 |
 |
 |
 |
 |
 |
 |
 |
 |
 |
 |
 |
 |
 |
 |
 |
 |
 |
 |
 |
 |
 |
 |
 |
 |
 |
 |
 |
 |
 |
 |
 |
 |
|
|
|
|
|
|
|
|
|
|
|
|
|
|
|
|
|
|
|
|
|
|
|
|
|
|
|
|
|
|
|
|
|
|
|
|
|
|
|
|
|
|
|
|
|
|
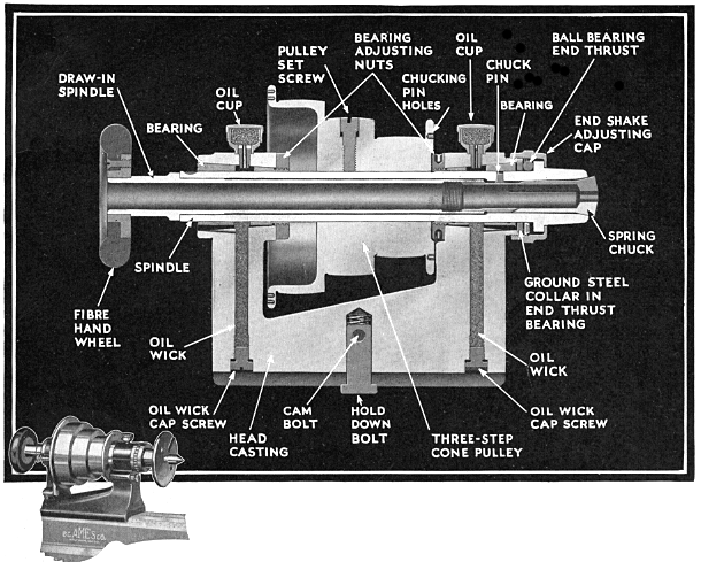 |
|
|
|
|
|
|
Section through an early Ames bench-lathe headstock. The headstock was available in two sizes (but of the same centre height) to take collets with a maximum capacity of either 5/8" or 1" with spindle bores of 3/4" and 11/8" respectively. The collets could be of either the draw-in type, or closed by a lever mechanism. The hardened spindle was machined from a solid bar of alloy steel, case hardened then ground and lapped. This method of production produced a spindle which was hard on the outside but "soft" within - and consequently extremely tough. The outside of the spindle front was ground to a 4 degree taper onto which faceplates, chucks and the larger sizes of step collets and their closers could be drawn. The inside of the spindle nose was ground to an 11 degree taper to seat and close collets. The cast-iron headstock bearings, oil-grooved and finely lapped, were parallel on the inside and tapered on the outside. Adjusting nuts, acting on square-section threads, drew the bearings into tapered seats within the headstock casting and compressed them concentrically. The combination of a hardened steel spindle running in cast-iron bearings was a proven method of obtaining long life and cool running; the spindle end thrust was taken by a ball race, positioned immediately behind the spindle nose, and carrying an adjusting ring to limit end play. The location of the thrust bearing, immediately behind the chuck on the "end" of the spindle, was unknown on any other lathe of this (precision) type. The larger of the pulley flanges carried two rings of 60 and 72 indexing holes, with a further ring of larger holes around the smaller flange which designed to assist in the removal of chucks and collets, etc., from the spindle nose. Later Ames lathes followed the lead of Wade in fitting their bench lathes with precision ball-bearing headstocks - the lathe illustrated here is so equipped..
|
|
|
|
|
|
|
|
|
|
|
|
|
|
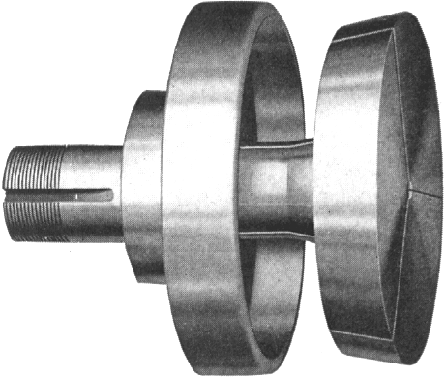 |
|
|
|
|
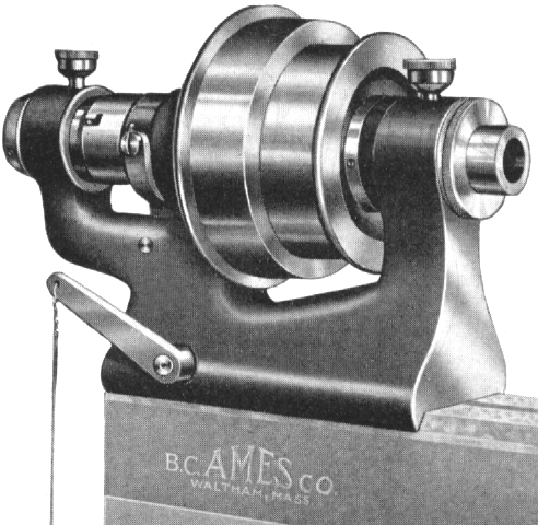 |
|
|
|
|
|
"Step chuck" with its external closing adaptor. Step chucks were used to hold diameters larger than the headstock spindle would admit. They were made of cast iron and supplied with a 1/4" hole drilled through the centre. To use them, the face was turned out to a suitable depth and diameter to accommodate the workpiece, which was then tightly gripped as the collet was drawn back against the closing ring. They were made in 2" and 4" diameters for both the 5/8" and 1" capacity headstocks.
|
|
|
|
|
|
|
|
|
|
|
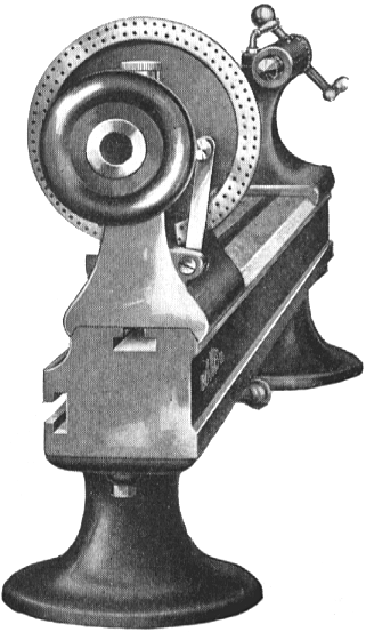 |
|
|
|
|
|
|
|
|
The Three-bearing, 2-step pulley Headstock was designed for production work. An extension at the left-end of the headstock carried a third bearing which supported an integral, quick-action collet opening and closing device. The device was intended to overcome the inherent tendency of collets to draw work backwards when they were tightened, making it difficult to obtain exact depth setting on repetition work. In this design the collet remained "stationary" whilst, ingeniously, the headstock spindle moved forwards and backwards to tighten and release it. The mechanism was foot-operated, so leaving the operator's hands free to manipulate the compound slide rest, or other attachments, and feed material into the collet. 2-step pulleys were also used on other examples of precision bench lathes adapted for production work, including those by W.H.Nichols and Bausch & Lomb
|
|
|
|
|
|
|
|
|
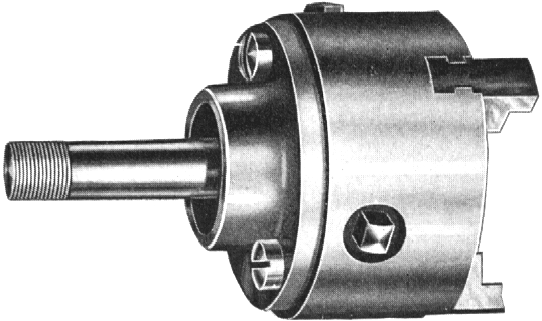 |
|
|
|
|
|
|
|
|
3-jaw chuck showing the backplate with its tapered seat which drew onto the 4 degree taper on the outside of the headstock spindle.
|
|
|
|
|
|
|
|
|
|
|
|
|
|
|
|
End view of bed showing the double ring of 60 and 72 indexing holes on the spindle-pulley flange.
|
|
|
|
|
|
|
|
|
|
|
|
|
|
|
|
|
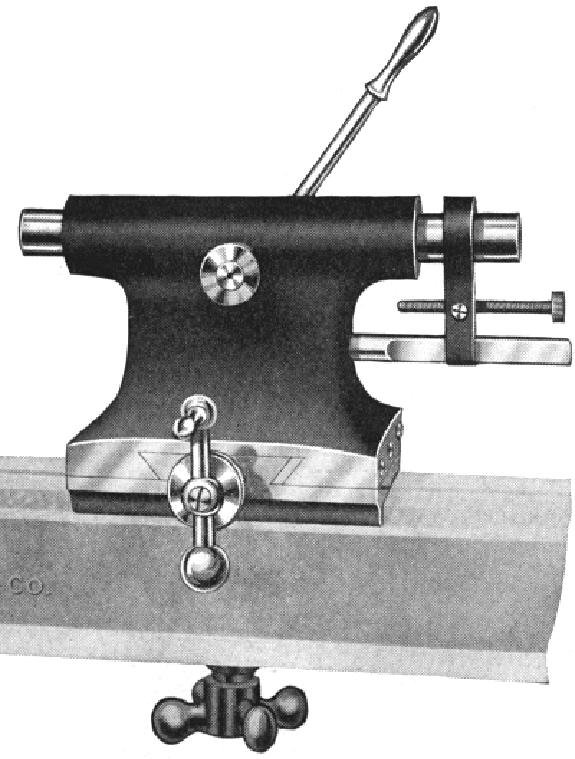 |
|
|
|
|
|
|
A common accessory on high-class bench lathes - a lever-action tailstock fitted to a screw-operated cross slide.
|
|
|
|
|
|
|
|
|
|
|
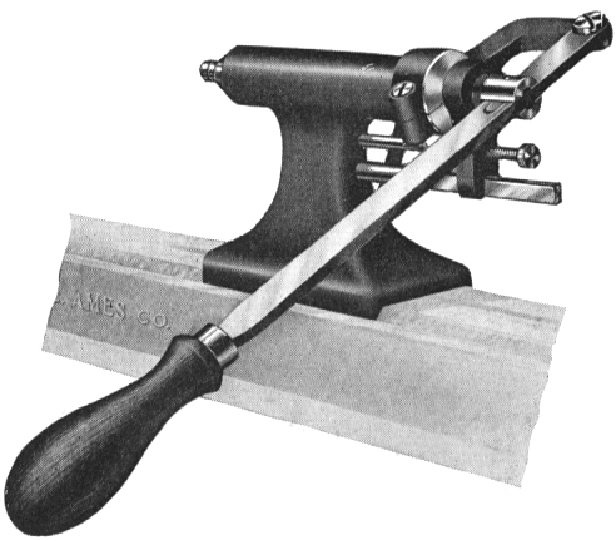 |
|
|
|
|
|
|
A standard tailstock with lever control of the 3" travel barrel - by far the best way of feeling what is happening to small drills, reamers and taps, etc. The long handle multiples the reaction of the tool to its job and so gives vastly superior control in comparison with a screw-operated feed.
|
|
|
|
|
|
|
|
|
|
|
|
|
|
|
|
|
|