 |
 |
 |
 |
 |
 |
 |
 |
 |
 |
 |
 |
 |
 |
 |
 |
 |
 |
 |
 |
 |
 |
 |
 |
 |
 |
 |
|
|
|
|
|
|
|
|
|
|
|
|
|
|
|
|
|
|
|
|
|
|
|
|
|
|
|
|
|
|
|
|
|
|
|
|
|
|
|
|
|
Once a competitor in the South Bend, Delta and Sheldon market, the Logan lathe is still actively supported by the Logan Actuator Company, descendants of the original manufacturer, who offer a friendly and efficient service and have much data published on their web site; the section at http://www.lathe.com/models.htm being especially useful in checking the specification of a particular Logan model. Logan lathes were available in 9", 10", 11", 12" and 14" versions (with a later 15" automatic turret lathe, the "Electri-matic", and a centre lathe the "Powermatic", being made as well). From 1940 until 1971 the company made, according to their records, some 90,000 lathes sold under the "Logan" and "Wards" names, these including standard "Engine" types (backgeared and screwcutting) as well as a number of Turret and Hand Screw models together with the range of useful accessories. All Logan lathes were fitted with one double-row, pre-loaded ball-bearing behind the spindle nose and a standard single -row bearing at the other end. The bearings were set with the correct loading at the factory, and sealed "for life" with grease. Although the headstocks of the 9", 10" and 11" machines were of very similar appearance and design, the 11" model was fitted with a heavier, larger-bore spindle similar to its bigger brothers. With a collet capacity of 0.5" and a spindle bore of 25/32", the two smallest lathes in the range had capacities not dissimilar to their immediate competitors. The headstocks of the 12" and 14" lathes were able to accept collets with a maximum capacity of 1" - and had a useful 13/8" spindle bore; they were also much more massively constructed - a very necessary feature if the increase in centre height was to be justified by a genuine ability to handle heavier jobs and maintain a quicker rate of metal removal. Models made during the earliest years of production had an apron with a single quadrant control that both selected, and engaged, the power sliding and surfacing feeds - while later versions were considerable improved (and much safer to operate) with the quadrant lever used to select the feed and a separate lever provided to engage and disengage it. The first countershafts were also different (and distinctive) being of "open" construction with each thin upright pierced midway to form a bearing housing. A further clue to the maker's position in the market comes from the screwcutting gearbox which, instead of enjoying oil-sump lubrication (and hence long-term reliability) needed the operator to give it the occasional squirt oil from a can - though this was no different to a number of competing models including the 9-inch South Bend and early Clausing machines Eventually the Logan line was bought by Houdaille, who moved the plant to the Powermatic manufacturing centre where, after a redesign, they were marketed with Montgomery Ward branding..
|
|
|
|
|
|
|
|
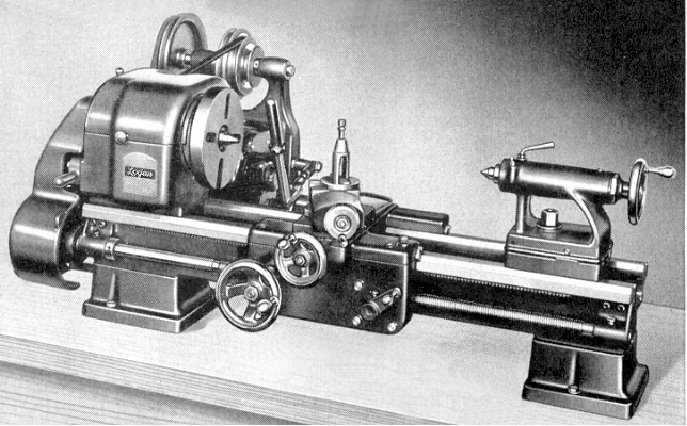 |
|
|
|
|
|
|
Logan 9" with screwcutting by changewheels and plain apron - circa 1954 The 9" Logan, although strongly built from honest materials, was designed to be produced as economically as possible and, in 1954, cost (in basic form) just $249 - in the same year the Atlas/Craftsman 6" lathe was $145 and their 12" lathe $260. The price is put in perspective by the next largest Logan lathe, the 10" which, with power cross feed as standard (but screwcutting with changewheels) was considerably more expensive at $410.
|
|
|
|
|
|
|
|
|
|
|
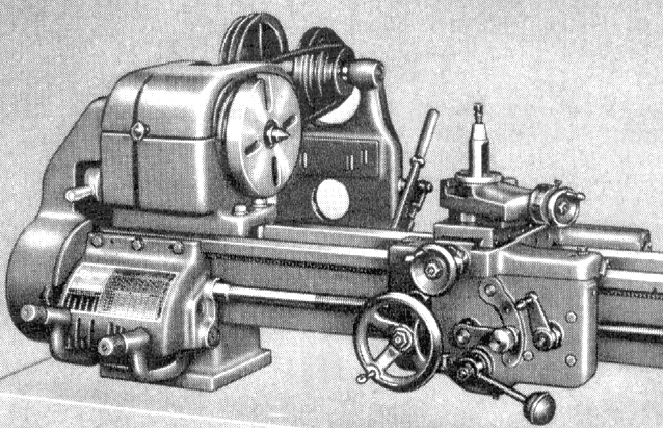 |
|
|
|
|
|
|
|
|
|
|
|
|
Logan 9" with screwcutting gearbox and power cross feed with separate selection and engagement controls - but without an electric motor fitted as offered circa 1956 The 9" Logan lathe was available with a capacity of either 17" or 28" between centres and, by 1956 at least, could be ordered with various combinations of a screwcutting gearbox and power-feed apron. Like South Bend and Boxford, the range divided into simple groups: Plain apron and changewheel screwcutting - Model 9B28-61 Powered apron and changewheels - Model 9B28-41 Plain apron and screwcutting gearbox - Model 9B9B28-21 Powered apron and screwcutting gearbox - Model 9B28-1 In the case of the 17" between centres lathes the model designations were identical - but with the figure 17 substituted for 28. With a nose thread of 1.5" x 8 t.p.i., a bore of 25/32" and a collet capacity of 0.5" the No. 3 Morse taper spindle, ran on sealed-for-life ball races, the pre-loading of which was set at the factory. The makers claimed that the spindle run-out 12" away from the nose was as little as 0.001"; an adaptor was supplied to sleeve the spindle from a No. 3 Morse taper to a No. 2. Of traditional American pattern, the ground-finish bed had two raised Vs and two flats, the saddle ran on one V and one flat - the tailstock on the other V and flat. The bed could, at extra cost, be ordered flame-hardened. Mounted independently of the lathe, the simple, bronze-bearing countershaft was able to provide twelve speeds of 55, 80, 112, 144, 200, 253, 353, 459, 645, 831, 1157 and 1450 rpm. - although the very early 9-inch lathes may have had the backgear speeds set somewhat lower. The motor, fastened directly to the countershaft casting, was fitted with a two-step pulley - whilst the countershaft-to-spindle drive used a 3-step V pulley. The belt was tensioned by a traditional "over-centre" lever with a screwed adjuster. Although Logan lathes are rare in Great Britain, in early 1999 a strange 9" lathe, with no maker's markings and looking like across between a South Bend and a Boxford was hauled out of a van in the author's driveway with the riposte, "Bet you don't know what this is, then!". As the owner didn't believe me when I suggested that it might be a Logan from the USA, I told him to check if the spare headstock bearings that lay in the bottom of the accompanying bits-and-pieces box were marked "New Departure", a name unheard of amongst amateur engineers in England and often fitted to Logan lathes. He almost fell over backwards when that, indeed, proved to be the case..
|
|
|
|
|
|
|
|
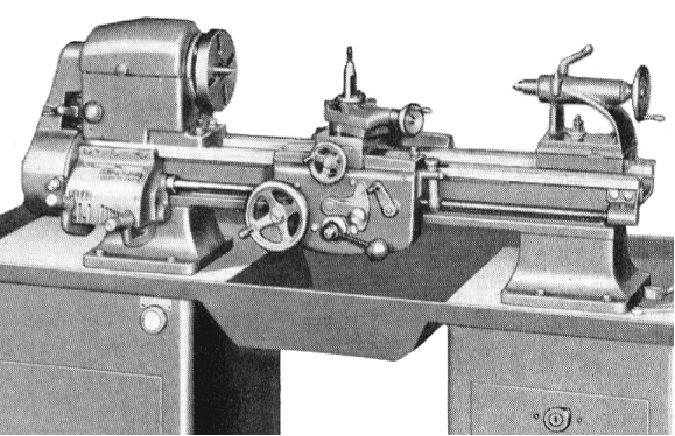 |
|
|
|
|
|
|
Logan 10" Model 1825 on the underdrive cabinet stand with screwcutting gearbox and power cross feed.
Although one might have expected Logan to build their popular 10-inch lathe on the same bed as the 9" model, this was not the case, instead it was 7/8" wider over the ways and the standard between-centres capacity increased from 17" to 24" and the longer-bed version from 28" to 33". This was obviously a serious upgrade, and not some mere tinkering with the specification. Fitted as standard with power cross feed the lathe had, like the 9-inch, the option of screwcutting by changewheels or by a full threads and feeds' gearbox. It could be supplied for bench or stand mounting with, originally, flat belt drive. By 1953 V belts had been introduced and the bench model employed all-V-belt drive, 12-speed, rubber-mounted countershaft unit with its spindle running on ball bearings. The belt tension between lathe and countershaft was relaxed by an automatic coupling when the headstock-guard cover was raised. Alternatively, in the 24" version only, it could be fitted to a neat, underdrive cabinet stand which held a 16-speed, ball-bearing countershaft which used three belt runs to transmit power to the headstock spindle. The first belt, from the two-step motor pulley, was arranged in a South Bend-like manner with a double-step V pulley on the motor transmitting power via a V belt to a large-diameter, two-step flat pulley on the countershaft. A standard V belt and pulley arrangement then provided a choice of 4 (rather close) ratios to an upper countershaft - and from there a double V belt took the drive to a pulley outboard of the left-hand headstock spindle bearing. The models intended for bench mounting could also be fitted to one of the maker's simple floor stands with cast-iron legs and sheet-steel chip trays. Apart from the increase in centre height, the headstock assembly seems to have been almost identical to that used on the 9". The spindle was fitted with a No. 3 Morse taper, a nose thread of 1.5" by 8 t.p.i., a bore of 25/32, a collet capacity of 0.5" and, like that of all Logans of the period, pre-loaded, grease-sealed, precision ball bearings - in the case of the 10-inch one double-row at the front and a single row bearing at the rear. An adaptor was supplied to sleeve the spindle nose from a No. 3 Morse taper to a No. 2. Machines intended for bench mounting were given twelve spindle speeds - whilst those fitted to the underdrive cabinet stands boasted a useful sixteen. The speeds were not the same as those of the 9" lathe, although the lowest and highest speeds of each were to within a few r.p.m of each other. The simple, plain-bearing countershaft, mounted independently of the lathe, was able to provide twelve speeds which, on the earliest lathes from 1941, ranged through 30, 56, 70, 104, 131, 244 in back gear and 179, 334, 420, 620, 780 and 1450 r.p.m. in open speed. Later lathes had all but the top speed increased slightly (which would not have helped with screwcutting on the lowest speed) and were geared to produce 55, 80, 112, 144, 200, 253, 353, 459, 645, 831, 1157 and 1450 r.p.m. The 16-speed underdrive version had a slightly different range which, on lathes built from the early 1950s, covered: 38, 53, 69, 96, 82, 112, 148 and 205 rpm in backgear and 228, 318, 414, 490, 576, 676, 888 and 1230 r.p.m. in direct belt drive. A full range of equipment to convert the lathes into production machines was available and included six-station capstan and lever-operated turret assemblies, lever and screw-feed cut-off slides with twin toolposts and quick-action collet closers. Very early lathes were fitted with a different design of apron and saddle to the later machines--the first aprons being equipped with a leadscrew half-nut guide made from a stamping and secured with two recessed machine-screws and two pins, the whole apron being about 91/4 inches long. Later, to improve rigidity, the half-nut guide was machined from a solid block and held in place with 4 exposed hex bolts - this type of apron, and hence the saddle, being some 3/4-inch or so longer. In 1954 a 10" x 24" Logan, with power cross feed as standard (but screwcutting with changewheels), cost $410; adding a gearbox increased the price to $510 whilst the most expensive model, mounted on a full cabinet stand, was listed at $647. Experienced users of 10" Logan lathes report that they are a heavy and sturdy unit, vastly superior to the more common Atlas-Craftsman lathes. However, to be fair, the latter two were considerably cheaper - the 12" Craftsman version costing only $260 in basic form or $330 with a screwcutting gearbox. Given a choice today of either an Atlas-Craftsman or Logan lathe in similar condition, it must be obvious which is going to make the better long-term investment. The lightest 10" lathe for bench mounting weighed 435 lbs whilst the heaviest, on the cabinet stand, turned the scales at 765 lbs.
|
|
|
|
|
|
|
|
|
|
|
|
|
|
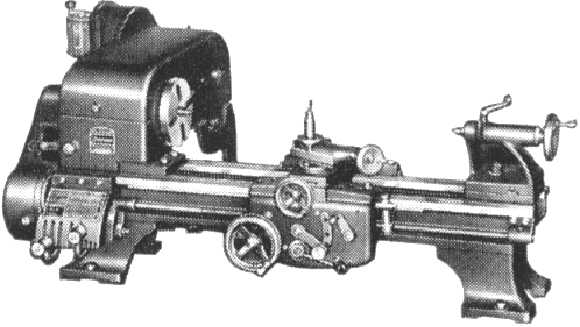 |
|
|
|
|
|
|
Logan 10" Model 1815 for bench mounting with screwcutting gearbox and power cross feed. This model was supplied with a 12-speed, rubber-mounted countershaft unit - which an automatic coupling to release the belt tension when the headstock-guard cover was raised.
Early 10-inch Lathes Spindle Bearings - a note by Jerrold Tiers:
On early lathes there is a flat "spring-ring", grooved into the outside of the outer race, that bears on the headstock casting for thrust; a 3-bolt cover fits behind the swarf deflector on the spindle and clamps the ring to the headstock. Swarf deflectors are now unavailable for either bearing, so it is best not to remove them - even if this seems necessary. The front bearing is a tight sliding fit in the headstock - and held to the spindle by a threaded ring. No preload is applied externally, as it is "built in". The rear bearing, which simply presses into the rear carrier on the headstock, is located by spacers and a nut on the end of the spindle.
|
|
|
|
|
|
|
|
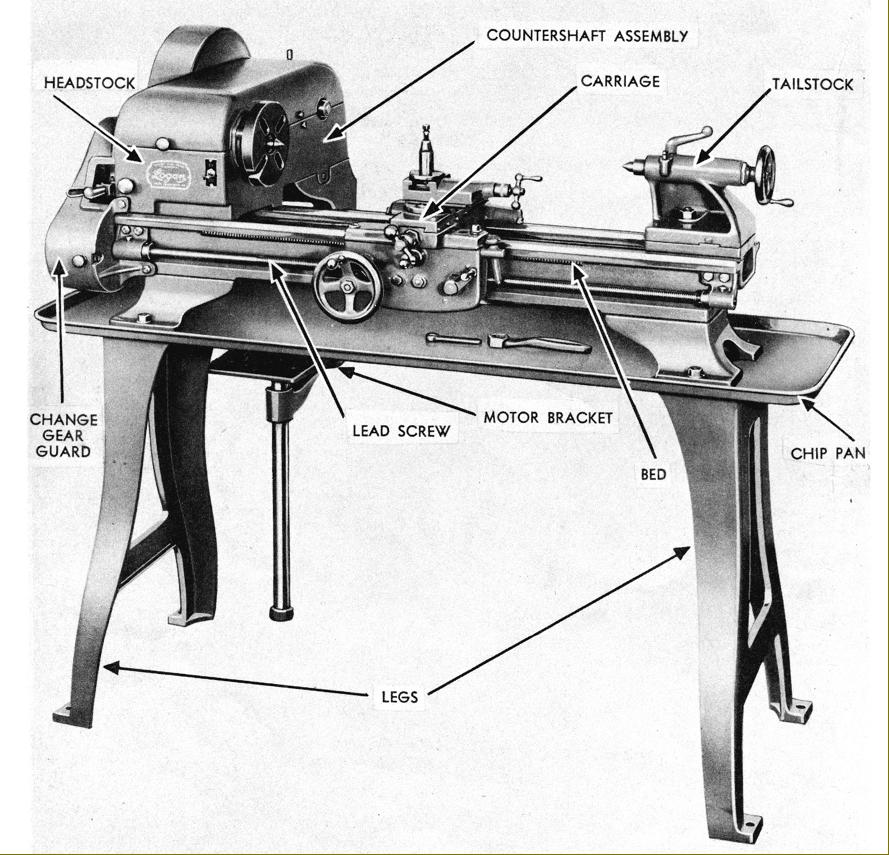 |
|
|
|
|
|
An early Logan Model 210 10-inch lathe on the maker's cast-iron "standards" with a "built-on" countershaft unit. The lathe was sold as the Model 200 for bench mounting and is also found with Montgomery-Ward badges
|
|
|
|
|
|
|
|
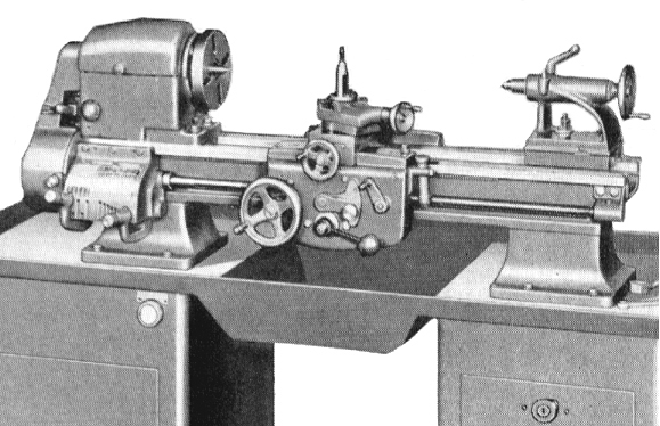 |
|
|
|
|
|
|
Logan 11" Model No. 1955 on steel pedestal cabinet base with one storage cupboard. Although the Logan 11" lathe (and the 12") used the same bed as the 10-inch - and the regular model of both sizes had the same between-centres' capacity of 24" - the long-bed version of the 11-inch was able to accept an additional 6" in length, giving a total (and very useful) capacity of 30". Fitted as standard with both a screwcutting gearbox and power cross feed the lathe was unusual in having, for so substantial a machine, the option to be supplied for bench (or leg) mounting with a separate all-V-belt drive, 16-speed, rubber-mounted countershaft unit with its spindle running on ball bearings. Because the countershaft was necessarily heavy, it was supported by on what the makers described as a patented three-point suspension, part of which included a cast-iron support bracket which, on the stand-mounted machines, reached right down to the floor. As on the 10" lathes, the belt tension between lathe and countershaft was relaxed by an automatic coupling when the headstock-guard cover was raised As a better option the lathe could also be supplied fitted to a neat, underdrive cabinet stand that held a 16-speed, ball-bearing countershaft with three belt runs to transmit power to the headstock spindle. The first belt, from the two-step motor pulley, was arranged in a South Bend-like manner with a double-step V pulley on the motor transmitting power via a V belt to a two-step flat pulley on the first shaft.. A standard V belt and pulley arrangement then provided a choice of 4 (rather close) ratios to an upper countershaft - and from there a double V belt took the drive to a pulley outboard of the left-hand headstock spindle bearing. Whilst the headstock assembly looked, externally, to be almost identical to that used on the 10" lathe it appears to have been fitted with the much more substantial, hardened and ground spindle from the larger lathes of the range. The bore of 13/8" allowed a collet capacity of 1" and an increase in the size of the spindle nose thread to 2.25" x 8 t.p.i. At this sort of size and capacity, an L-00 series or Camlock spindle nose fitting would have been preferred, but that extra-cost option was restricted to the 14" lathe. Like smaller Logans of the period the spindle, ran on pre-loaded, grease-sealed precision ball bearings - but, instead of the arrangement used on the 10-inch lathe (which had a double-row bearing at the front and a single row at the rear) the 11-inch lathe employed a single-row bearing in both locations. Whilst the 9-inch and 10-inch Logan lathes (except those with push-type collets and bar-feed, Model 830 and 1830) had a standard No. 3 Morse taper in their spindle - with an adaptor to sleeve it down to a No. 2 for regular work - the 11-inch used (like some South Bend models) a proprietary taper. Whilst this arrangement gave a slightly larger spindle bore it resulted in the need for a special adaptor - a ordinary No 3 Morse might appear to fit, but it doesn't - you will need the special part that is still available from Logan. A 0.75 h.p. ball-bearing motor (of unspecified phase) through drove the spindle through a range of 16 speeds, the bench and simple-stand models having 50, 62, 75, 90, 145, 170, 200 and 235 rpm in backgear and 325, 385, 470, 535, 885, 1020, 1230 and 1430 rpm. A slightly different range was specified for the cabinet models: 38, 53, 69, 96, 82, 112, 148 and 205 r.p.m. in backgear and 228, 318, 414, 490, 576, 676, 888 and 1230 r.p.m. in direct drive. A full range of equipment to convert the lathes into production machines was available and included six-station capstan and lever-operated turret assemblies, lever and screw-feed cut-off slides with twin toolposts and quick-action collet closers. Lightest of the 11" lathes for bench mounting weighed 505 lbs while the heaviest, on the cabinet stand, turned the scales at 890 lbs.
|
|
|
|
|
|
|
|
|
|
|
|
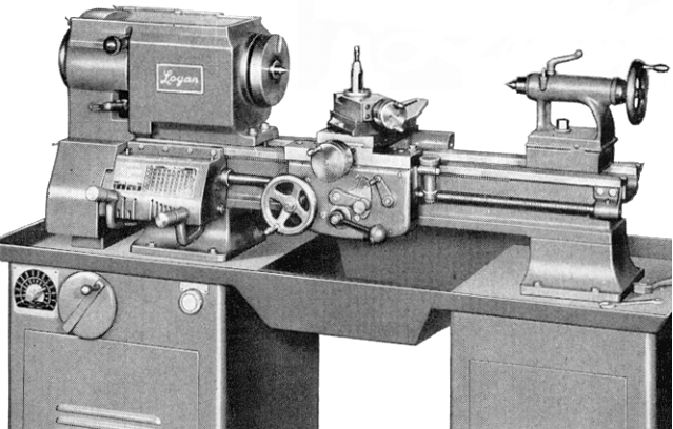 |
|
|
|
|
|
|
Logan 12" lathe Model 2555-V on Steel Cabinet Pedestal with a single-cupboard
Although the Logan 12-inch" lathe used the same bed as the 10 and 11-inch machines because of its slightly longer, more robust headstock its between-centres' capacity was one inch less in both its standard and long-bed versions at 23" and 35" respectively. Supplied as standard, on a underdrive cabinet stand with 1 HP 3-phase variable speed drive - the lathe was also fitted with a screwcutting gearbox and power cross feed as part of its regular specification. Significantly different to the smaller models the headstock assembly was fitted with a much more substantial, hardened and ground spindle - although this was also used by the 11" lathe, but in a lighter assembly. The bore of 13/8" allowed a collet capacity of 11/16 " and a generously-proportioned spindle-nose thread of 2.25" x 8 t.p.i. However, at this sort of size and capacity, an L-00 series or Camlock spindle-nose fitting would have been far preferable to a thread, and indeed, the former was available, but only as an option and at extra cost. The spindle, like that of all Logans of the period, ran on pre-loaded, grease-sealed precision ball bearings - and in the case of this 12-inch lathe, a total of four were used. An adaptor was supplied to sleeve the spindle nose from a No. 3 Morse taper to a No. 2 for regular work. A full range of equipment to convert the lathes into production machines was available and included six-station capstan and lever-operated turret assemblies, lever and screw-feed cut-off slides with twin toolposts and quick-action collet closers. The lightest 12" lathe weighed 1040 lbs, the heaviest 1075 lbs.
|
|
|
|
|
|
|
|
|
|
|
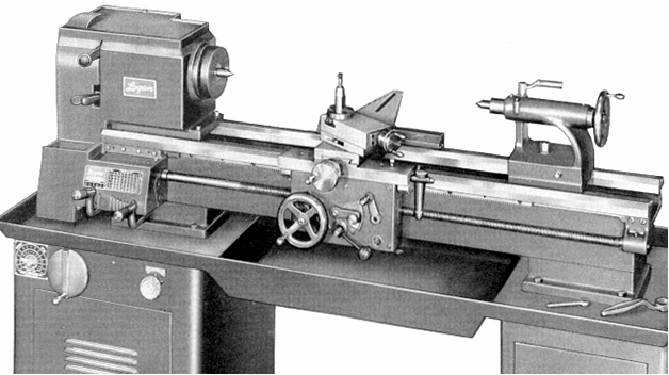 |
|
|
|
|
|
|
14" Logan Model 6560 with taper turning unit.
Largest of the early 1950s machines made by the Logan Company the 145/8" x 40"" employed a much more massive, ground-finish bed than the smaller models, a full 10" wide across the ways (as a comparison, the rugged 12" Colchester Student has a bed 83/8" wide). Although a large, heavy, machine no separate powershaft was fitted for sliding and surfacing speeds, the same simple, slotted leadscrew arrangement as used on the lighter lathes being employed instead - however, the apron was oil filled, a screwcutting gearbox and power feeds were supplied as standard and the tailstock was fitted with a No. 3 Morse taper socket. Spindle speeds, running from 38 to 186 rpm in backgear and 240 to 1200 rpm in direct drive, were controlled by a continuously-variable transmission, exactly as used on the other lathes, with the power supplied by a 1750 rpm, 2 H.P. 3-phase motor controlled by a factory-fitted drum-type reversing switch. The drive system was dynamically balanced, to ensure the smoothest possible running and minimise the transmission of vibration marks to the workpiece. Like that of all Logans of the period the 13/8" bore spindle, ran on pre-loaded, grease-sealed precision ball bearings - a pair of double-row bearing at the front and a single row bearing at the rear - and carried a 2.25" diameter 8 t.p.i thread. Fortunately a L-00 taper was available as an optional extra and, all things being equal, a used lathe with this fitting would be much preferable to one with a screwed nose. Supplied with each 12" lathe was a driver plate, two No. 3 Morse taper centres, a dial thread indicator, a spindle sleeve adaptor to No. 2 Morse taper - and a tailstock wrench. With an overall length of 83", a width of 27" and a height of 51" with a motor installed it weighed approximately 1850 lbs. A developed version of the machine - the Model 6565 - featured a top speed of 2500 rpm, a hardened bed, and possibly other improvements.
|
|
|
|
|
|
|
|
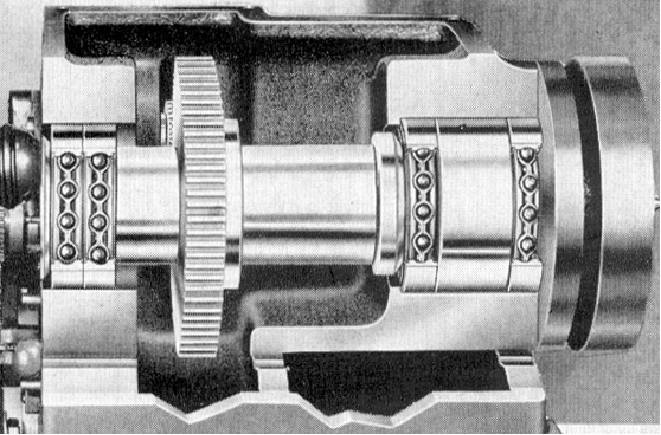 |
|
|
|
|
|
|
Logan 12" spindle, bearings and backgear All Logan lathes had spindles supported on grease-packed ball-races , with the preload set by the bearing manufacturers. Although the headstocks of the 9", 10" and 11" machines were of very similar appearance and design, the 11" model appears to have been fitted with the heavier, larger-bore spindle from its bigger brothers but with a single-row bearing at both front and rear. The 12" and 14" lathes both had more massive headstocks in line with their much heavier-duty capacity. The precision bearings were manufactured by "New Departure" and allowed Logan to claim, for these models, a total run-out of within 0.0005" twelve inches from the front bearing. On early 10-inch lathes there was a flat "spring-ring", grooved into the outside of the outer race, that bores on the headstock casting for thrust; a 3-bolt cover fitted behind the swarf deflector on the spindle and clamped the ring to the headstock. Swarf deflectors are now unavailable for either bearing, so it is best not to remove them - even if this seems necessary. A tight sliding fit in the headstock the front bearing was held to the spindle by a threaded ring with (as it is built in) no externally-applied preload necessary. The rear bearing, which simply pressed into the rear carrier on the headstock, was located by spacers and a nut on the spindle end..
|
|
|
|
|
|
|
|
|
|
|
|
|
|
|
|