 |
 |
 |
 |
 |
 |
 |
 |
 |
 |
 |
 |
 |
 |
 |
 |
 |
 |
 |
 |
 |
 |
 |
 |
 |
 |
 |
 |
 |
 |
 |
 |
 |
|
|
|
|
|
|
|
|
|
|
|
|
|
|
|
|
|
|
|
|
|
|
|
|
|
|
|
|
|
|
|
|
|
|
|
|
|
|
|
|
|
|
|
|
|
|
|
|
7-inch Woodhouse & Mitchell "Junior" Lathe Formed in 1881 from Wood, Baldwin, Mitchell & Woodhouse Ltd, and originally makers of stationary steam engines, Woodhouse and Mitchell were to become better known for their range of heavy industrial lathes. Of their smaller machines the most popular in post-WW2 years (and sold with both Woodhouse & Mitchell and Town Woodhouse badges), was the 7-inch Junior - very much the baby of the Company's traditional range with the sales literature for the model adopting a rather patronising tone - as though such a small machine was really rather beneath them. However, an even smaller, plain-turning precision model has recently (2012) come to light with around a 3" centre height and about 10 inches between centres - it is shown towards the bottom of the page). While Woodhouse and Mitchell were indeed better known for their much larger lathes (and Town Woodhouse for their radial-arm drills), the junior was exceptionally well specified and built to a very high standard using top-quality. The bed, massively strong and diagonally braced between the walls for added strength used a combination of flat and V-ways with the saddle guided on a large V at the front and a flat at the rear. Separate rear V and front flat guides were provided for the tailstock. As standard the bed was provided with a detachable gap piece but, even without removing it, work up to 1" thick could be to be machined on the full diameter of the faceplate; with the gap piece out the thickness of work on the faceplate could be increased to 8 inches. The majority of lathes were supplied with a 36" capacity between centres, but longer beds giving 45", 54" and 72" between centres were also available, though the 72" version is very rare. 8 spindle speeds were provided, in geometric progression, and the customer could choose from five ranges, though others, unadvertised, may have been available. All were rather slow by today's standards but perfectly suitable for the standard cutting tools in use at the time and ideal for amateur or general repair-workshop use today: 30 - 437 r.p.m.; 30 -900 r.p.m.; 44 - 640 rpm; 50 - 750 r.p.m. and 60 - 874 rpm. The main spindle was made from a heat-treated, high-carbon steel-tubular forging machined and ground-finished. It was bored through to clear 1-inch, threaded 2.5" x 4 t.p.i (and tapered inside 1 in 12 to hold an adaptor with a No. 3 Morse taper) and ran on "selected" high-accuracy taper-roller bearings. Later versions of the Junior were built with an LO size American long-nose headstock spindle taper and bored through to clear approximately 1.6"/40 mm. They were also available with the option of a 2-speed motor that gave a total of sixteen 16 forward speeds from around 44 to 1280 rpm. These lathes can be recognised by their electrical switches mounted on the front face of the stand on the electrical cabinet door. All the sliding change gears within the headstock were made of heat-treated nickel steel with the spindle gears and clutch in high-tensile cast iron with the shafts of high-carbon steel. The feed-reversing mechanism to the feeds and screwcutting gearbox was carried within the headstock (where it benefited from a constant supply of oil) and incorporated a "one tooth" clutch so that the reversal of feed during screwing maintained screwcutting pitch relationships. Drive to the headstock was by either a single or double V-pulley from a foot-mounted motor fastened to the back of the headstock foot - the double pulley being a late replacement and obviously intended to give some reserve of capacity when the machine was being used hard. An oil-immersed, multi-plate clutch was fitted inside the headstock and controlled by a conveniently placed lever just below and to the left of the gap in the bed. Continued below:
|
|
|
|
|
|
|
|
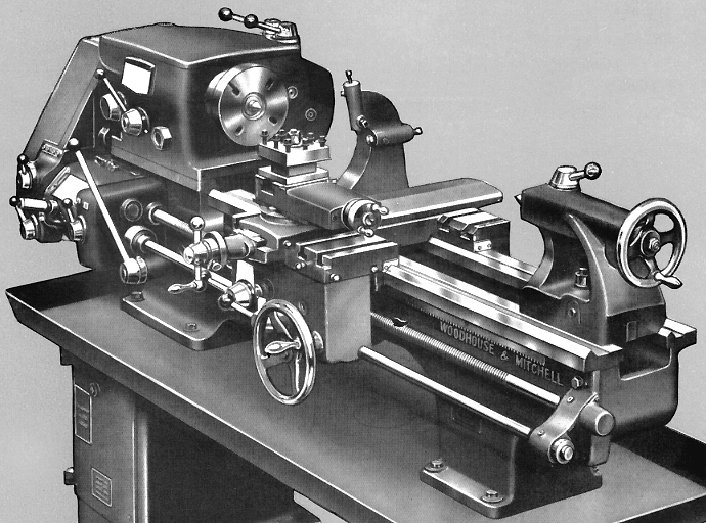 |
|
|
|
|
|
|
Woodhouse & Mitchell/Town Woodhouse "70 Junior" circa 1955. Later versions had the option of a full cabinet stand that has been found constructed in both heavy steel plate and cast-iron
|
|
|
|
|
|
|
|
|
Continued: Provided with two T-slotted wings towards its tailstock end and a single towards the clutch, the saddle was guided on a front Vee and a rear flat. Of double-wall design, the apron contained gears of heat-treated nickel-steel with high-carbon steel shafts and a phosphor-bronze worm wheel to pick up the drive from the separate power shaft. Both the sliding and surfacing feeds were controlled by single-lever operated tumbler arrangement with a cam-locking action - interlocked, of course, with the clasp-nut engagement handle to prevent inadvertent simultaneous engagement and the resulting mechanical marmalade. The rack was of high-carbon steel, and the pinion which engaged it of heat-treated, nickel chrome-molybdenum steel. The basic machine was fitted with a simple 3-speed gearbox on the end of the leadscrew giving a choice of three sliding and surfacing feeds for each setting of the changewheels (with feed rates of: 0.030", 0.015" and 0.007" inches per revolution). To guard against over-enthusiastic use by inexperienced apprentices (or impatient piece-work operators) a pre-loaded slipping clutch was fitted to the feed shaft. The set of changewheels provided for cutting all standard English threads together with a 127T metric translation wheel A Norton-type, quick-change, screwcutting gearbox was available at extra cost and this gave 32 feeds and pitches (though late models had an improved specification with 72 feeds and pitches) - and was supplied complete with additional changewheels for generating metric pitches. available The leadscrew was properly mounted in tension with ball thrusts at each end and cut to give a pitch error which did not exceed 0.002" in any 12 inches. A rather fine touch - and very unusual - was the provision of an additional support guide for the leadscrew immediately before it passed thorough the clasp nuts, a fitting designed to reduce both bending stress and wear A thread-dial indicator was part of the standard specification. With a 3-Morse taper spindle, the tailstock was the only part of the lathe to show any evidence at all of cost-cutting, being provided with loose (self-hiding) spanner to lock it to the bed. A built-in, lever-operated cam-action cross-shaft would have been much preferable and could be provided - but at extra cost. One interesting point about the design of the Junior was the arrangement of the taper-turning attachment - this being very fast and simple to engage with just a clamp tightened to the rear of the machine - no more than a minute's work being required to bring it into action. In addition the unit allowed use of the cross slide's full travel range. Equipment provided with a lathe when new was basic: stand with suds tray, a 4-way toolpost, a small faceplate, drive plate, travelling steady, a set of spanners and changewheels. Additional accessories such as chucks, a fixed steady, larger faceplate, taper turning attachment and electric coolant pump and suds tank could be supplied at extra cost. Following the example set by the Company's larger lathes, the "Junior" was made entirely of controlled-quality materials and constructed to Schlesinger limits of accuracy. All levers and handwheels were chromium plated and, to complete a sound, English-built job, the lubrication points were fitted with dirt-excluding nipples. Many years ago a friend of the writer found a "Junior" tipped upside down in a scrapyard. Although rusty and looking thoroughly dishevelled, the quality of construction was such that only a careful clean, adjustment of clearances, replacement of the odd broken handle and replenishment of oils was needed to put it back into daily, productive use..
|
|
|
|
|
|
|
|
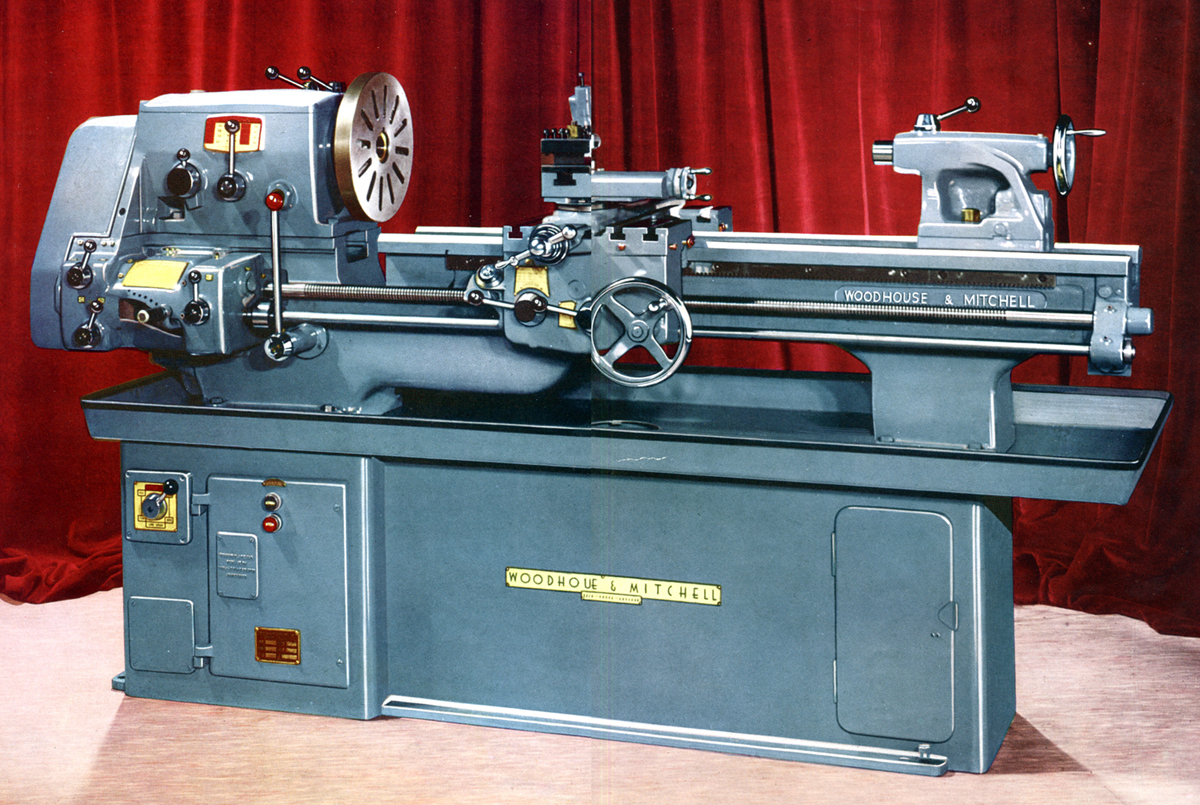 |
|
|
|
|
|
|
Woodhouse & Mitchell/Town Woodhouse "70 Junior" circa 1957. This is a late version with an L0 spindle nose and increased bore
|
|
|
|
|
|
|
|
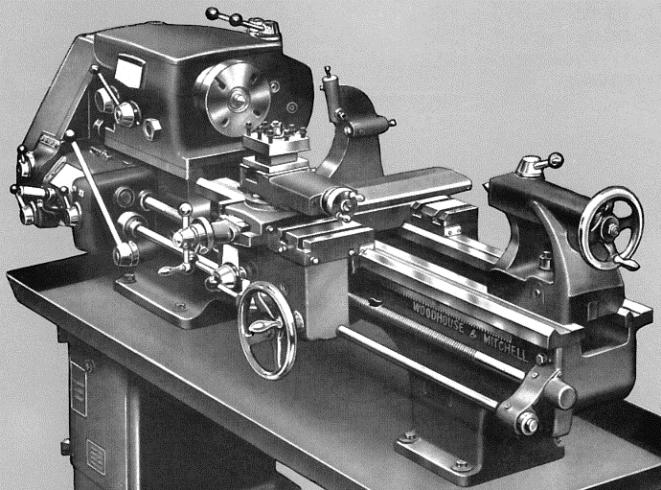 |
|
|
|
|
|
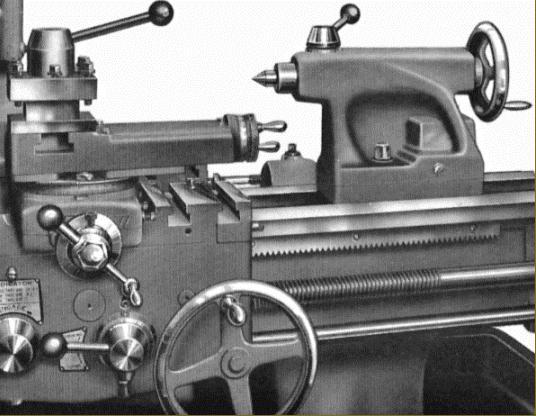 |
|
|
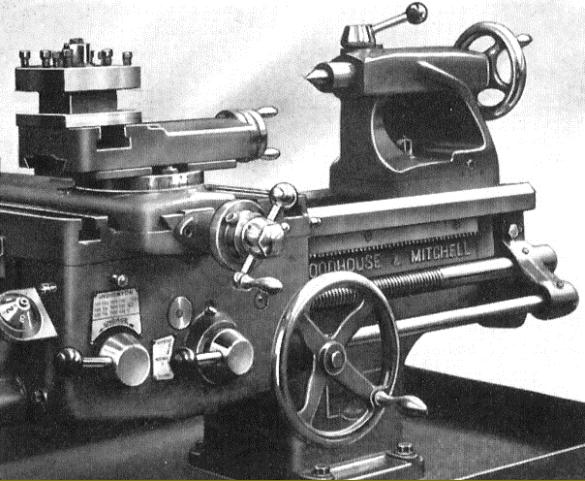 |
|
|
|
|
|
|
|
|
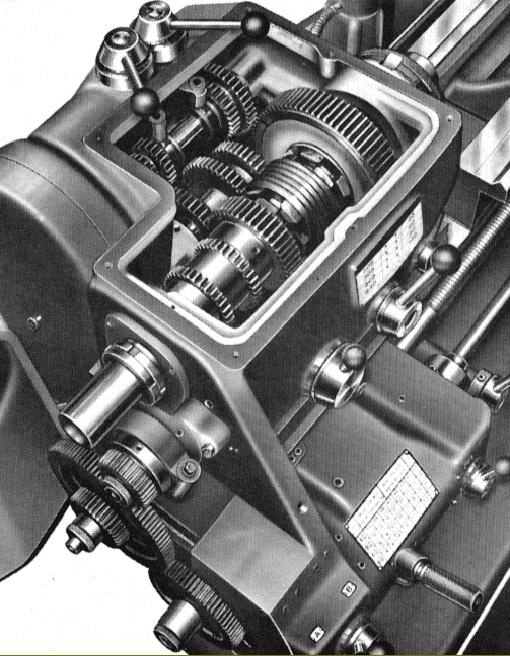 |
|
|
|
|
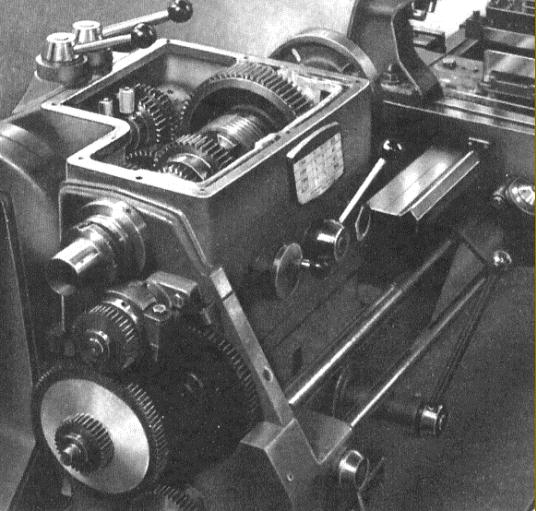 |
|
|
|
|
|
|
|
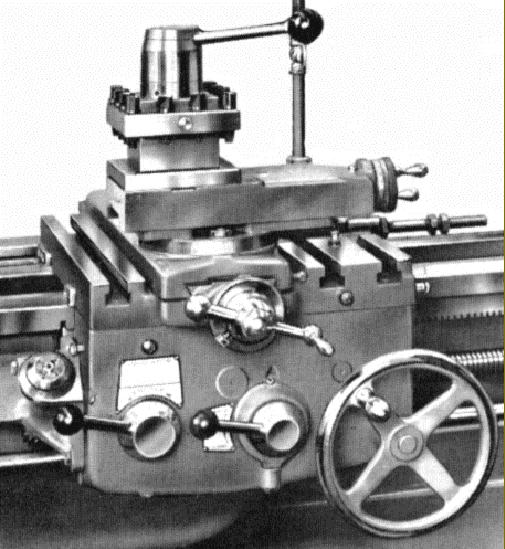 |
|
|
|
|
|
|
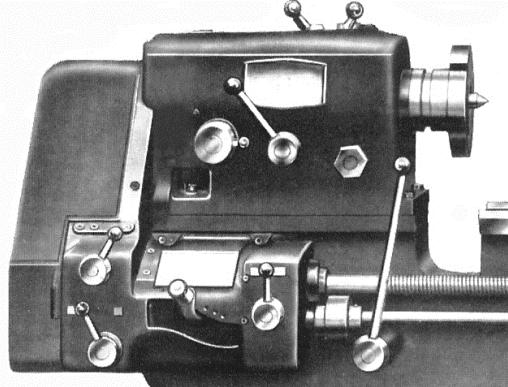 |
|
|
|
|
|
|
|
|
|
|
|
|
|
|
|
|
|
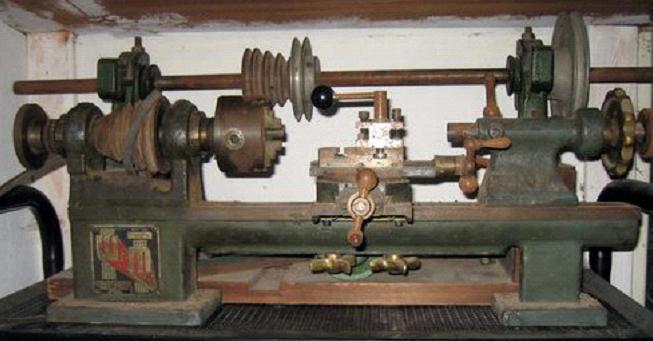 |
|
|
|
|
|
|
Around 3" x 10" the history behind this little Woodhouse & Mitchell plain-turning precision bench lathe is unknown - though an identical version was sold with the letters B.W.C. cast into the bed. Lathes of this type began with the American Stark, in 1862, and continued in much the sale form until somewhat modernised in the 1940s - hence dating them can be difficult, if not impossible. For example, the headstock of the B.W.C. carried a 4-step V-pulley that might have been intended use with either a heavy round leather belt or an ordinary V-type; if the former was the case then the lathe would have been from the period 1900 to 1930 and if the latter, from the 1930s or 1940s. However, the tiny micrometer dials on later models do suggest a pre-1930 date. Most lathes of this type, being for use by toolmakers, had an exemplary finish (even to beds being form-milled and then hand scraped) but in this respect the Woodhouse & Mitchell fell short, with the main castings being left in a comparatively rough state. However, despite this cosmetic failing (possibly as a consequence of manufacture during the 1914-18 war) the lathe was well made with the headstock spindle running in parallel-bore, conical outside bearings whose clearances were finely adjustable by pairs of opposed castellated rings that drew them into tapered seats. The headstock spindle carried a 4-step cast-iron pulley - with a very distinctive cone angle at its left left-hand end - and with the outer flange carrying a ring of indexing holes located by a good-sized pin that passed through the face of the headstock casting. The pulley was not intended to accept a V-belt - the use of those on small lathes began in the early 1930s with their adoption by Atlas in the USA - but a round leather belt, sometimes known as a "gut" drive. Although some precision bench lathes like the American Waltham relied upon a vertical surface to locate the compound slide assembly conventional wisdom dictated that such a lathe required a bed with a narrow, flat top and bevelled sides to ensure that the headstock, carriage and tailstock were all clamped across its full width and maintained in perfect alignment The Woodhouse & Mitchell departed from this orthodoxy and employed a conventional, flat-topped design with 90-degree sides. The carriage was clamped by two studs with its sliding fit - against the two front inner vertical surfaces only - adjusted by two gib screws that bore against a bronze gib block. The simple, lever-action tailstock and the headstock were both aligned by a tennon that fitted into a narrow slot that ran down the bed's centre line, with the headstock retained by two through bolts and the tailstock by an angled block that was drawn against the inside of the bed slot by a bolt. With two T-slots, the top slide sat on a crudely calibrated swivelling base (the engraved marks in the example shown may not be original) with the mounting in the form of a circular T-slot cut into the cross slide. The latter casting was very short - leaving (like the top slide) the Whitworth-form feed screw exposed at both front and back - and also rounded off on its corners so (unnecessarily) reducing its contact area with the base. In common with many contemporary lathes of the late 19th and early 20th centuries, on early versions of the B.C.W. no micrometer collars were fitted to either feed screw. However, what must be later machines did have them fitted, although there is, of course, the possibility that they were an optional extra. If any reader has a Woodhouse and Mitchell precision lathe, or a B.W.C., or literature concerning them, the writer would be very interested to hear from you..
|
|
|
|
|
|
|
|
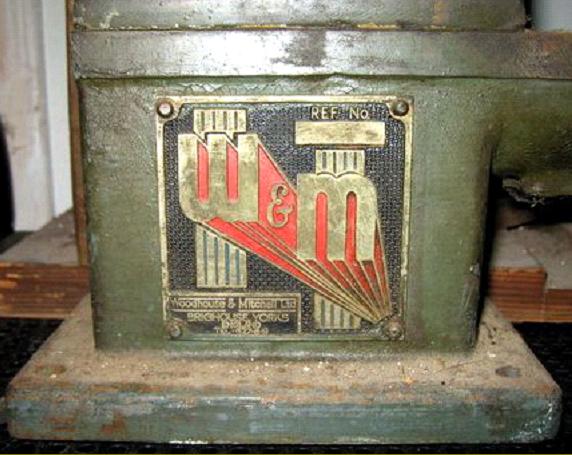 |
|
|
|
|
|
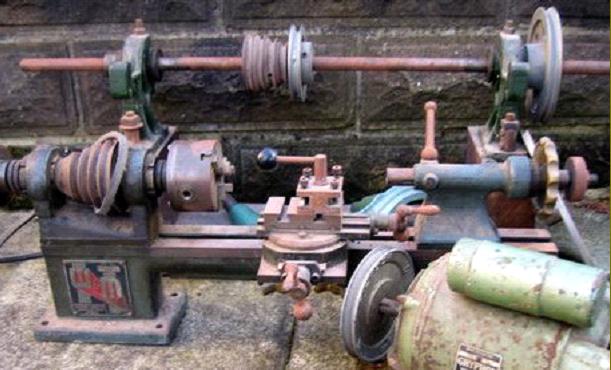 |
|
|
|
|
|
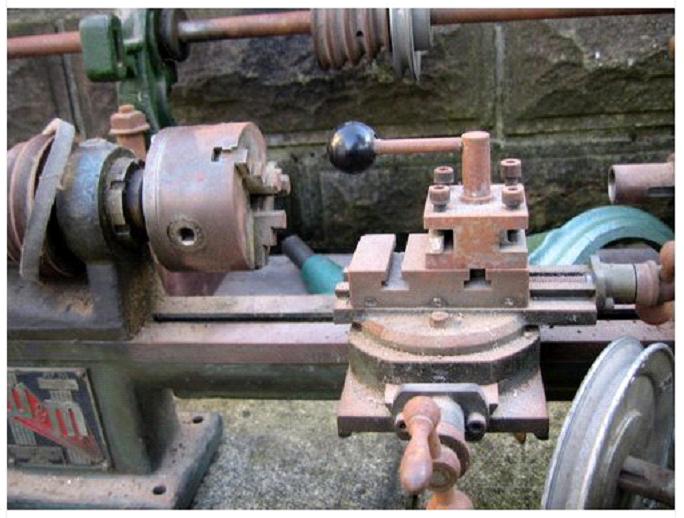 |
|
|
|
|
|
|
|
|
|
|
|
|
|