 |
 |
 |
 |
 |
 |
 |
 |
 |
 |
 |
 |
 |
 |
 |
 |
 |
 |
 |
 |
 |
 |
 |
 |
 |
 |
 |
 |
 |
 |
 |
 |
 |
 |
 |
 |
 |
 |
 |
 |
 |
 |
 |
 |
 |
|
|
|
|
|
|
|
|
|
|
|
|
|
|
|
|
|
|
|
|
|
|
|
|
|
|
|
|
|
|
|
|
|
|
|
|
|
|
|
|
|
|
|
|
|
|
|
|
|
|
|
|
|
|
|
Believed to have been developed first by Joseph Nason of New York, who obtained US Patent No. 10,383 on January 3, 1854 for an "arrangement for cutting screws in lathes." the "chase" system of screwcutting was widely used on precision bench lathes of all makes. The P & W was no exception and could be provided with an arrangement whereby a T slot, which ran down the back face of the bed, held supports that carried a sliding shaft holding a toolholder on the end of a cast arm. Above this, at the headstock end, was a "master thread" driven by a selection of gears from the end of the main spindle in such a way that each "master" had its threading range extended by a multiple of six. A follower (with an insert carrying a few threads of the same pitch) pressed against the "master thread" and transmitted its form to the workpiece via a sliding shaft and threading tool held in an adjustable slide rest (illustrated left). Whilst this system produced absolutely accurate threads - and was especially suited to delicate operations on thin-wall tubes used to construct such items as microscopes and telescopes - the length and pitch of thread that could be cut depended upon the availability of the appropriate "master". Rather cleverly, each Pratt and Whitney "master" was supplied complete with a hob at one end for chasing a nut to suit the thread being generated by the lathe. A very simple form of this screwcutting mechanism can be seen on the Goodell-Pratt Pages and other pictures of similar mechanisms on the Stark, Waltham Machine Works, Ames and Wade lathes. Besides the system whereby the tool slid, another form of chase screwcutting involved a sliding headstock spindle - a system that was to be even more highly developed when used on mass-production "Swiss Autos" used in the manufacture of tiny screws and other fittings for the horological and instrument trade. Makers of sliding-headstock spindle machines included most of the German makers of bench precision lathes including Boley, Lorch, Wolf-Jahn, Kärger and Auerbach. .
|
|
|
|
|
|
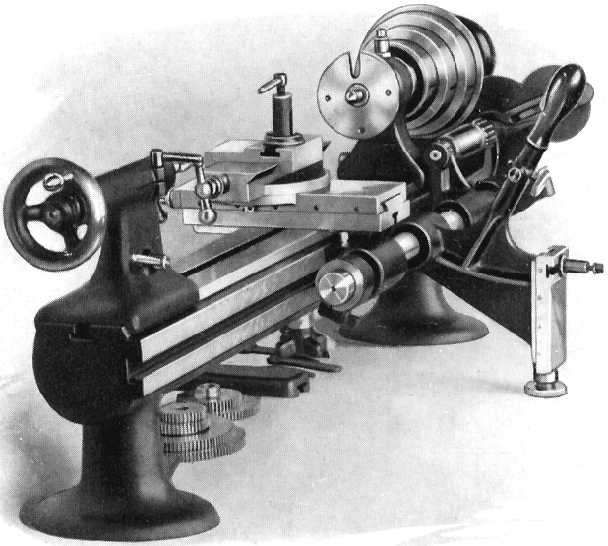 |
|
|
|
|
|
|
In this picture the toolholder is swung right back and rests on the bench behind the lathe.
|
|
|
|
|
|
|
|
|
|
|
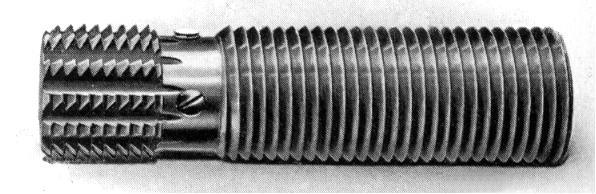 |
|
|
|
|
|
|
|
|
|
Master thread with, on the left-hand end, a hob of the same pitch for the manufacture of replacement units
|
|
|
|
|
|
|
|
|
|
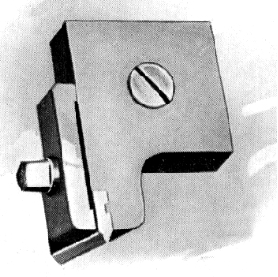 |
|
|
|
|
|
|
|
|
|
|
|
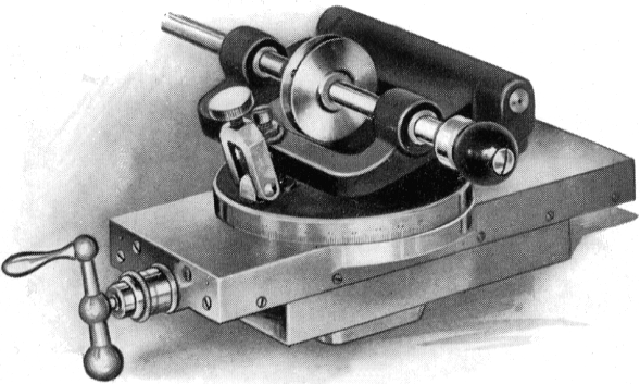 |
|
|
|
|
|
|
Grinding Rest with Traversing Spindle
|
|
|
|
|
|
|
|
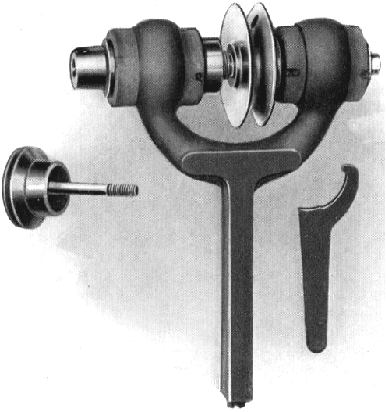 |
|
|
|
|
|
Tool Post Grinder Three types of grinding attachment were available, all driven from an extra pulley on the overhead countershaft unit. - "Grinding Rest with Traversing Spindle"; this type mounted directly on the slide rest and could be moved in and out by hand. To assist in taking measurements the device was arranged to hinge out of the way and could be locked down when in operation by the U-shaped catch. - Slide-rest Grinder"; intended for fitting to the cross slide, this was a simpler device which used a similar spindle to that in the "Grinding Rest" unit. - "Tool Post Grinder"; this was mounted in the regular toolpost and used the traversing movement of the compound slide to set the wheel position. Two sizes of internal wheel arbor, 1/8" and 1/4" were available as well a range of external and internal grinding wheels.
|
|
|
|
|
|
|
|
|
|
|
|
|
|
|
|
|
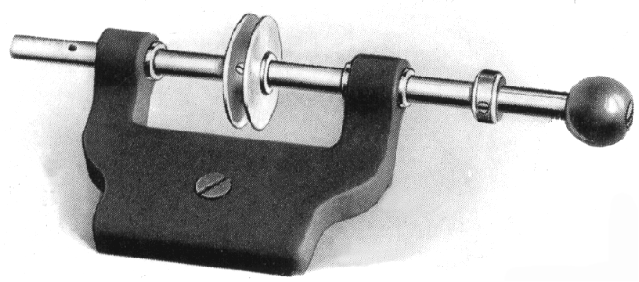 |
|
|
|
|
|
|
Internal and light external grinding attachment.
|
|
|
|
|
|
|
|
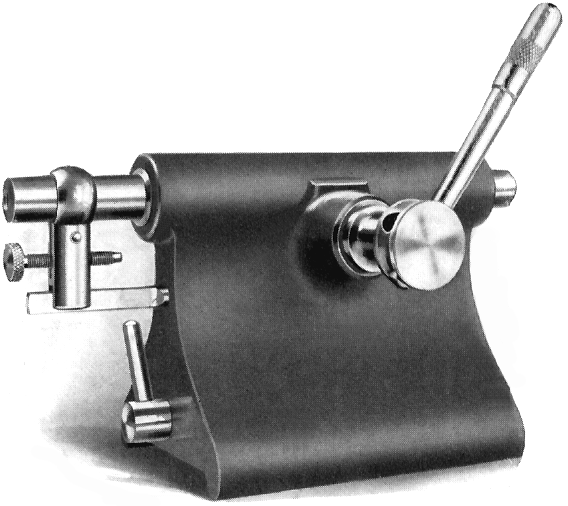 |
|
|
|
|
|
|
Plain Lever-action Tailstock with rack-feed barrel and adjustable depth stop. This tailstock was also available mounted on a "cross slide" unit.
|
|
|
|
|
|
|
|
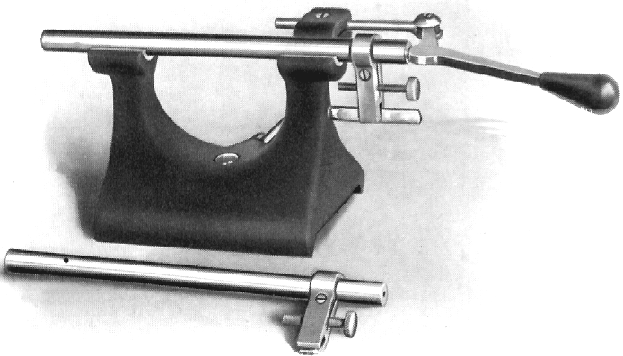 |
|
|
|
|
|
|
Half-Open Tailstock - designed for light manufacturing work where quick interchange of spindles and tools was required.
|
|
|
|
|
|
|
|
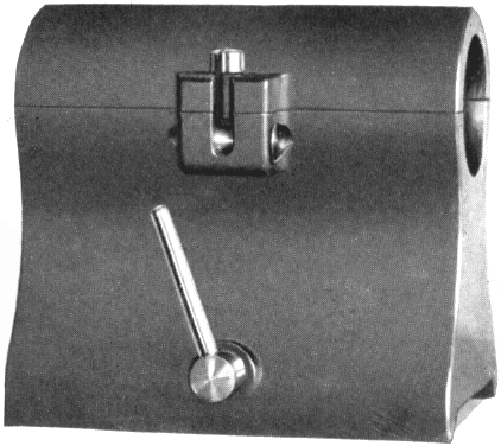 |
|
|
|
|
|
|
"Quill Rest" This special fitting was designed for extremely accurate work and placed just in front of the headstock and driven from it. The top of the tailstock was arranged to hinge open to allow the rapid changing of quills which were available in two styles, the "chuck" type, the front end of which was a duplicate of the headstock spindle, and the "faceplate" type which was available with either tapped holes (1/4" -20 U.S.F. arranged in eight rows) or T slots
|
|
|
|
|
|
|
|
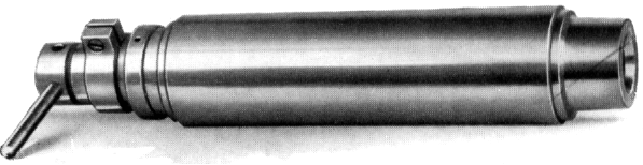 |
|
|
|
|
|
|
|
|
|
|
|
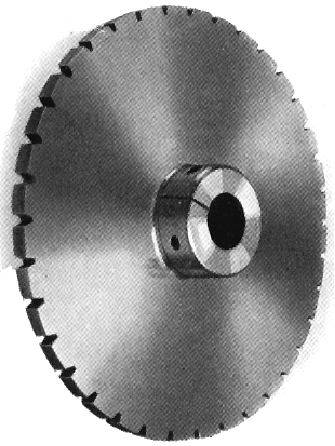 |
|
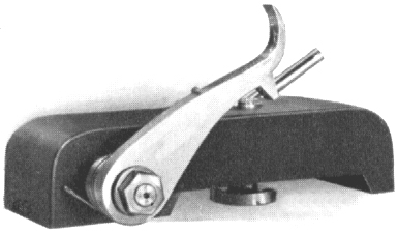 |
|
|
|
|
|
|
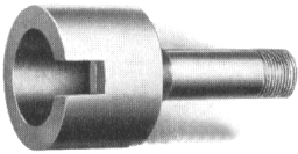 |
|
|
|
|
|
|
|
|
|
|
|
Quill Driver - pulled into headstock by the standard collet draw tube
|
|
|
|
|
|
|
|
|
|
|
|
|
|
|
|
|
|
|
|
Index Pawl and Block This accessory could be used either on the headstock or the Quill Rest. An index pawl unit was clamped to the bed and the Index Plate (shown below) mounted above it on either the rear of the headstock spindle - or on any of the Quill Rest quills.
|
|
|
|
|
|
|
|
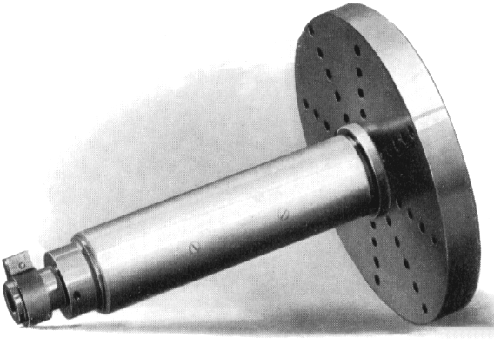 |
|
|
|
|
|
|
|
|
|
|
|
|
|
|
|
|
|
|
|