 |
 |
 |
 |
 |
 |
 |
 |
 |
 |
 |
 |
 |
 |
 |
 |
 |
 |
 |
 |
 |
 |
 |
 |
|
|
|
|
|
|
|
|
|
|
|
|
|
|
|
|
|
|
|
|
|
|
|
|
|
|
|
|
|
|
|
|
|
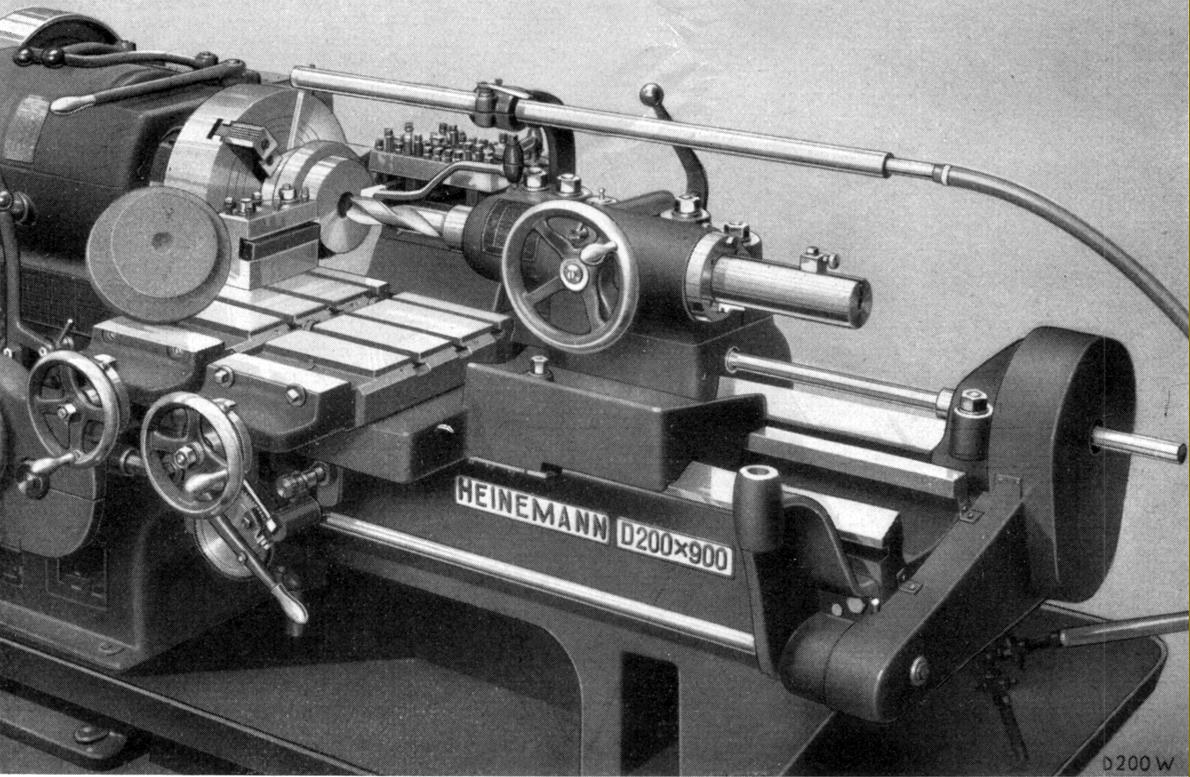 |
|
|
|
|
|
|
Multi-tool lathe Type D200 x 900 fitted with a special tailstock (Type Bo) for drilling and boring and an automatic cross-feed assembly (Type Pa). The arrangement was intended to allow the lathe to take the place of chucking automatics on heavy work. The picture shows a forged steel cluster-gear 213 mm in diameter and 120 mm long being turned, bored and faced simultaneously in 9.8 minutes.
|
|
|
|
|
|
|
|
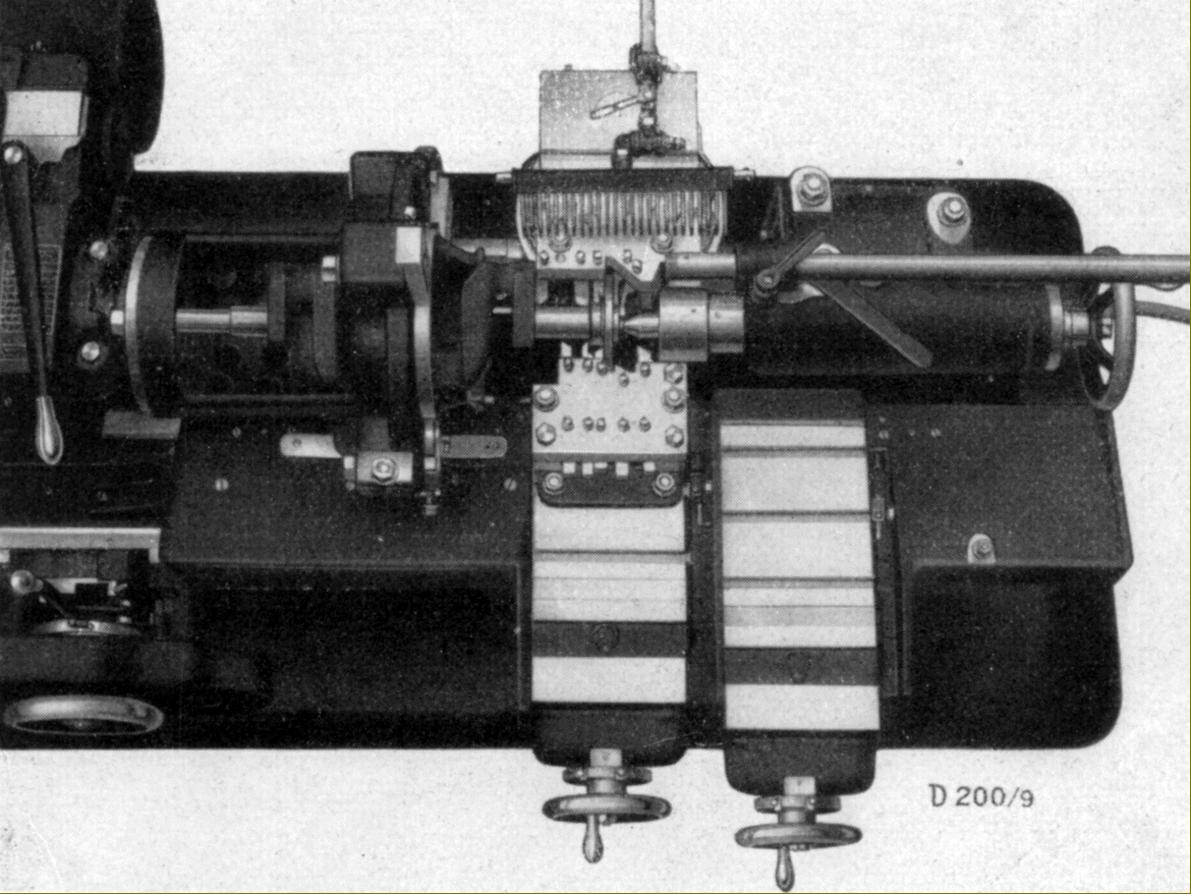 |
|
|
|
|
|
A "pot chuck" and roller steady being used to hold a four-throw crankshaft. Time taken to machine the centre bearing and both ends was 32 minutes
|
|
|
|
|
|
|
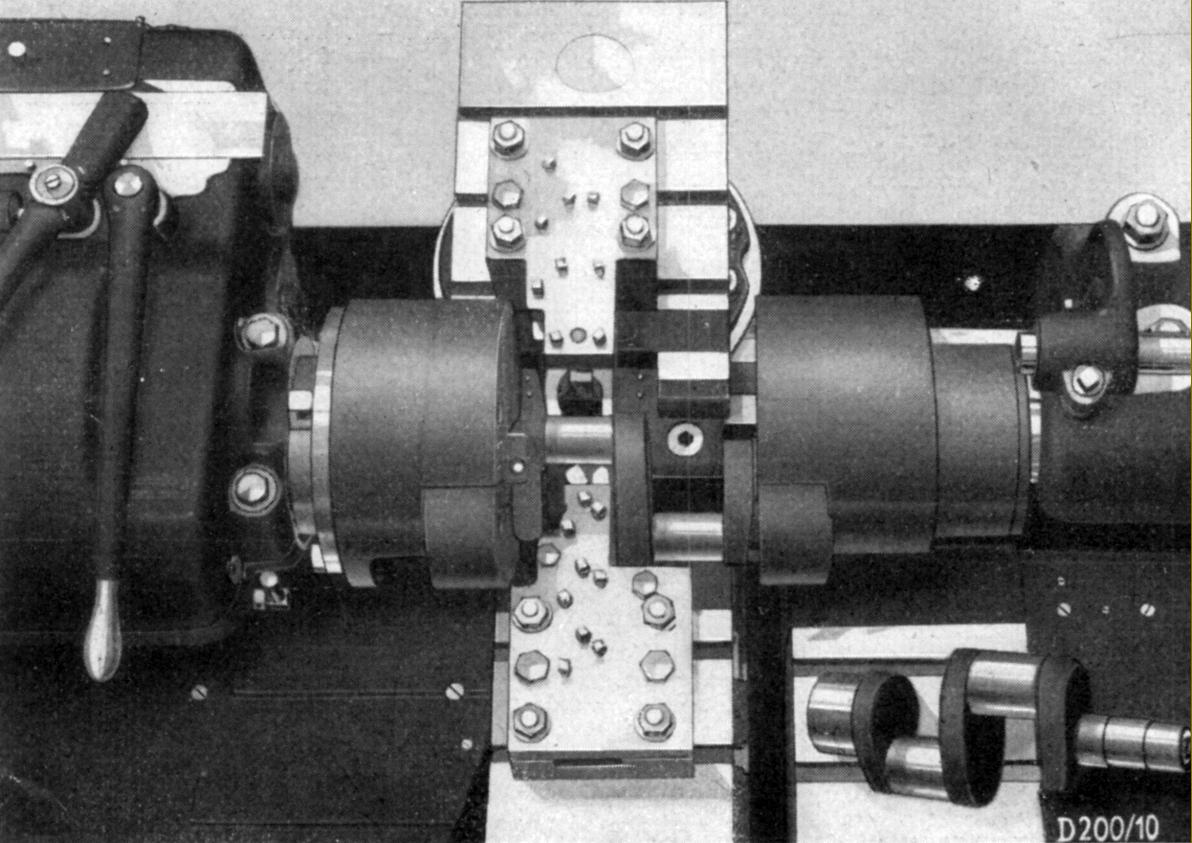 |
|
|
|
|
|
|
Turning the crankpins of a two-throw crankshaft using a "pot Chuck". The time for roughing and finishing this 50 mm diameter by 65 mm long job was 12 minutes
|
|
|
|
|
|
|
|
|
|
|
|
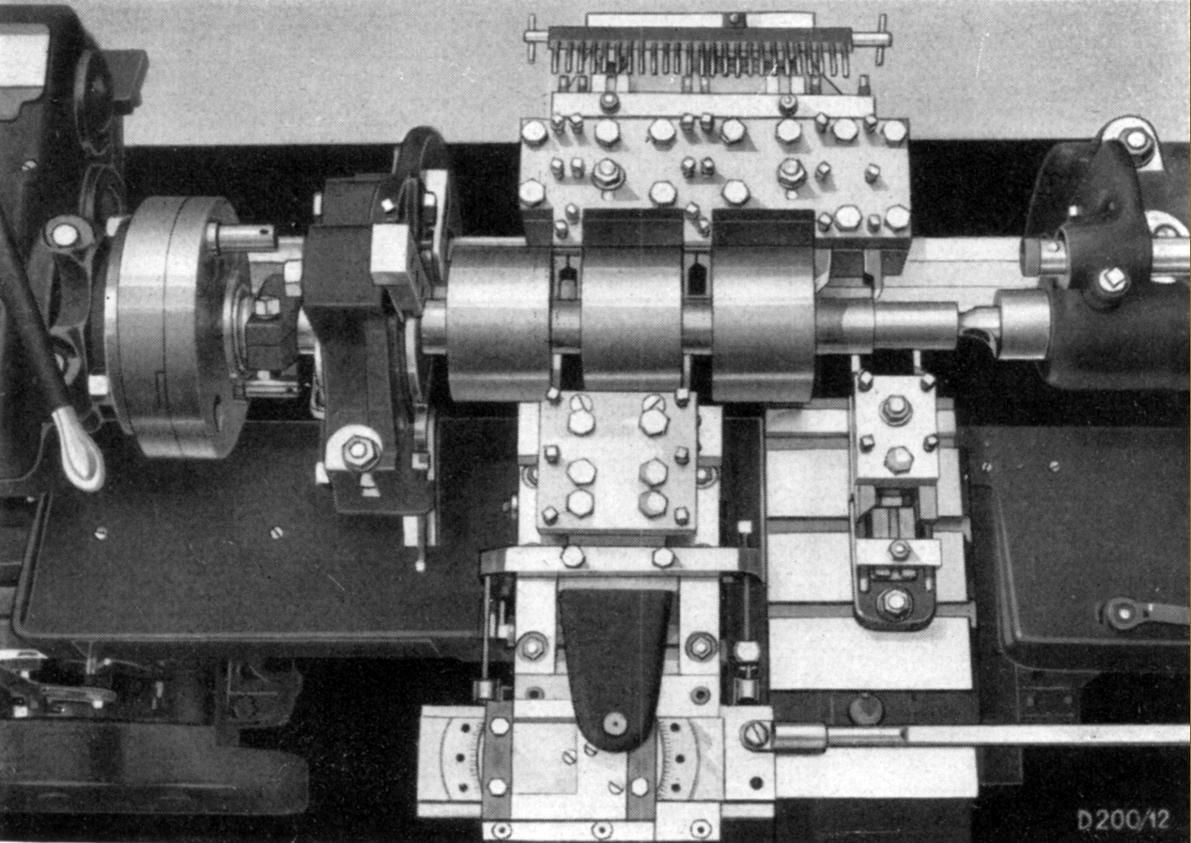 |
|
|
|
|
|
|
Turning a 4-cylinder crankshaft from a solid billet 180 mm in diameter and 750 mm long. This lathe is fitted with an attachment (Type Kpz) that gave a quick return of the cuttings tools mounted on the longitudinal slide
|
|
|
|
|
|
|
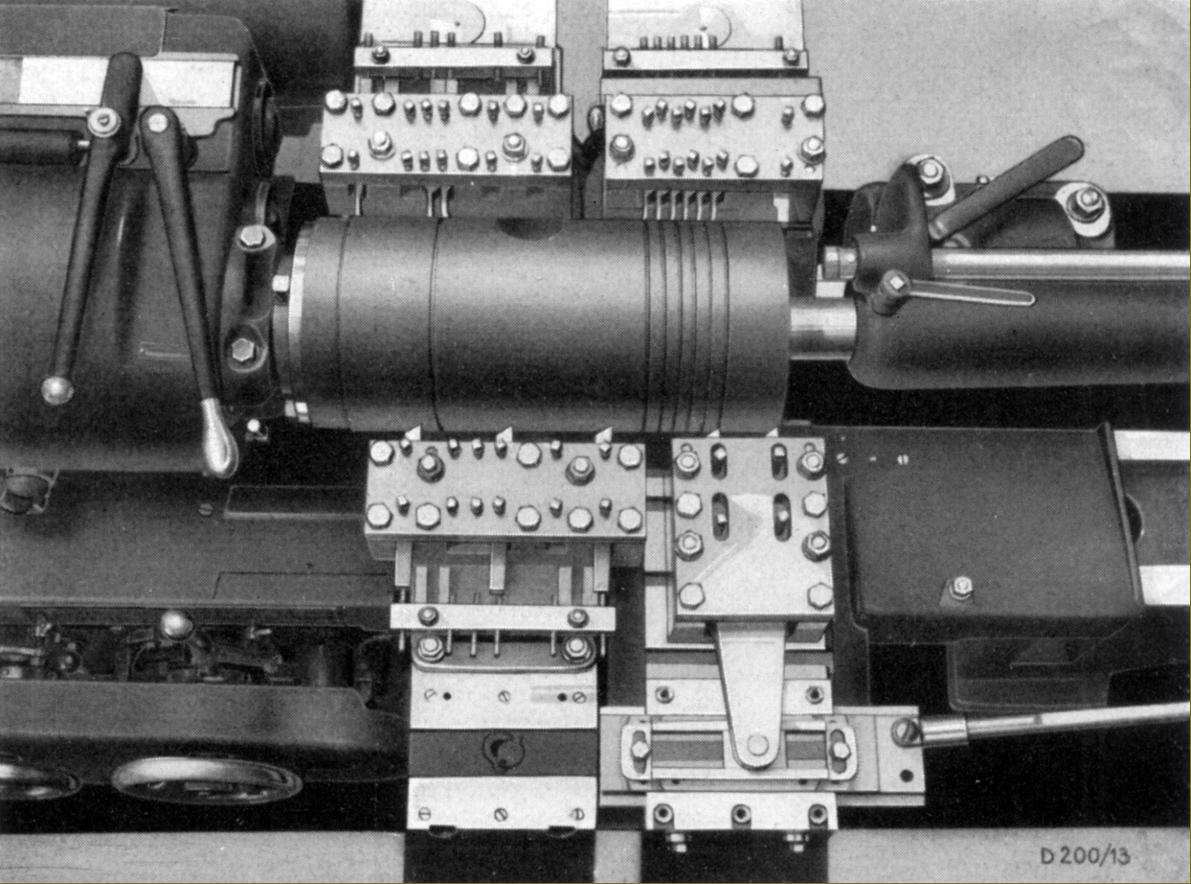 |
|
|
|
|
|
|
Turning a heavy Diesel engine piston 280 mm in diameter and 530 mm long. Two cross slides and two longitudinal slides are in use - the latter pair arranged so that the right-hand unit taper turns while that to the left turns cylindrically. Time for both roughing and finishing 18 minutes
|
|
|
|
|
|
|
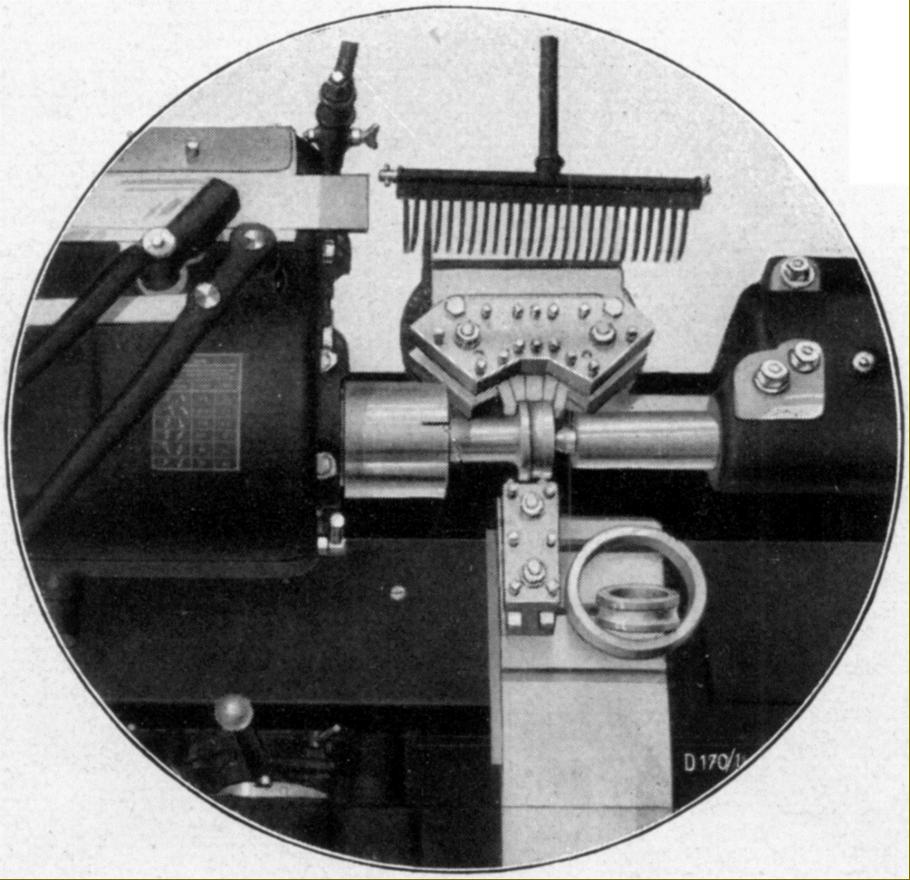 |
|
|
|
|
|
|
|
|
|
Turning the inner and out rings of a 150 mm diameter 35 mm wide ball bearing. The ring is held on an expanding mandrel actuated by a lever with the longitudinal and cross slides doing the roughing and finishing in one setting: time 1.5 minutes.
|
|
|
|
|
|
|
|
|
|
|
|
|
|
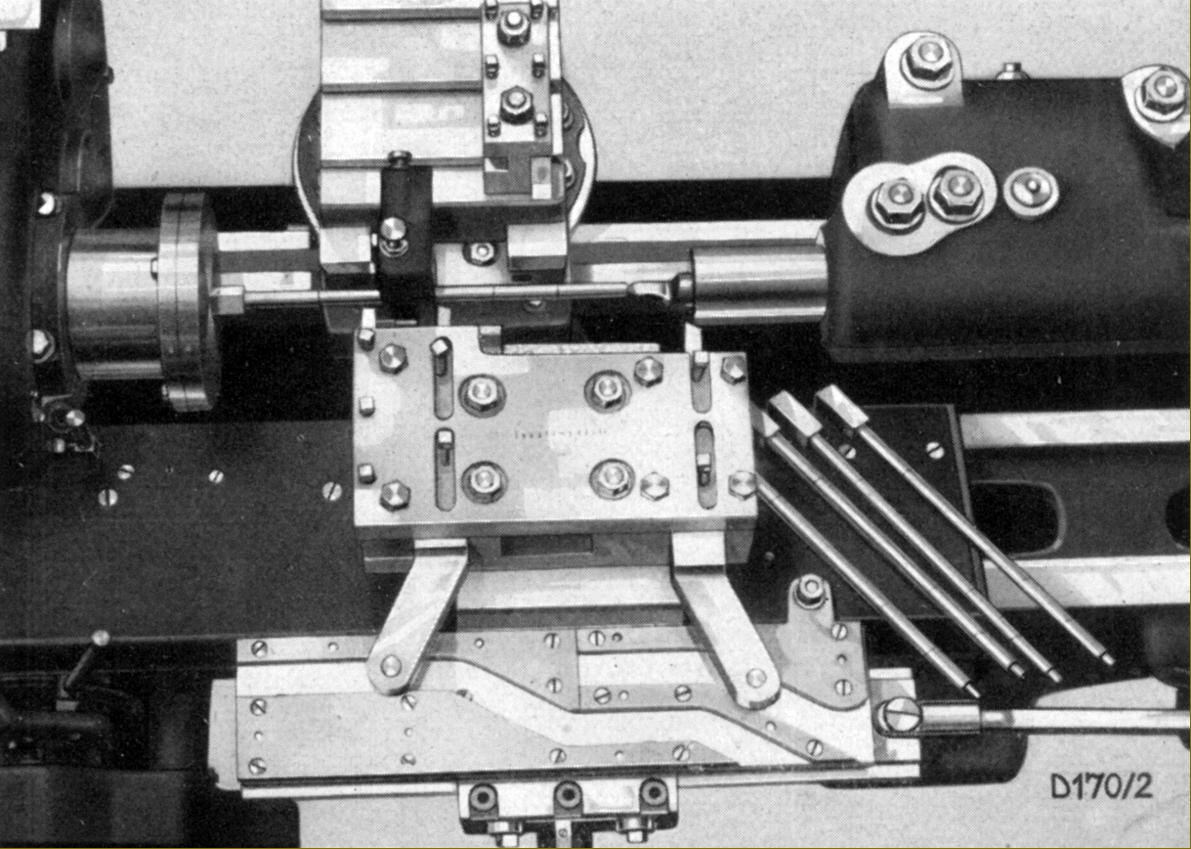 |
|
|
|
|
|
|
Turning push rods from an automobile gearbox. Made from 19 x 19 mm square bar the rods were 320 mm long and supported by a travelling roller steady. Machining time 4.5 minutes.
|
|
|
|
|
|
|
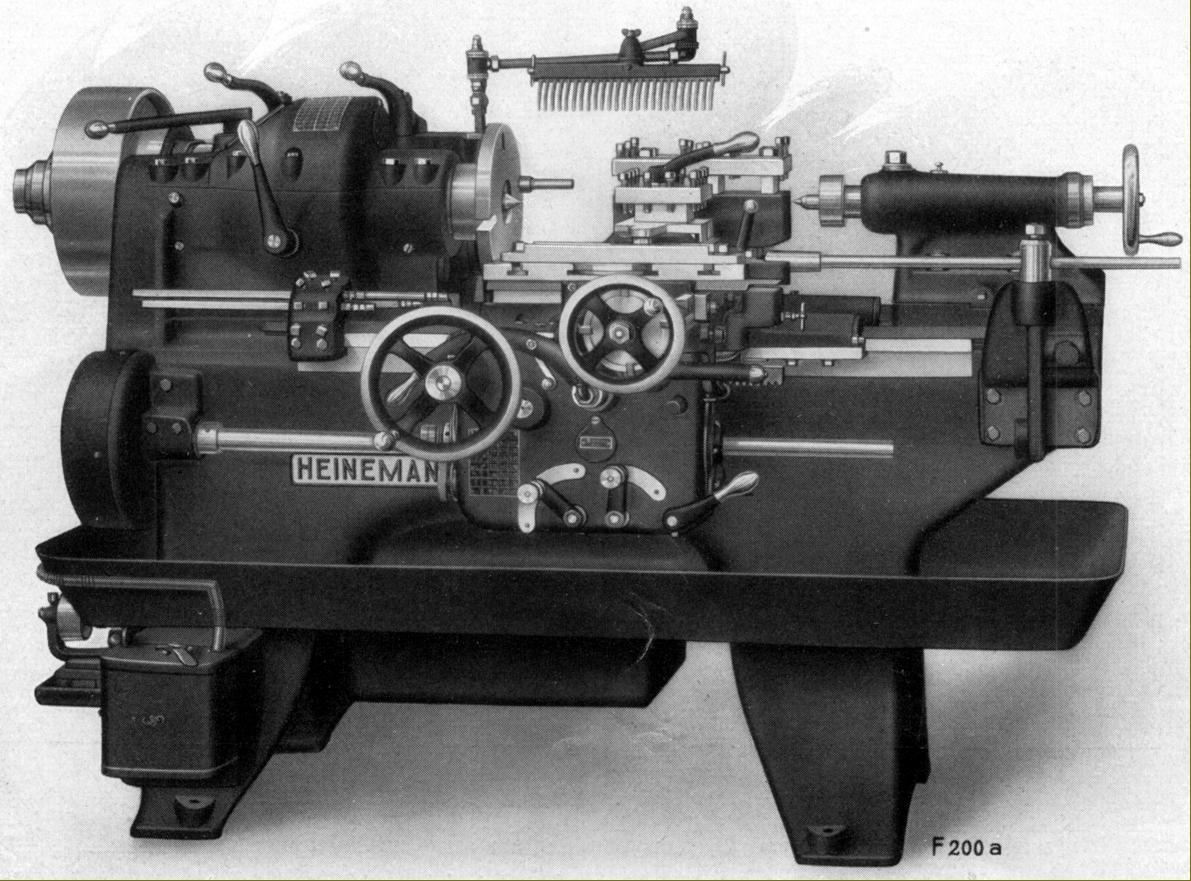 |
|
|
|
|
|
|
Production lathe Type F200. First exported to America, this lathe was designed for turning small quantities of repetition work that could not be done economically on a multi-tool lathe - or for work which, owing to its shape, did not allow the longitudinal and cross slides of such a lathe to work simultaneously. The makers reported that customers had employed the F200 for the manufacture of belt pulleys, multi-step cone pulley, changewheel blanks, bearings, bolts, plain and armature shafts, pistons and crankshafts, etc. It was also suggested that work started on a capstan or semi-automatic lathe could be finished to a high degree of accuracy by being mounted been centres on an expanding mandrel.
|
|
|
|
|
|
|
|
|
|
|
|
|
|