 |
 |
 |
 |
 |
 |
 |
 |
 |
 |
 |
 |
 |
 |
 |
 |
 |
 |
 |
 |
 |
 |
 |
 |
 |
 |
 |
 |
 |
 |
 |
 |
 |
 |
 |
 |
 |
|
|
|
|
|
|
|
|
|
|
|
|
|
|
|
|
|
|
|
|
|
|
|
|
|
|
|
|
|
|
|
|
|
|
|
|
|
|
|
|
|
|
|
|
|
|
|
|
|
|
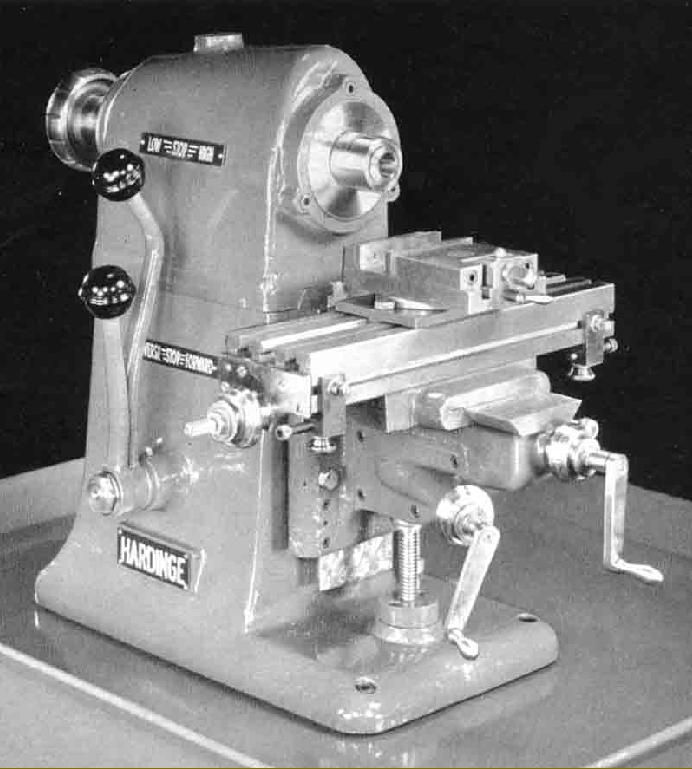 |
|
|
|
|
|
|
Hardinge BB4 Appearing to have been advertised with just the Hardinge, as distinct from the Cataract name, were the small BB4, a developed version of the light-duty horizontal MD4 with a pre-loaded ball-bearing spindle only and taking 4C collets; a quite beautiful high-speed miniature vertical version, the BB2V that used 2VB collets and a tool-room horizontal miller that could be supplied in either "TM" form as an ordinary universal plain (with an optional vertical head) or as the "UM" when fitted with a swivelling table designed to mount a universal spiral-dividing head for cutting spirals. Like all small Hardinge millers the BB4 and BB2V were superbly made from top-quality materials and finished to a high standard. Although a relatively small machine, with a table having a working surface just 12" long by 33/16" wide and the BB4 without an overarm support for its cutters, the hardened and ground pre-loaded ball-bearing 4C collet spindle was driven by 3 V belts - an arrangement that must have provided a more-than-adequate surplus of grip over metal-removing ability. The maximum collet size was 3/4" and the 8 spindle speeds, driven from a 2-speed motor under-slung within the standard sheet-metal cabinet stand, ranged from 180 to 3000 rpm. With hand-scraped ways - and positive locks - the table was almost identical to that fitted to the earlier MD3/MD4 being the same 12 inches long but, at 33/16", just 1/16" narrower. Unfortunately the table travel was slightly reduced on all three axes with a longitudinal movement of 5", traverse of 31/8" and vertical of 5". A generous 24" x 29", the chip tray sat on a stand with a 39" x 38" plan foot - a measurement that included an allowance for the opening of the cabinet's collet and tool-storage doors. In its originally-advertised form the miller was supplied complete with an indexing head that carried a 60-notch index plate (others were available to order), a tailstock and centre to match the dividing head, a draw-in sleeve tube to hold collets, a swivel-base vise and the necessary handles and wrenches. Extras included a swivel base for the indexing unit and, for the table, a rack-and-pinion lever-operated drive and even a power-feed unit - those these are rare and seldom found. As an option, but not illustrated in the company's sales literature, was an overarm support for the spindle, presumably like that used on the later No. 5 machines. However, eventually the Hardinge habit of supplying an indexing dividing head and tailstock with each miller as standard had stopped and these useful items were confined to the expensive Accessory List. Continued below:
|
|
|
|
|
|
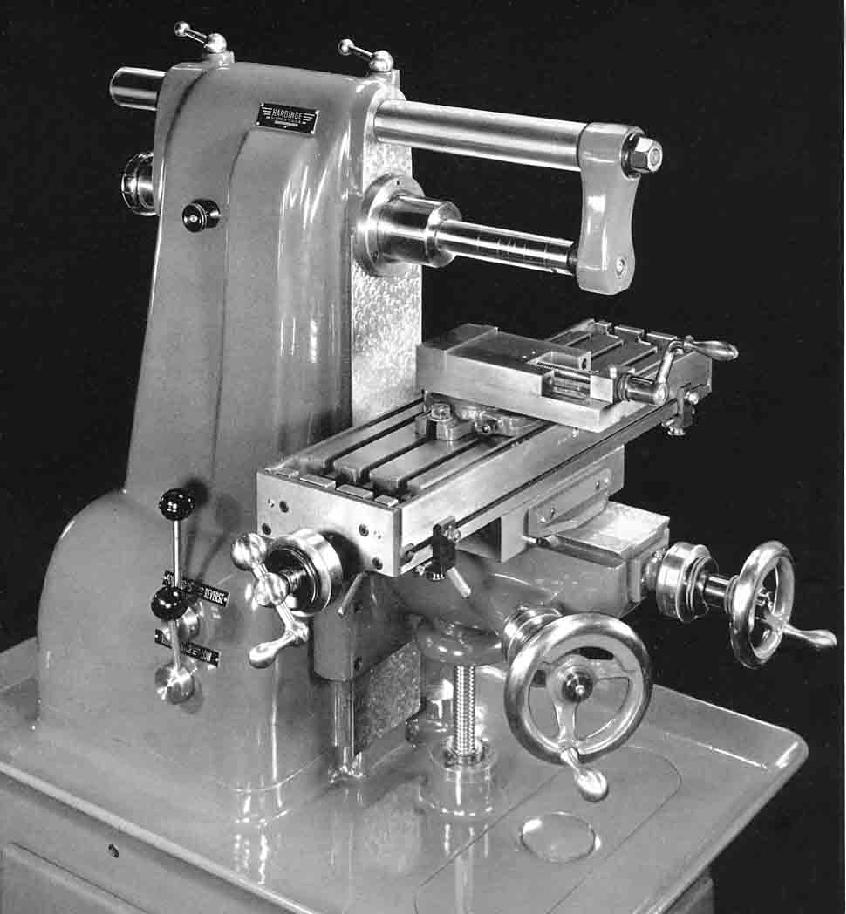 |
|
|
|
|
|
Hardinge TM/UM Miller - and copy by Richard Haighton of Burnley, England Made from the mid 1930s until 1977 (an astoundingly long run) the best known and most common of the Hardinge miller range, the TM/UM, was a carefully-designed, heavily-constructed machine intended to be strong and accurate enough for both production and toolroom work. Interestingly, because nothing similar was being built in the United Kingdom, Richard Haighton Ltd. of Canning Street, Burnley (makers of the Haighton Cadet lathe) produced a short run of close copies, probably in either the late 1950s or early 1960s Branded as the Haighton Major HSU1 it is a very rare machine - and few can survive. Fitted with an ordinary table the TM was the standard machine while the UM, with a swing table, was the "Universal" model. With a working area of 203/4" x 61/2", the table had a longitudinal travel of 14" (11 =1/2" with power feed) a traverse feed of 51/2" and a vertical movement of 131/4". The optional table power-drive attachment gave rates of travel from 1/8" to 13" per minute and was unusual in providing a total of 32 different feeds. All the gibs strips were of the proper tapered type, giving better support and allowing more precise adjustment. A thoughtful touch was the ability to disengage the transverse handwheel engagement; once released, by sliding a collar towards the micrometer dial, the operator could walk around the machine without fear of nudging the handle and upsetting the position of the table. The double nuts for longitudinal and traverse feed screws were adjustable for backlash and the 3"-diameter micrometer dials were larger than other Hardinge millers with, for the first time, parallel engraved surfaces instead of the bevelled ones used previously. Carrying a 5C collet nose - hardened and ground like all those fitted to Hardinge machine tools - the spindle ran in pre-loaded, grease-packed-for life ball bearings and had 8 speeds from 110 to 1850 rpm. The two speed motor was held on a pivoting plate within the sheet metal cabinet stand and used a 4-step V-belt pulley to transmit power to a 2-step V belt countershaft with the drive then taken vertically upwards, via 2 V belts, to the spindle. Motor-speed switching was controlled by the usual Hardinge method of two concentrically mounted levers, one selecting high and low speeds and stop, the other forward and reverse with a second, separate, stop function. Available as a 7/8" or 1" diameter, the cutter arbor was ground on its end in the form of a 5C collet and held into the spindle by a draw bar equipped with a ball-thrust bearing; it was supported by a drop bracket containing a precision ball race while the solid steel 2"-diameter overarm was ground and lapped to be a perfect fit within the main casting. Although not supplied as standard, provision was made to retro-fit a coolant system with all the necessary holes drilled and then sealed with plugs to stop dirt entering. Oil cups were provided to lubricate the longitudinal and traverse feed nuts and the table and carriage slides - in the latter case lines scribed on the table and carriage had to be lined up before oiling to allow the lubricant to reach its correct destination..
|
|
|
|
|
|
|
|
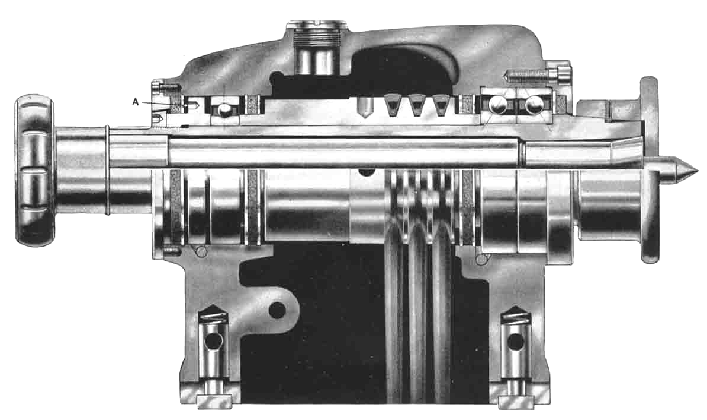 |
|
|
|
|
|
|
Headstock from the BB4 vertical miller with grease-packed, pre-loaded precision ball bearings and 3 V-belt drive
|
|
|
|
|
|
|
|
|
|
|
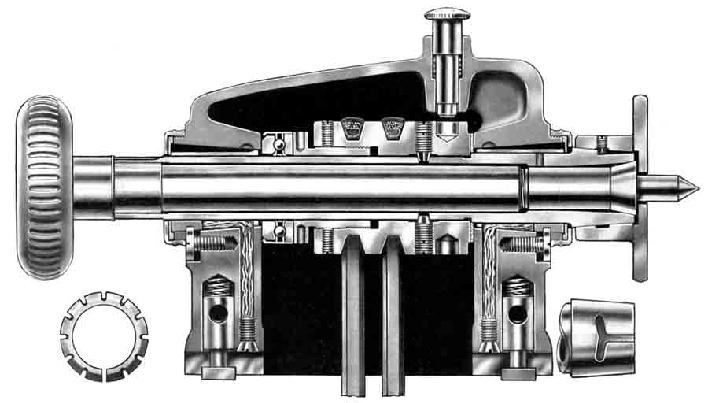 |
|
|
|
|
|
|
Headstock as used on the plain bearing millers with 2 V-belt drive and wick-supplied lubrication
|
|
|
|
|
|
|
|
|
|
|
|
|
|
|
|
|
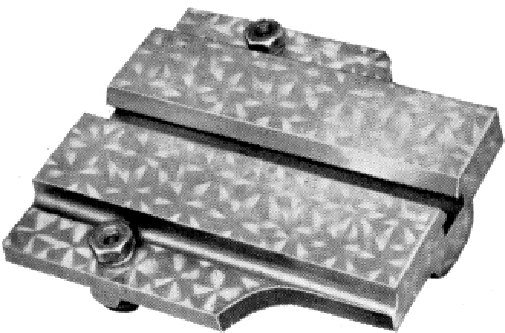 |
|
|
|
|
|
|
Right-angle accessory base
|
|
|
|
|
|
|
|
|
|
|
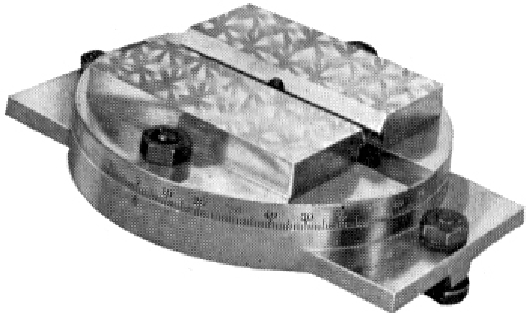 |
|
|
|
|
|
|
Swivel Base. Designed to allow the indexing head or "Universal Adaptor" (below) to be mounted at an angle on the table and work machined at an angle or taper.
|
|
|
|
|
|
|
|
|
|
|
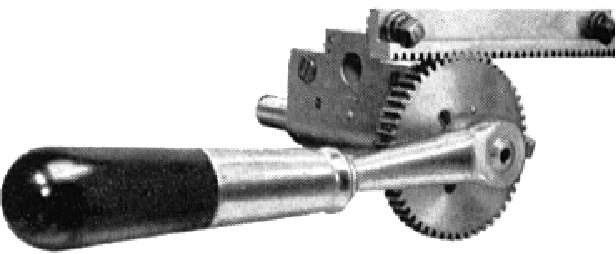 |
|
|
|
|
|
|
Rack-operated table lever feed
|
|
|
|
|
|
|
|
|
|
|
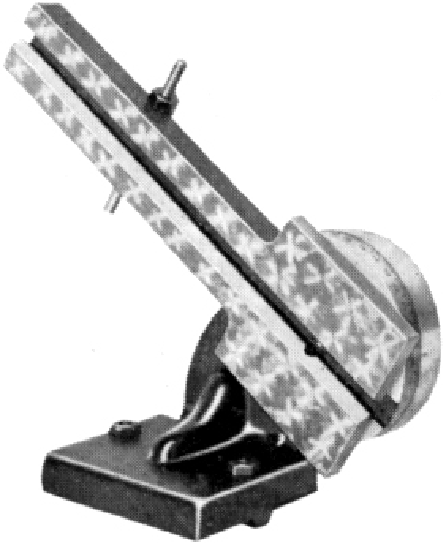 |
|
|
|
|
|
|
Universal Adaptor. This device could be fitted either directly to the milling machine table (so that the swivel table was aligned at 90° to the headstock) or mounted on the swivelling base above - so allowing work to be machined at any angle. The 10-inch long T-slotted table could accept any of the usual table-mount accessories including indexing heads and tailstocks.
|
|
|
|
|
|
|
|
|
|
|
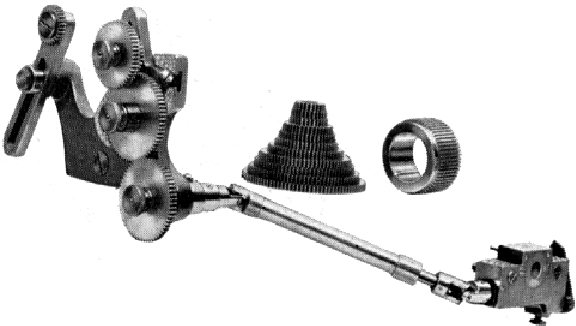 |
|
|
|
|
|
|
A range of table power feeds, with adjustable automatic knock off and incorporating a right-angle worm-and-wheel gearbox, was provided by the drive normally used as a lathe screwcutting attachment. Later power-feed units were altered and designed specifically for the miller. Another power feed attachment has also been located (so rare that it never made the known catalogues) that used a stepped pulley from the No. 3 headstock, a round leather belt and a second stepped pulley on a bracket off the mill base to drive the usual right angle drive gear box and universal drive shaft.
|
|
|
|
|
|
|
|
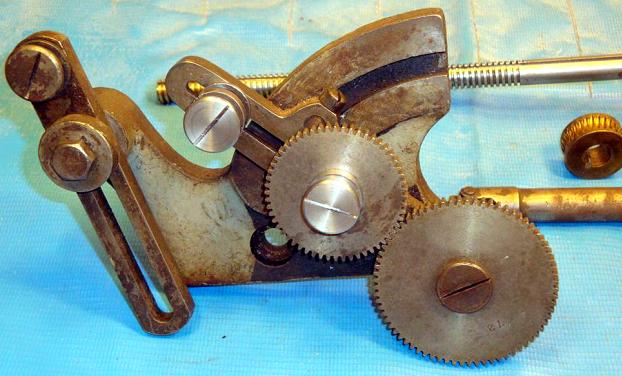 |
|
|
|
|
|
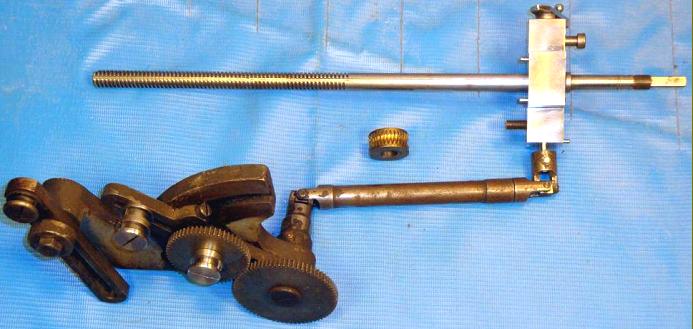 |
|
|
|
|
|
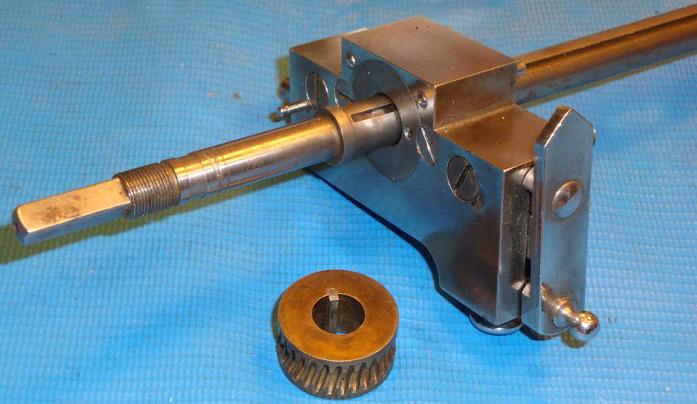 |
|
|
|
|
|
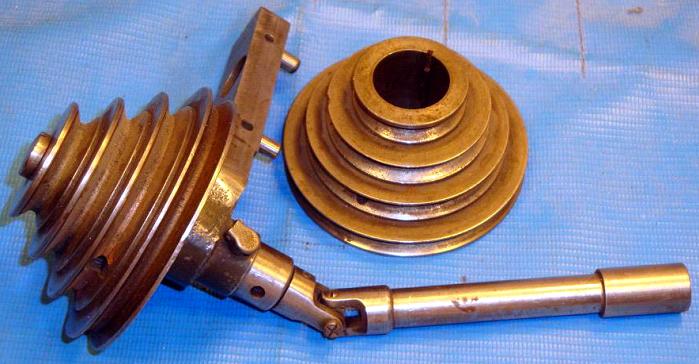 |
|
|
|
|
|
|
|
|
|
|
|
|
|