 |
 |
 |
 |
 |
 |
 |
 |
 |
 |
 |
 |
 |
 |
 |
 |
 |
 |
 |
 |
 |
 |
 |
|
|
|
|
|
|
|
|
|
|
|
|
|
|
|
|
|
|
|
|
|
|
|
|
|
|
|
|
|
|
|
|
|
|
|
|
|
|
In production during the 1950s and 1960s and, according to the makers, designed as precision lathes able to take full advantage of the latest developments in turning tool technology, the Rosenfors RL Series of lathes was built in two centre heights: the RL-8 of 215 mm (8.5-inch) and the RL-10 of 265 mm (10.5-inch). Unlike the more work-a-day RS Series, the two types were not built with custom parts to fit them for a particular task, the only difference being the height of the headstock, tailstock and top and cross slide castings. As a dedicated precision toolroom lathe no gap-bed option was offered, but several between-centres capacities were available, the shortest being 1000 mm (40") - and then at 500 mm intervals up to 3000 mm (118"). With massive triangular cross girths between the walls, and of an enormous depth and weight, the bed was exceptionally rigid. The width of 415 mm (16.3 inches) over the carriage guides was also getting on for twice the centre eight - always a good rule-of-thumb test for a lathe aspiring to tool-room status. A combination of V and flat ways was used and the option offered, at extra cost, of hardened steel ways that could be unbolted and replaced. The bed was supported on separate cast-iron headstock and tailstock end plinths with an additional central support fitted to the long-bed versions. Continued below:
|
|
|
|
|
|
|
|
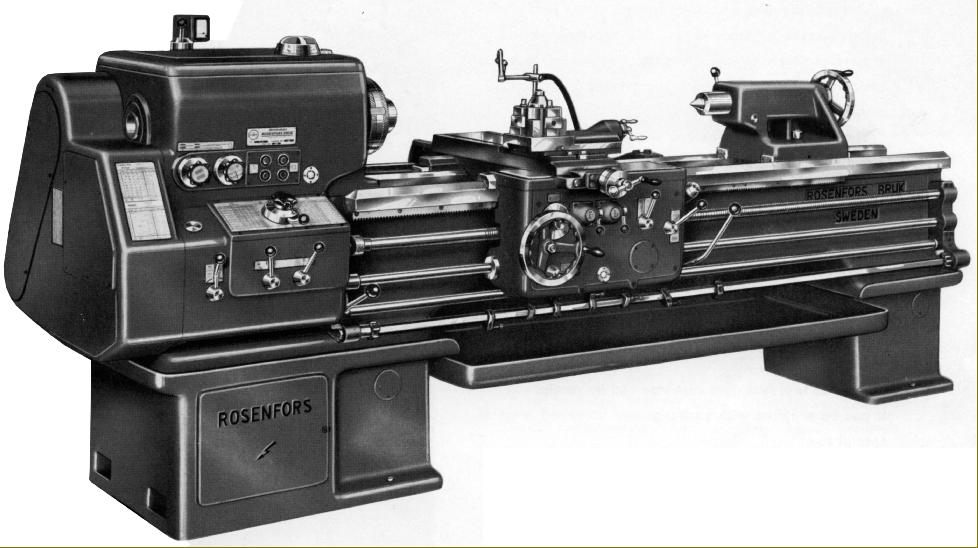 |
|
|
|
|
|
|
Rosenfors RS-25/RS-30F heavy-duty lathe
Continued: With all gears and shafts hardened and ground - and everything turning on roller and ball races - the heavily-built headstock could be supplied with either a manual speed change by four levers arranged in concentric pairs on two shafts or with hydraulic operation - in which case speed selection demanded little more than rotating a dial. Twenty-four speeds were provided, from 15 to 1500 r.p.m. powered by a 15 h.p. motor bolted to the back of the headstock-end bed plinth and with the drive taken by five V-belts. Also available was an alternative specification - a 20 h.p. that enabled an improved speed range from 20 to 2000 r.p.m. to be offered - both motors were fitted with an amp metre to gauge the loading being applied. Inside the headstock was either an English Matrix or German Ortlinghaus multi-disc forward/reverse clutch unit combined with a separate - and very powerful - electrically-operated multi-disc brake that came on automatically as the operator selected neutral. Controlled by a third-rod system, with control levers just outboard of the gearbox and pivoting from the right-hand face of the apron, the system allowed the spindle to be started, stopped and reversed with consummate ease. Massively built, the spindle had a diameter of 100mm where it passed through the front bearing, a bore of 60 mm and a metric 70 internal taper. It ran in three selected, high-precision bearings - an adjustable double cylindrical roller at the front, a single roller at the back plus another of the same type in a mid-way support. As the rollers bearings were not the tapered type, thrust was taken separately against a ball bearing at the rear. The spindle nose was hardened, with option of either a standard American Long-nose taper in an L2 size - or an American A1-6. Continued below:
|
|
|
|
|
|
|
|
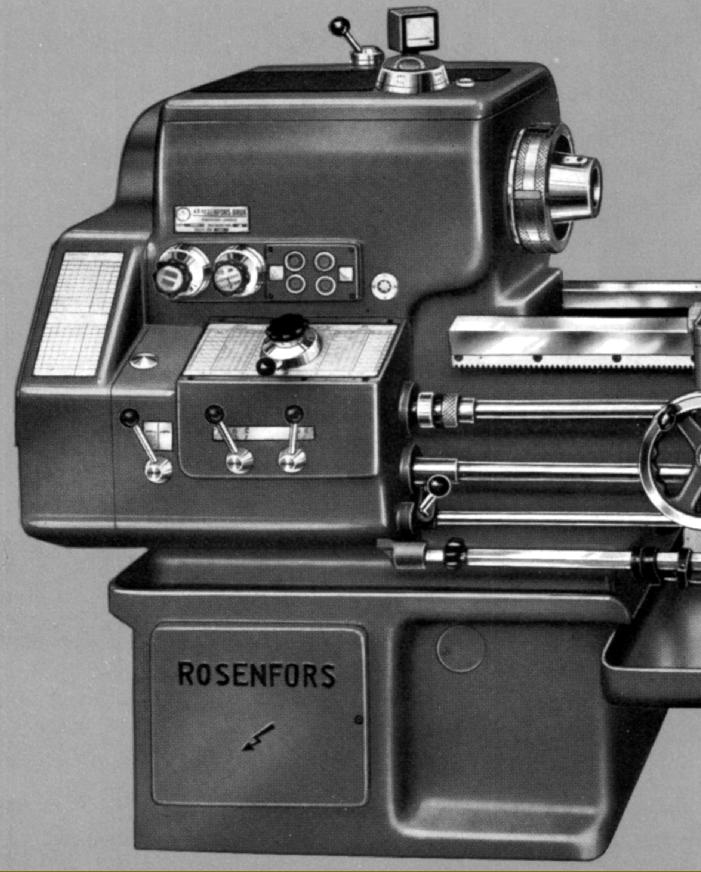 |
|
|
|
|
Continued: Screwcutting and feeds were generated by an entirely enclosed, oil-bath-lubricated gearbox holding hardened and ground gears and shafts running in ball or roller bearings. Working in conjunction with a gear system mounted inside the headstock that allowed a range of very coarse threads (long leads) to be produced at a ratio of 8 : 1 (at slow speeds only) the box was able to generate sixty inch threads from 0.25 to 60 t.p.i. and, by operating a single lever, seventy-two metric from 0.5 to 120 mm pitch. Without the special coarse-thread reduction gearing in operation the normal thread range spanned forty-five changes, this being the number of power-feed rates that could be used in day-to-day work. The full thread range required no changes of gear, or for any to be dismounted or repositioned. However, to gain access to modul and diametral pitches, a little effort was required - the sealed changewheel cover had to be opened (the gears ran in an oil bath) and the outer gear on the drive shaft reversed. Once done this gave thirty-three modul leads between M = 0.25 and M = 15 and sixty-two diametral from Dp1 to Dp120. Not only was the powershaft protected by a safety overload clutch, so was the leadscrew - an unusual fitting on any lathe. The forty-five feed rates varied from 0.1 to 3 mm (0.004" to 0.12") per revolution of the spindle and half that rate for the cross feed. The feeds could be reversed at the headstock, through a built-in tumble-reverse-like mechanism, or by a separate lever on the apron positioned immediately below the carriage handwheel. Fitted as apart of the regular equipment was an automatic release for the longitudinal feed. This used a lower rod, to which were fitted six adjustable stops, and a rotating micrometer head on the apron that caused the mechanism to trip. Continued below:
|
|
|
|
|
|
|
|
|
|
|
|
|
|
 |
|
|
|
|
|
|
Continued: Doubled-walled, with all shafts supported at both ends, the apron had an oil sump in the base with an automatic pump to distribute lubricant around the interior and to the cross-slide and bed ways. Longitudinal and cross feeds were controlled by that most desirable of features (first used by Hendey in the USA) of separate toothed-couplings operated by individual levers with a separate snap-in, snap-out engagement lever that operated by lifting the power-shaft-mounted worm gear into and out of mesh. The full-circle carriage handwheel was fitted to the left-hand side of the apron and could be disengaged if the power-feed mechanism was in use. Continued below:
|
|
|
|
|
|
|
|
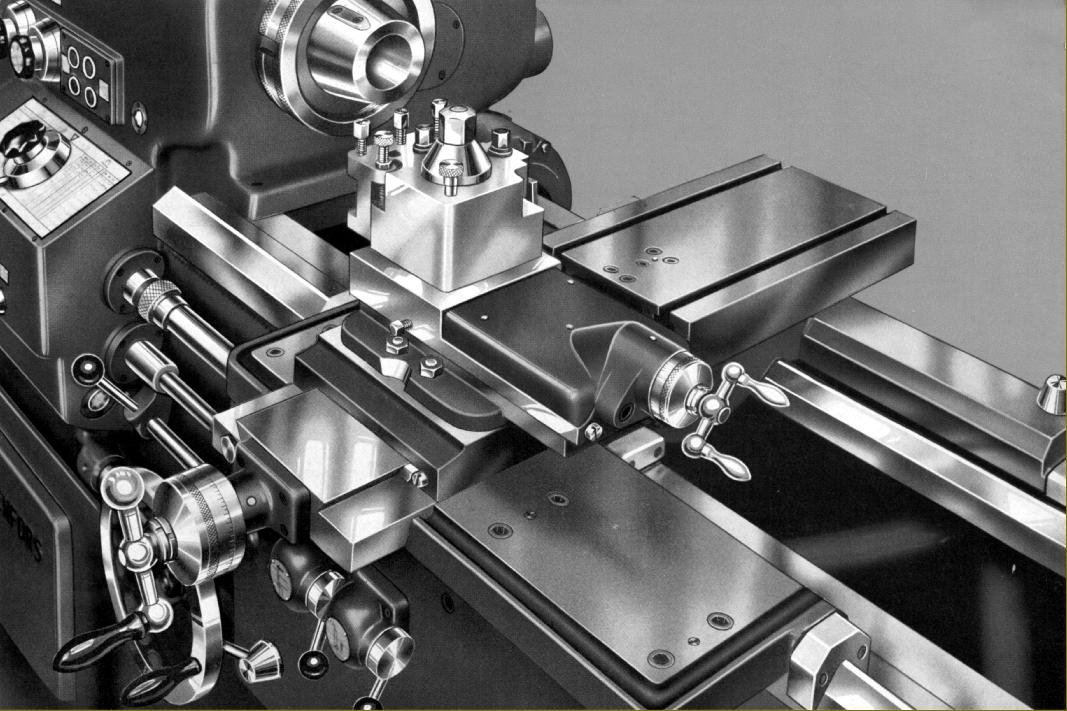 |
|
|
|
|
|
Continued: As on the contemporary RS models, realising that few operators would bother to use the saddle as a boring table, Rosenfors wisely did not bother machining the long saddle wings with T-slots, the wide surfaces being left flat with a shallow drain grove around the edge. As the bed ways reached only a short distance in front of and behind the headstock so that the cutting tool could reach right up to the spindle nose, the compound slide assembly was positioned to the left of the carriage centre line. Ruggedly constructed, the compound slide assembly had tapered gib strips on top and cross slides and feed screws fitted with radial needle-roller thrust bearings. As a further refinement, the cross-feed screw was held in tension and fitted with a two-part bronze nut, adjustable to eliminate backlash. Fitted as standard was a full-length cross-slide with a surface at the rear machines with two transverse T-slots to mount either a "Roscop" No. 2 (maximum diameter variation 140mm/5.5") or No. 12 (up to 195 mm/7.875" diameter variation) hydraulic copying attachment or a rear toolpost. Bolted to the cross-slide by four T-bolts the top slide had a cut-away at the front to reveal the degree engraving inscribed into the surface of the cross slide. The feed-screw was split in two with an upper section connected to the lower by 1 : 1 gears, this mechanism lifting the outer part of the screw so that, when cross-slide was drawn fully back, the top-slide's micrometer dial could be swung clear over the other. Plain (American style) 4-way or a Dickson-type quick-set toolholder could be fitted, with all charged extra. Designed for very heavy work, the tailstock was clamped to the bed by two bolts, though these were equipped with loose, self-hiding spanners, and fitted with an oil feed to the ways from a small reservoir. The 4-inch diameter barrel was hardened and ground, ran in a honed bore and was equipped with a drill-tang knock-out slot and an engraved ruler scale. At extra cost the tailstock could be connected to the carriage (for movement under power) and arranged so that it disengaged at the correct place by using the normal longitudinal feed knock-off stops. If any reader has a Rosenfors machine tool, the writer would be interested to hear from you
|
|
|
|
|
|
|
|
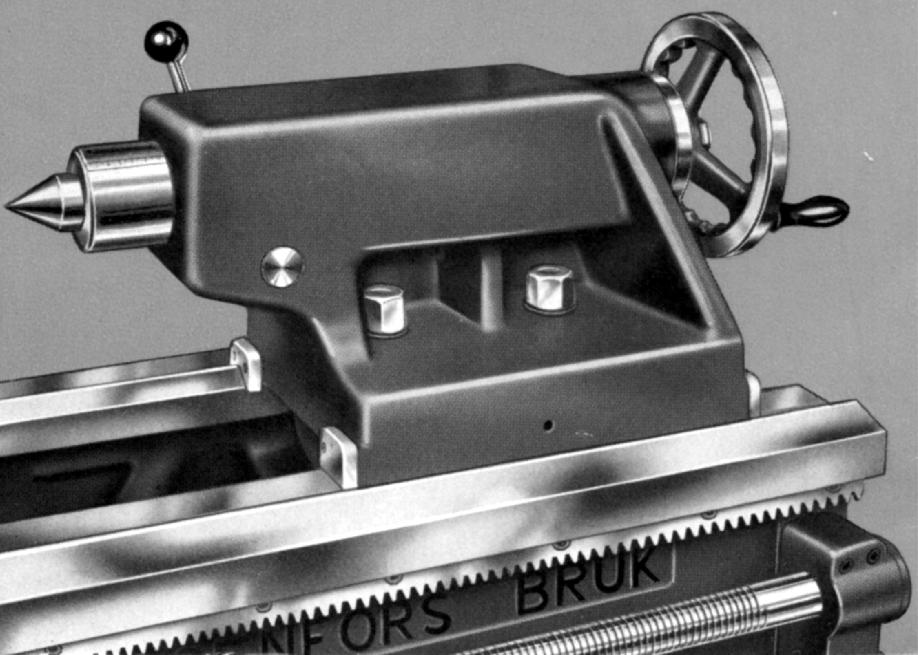 |
|
|
|
|
|
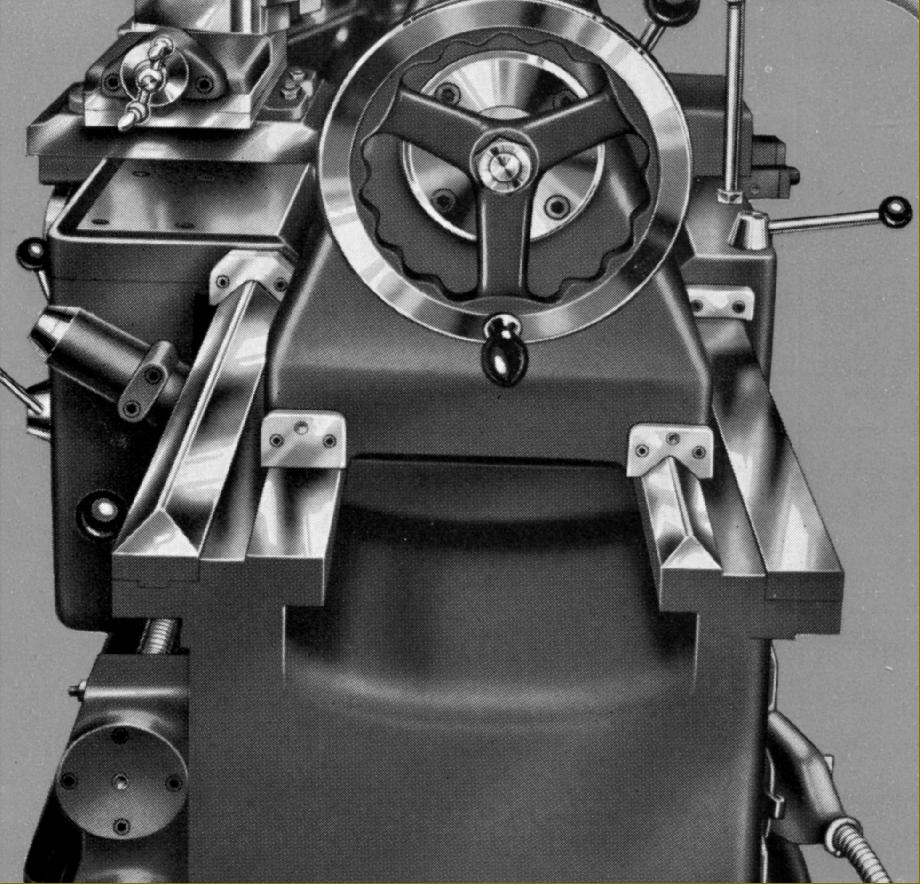 |
|
|
|
|
|
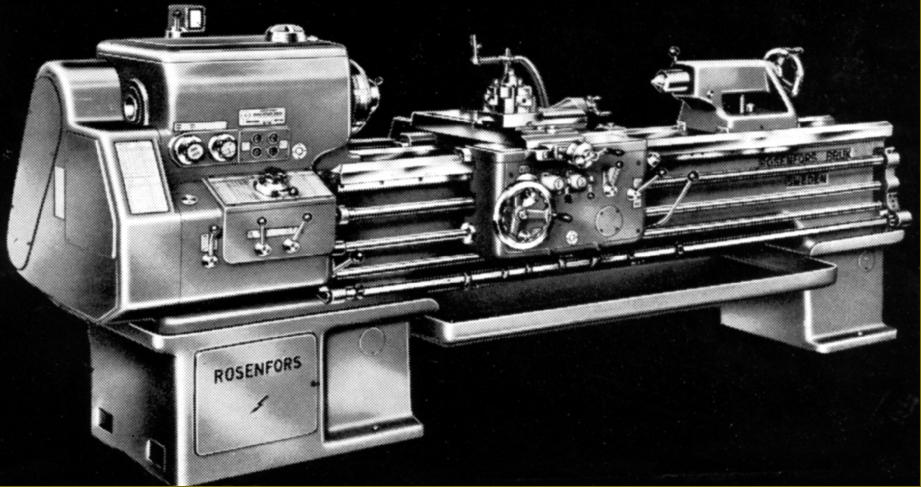 |
|
|
|
|
|
|
|
|
|
|
|