 |
 |
 |
 |
 |
 |
 |
 |
 |
 |
 |
 |
 |
 |
 |
 |
 |
 |
 |
 |
 |
 |
 |
 |
 |
 |
 |
 |
 |
 |
 |
 |
 |
 |
 |
 |
 |
 |
 |
 |
 |
 |
 |
 |
 |
 |
 |
 |
 |
 |
|
|
|
|
|
|
|
|
|
|
|
|
|
|
|
|
|
|
|
|
|
|
|
|
|
|
|
|
|
|
|
|
|
|
|
|
|
|
|
|
|
|
|
|
|
|
|
|
|
|
|
|
|
|
|
|
|
|
|
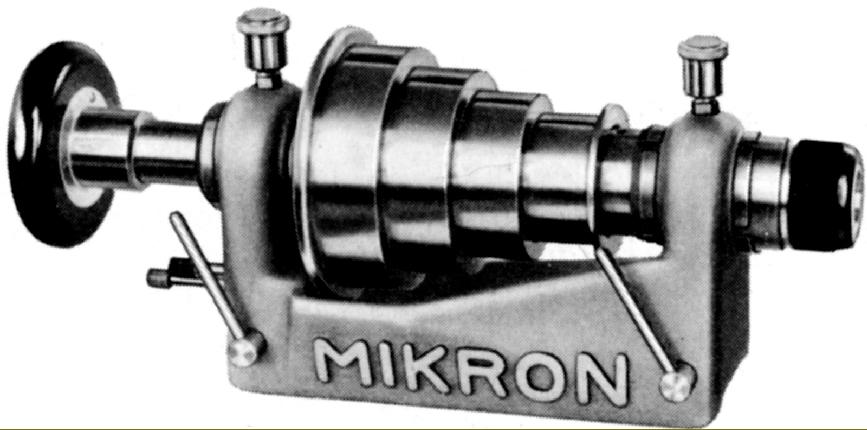 |
|
|
|
|
|
|
Reversed in comparison with a conventional lathe the 4-step headstock pulley of the ordinary headstocks sat with its largest diameter to the left (allowing the front bearing to be surrounded by a greater mass of metal) with drive by a 30 mm wide flat belt. The cone diameters were 61, 79, 97 and 115 mm - and the general speed range ran from 200 to 2000 r.p.m - though this was, of course, greatly affected by the type of drive system and motor employed. The end flange of the largest pulley was provided with two circles of indexing holes - 60 and 8 - with the latter made larger in diameter to allow for their use as a spindle lock. A very similar unit, headstock 8B, was fitted for heavy-duty work with double-cone bearings and another, the 2C, supplied with a backplate, centre holder and centre permanently mounted
|
|
|
|
|
|
|
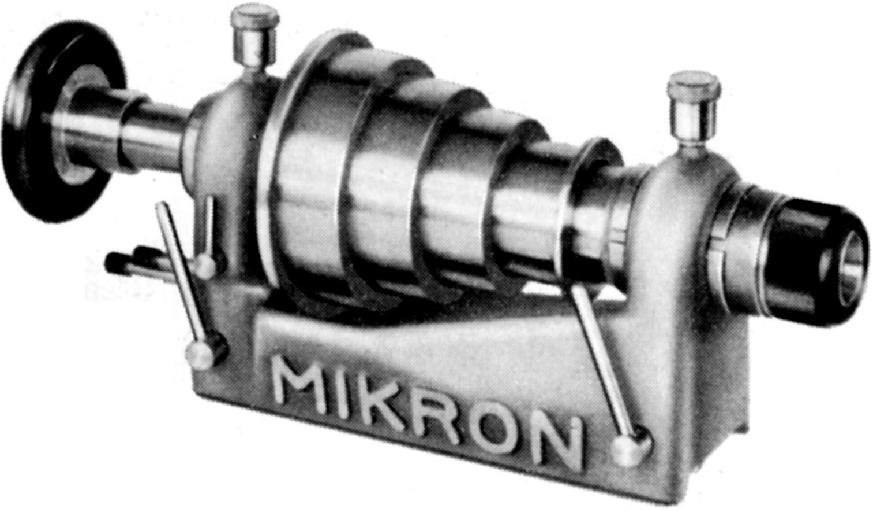 |
|
|
|
|
|
|
Headstock No. 9 - a very rare version built with a 3 : 1 ratio epicyclic reduction gear inside (a model that can be identified by the small locking-pin lever below the left hand bearing)
|
|
|
|
|
|
|
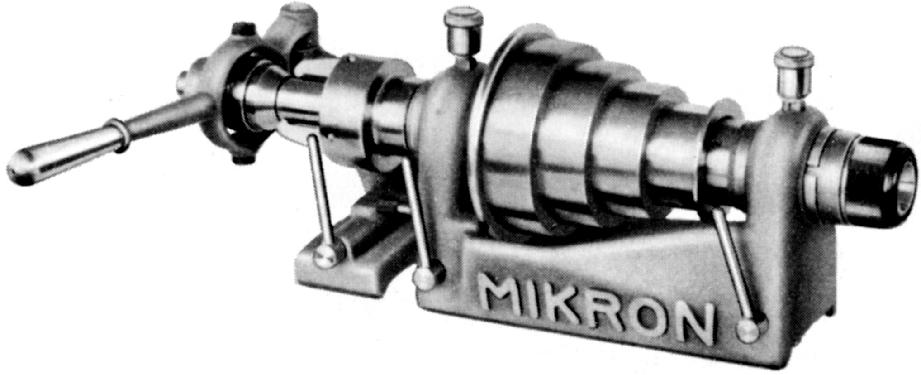 |
|
|
|
|
|
|
Headstock No. 10 - the No. 8 headstock was equipped with a quick-action, lever-operated collet closer
|
|
|
|
|
|
|
|
|
|
|
|
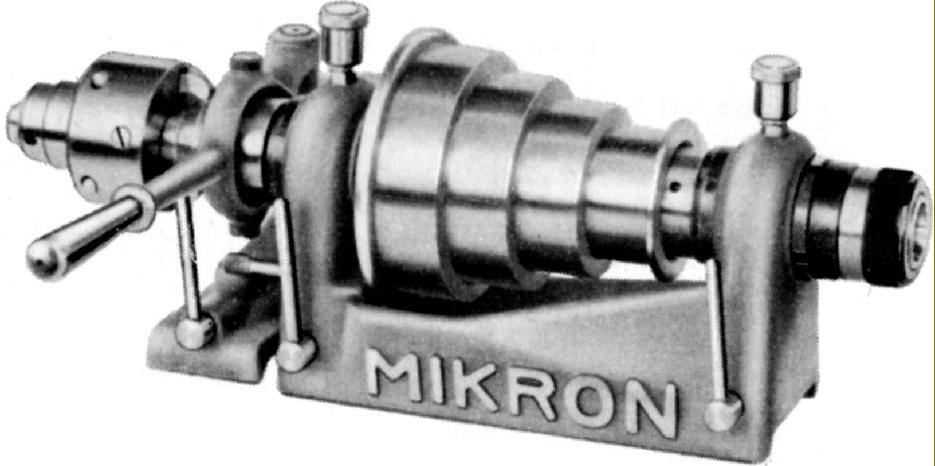 |
|
|
|
|
|
|
Headstock No. 11. An interesting assembly with a lever-action collet closer that that moved over the collet and pressed it inwards instead of pulling - the aim being to increase consistency of positioning by maintaining the relative position of the collet to the spindle regardless of slight variations in stock diameter. This arrangement was intended for consistently of tolerances in a production environment, better ultimate accuracy being afforded by the conventional pull-type closer
|
|
|
|
|
|
|
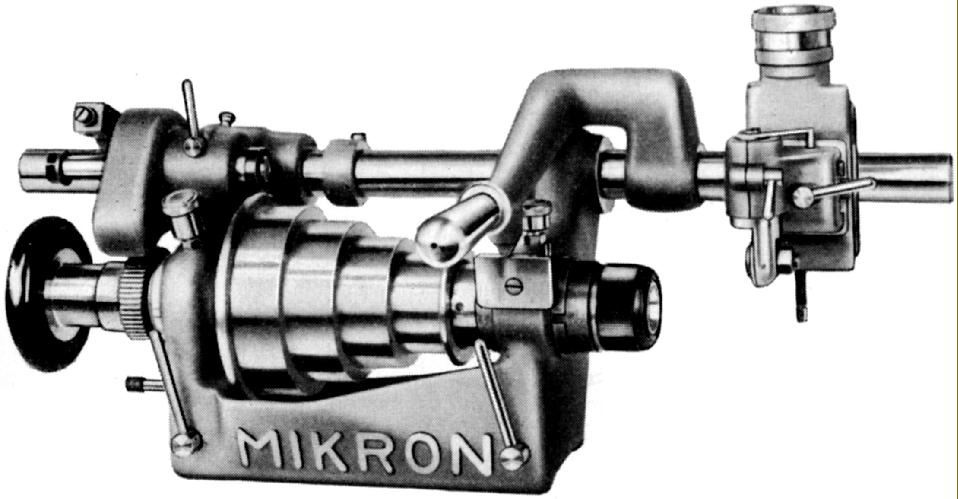 |
|
|
|
|
|
|
Headstock No. 12 fitted with a robust, permanently-mounted thread-chasing apparatus (No. 12) designed for cutting the fine threads used on microscopes and telescope bodies. 35 mm long hobs were employed and arranged via gearing so that the ratio between the pitch of the hob and the work was 2 to 1. (i.e. the pitch of the thread-generating screw was twice that of the work produced)
|
|
|
|
|
|
|
|
|
|
|
|
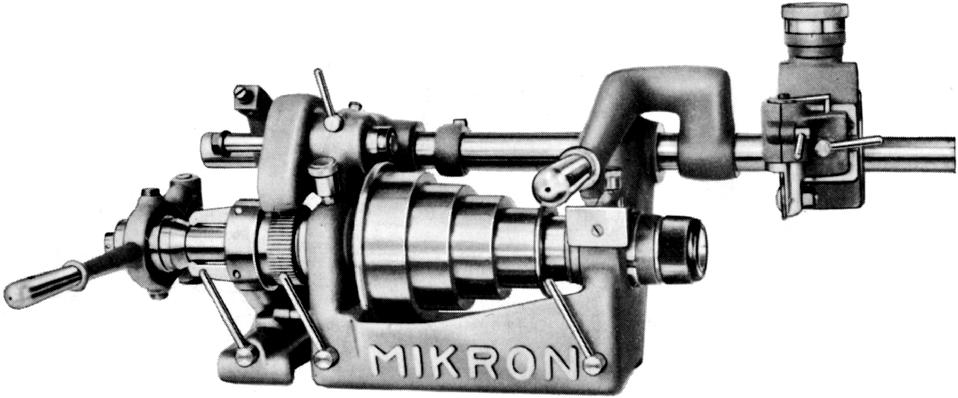 |
|
|
|
|
|
|
Headstock No. 13. Identical to the No. 12 but fitted with a lever-operated collet closer
|
|
|
|
|
|
|
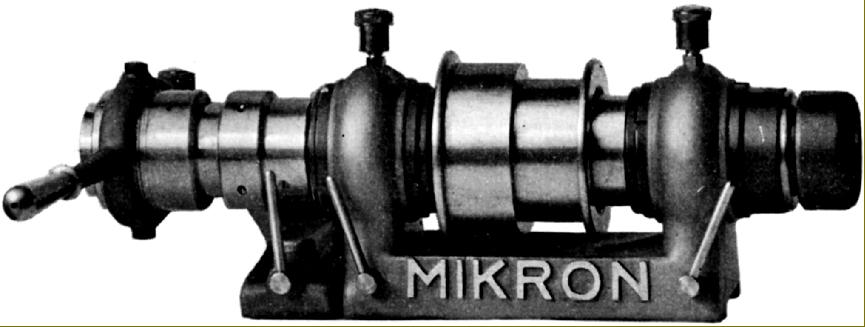 |
|
|
|
|
|
|
Headstock No. 14. For production use only this had a spindle bored to take bar up to 26 mm in diameter and to accept standard brown and Sharpe collets. Drive was by a two-step cone pulley (90 and 110 mm) with drive by a 40 mm wide flat belt. A draw-tube closer could not be fitted and the nose, being unthreaded, was unable to mount chucks or backplates
|
|
|
|
|
|
|
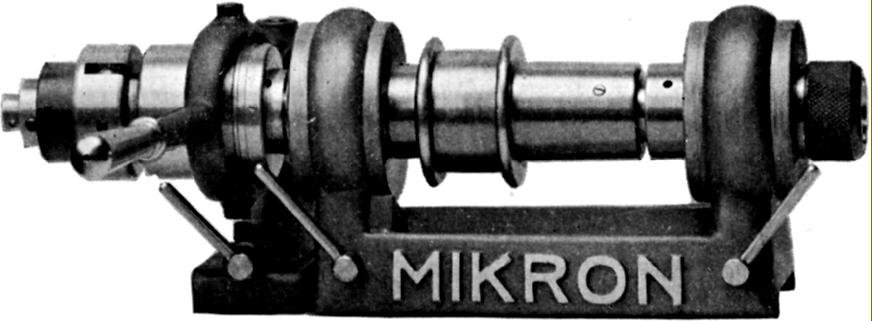 |
|
|
|
|
|
|
Headstock No. 15 (lever closer) and 15a (draw-tube closer). Adjustable roller bearings (the only Mikron so-equipped) suitable for speeds up to 6,000 r.p.m. were used. Both had maximum collet capacities of 14.65 or 16 mm and carried a single 65 mm diameter cone pulley for a 35 mm flat drive belt
|
|
|
|
|
|
|
 |
|
|
|
|
|
|
Headstock No. 17. This was one of a set of four very large spindle-bore headstocks the 17, 18, 19 and 20. These resembled the ordinary No. 8 - with the hardened, ground and lapped spindle running in parallel-bore, externally tapered bearings tapered on their outside - but with a hole able to take 40 mm bar. A 3-step cone pulley was fitted (diameters 104, 122 and 140 mm) with drive by a 35 mm wide belt. The No. 17 used a draw-tube to retain collets (fitted with a ball-thrust race) while the No 18 was identical, but with a lever-action closer. Using the same basic casting, and other parts, the Nos. 19 and 20 were intended for optical work on brass and mild steel tubing and came equipped with a built-in thread-chasing attachment. 35 mm long hobs were employed and arranged via gearing so that the ratio between the pitch of the hob and the work was 2 to 1. (i.e. the pitch of the thread-generating screw was twice that of the work produced). No. 18 used a collet draw-tube, No. 20 a lever-operated closer
|
|
|
|
|
|
|
|
|
|
|
|
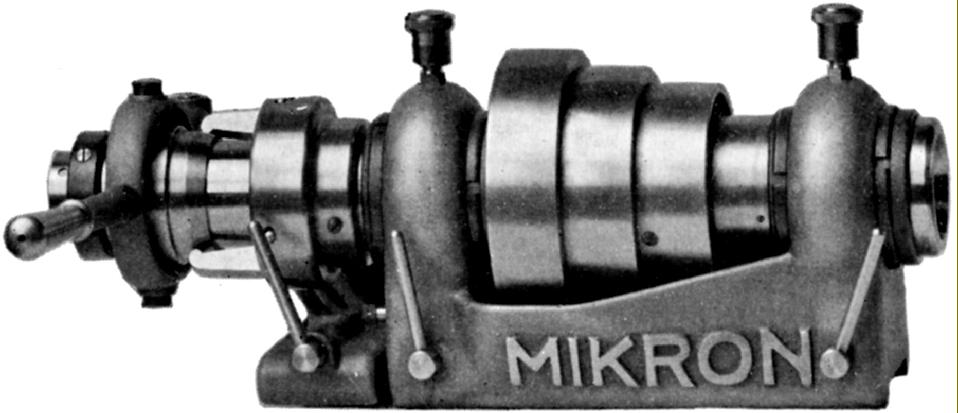 |
|
|
|
|
|
|
Headstock No. 18. Big-bore 40 mm spindle with lever-action collet closer
|
|
|
|
|
|
|
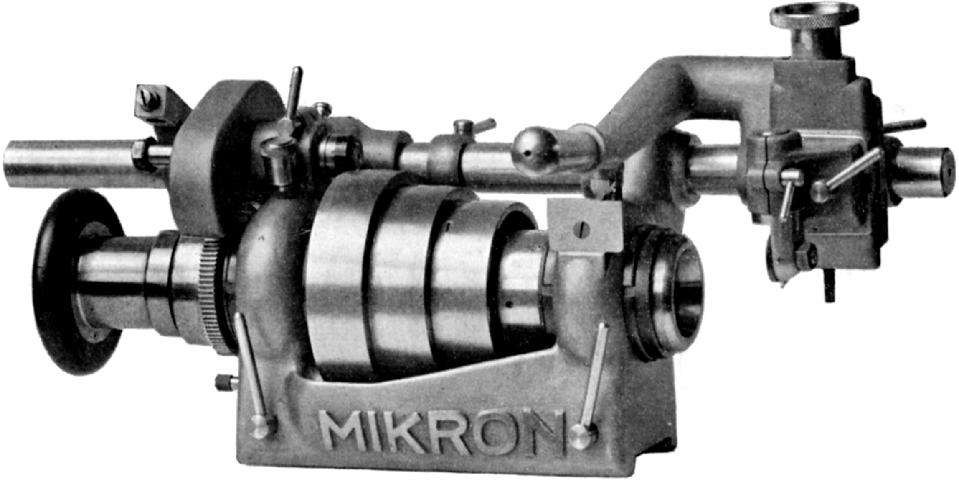 |
|
|
|
|
|
|
Headstock No. 19. Big-bore 40 mm spindle with draw-tube collet closer and fitted with an integrated thread chasing mechanism. Designed for cutting the fine threads used on microscopes and telescope bodies 35 mm long hobs were employed and arranged via gearing so that the ratio between the pitch of the hob and the work was 2 to 1. (i.e. the pitch of the thread-generating screw was twice that of the work produced)
|
|
|
|
|
|
|
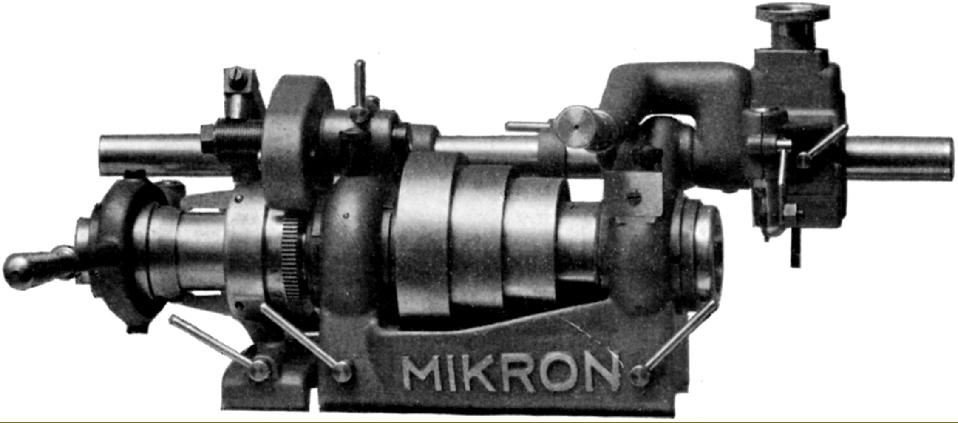 |
|
|
|
|
|
|
Headstock No. 20. Identical to the No. 19 with a 40 mm bore spindle but a lever-action collet closer
|
|
|
|
|
|
|
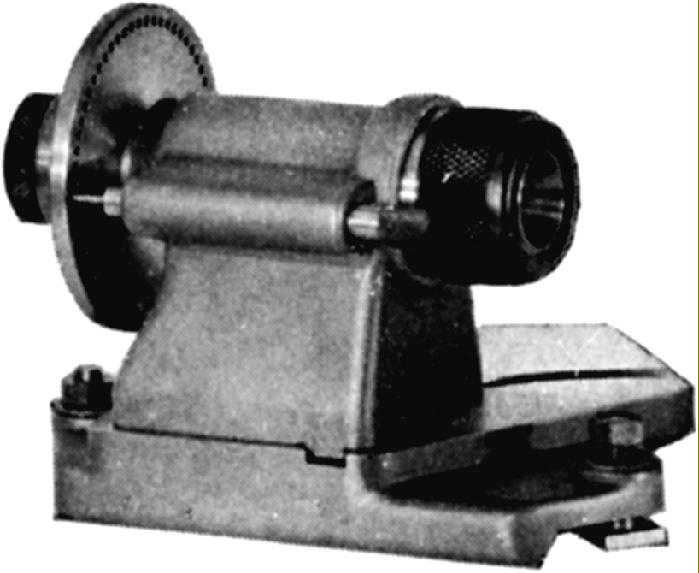 |
|
|
|
|
|
|
Headstock No. 16. This was for slotting work only (see accessories Nos. 36 and 37) and was mounted on a swivel base able to be turned 45° in each direction from zero. The nose was bored to accept collets of 14.5 or 16 mm capacity and provided with a thread to mount the usual accessories
|
|
|
|
|
|
|
|
|
|
|
|
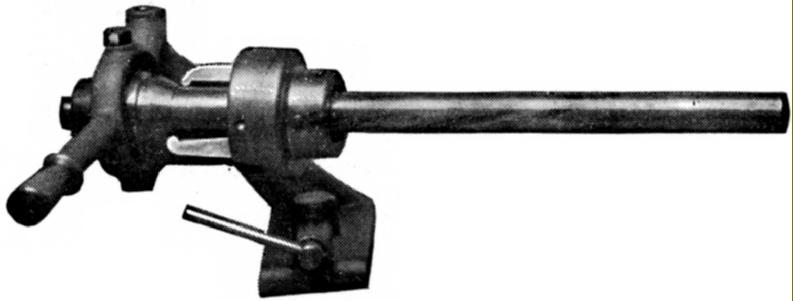 |
|
|
|
|
|
|
No. 88 lever-operated collet draw-in attachment. The lever was 250 mm long and worked through a toggle ratio of 4 : 1. The toggle closing collar, sleeve and thrusts pads are hardened and ground
|
|
|
|
|
|
|
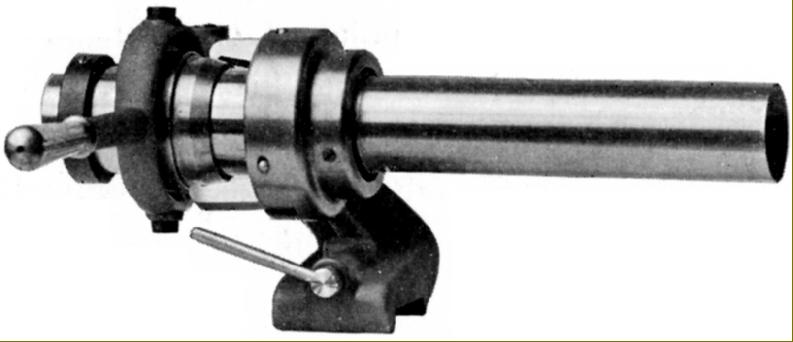 |
|
|
|
|
|
|
No. 89 lever-operated draw-in attachment. The lever was 285 mm long and worked through a toggle ratio of 4 : 1. The toggle closing collar, sleeve and thrusts pads are hardened and ground
|
|
|
|
|
|
|
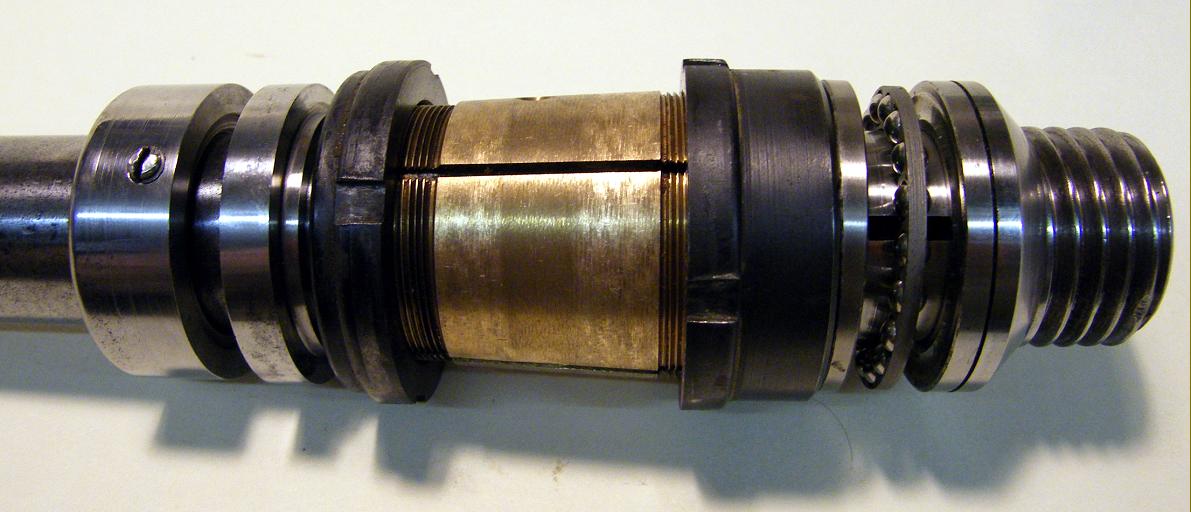 |
|
|
|
|
|
Typical Mikron spindle and front bearing assembly. Note the cone-shaped bearing with buttressed threads - designed to be drawn into the tapered seats of the headstock casting - and the front-mounted end-thrust absorbing ball race
|
|
|
|
|
|
|
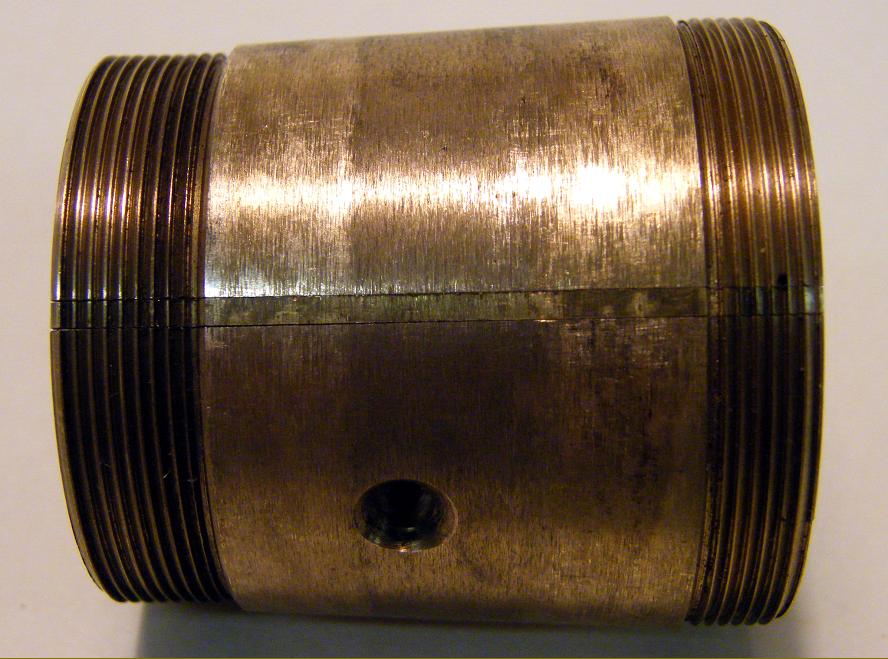 |
|
|
|
|
|
|
|
|
|
|
|
|
|
|
|
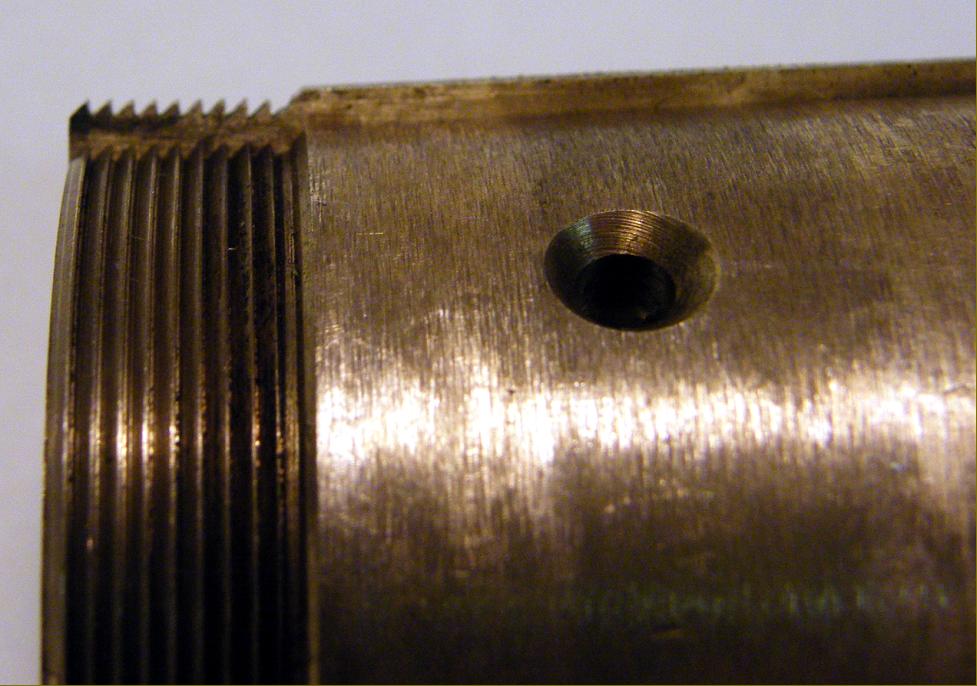 |
|
|
|
|
|
|
Close-up shot of the bearing's buttressed threads
|
|
|
|
|
|
|
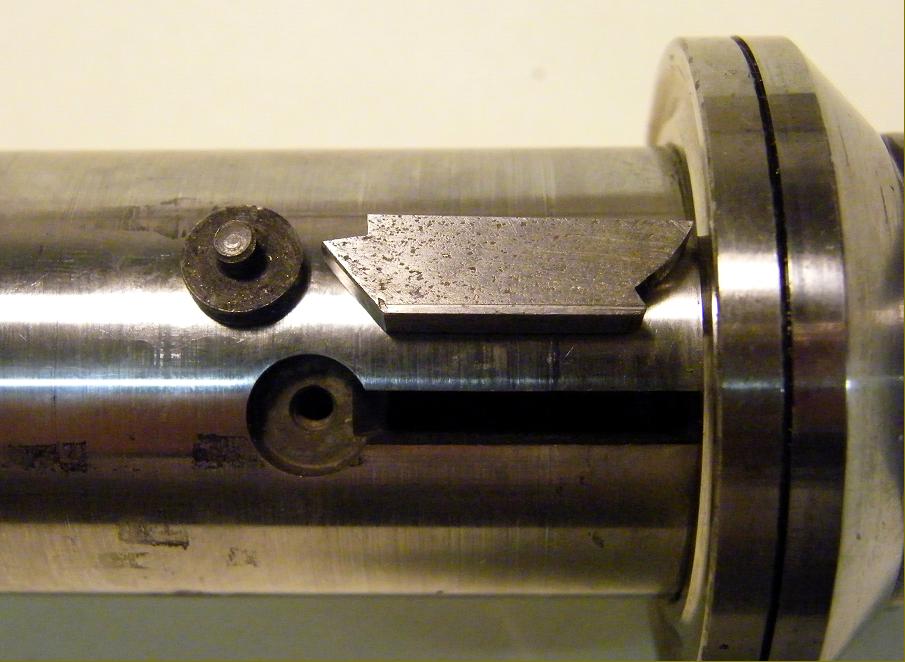 |
|
|
|
|
|
|
Ingenious, beautifully-made easily-removable key
|
|
|
|
|
|
|
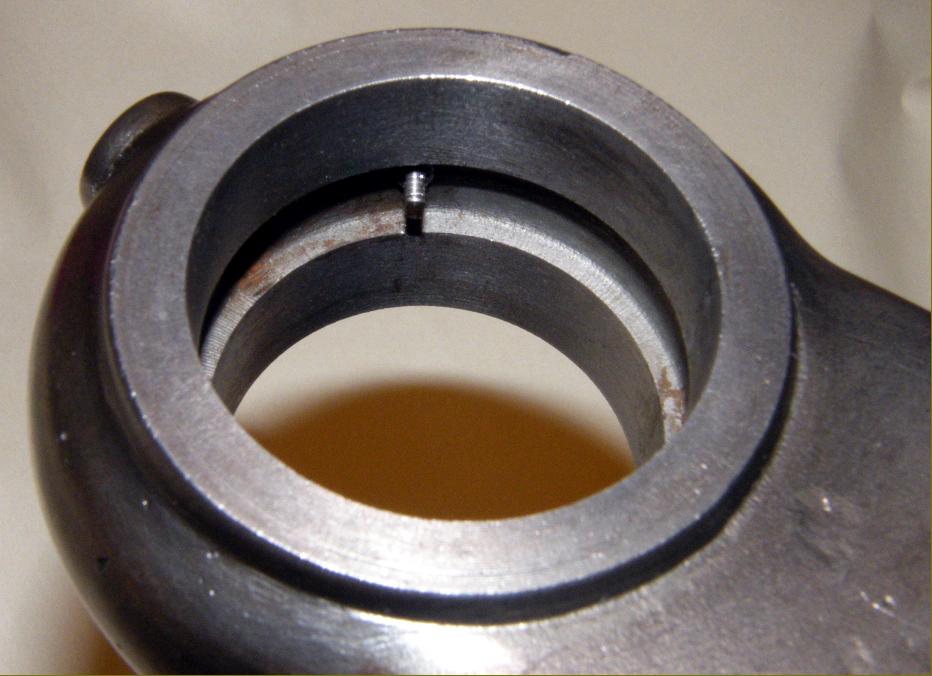 |
|
|
|
|
|
|
Tapered bearing seat in the headstock casting
|
|
|
|
|
|
|
|
|
|
|
|
|
|