 |
 |
 |
 |
 |
 |
 |
 |
 |
 |
 |
 |
 |
 |
 |
 |
 |
 |
 |
 |
 |
 |
 |
 |
 |
 |
 |
 |
 |
 |
 |
 |
 |
 |
 |
 |
 |
 |
 |
 |
 |
 |
 |
 |
 |
 |
 |
 |
 |
 |
 |
 |
 |
 |
 |
 |
 |
 |
 |
 |
 |
 |
 |
|
|
|
|
|
|
|
|
|
|
|
|
|
|
|
|
|
|
|
|
|
|
|
|
|
|
|
|
|
|
|
|
|
|
|
|
|
|
|
|
|
|
|
|
|
|
|
|
|
|
|
|
|
|
|
|
|
|
|
|
|
|
|
|
|
|
|
|
|
E-Mail Tony@lathes.co.uk Home Machine Tool Archive Machine Tools For Sale & Wanted Machine Tool Manuals Machine Tool Catalogues Belts Accessories Books
Ernst Kreißig (Glashütte) Watchmaker's Lathe - part 1 of 4
Glashütte Lathe Part 2 Glashütte Boxed Later Model Kreißig Screw-head Tool
Of ingenious design and beautiful execution, the triangular-bed Glashütte lathe was manufactured - as far as is known - from the late 1800s into the early years of the 20th century by Ernst Kreißig (Kreissig), a maker of tools for the horological trade from the Glashütte area near Dresden , Germany. Glashütte was not only the German centre of high-class watchmaking (and a watch-makers' school) but also home to several machine-tool builders including Karl Renner. Although Kreißig offered several versions of his lathe (including an interesting survivor, No. 295) his later models were more conventional in appearance, resembling those from Lorch and Boley - an interesting survivor, as a boxed kit, can been seen here, its differences in comparison to the early model on this page being quite clear. While the triangular bed might be considered signature design for many makes of high-quality, precision lathes from the late 1700s to the late 1800s - the most famous being Henry Maudsley's revolutionary screwcutting lathe of around 1800 - its use on so small a machine was unusual, few examples being offered by other makers. With the possibility that the first Glashutte lathe was made circa 1868, this would make it earlier than the better-known G. Boley triangular bed model. Ted Crom in his book "Horological Clock Tools 1700-1900" shows early Boley lathes of the same type as the Glashutte reproduced from a catalogue printed in London circa 1875. The same publication also had illustrations of long collets, similar to those used with the Glashutte lathe No. 481 below, but pulled into a headstock with a drawbar in the modern way. After WW2 Kreißig was trapped inside the Russian-occupied zone and, with machines only able to be bought with hard-to-obtain West German D.Marks, most of the company's output was destined for local consumption. Because the type of draw-in collets retained by a threaded tube passing up a hollow headstock spindle had yet to be invented (a development first incorporated in the American Webster Whitcomb lathe of 1888/9) the headstock of the Kreissig had to be designed in an ingenious way. This was accomplished by separating it into two sections with that on the left (its shape strongly reminiscent of watchmaker's "turns") supporting a 2-step pulley with the drive transmitted, through a pin and dog, to a spindle held in the other, right-hand element. The arrangement left a length of spindle exposed along its middle section through which was cut a slot, matching one also broached through the solid, 5.3 mm diameter stem of each collet. To lock a collet in place a long key was passed through the slots - leaving its ends protruding from each side of the spindle - and a knurled-edge ring screwed backwards against it to retain the collet. Although this assembly performed perfectly, it did require advanced standards of engineering craftsmanship to work accurately - skills that, without the aid of yet-to-be-invented shaping, planning or grinding machines, would have involved the finest of hand-fitting skills. An unusual attachment for the time - and remarkably sophisticated and delicate in operation - was a compound slide rest. Fitted with beautifully-made horn handles this followed customary practice by using ordinary right-hand threads - so giving a "cack-handed" operation where turning the screw "inwards" caused the slide to move "out". The rest of the lathe also reflected early 19th century ideas with even the fixed steady/boring collar mimicking those used on larger ornamental turning lathes with a series of different diameter bevelled holes around the periphery of a rotatable disc. The Glashütte is rare, only a handful having come to light in recent years with serial numbers: 295, 481 and 534 plus one, later boxed set. If any reader has a Glashütte, the writer would be interested to hear from you. Examples of other makers who offered triangular beds include: Boley, H Strube & Filse (also from Paris), Dalgety, an unknown make from France, yet another of East German origin and, of course, the clever Henry Maudsley with his original screwcutting-by-changewheels lathe..
|
|
|
|
|
|
|
|
|
|
|
|
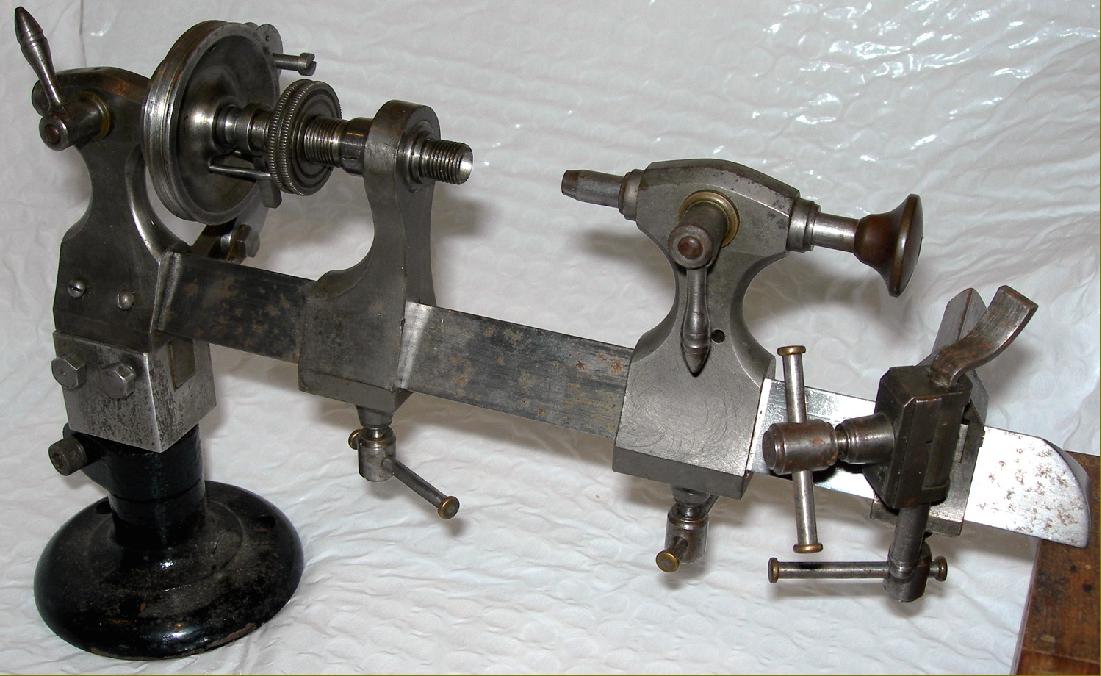 |
|
|
|
|
|
|
Despite 50 years of storage the original finish has suffered little. The shape of headstock and tailstock reflected that of contemporary watchmakers' "turns"
|
|
|
|
|
|
|
|
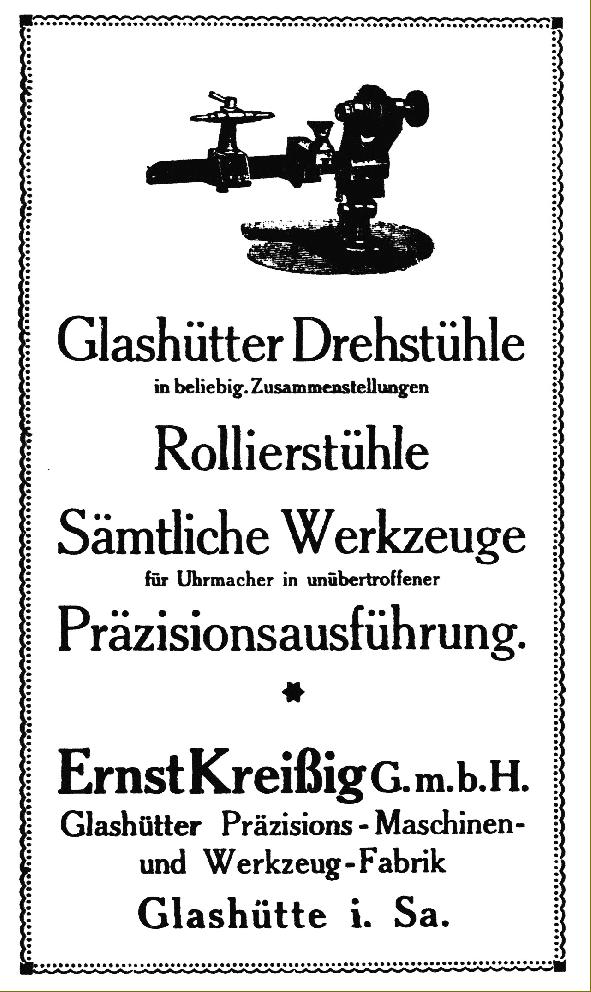 |
|
|
|
|
|
|
|
|
|
|
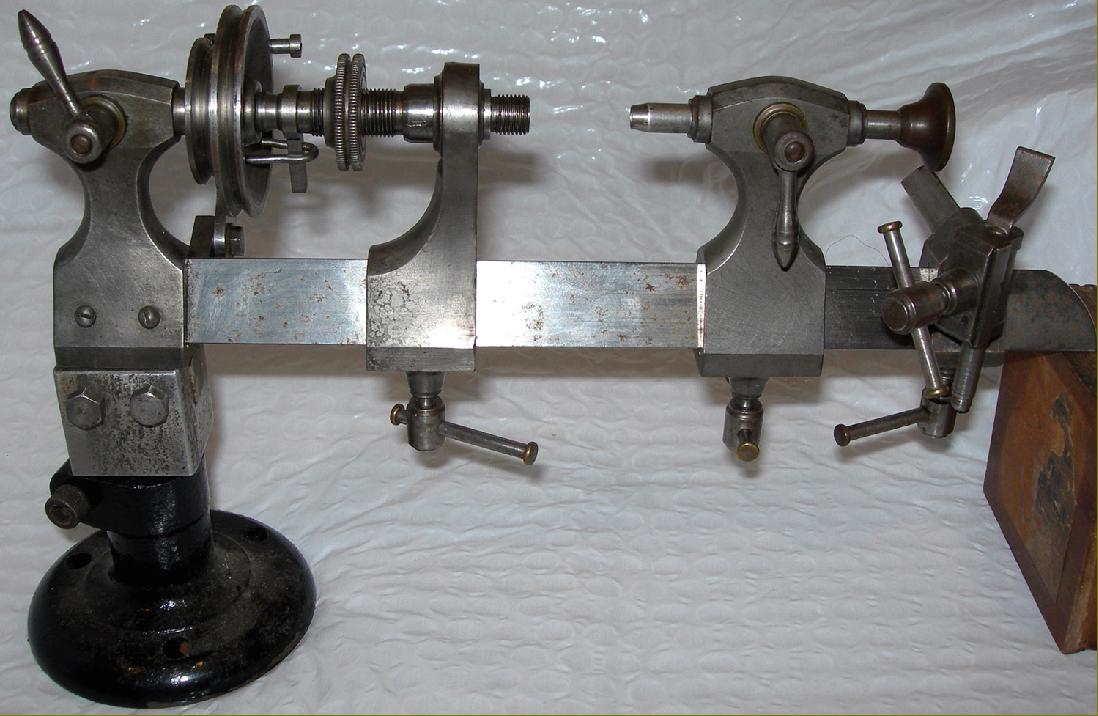 |
|
|
|
|
The ingenious arrangement of the two-part headstock assembly showing the drive pulley and the dog-driven spindle.
|
|
|
|
|
|
|
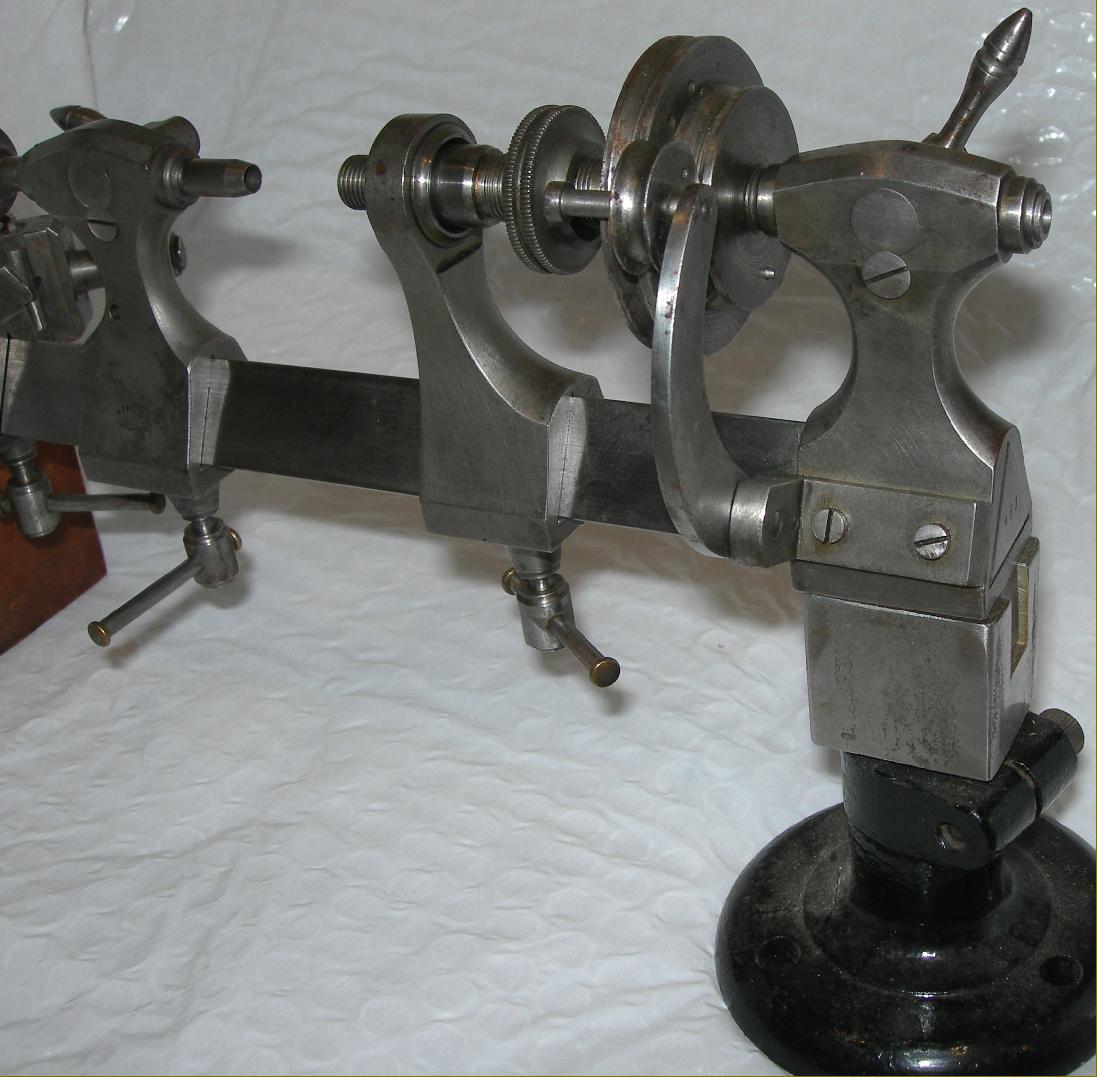 |
|
|
|
|
|
|
Rear view of the headstock showing the adjustable, belt-tensioning jockey pulley
|
|
|
|
|
|
|
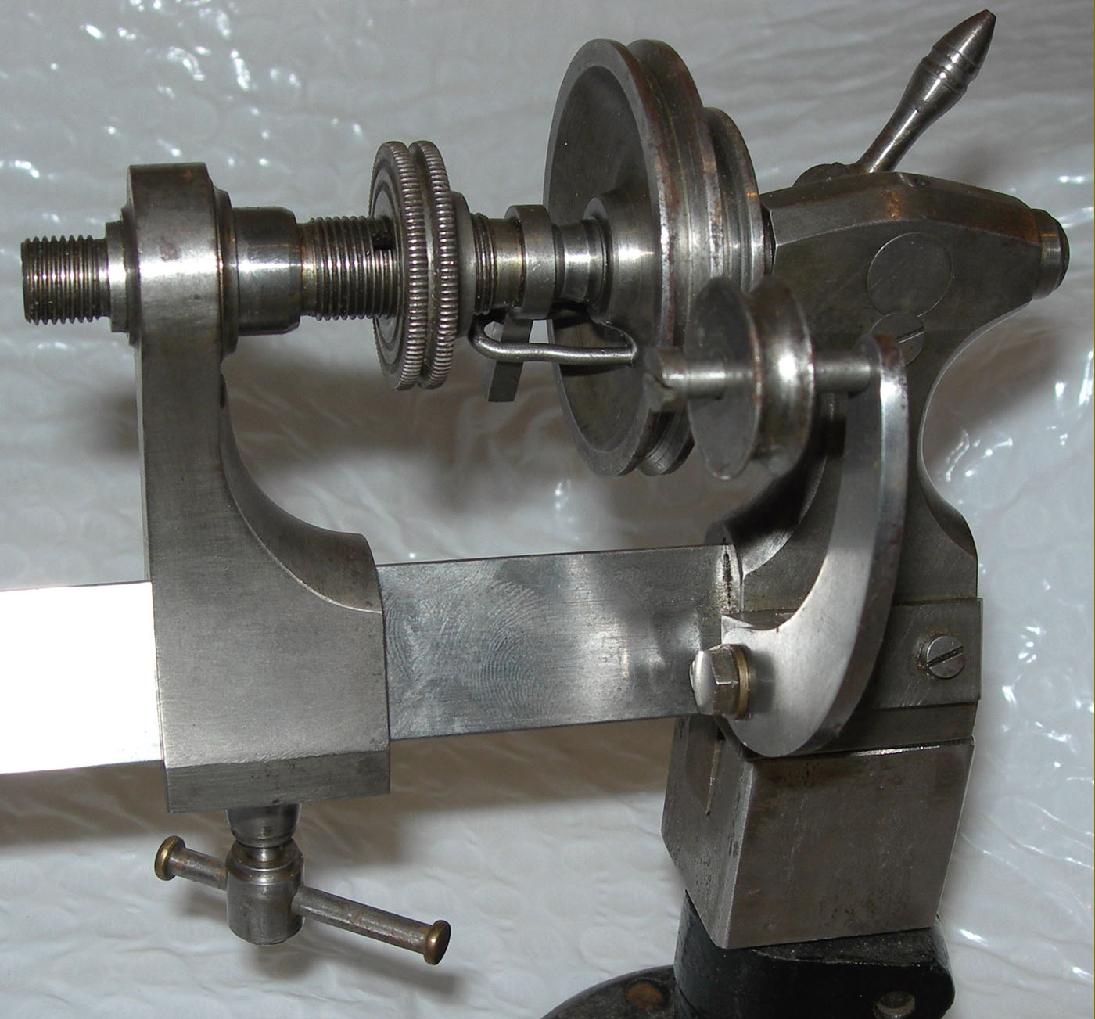 |
|
|
|
|
|
|
Visible just in front of the knurled-edge ring is the slot to accept the collet retaining key
|
|
|
|
|
|
|
|
|
|
|
|
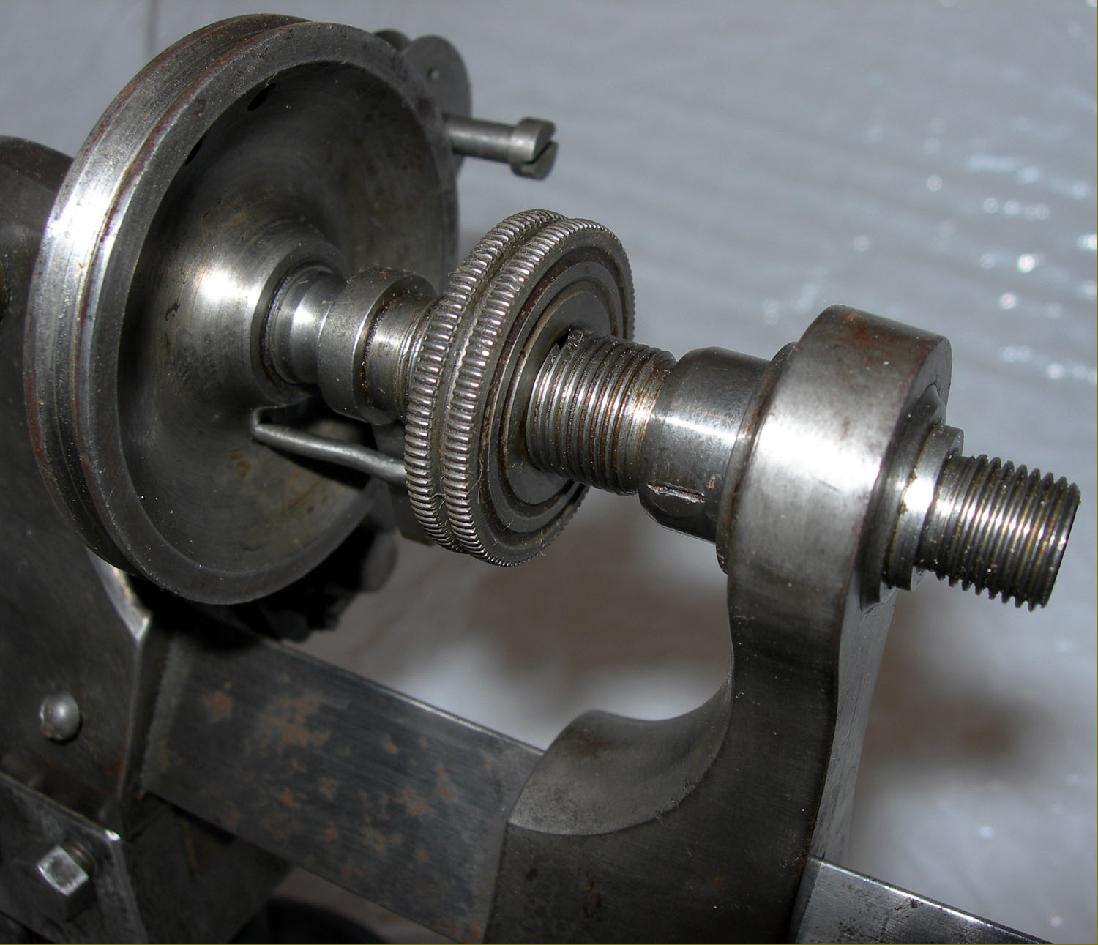 |
|
|
|
|
|
|
The knurled-edge collet tensioning ring. Note the left-hand thread on the end of the spindle - a fitting used only to hold a stepped-collet compression ring
|
|
|
|
|
|
|
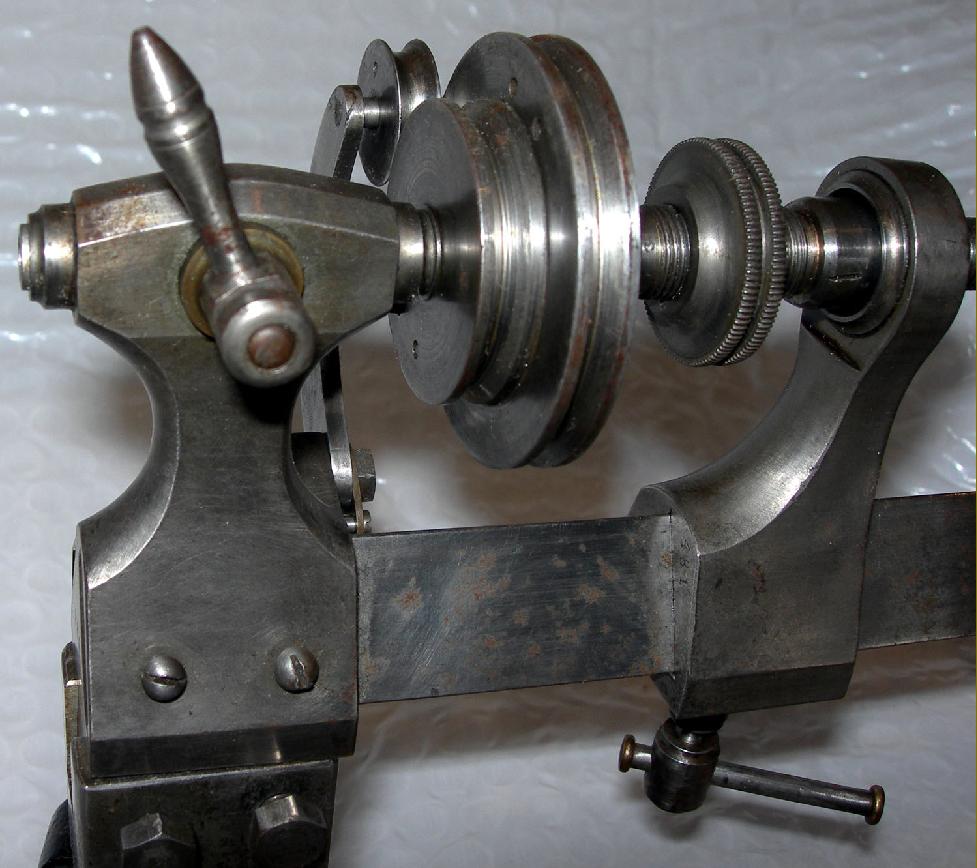 |
|
|
|
|
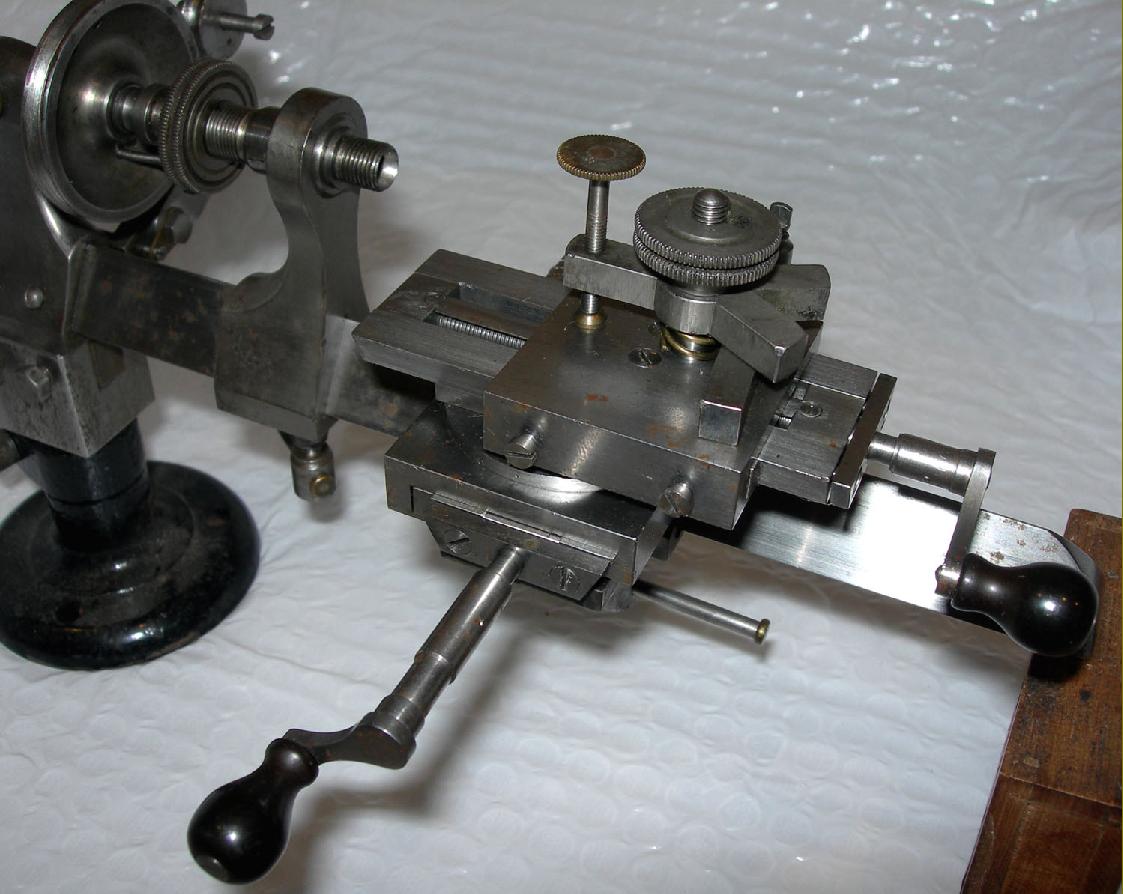 |
|
|
|
|
|
|
For its age the compound slide rest, with its horn handles, was remarkably sophisticated and delicate in operation
|
|
|
|
|
|
|
|
|
|
|
|
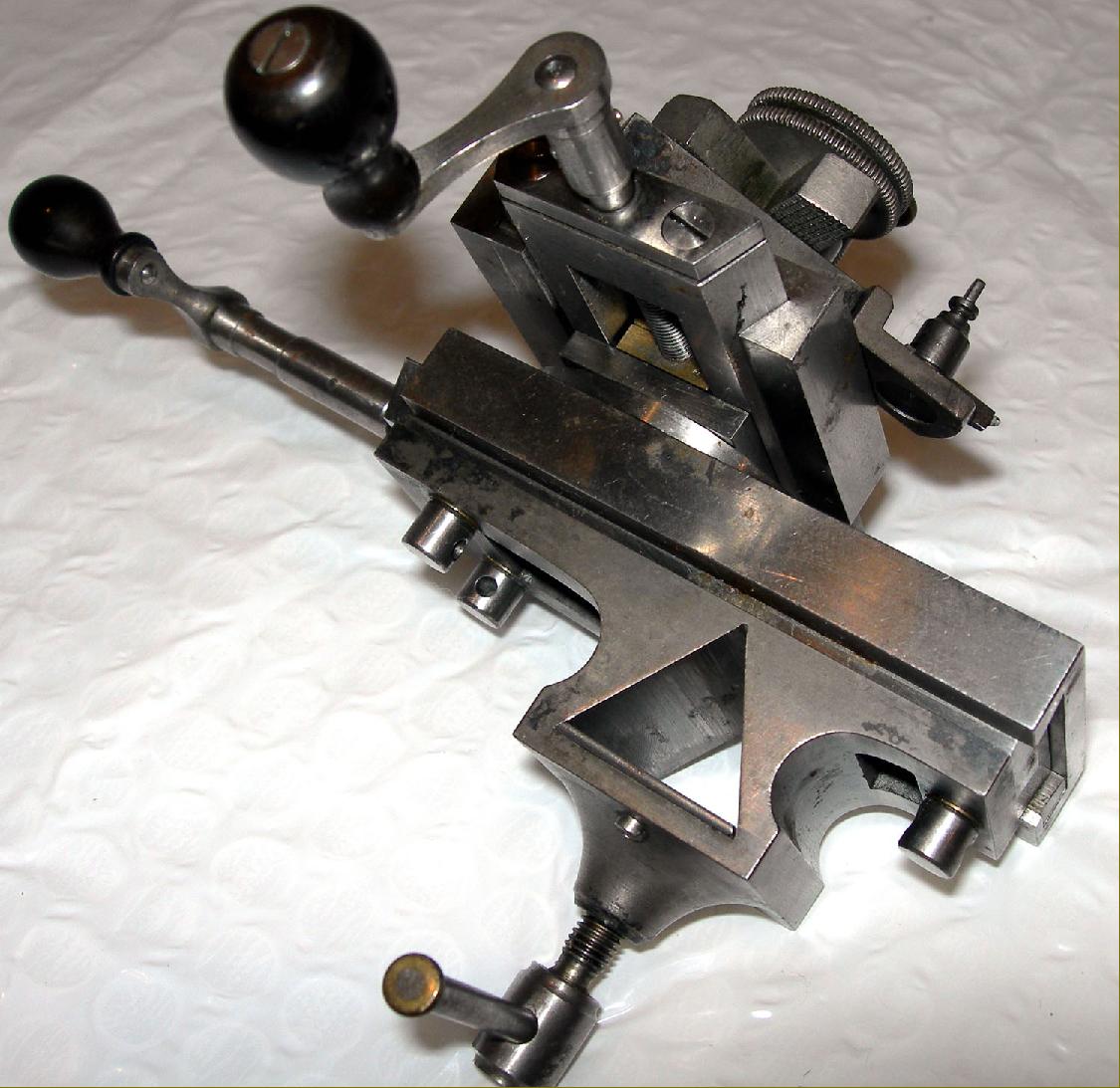 |
|
|
|
|
|
|
The superb standard of construction is even more apparent in this picture of the slide removed from the bed
|
|
|
|
|
|
|
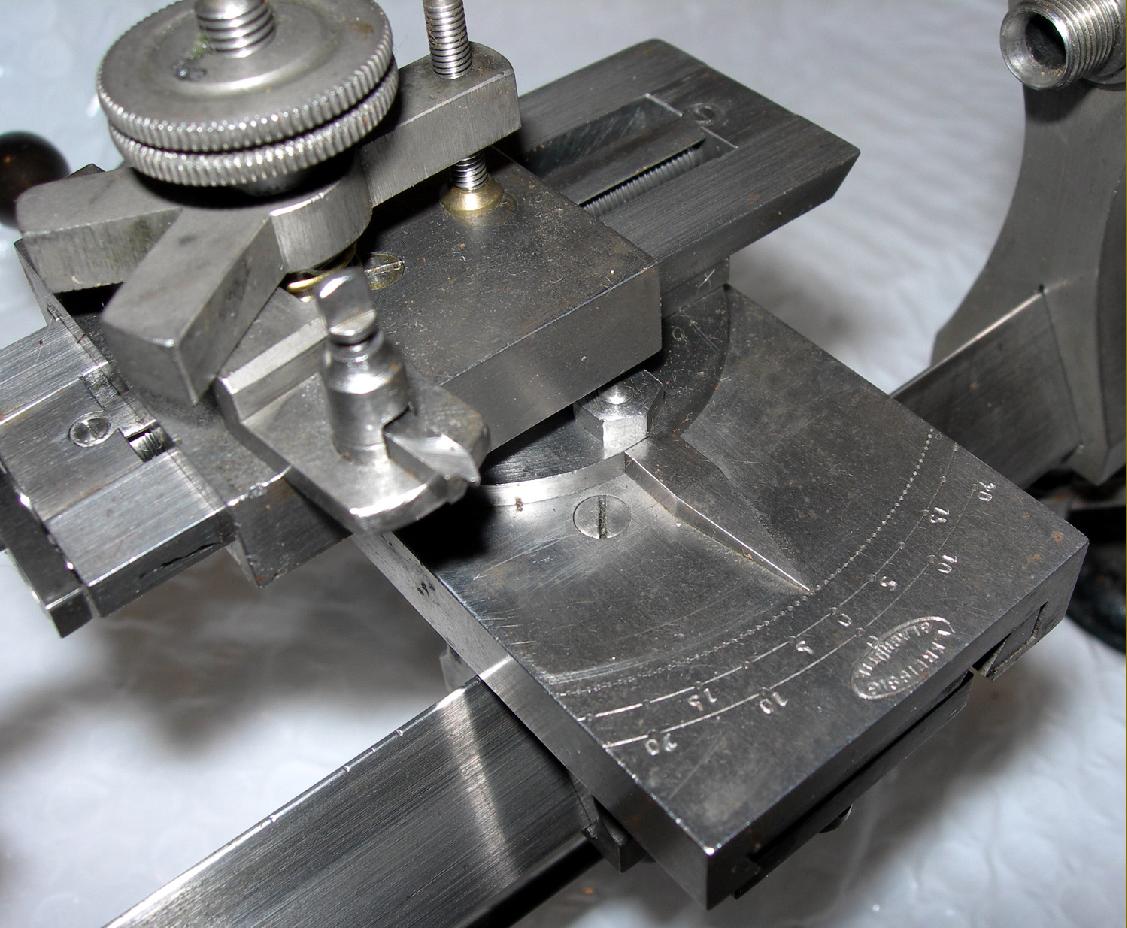 |
|
|
|
|
|
|
The compound slide came with its own miniature toolholder
|
|
|
|
|
|
|
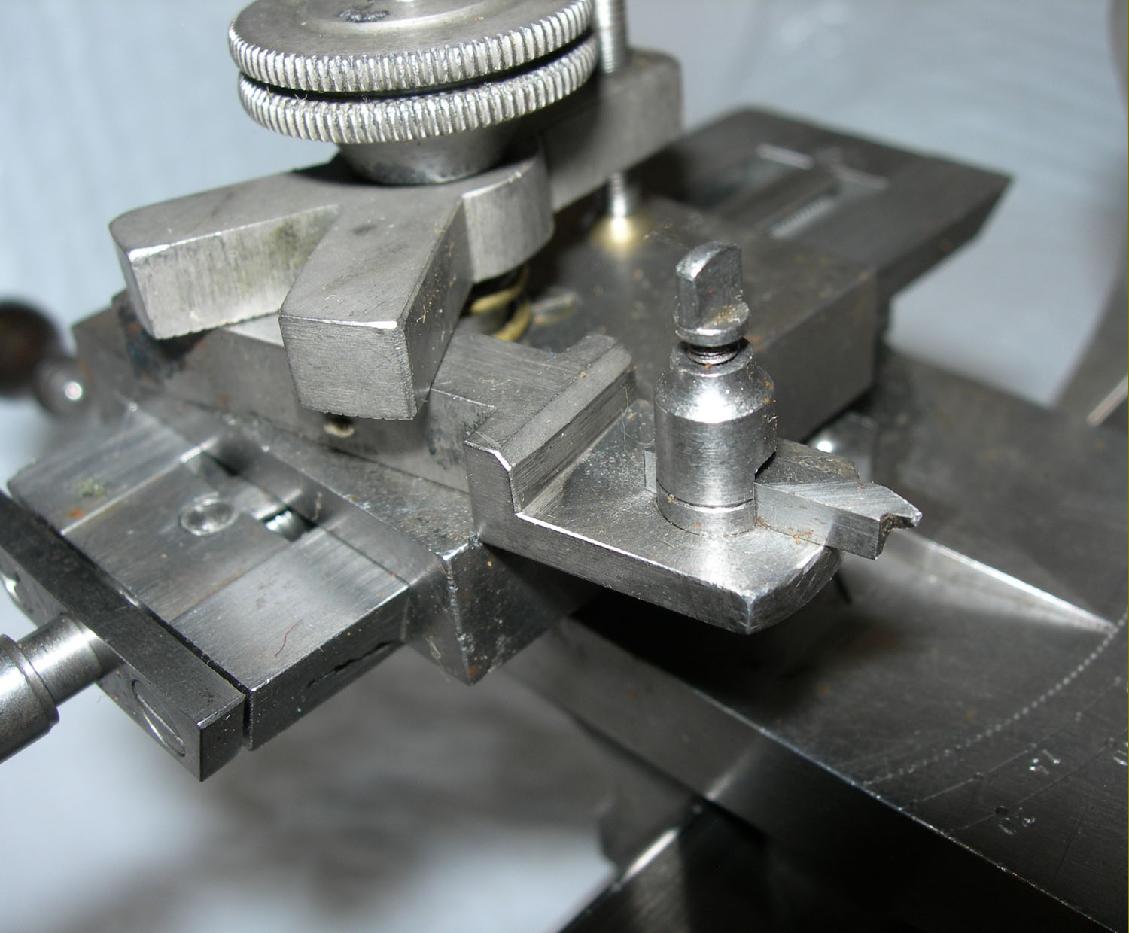 |
|
|
|
|
|
With the light cutting forces involved in watch-making work simple thumb screws on tool clamp and toolholder were sufficient to hold them safely in place
|
|
|
|
|
|
|
|
|
|
|
|
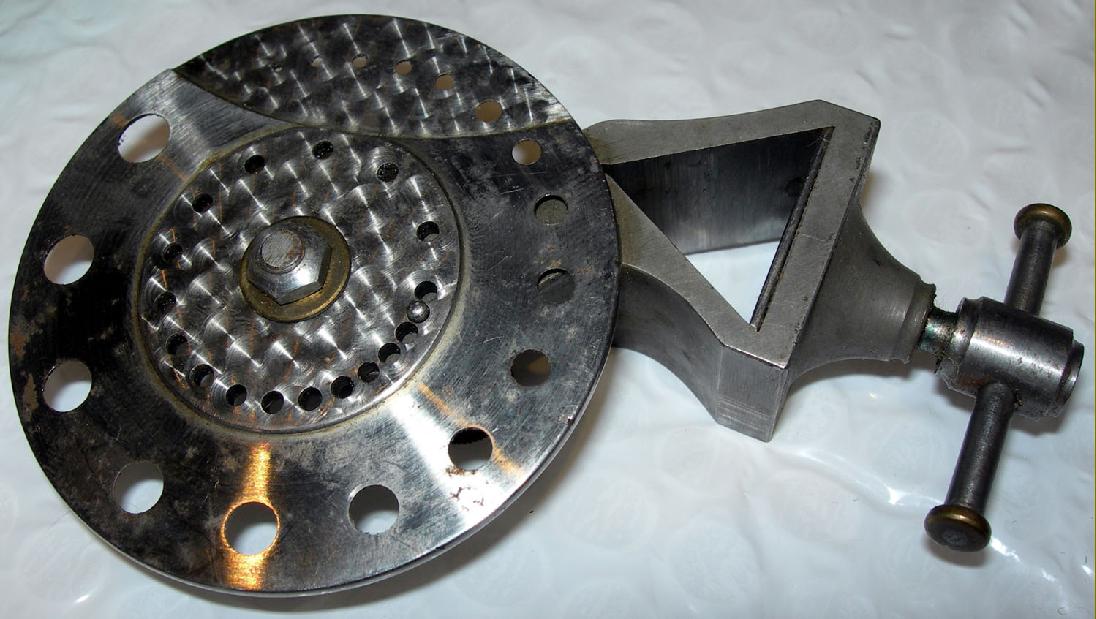 |
|
|
|
|
|
|
The self-centering drilling plate mimicked the design of those used on contemporary larger ornamental-turning lathes with a series of pre-formed bevelled holes around the periphery of a disc that can be rotated into position. Its use was as a steady, when boring into the end of a job, and had to provided set-up by the makers on a new lathe to ensure absolute accuracy of alignment.
|
|
|
|
|
|
|
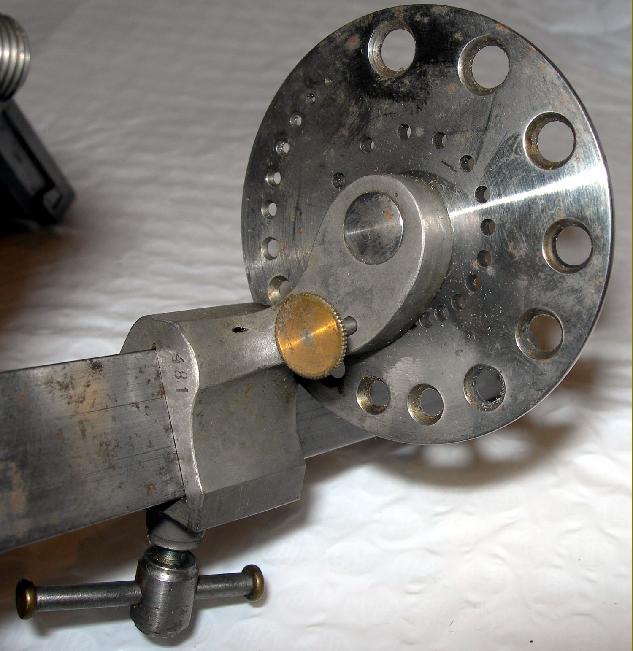 |
|
|
|
|
|
|
The holes were aligned with the spindle axis by a pin
|
|
|
|
|
|
|
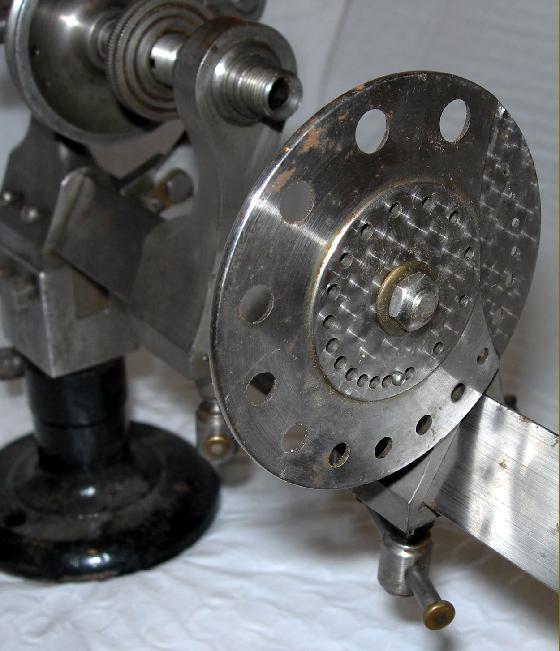 |
|
|
|
|
|
|
The fixed steady/boring collar in place
|
|
|
|
|
|
|
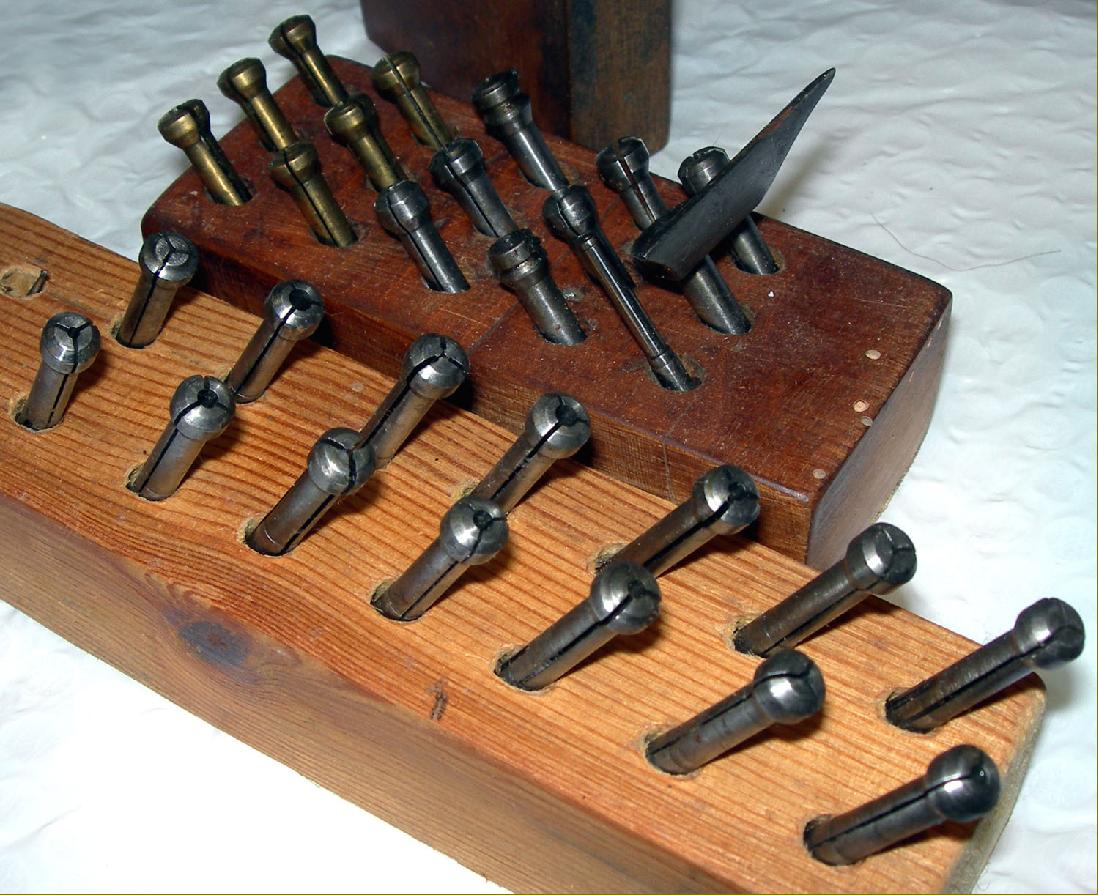 |
|
|
|
|
|
To reach the retaining key the collets had to be unusually long and fitted with a solid shaft to their rear
|
|
|
|
|
|
|
|
|
|
|
|
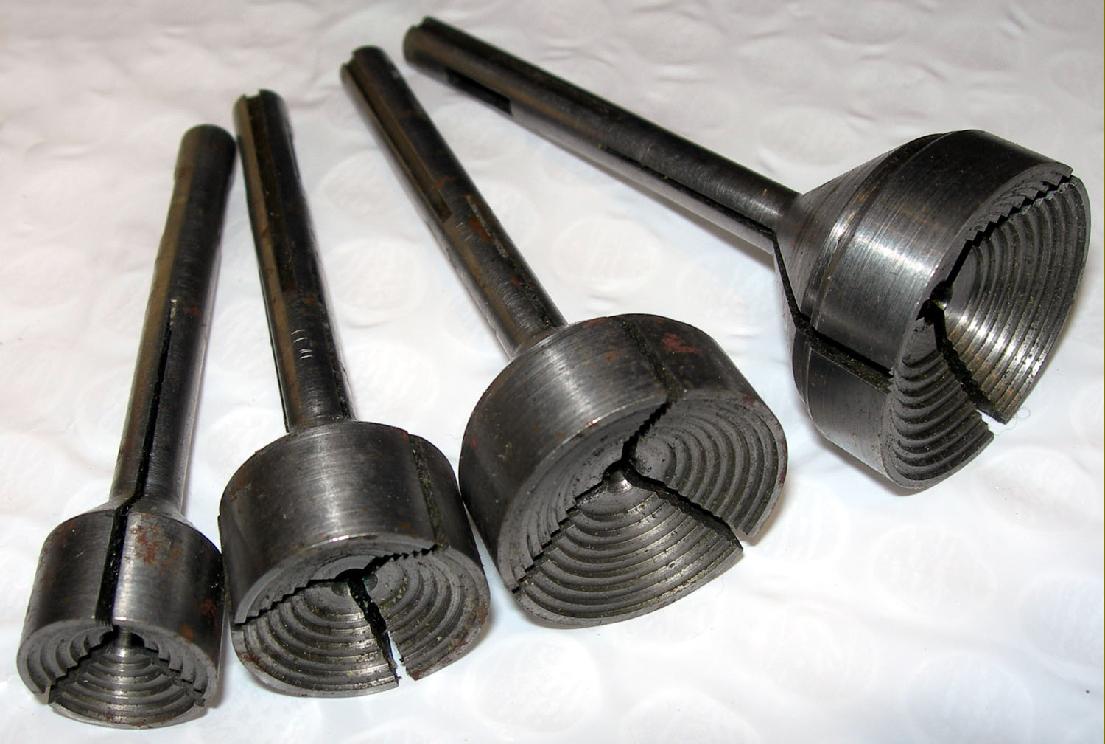 |
|
|
|
|
|
|
|
|
|
Stepped collets - compressed by a ring screwed onto the (left-hand) threaded spindle nose
|
|
|
|
|
|
|
|
|
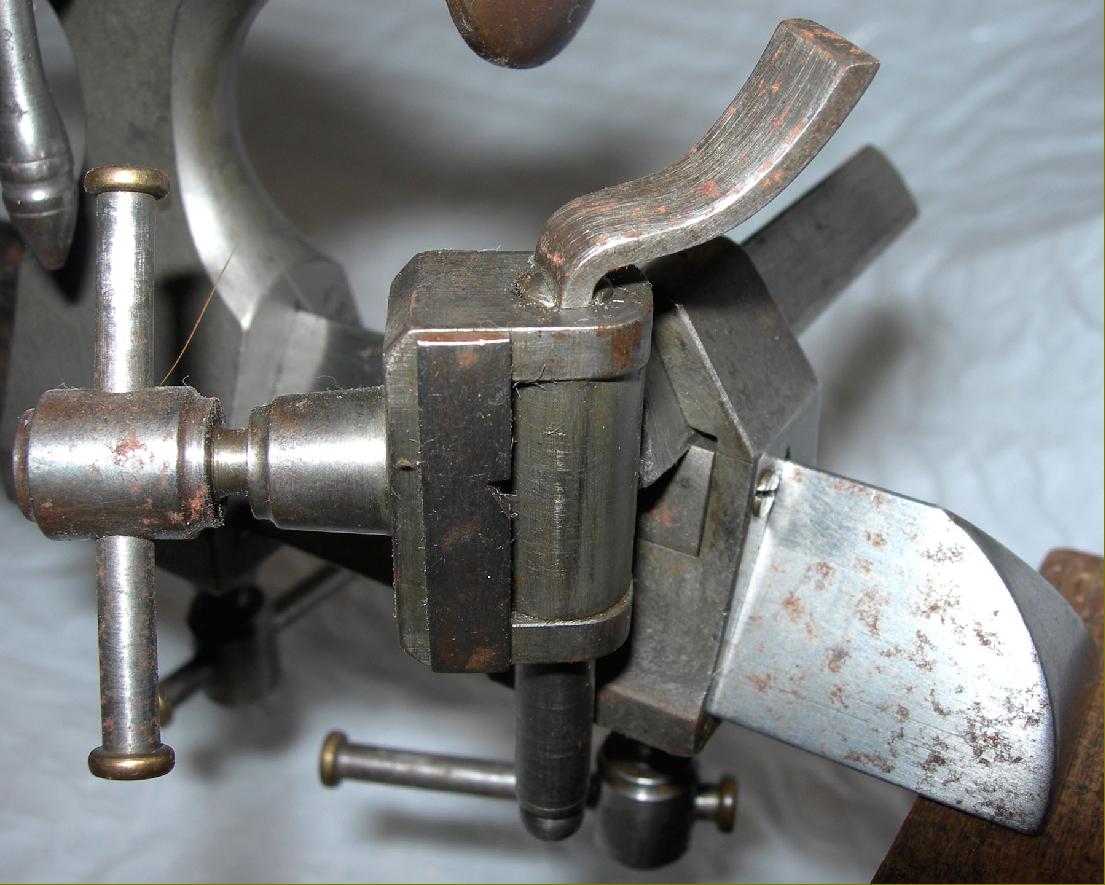 |
|
|
|
|
|
|
Adjustable, pivoting handrest
|
|
|
|
|
|
|
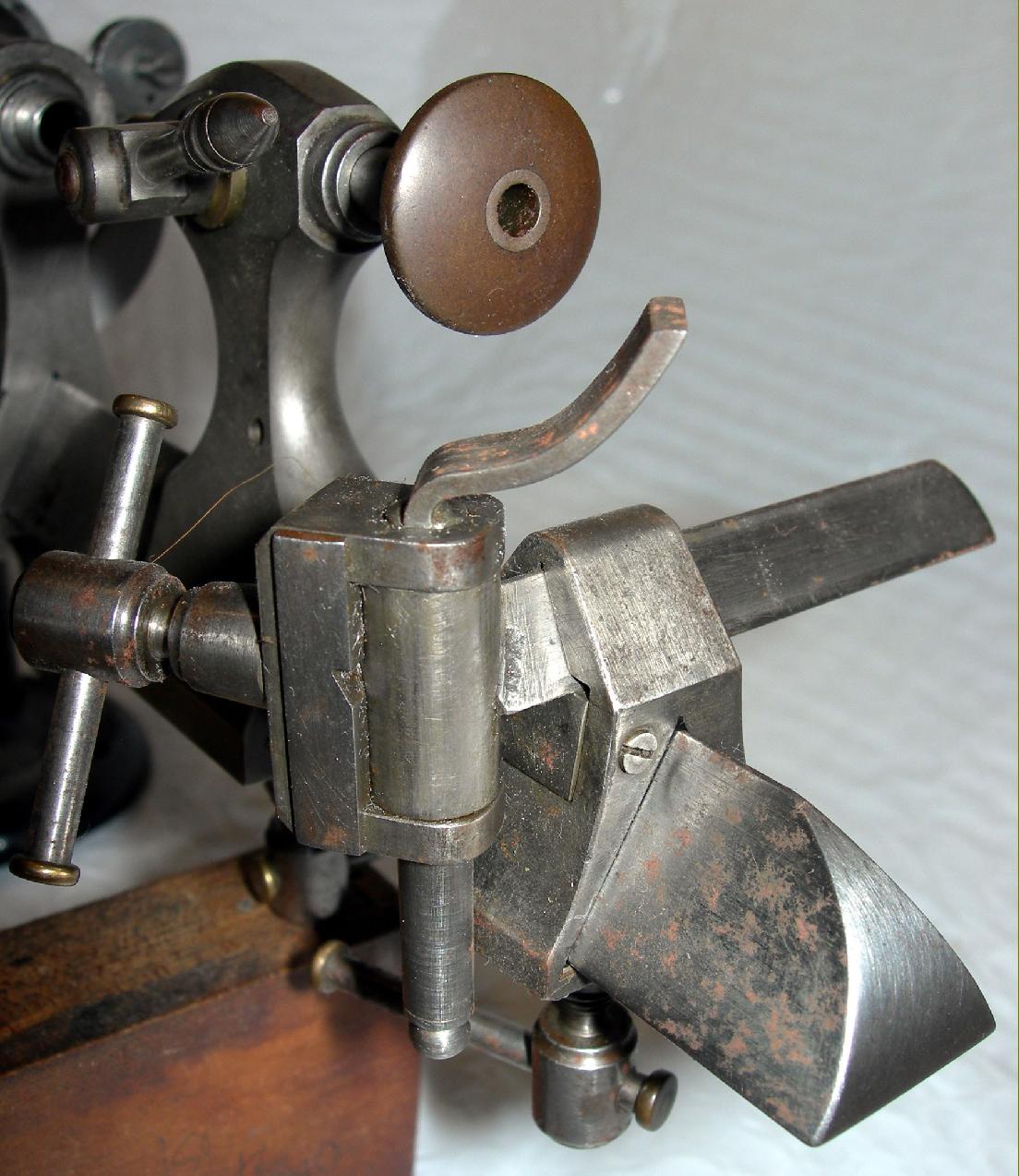 |
|
|
|
|
|
|
|
|
|
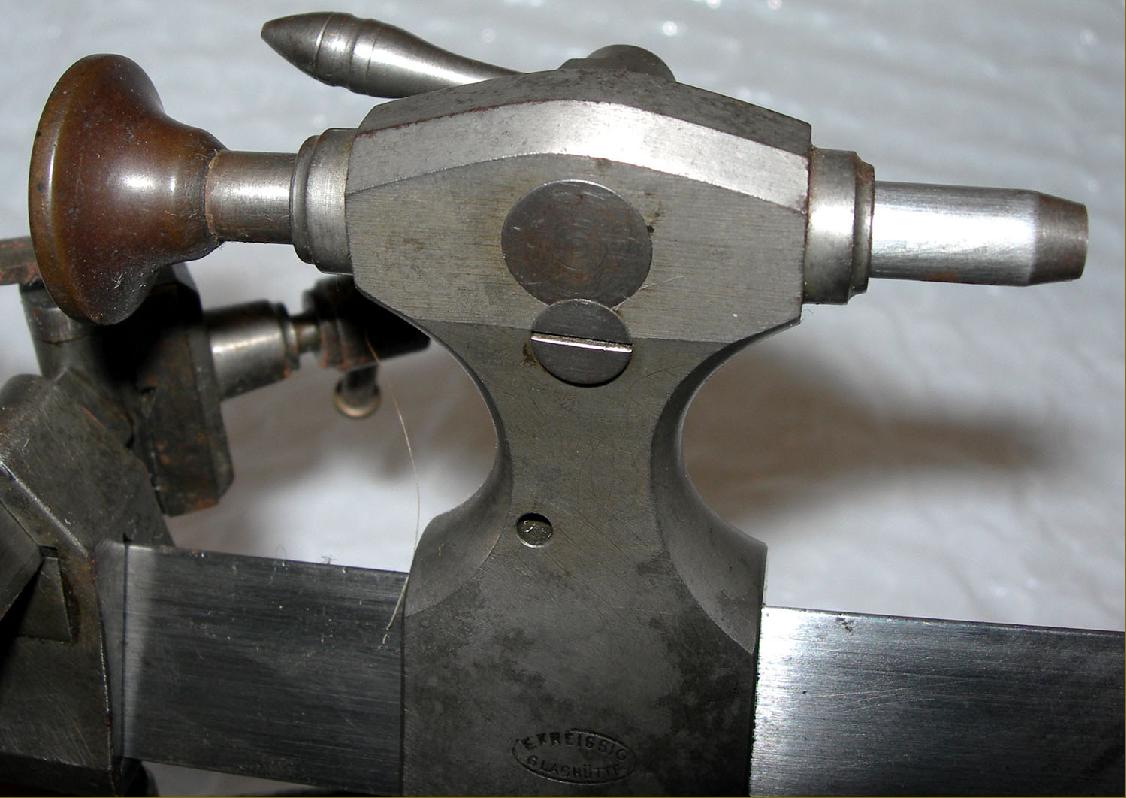 |
|
|
|
|
|
|
Standard "push" spindle tailstock
|
|
|
|
|
|
|
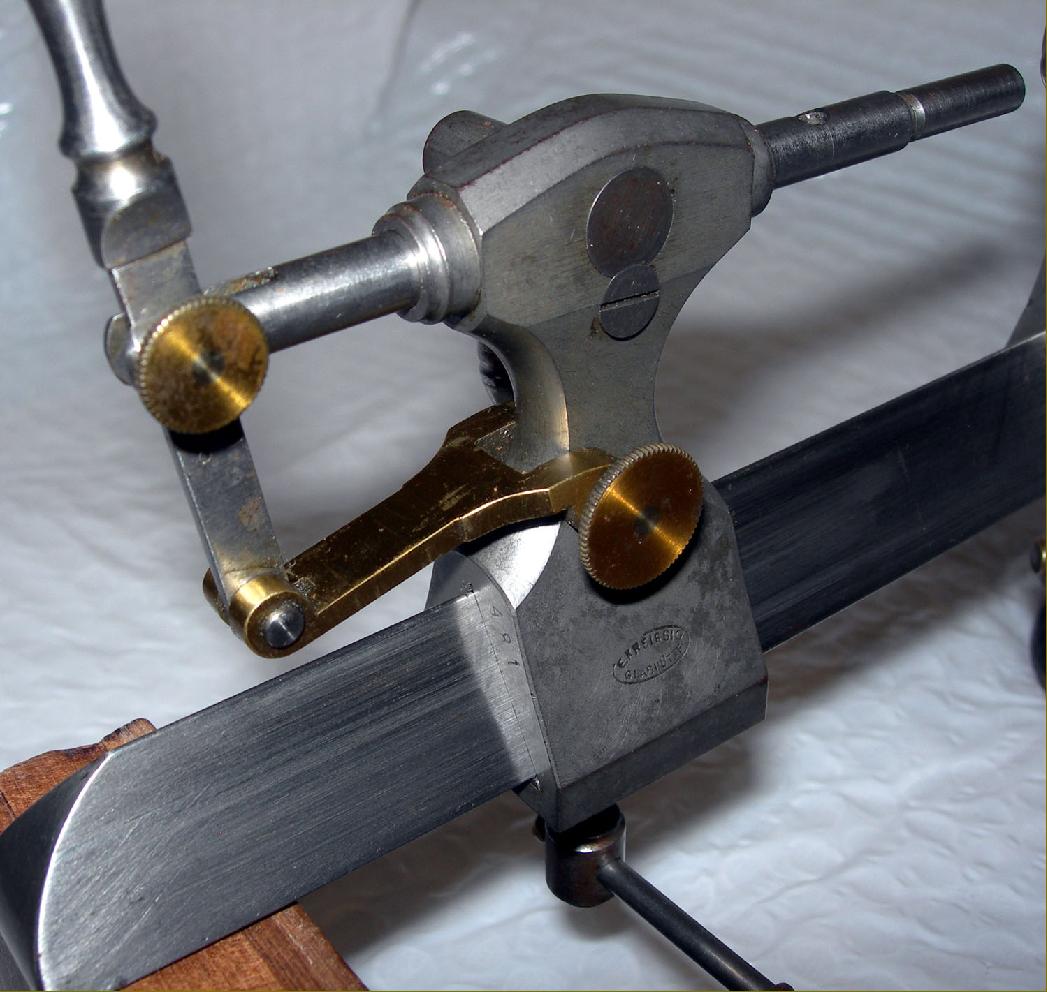 |
|
|
|
|
|
|
A neatly-made lever-action tailstock assembly was also available
|
|
|
|
|
|
|
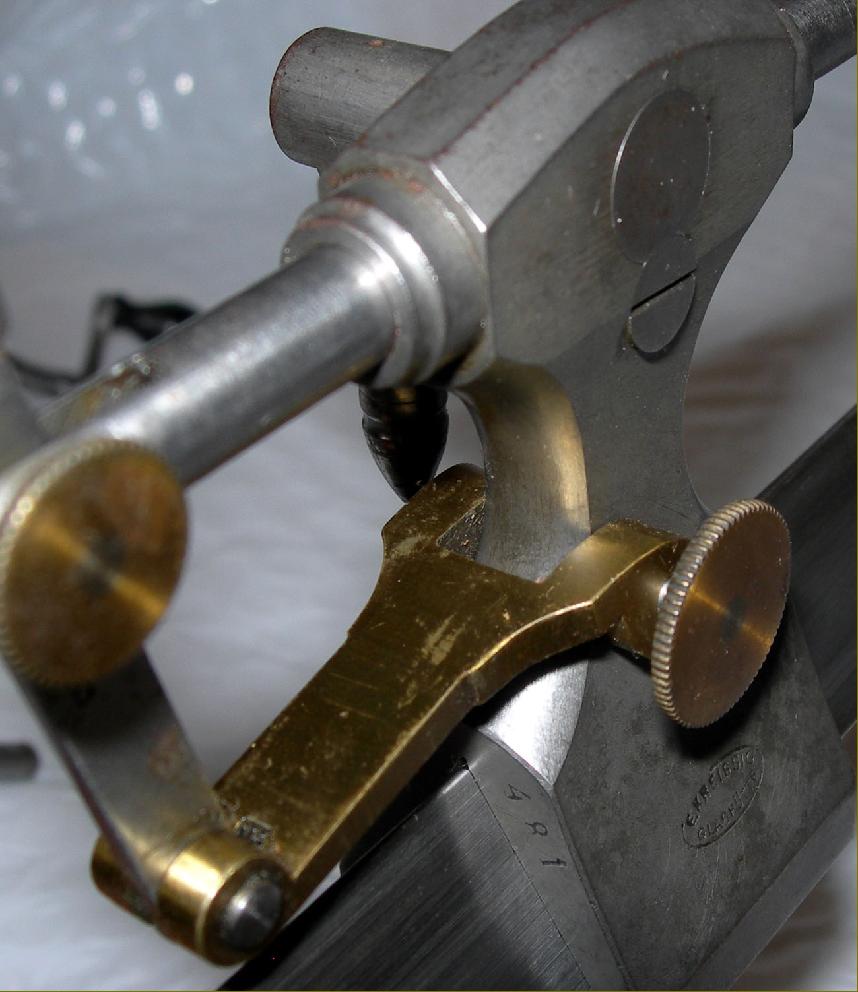 |
|
|
|
|
|
|
high-quality handwork on the lever-action tailstock 's bronze pivot bar
|
|
|
|
|
|
|
|
|
|
|
|
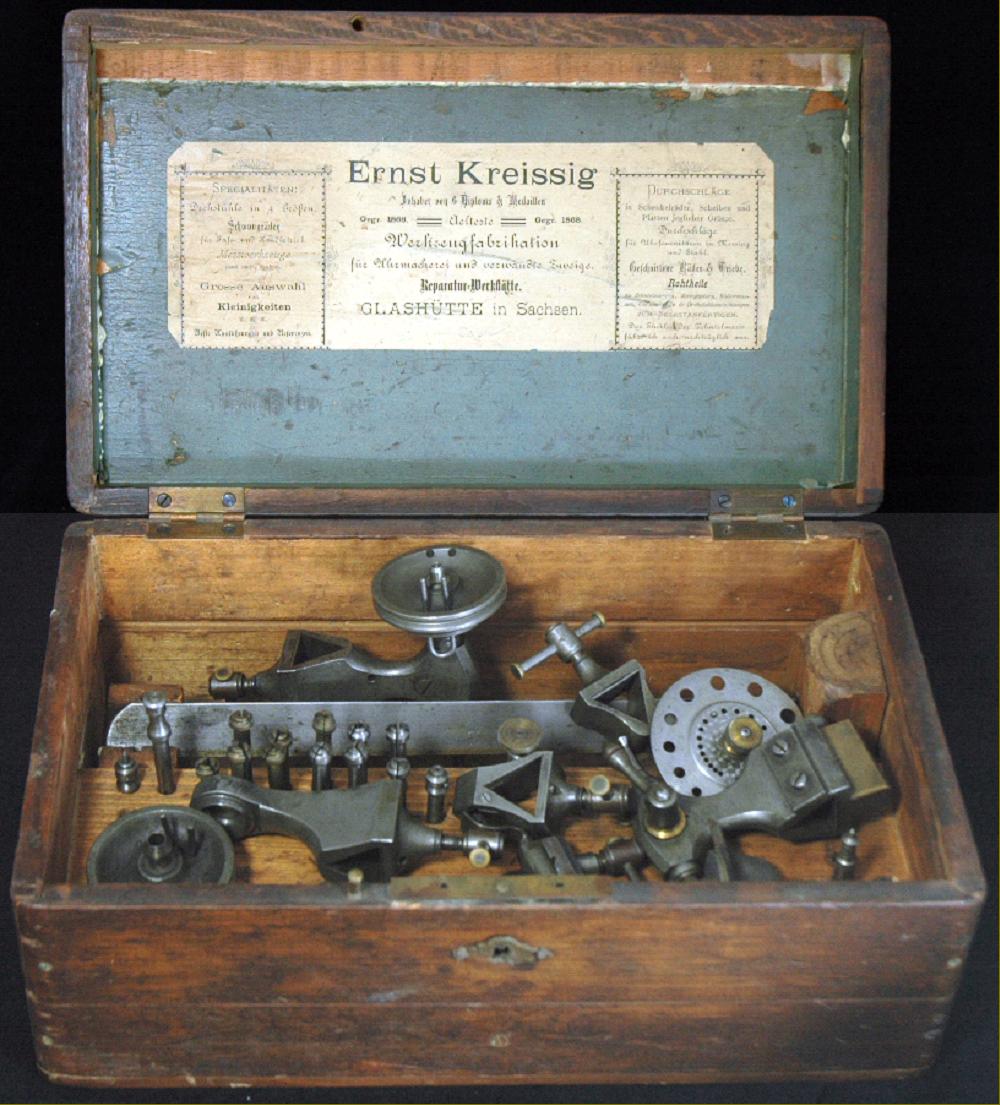 |
|
|
|
|
|
|
Glashutte Serial No. 534 - in its maker's box and resident in the United States
|
|
|
|
|
|
|
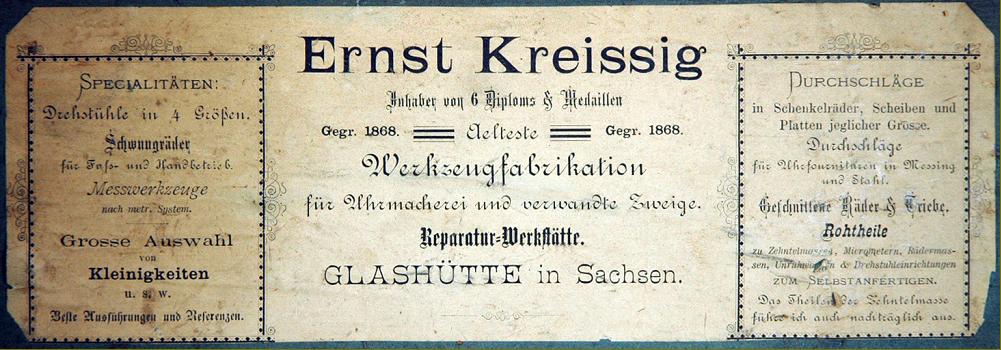 |
|
|
|
|
|
|
|
|
|
|
|
|