 |
 |
 |
 |
 |
 |
 |
 |
 |
 |
 |
 |
 |
 |
 |
 |
 |
 |
 |
 |
 |
 |
 |
 |
 |
 |
 |
 |
 |
 |
 |
 |
 |
|
|
|
|
|
|
|
|
|
|
|
|
|
|
|
|
|
|
|
|
|
|
|
|
|
|
|
|
|
|
|
|
|
|
|
|
|
|
|
|
|
|
|
|
|
|
|
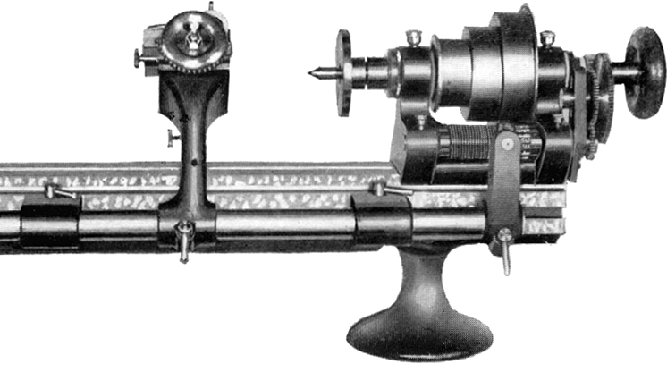 |
|
|
|
|
|
|
Rear view of a very early Wade Precision Bench Lathe fitted with Chase screwcutting. The headstock casting was a special unit with lugs at the back to carry the Master Thread.
|
|
|
|
|
|
|
|
|
|
|
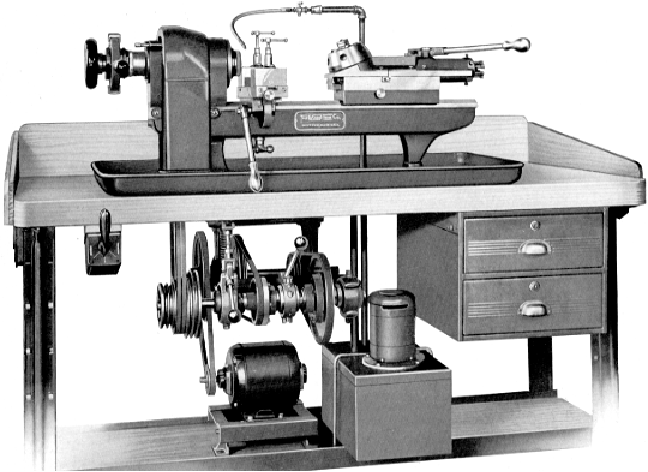 |
|
|
|
|
|
|
|
|
|
Described by Wade as their "Unit Motor Drive" the construction of the underdrive stands was unusual in that the main framework was fabricated from stampings; the top was a heavy lamination of wood, with the lathe sitting in a metal chip and coolant collection tray. The countershaft unit was designed to provide 6 forward and reverse speeds in geometric progression from 200 to 2000 rpm. The pulley system included clutches, built into the shafts, which were operated by a levers protruding more or less horizontally from the centre of the assembly. One clutch switched the drive between high and low ratios in a ratio of 4:1 whilst the other stopped and started the drive. A Simplified Motor Drive was also available which, while identical in layout to the above, lacked the clutches and had a narrower speed range.
|
|
|
|
|
|
|
|
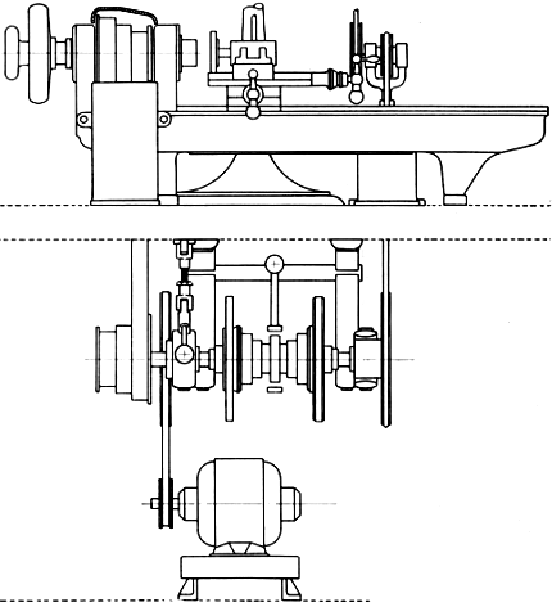 |
|
|
|
|
|
|
The countershaft assembly in this drawing, while similar to that in the photograph, has an auxiliary power take-off on the right-hand side that rose to drive an "overhead" used to power grinding, milling and drilling attachments held in the position normally occupied by the lathe's toolpost.
|
|
|
|
|
|
|
|
|
|
|
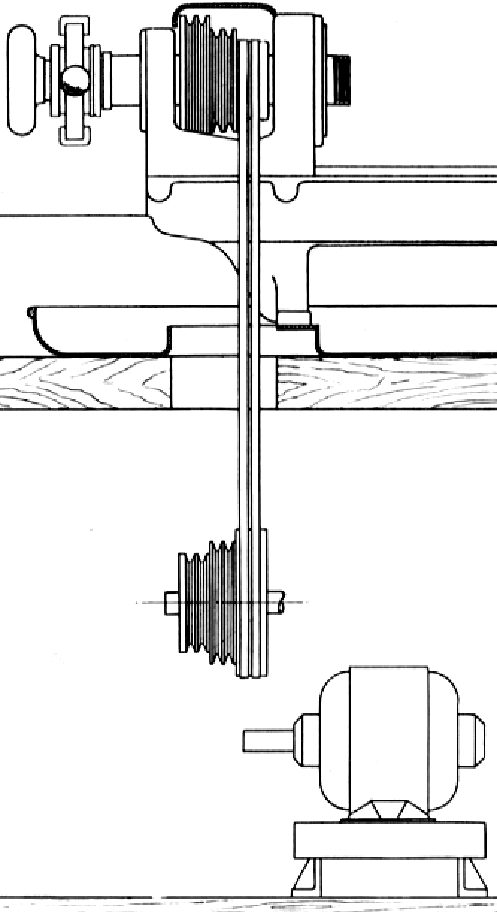 |
|
|
|
|
|
|
A variation in the drive available for the No. 7 lathe was the use of twin V belts for increased torque transmission. No method of slackening the belts seems to have been provided, but the makers claimed that "It has been found that these (V belts) can be shifted over the step cone pulley practically as easily as the flat belt." As the President said, it all depends what you mean by practically …..
|
|
|
|
|
|
|
|
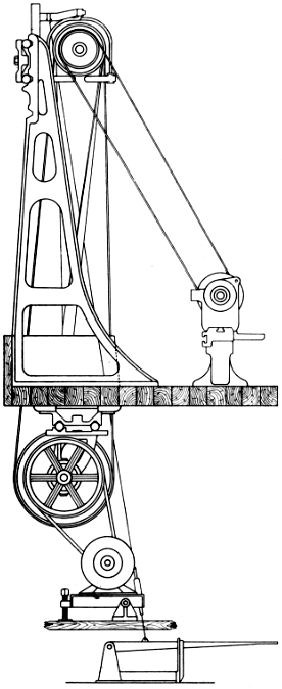 |
|
|
|
|
|
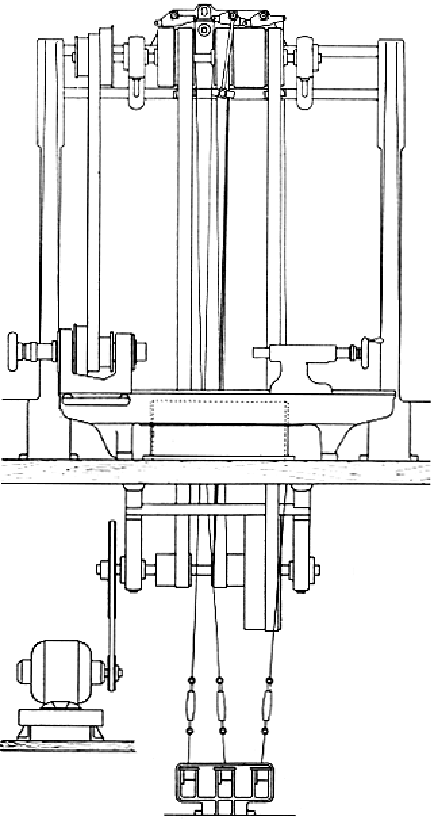 |
|
|
|
|
|
|
|
|
|
The Wade Overhead Countershaft is a good example of how complex and expensive lathe drive systems used to be before the development of compact, built-on drive units. The drive system started with an under-slung motor and an attendant pulley system which drove up to a large "fast-and-loose" pulley system carried on flamboyant cast-iron columns above the lathe - a similar arrangement can be seen here driving an 8A Toolmaker's lathe. Foot-operated pedals controlled the sliding of the belt from the "loose" idle pulley to the "fast" drive pulley - whilst a second drive, from the right-hand side of the underneath countershaft, gave a higher range of speeds. A third drive, again "fast-and-loose" pulley controlled, but from a twisted belt, produced reverse. The whole mass of cast iron, bearings, hanger brackets, belts, pedals, wires, belt-shifters, nuts, bolts, screws and washers provided just six forward speeds in geometric progression from 200 to 1750 rpm - and three in reverse.
|
|
|
|
|
|
|
|
|
|
|
|
|
|
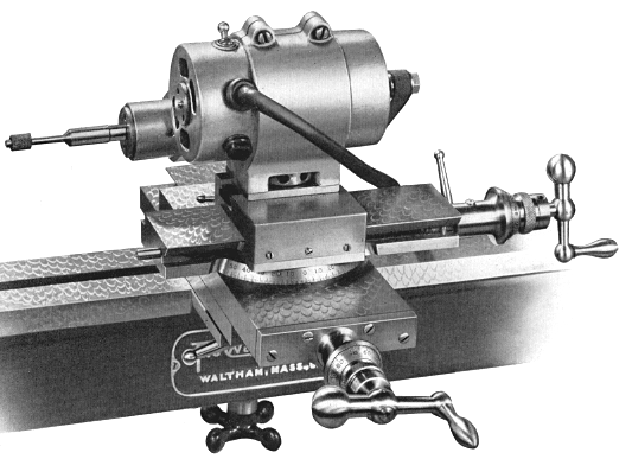 |
|
|
|
|
|
|
Grinding Attachment with integral motor drive
|
|
|
|
|
|
|
|
|
|
|
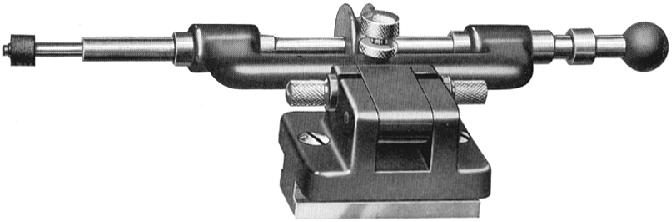 |
|
|
|
|
|
Internal Grinding Attachment
|
|
|
|
|
|
|
|
|
|
|
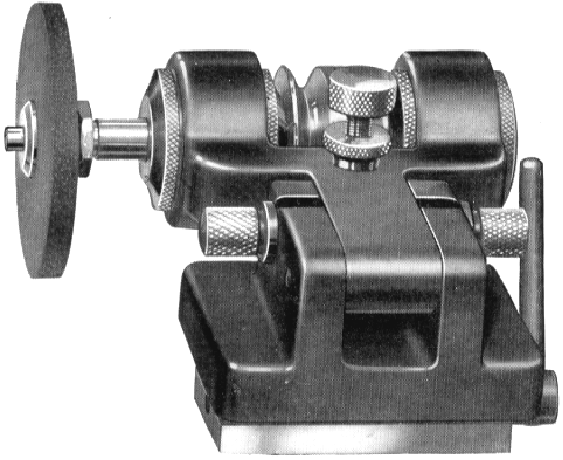 |
|
|
|
|
|
|
External Grinding Attachment
|
|
|
|
|
|
|
|
|
|
|
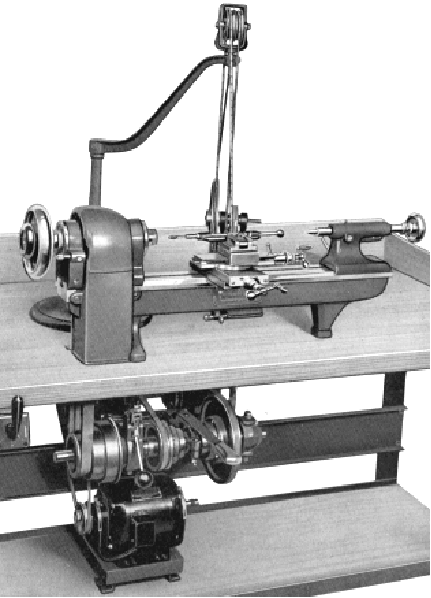 |
|
|
|
|
|
|
Wade Precision bench Lathe fitted to an "Underdrive" stand with an extension drive to an overhead Auxiliary Countershaft designed to power Grinders and High-speed Spindles held on the compound slide rest. Ball bearings were used throughout the assembly.
|
|
|
|
|
|
|
|
|
|
|
|
|
|
|