 |
 |
 |
 |
 |
 |
 |
 |
 |
 |
 |
 |
 |
 |
 |
 |
 |
 |
 |
 |
 |
 |
 |
 |
 |
 |
 |
 |
 |
 |
 |
 |
 |
 |
 |
 |
 |
 |
 |
 |
 |
 |
 |
 |
 |
|
|
|
|
|
|
|
|
|
|
|
|
|
|
|
|
|
|
|
|
|
|
|
|
|
|
|
|
|
|
|
|
|
|
|
|
|
|
|
|
|
|
|
|
|
|
|
|
|
|
|
|
|
|
|
|
|
|
|
Taylor Model 626 Trimming and Beading Lathe. This lathe was designed for finishing off products that had been stamped out in a "Drawing Press". When the job was removed from the press an uneven flange of waste material was left around the periphery that needed to be cut off; following that operation the lathe could be used with another tool to curl over the newly-trimmed edge whilst simultaneously binding in a length of wire to stiffen it.
|
|
|
|
|
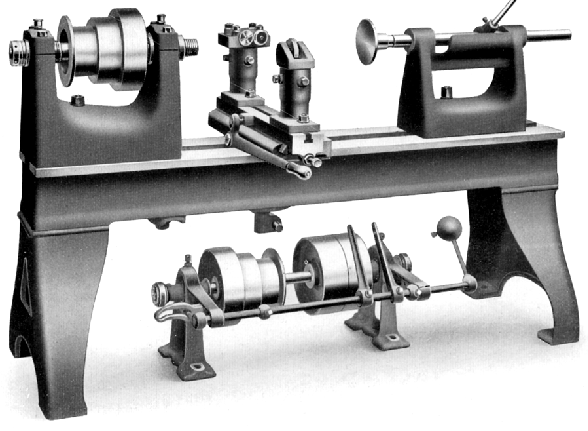 |
|
|
|
|
|
|
|
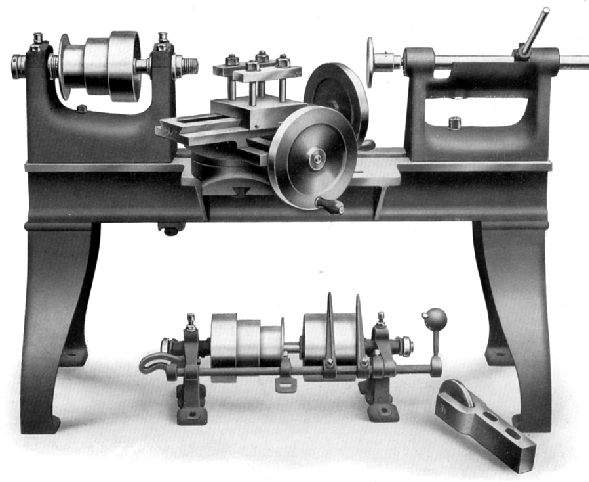 |
|
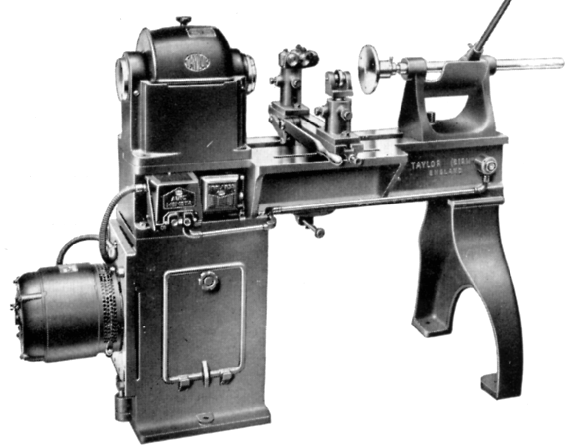 |
|
|
|
|
|
Taylor Model 1417 circa 1945. The first Beading and Trimming lathe to be mounted on a self-contained underdrive stand.
|
|
|
|
|
|
|
|
|
|
Taylor Rolling Lathe Model 633 of the 1920s. This machine was intended for smoothing out the wrinkles often left in work that had been through a Drawing Press. Turned with enough energy the large, heavy handwheels of the compound slide rest enabled a degree of "flywheel effect" to be built up so aiding the evening-out process.
|
|
|
|
|
|
|
|
|
|
|
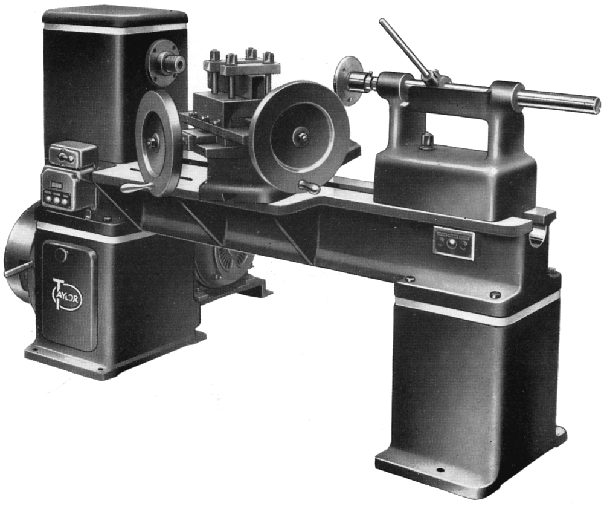 |
|
|
|
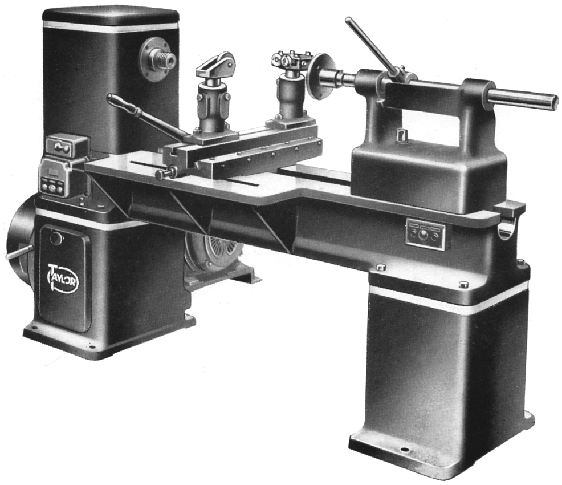 |
|
|
|
|
|
|
Taylor Model 1568 Trimming & Beading lathe. This adaptation of the spinning lathe was designed for finishing off products that had been stamped out in a "Drawing Press". When the job was removed from the press an uneven flange of waste material was left around the periphery that needed to be cut off; following that operation it was usual to curl over the clean edge to form a bead - sometimes with a wire insert - to stiffen it.
|
|
|
|
|
|
|
|
|
|
Taylor Rolling Lathe - 1950s to the 1970s - heavy plinths under both headstock and tailstock ends of the bed and an improved drive system - but the unique compound slide rest remained unchanged.
|
|
|
|
|
|
|
|
|
|
|
|
|
|
|
|
|
|
|
|
|
|
|
|
Taylor Brass-finishers' Lathes
Brass-finishers' was an old-fashioned term used to describe a particular class of simple, plain-turning lathe that could be used for machining and screwing all manner of brass articles by means of hand tools against a T rest or (sometimes) with the aid of an un-calibrated but rugged compound slide rest. Brass can be turned relatively easily with a sharp tools (and a modicum of skill) and the material was once widely used for the hundreds of small, everyday items that today would be moulded in plastic. The lathes were not in any way sophisticated but just well-built, reliable and easily-adjusted workhorses that could absorb thousands of hours of rough use by piece-work operators trying to put shoes on their children's feet and the occasional jam or butter on the family's daily bread..
|
|
|
|
|
|
|
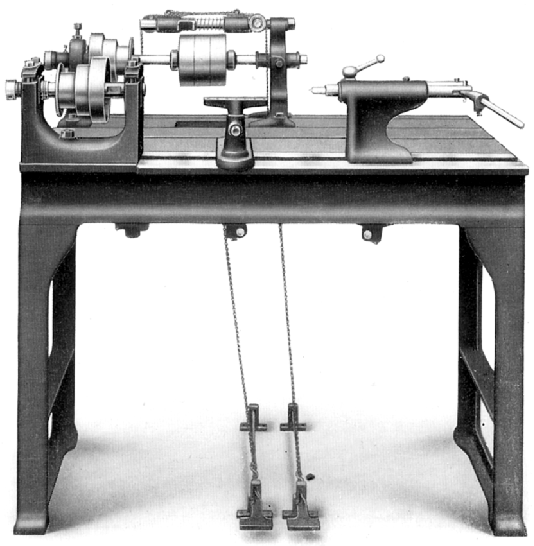 |
|
|
|
|
Taylor Models K16 and K17 41/2-inch and 61/2-inch Brass-finishers' Reversing lathe on the maker's cast-iron stand. Taylor's claimed some improvements for this machine in comparison with their earlier designs: the headstock of both lathes carried a hardened and ground spindle running in bronze bearings with "collars" in gun-metal on the smaller machine and hardened steel on the larger. Thrust was taken out using ball-races against the inside of the left-hand bearing, a design that the company claimed would not, " heat up under heavy pressure." The stand was simple, but interesting; instead of the usual splayed legs (against which workers could trip) these were arranged to be a straight as possible and to project no further forwards than the front edge of the bed; the aim was to give as much clearance in narrow gangways as possible and, to further this ideal, if several lathes were to be mounted next to each other the beds were machined on their ends so that they bolted together and, then, to save money, mounted in pairs on strengthened legs. To aid stability and rigidity the lathes were bolted not only to each other but also both the floor and wall as well - as shown in the picture below and in a sectional drawing here. The 'fast-and-loose' countershaft was designed for quickness of use and operated by two foot pedals that controlled which of two belts, each running in opposite directions on 'loose' pulleys, was to be flicked across to engage the central 'fast' (drive) pulley. Each foot pedal had a catch that enables it to be locked down when a long cut was being taken, yet to release it only a tap with the foot against its side was needed. The selector shaft that moved the belts could be mounted either on the top of the stand (as shown in the picture above) or bolted to the wall or ceiling; missing from the picture are the two belt-shifting claws that would normally have been carried by the selector unit..
|
|
|
|
|
|
|
|
|
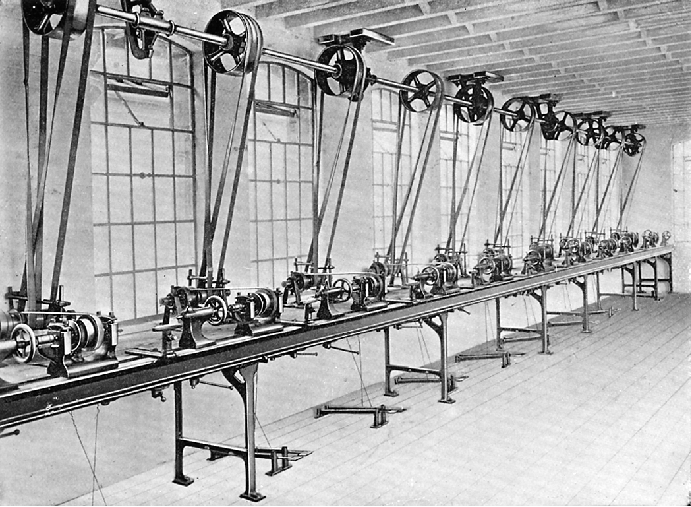 |
|
|
|
|
A set of Taylor "reversing" spinning lathe set up in pairs with their beds joined end to end and stands bolted to both floor and wall (in preparing the picture for publication the graphic artist painted out the joints between the individual beds). Two belts connected each lathe to the overhead line shafting; one belt was set for direct drive the other was "crossed" to reverse the direction of rotation. A sectional drawing of the multi-lathe arrangement can be seen here.
|
|
|
|
|
|
|
|
|
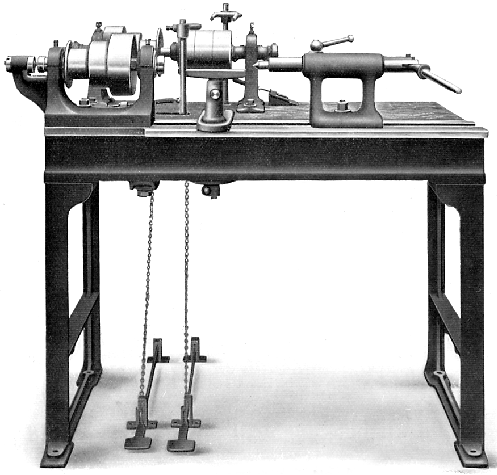 |
|
|
|
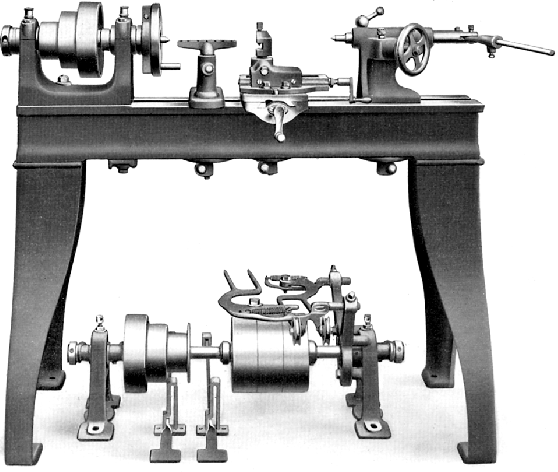 |
|
|
|
|
|
|
Taylor Model 460 61/2-inch Brass-finishers' lathe with compound slide rest and either 13/16" or 1 3/8" hole through the spindle and an externally threaded nose. The tailstock was unusual in carrying an expensive-to manufacture and complex arrangement whereby the barrel could be moved by either a lever or a screw thread. This lathe could double both a brass-finishers' lathe and a general-purpose plain-turning machine for simple jobs.
|
|
|
|
|
|
|
Taylor Model Y4 (bench countershaft) and Y5 (separate countershaft) 7-inch centre height heavy-duty reversing brass-finishers' lathe. These lathes were heavier and of a more sturdy constructed than the K16 and K17 Models (above) and fitted with high-speed cone-bearing headstocks with the end thrust of the internally-threaded (1-inch Whitworth) spindle taken out by the (old-fashioned) method of a hardened end cap bearing against a bracket bolted to the left hand face of the casting.
|
|
|
|
|
|
|
|
|
|
|
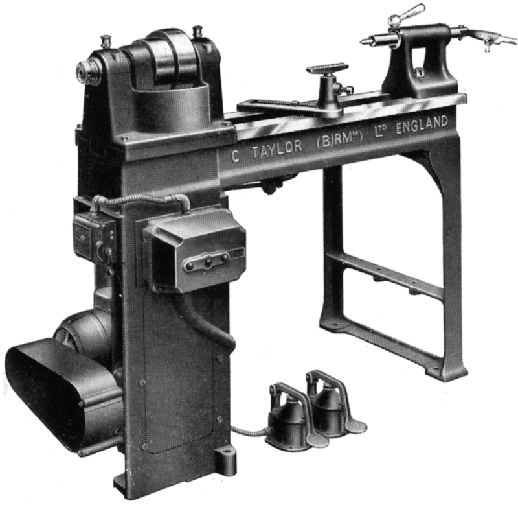 |
|
|
|
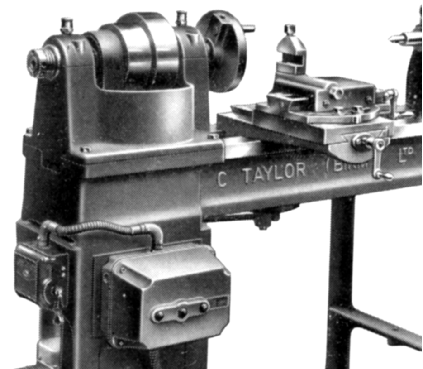 |
|
|
|
|
|
|
|
|
Model 1376 - an early under-drive brass-finishers' lathe with compound slide rest.
|
|
|
|
|
|
|
Taylor Model 1375 - the first of the brass-finishers' under-drive lathes was advertised alongside the early open-headstock models. Surprisingly the stand used was not the same as that employed on the first under-drive spinning lathes but had an L-shaped headstock-end plinth with the left-hand side and back cut away. The reverse was electrical and controlled by two foot switches between the stand's legs.
|
|
|
|
|
|
|
|
|
|
|
|
|
|
|
|
|
|