 |
 |
 |
 |
 |
 |
 |
 |
 |
 |
 |
 |
 |
 |
 |
 |
 |
 |
 |
 |
 |
 |
 |
 |
 |
 |
 |
 |
 |
|
|
|
|
|
|
|
|
|
|
|
|
|
|
|
|
|
|
|
|
|
|
|
|
|
|
|
|
|
|
|
|
|
|
|
|
|
|
|
|
|
|
A heavily-built lathe, constructed to Schlesinger's limits of accuracy, the Rollo Supreme was available as two models - though distinguished only be their centre height for in all other respects the two lathes were identical. The bed was over 11" wide and the all-geared headstock of massive proportions. A detachable gap was provided as standard, but the option was offered of a straight-bed machine if so desired; with the gap removed a piece of metal 24" in diameter and 8" thick could be turned on the 8.5" model. The standard capacity between centres was 3 feet, but any length up to 6 feet could be ordered in foot intervals. Eight speeds were provided, from 24 to 450 rpm, and although these were all rather slow by today's standards, they were perfectly suitable for the cutting tools in use at the time. The spindle was bored to pass a 2" diameter bar and rotated on taper roller bearings, the idler and layshafts of the geared headstock turned on ball races and all the gears were made from 50 ton gear-steel cut from the solid. Early models were fitted with a metal-to-metal cone clutch with could be adjusted through a cover on the back of the headstock; later machines had a BOM multi-plate clutch, which was maintenance and adjustment free. Unusual for the time, the lathe was supplied as standard able to generate both English and Metric threads without the substitution of different changewheels. The drive from the headstock arrived first at an auxiliary five-speed gearbox , the control handle for which was the first to the left-hand side of the machine and marked from A to E. This control could be moved to change the selected sliding and surfacing speeds whilst the spindle was turning. The drive then fed into an English/Metric selector box with a control lever on its detachable front face, before finally arriving at a conventional 12-speed Norton pattern quick-change screwcutting gearbox. English threads from 2 to 56 t.p.i could be cut (including the 11.5 t.p.i American pipe thread) and metric threads from 0.25 mm to 9.5 mm pitch. All the gears in the system were steel, not cast iron, and ran in oil baths..
|
|
|
|
|
|
|
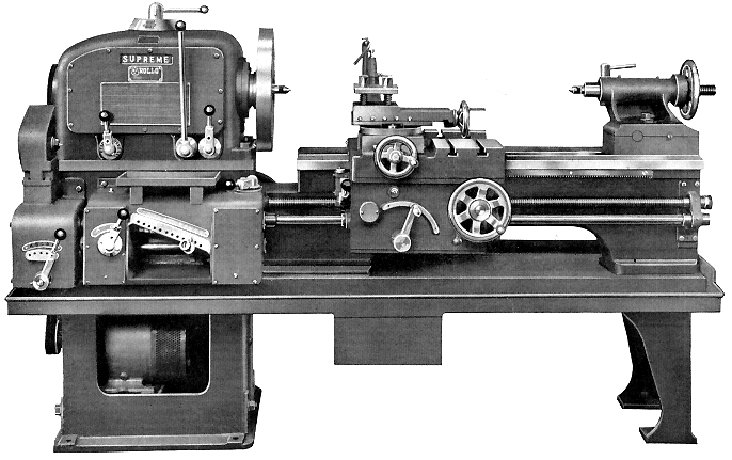 |
|
|
|
|
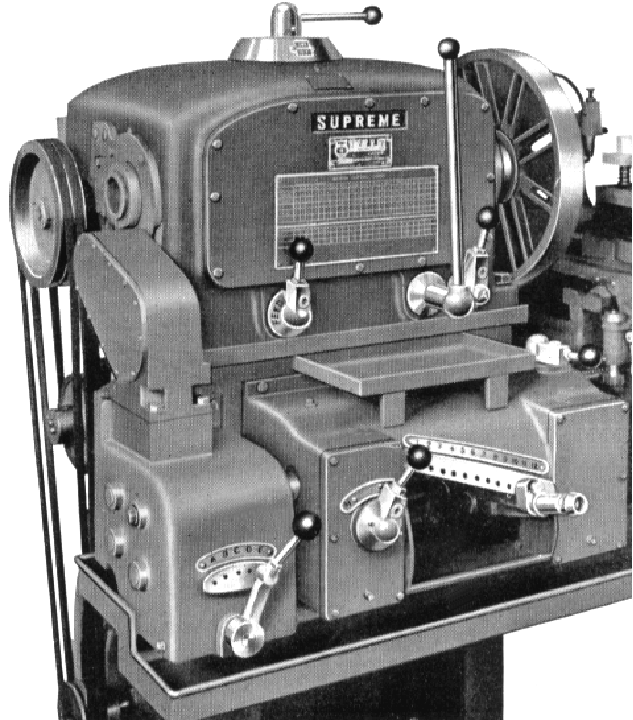 |
|
|
|
|
|
|
The lathe was unusual for the time in being able to cut both English and Metric threads without the substitution of different changewheels. The drive from the headstock arrived first at an auxiliary five-speed gearbox , the control handle for which was the first to the left-hand side of the machine and marked from A to E. This control could be moved to change the selected sliding and surfacing speeds whilst the spindle was turning. The drive then fed into an English/Metric selector box with a control lever on its detachable front face, before finally arriving at a conventional 12-speed Norton pattern quick-change screwcutting gearbox. English threads from 2 to 56 t.p.i could be cut (including the 11.5 t.p.i American pipe thread) and metric threads from 0.25 mm to 9.5 mm pitch. All gears in the system were steel, not cast iron, and ran in oil baths.
|
|
|
|
|
|
|
|
|
|
|
|
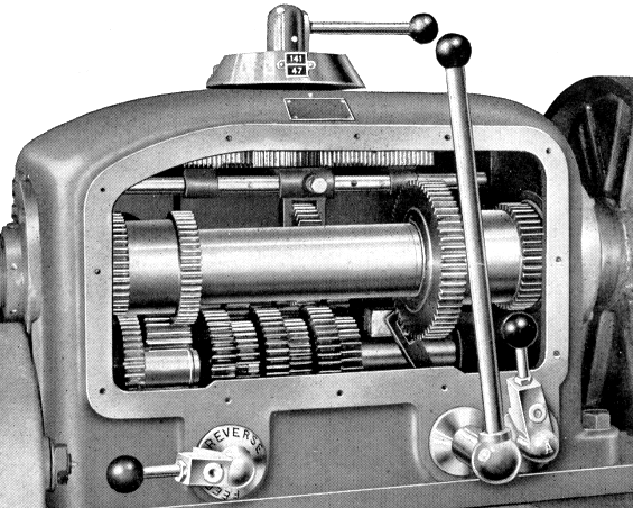 |
|
|
|
|
|
|
Of massive construction, the headstock was provided with eight speeds, from 24 to 450 rpm, and although these were all rather slow by today's standards, they were perfectly suitable for the cutting tools in use at the time. The spindle was bored to pass a 2" diameter bar and rotated on taper roller bearings, the idler and layshafts of the geared headstock turned on ball races and all the gears were made from 50 ton gear steel cut from the solid. Early models were fitted with a metal-to-metal cone clutch with could be adjusted through a cover on the back of the headstock; later machines had a BOM-L multi-plate clutch by Crofts of Bradford - a unit that was maintenance and adjustment free.
|
|
|
|
|
|
|
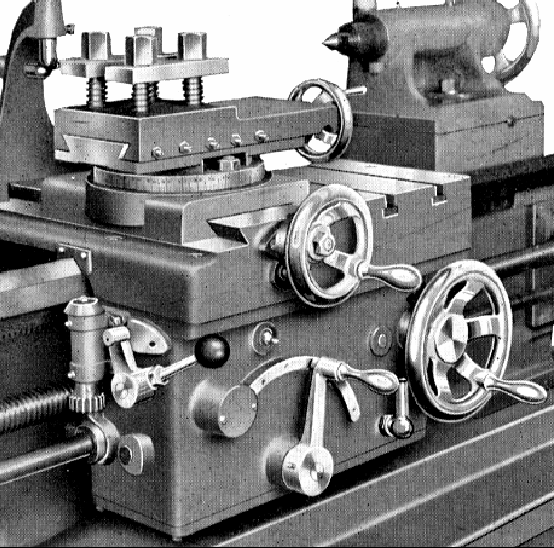 |
|
|
|
|
|
|
The saddle was fitted with two T slots on its right-hand surface for boring work, the cross feed screw ran in ball bearings at both front and back--though the micrometer dials were far too small, a common failing at that time. The oil level indicator for the apron was, inside of a window, an external, sight-glass tube - and so very vulnerable to accidental knocks and blows.
|
|
|
|
|
|
|
|
|
|
|
|
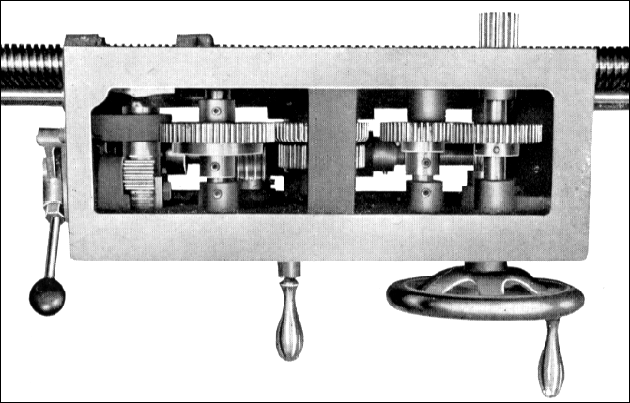 |
|
|
|
|
|
The solidly-constructed apron was of the double walled box type with a removable floor - ideal for a through clean-out of the oil bath in which the gears ran
|
|
|
|
|
|
|
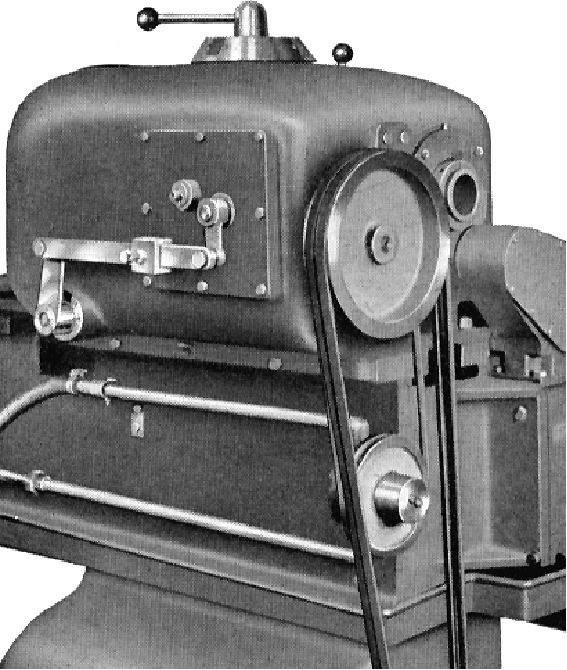 |
|
|
|
|
|
|
Twin V-belt drive from base-mounted motor. The lever mechanism on the back of the headstock operated either a cone or multi-plate clutch.
|
|
|
|
|
|
|
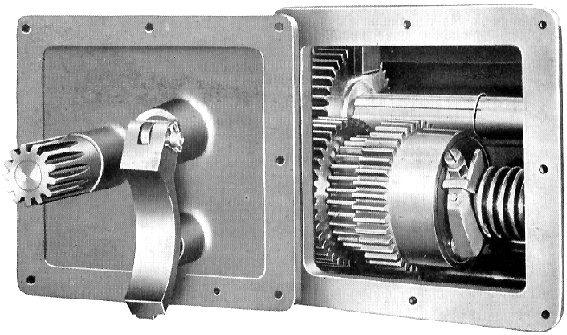 |
|
|
|
|
|
Inside the adjustment cover of the cone-clutch model.
|
|
|
|
|
|
|
|
|
|
|
|
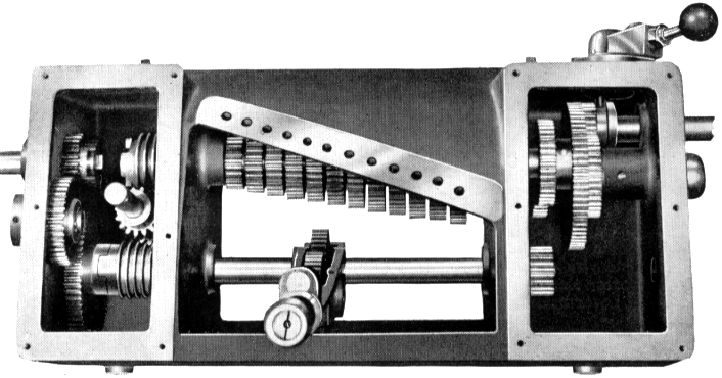 |
|
|
|
|
|
|
Screwcutting gearbox with all covers removed. In the left-hand compartment were two dog clutches, with the lower one, providing English threads, shown engaged. To obtain Metric threads the handle shown to the upper right moved a shaft through the nest of gears and engaged the upper dog clutch whilst simultaneously disengaging the lower. The nest of gears then became the driven gears, rather than the driving. The same movement of the lever disconnected the right-hand gear on the top shaft and engaged the gear on the right-hand end of the bottom shaft. The drive passed into the right-hand compartment - which contained the Metric-translations gears.
|
|
|
|
|
|
|
|
|
|
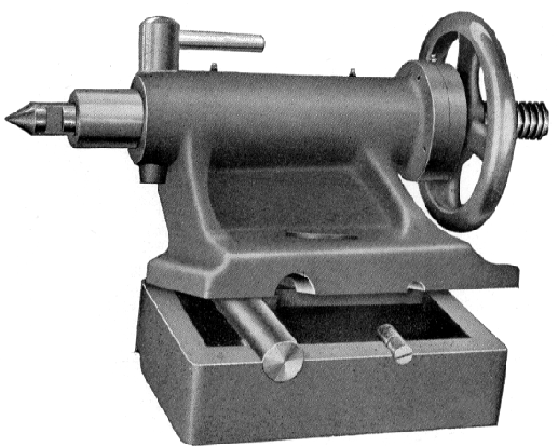 |
|
|
|
|
|
The location of the upper and lower parts of the No. 3 Morse taper tailstock was maintained not by the usual rectangular strip, but by a ground bar, just like that used on the tiny Flexispeed lathe.
|
|
|
|
|
|
|
|
|
|
|
|
|
|