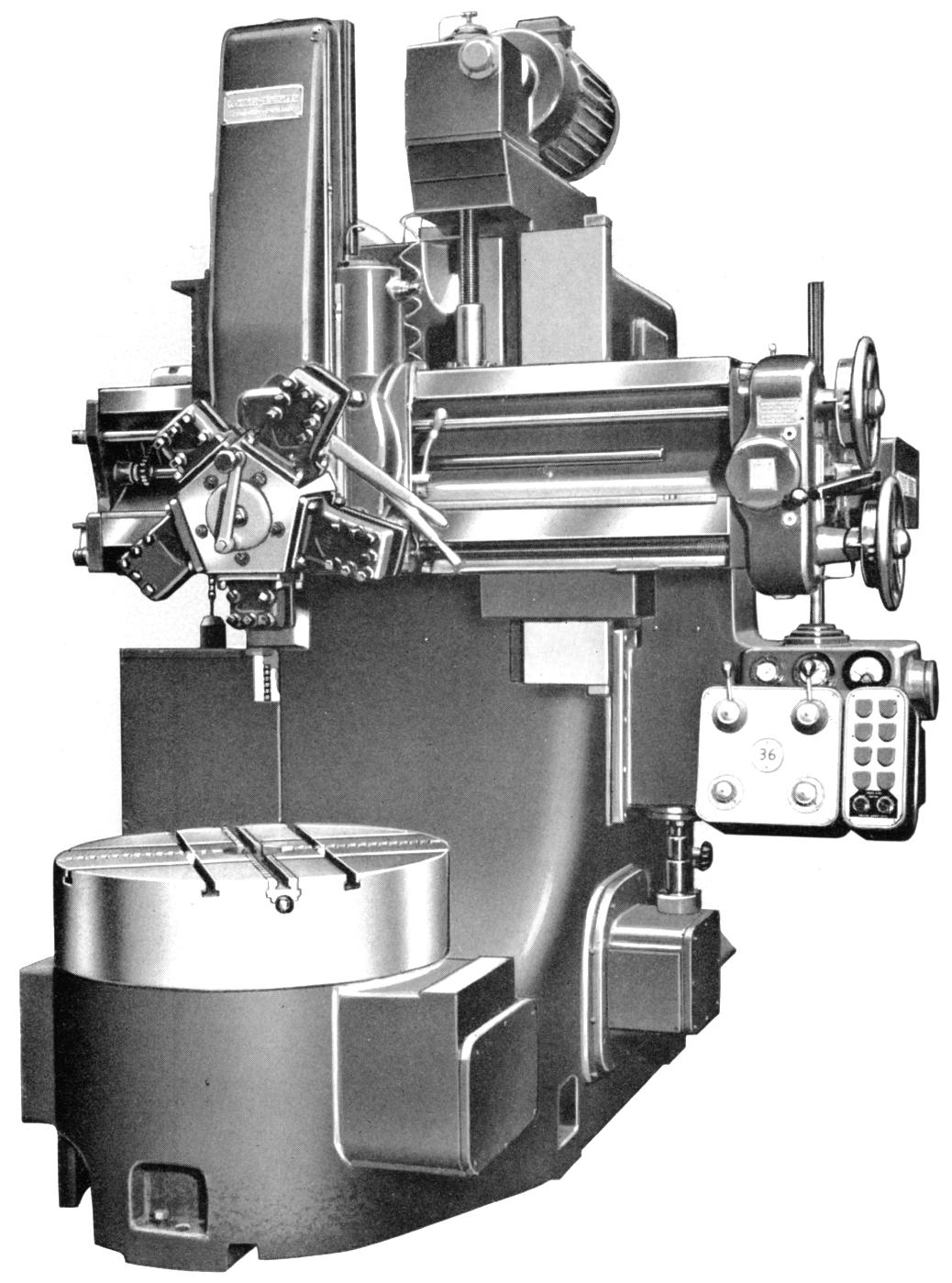 |
|
|
|
|
|
|
|
|
Standard 30-inch Series 2 Model EH Single with its elevating cross slide
|
|
|
|
|
|
|
|
|
|
|
|
|
|
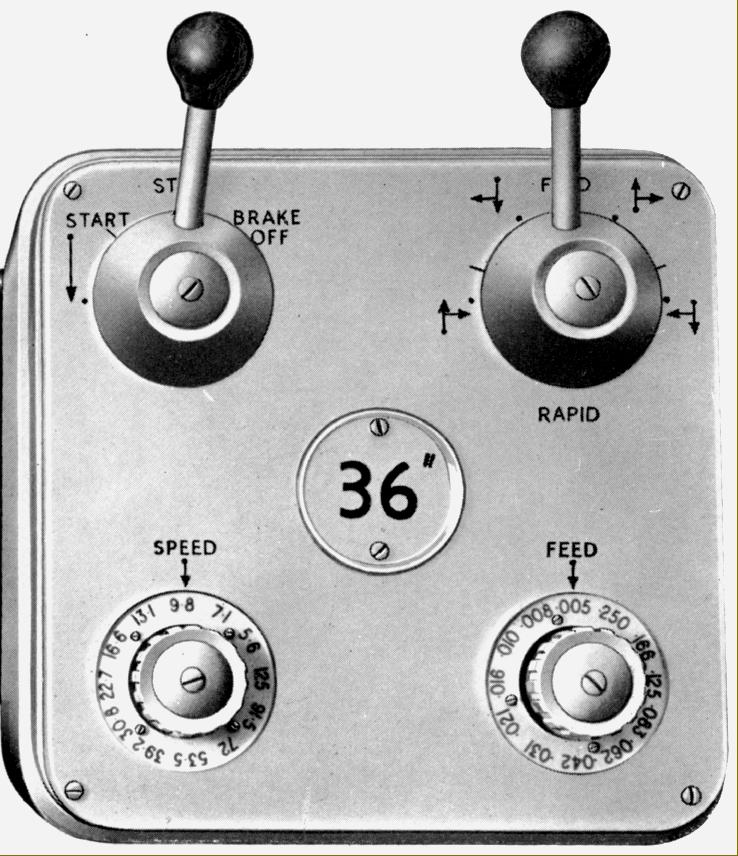 |
|
|
|
|
|
|
|
|
|
|
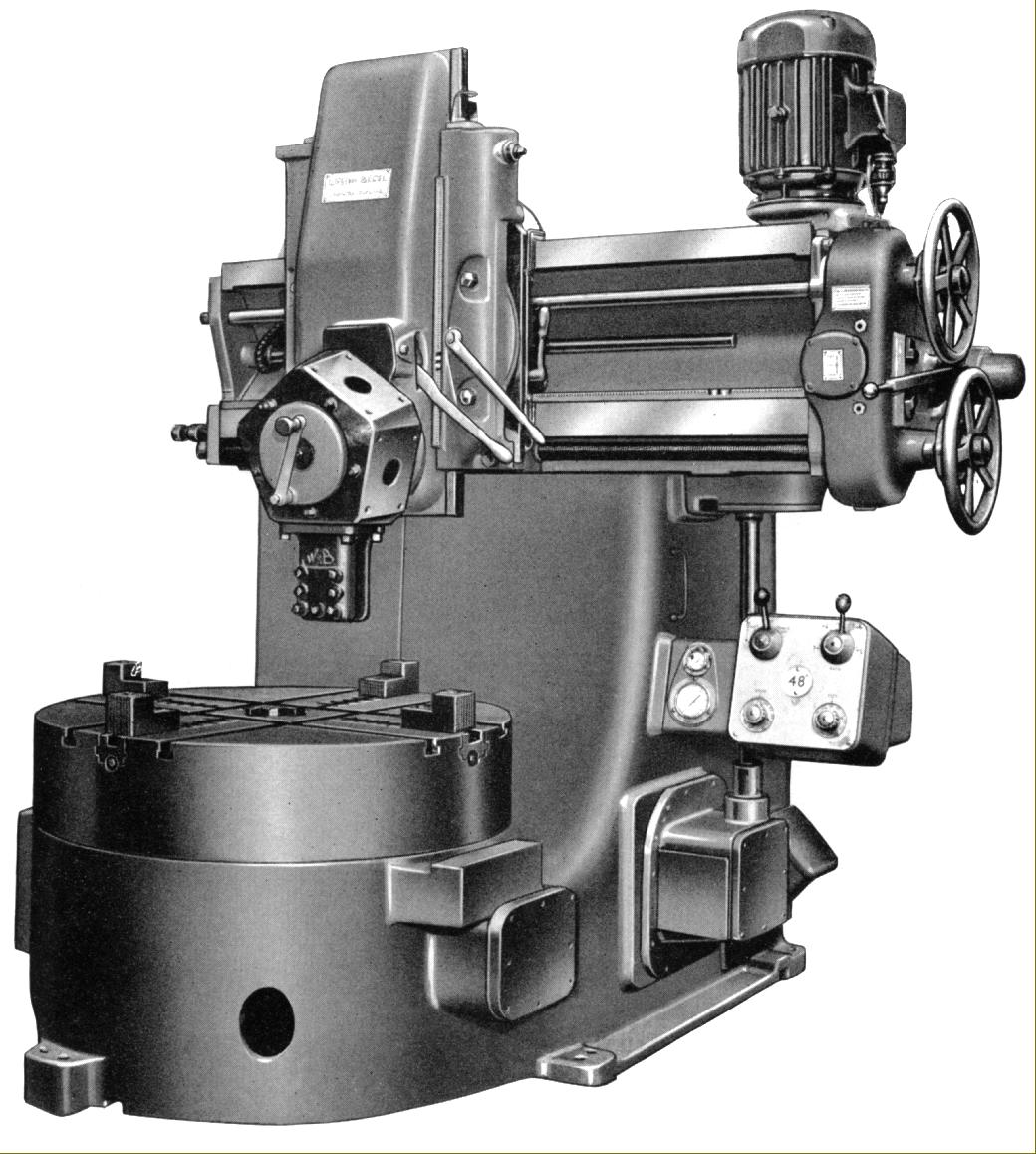 |
|
|
|
|
|
|
|
|
Standard 48-inch Series 2 Model DH Single
|
|
|
|
|
|
|
|
|
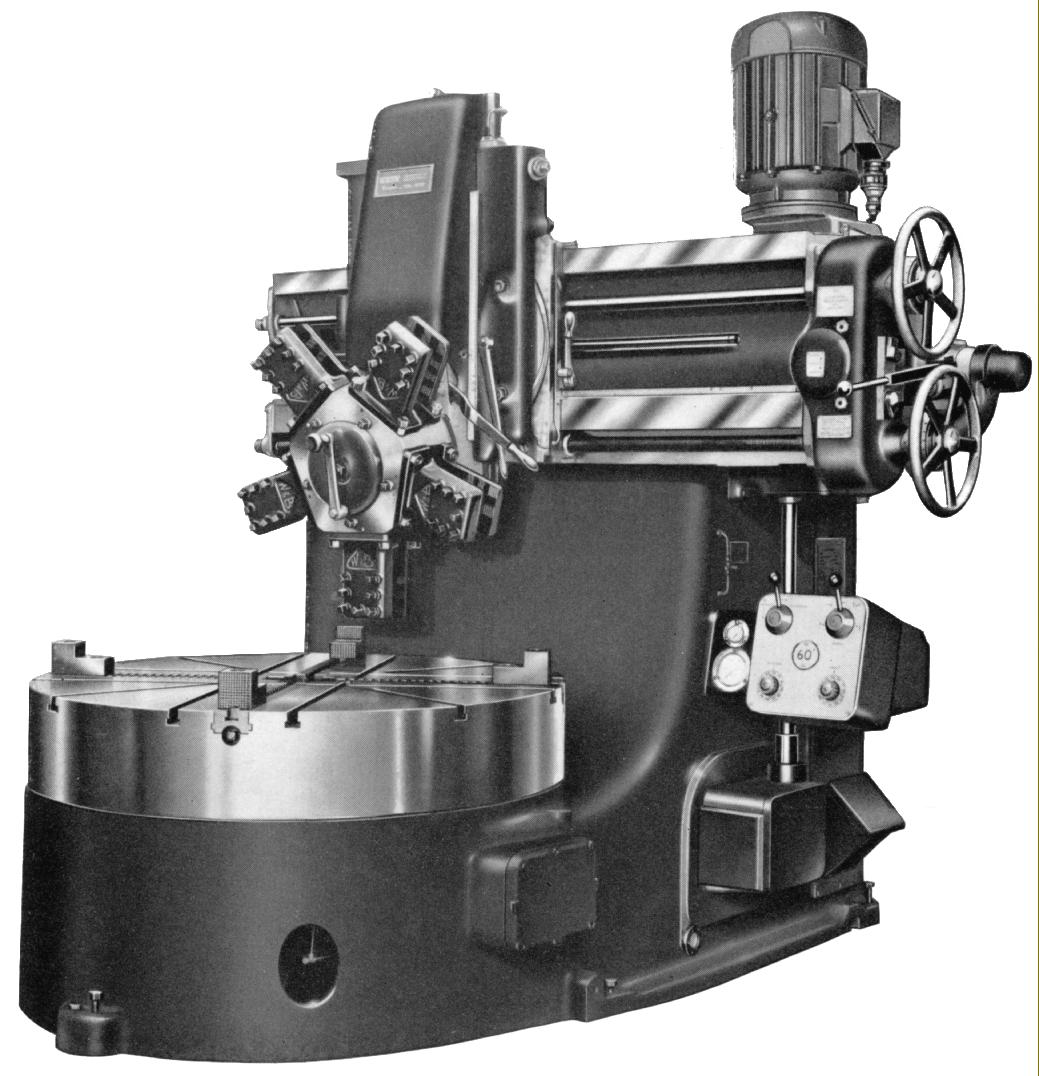 |
|
|
|
|
|
|
|
|
Standard 60-inch Series 2 Model DH Single
|
|
|
|
|
|
|
|
|
|
|
|
|
|
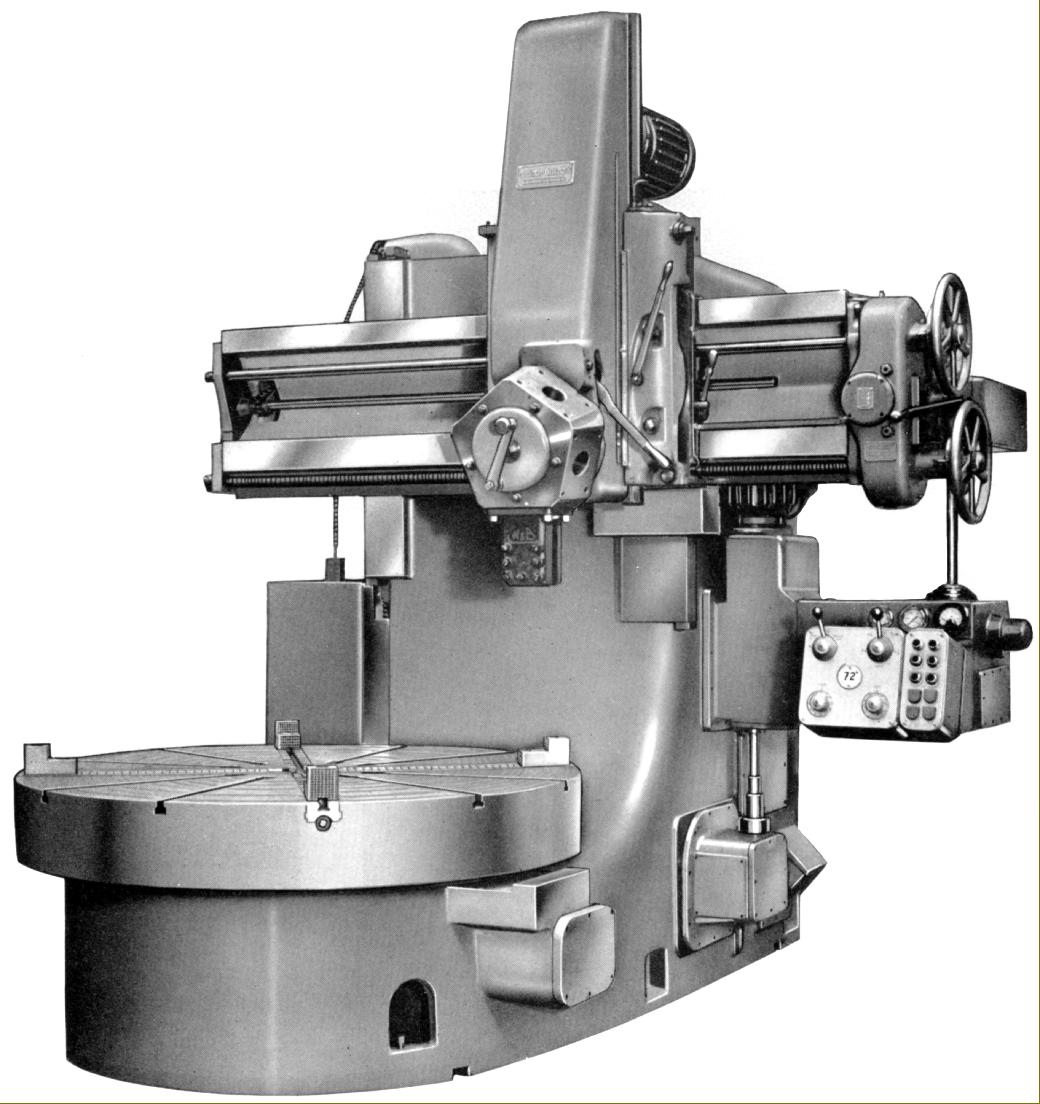 |
|
|
|
|
|
|
|
|
Standard 72-inch Series 2 Model EH with elevation cross rail
|
|
|
|
|
|
|
|
|
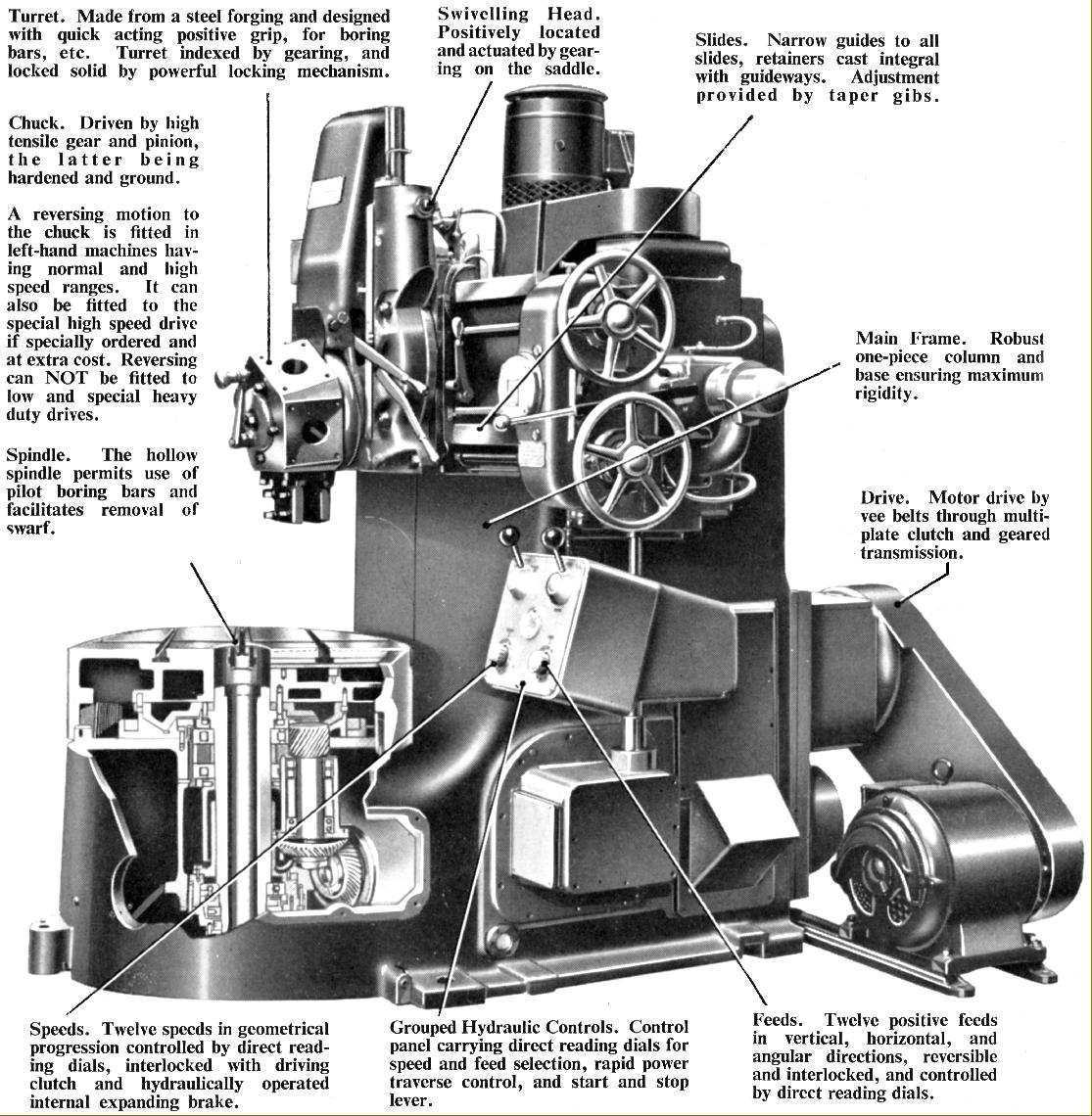 |
|
|
|
|
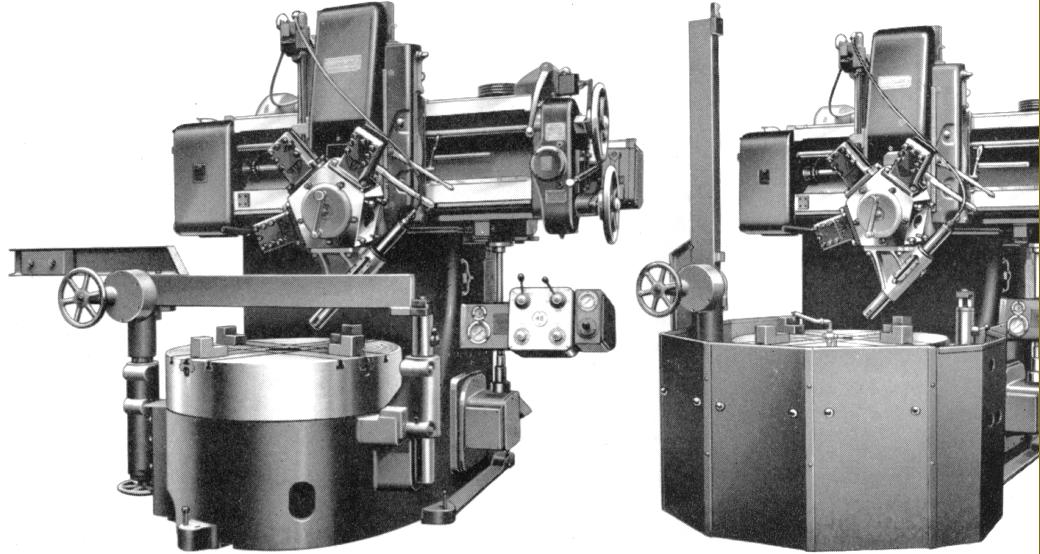 |
|
|
|
|
|
|
|
|
A copying bean was available: shown left in its working position and, right, parked.
|
|
|
|
|
|
|
|
|
|
|
|
|
|
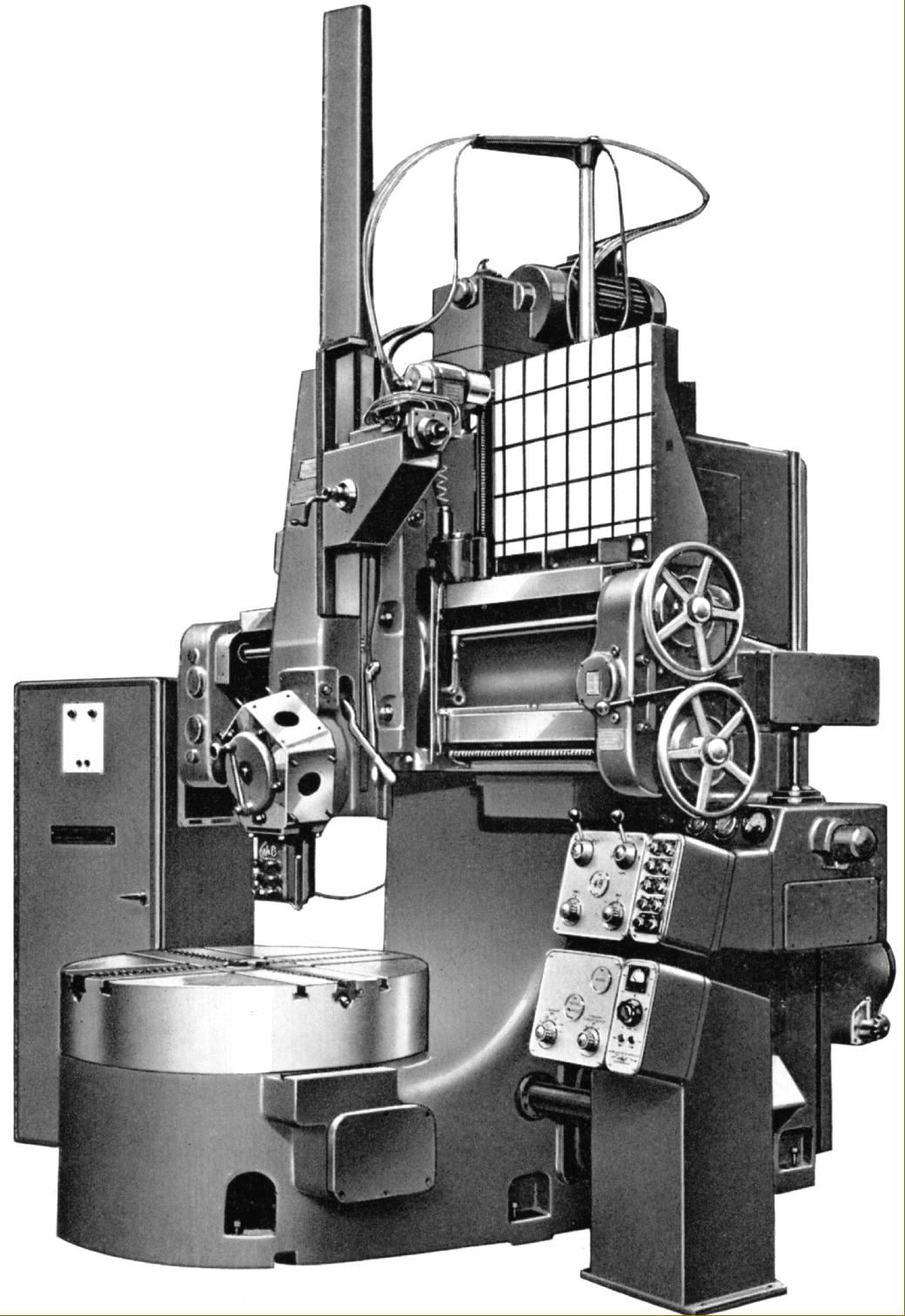 |
|
|
|
|
|
|
|
|
48-inch Series 2 Model EH Single with electronically controlled copying
|
|
|
|
|
|
|
|
|
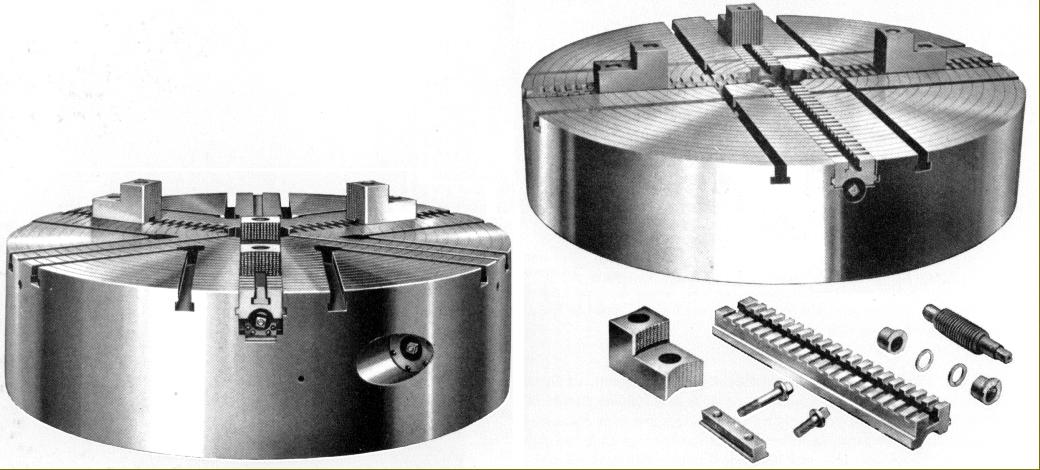 |
|
|
|
|
|
|
Two types of manually operated chucks were offered: an independent 4-jaw and a self-centring 3-jaw. Both came in a range of sizes, had bodies (and all other fittings) in a hardened and ground steel and each was equipped with T-slots for the mounting of special fixtures. When a machine was intended for continuous or batch production, hydraulic clamping of the jaws could be fitted, power being supplied by a separate motor-driven pump unit.
|
|
|
|
|
|
|
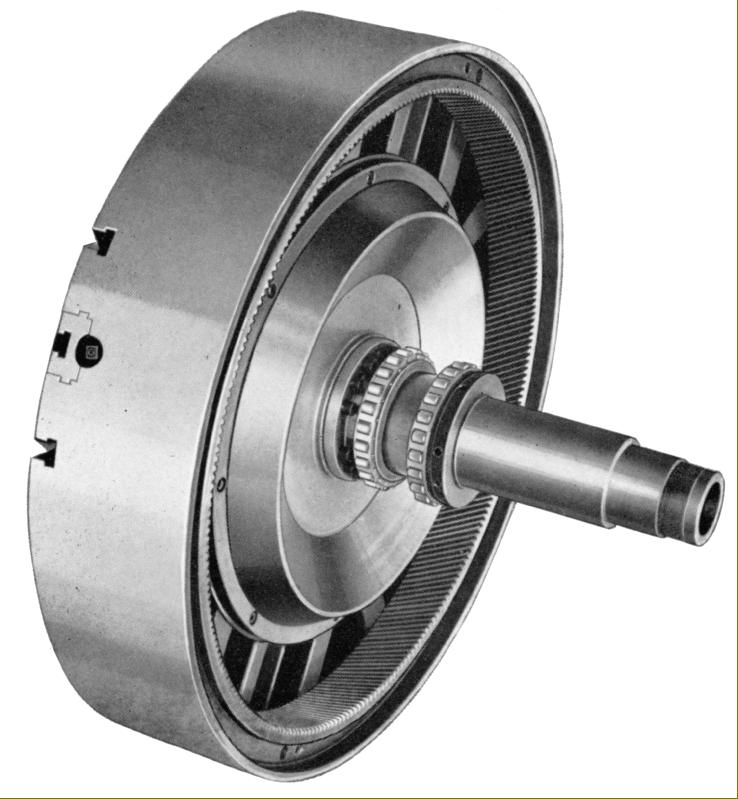 |
|
|
|
|
|
|
Larger models in the 48-inch, 60-inch and 72-inch sizes had their work-holding chuck carried on a forged steel spindle supported in parallel roller bearings for radial loads with thrust taken, in this case, by a large diameter, pressure lubricated plain bearing of the conical type. However, depending upon the speed range and class of work for which the machine was intended, a flat version was also manufactured
|
|
|
|
|
|
|
|
|
|
|
|
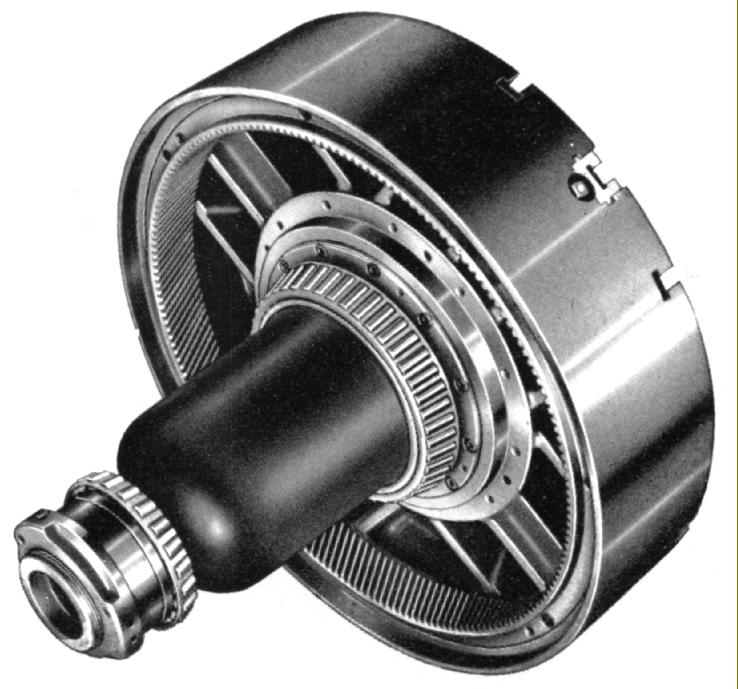 |
|
|
|
|
The chuck on the smallest model was carried on a large diameter spindle in a Meehanite cast iron. Taper roller bearings that carried both radial loads and the considerable vertical thrust. In this example the internal drive gear was formed on the inside wall of the chuck
|
|
|
|
|
|
|
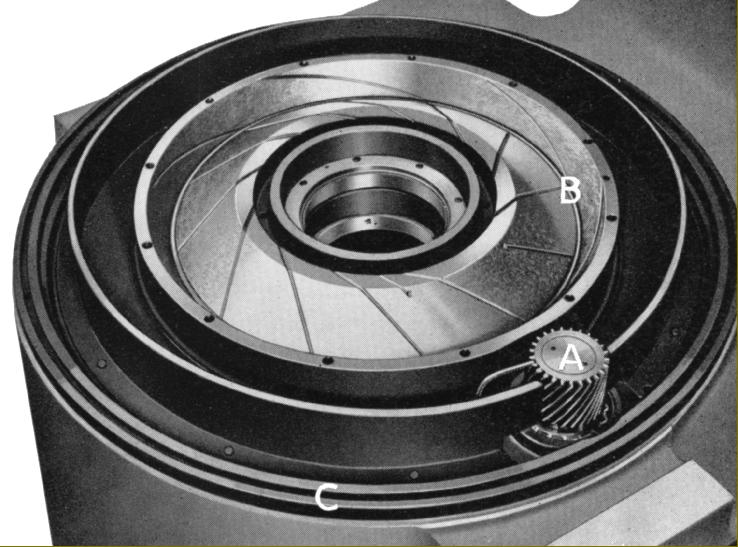 |
|
|
|
|
|
|
Underside of a late-type work-holding chuck showing: A the hardened and ground drive pinion; B the chuck seating, to take vertical thrust, in the form of a conical seating lubricated under pressure and fitted with a gauge. An alternative fitting was a flat thrust face, also pressure lubricated; C the chuck rim, formed so as to exclude coolant and swarf
|
|
|
|
|
|
|
|
|
|
|
|
|
|