 |
 |
 |
 |
 |
 |
 |
 |
 |
 |
 |
 |
 |
 |
 |
 |
 |
 |
 |
 |
 |
 |
 |
 |
 |
 |
 |
 |
 |
 |
 |
 |
 |
|
|
|
|
|
|
|
|
|
|
|
|
|
|
|
|
|
|
|
|
|
|
|
|
|
|
|
|
|
|
|
|
|
|
|
|
|
|
|
|
|
|
|
|
|
|
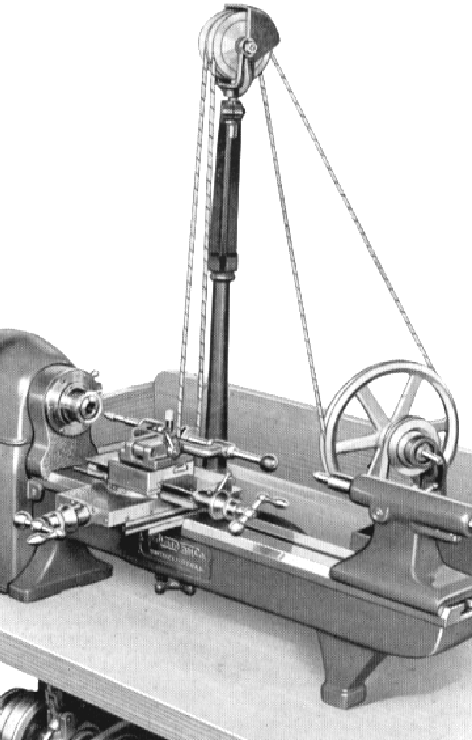 |
|
|
|
|
|
|
Auxiliary Drive For Toolpost Mounted Attachments
|
|
|
|
|
|
|
|
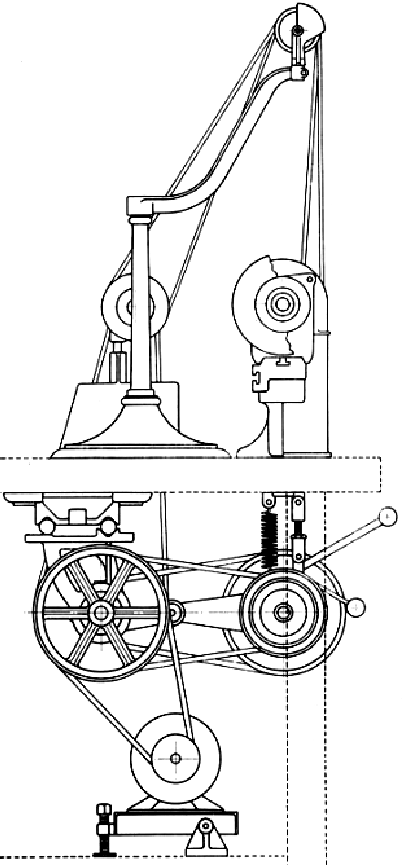 |
|
|
|
|
|
|
|
|
|
Countershaft drive unit complete with an "overhead" to run toolpost-mounted high-speed grinding and milling spindles.
|
|
|
|
|
|
|
|
|
|
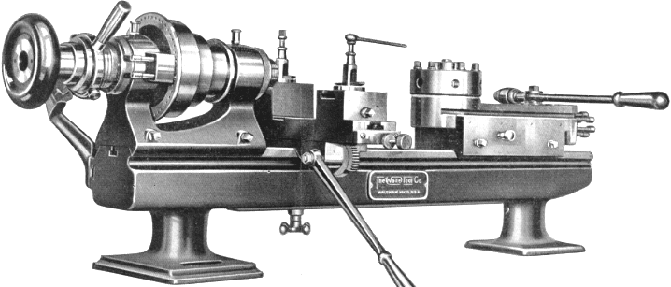 |
|
|
|
|
|
|
Early Wade Precision Bench Lathe set up for production work. The Turret Attachment had six holes of 5.8" diameter, indexed automatically and had a working travel of 3" plus an indexing travel of 1.25" - giving a total movement of 4.25". The Double Cross Slide had a movement of 2" and used either standard tool holders or special ones made in a circular form. The Swivel Slide (illustrated below) could be used in place of the front block, and accepted the standard tool post.
|
|
|
|
|
|
|
|
|
|
|
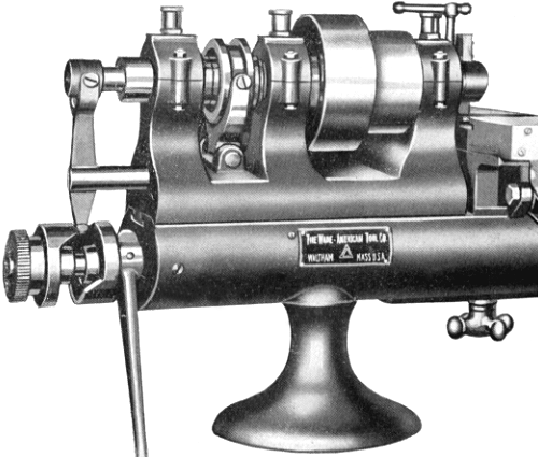 |
|
|
|
|
|
|
The Three-bearing Headstock was designed for production work. This was a sturdily-built unit with a full-length mounting on the bed, not a mere extension to the length of the casting. The device was intended to overcome the inherent tendency of collets to draw work backwards when they were tightened, making it difficult to obtain exactly depth setting on repetition work. In this design the collet remained "stationary" whilst, ingeniously (and in a similar manner to that used on German Lorch lathes) the headstock spindle moved forwards and backwards to tighten and release it. In this case the mechanism is shown with a "wire-feed" arrangement whereby the stock to be turned was drawn into the spindle by the same movement of the lever that opened and closed the collet. An interesting comparison can be made with the Ames unit illustrated here.
|
|
|
|
|
|
|
|
|
|
|
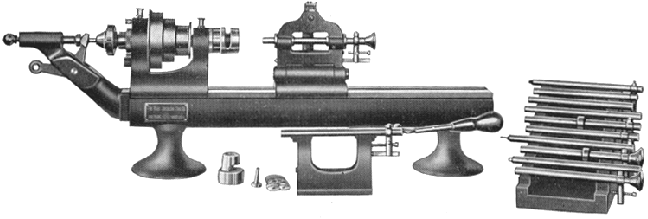 |
|
|
|
|
|
|
An adaptation of the "half-open" tailstock, a traditional accessory for Precision Bench Lathes and often employed in factories where they were used for semi-mass production processes which required only very light machining operations. The casting was "open" to facilitate rapid changes of spindle, of which a set would be kept by the machine, each equipped with a different tool. The spindles could be pushed by hand, or with a lever. The set up illustrated shows a boring operation on clock wheels (where the central hole is being bored true to the circumference after the gears are cut) using, in this case, a special jewelling rest and balloon head.
|
|
|
|
|
|
|
|
|
|
|
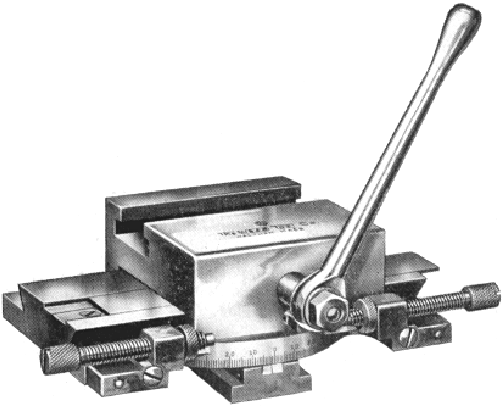 |
|
|
|
|
|
|
The Wade Lever-operated Swivel Slide was manufactured for many years and could be fitted to a variety of single, double and compound slide rests.
|
|
|
|
|
|
|
|
|
|
|
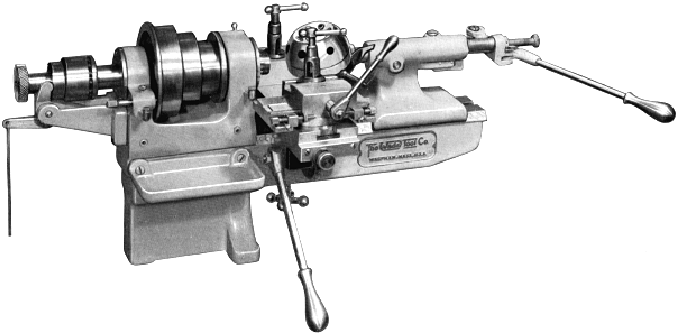 |
|
|
|
|
|
|
Short-bed production model (21-inches long) with lever-operated slides and tailstock-mounted hand-indexed capstan unit.
|
|
|
|
|
|
|
|
|
|
|
|
|
|
|
|
|
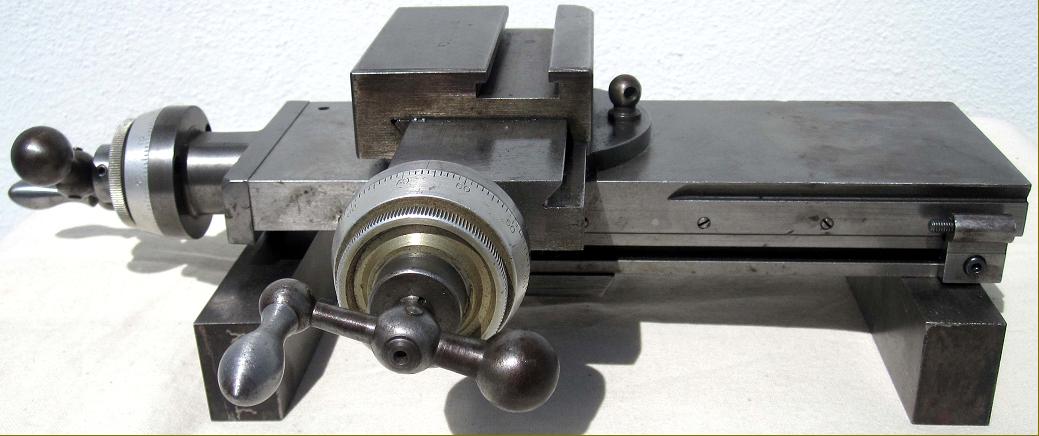 |
|
|
|
|
|
|
The beautifully constructed Wade compound slide rest
|
|
|
|
|
|
|
|
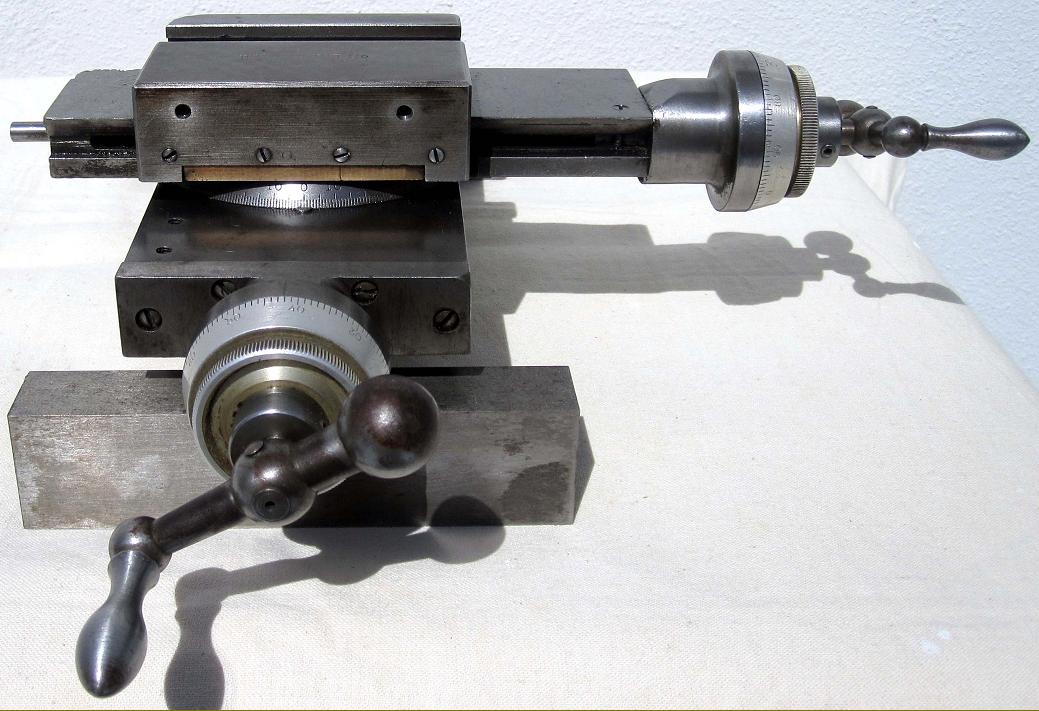 |
|
|
|
|
|
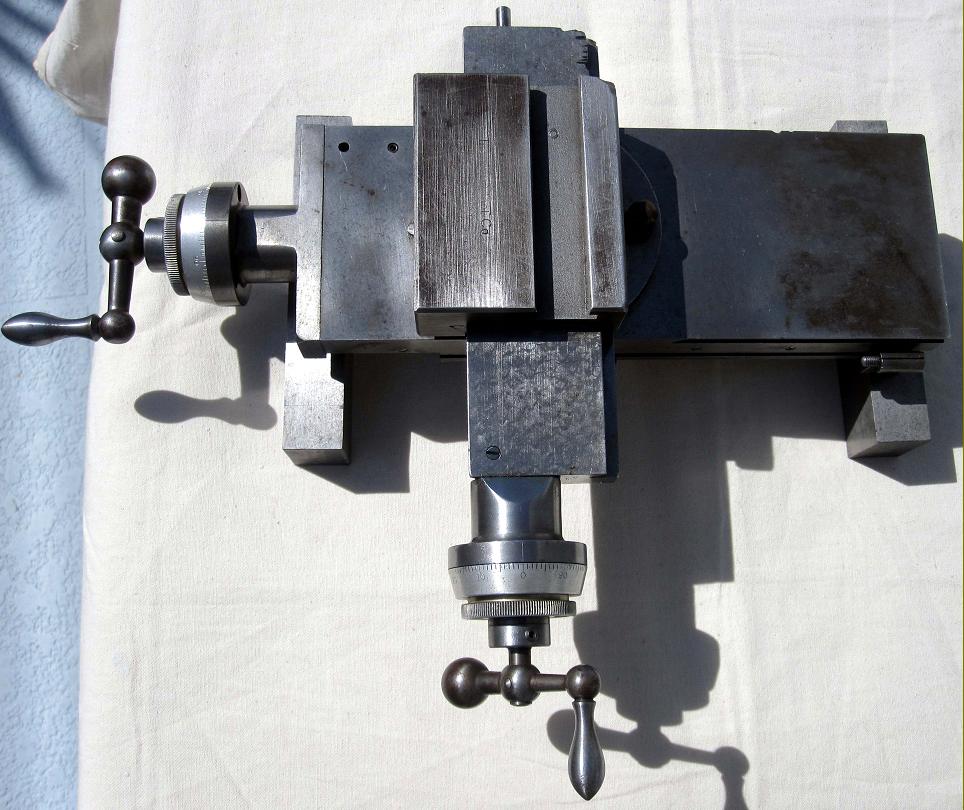 |
|
|
|
|
|
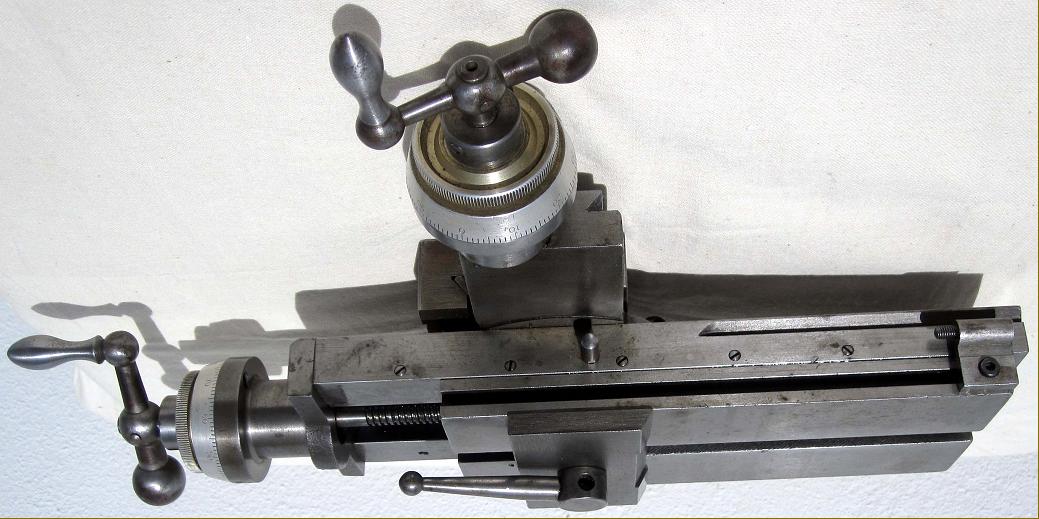 |
|
|
|
|
|
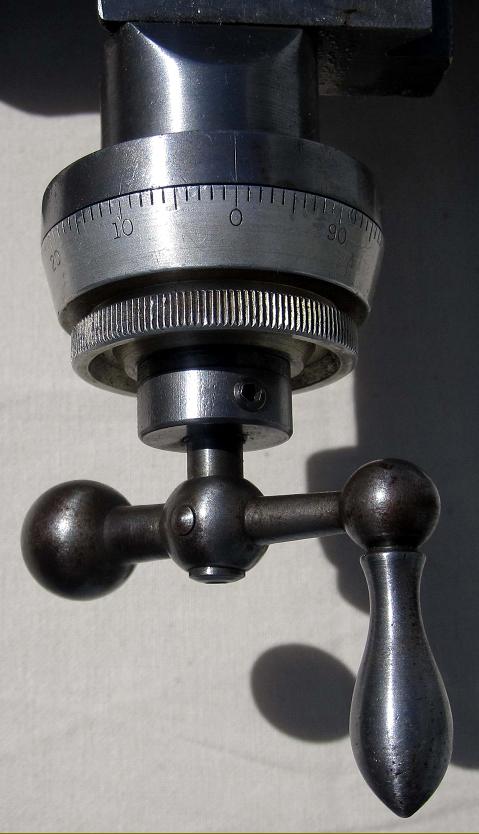 |
|
|
|
|
|
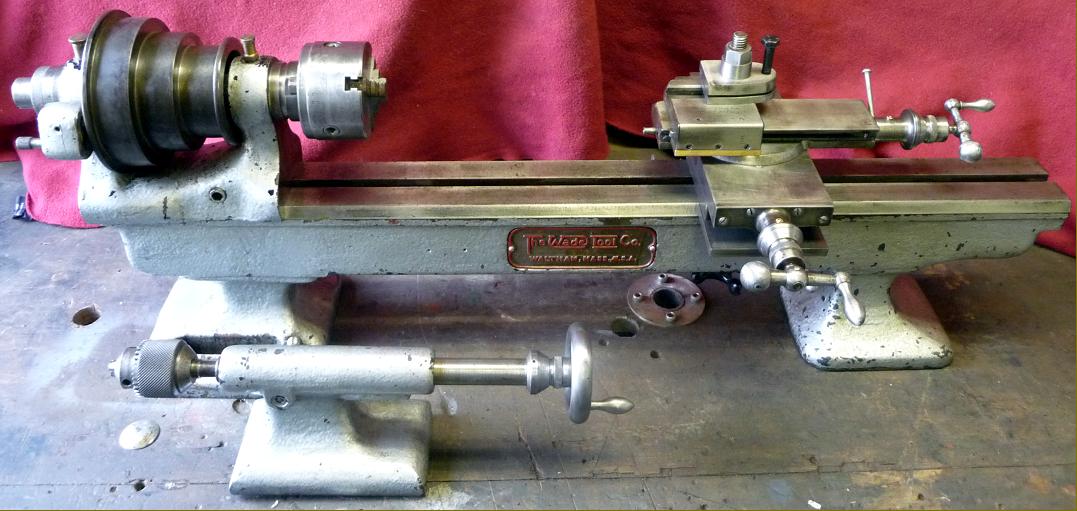 |
|
|
|
|
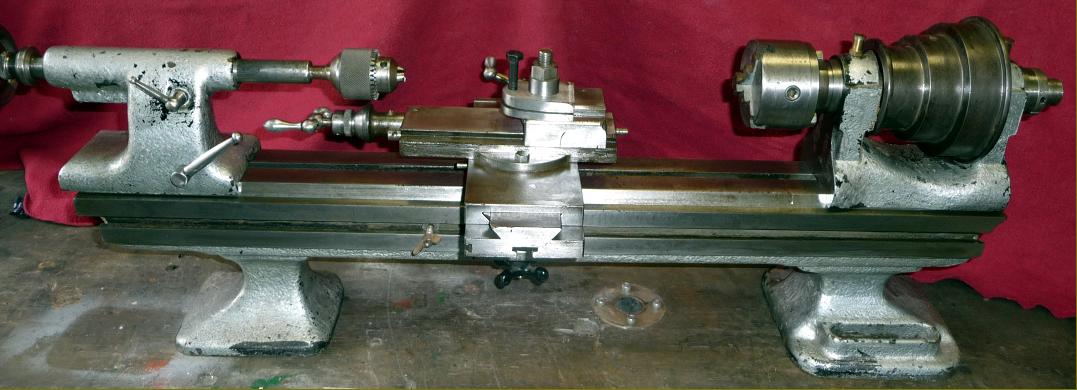 |
|
|
|
|
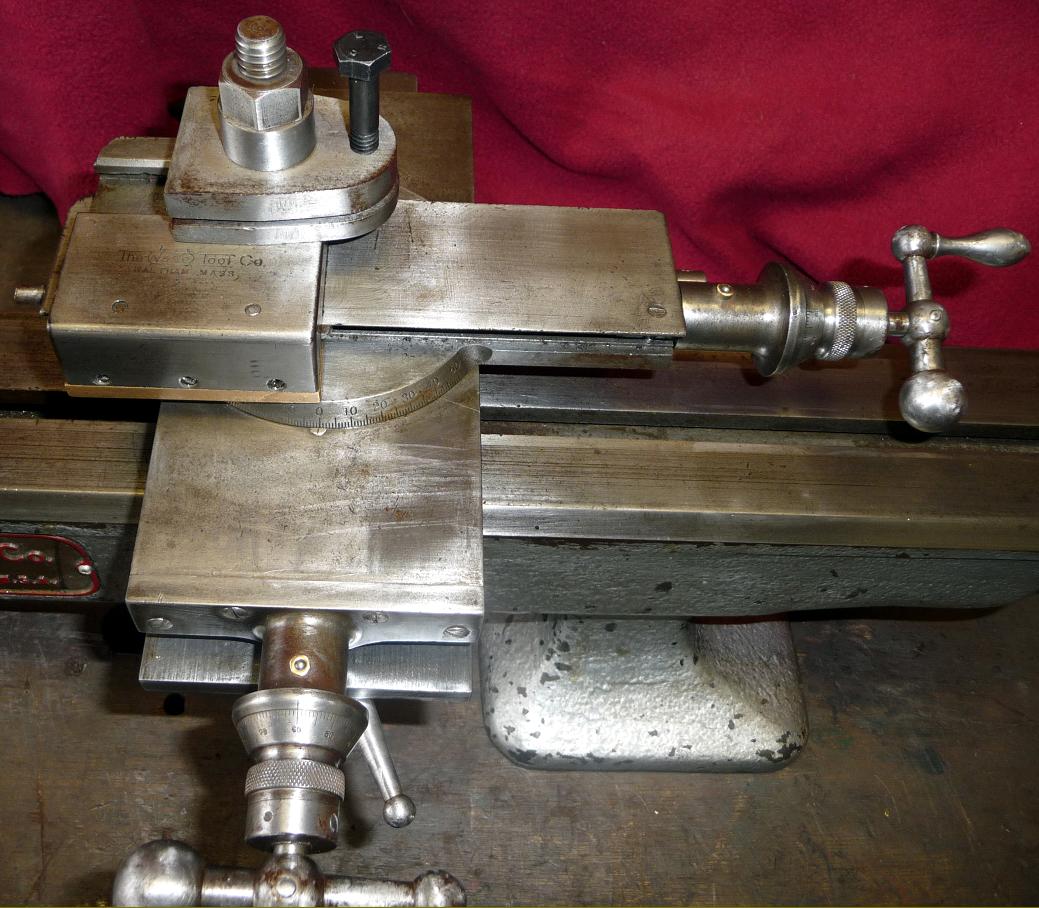 |
|
|
|
|
|
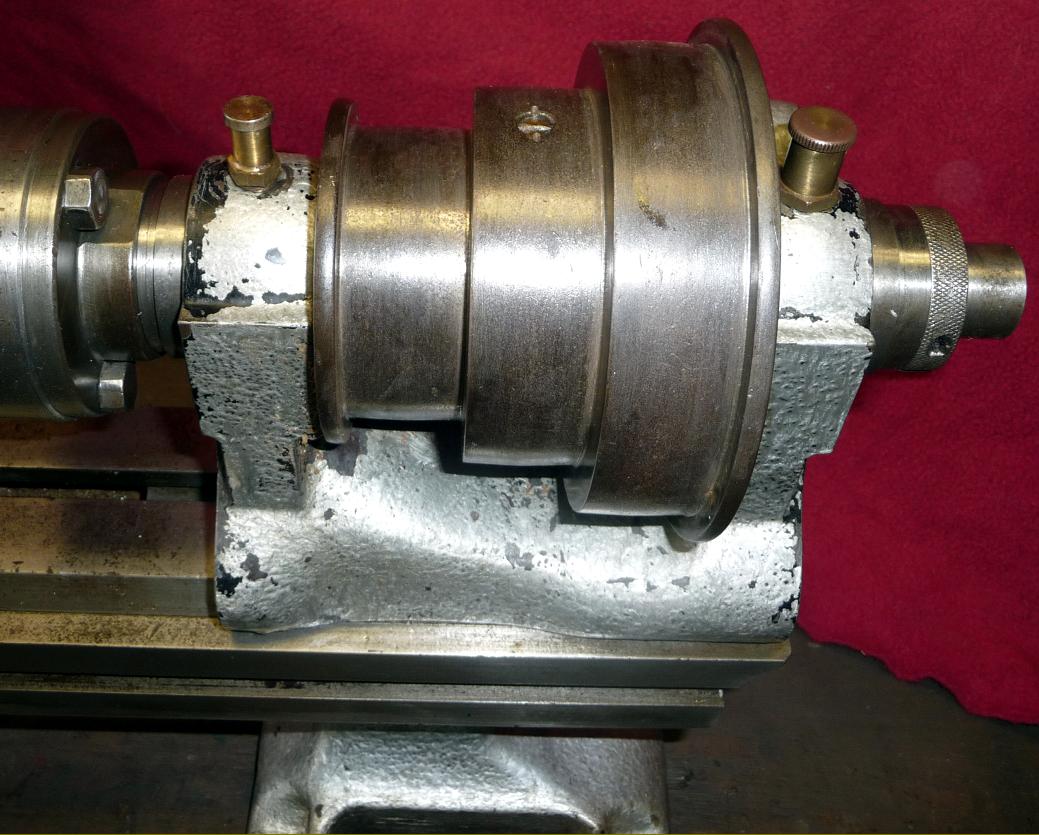 |
|
|
|
|
|
|
|
|
|
|
|
|
|