 |
 |
 |
 |
 |
 |
 |
 |
 |
 |
 |
 |
 |
 |
 |
 |
 |
 |
 |
 |
 |
 |
 |
 |
 |
 |
 |
 |
 |
 |
 |
 |
 |
 |
 |
 |
 |
 |
 |
 |
 |
 |
 |
 |
|
|
|
|
|
|
|
|
|
|
|
email: tony@lathes.co.uk Home Machine Tool Archive Machine-tools Sale & Wanted Machine Tool Manuals Catalogues Belts Books Accessories
Weiler Home Page and Condor Lathe
Weiler Primus
Weiler Praktikant
Weiler Praktikus
Weiler LZ280 & LZ300
Weiler LZ330
Commodor
Ergodor
Matador
Weiler 260 Series Plain Precision & Production Lathes
Weiler Lathes 1950s/60s including: LD-220, MD-220/W, LD220W, LCD-220, LZD-220, LD-250, LDS-250, LDT-250, MF-220, RDT-260, LZT-280N, LDT-250/6 & Variants
Handbooks, Parts Manuals & catalogues are available for Weiler lathes ...and the CONDOR
|
|
|
|
|
|
|
|
|
|
|
|
|
|
|
|
|
|
|
|
|
|
|
|
|
|
|
|
|
|
|
|
|
|
|
|
|
|
|
|
|
|
|
|
|
|
|
|
|
|
|
|
|
|
|
|
Long enjoying a fine reputation as a maker of high-quality lathes, together with a limited range of small milling machines, over many years the Weiler Company concentrated on a relatively limited range of conventional smaller models including simple plain-turning bench types, production capstan and toolroom-class screwcutting models. Models included the Commodor, Condor, Ergodor , Matador, Praktikant, Praktikus, Primus, Turnomat, the 260 Series of precision plain-turning types (in toolmaker, second-operation and capstan types) and other, similar types of smaller lathe that included screwcutting models sold in various forms and specifications as the conventional 220, 250, RDT-260 and 280 and the rarer variable-speed drive LD220W. The digits included in all Weiler lathe model designations referred to the swing - i.e. double the centre height so making, for example, the LZ280 a machine with a centre height of 140 mm (5.5") Starting life in the early 1950s, backgeared and screwcutting Weiler lathes began with the types RDT-260 and LZT-280 followed quickly by the LD220W and LD-250. By late in the decade the improved and larger LZ-280 and LZ-300 had been introduced alongside the larger LZ-330 (though at the time the earlier models, including the LZ-280, were still being offered as less costly alternatives). Finally, the LZ330 was to be renamed the "Condor" and modified in respect of spindle speeds and its screwcutting and feeds gearbox - where its traditional Norton-type, with a sliding tumbler working along an open slot along the front, was replaced by a superior, sealed, all-lever version. As with the LZ300, buyers of the Condor were offered a choice of two drive systems: the Type W used a mechanically operated, infinitely variable-speed mechanism and was intended for use by toolmakers, while the Type VS employed an interesting oil-bath-lubricated, pre-selector gearbox intended to be more efficient in general work and production processes (this successful, well-engineered arrangement was to be found on other models of Weiler lathe, including the Condor, and provided the customer with a sensible choice of options). Type W lathes are easily recognised by the large drum control wheel fitted to the front face of the strand immediately below the headstock while the Type VS had its controls in the same position but with a speed selector dial to right and an engagement lever to the left. In all other respects the W and VS were identical, with a 165 mm (6.5") centre height, accepting 800 mm (32") between centres and supplied on an integrated, robust sheet-metal cabinet stand that held the drive system, electrical switchgear and with a large storage cupboard, with locking doors, occupying the central section. The following notes apply only to the Condor version - details of the LZ330 can be found here: Weiler Condor Final drive to the spindle on both the W and VS was by twin, matched V-belts; the headstock pulley was arranged to run in own bearings - with the drive transmitted to the spindle though a sliding, internal-tooth clutch. With this system the spindle was relieved of all belt loads and isolated, to a large extent, from vibrations set up within the transmission system. As genuine, matched sets of belt pairs now appear to be unavailable, (and a pair of ordinary belts can cause noise and vibration), today the solution is to use a belt of the accurately made T-Link type.Fitted with a 2 h.p. motor, the variable-speed unit (Type W) gave stepless changes (on 50 Hz) from 46 to 1650 r.p.m. or (on 60 Hz) from 56 to 2000 r.p.m. while the oil-bath-lubricated pre-selector gearbox model (Type VS)- in conjunction with backgear and a 4 h.p. motor - gave eighteen spindle speeds of 24, 34, 50, 80, 115, 135, 165, 190, 235, 285, 335, 440, 500, 630, 930, 1330, 1900, and 2800 r.p.m. Alternatively, special speed ranges could be ordered that, by using a two-speed 3.0/4.0 h.p. motor, extended the range downwards to as low as 12 r.p.m. while leaving the usefully-high top speed unchanged. The variable-speed drive also had the optional of a two-speed motor installation; again, with an unchanged top speed - but with the bottom speed reduced to 23 r.p.m. (50 Hz) or 28 r.p.m. (60 Hz). Electrical control of the motor's stop, start and reverse was by a lever pivoting from the apron's right-hand face - the rod it operated being connected to a switch within the right-hand cabinet leg; unfortunately, the front face of this leg was also the location for the electrical controls, non of which appear to have been duplicated near the headstock. Should the operator's have been involved in an industrial-quality accident, not having immediate access to an emergency stop button would have seriously impaired his or her chances of survival. If you own a Weiler, arranging a kill switch on or near the headstock - or as a minimum one between the stand legs - would be a wise precaution. Continued below:
|
|
|
|
|
|
|
|
|
|
|
|
|
|
 |
|
|
|
|
|
|
Weiler Condor Model VS with pre-selector drive
Continued: Fastened, together with its drive motor on a cast-iron base plate and "cushion" mounted within the stand under the headstock, the wide Vee-belt driven speed-variator unit was of the traditional mechanical "expanding-and-contracting" type where one pulley was actively opened and closed (by a drive carried from the operator's handwheel along a flexible shaft) - with the other spring loaded. Drive to the headstock was by twin, matched V-belts to a pulley that ran on its own ball race with the drive transmitted to the spindle though a sliding internal tooth clutch - the spindle was thus being relieved of all belt loads and isolated, to a large extent, from vibrations set up within the transmission system ((as genuine, matched sets of V-belt pairs now appear to be unavailable - and a pair of unmatched, ordinary belts can cause noise and vibration) - today the solution is to use a belt of the accurately made T-Link type). Backgear, at a ratio of 5.7 : 1, was fitted and all headstock gears were hardened and shaved and lubricated by an oil bath. The spindle, bored through 1.5" (38 mm) was made from a manganese-chrome alloy steel forging, completely case hardened (not just the nose) and finish ground along its length. It ran in double-row cylindrical roller bearing at the front and in two adjustable combined thrust and angular-contact bearings at the rear. Three different spindle-nose fittings were offered, all with a No. 5 Morse taper in the spindle: a DIN 800/M 60x4 thread (original equipment on the older Model LZ 330), a D1-4" Camlock to special order and, as standard, a DIN 55 022/5 Bayonet flange. As on some other, high-quality lathes the screwcutting and feeds gearbox on the Model VS (but not the Model W) could be driven from either the changewheels (carried in an enclosed housing with an oil bath for lubrication) or through a V-belt system arranged to give faster cutting speeds on production work that required a high-grade surface finish - the intention being that the spindle was run in direct belt drive with its inherent smoothness preventing the harmful effects of backgear vibration being transferred to the workpiece. Using the mechanism (engaged through a clutch lever), the 30 rates of sliding feed ranged from 0.038 to 0.310 mm (0.0015" to 0.10125) per rev. Completely enclosed, the screwcutting and feeds gearbox incorporated the leadscrew reversing mechanism (so obviating the need to include this in the changewheel drive) and drove both the usual leadscrew for screwcutting and a separate shaft to drive the sliding and surfacing feeds. All gears were mounted on hardened and ground shafts running in bronze or ball bearings and the box could generate 60 rates of feed, English threads from 2 to 45 t.p.i. and metric pitches from 0.35 to 12 mm. By changing either one pick-off gear - or employing some of the extra changewheels supplied as standard - an extended ranges of pitches could be generated as well as Diametral and Module types. Double-walled, the oil-bath apron was a model of simplicity and strength. Shafts ran at both ends in bronze bushes or ball races with all gears heat-treated and cross-shaved. Feed direction - sliding or surfacing - was selected by a push-pull knob and, as the feed-shaft passed through a knock-off wormbox, the engagement and disengagement required only the lightest of touches on the lever - no matter how deep the cut. Most usefully, both feeds directions were equipped with adjustable knock-off stops that also doubled as overload protection. Unfortunately the carriage traverse handle was fitted to the left, so positioning the operator's hand to receive stray, red-hot turnings - though as compensation the wheel was equipped with a large-diameter zeroing micrometer dial. Of Acme form, the cross and top slide feed screws ran through bronze nuts and were supported on ball races with the cross-feed nut of the anti-backlash type and able to be adjusted from the outside. The micrometer dials were of large diameter, dull-chrome plated and fitted with friction adjusters that gave a light, non-stick action yet were secure from accidental re-setting. The cross slide was machined with two traverse T-slots behind the top slide, so allowing a rear toolpost or other accessory to be mounted. Of the other, similar contemporary Weiler lathes, the Matador was a slightly smaller machine than the Condor with a centre height of 5.87" and a capacity between centres of 20"; unlike the Condor is was not described as suitable for "Toolroom and Production" but simply as a "Toolroom" lathe. The electric motors were generally less powerful in the non variable-speed models and, while the general lines of the lathe were very similar, there were numerous significant differences. Later Weiler models followed much the same layout - some are still in production today - and included the Praktikant, Praktikus and Primus,
|
|
|
|
|
|
|
|
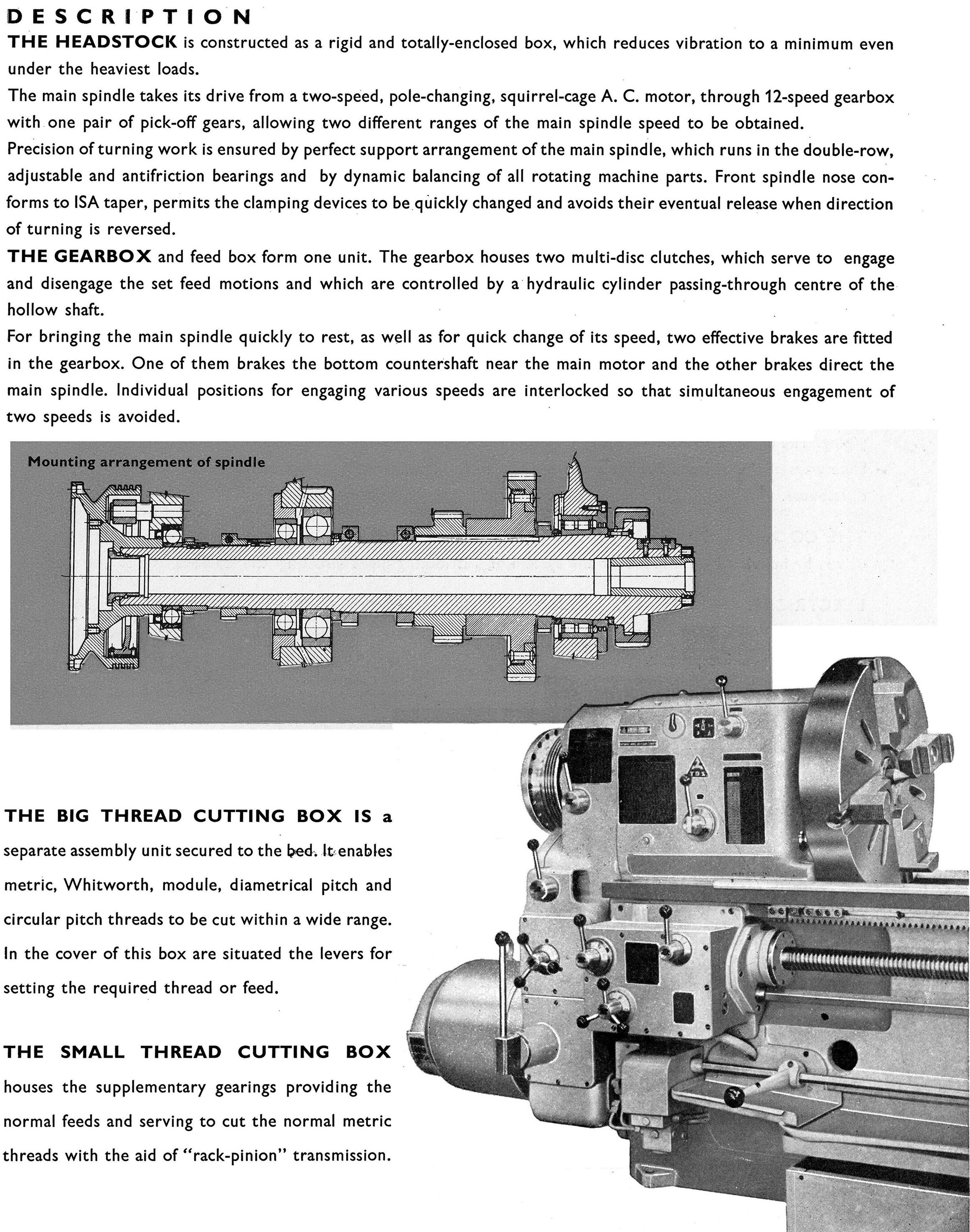 |
|
|
|
|
 |
|
|
|
|
|
|
|
|
|
|
 |
|
|
|
|
 |
|
|
|
|
|
 |
|
|
|
|
|
|
Complete transmission system of the Model VS showing the twin V-belt drive from motor to the 9-speed, car-like pre-selector gearbox then by another double V-belt to a pulley on the headstock spindle that ran in its own bearings. In conjunction with 1 : 5.7 ratio backgear this arrangement gave 18 spindle speeds of 24, 34, 50, 80, 115, 135, 165, 190, 235, 285, 335, 440, 500, 630, 930, 1330, 1900, and 2800 r.p.m. Alternatively, special speed ranges could be ordered which, by using a two-speed 3.0/4.0 hp motor, extended the range downwards to as low as 12 r.p.m. whilst leaving the usefully-high top speed unchanged.
|
|
|
|
|
|
|
|
|
|
|
|
|
|
 |
|
|
|
|
|
|
The speed-variator unit, with its wide V-belt, was fastened, together its drive motor, on a cast-iron base plate and "cushion" mounted within the stand under the headstock. The drive system was of the traditional mechanical "expanding-and-contracting" type where one pulley was actively opened and closed by a drive carried from the operator's handwheel along a flexible shaft to a bevel box on the end of the motor shaft - with the other pulley spring loaded; the diagram above should make the principle of operation clearer. Stepless changes (on 50 Hz) gave from 46 to 1650 r.p.m. or, on 60 Hz, from 56 to 2000 r.p.m. With the optional two-speed motor installed the top speed remained unchanged but the bottom speed was reduced to 23 rpm (50 Hz) or 28 rpm (60 Hz).
|
|
|
|
|
|
|
|
|
|
|
 |
|
|
|
|
|
|
The simple clean lines of the Weiler Condor were enhanced by machine-finished or plated control levers and bosses - and it was probably no accident that its appearance was further improved by the use of tight radii along its outline edges. Unaccountably, inconveniently - and of potentially danger - all the electrical controls, apart from an apron-mounted switch, were positioned out of reach on the right-hand cabinet leg. If you have one of these lathes a wide move is to relocate the controls to within easy reach of an operator
|
|
|
|
|
|
|
|
|
|
|
 |
|
|
|
|
|
|
Divided into three sections the left-hand section of the headstock held the mechanism through which the changewheels and power-feed shaft were driven; the central part isolated the twin spindle-drive V-belts from oil contamination while the right-hand compartment contained the hardened and ground headstock gears, 5.7 : 1 "backgear" and the lubricating-oil bath. An oil-level inspection window was provided. The spindle, bored through 1.5" (38 mm) was made from a manganese-chrome alloy-steel forging, completely case hardened (not just the nose) and finish ground along its length. It ran in double-row cylindrical roller bearing at the front and in two adjustable, combined thrust and angular-contact bearings at the rear. Three different spindle-nose fittings were offered, all with a No. 5 Morse taper: a DIN 800/M 60x4 thread (original equipment on the older Model LZ 330), a D1-4" Camlock to special order and, as standard, a DIN 55 022/5 Bayonet flange.
|
|
|
|
|
|
|
|
|
|
|
|
|
|
 |
|
|
|
|
|
|
As on some other, high-quality lathes, the screwcutting and feeds gearbox on the Model VS (but not the Model W) could be driven from either the changewheels (carried in an enclosed housing with an oil bath for lubrication) or through a V-belt system arranged to give faster cutting speeds on production work that required a high-grade surface finish. The intention was that the spindle, run in direct-belt drive with its inherent smoothness, preventing the harmful effects of backgear vibration being transferred to the workpiece. Using the mechanism (engaged through a clutch lever), the 30 rates of sliding feed ranged from 0.038 to 0.310 mm (0.0015" to 0.10125) per rev.
|
|
|
|
|
|
|
|
|
|
|
 |
|
|
|
|
|
 |
|
|
|
|
|
|
Interior of the Condor's screwcutting gearbox. The screwcutting and feeds gearbox was a completely enclosed, oil-bath design and had the ability to generate 60 rates of feed, English threads from 2 to 45 and metric pitches from 0.35 mm to 12 mm. By changing either one pick-off gear - or employing some of the extra changewheels supplied as standard - Diametral and Module pitch threads could be generated as well.
|
|
|
|
|
|
|
|
|
|
|
|
|
|
|
|
|
 |
|
|
|
|
|
|
Double-walled, the oil-bath apron was a model of simplicity and strength. Shafts ran at both ends in bronze bushes with heat-treated and cross-shaved gears. Feeds were selected by a push-pull knob and, as the feed-shaft passed through a knock-off wormbox, the engagement and disengagement required only the lightest of touches on a single lever - no matter how deep the cut. Most usefully - from both convenience and safety considerations - both directions of feed were fitted with adjustable knock-off stops. Held in gibbed, adjustable guides, the leadscrew clasp nuts were of a shell-shaped, split-bush designed for easy renewal. Unfortunately the carriage traverse handle was fitted on the left of the apron - positioning the operator's hand to receive its fair share of red-hot turnings - though as compensation if was equipped with a large-diameter zeroing micrometer dial. Of Acme form, the cross and top slide feed screws ran through bronze nuts and were supported on ball races with the cross-feed nut of the anti-backlash type and able to be adjusted from the outside. The micrometer dials were of large diameter, dull-chrome plated and fitted with friction adjusters that were light to adjust yet secure from accidental re-setting. The cross slide was machined with two traverse T-slots behind the top slide, so allowing a rear toolpost or other accessory to be mounted. Electrical control of the motor stop, start and reverse was by a lever pivoting from the apron's right-hand face - the rod it operated activated a switch positioned within the right hand cabinet leg; unfortunately, the front face of this leg was the location chosen for the other electrical controls, non of which appear to have been duplicated near the headstock. If your right hand was being involved in an industrial-quality accident having to kick out wildly with a foot to stop the lathe would not have improved your chances of survival. If you own a Weiler, arranging an extra switch on or near the headstock - or as a minimum a kill-switch between the stand legs - would be a wise precaution..
|
|
|
|
|
|
|
|
 |
|
|
|
|
|
|
Electrical stop, forward and reverse switch fastened to the right-hand end of the apron.
|
|
|
|
|
|
|
|
|
|
|
 |
|
|
|
|
|
|
|
|
|
Hydraulic Copying Attachment
|
|
|
|
|
|
|
|
|
|
|
|
|
|
|
|
 |
|
 |
|
|
|
|
|
|
|
|
|
|
|
Hydraulic Copying Attachment - component parts.
|
|
|
|
|
|
|
|
|
|
|
|
|
|
|
|
|
|
|
 |
|
|
|
|
|
|
|
|
|
|
|
|
|
|
|
Weiler Primus
Weiler Praktikant
Weiler Praktikus
Weiler LZ280 & LZ300
Weiler LZ330
Commodor
Ergodor
Matador
Weiler 260 Series Plain Precision & Production Lathes
Weiler Lathes 1950s/60s including: LD-220, MD-220/W, LD220W, LCD-220, LZD-220, LD-250, LDS-250, LDT-250, MF-220, RDT-260, LZT-280N, LDT-250/6 & Variants
Handbooks, Parts Manuals & catalogues are available for Weiler lathes ...and the CONDOR
Weiler Home Page and Condor Lathe email: tony@lathes.co.uk Home Machine Tool Archive Machine-tools Sale & Wanted
Machine Tool Manuals Catalogues Belts Books Accessories
|
|
|
|
|
|