 |
 |
 |
 |
 |
 |
 |
 |
 |
 |
 |
 |
 |
 |
 |
 |
 |
 |
 |
 |
 |
 |
 |
 |
 |
 |
|
|
|
|
|
|
|
|
|
|
|
|
|
|
|
|
|
|
|
|
|
|
|
|
|
|
|
|
|
|
|
|
|
|
|
|
|
|
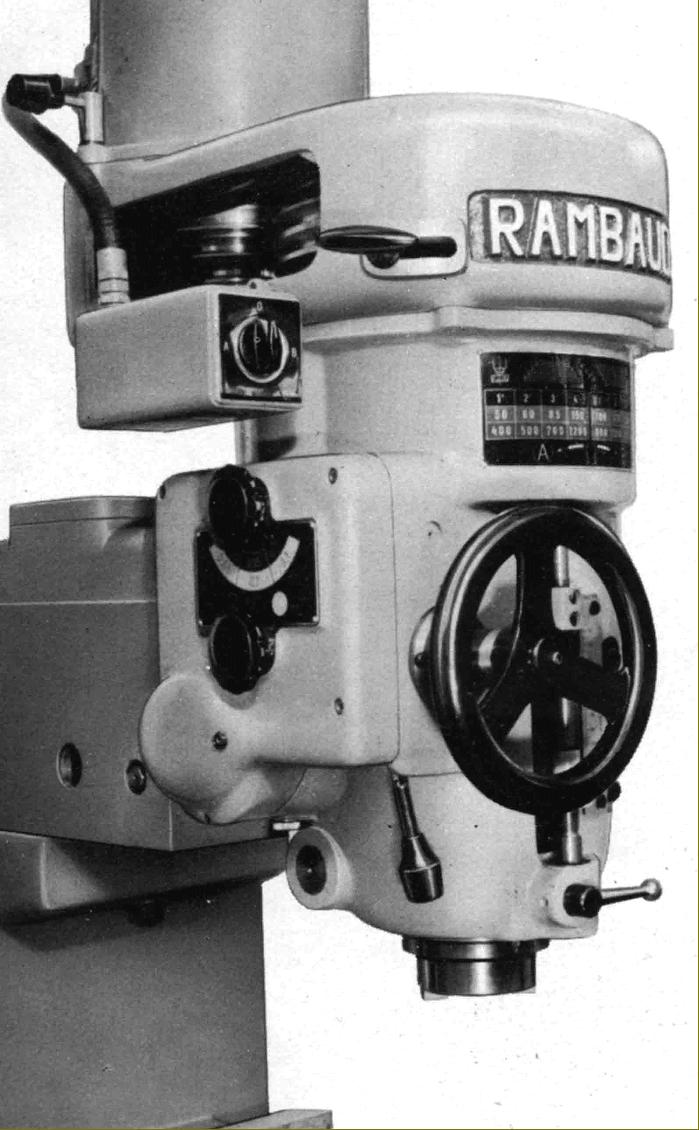 |
|
|
|
|
|
|
Head as used on both late models of the Rambaudi V3
|
|
|
|
|
|
|
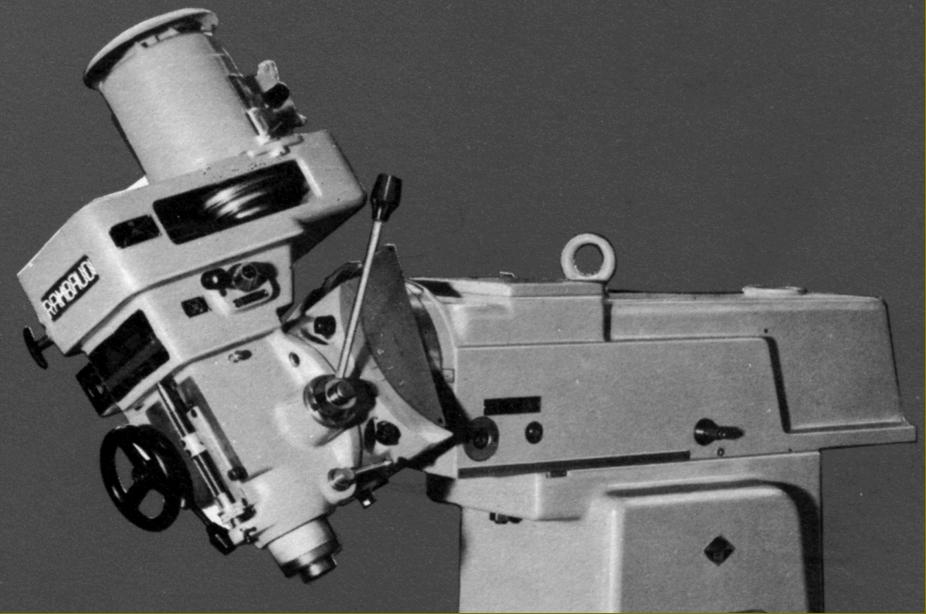 |
|
|
|
|
|
|
None of the Rambaudi ram-head millers was fitted with a "nodding" head as standard, instead this was a facility offered as an option. However, in place of the usual very simple clevis (that always introduced an unwanted element of flexibility together with the added difficulty of getting back to a zero setting), the assembly consisted of a ram-end adapter formed as a semi circle to which a matching casting on the back of the vertical head was clamped. With a huge contact face spread over 180° rigidity was much improved and the head held firmly despite its considerable mass.
|
|
|
|
|
|
|
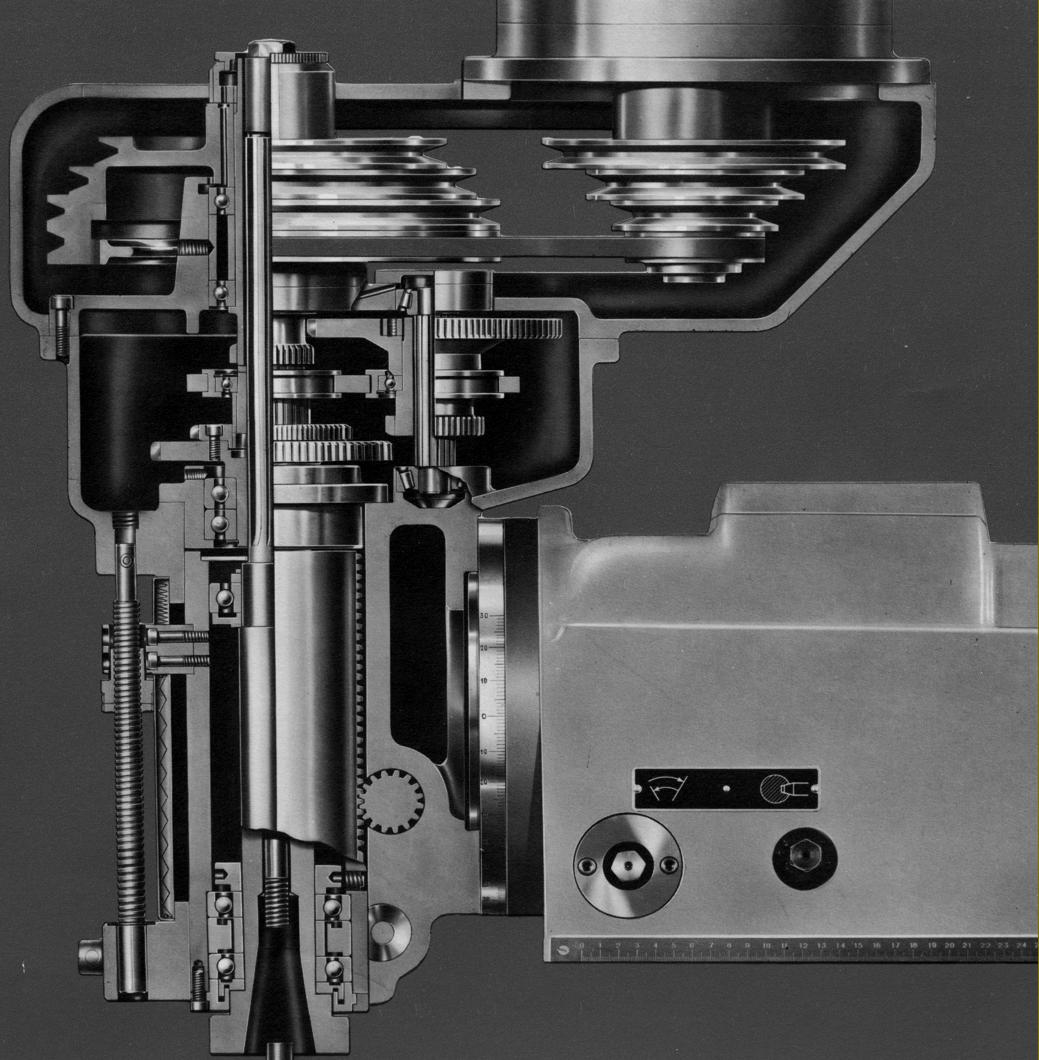 |
|
|
|
|
|
Section through the high-speed (ball-bearing) vertical head used on the V3
|
|
|
|
|
|
|
|
|
|
|
|
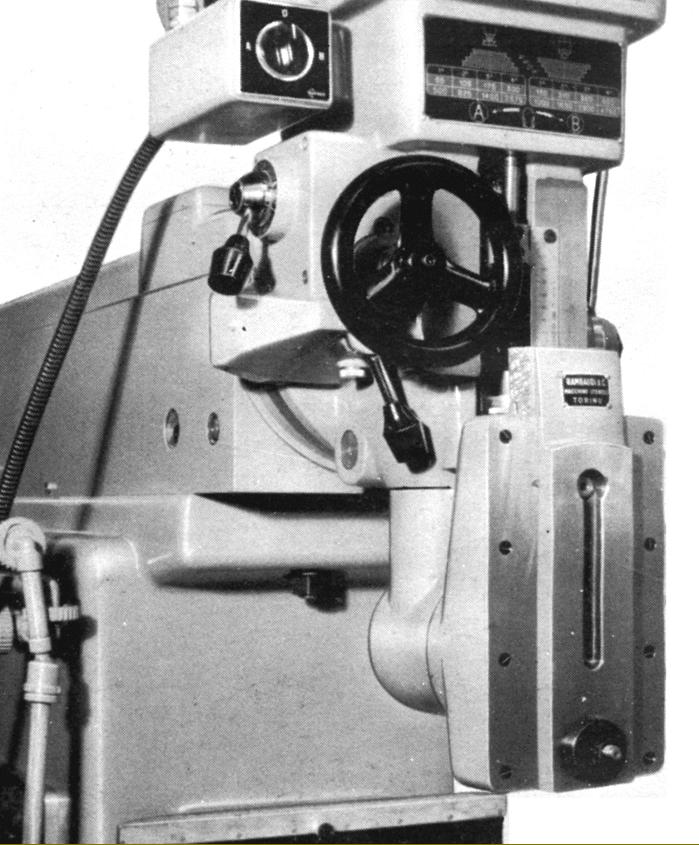 |
|
|
|
|
Slotting head for the V2 and V3 - stroke adjustable between 0 and 3.2"
|
|
|
|
|
|
|
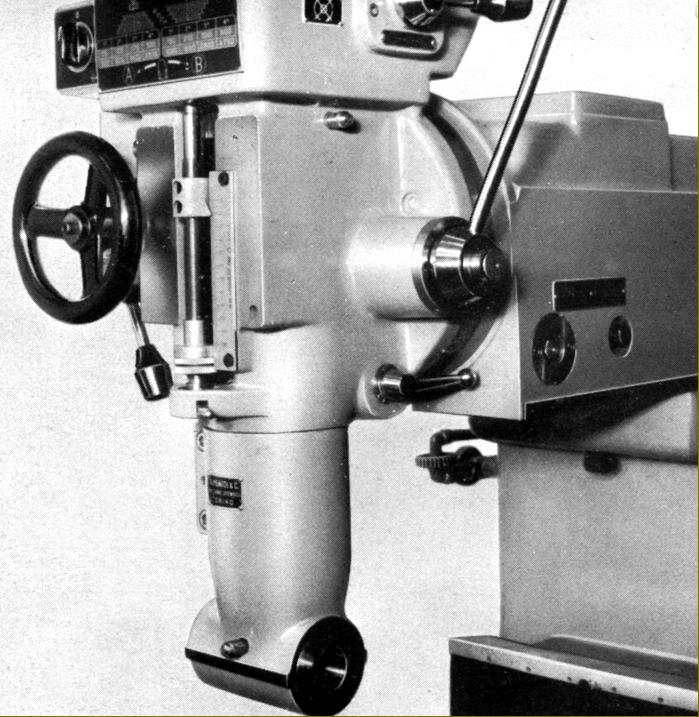 |
|
|
|
|
|
|
Right-angle milling attachment
|
|
|
|
|
|
|
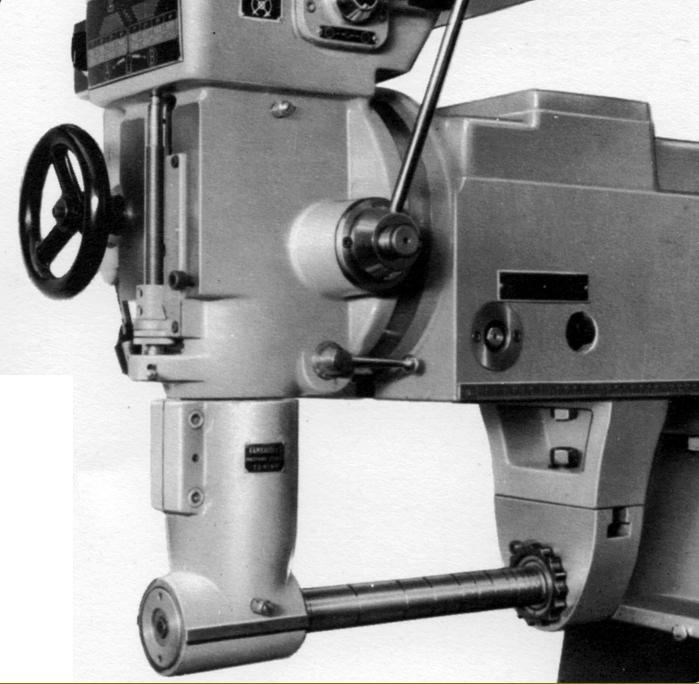 |
|
|
|
|
|
|
Right-angle adapter with arbor and drop bracket arranged for horizontal milling
|
|
|
|
|
|
|
 |
|
|
|
|
|
|
Table feed screws were hardened and ground with that for the longitudinal drive running in an oil bath and made in two short sections, left and right and spring loaded against each other. The screws, around 3" in diameter, engaged against a long, semi-circular nut (a helicoidal rack) fastened to the underside of the table - this ingenious and beautifully constructed arrangement (adjustable to eliminate backlash) giving a huge surface area to slow down the rate of wear.
|
|
|
|
|
|
|
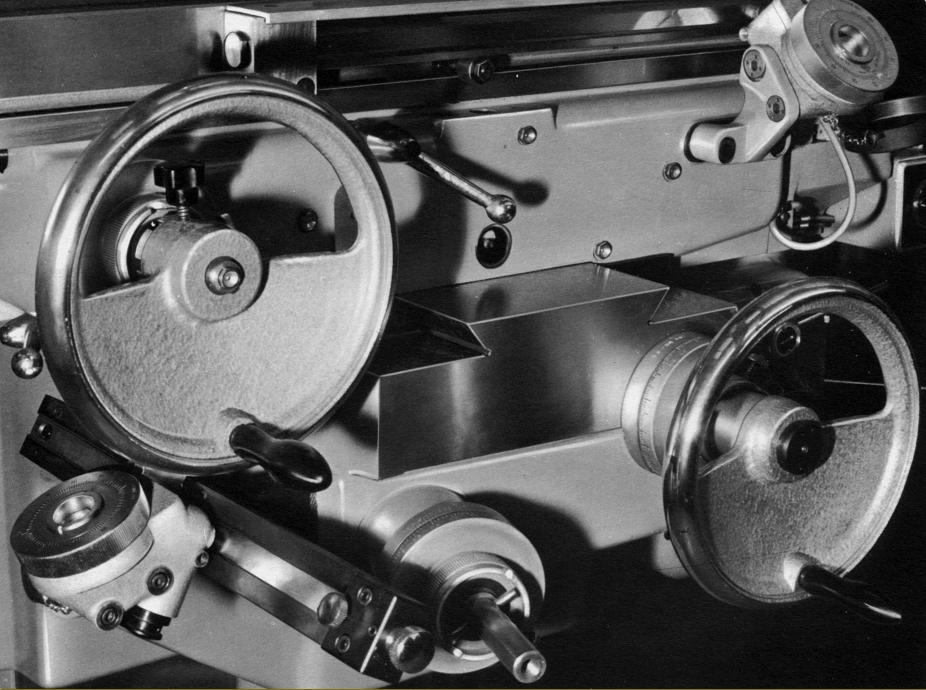 |
|
|
|
|
Optical readers fitted to a V2/V3. Although accurate these were delicate and today are seldom found in working order
|
|
|
|
|
|
|
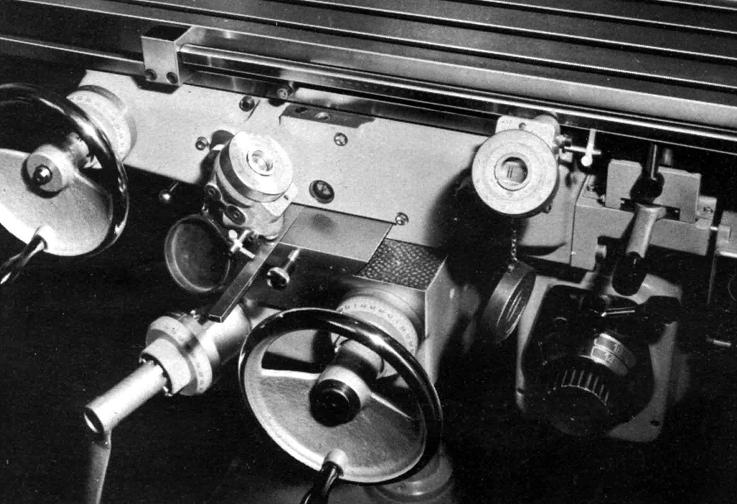 |
|
|
|
|
|
|
Another view of the optical readers
|
|
|
|
|
|
|
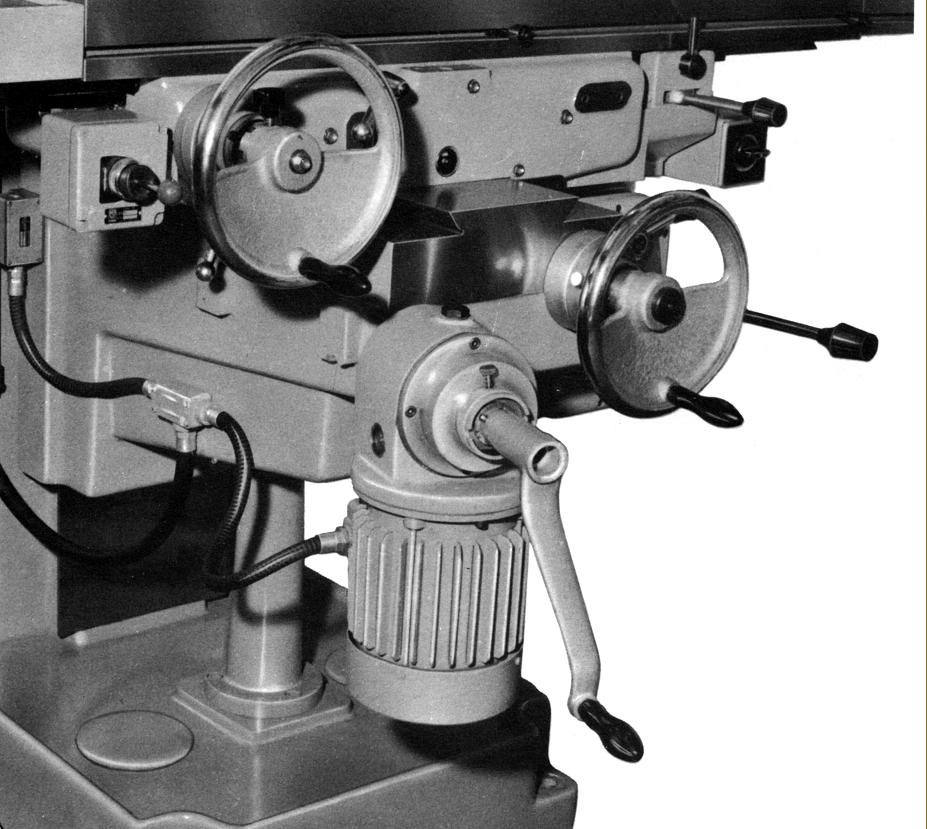 |
|
|
|
|
|
|
Optional power vertical rapid feed attachment
|
|
|
|
|
|
|
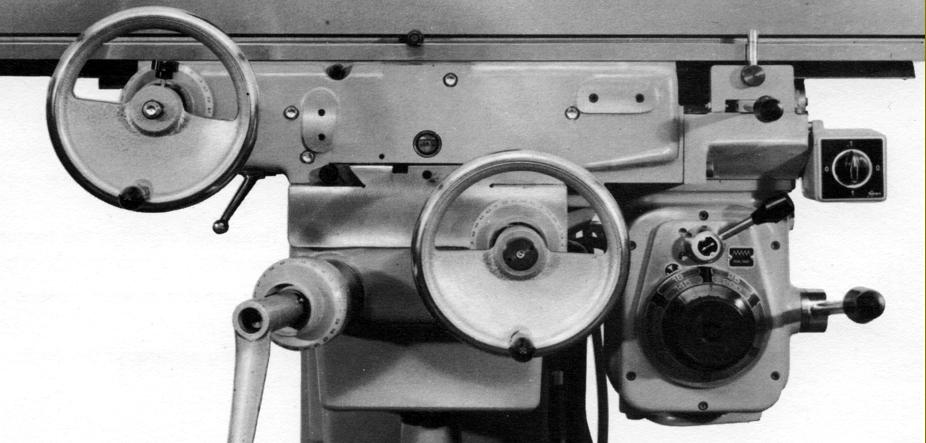 |
|
|
|
|
|
|
All major controls, including the table's horizontal feed (handwheel, top left) were arranged at the front of the machine
|
|
|
|
|
|
|
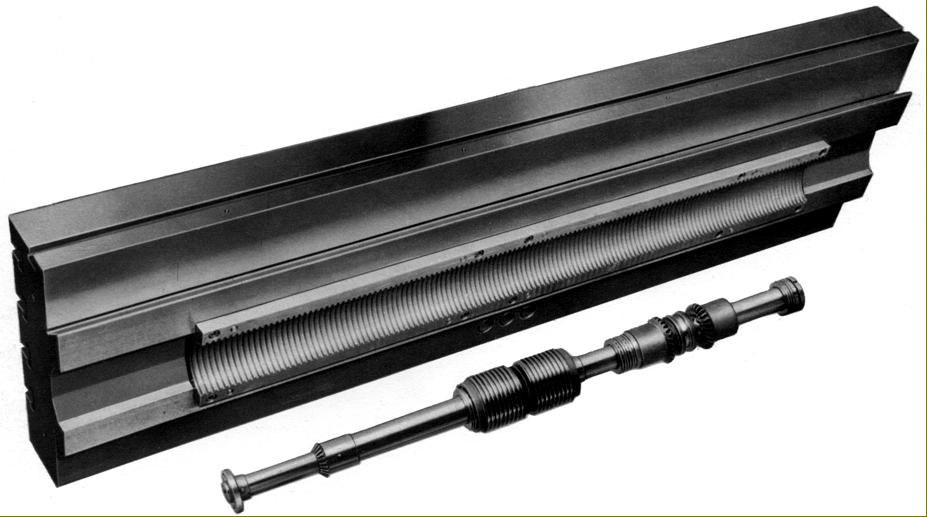 |
|
|
|
|
|
|
Table feed screws were hardened and ground with that for the longitudinal drive running in an oil bath and made in two short sections, left and right and spring loaded against each other. The screws, around 3" in diameter, engaged against a long, semi-circular nut (a helicoidal rack) fastened to the underside of the table - this ingenious and beautifully constructed arrangement (adjustable to eliminate backlash) giving a huge surface area to slow down the rate of wear
|
|
|
|
|
|
|
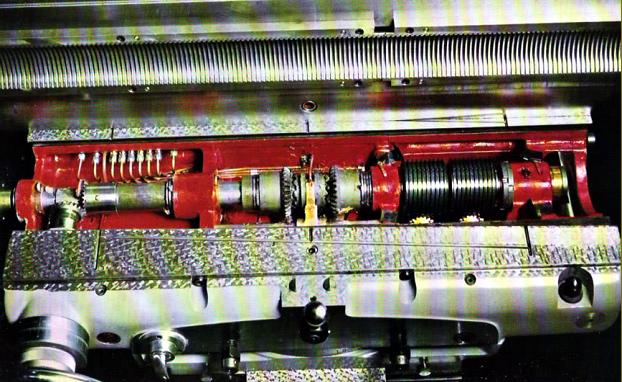 |
|
|
|
|
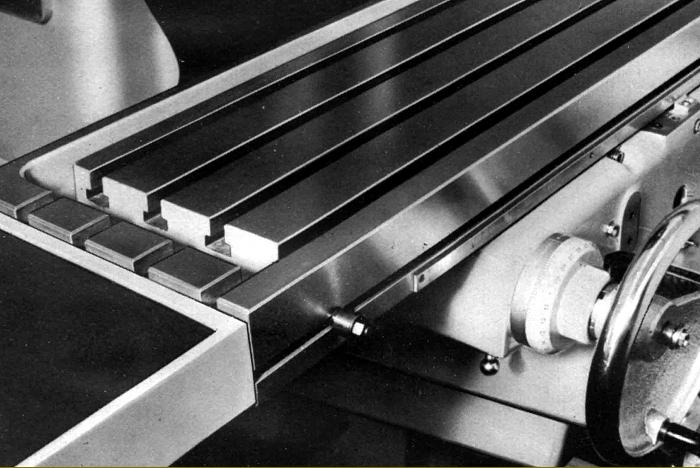 |
|
|
|
|
|
|
|
|
|
|
|