 |
 |
 |
 |
 |
 |
 |
 |
 |
 |
 |
 |
 |
 |
 |
 |
 |
 |
 |
 |
 |
 |
|
|
|
|
|
|
|
|
|
|
|
|
|
|
|
|
|
|
|
|
|
|
|
|
|
|
|
|
|
|
|
|
|
|
|
|
|
|
|
|
Purcell lathes were manufactured by Purcell Engineering Co. (1940) Pty. Ltd. and distributed by the well-known Demco Machinery Co. Pty. Ltd. of Sydney, Australia. Until the production, in the late 1940s, of these very heavily built 10.5, and 12.5-inch models the company's regular range had been the general workshop and light-duty Visby and New Visby (with Mk. 1, Mk. 2 and Mk. 3 versions stretching production into the 1960s) the heavier 8.5-inch Conemaster and otherwise identical but geared-head Record, a South Bend "9-inch" copy and various special-purpose machines including railway wheel turning, long-hole-boring and facing lathes. However, lacking a genuinely heavy, all-purpose industrial-strength machine, Purcell decided, in the late 1940s, to remedy this with a pair of new, indigenously designed models, the simply named 10.5" and 12.5" that were, apart from their centre height and capacity in the gap, identical in all respects. Continued below:
|
|
|
|
|
|
|
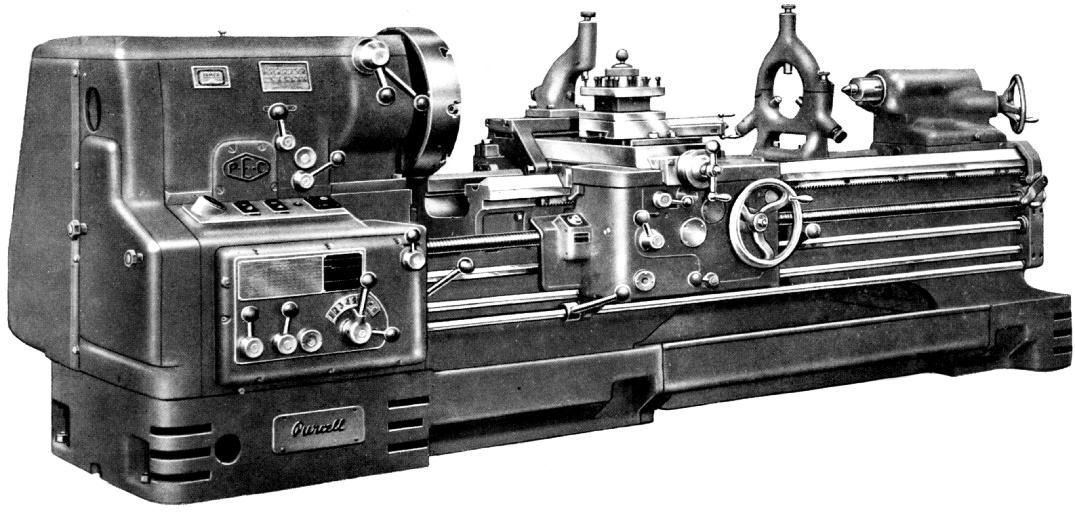 |
|
|
|
|
|
Continued: Cast in Purcell's own foundry from a close-grained cast iron, the massive one-piece bed reached from ways to floor with no need for separate mounting pedestals. Two ground V-ways and two flats were used to guide saddle and tailstock with (due to the bed's enormous strength and rigidity) a deep and wide gap able to machine a disc of material just over 39 inches (43 on the larger model) in diameter and 13 inches thick. A choice of capacities was available - 78, 102, 130, 154 or 178 inches between centres - though the maker would provide up to thirty-feet if required, each additional foot of length adding around ½ ton to the 6.75 tons of the 78-inch model. Some of the additional weight was accounted for by the additional support plinths required: lathes from 10' 10" onwards requiring one; those up to 18' 6" two; up to 24' 10" three and anything longer four. Each section added 2.5% to the price - but did include the necessary shaft supports and additional chip trays. Running on a conventional symmetrical front V and rear flat, the saddle was fitted with the usual type of felt wipers (but not the long way-guards used on the later New Visby model). Rather than simple keeper plates, fully-adjustable gibs were fitted front and rear, the aim being to provide a good sliding fit yet rigid assembly when using an inverted rear toolpost for parting off. Continued below:
|
|
|
|
|
|
|
|
|
|
|
|
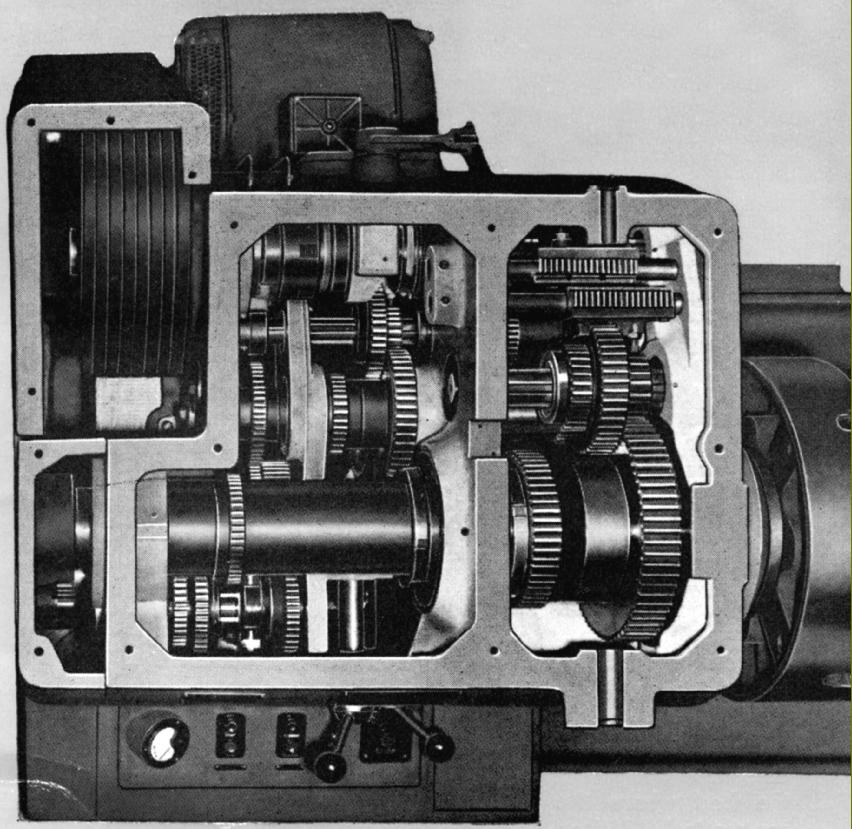 |
|
|
|
|
|
|
Continued: Fitted with a 970 r.p.m. 15 h.p. motor as standard, it was possible to specify ones up to 25 h.p. if extra heavy-duty work was contemplated. Electrical controls were grouped together on top of the screwcutting gearbox together with a then fashionable Ampere-meter. Mounted at the rear of the lathe on a vertically adjustable plate, the motor drove to the headstock through eight B-section V-belts with the drive then passing through an oil-immersed combined clutch and brake clutch. Control of the clutch was through a third-rod system with duplicated control levers, one just outboard of the screwcutting gearbox and the other fastened to the right-hand wall of the apron. Headstock gears were manufactured from a nickel-chrome-moly. steel and ran on hardened shafts supported in ball or roller races. Twelve speeds were provided ranging from 9 to 550 r.p.m. or, with a 2-speed motor, a more useful 24 that ran from 7 to 830 r.p.m. Hardened on its American standard 11.A.1 (11-inch diameter) short-flange nose, the 3.625-inch bore headstock spindle ran in three bearings. The front and middle precision Timken taper-roller type were preloaded to a figure in excess of that experienced during the heaviest cuts, whilst the end of the assembly was supported in a precision-type ball-bearing race. Continued below:
|
|
|
|
|
|
|
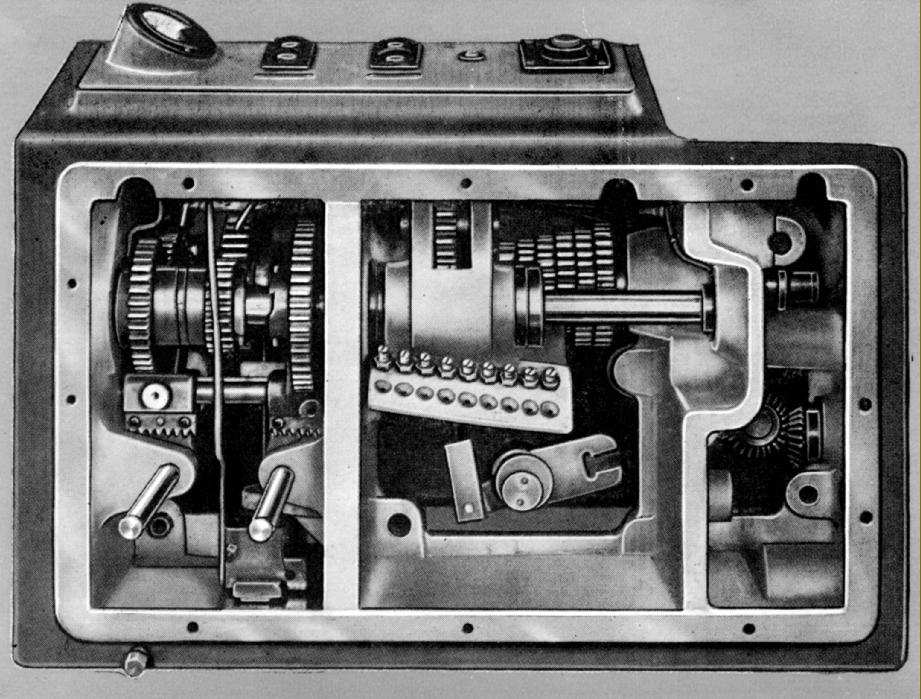 |
|
|
|
|
|
|
Continued: Sealed inside an oil-tight casing the screwcutting and feeds' gearbox was fitted with pressure lubrication. The box could be switched to fine or coarse feeds by a headstock-mounted lever with 63 pitches and rates of feed available from 4 to 30 t.p.i. as standard 0 though 4 to 28 t.p.i. was also quoted in some literature. By special arrangement, other pitch ranges could be provided, as could additional changewheels to extend the threading range. Longitudinal feed rates spanned 0.004" to 0.480" per revolution of the spindle with the cross-feed rate set to be twice as fine. Mounted in roller bearings the 2-inch diameter leadscrew was held in tension and could be reversed end for end when worn. Also benefiting from anti-friction bearings, the feed shaft and control rods were provided, on models admitting 14' 10" or more, with automatically positioning support shaft. Continued below:
|
|
|
|
|
|
|
|
|
|
|
|
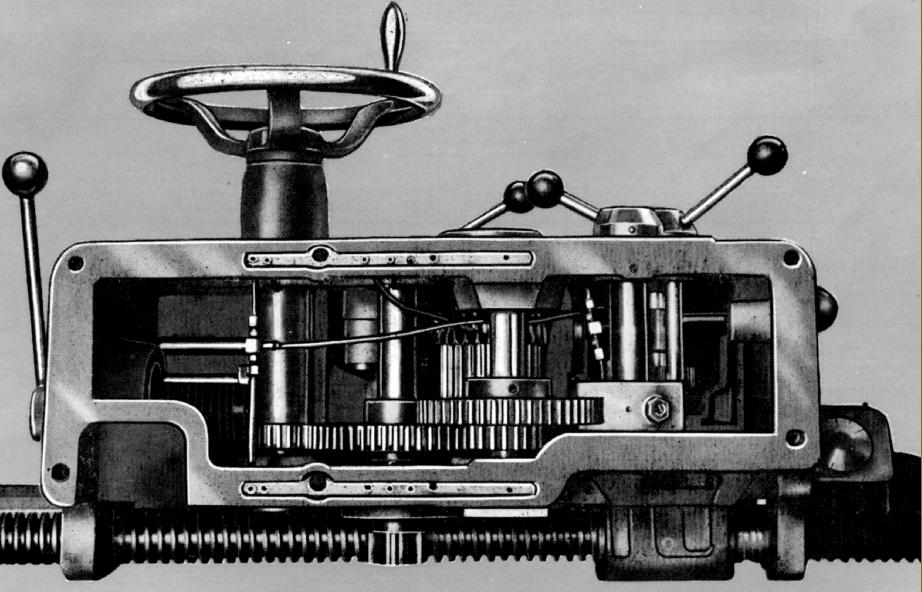 |
|
|
|
|
|
|
Continued: Of massive, one-piece construction and doubled walled, the apron was equipped throughout with ball and roller bearings and pressure lubrication - a network of pipes directing oil to the vital points - and a built-in thread-dial indicator. As on some of the smaller Purcell lathes an instant drop-in-and-out worm box was used to start and stop the feeds - though with the additional refinement of a control to vary the point at which an automatic overload release tripped the drive - as well as a control lever to instantly reverse the feed without needing to stop the drive first. Not used on early versions, but fitted as standard later on, a rapid traverse mechanism powered by a 1 h.p. motor was fitted to the carriage drive - giving rapid repositioning either up or down the bed or across. Continued below:
|
|
|
|
|
|
|
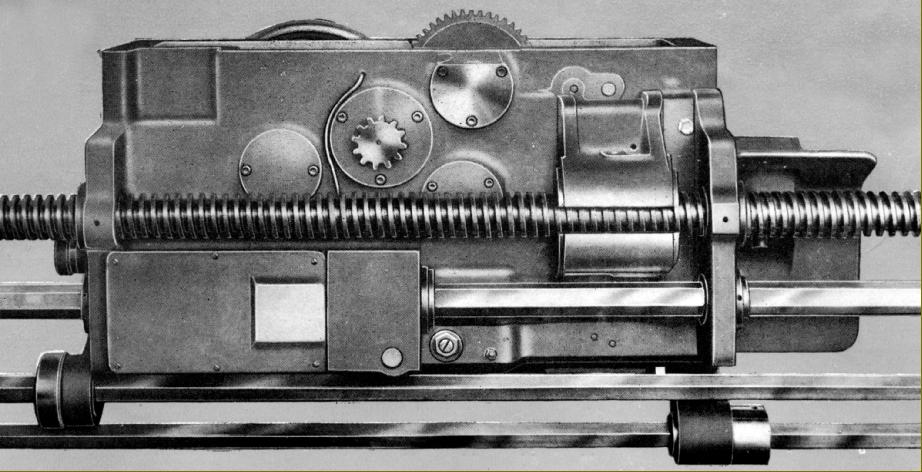 |
|
|
|
|
|
|
Continued: Fitted with taper gib strips, the compound slide assembly had a top slide with 9 inches of travel and able to be swivelled through 360°. It was fitted as standard with a steel 4-way toolpost - though (annoyingly for the operator) this was fitted with a quick-index mechanism that only engaged in four positions. Micrometer dials were satin-chrome finished and the Acme-form feed-screws, supported in ball races where they passed through their end plates, fitted with balanced handles - that on the top slide being of the two-handle short type. A useful refinement on the 20-inch travel cross-slide was the provision of a feed nut that could be adjusted to eliminate backlash. Suitably massive, the tailstock could be hooked to the carriage for ease of movement over long travels (the same device could be adapted at the factory to provide a power feed to the tailstock) or repositioned by the operator using the rack-and-pinion gearing provided. Aided by its oil-immersed, worm-and-wheel gearing, the 3.875-inch diameter No. 5 Morse taper spindle had a travel of 12.25 inches.
|
|
|
|
|
|
|
|
|
|
|
|
|
|
|
|