 |
 |
 |
 |
 |
 |
 |
 |
 |
 |
 |
 |
 |
 |
 |
 |
 |
 |
 |
 |
 |
 |
 |
 |
 |
 |
 |
 |
 |
 |
 |
 |
 |
 |
 |
 |
 |
 |
 |
 |
 |
 |
 |
|
|
|
|
|
|
|
|
|
|
|
|
|
|
|
|
|
|
|
|
|
|
|
|
|
|
|
|
|
|
|
|
|
|
|
|
|
|
|
|
|
|
|
|
|
|
|
|
|
|
|
|
|
|
|
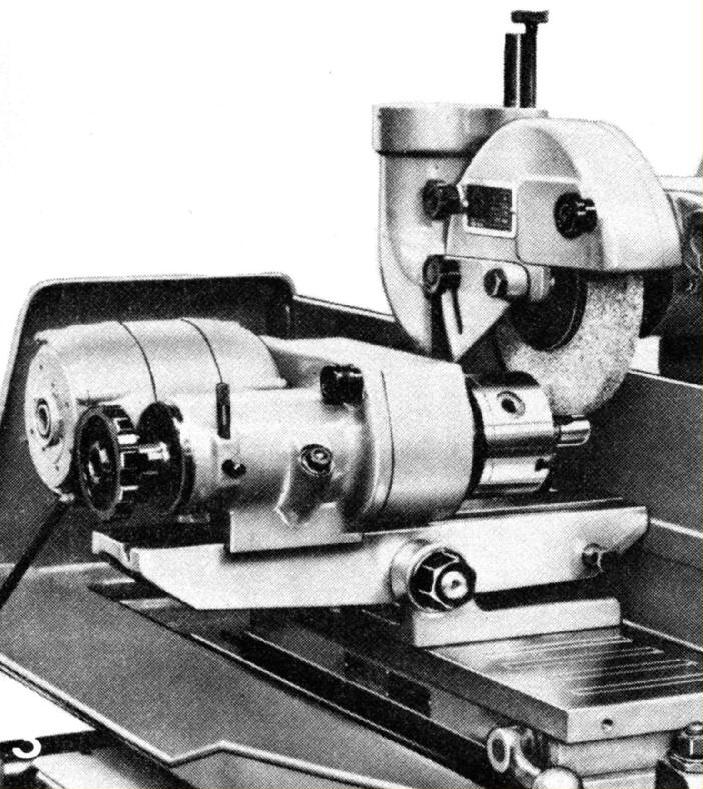 |
|
|
|
|
|
|
|
|
|
Precision Circular Grinding Attachment: this consisted of a baseplate mounted centrally on a tilting sine platform. Three speeds were available from the self-contained motor and drive assembly with the workhead accepting collets, a 3-jaw chuck or a No. 1 Morse taper centre. The maximum swing was 4.5 inches (114 mm)
|
|
|
|
|
|
|
|
|
|
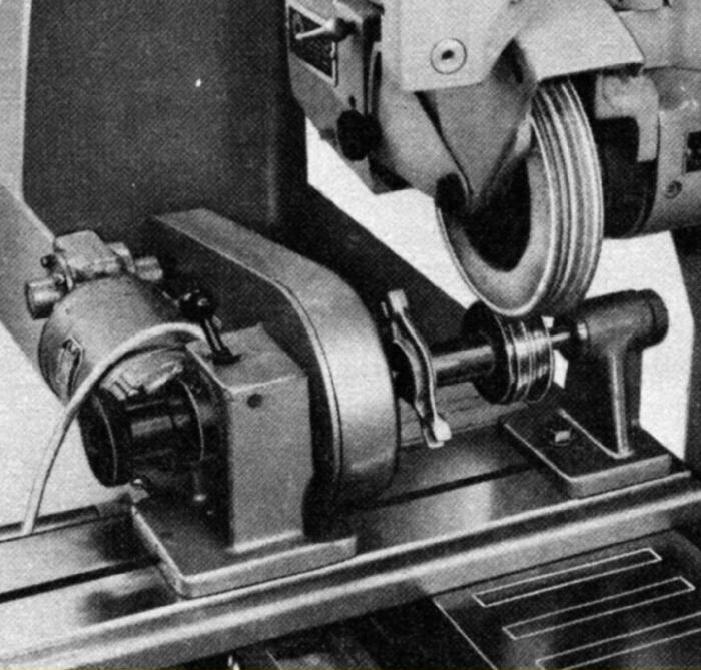 |
|
|
|
|
|
|
|
|
|
"Mayform" Cylindrical Grinding Attachment. This had a 3-speed live and dead spindle workhead with spring-loaded centres and with a length capacity of 12 inches (305 mm). The workhead was able to move along the base unit with the tailstock remaining fixed--so allowing full use to be made of the machine's cross slide travel.
|
|
|
|
|
|
|
|
|
|
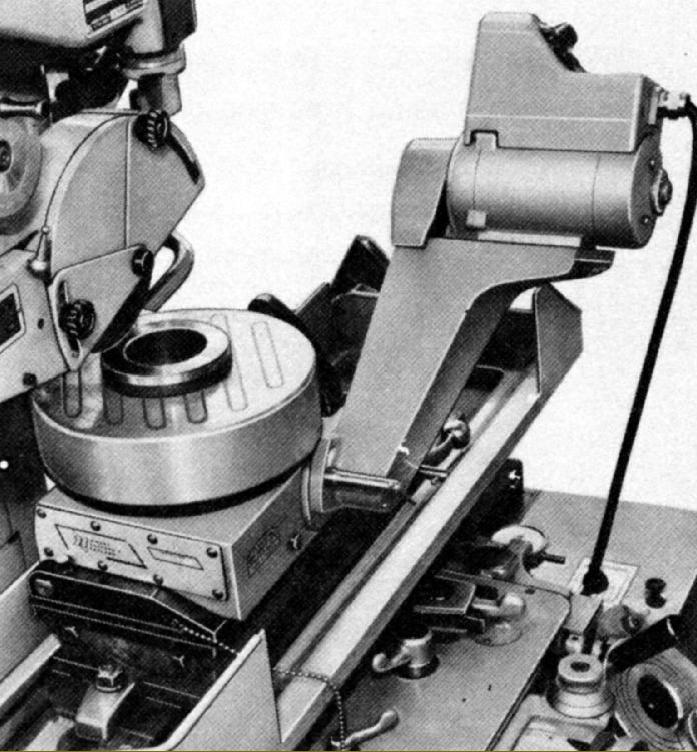 |
|
|
|
|
|
|
"Bowers" Inclinable Rotary Table. This unit was able to rotary grind wet or dry at angles from 0 to 45-degrees. The rotating magnetic chuck was driven by a sealed gearbox mounted on a sine table with a 5-inch (127 mm) sine bar setting. The gearbox was driven by a variable-speed 1-phase motor which, for increased capacity, was mounted on a moveable arm.
|
|
|
|
|
|
|
|
|
|
|
|
|
|
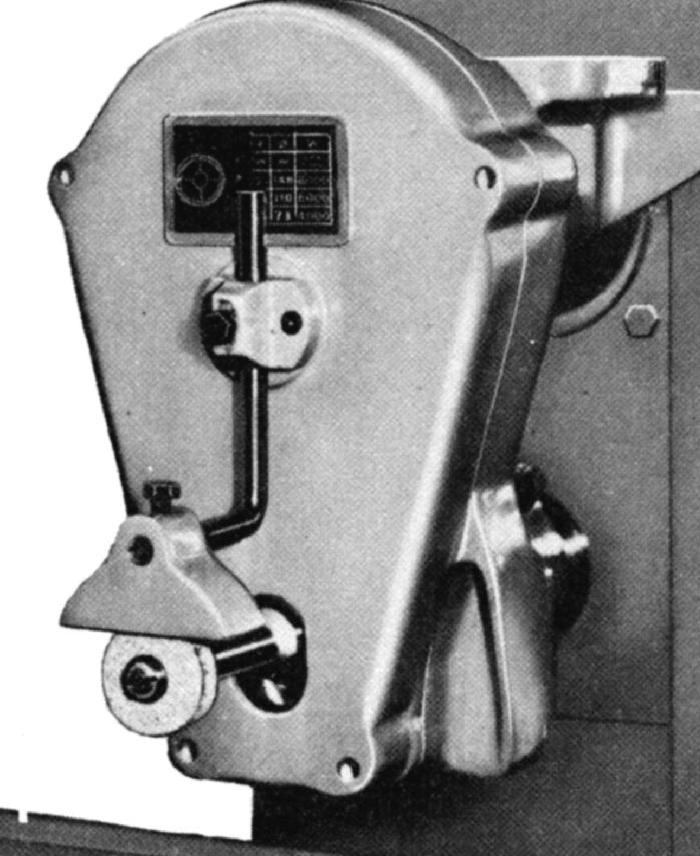 |
|
|
|
|
|
|
|
|
|
High Speed Grinding Attachment. To grind narrow slots and small radii, etc. this 3-speed unit was driven by belt from the main spindle at 4,000, 6,000 or 8,000 r.p.m.
|
|
|
|
|
|
|
|
|
|
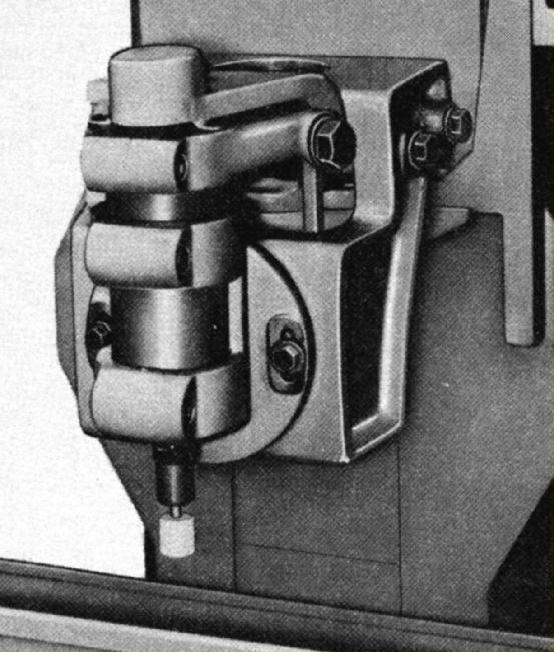 |
|
|
|
|
|
|
|
|
|
Vertical Grinding Attachment This unit, able to be tilted 10 degrees in either direction, was fitted to the wheel head and driven at up to 13,000 r.p.m.
|
|
|
|
|
|
|
|
|
|
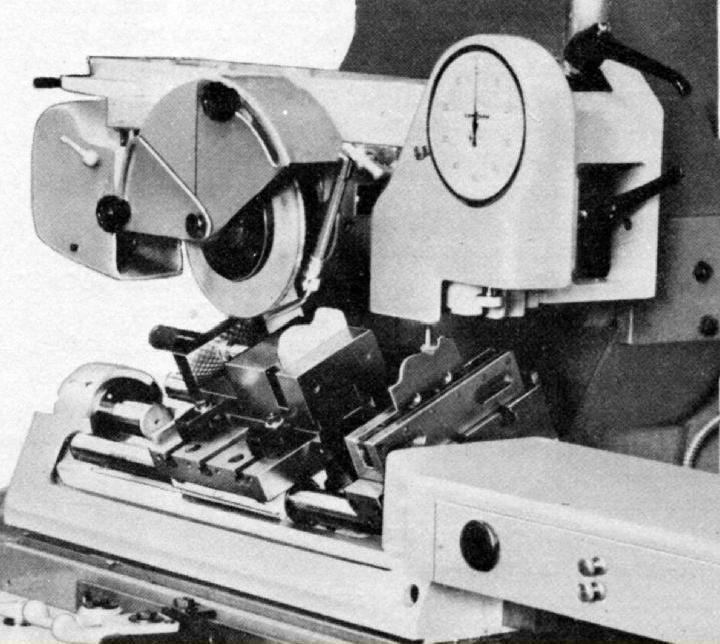 |
|
|
|
|
|
|
|
|
"Copiform" Surface/Profile Attachment. Made to fit a variety of Jones & Shipman grinders this unit adapted the host machine for accurate profile grinding. The working principle was simple but ingenious - a stylus being traversed over a template, using the cross and vertical feeds, whilst maintaining a zero setting on a large dial to which it was attached). The workpiece, set in line with the template, was passed under the grinding wheel on a reciprocating table. The grinding of vertical faces could also be accommodated by swivelled the template holder over to present them at an angle.
|
|
|
|
|
|
|
|
|
|
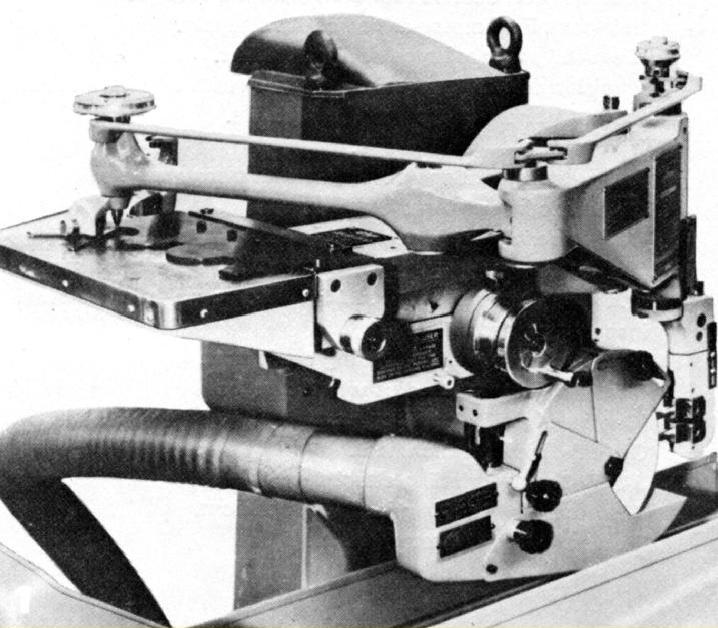 |
|
|
|
|
|
|
|
|
|
"Diaform" Wheel Forming Attachment. Made to fit many makes of grinder this unit was designed as a means of quickly and accurately "form dressing" (profiling) the grinding wheel. The shape was transferred pantographically from a prepared template and the wheel cut with a diamond-tipped tool. The template was made considerably oversized and the pantograph arm, manipulated by the operator, transferred the profile at a reduced ratio to the cutter. By this means both simple and complex shapes could be generated in a matter of minutes and increased accuracy obtained with the minimum of effort.
|
|
|
|
|
|
|
|
|
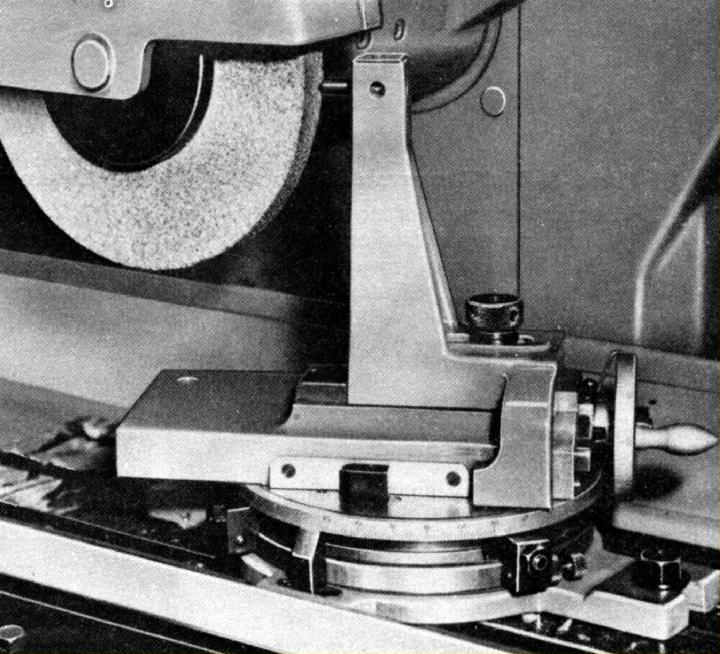 |
|
|
|
|
|
|
|
|
|
Radius/Angular Wheel Forming Attachment. An essentially simple - but beautifully-made device - designed for use on a variety of Jones and Shipman grinders and able to create angles and concave and convex radii up to I-inch (25 mm) on the grinding wheel. The pillar carrying the diamond cutter was arranged to slide horizontally on its base under the precise control of a graduated, handwheel turning a very fine-pitch screw. The pillar base was mounted on ball bearings and could be swung through 360 degrees. The height from base to diamond point was 7 13/32" (188 mm) with two alternative holes provided in which to mount the cutter. The degree-graduated swivelling base carried adjustable stops with - for obtaining extremely accurate settings - stop blocks that permitted the use of slip gauges. Supplied with the unit was an auxiliary base that allowed it to be mounted on a magnetic chuck or vice.
|
|
|
|
|
|
|
|
|
|
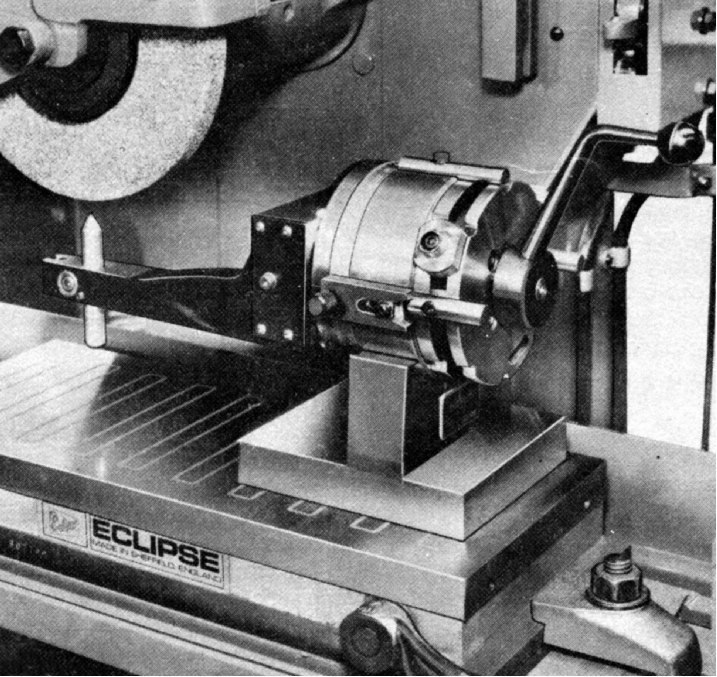 |
|
|
|
|
|
|
|
|
|
"Diaform" Tangent/Radius Dresser. Intended for the production of simple profiles on grinding wheels up to 10-inches in diameter this unit could be mounted on a number of Jones 7 Shipman grinders. All the operator had to do was pull the lever - this gave a smooth, single-handed action with a continuous movement that left no dwell marks in the wheel. The angle setting could be carried out in two ways: by setting stops against a graduated ring or by using slip gauges to make use of the sine bar principle. The radius setting was archived by the use of a 2-inch (51 mm) micrometer gauge.
|
|
|
|
|
|
|
|
|
|
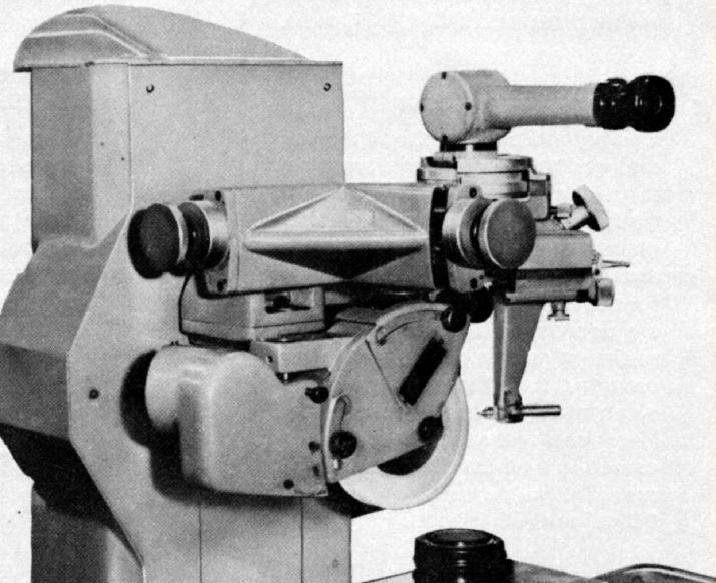 |
|
|
|
|
|
|
|
|
|
"P.G." Projectorscope Form Grinding Inspection Attachment. Intended to simplify form grinding of regular or irregular shapes whilst allowing visual control during all stages of the grinding process - the profiles of both wheel and the workpiece being under constant optical supervision. A lighting attachment directed a parallel beam of light at the workpiece so as to create a silhouette on a 7.5-inch (190 mm) diameter screen. By this means the job could be compared exactly with a tracing or acetate drawing at a choice of either 10 or 20 times magnification.
|
|
|
|
|
|
|
|
|
|
 |
|
|
|
|
|
|
|
|
|
|
|
|
|
|
|
|
|
|
|
|
|
|
|
|
|
|
|