 |
 |
 |
 |
 |
 |
 |
 |
 |
 |
 |
 |
 |
 |
 |
 |
 |
 |
 |
 |
 |
|
|
|
|
|
|
|
|
|
|
|
|
|
|
|
|
|
|
|
|
|
|
|
|
|
|
|
|
|
|
|
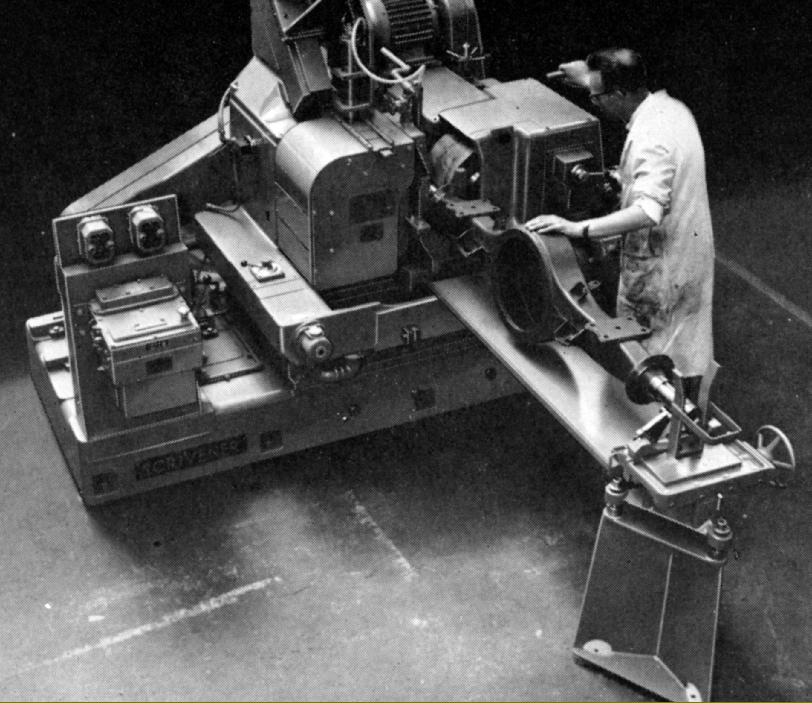 |
|
|
|
|
|
A vehicle rear axle supported on an outboard support fitted to a No. 3 grinder
|
|
|
|
|
|
|
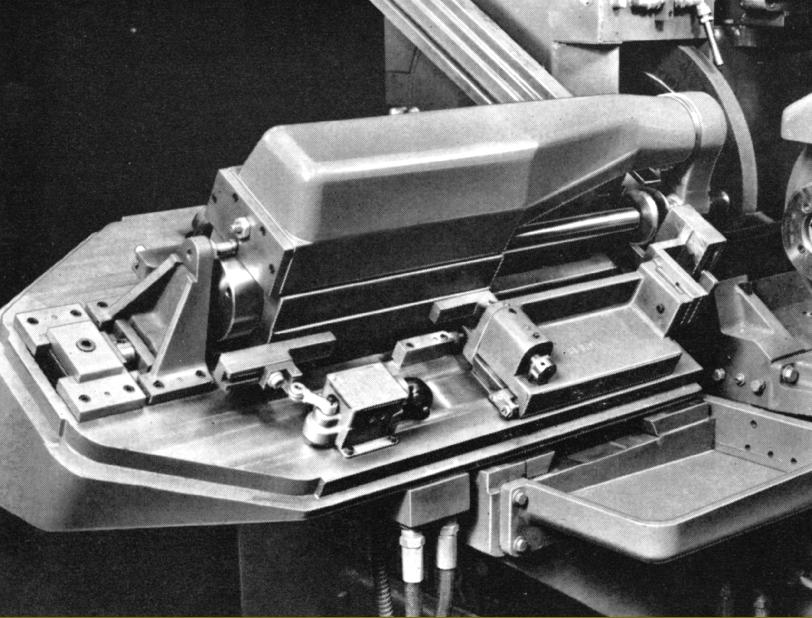 |
|
|
|
|
|
|
Equipment for ball-bearing spherical outer races to be fed by a "push-feeder" fitted to a No. 2G grinder controlled-cycle automatic. Plunge ground on their diameter, the production rate was 120 parts per hour.
|
|
|
|
|
|
|
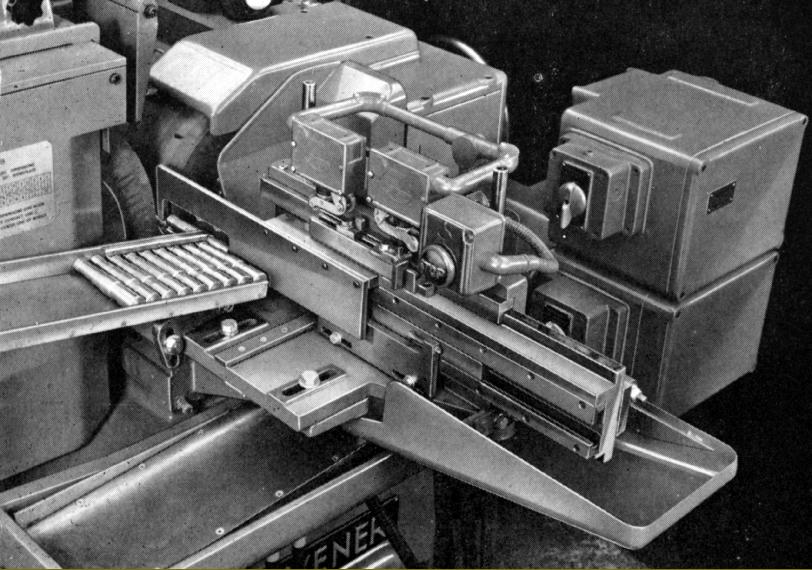 |
|
|
|
|
|
|
Multi-diameter shafts being fed by a "push feeder" into a No. 2G controlled-cycle automatic. Plunge ground on three diameters, the production rate was 180 per hour.
|
|
|
|
|
|
|
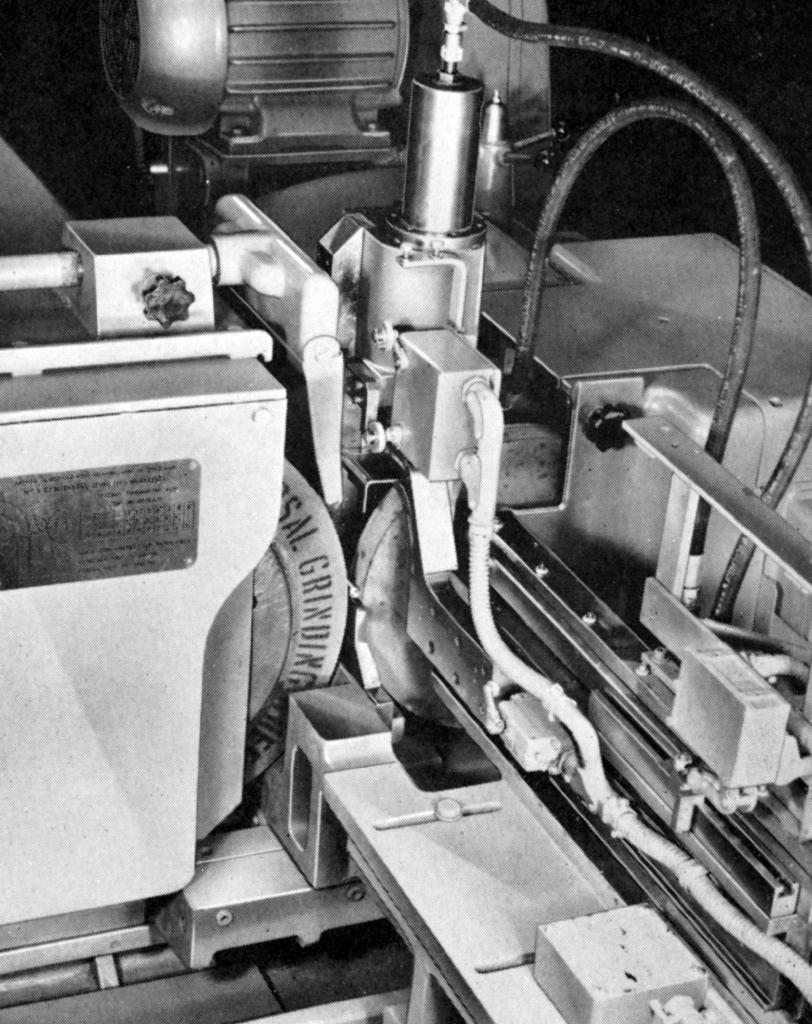 |
|
|
|
|
|
|
An "overhead loader system" consisting of a combined push-feed and rise-and-fall safety loading attachment fitted to a No. 3 controlled-cycle automatic. The worm shaft being manufactured was plunge ground on its two end diameters (with one roughing and one finishing operation), the production rate being 100 per hour.
|
|
|
|
|
|
|
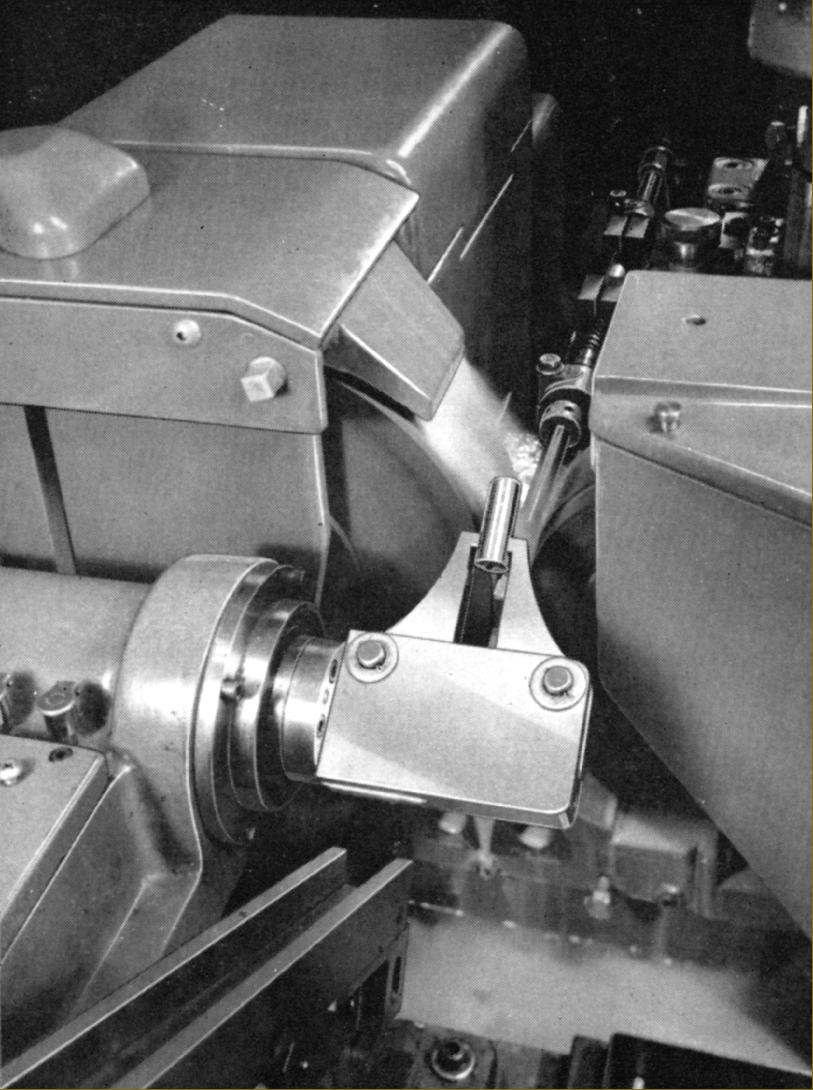 |
|
|
|
|
|
|
A "swing-overloader" shown positioning a barrel to be ground on a No. 0 controlled cycle machine. An auto ejector, variable timer and fine-feed was also fitted. The component was Plunge ground on two diameters, with a production rate of 240 per hour.
|
|
|
|
|
|
|
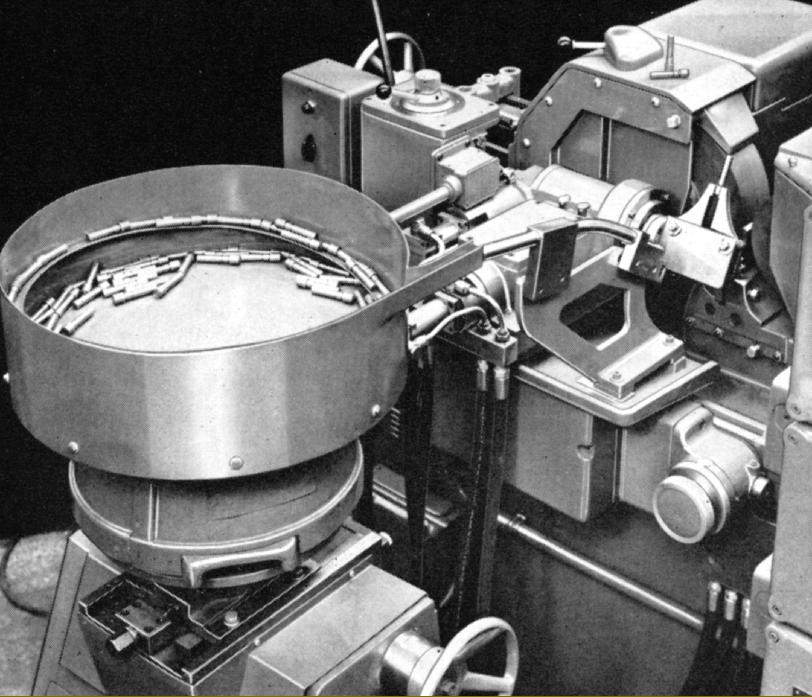 |
|
|
|
|
|
|
A "swing-overloader" and vibratory feeder together with a custom workplate and an auto ejector shown plunge grinding a punch on two diameters and a taper. The production rate was 400 per hour.
|
|
|
|
|
|
|
|
|
|
|
|
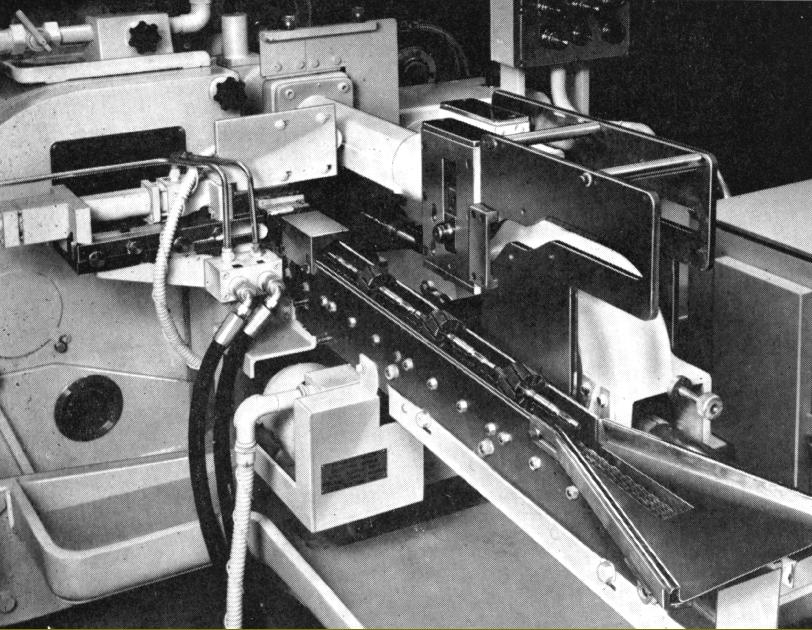 |
|
|
|
|
|
|
A No. 2G controlled cycle automatic being used to grind rotor shaft assemblies. The loading equipment in use consists of a conveyor, "roto-tip" feeder, custom wheel spacers, workrest and formers together with a micro-sizing unit and variable timer. Plunge ground on two diameters, the production rate was 350 per hour.
|
|
|
|
|
|
|
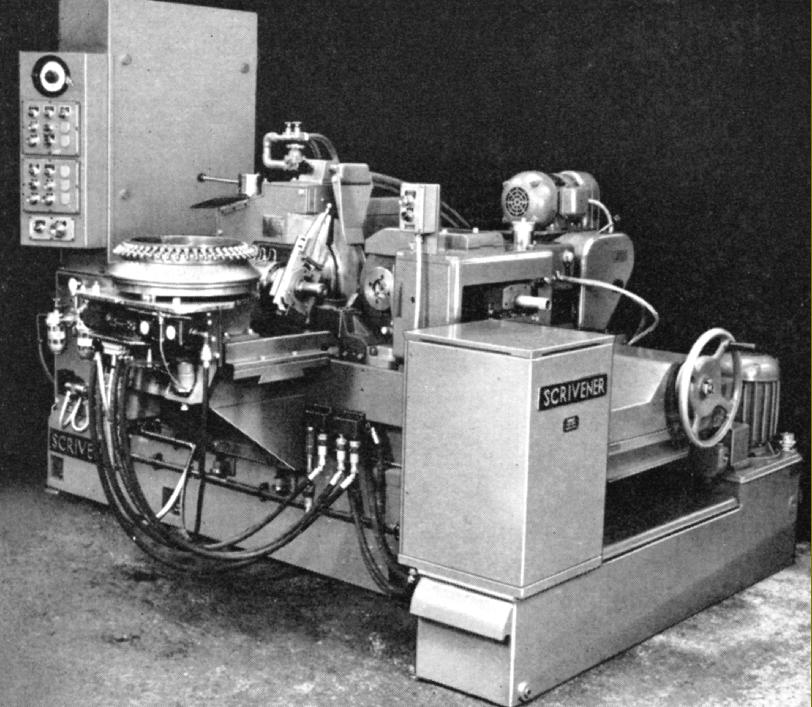 |
|
|
|
|
|
|
A "swing-overloader" feeding ball pins into a No. 2G controlled-cycle automatic. The equipment used included a rotary indexing magazine, transfer fingers, a custom workplate, a rear radius-truing attachment and special formers. The spheres were ground simultaneously on their outside and with a radius at a production rate of 240 per hour.
|
|
|
|
|
|
|
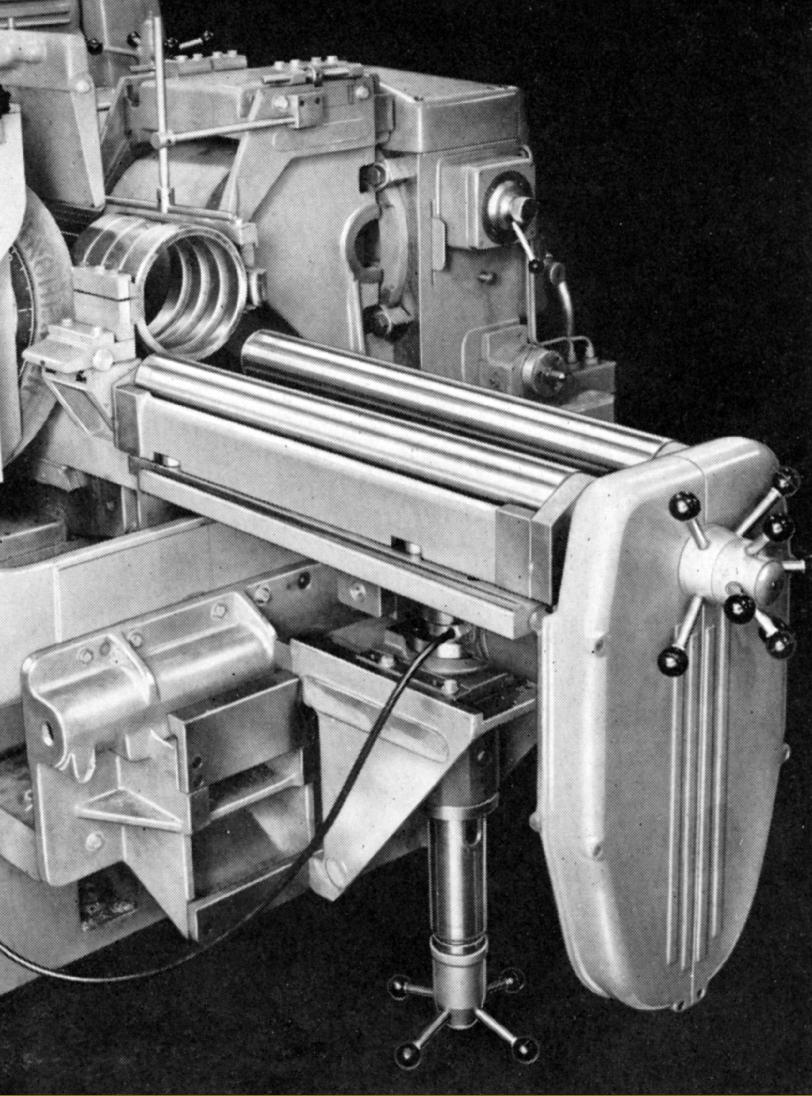 |
|
|
|
|
|
|
In this photograph a set of transport rollers is being used to feed roller bearing outer rings into a No. 3 cylindrical grinder. Other accessories fitted are guide arms, a rod-type top plate, a rear chute and a micro-sizer. Ground on the outer diameter the production was at the rate of 14 inches per minute.
|
|
|
|
|
|
|
|
|
|
|
|
|