 |
 |
 |
 |
 |
 |
 |
 |
 |
 |
 |
 |
 |
 |
 |
 |
 |
 |
 |
 |
 |
 |
 |
 |
 |
 |
 |
 |
 |
 |
 |
 |
 |
 |
 |
 |
 |
 |
 |
 |
 |
 |
 |
 |
 |
 |
 |
 |
 |
 |
 |
 |
 |
 |
 |
 |
 |
 |
 |
 |
 |
 |
 |
 |
 |
 |
 |
 |
 |
 |
 |
 |
 |
 |
 |
 |
 |
 |
 |
 |
 |
 |
 |
 |
 |
 |
 |
 |
 |
 |
 |
 |
 |
 |
 |
 |
 |
 |
|
|
email: tony@lathes.co.uk Home Machine Tool Archive Machine-tools for Sale & Wanted Machine Tool Manuals Machine Tool Catalogues Belts Books Accessories
Cataract Lathe Accessories Cataract Accessories Cataract Stands & Drives Cataract Drills & Pinion Cutter
"Quick-change" Toolroom Lathe Cataract Millers Hardinge History
Cataract Home Page Hardinge Elgin Lathes & Millers
Literature for Cataract machines is available
|
|
|
|
|
|
|
|
|
|
|
|
|
|
|
|
|
|
|
|
|
|
|
|
|
|
|
|
|
|
|
|
|
|
|
|
|
|
|
|
|
|
|
|
|
|
|
|
|
|
|
|
|
|
|
|
|
|
|
|
|
|
|
|
|
|
|
|
|
|
|
|
|
|
|
|
|
|
|
|
|
|
|
|
|
|
|
|
|
|
|
|
|
|
|
|
|
|
|
|
|
|
|
|
|
|
|
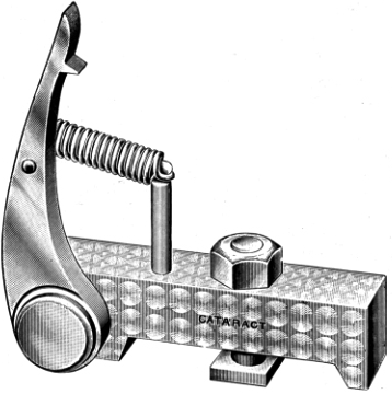 |
|
|
|
|
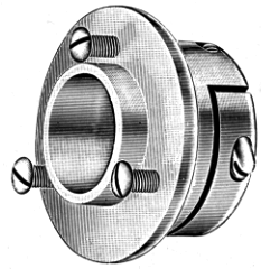 |
|
|
|
|
|
|
|
|
|
|
|
Above: Adaptor to carry Division Plates on the end of the headstock spindle.
Left: Latch Unit which clamped to the bed beneath the division plate and indexed rotation the headstock spindle.
|
|
|
|
|
|
|
|
|
|
|
|
|
|
All the cone driven (open-headstock) Cataract lathes were provided with a ring of 60 holes for indexing. When a greater range was required a special holder, to which division plates could be attached by three screws, could be clamped on the end of the headstock spindle. The headstock then had to be moved forwards slightly, and the latch unit fitted to the bed. A similar attachment was also available for the enclosed-headstock models
|
|
|
|
|
|
|
|
|
|
|
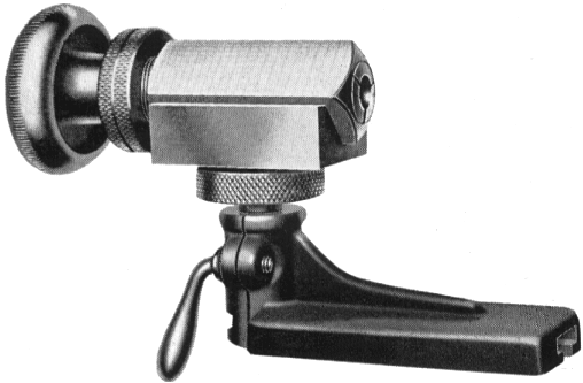 |
|
|
|
|
|
|
|
Screw Slotting or Milling Device. This unit was designed to allow the slotting of small screw heads and for performing milling operations that would otherwise have tied up a more valuable milling machine. It was used in conjunction with the headstock and a milling cutter or saw arbor. It was equipped to accept either the 3C, 4C or 5C collets supplied with the lathe. The complete collet holder could be lifted from the V block to ease the insertion of parts; the two knurled thumb nuts inboard of the collet drawbar wheel acted as an adjustable stop to set the depth of cut. The height of the unit could be varied by lifting it from the base casting - or finely adjusted with the large screwed ring above the locking handle.
|
|
|
|
|
|
|
|
|
|
|
|
|
|
|
|
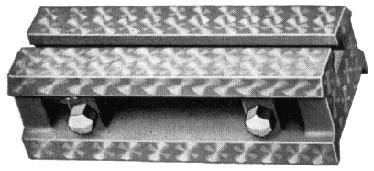 |
|
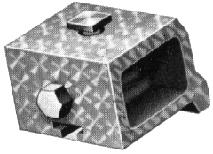 |
|
|
|
|
|
|
|
|
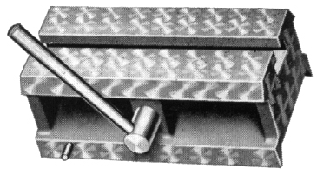 |
|
|
|
|
|
2" high Raising Blocks for the headstock, compound slide rest and tailstock. These blocks fitted all models of Cataract bench lathe.
|
|
|
|
|
|
|
|
|
|
|
|
|
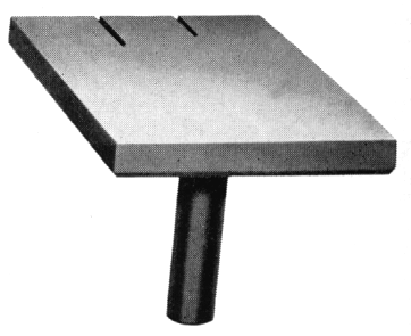 |
|
|
|
|
|
|
|
|
|
|
|
|
|
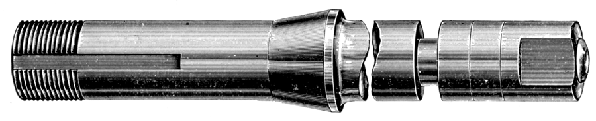 |
|
|
|
|
|
|
Saw Arbor - by which means fine slitting saws and light milling cutters could be mounted.
|
|
|
|
|
|
|
|
|
|
|
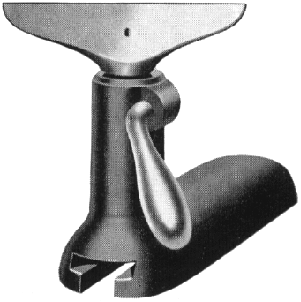 |
|
|
|
|
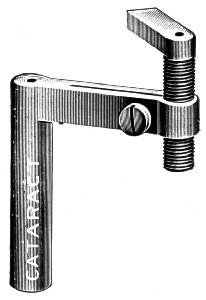 |
|
|
|
|
|
|
|
|
An L-shaped rest, to socket into the casting on the left, and designed to enable the worker to "get into awkward corners."
|
|
|
|
|
|
|
|
|
|
|
|
|
|
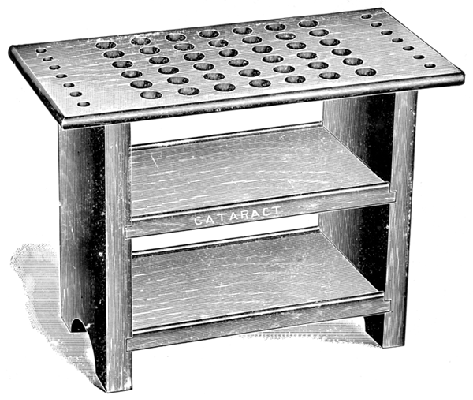 |
|
|
|
|
|
|
|
|
|
Constructed in Cherry wood, and made to special order only, this beautiful 14 " x 7" by 10.5" high accessory was designed as standard to take No. 3 "chucks" and centres - but could also be supplied with holes to the customer's own requirements.
|
|
|
|
|
|
|
|
|
|
|
|
|
|
|
|
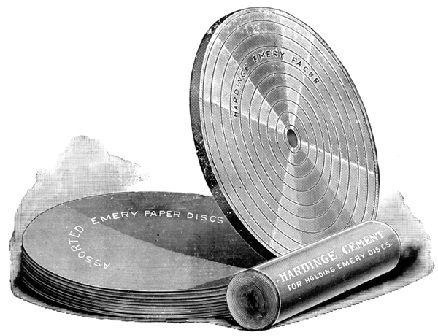 |
|
|
|
|
|
|
|
|
A large-diameter, cast-iron faceplate fitted with the standard cataract taper-and key-spindle nose fitting and designed to be covered with glued-on emery paper for finishing operations.
|
|
|
|
|
|
|
|
|
|
|
|
|
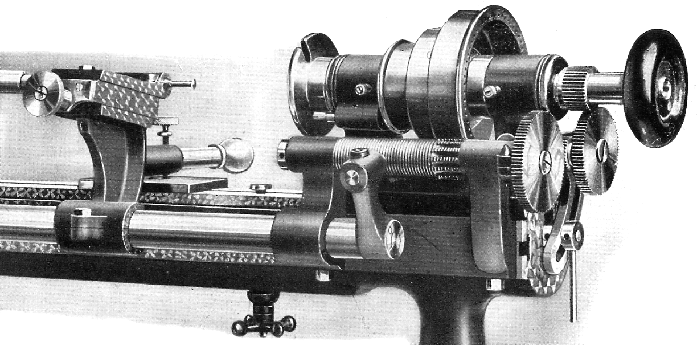 |
|
|
|
|
|
|
"Chase" Screwcutting Attachment and associated gearing
The Cataract lathe could, like most quality lathes of its type, be provided with either changewheel-driven "top-slide" or traditional "chase" screwcutting - the latter system was devised by Joseph Nason of New York who obtained US Patent No. 10,383 on January 3rd, 1854 for an "arrangement for cutting screws in lathes." In the Cataract interpretation a T slot, which ran down the back face of the specially-cast bed, held supports carrying a sliding transmission bar and, above it, a "master thread". At the headstock end of the assembly additional gearing was provided to extend the threading range (by a multiple of six) for each Thread Master used. A follower (with an interchangeable tip carrying a few threads of the same pitch) pressed into the Master Thread and transmitted its motion, via a sliding bar, to a threading tool held against the workpiece in an adjustable toolholder. Whilst this system produced absolutely-accurate threads, and was especially suited to delicate operations on the thin-wall tubes used to construct such items as microscopes and the bodies of camera lenses, the length of thread that could be cut, and the number of threads per inch or mm, depended upon the availability of the appropriate Thread Master. A useful touch was that Cataract Master Threads (like those from Pratt & Whitney) could be supplied complete with a hob at one end for chasing nuts to suit the thread being generated in the lathe. An alternative form of screwcutting, and the only type available on lathes with a "plain" bed, was provided with a set of changewheels and a splined, universally-joined shaft which drove the top slide; the arrangement is illustrated below..
|
|
|
|
|
|
|
|
|
|
|
|
|
|
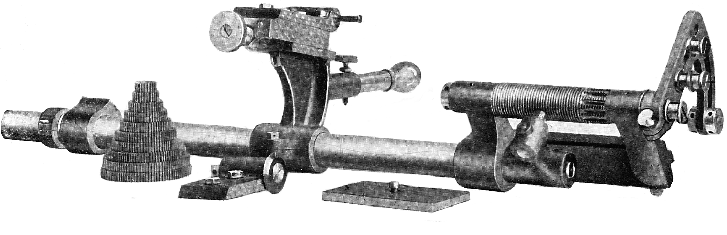 |
|
|
|
|
|
Component parts of the chase-screwcutting kit
|
|
|
|
|
|
|
|
|
|
|
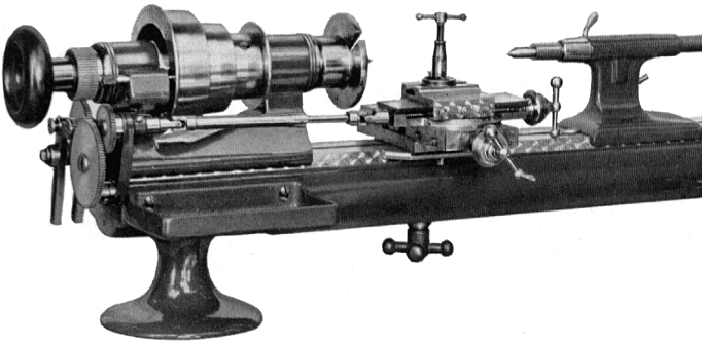 |
|
|
|
|
|
|
In order to provide a power feed, and a screwcutting facility, a sliding drive shaft, with universal joints, took motion from changewheels on a quadrant arm to the top slide. This was an accessory available from almost all makers of high-quality bench lathes.
|
|
|
|
|
|
|
|
|
|
|
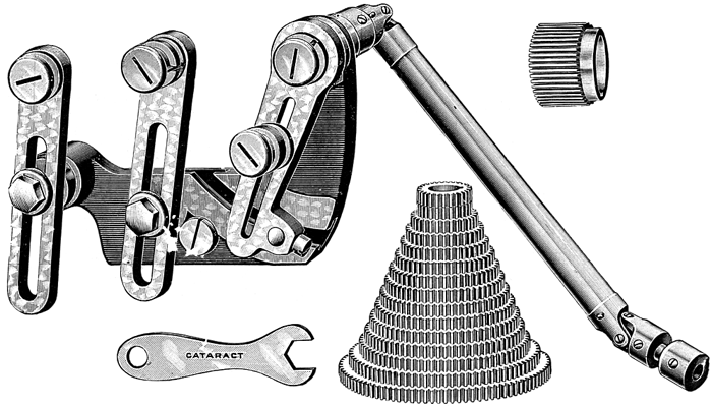 |
|
|
|
|
|
|
Component parts of the power-feed kit
|
|
|
|
|
|
|
|
|
|
|
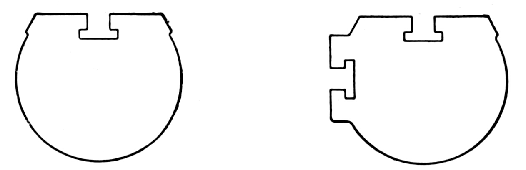 |
|
|
|
|
|
|
The beds for plain and screwcutting lathes were different; on the left is the "plain" bed and on the right that used when "chase screwcutting" was fitted.
|
|
|
|
|
|
|
|
|
|
|
|
|
|
|
|
|
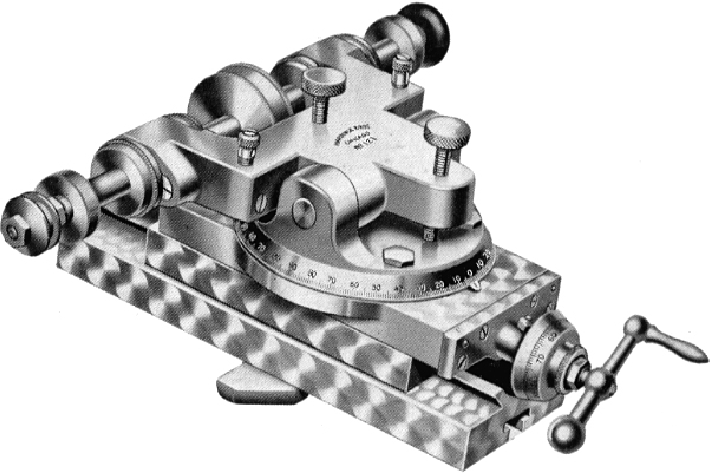 |
|
|
|
|
|
|
Cataract Universal Three-slide Grinder Although casual use of a lathe as a grinding machine can have grave consequences for its longevity, if careful precautions are taken to keep the abrasive dust away from slideways, screws and bearings, no harm need be done. In the days when one lathe might be called upon to perform many functions, all makers of precision bench lathes, including Cataract, offered their customers a comprehensive range of grinding attachments. Shown above is a unit designed to be used for both internal and external grinding, attached to the bed in the same manner as the compound slide rest. The middle slide was not fitted with a feed screw, but was provided with an adjustable stop so that the upper section of the unit could be instantly withdrawn from the work - and reset immediately in the same position without disturbing the setting of the feed dial. The hardened, ground and lapped spindle, 10" long, 0.490" in diameter with a Hardinge No. 3 taper in each end, had a maximum travel of 2.625" and could be run at 10,000 rpm. The swivel base was 4.5" in diameter and the upper part of the assembly was securely held to the lower by four bolts. In use, the longitudinal feed of the spindle was controlled by hand - the round black knob on the end, fitted with hardened and ground bearings, providing a thumb and finger grip; all the grinding attachments listed by the Cataract operated the sliding feed in this simple but effective way. Whilst comprehensive in range, and type, Cataract accessories were not greatly different from those of their competitors, with the possible exception of the beautiful "Universal Three-slide Grinder", shown below.
|
|
|
|
|
|
|
|
|
|
|
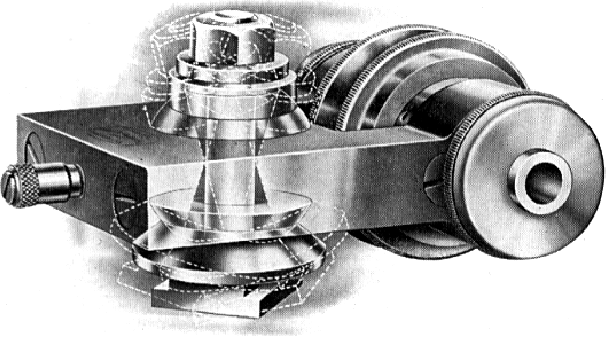 |
|
|
|
|
|
|
Universal Grinder This 10,000 rpm unit, only 3.625" x 4.5" x 2", was mounted on a stud which allowed universal movement around a vertical axis. Designed to allow the grinding of components which would otherwise have required specialised equipment and machinery, the device mounted in place of the toolpost - and hence its movements were controlled by the feed screws of the compound slide.
|
|
|
|
|
|
|
|
|
|
|
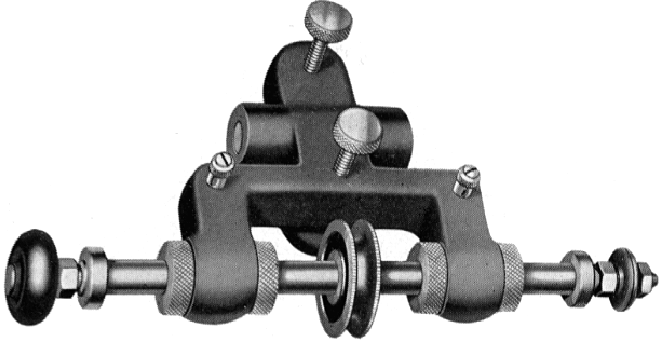 |
|
|
|
|
|
|
Adjustable Height Grinder This grinding head was held in the toolpost T slot of the top slide and its cross feed controlled by the slide rest feed screw. Suitable for internal and external grinding, the 8.125" long spindle, 0.490" in diameter and capable of 10,000 rpm was hardened, ground and lapped all over and fitted with a Hardinge No. 3 taper in each end - a feature which led the makers to claim that the spindle could be reversed to compensate for wear. As usual, the longitudinal feed was controlled by hand - the round black knob on the end, fitted with hardened and ground bearings, providing a thumb and finger grip with which to advance and return the spindle.
|
|
|
|
|
|
|
|
|
|
|
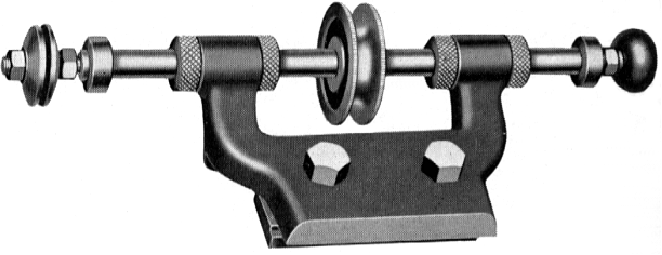 |
|
|
|
|
|
|
Permanent Height Grinder This was the simplest grinding head available for the cataract lathe and built to run exactly on centre height. The only means of making any adjustment was to pack shims underneath the base.
|
|
|
|
|
|
|
|
|
|
|
|
|
|
|
|
|
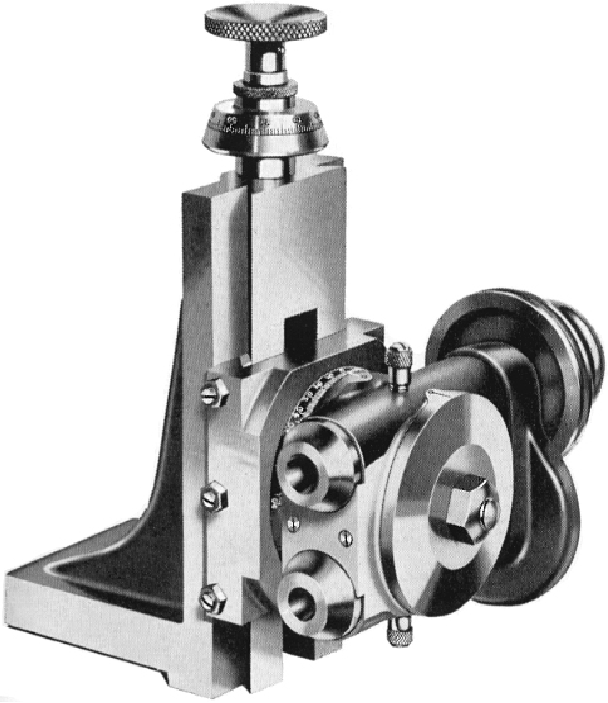 |
|
|
|
|
|
|
|
|
|
Surely unique amongst lathe-mounted milling slides this special twin-spindle Cataract unit can only have been equalled or outclassed by that available for lathes produced by the Waltham Machine Works. Intended to tackle difficult, precision-milling jobs the device was mounted in place of the toolpost, and so had available the full range of movements allowed by the compound slide rest. The cutter head carried two hardened, ground and lapped spindles, each revolving in adjustable bearings. One spindle carried a standard Hardinge 1C collet and draw bar, the other a No. 4 Brown & Sharpe taper. The cutter head could be swivelled and, by removing the retaining nut and inverting it on its seating , the heads made to change places. At the driven-end was 3 :1 gear set, with interchangeable driver and driven gears. Input speeds of 300 and 600 rpm from the overhead drive, or grinder countershaft, gave spindle speeds of 100, 200, 300, 600, 900 and 1800 rpm.
|
|
|
|
|
|
|
|
|
|
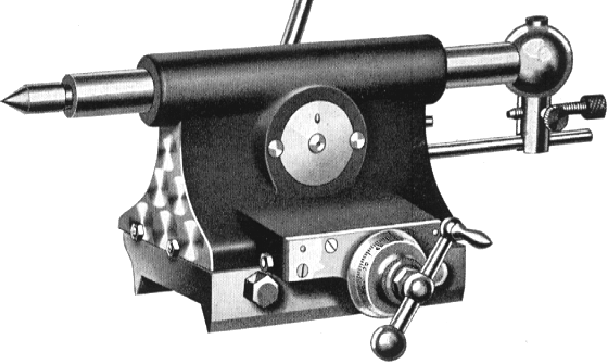 |
|
|
|
|
|
|
Lever-action Tailstock with Cross Feed This tailstock was, for its time, substantially built, and designed to assist in boring, chambering and facing operations whilst being also perfectly useable as a standard unit. The cross-slide movement was 2.25" and the micrometer dial was of the zeroing type. The barrel, 10.375" long and 0.787" in diameter, had a rack and pinion drive with a feed-length of 2.75". An adjustable stop, with a hardened pin, was fitted between the barrel and its steady rod.
|
|
|
|
|
|
|
|
|
|
|
 |
|
|
|
|
|
|
Spring Lever Tailstock This was designed for production drilling, reaming, counter-boring, tapping, etc., as well as for use a normal tailstock. However, the 9" long, 0.787" diameter barrel must have been limited in its usefulness by a maximum travel of only 1.25"
|
|
|
|
|
|
|
|
|
|
|
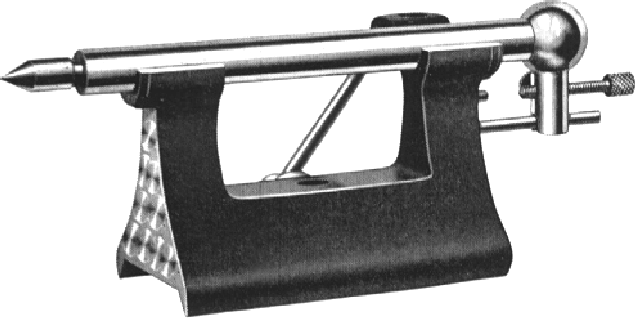 |
|
|
|
|
|
|
Half-open Tailstock This tailstock, of a type once popular with makers of similarly high-class lathes, was used for light drilling, tapping and reaming. The aim was to have several spindles available, each fitted with a different tool and so rapidly interchangeable; two spindles were provided as standard with each tailstock. This unit was also available fitted with a lever-feed mechanism.
|
|
|
|
|
|
|
|
|
|
|
|
|
|
|
|
|
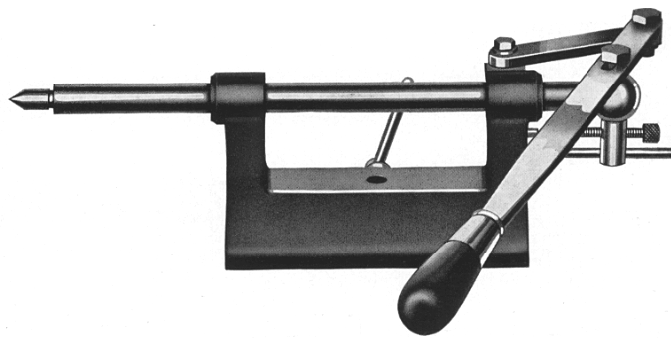 |
|
|
|
|
|
|
Long-stroke (5.5") lever-action tailstock This unit was specially adapted for the drilling of very precise, deep holes in the manufacture of fountain pens and automatic pencils - whose makers often employed banks of Cataract lathes in their works.
|
|
|
|
|
|
|
|
|
|
|
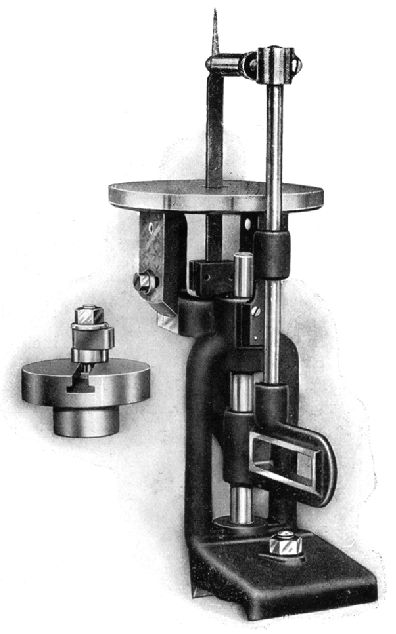 |
|
|
|
|
|
|
|
|
A powered filing attachment - driven from the lathe spindle nose by an adjustable eccentric. This useful accessory was intended for the finest of work by the most skilled of workers.
|
|
|
|
|
|
|
|
|
|
|
|
|
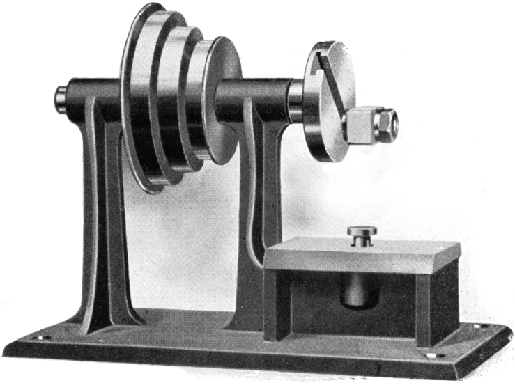 |
|
|
|
|
|
|
|
|
Filing Attachment Stand Where the filing attachment was in regular use, or the lathe busy, this separate stand and drive system was available which made the unit self-contained.
|
|
|
|
|
|
|
|
|
|
|
|
|
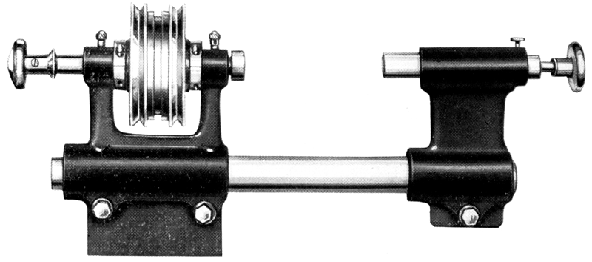 |
|
|
|
|
|
|
Horizontal Tapping Machine. The unit was intended for the rapid tapping of small parts; both headstock and tailstock were sized to accept No. 1 cataract draw-in collets - which had a maximum capacity of 0.25" - and the workpiece could be held in either. The headstock carried two "round-rope" pulleys, each intended to be driven in opposite directions and engaged by a simple cone clutch fitted between them. By this means the tap could be run into the job, then immediate reversed out by engaging the other drive - although the lever system which accomplished this task was not illustrated in the maker's catalog.
|
|
|
|
|
|
|
|
|
|
|
|
|
|
|
|
|
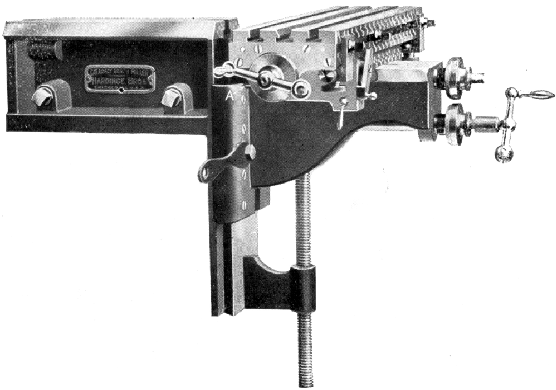 |
|
|
|
|
|
|
Horizontal Milling Attachment This neat assembly bolted to the end of the lathe bed and employed the headstock - in a reversed setting - to provide a cutter holding facility. More information about cataract Millers can be found here.
|
|
|
|
|
|
|
|
|
|
|
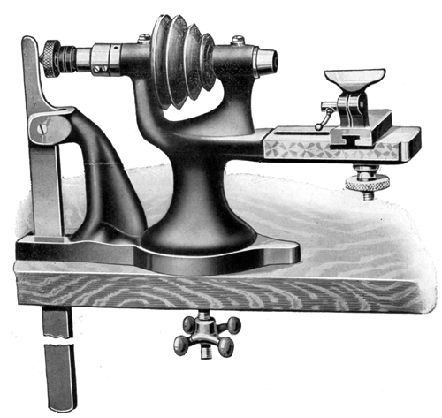 |
|
|
|
|
|
|
|
|
A special "Speed Lathe" model the "Cataract No. 1 Filing Head" or "Lathe A" - used for polishing and simple hand turning. The (foot-operated) lever bearing against the end of the spindle was used to open and close collets quickly for production work.
|
|
|
|
|
|
|
|
|
|
|
|
|
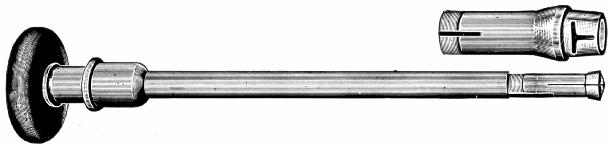 |
|
|
|
|
|
|
Standard draw-in collet draw tube shown with a special collet carry a replica of the standard Cataract spindle-nose fitting.
|
|
|
|
|
|
|
|
|
|
|
 |
|
|
|
|
|
|
A special "Auxiliary Chuck" Accessory with a step-down Cataract No. 1 Collet accept smaller collets for ultra-fine work. Cataract made a huge range of collets (called at the time "chucks") to fit a wide variety of other makers' machines. The tradition is continued today with Hardinge, the company who bought Cataract, being one of the world's largest suppliers of collets.
|
|
|
|
|
|
|
|
|
|
|
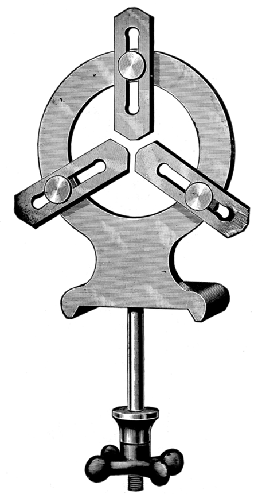 |
|
|
|
|
|
|
|
|
|
|
|
|
|
|
|
|
|
|
|
Cataract Accessories Cataract Stands & Drives
Cataract Drills & Pinion Cutter
"Quick-change" Toolroom Lathe Cataract Millers
Hardinge History
Cataract Home Page Hardinge Elgin Lathes & Millers
Literature for Cataract machines is available
Cataract Lathe Accessories email: tony@lathes.co.uk Home Machine Tool Archive Machine-tools for Sale & Wanted Machine Tool Manuals Machine Tool Catalogues Belts Books Accessories
|
|