 |
 |
 |
 |
 |
 |
 |
 |
 |
 |
 |
 |
 |
 |
 |
 |
 |
 |
 |
 |
 |
 |
 |
 |
 |
 |
 |
 |
 |
 |
 |
 |
 |
 |
|
|
|
|
E-MAIL Tony@lathes.co.uk Home Machine Tool Archive Machine-tools for Sale & Wanted Machine Tool Manuals Machine Tool Catalogues Belts Books Accessories
Cincinnati Toolmaster Milling Machines Model MT Toolmaster Home Page Toolmasters Type DD Toolmaster Type MT Cincinnati Home Page Dial Type Millers Cinedo Millers Contourmaster 8" x 18" Tool & Die Miller If you have an MT Toolmaster the writer would be interested to hear from you
Operation Manual for the MT Toolmaster available here Maintenance & Parts Manuals for the MT Toolmaster available here
Model MT Produced (it is believed) from late 1971 onwards, the third and final version of the Toolmaster, the MT, was very similar in general appearance to the DD but with numerous detail differences and revised controls. The miller was available in four models that varied only in their table, saddle and knee feed arrangements, these could be: all-manual feeds, one axis drive, two axis drive or a three axis drive with variable-speed DC motors. In addition, the customer was once again offered a choice of vertical heads with the inclusion of a 3 h.p. heavy-duty, all-geared overarm Type HV (versions of which had been offered for many years on other Cincinnati models) or the option of a high-speed head with a 3 h.p. motor replacing the standard 2 h.p. By using drive motors of different speeds the geared-overarm was offered with a choice of four speed ranges: 60 to 900 r.p.m, 75 to 1130 rpm., 90 to 1330 r.p.m. or 115 to 1730 r.p.m - with models on a 60 Hz supply running some 15 to 20% faster. Whilst the standard (variable-speed) head included a reduction gearbox - and ran from 80 to 3100 r.p.m. on a 50 Hz supply (80 to 3600 r.p.m. on 60 Hz) - the 3 h.p. high-speed version had a single, belt-drive-only range that spanned 1200 to 6000 r.p.m. and was fitted with just a fine-feed handwheel - there being no quick-action drilling lever. With just very high speeds available, the 3 h.p. head was not suitable for the fitting of either power down-feed or a tapping attachment - though both these accessories could, of course, be used on the 2 h.p. model. All heads had a 40 NS nose as standard, though the option was available, at extra cost, of a Cintiloc spindle quick-change nose that did away with the need for a drawbar and, on the 3 .h.p. head only, two additional factory-fitted options of Erickson or Kwick Switch collet holders. Table and Feeds Having offered both 42 and 51-inch tables on the DD, Cincinnati now settled on a compromise 48" x 12" table with a (hand-feed) longitudinal travel of 30 inches, a cross feed of 10 inches and vertically (unchanged) at 17 inches. However, although not listed amongst the options, it is almost certain that a customer would have been able to specify a longer table if needed. One turn of either table handwheel - these were now a full-circle safety type with folding grips - moved the table 6mm on metric machines and 0.2-inches on inch versions. The metric dials were graduated into 300 divisions, equal to 0.02 mm of movement per graduation, and the inch versions calibrated so that their 200 divisions represented a table movement of 0.001-inch per interval. Instead of the handy variable-speed units used on the table, saddle and knee of the DD, on the MT these drives (except on the DC-motor type) reverted to the earlier Toolmaster type of a fixed-ratio gearbox, each with a separate motor. These offered ten feed rates from ½-inch to 90-inches per minute on 50 Hz, and from ¾" to 108-inches on 60 Hz. Rapids were included with all the power-feed models - though as a result there was a reduction in hand-feed table travel of a little over 1.5-inches, the effect being compounded by the incorporation of permanently-mounted, automatic safety disengage stops at each end of the table's front-face T-slot. The DC model (easily recognised by the downward-pointing motor underneath the left-hand end of the table) could be fitted with a plug-board control system that enabled programming cycles to be constructed in up to thirty-two steps and fourteen functions: four each of longitudinal and across, five vertical and rapids. In addition, extra functions could be also be programmed including the use of coolant, an indexing table, or a cycle interrupt, etc. Lubrication was, as before, by a pair of one-shot lubricators (pull and release) or, at extra cost, by a fully automatic system with a pumped supply to the sliding surfaces..
|
|
|
|
|
|
|
|
|
|
|
|
|
|
|
|
|
|
|
|
|
|
|
|
|
|
|
|
|
|
|
|
|
|
|
|
|
|
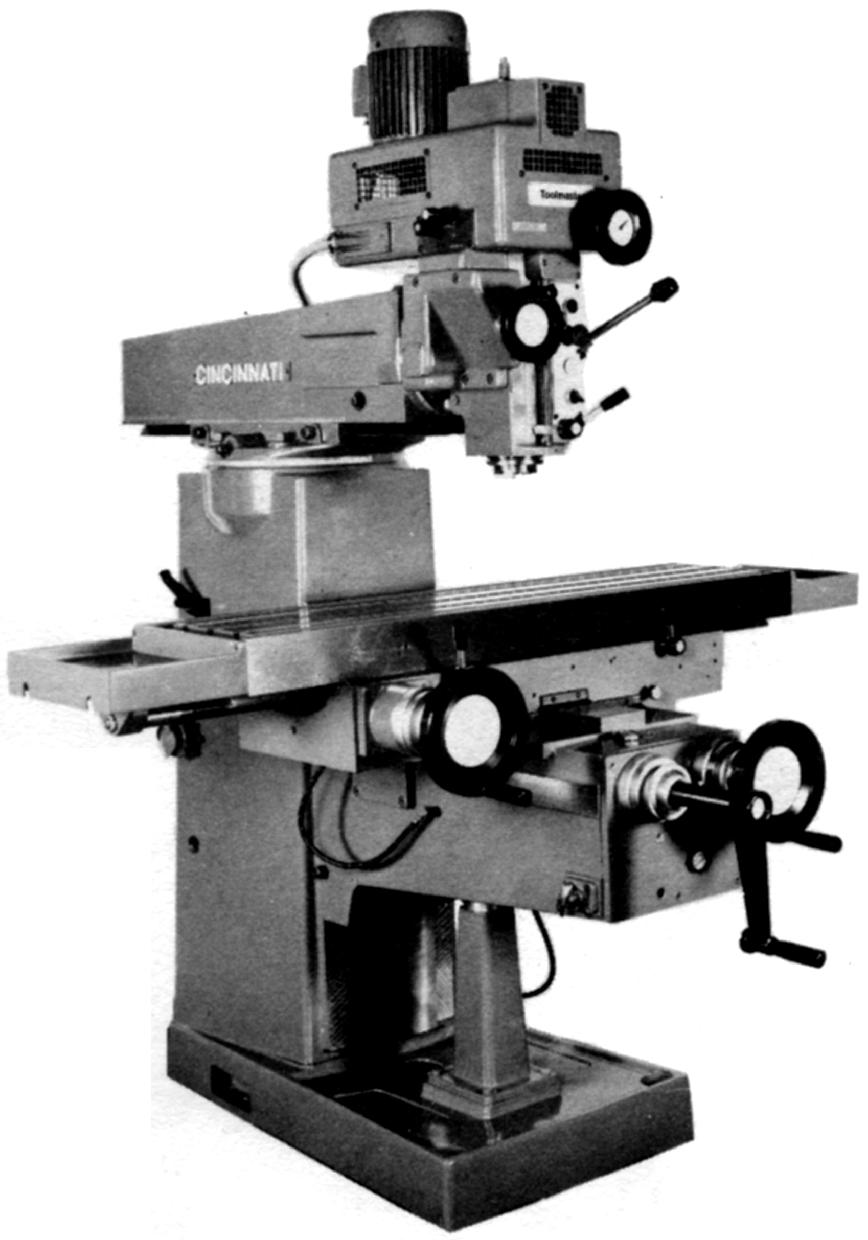 |
|
|
|
|
|
|
Toolmaster Model MT in basic specification with hand feed to table and quill
|
|
|
|
|
|
|
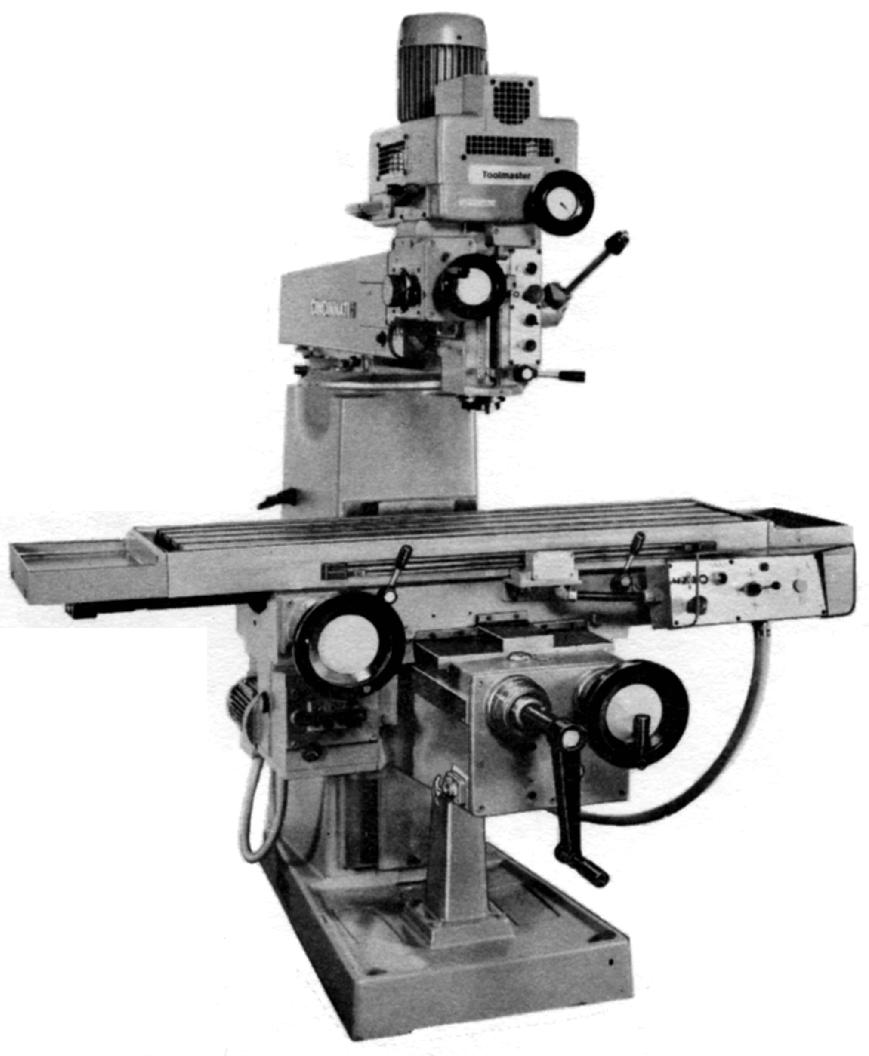 |
|
|
|
|
|
|
Toolmaster MT with single axis (table) drive and a power-feed attachment to the quill
|
|
|
|
|
|
|
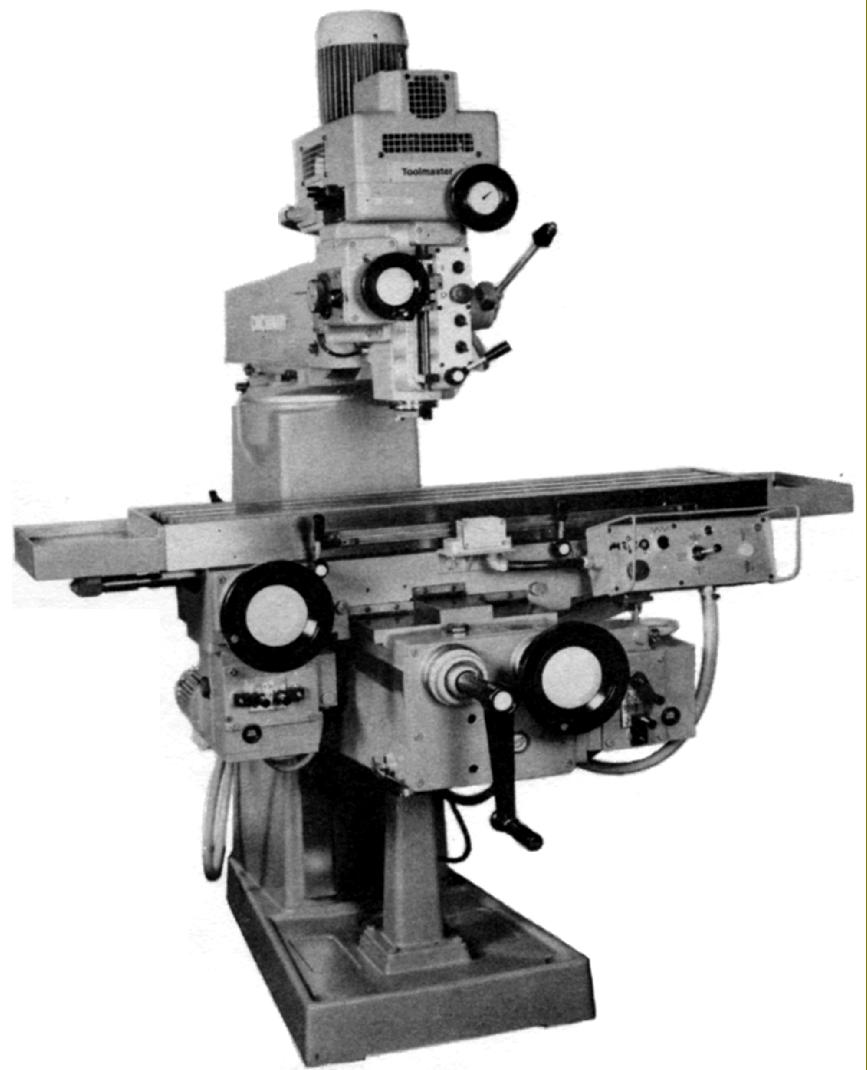 |
|
|
|
|
|
|
Toolmaster MT with 3-axis drive - table, saddle and quill
|
|
|
|
|
|
|
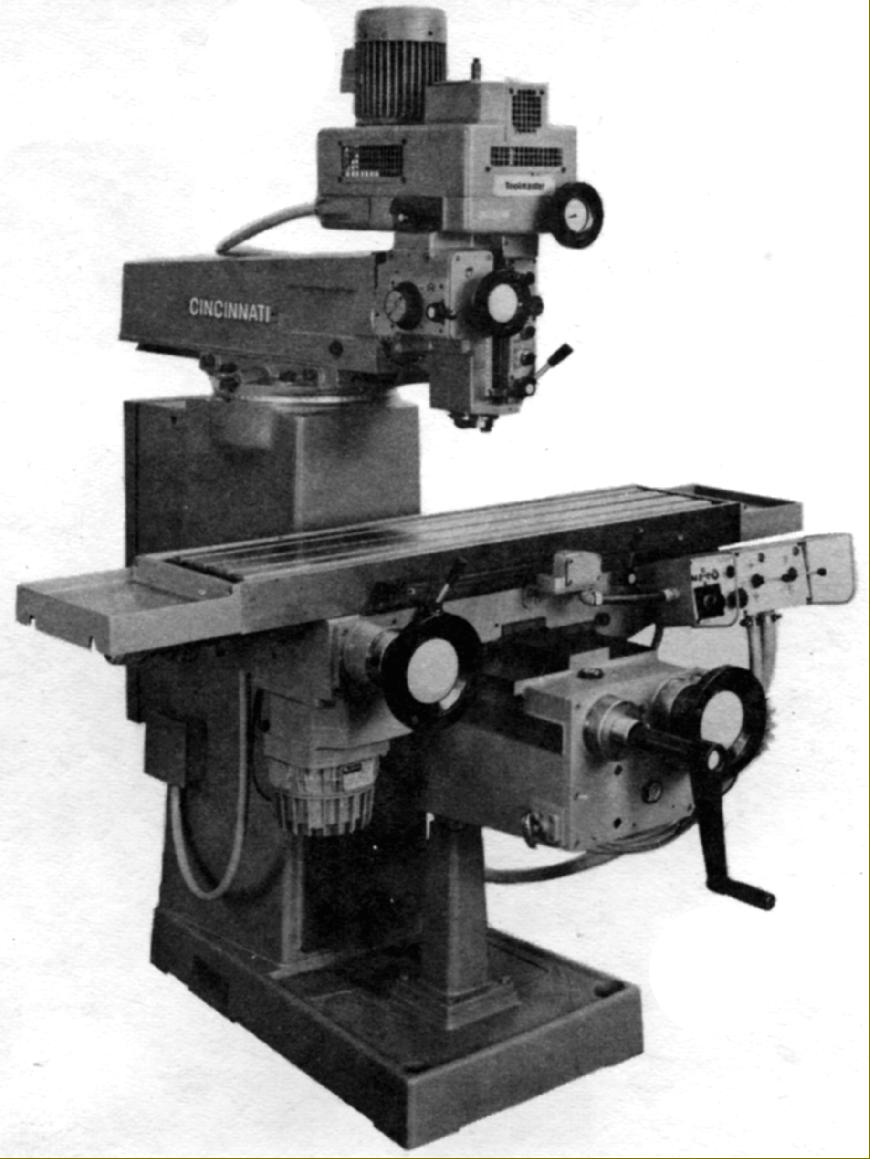 |
|
|
|
|
|
|
Toolmaster Mt with 3-axis DC variable-speed motor drive
|
|
|
|
|
|
|
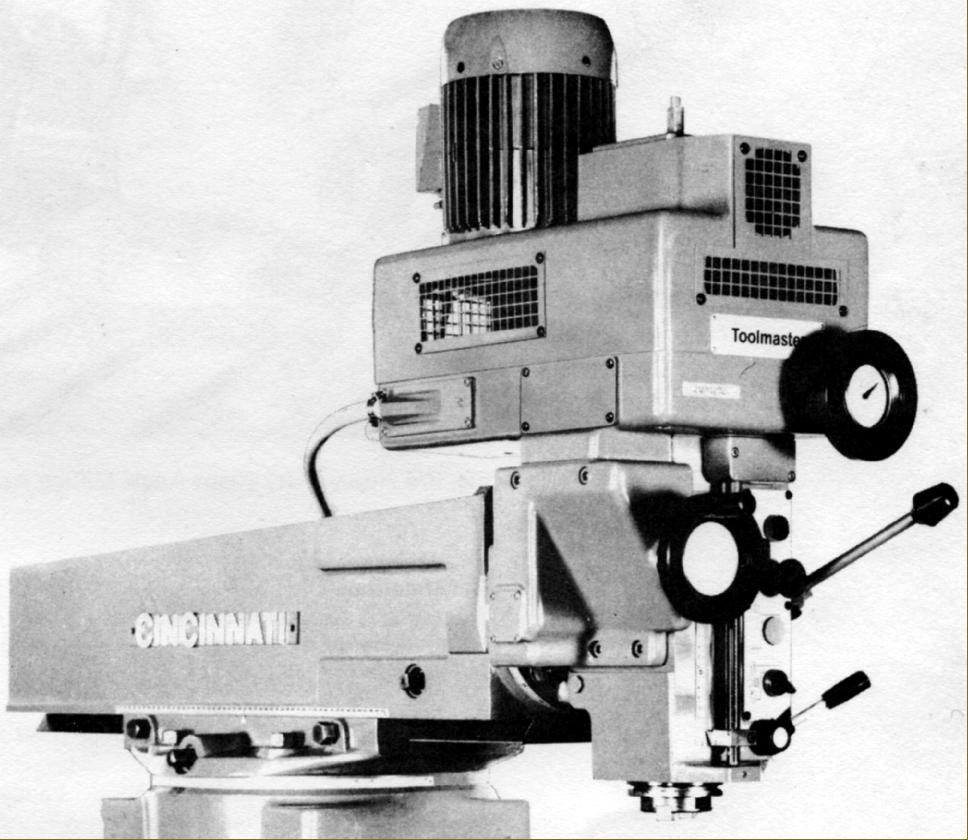 |
|
|
|
|
|
|
High-speed 3 h.p. head with a belt-drive-only speed range that spanned 1200 to 6000 r.p.m.
|
|
|
|
|
|
|
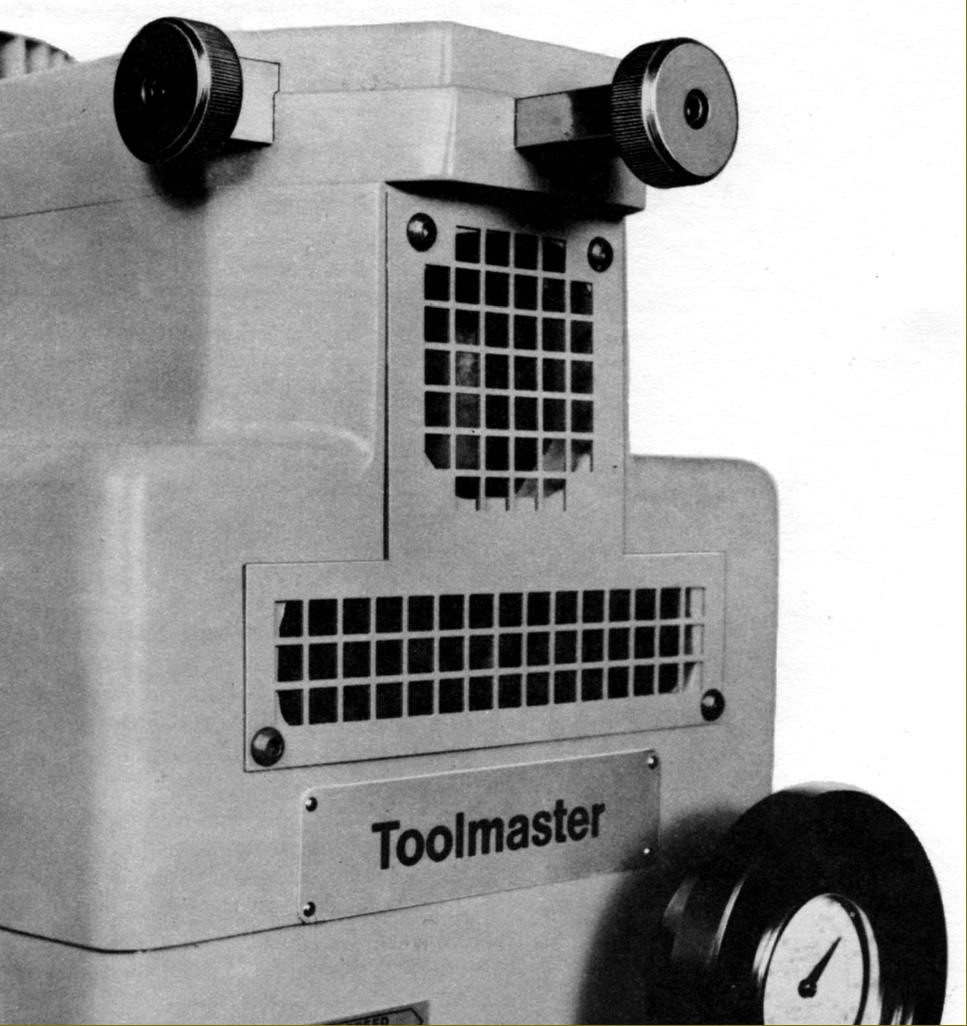 |
|
|
|
|
|
|
Optional extra - a draw-bar lock. This two-button device locked the draw-bar during tool changes and incorporated a microswitch to electrically isolate the spindle motor.
|
|
|
|
|
|
|
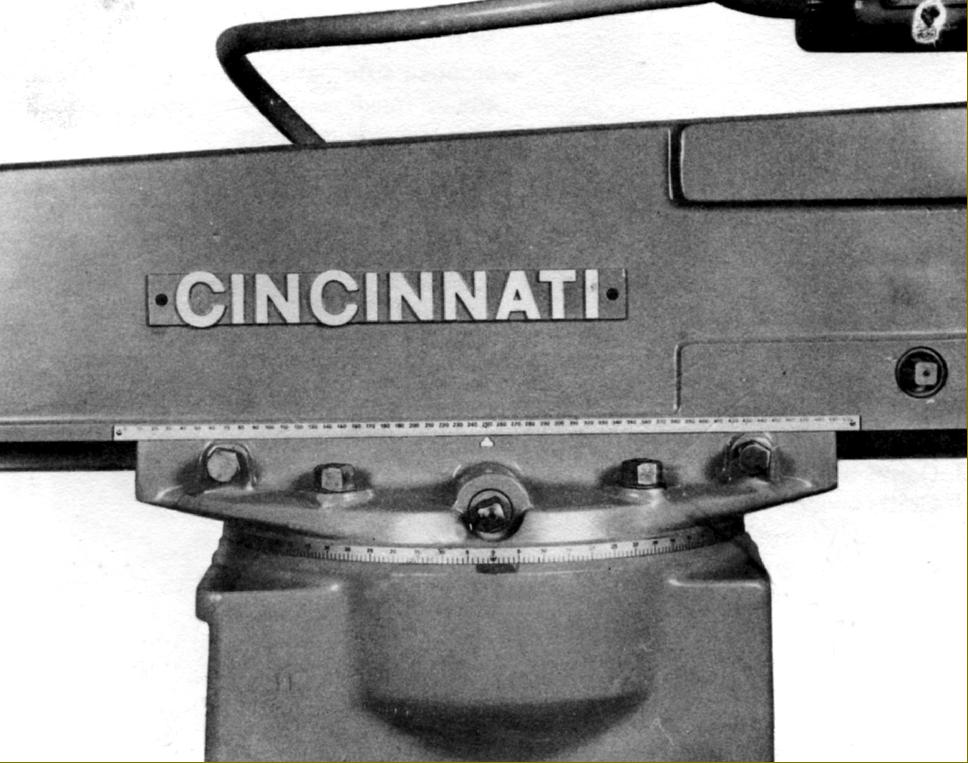 |
|
|
|
|
|
|
Ram swivel on top of the column. The ram extended by rack-and-pinion gearing
|
|
|
|
|
|
|
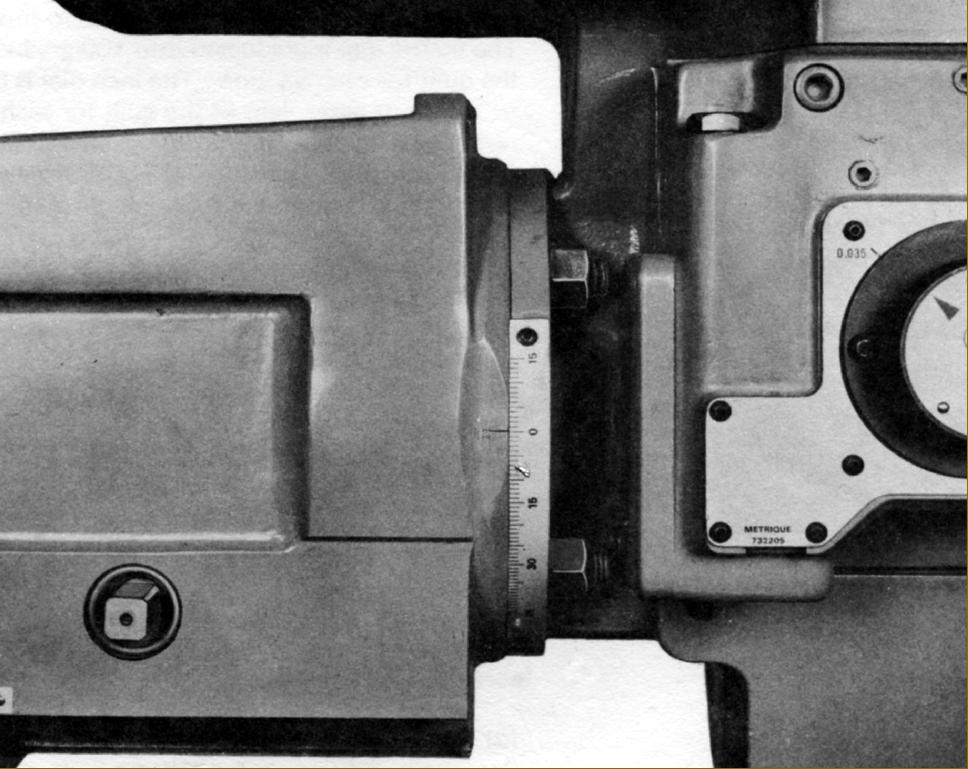 |
|
|
|
|
|
|
The head was secured to the end of the ram with four bolts and turned by worm-and-wheel gearing
|
|
|
|
|
|
|
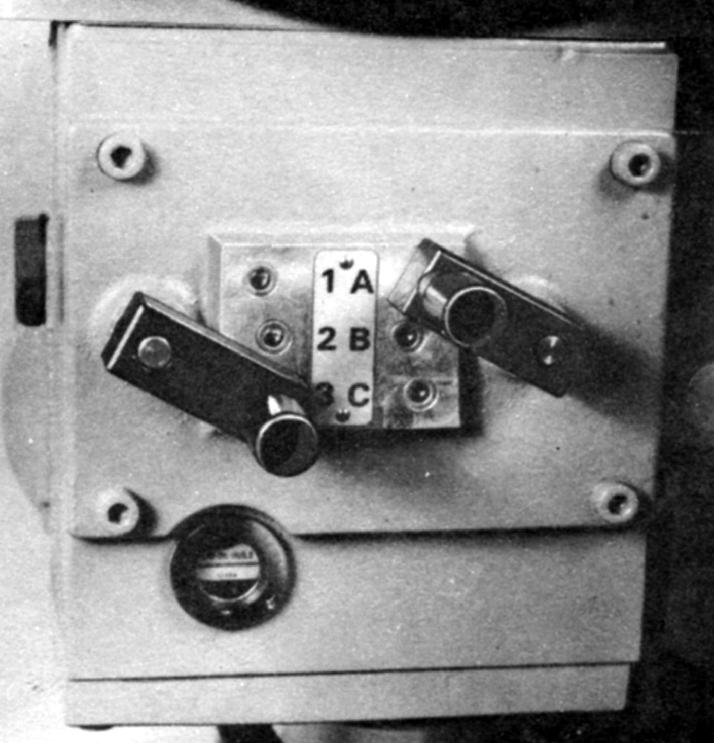 |
|
|
|
|
|
|
Table-feed gearbox controls
|
|
|
|
|
|
|
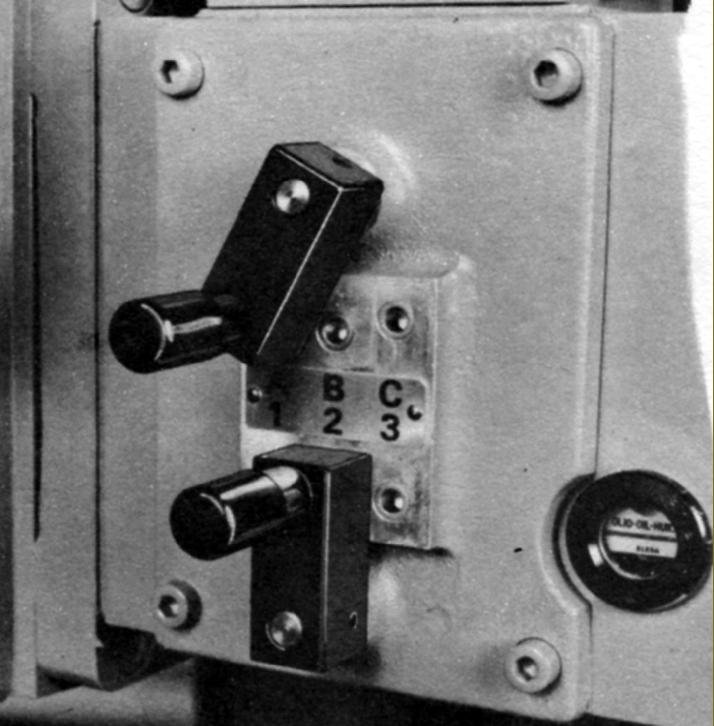 |
|
|
|
|
|
|
|
|
|
Saddle-feed gearbox controls
|
|
|
|
|
|
|
|
|
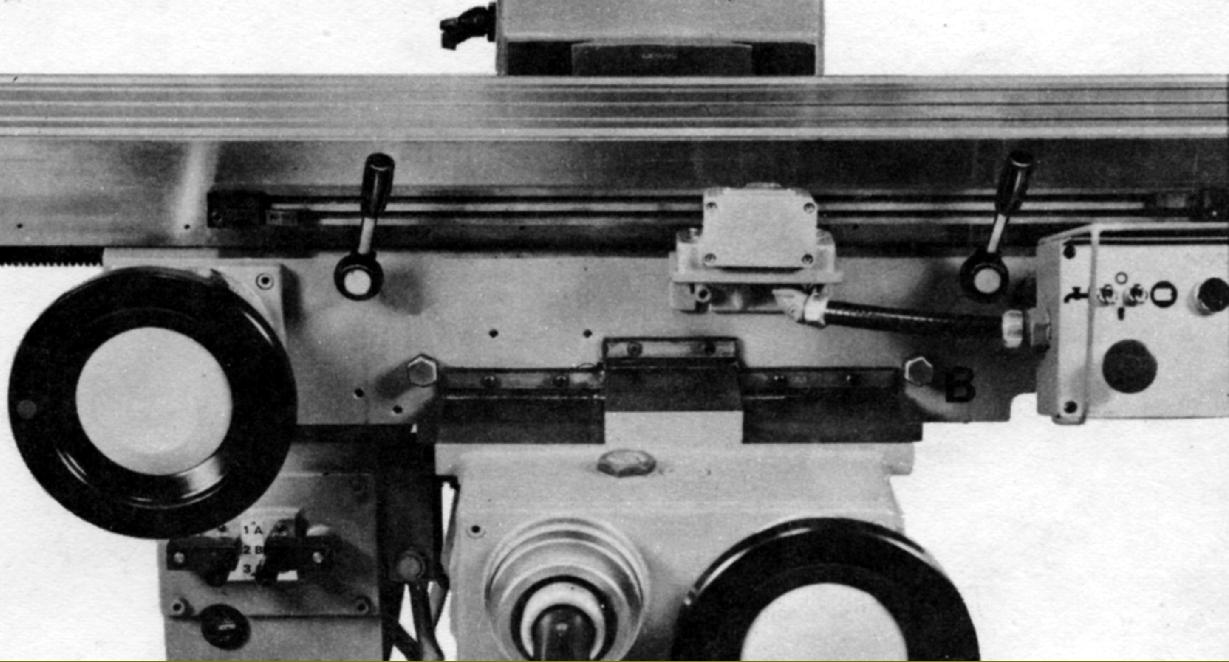 |
|
|
|
|
|
|
|
|
Toolmaster MT table and knee. Note the less-than-full-length T-slot in the front of the table - an instant MT recognition point
|
|
|
|
|
|
|
|
|
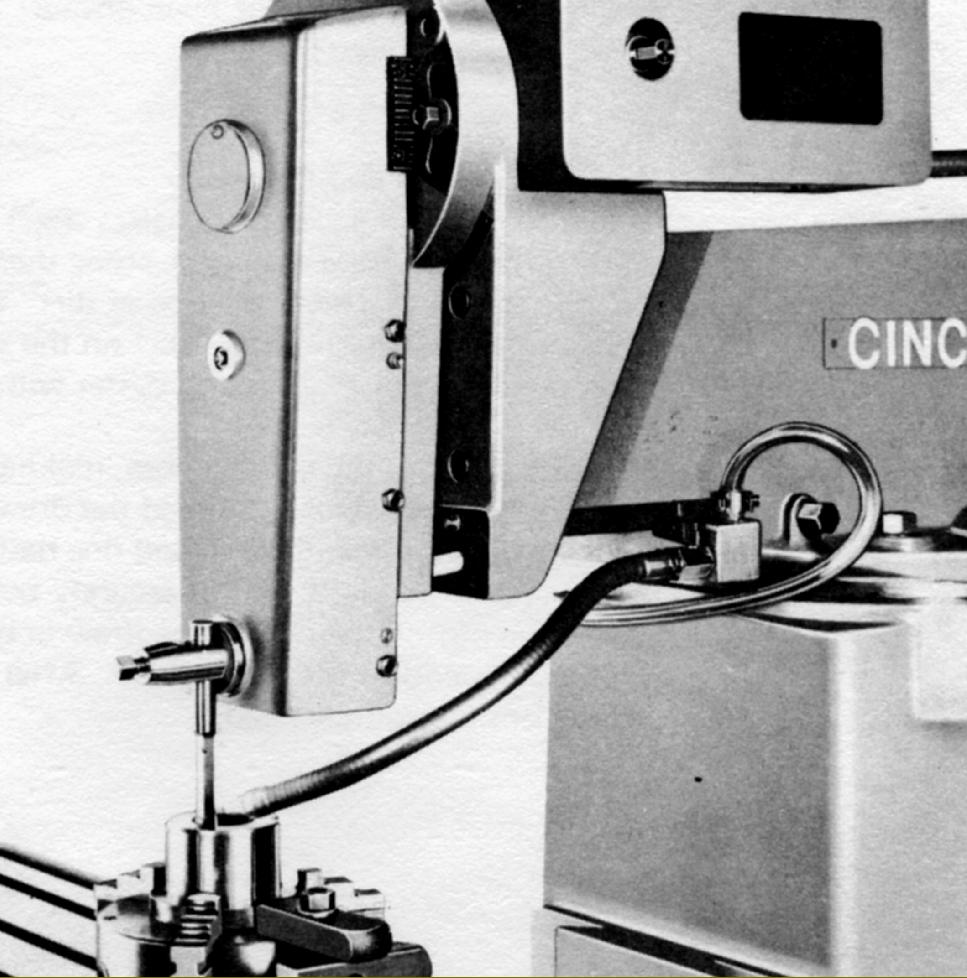 |
|
|
|
|
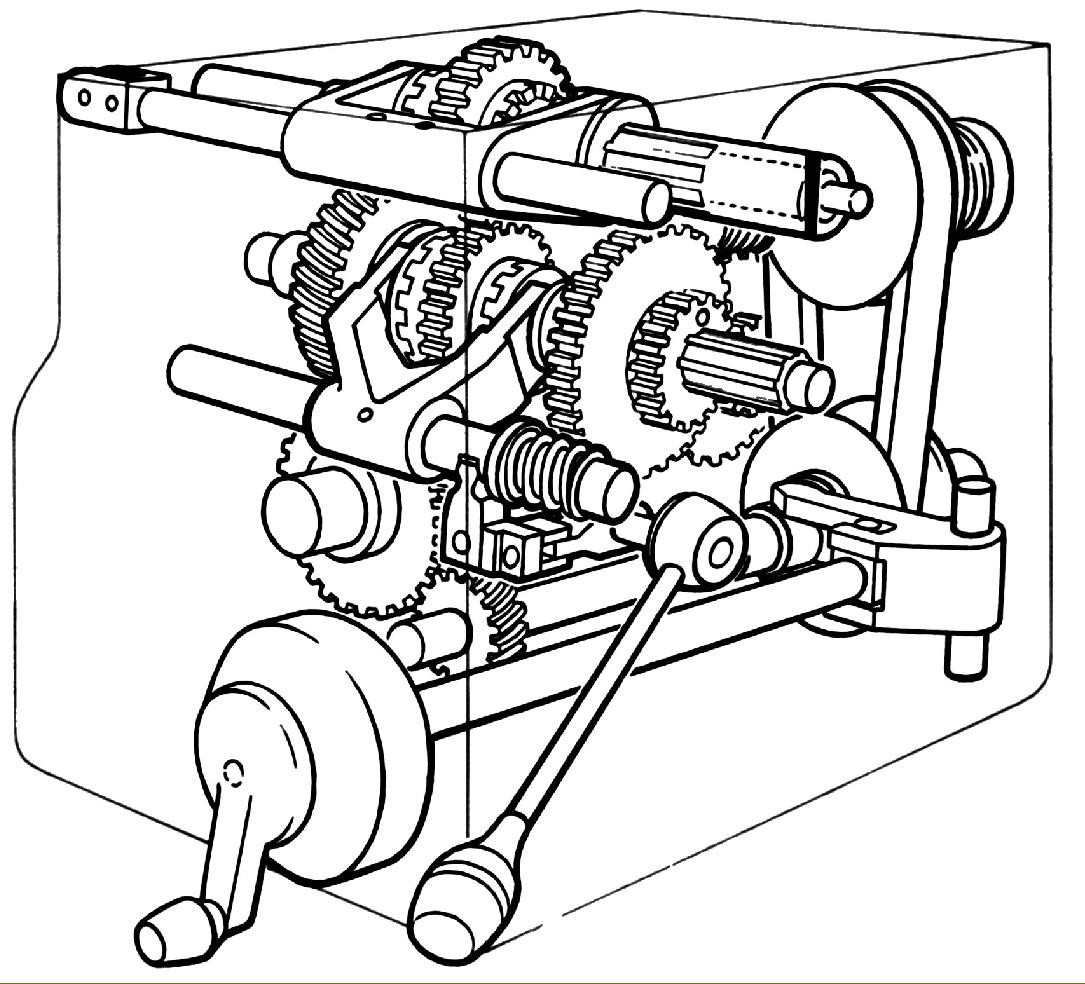 |
|
|
|
|
|
|
Table power-feed gearbox with infinitely variable-speed drive
|
|
|
|
|
|
|
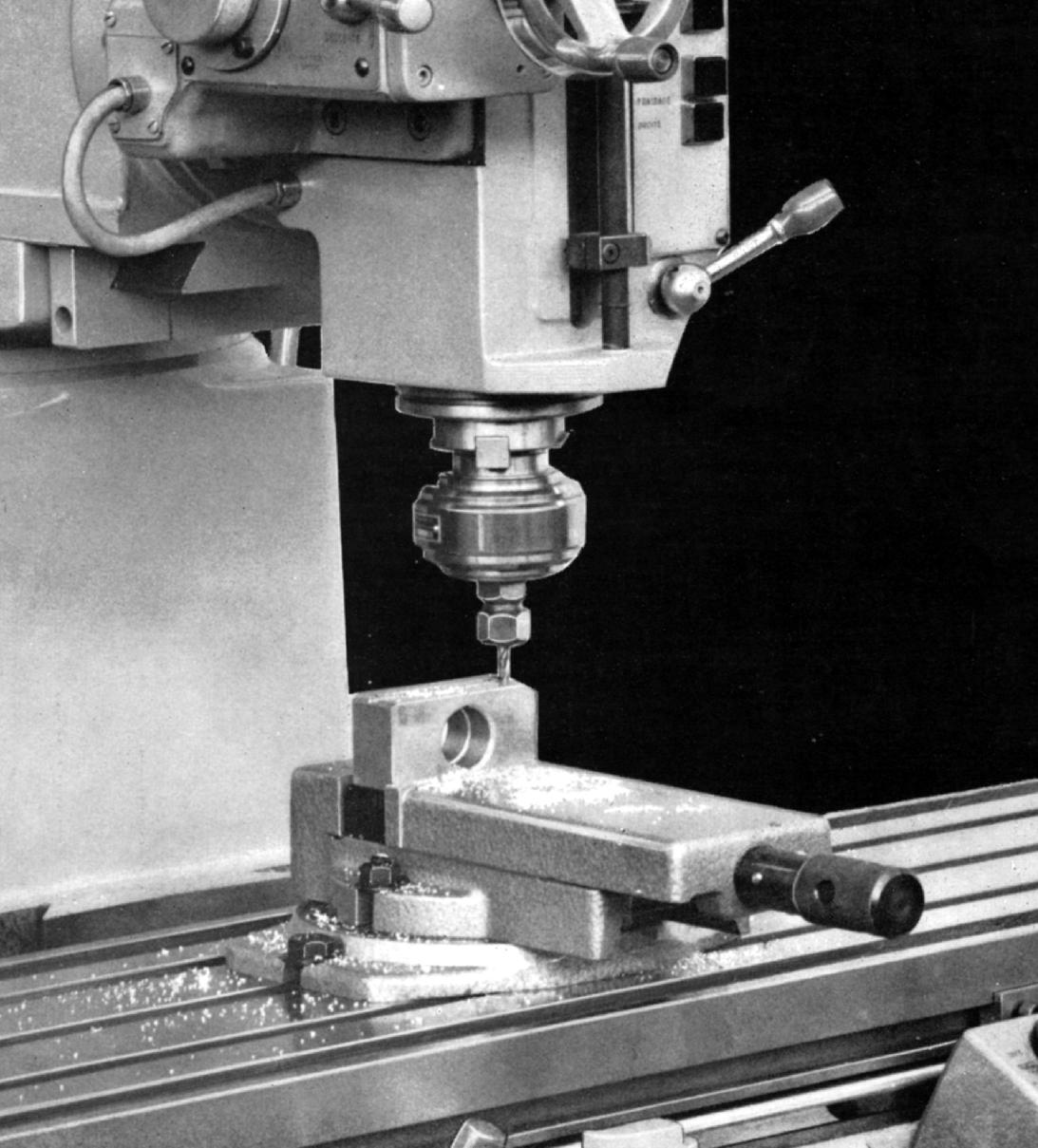 |
|
|
|
|
|
|
High-speed multiplier attachment - just like the one on your electric drill, but better made …..
|
|
|
|
|
|
|
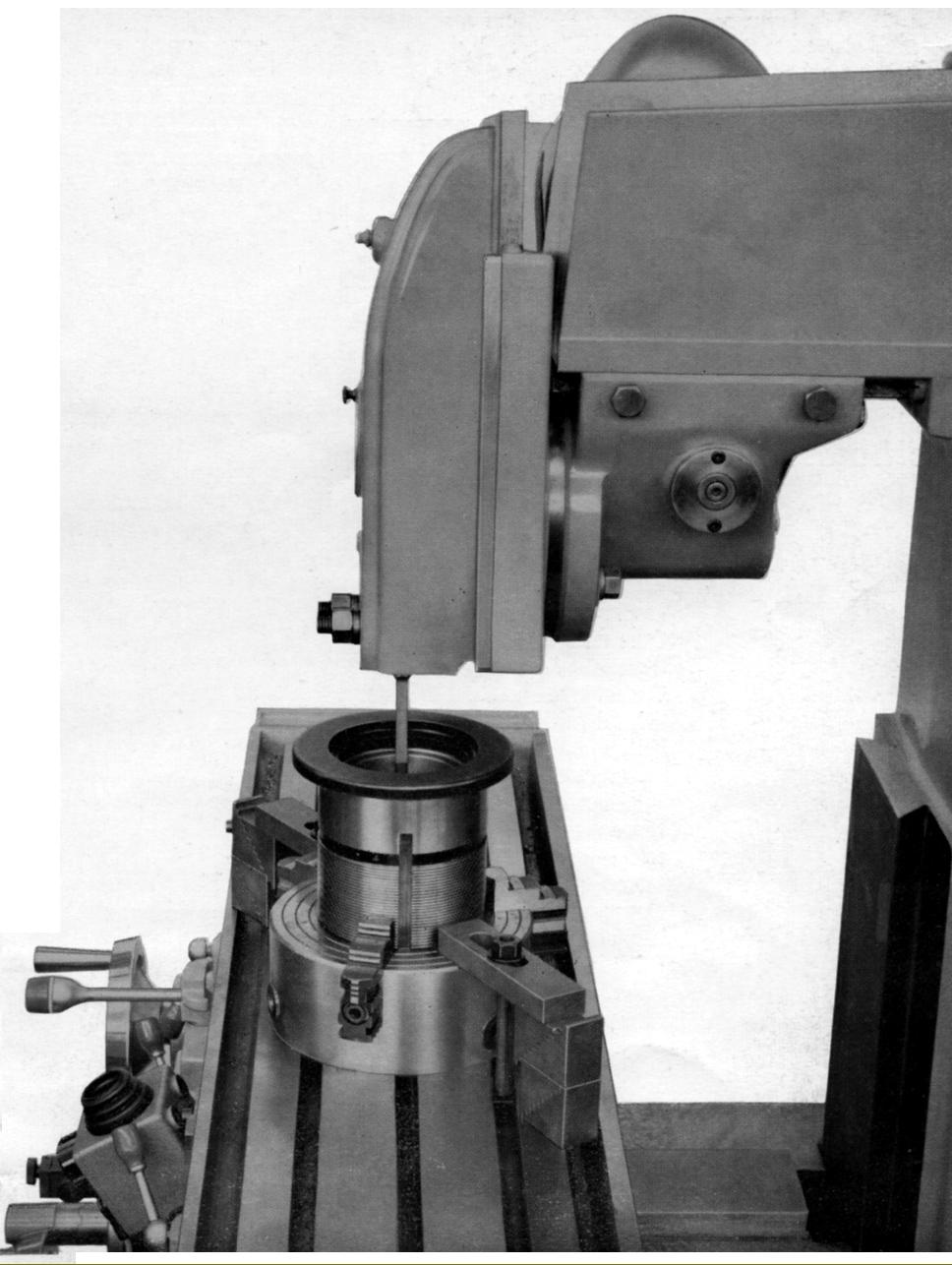 |
|
|
|
|
|
|
|
|
|
|
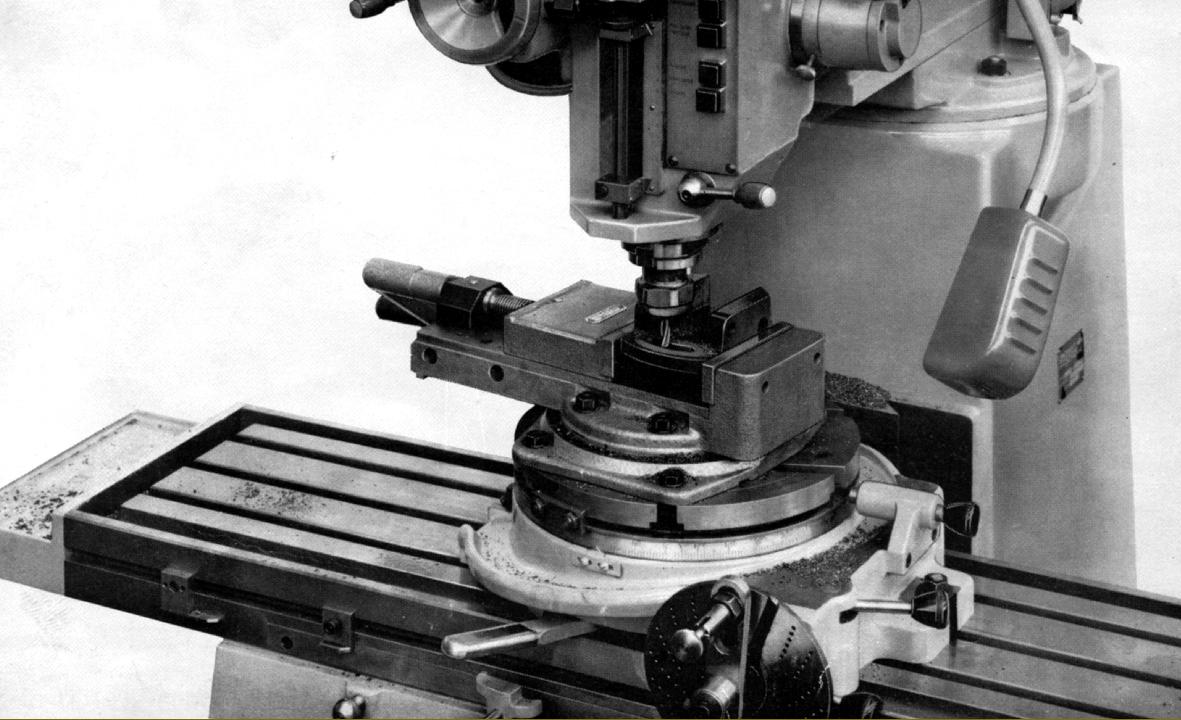 |
|
|
|
|
|
|
Rotary table with dividing plate and the low-height, swivel-base machine vice
|
|
|
|
|
|
|
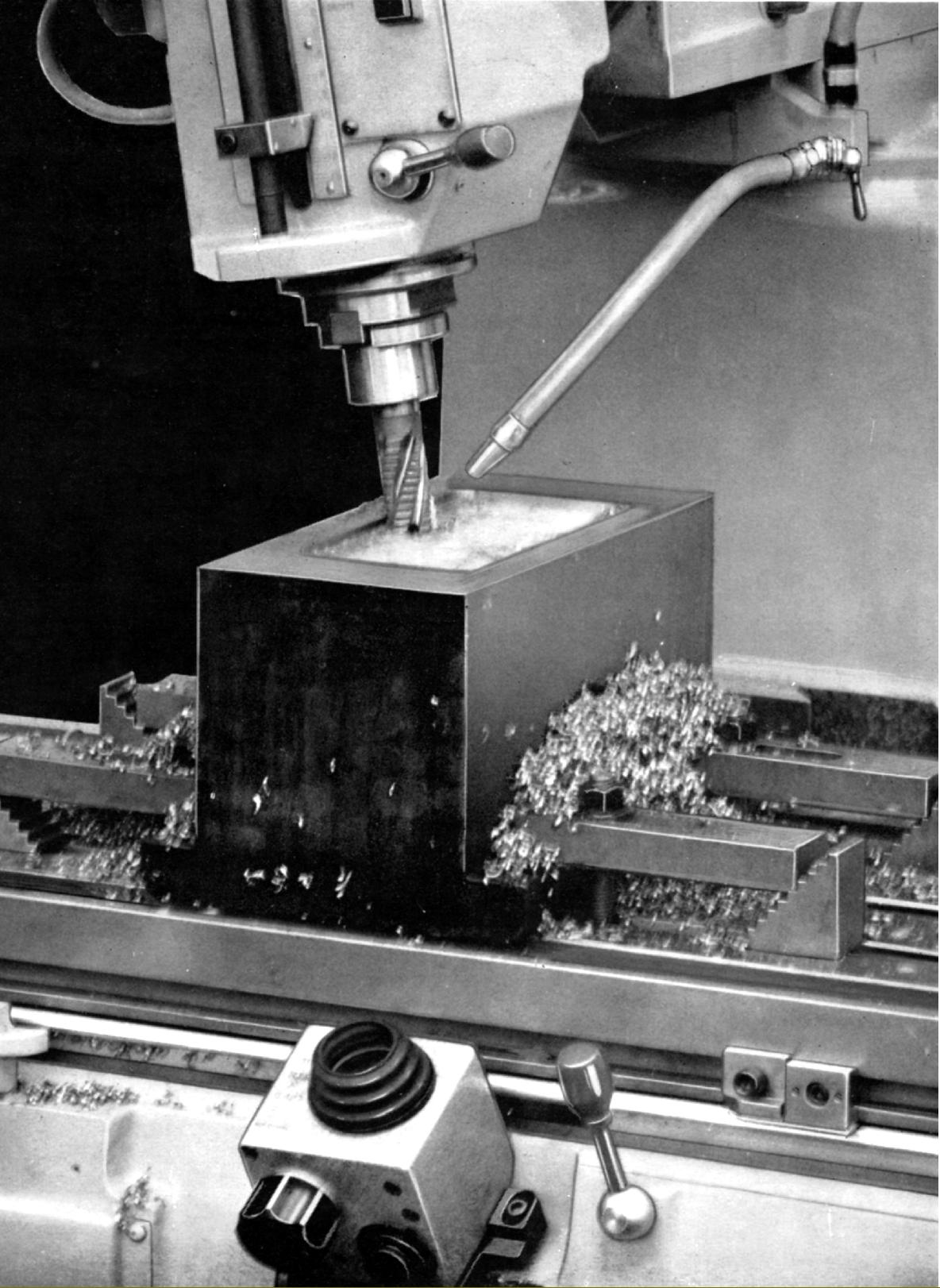 |
|
|
|
|
|
|
The start of a die-sinking operation
|
|
|
|
|
|
|
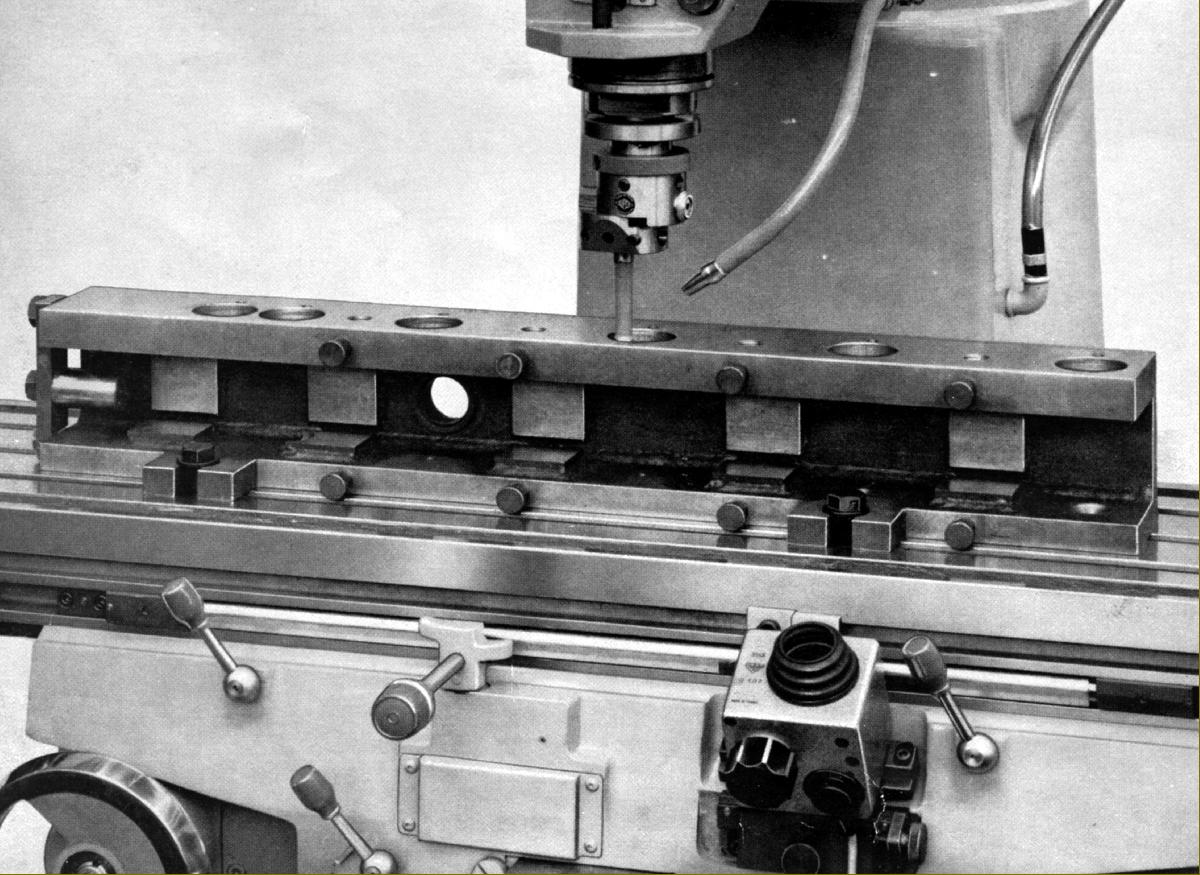 |
|
|
|
|
|
|
Boring head in use with (mounted on the front of the saddle) optical positioning equipment
|
|
|
|
|
|
|
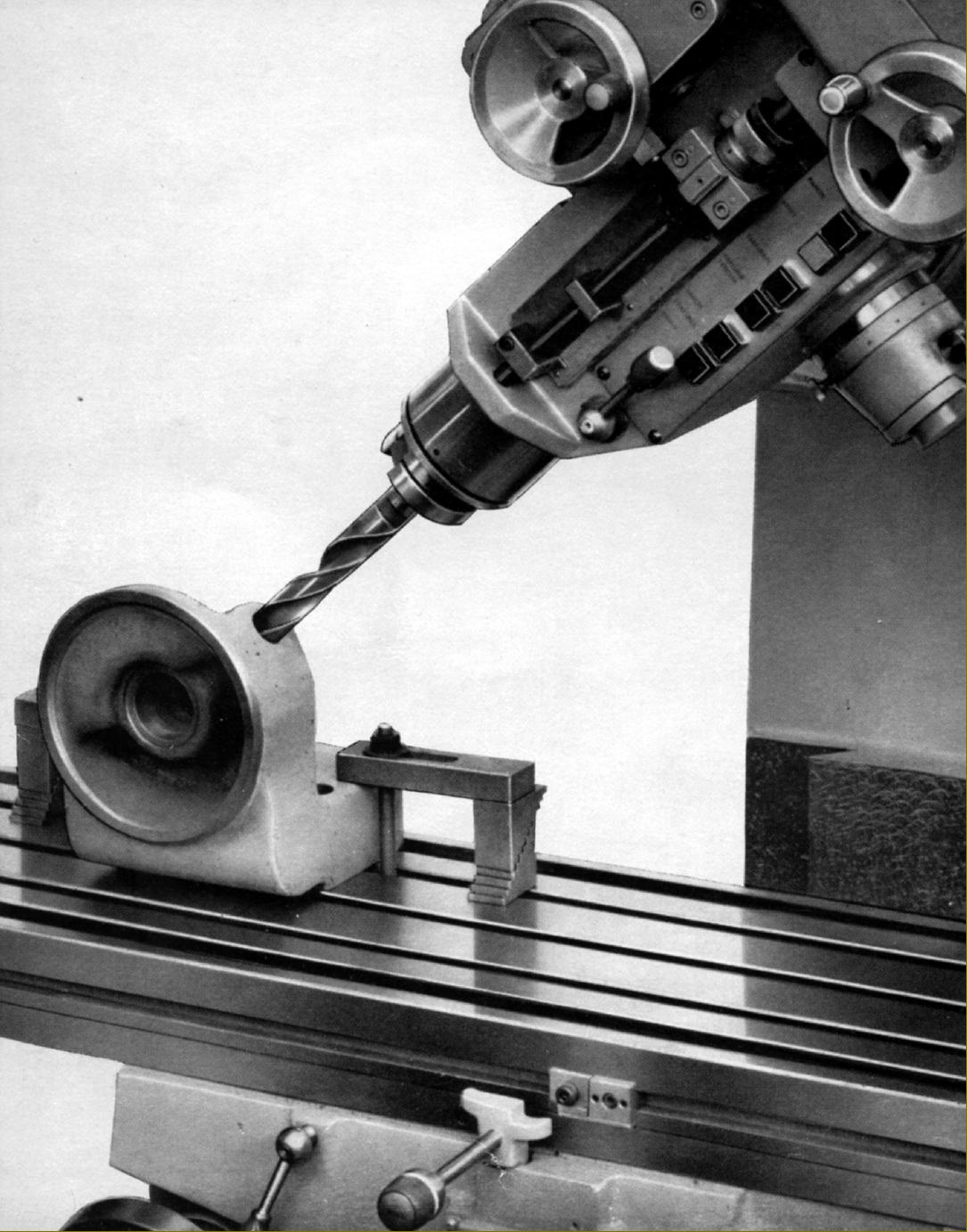 |
|
|
|
|
|
|