 |
 |
 |
 |
 |
 |
 |
 |
 |
 |
 |
 |
 |
 |
 |
 |
 |
 |
 |
 |
 |
 |
 |
 |
 |
 |
 |
 |
 |
 |
 |
 |
 |
 |
 |
 |
 |
 |
 |
 |
 |
 |
 |
 |
 |
 |
 |
 |
 |
 |
 |
 |
 |
 |
 |
 |
 |
 |
 |
 |
 |
|
|
|
|
|
|
|
|
email: tony@lathes.co.uk Home Machine Tool Archive Machine-tools Sale & Wanted Machine Tool Manuals Catalogues Belts Books Accessories
Veem & Premo Lathes Other Australian-built lathes: Advance, Brackenbury & Austin, Burden, Clisby, Great Scott & Conrik, Hercus, A.E.Herbert, Premo, Qualos, Macson, Mars, Nuttall, Parkanson, Purcell, Rolfe, Sheraton, Tillico, T.N.C. Veem
A manual is available for the Premo/Veem lathe
Early Premo Lathe
|
|
|
|
|
|
|
|
|
|
|
|
|
|
|
|
|
|
|
|
|
|
|
|
|
|
|
|
|
|
|
|
|
|
|
|
|
|
|
|
|
|
|
|
|
|
|
|
|
|
|
|
|
|
|
|
|
|
|
|
|
|
|
|
|
|
|
|
|
|
|
|
|
Some confusion surrounds the origins of the identical 5.5" x 24" (280mm x 610mm) Veem and Premo lathes with the former being listed as built Veem Engineering Services of 14 Whyalla Street, Willetton, Western Australia (later of 22 Baile Road, Canning Vale, WA 6155) and the latter by Tulloch Ltd.* Concord Road, Rhodes, New South Wales. However, even that is not the full story for early Premo-badged lathes had an open, V-belt drive headstock and carried a plate proclaiming: "Designed and manufactured by Brackenbury and Austin, Pty Ltd Engineers Sydney N.S.W.". Advertised frequently by the agents Goodall from 1949 through the early 1950s, the earliest known publicity for the "Premo" was in the Sydney Morning Herald for the 15th of January, 1949 "Premo 5.25 gap bed hollow spindle screwcutting lathes. For early delivery book your order now" - the occasion almost certainly coinciding with the lathe's introduction. The first version of the lathe (maker unknown) was well built but entirely conventional for the time: 5.25" centre height, 24" between centres, roller-bearing headstock, gap-bed, backgeared and screwcutting with tumble reverse, a T-slotted (but rather short) cross slide and a built on motor/countershaft unit - though the use of flat belt drive (when similar American machines had switched to V-belts in the early 1930s) was hardly an up-to-date feature. In 1953 a heavily revised lathe (known to have been designed and manufactured by Brackenbury and Austin) was introduced. This had a centre height of 5.5-inches and a screwcutting and feeds gearbox - the first advertisement (in February of that year) in the Sydney Morning Herald proclaimed: "Inspect the new 5.5" Premo lathe with quick change gear box and automatic feeds. Details gladly forwarded on request." In November, 1954 a further advertisement by Goodall proclaimed the virtues of a modified cabinet stand: "5.5" Premo Timken taper bearing bench and pedestal lathes. Inspect the new deluxe cabinet stand for these machines". By the early 1960s the design had dated and a heavily revised Mk. 3 (now manufactured by Tulloch Ltd.) was introduced with more modern, angular lines to the bed and headstock (though the apron and tailstock remained unchanged) lines and a number of mechanical refinements. With Australian metrication in the 1970s came further changes with the lathe now constructed by Veem and labelled the Mk. 3M (the lathe painted blue below). Continued below:
|
|
|
|
|
|
|
|
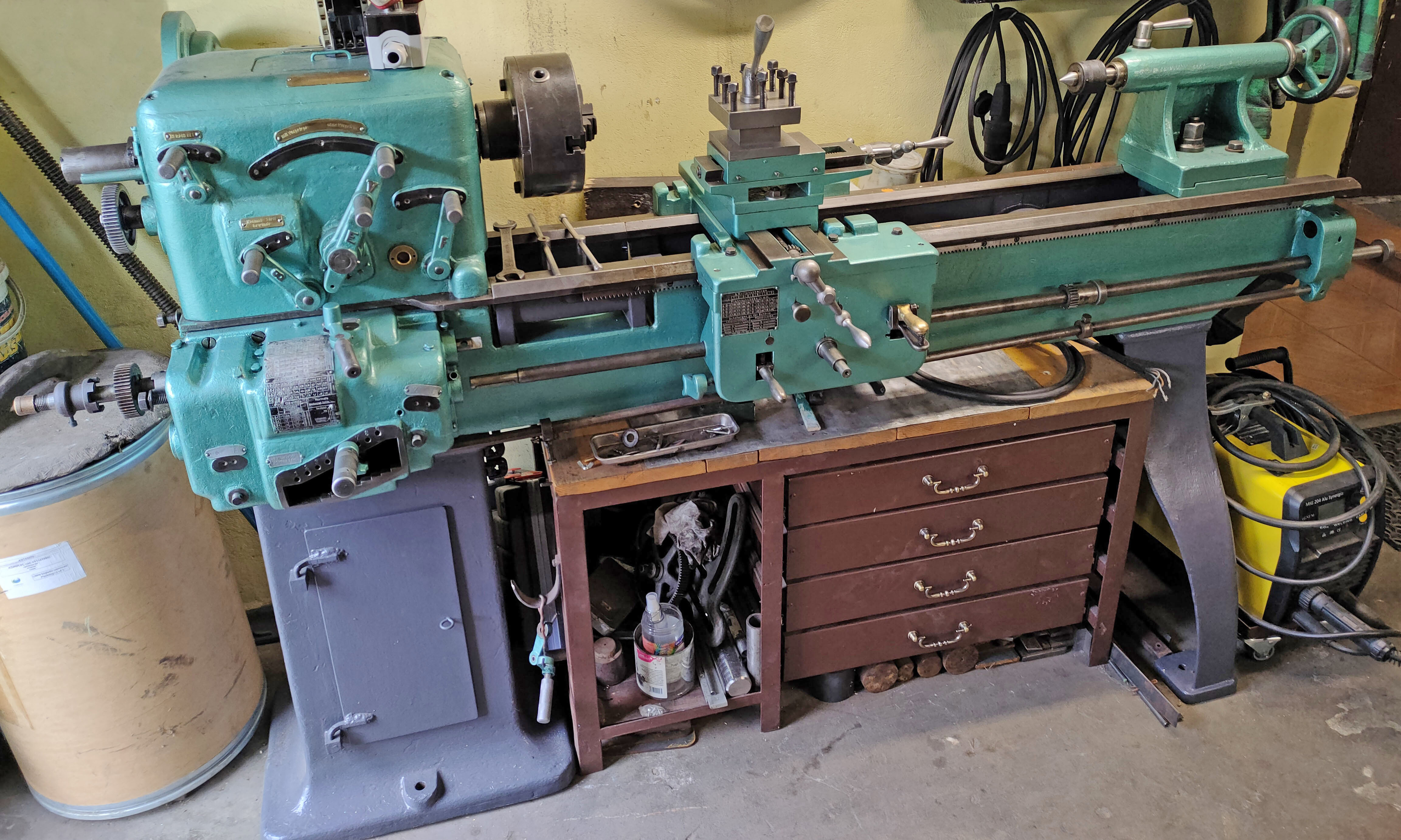 |
|
|
|
|
|
|
|
|
The original (Mk. 1) "Premo" was advertised frequently by Goodall from 1949 through the early 1950s. The earliest publicity so far discovered was in Sydney Morning Herald for the 15th of January, 1949: "Premo 5.25 gap bed hollow spindle screwcutting lathes. For early delivery book your order now" - the occasion almost certainly coinciding with the lathe's introduction. Should any reader have a lathe like this, the writer would be interested to hear from you
|
|
|
|
|
|
|
|
|
|
|
|
|
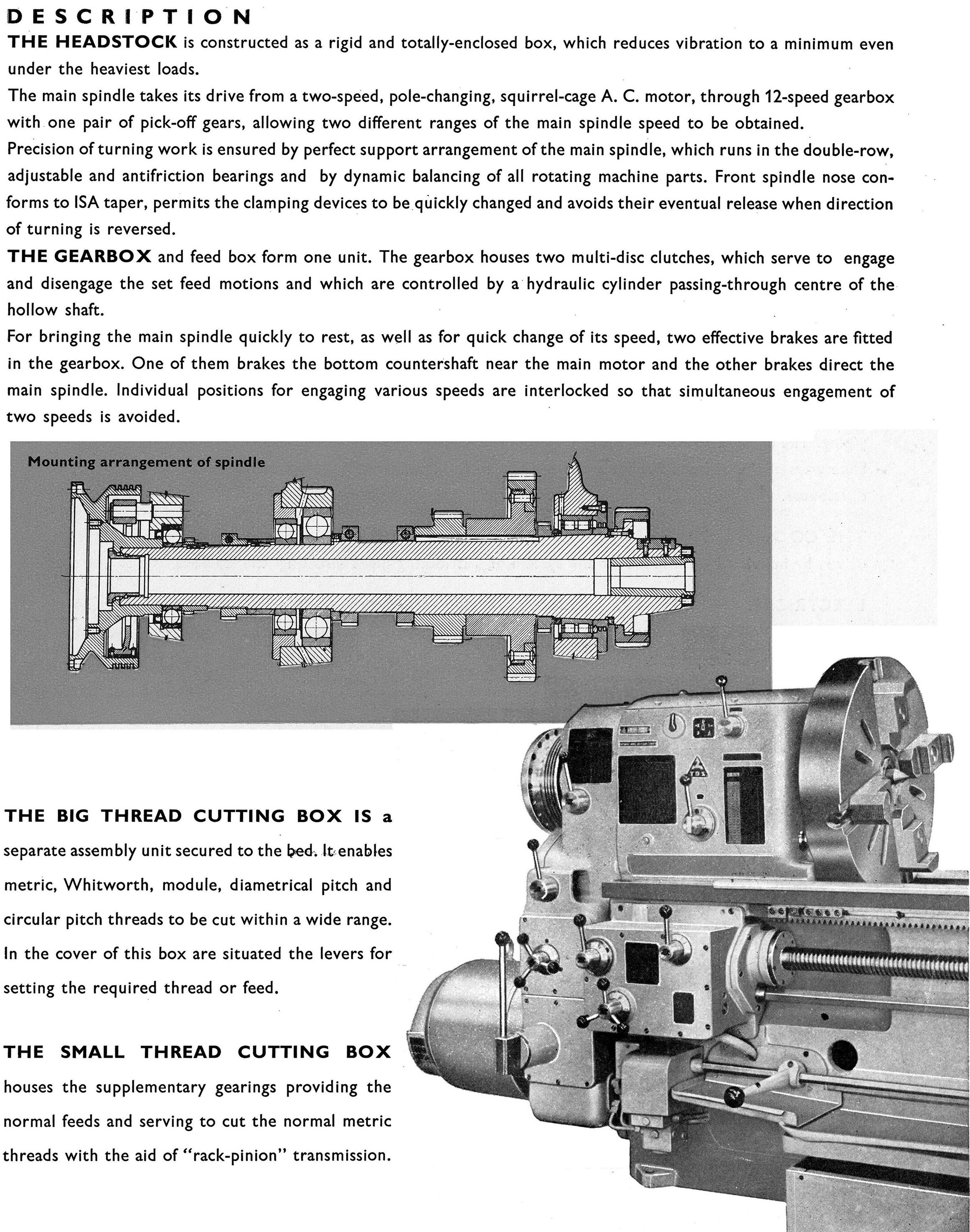 |
|
|
|
|
|
|
Designed and manufactured by Brackenbury and Austin, the new Mk. 2 5.5-inch Premo with a full screwcutting and feeds gearbox can be traced back to February, 1953 when an advertisement in the Sydney Morning Herald proclaimed: "Inspect the new 5.5" Premo lathe with quick change gear box and automatic feeds. Details gladly forwarded on request." In November, 1954 a further advertisement by Goodall proclaimed the virtues of a modified cabinet stand (as above): "5.5" Premo Timken taper bearing bench and pedestal lathes. Inspect the new deluxe cabinet stand for these machines".
|
|
|
|
|
|
|
|
 |
|
|
|
|
|
Mk. 3 - Badged as a "VEEM" this 5" x 24" (280mm x 610mm) lathe circa 1976 is shown on its maker's cabinet stand
Continued: Heavily built and (apart from the arrangement of its patented drive system) an entirely conventional backgeared and screwcutting lathe the last version Weem/Premo had a permanent (but rather slim) 360 mm-swing gap in its 180 mm wide, ground-finished, close-grained, mehanite-iron V-way bed. As was normal practice, the carriage and tailstock both ran on their own pair of V and flat ways. Although not mentioned by the makers in their sales literature, the back of the bed was machined flat and tapped to allow the mounting of a "Maximat" self-powered (swivelling-head) vertical milling attachment as used on a wide range of Emco lathes and stand-alone millers. Formed as a heavy, box-section casting the headstock was fitted with a flat, hinge-up lid that doubled as a useful tool tray - the opening allowing not only maintenance of the belt and gears but access to the oil nipple used to lubricate the spindle when the lathe was running in backgear. The engagement of backgear was by a single lever on the front face of the headstock which, when moved, had the effect of simultaneously disengaging the bull gear from the drive pulley and causing the other gears to come into mesh. As on some Colchester lathes, the headstock could, be adjusted on the bed and one owner reports being able to achieve a setting that produced an accuracy of better than 0.0001" 6 inches away from the nose of a 3-jaw chuck. Made from nickel steel, and running in generously large class 3 (close tolerance) Timken taper roller bearings, the 1.0156" (25.8mm) bore, No. 4 Morse taper headstock spindle was (users report) able to absorb very heavy cuts without chatter. The spindle was driven by a long-life, oil resistant toothed belt from an internal layshaft mounted across the rear of the headstock; the layshaft carried a 4-step V-belt pulley on its outer end driven by a 1.5 hp motor that was mounted on a platform hinged on the back of the headstock. 8 speeds were available, from 38 to 1300 rpm, and to change them the combined belt and gear-guard cast-aluminium cover had to be swung open and the drive belt from motor to headstock layshaft released by a combined mechanism that used a long "over-centre" action lever to slacken and apply the tension - together with an adjustable toggle (with a left-hand thread at one end a right-hand at the other) to adjust it. A useful practical touch was the inclusion of a wall across the inside of the changewheel cover that prevented lubricant from the gears being thrown onto the drive belt. A 1.5 hp 3-phase 450 volt motor was fitted as standard but the makers offered the option of single-phase electrics with a 240 volt, 1.5 hp motor with that best-of-all-options - "capacitor start and run" to give both enhanced starting and running torque. The electrical control gear was neatly mounted on the headstock-end front panel of the braced, sheet-steel stand - the switches being easily reached by the operator from his normal working position; because many of these lathes were supplied to schools and technical training establishments, the electrics were safely isolated by a key-operated switch. A 32-volt transformer was supplied to power the low-volt lighting and motor controls. Unfortunately, the wiring was left exposed on the inside face and, to stop users from employing the space inside as tool storage, the (hinged) panel was locked closed with three screws. The right-hand side of the cabinet was provided with a full-height hinged door with two shelves sufficient to hold the lathe's standard equipment together with a number of accessories. The rear of the centre section was arranged to accommodate an (optional) coolant pump and tank that, if fitted, was fed by a welded-in drain tube positioned directly above it. The rear of the saddle was supplied ready tapped to hold both the (extra-cost) taper turning attachment and the coolant distributor tube support bracket. Continued below:
|
|
|
|
|
|
|
|
 |
|
|
|
The cross slide was almost a full-length type with, unusually for a 5-inch lathe, two T slots across the rear; although the slots could have been used for holding a milling slide on the VEEM this was not done and instead the slide was mounted in the same degree-marked circular T-slot as the topslide. The micrometer dial locking screw (it has a brass pad at the end of its thread) is not original but a modification to overcome the disadvantages of the original "O" ring friction type.
|
|
|
|
|
|
|
|
|
Continued: Drive to the standard-fit metric screwcutting gearbox was through changewheels and a tumble-reverse mechanism; however, because the box could only generate 9 different pitches for each setting of the gears (and no sliding or reversible gear was fitted on the input shaft to double the range) extra changewheels had to be provided to enable a full threading range (from 0.5 to 3 mm pitch) to be obtained; conversion changewheels were also provided with the machine that allowed a good spread of English pitches, from 4 to 60 t.p.i., to be cut as well Unfortunately, on early versions of the lathe, the screwcutting arrangements meant that the thread-dial indicator could not be used in its ordinary form (with a single gear and dial) across all pitches and, instead of carrying the required gears on its shaft with some form of slotted mount to let them engage in turn with the leadscrew, it was supplied with three gears (and two dials) that had to be changed as required by the operator. Even then, the situation was not simple for, having fitted the correct combination of dial and gear, the engagement point varied from pitch to pitch and a chart had to be consulted to ensure that the clasp nuts were engaged at the right point. Fortunately, later machines were fitted with a modified thread indicator that carried three gears on its spindle (with two interchangeable dials) a modification that greatly simplified matters; the improved unit could also be retrofitted on earlier lathes. Of course, when cutting English threads, the clasp nuts (as on any other lathe) had to remain engaged whilst the whole gear train and spindle were electrically reversed to take the tool back to a point where the cut could be deepened. Reversible to even out wear the 22 mm-diameter 3 mm-pitch leadscrew was protected by a shear pin at the gearbox end and slotted along its length to provide a drive (through an apron-mounted worm and wheel) for the power sliding and surfacing feeds. Single-sided, with lubrication to bearings and gears from pipes and felts fed from a manually-filled oil gallery, the apron had power sliding and surfacing feeds; selection was by a centrally-mounted three-position quadrant lever that carried, concentrically with its pivot point, a knurled-edged knob that operated a simple cone clutch to wind the feeds into and out of engagement. Although there was no method of flicking the feeds in and out instantly (and safely) the clutch control wheel made up for this by being very sensitive in feel and working through just 1/8th of a turn. Unusually for a 5-inch lathe the cross slide was a full-length type, with two T slots across its rear section; although the slots could have been used for holding a milling slide on the VEEM the slide was designed to mount in the same degree-marked circular T-slot as the topslide. The gib strip was a solid "block" type that was held by screws against the roof of the slide and provided a far more rigid and, when properly adjusted, smoother-running assembly than would have been possible had the cheaper sort of the loose gib strip been used. The chrome-plated micrometer dials had large, flat, knurled edges (so that they could be gripped easily by oily fingers) and could be zeroed, with the setting held by the friction of "O" rings, an inexpensive but inherently unreliable system that was prone to allowing the setting to wander. To extend the cross slide travel and so make it more suitable for use as a boring table or with a milling slide (or milling attachment) the bracket that carried the cross-feed screw was constructed so that the slide could be drawn out over it until it reached the inner face of the micrometer dial. Fitted with a No. 2 Morse taper, the set-over tailstock had a self-eject barrel (engraved with metric graduations) with the body locked to the bed by a longitudinal shaft with the operating lever fitted at the rear under the barrel handle. Unfortunately the barrel was clamped by that crudest of methods, a long slit in the casting closed down by screw clamp. In 1953 a modified 5.5-inch Premo was introduced with a full screwcutting and feeds gearbox. The machine can be traced back to February of that year when an advertisement in the Sydney Morning Herald proclaimed: "Inspect the new 5.5" Premo lathe with quick change gear box and automatic feeds. Details gladly forwarded on request."
*Tulloch Ltd is a prominent heavy-engineering company of long standing. During W.W.2 they played a significant role in munitions production being responsible for "auxiliary marine craft". They were also one of the companies assigned to the production of the Cruiser tank for the Australian Army, undertaking the manufacture of the suspension. In post-war years they have been a leading manufacturer of railway locomotives and rolling stock..
|
|
|
|
|
|
|
|
 |
|
|
|
|
|
|
Veem, final assembly 1970s
|
|
|
|
|
|
|
|
 |
|
|
|
|
 |
|
|
|
|
|
|
Drive to the standard-fit metric screwcutting gearbox was though changewheels and a tumble-reverse mechanism. The guard cover was fitted with an internal dividing wall to stop lubricant from the gears being flung onto the drive belt.
|
|
|
|
|
|
|
|
|
|
|
 |
|
|
|
|
The top of the headstock, which was flat and formed with a lip so that it could be used as a convenient tool tray, was hinged at the rear to allow access to the connection that released the bull wheel from the spindle so that backgear could be engaged. A shear pin was fitted through the leadscrew under the O ring on the joining section. The screwcutting gearbox had just nine positions for the single tumble lever - and no sliding or reversible gear on the input shaft by which means many other makers had contrived to offer a choice of both fine and screwcutting feeds.
|
|
|
|
|
|
|
|
|
|
|
 |
|
|
|
|
|
|
The T-slotted cross slide and travelling steady
|
|
|
|
|
|
|
|
|
|
|
 |
|
|
|
|
|
|
Single-sided, with lubrication to bearings and gears from pipes and felts fed from a manually-filled oil gallery, the apron had power sliding and surfacing feeds; selection was by a centrally-mounted three-position quadrant lever that carried, concentrically with its pivot point, a knurled-edged knob that operated a simple cone clutch to wind the feeds into and out of engagement.
|
|
|
|
|
|
|
|
 |
|
|
|
|
|
|
The setting of drive belt from motor to headstock layshaft was controlled by a combined mechanism that used a long "over-centre" action lever to apply the tension together with an adjustable toggle (with a left-hand thread at one end a right hand at the other) to adjust it.
|
|
|
|
|
|
|
|
|
|
|
 |
|
|
|
|
|
|
3-point fixed steady with screw-adjustable jaws
|
|
|
|
|
|
|
|
|
|
|
 |
|
|
|
|
|
|
Travelling steady and metric thread-dial indicator - the latter supplied with three gears (and two dials) that had to be changed by the operator to suit the pitch being generated.
|
|
|
|
|
|
|
|
|
|
|
|
|
|
 |
|
|
|
|
|
|
Swivelling vertical slide mounted in place of the top slide. The feed screw end bracket is from a Myford ML10 - why tool up for an expensive mould when you can buy a finished unit "off the shelf" ?
|
|
|
|
|
|
|
|
|
|
|
 |
|
|
|
|
|
|
Fitted with a No. 2 Morse taper, self-eject barrel that was engraved with metric graduations, the set-over tailstock was locked to the bed by a longitudinal shaft with the operating lever fitted at the rear beneath the handwheel.
|
|
|
|
|
|
|
|
|
|
|
 |
|
|
|
|
|
|
The electrical switchgear was neatly mounted on the headstock-end cabinet door from where the switches could be easily reached by the operator from his normal working position; unfortunately, the wiring was left exposed on the inside of the door and so the cabinet could not (at least safely) be used to store loose tools.
|
|
|
|
|
|
|
|
|
|
|
 |
|
|
|
|
|
|
|
A Mk. 3M Veem data plate indicating manufacture during 1976
|
|
|
|
|
|
|
|
|
|
|
|
|
 |
|
|
|
|
|
|
Mk. 2 Premo lathe as introduced in 1953 and equipped with V instead of flat-belt drive, a screwcutting gearbox and a revised apron that provided power cross feed while also giving a much slower rate of sliding feed.
|
|
|
|
|
|
|
|
 |
|
|
|
|
|
 |
|
|
|
|
|
 |
|
|
|
|
|
 |
|
|
|
|
|
 |
|
|
|
|
|
 |
|
|
|
|
|
|
|
|
|
|
|
|
|
|
|
A manual is available for the Premo/Veem lathe
Early Premo Lathe
Other Australian-built lathes: Advance, Brackenbury & Austin, Burden, Clisby, Great Scott & Conrik, Hercus, A.E.Herbert, Premo, Qualos, Macson, Mars, Nuttall, Parkanson, Purcell, Rolfe, Sheraton, Tillico, T.N.C. Veem
Veem & Premo Lathes email: tony@lathes.co.uk Home Machine Tool Archive Machine-tools Sale & Wanted Machine Tool Manuals Catalogues Belts Books Accessories
|
|
|
|
|
|