 |
 |
 |
 |
 |
 |
 |
 |
 |
 |
 |
 |
 |
 |
 |
 |
 |
 |
 |
 |
 |
 |
 |
 |
 |
 |
 |
 |
 |
 |
 |
 |
 |
 |
 |
 |
 |
 |
 |
 |
 |
 |
 |
|
|
|
|
|
|
|
|
|
|
|
|
|
|
|
|
|
|
|
|
|
|
|
|
|
|
|
|
|
|
|
|
|
|
|
|
|
|
|
|
|
|
|
|
|
|
|
|
|
|
|
|
|
|
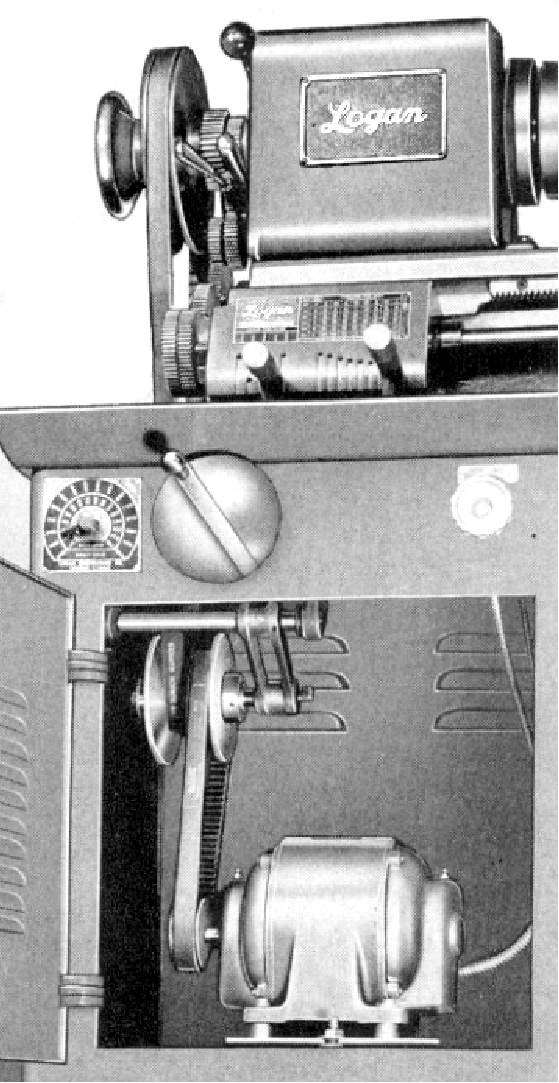 |
|
|
|
|
|
|
Logan Variable-speed Drive Unit Available as a "no-cost" option on some models the mechanical variable-speed drive unit was neatly built into the left-hand side of the cabinet stand. The motor pulley was fixed and the expanding and contracting pulleys fitted to a parallel shaft above. The lower (motor) belt was 38" long and the upper headstock drive belt 60" long. Depending upon the year of manufacture the speeds available varied slightly and also changed with the particular model and the exact type of motor employed: for example, until 1956, the factory figures for the 12" lathe suggested a range in backgear of 38 to 295 rpm and in direct drive 250 to 1575 r.p.m. whilst after this, the speeds were altered slightly to span 38 to 1400 rpm. The 14" appeared to use the same range of 38 and 1200 r.p.m. throughout its production run. Fitted to the 14" lathe the maker's standard-specification motor was a 2 h.p. 3-phase and for the 12" a 1 h.p. 3-phase. Although the larger lathes were required to have 3-phase motors, no such recommendation was made for the smaller machines, where 1-phase motors were considered adequate - that for the 11" being 0.75 h.p, the 10" a 0.5 h.p - and the 9" a 0.3 h.p. Interestingly, when the variable-speed drive was specified, the factory offered to fit the customer's own motor and dynamically balance the entire assembly, otherwise they "… cannot be responsible for vibration in your lathe." This was an eminently sensible precaution, as it can often be surprisingly difficult to set up even a simple motor-drive system - and have it run sweetly and effortlessly - without first having to spend a surprising amount of time fiddling with alignments and belt runs. A control wheel on the front of the cabinet operated the system - and required twelve turns to change the speed from maximum to minimum. A single oil cup provided lubrication for the entire assembly. A later Logan lathe, the "Powermatic", used an entirely different variable-speed drive that should not be confused with this earlier system..
|
|
|
|
|
|
|
|
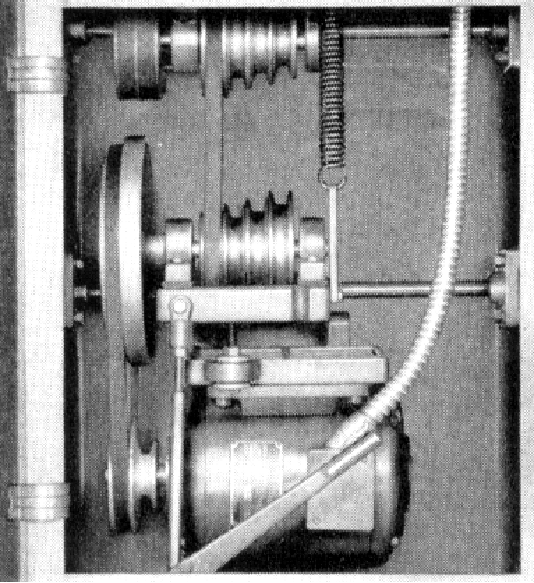 |
|
|
|
|
|
|
The standard underdrive system used three belt runs to transmit power to the headstock spindle. The first, from the motor, was arranged in a South Bend-like manner with a double-step V pulley on the motor transmitting power via a V belt to a flat pulley on the first countershaft. A standard V belt and pulley arrangement then provided a choice of 4 (rather close) ratios to an upper countershaft - and from there a double V belt took the drive to a pulley on the left-hand end of the headstock spindle.
|
|
|
|
|
|
|
|
|
|
|
|
|
|
|
|
|
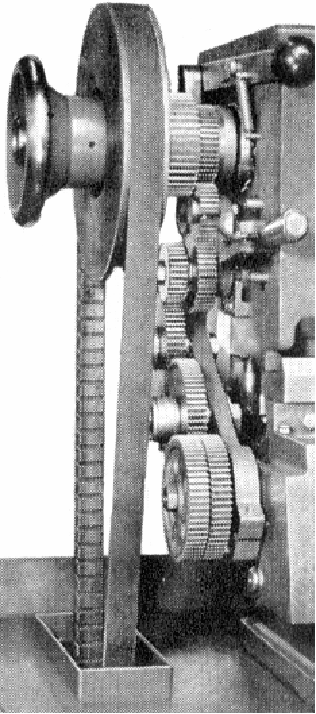 |
|
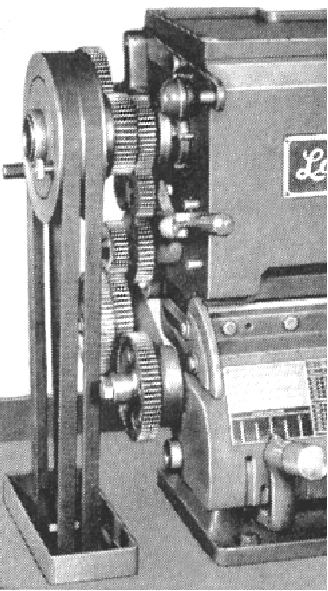 |
|
|
|
|
|
Twin V belt drive belts to overhung headstock-drive pulley.
|
|
|
|
|
|
|
|
|
|
|
|
|
|
|
|
|
|
Variable-speed drive belt to overhung headstock-drive pulley.
|
|
|
|
|
|
|
|
|
|
|
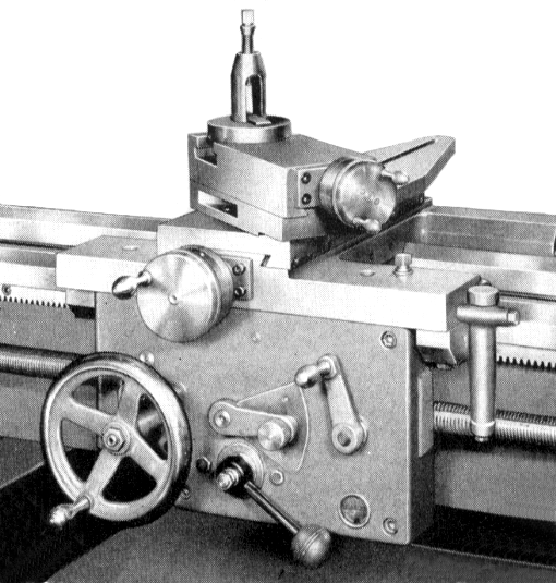 |
|
|
|
|
|
|
Logan 14" Lathe Carriage Assembly Large micrometer dials were standard on the bigger lathes but the smaller models suffered, like those on so many other makes, from dials which were too small for comfortable reading under operating conditions. Like South Bend and Sheldon, no separate powershaft was fitted, the drive for the power sliding and surfacing being taken from the leadscrew which, being slotted along its length, turned a key inside a worm wheel which was carried on the inside face of the apron. The feeds were selected by the usual lever, moving across a sector with three indents, and engaged by a friction clutch - the long, ball-ended operating lever for which can be seen emerging from the lower, central part of the apron in the picture above. The 14-inch lathe had an oil-bath apron.
|
|
|
|
|
|
|
|
|
|
|
|
|
|
|
|
|
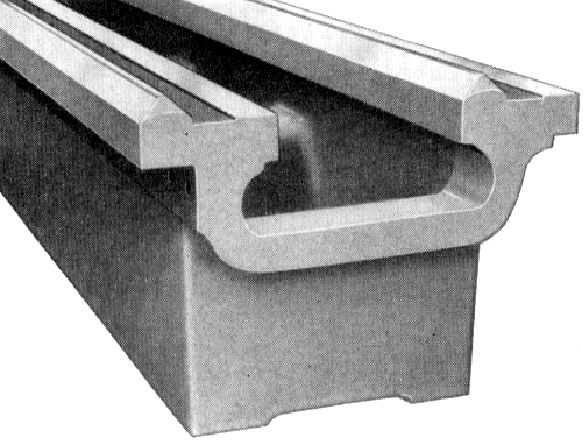 |
|
|
|
|
|
|
The Logan bed was seasoned before machining - as well as between machining operations. It was well ribbed and finish ground. For an extra charge (a tiny proportion of the lathe's cost) it could be supplied flame hardened - and hence given a greatly extended life. One wonders how many customers took advantage of this - if the number of Myford lathes in the UK so specified is anything to go by, probably far too few ….
|
|
|
|
|
|
|
|
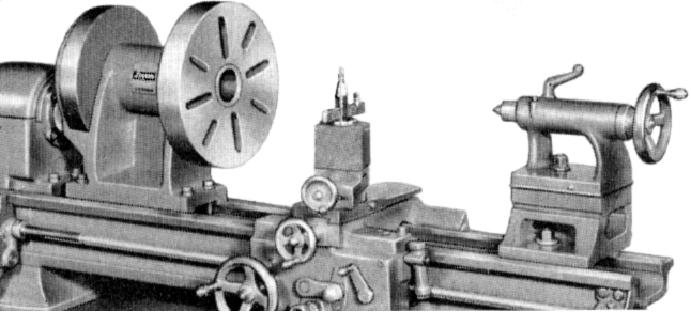 |
|
|
|
|
|
|
Auxiliary Head This was an unusual option, reserved for the 11" lathe, which consisted of a gear-driven auxiliary headstock with a ball-bearing spindle and a swing of 16". The unit could be mounted in ten minutes and, because of the slow-speed gear reduction, allowed threads four times coarser than standard to be cut. Raising blocks for the tailstock and toolpost were also available, as was a 10" faceplate. Logan offered a wide range of accessories for their lathes including the usual fixed and travelling steadies, metric transposing gears, lever action tailstocks, 4-way and Quick-set toolposts, micrometer bed stop, multiple-position carriage stop, threading stops, taper-turning units, mica undercutters, draw-in and lever-closed collet sets, etc. A a selection of parts to convert the lathes into self-contained production lathes was also manufactured and included bed-mounted indexing capstan units and cut-off slides with front and rear toolposts.
|
|
|
|
|
|
|
|
|
|
|
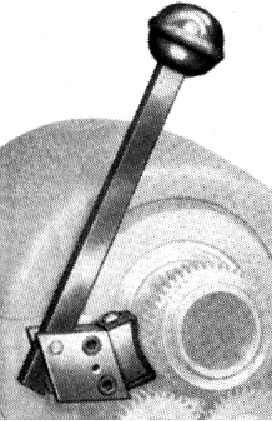 |
|
|
|
|
|
|
Spindle Brake - for the 11" lathe only. A very handy fitting seldom offered by any maker of smaller lathes
|
|
|
|
|
|
|
|
|
|
|
|
|
|
|
|
|
|
|
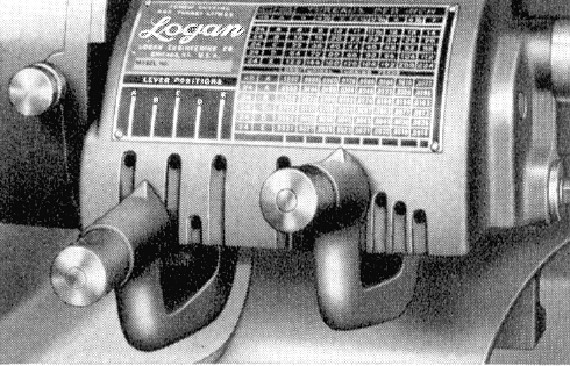 |
|
|
|
|
|
|
A Screwcutting Gearbox was available as an accessory to fit all lathes in the range not so equipped as standard and was supplied, complete with replacement leadscrews, under the following model numbers: LA-1200-1 for the 10" and 11" lathes with 24" centres LA-959-1 for the 10" lathe with 31" centres LA-958-1 for the 11" lathe with 36" centres
|
|
|
|
|
|
|
|
|
|
|
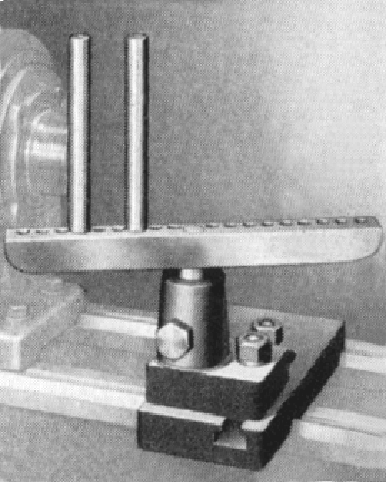 |
|
|
|
|
|
|
|
|
Metal Spinning Attachment to fit the 10", 11" and 12" lathes. The rest was 10" long and fitted to a special plate which clamped directly to the lathe bed.
|
|
|
|
|
|
|
|
|
|
|
|
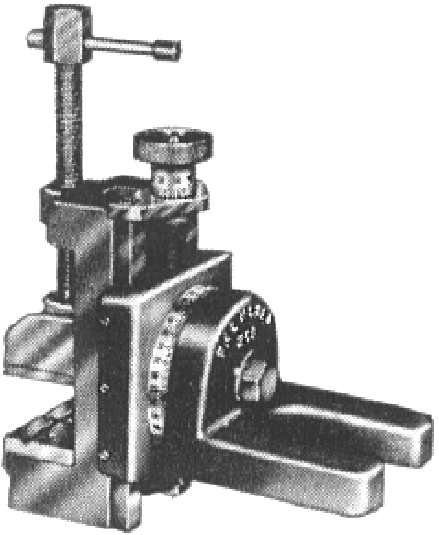 |
|
|
|
|
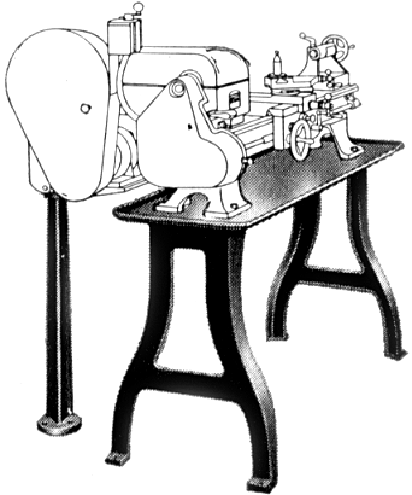 |
|
|
|
|
|
|
|
|
|
|
|
In order to mount a bench lathe on legs and a tray, Logan offered a special kit to support the countershaft unit.
|
|
|
|
|
|
|
|
|
|
Milling Attachment by the third-party supplier "Palmgreen"
|
|
|
|
|
|
|
|
|
|
|
|
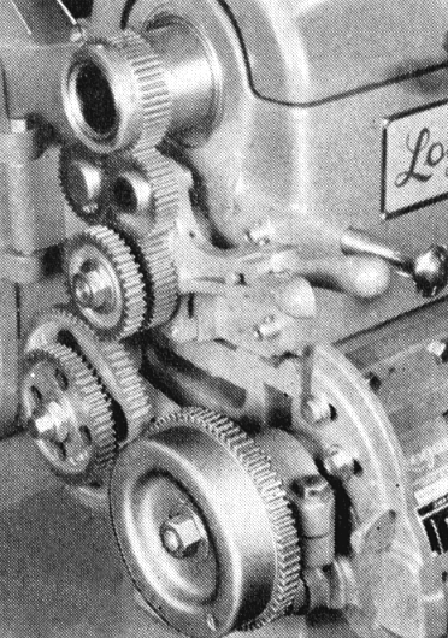 |
|
|
|
|
|
|
|
|
Automatic Gear-train Safety Attachment Designed to fit any Logan lathe with a screwcutting gearbox the unit consisted of a ratchet-like device contained within a drum-like extension to the large gearwheel fastened to the gearbox input shaft. In the event of a ham-fisted operator running the cutting tool violently into the workpiece (or chuck) - or just a build up of loads within the gearbox when generating threads, the overload protection instantly disconnected the drive to the carriage and announced its operation by a clicking noise. The unit would reset itself when the excessive strain was removed from the gear train.
|
|
|
|
|
|
|
|
|
|
|
|
|
|
|
|
|
|
|
|
|