 |
 |
 |
 |
 |
 |
 |
 |
 |
 |
 |
 |
 |
 |
 |
 |
 |
 |
 |
 |
 |
 |
 |
 |
 |
 |
 |
 |
 |
 |
 |
 |
 |
 |
 |
 |
 |
 |
|
|
|
|
|
|
|
|
|
|
|
|
|
|
|
|
|
|
|
|
|
|
|
|
|
|
|
|
|
|
|
|
|
|
|
|
|
|
|
|
|
|
|
|
|
|
|
|
|
|
|
|
|
Manufactured from the late 1980s onwards, the TOS FGS-25/32 and FGS-50 FGS-50/63 NC milling machines were a modern adaptation of the long-established and typical knee-type design. Instead of a single motor operating both the cutter and table-feed drives, the FGS employed a ram head into which was built a speed-change gearbox. Probably invented and first employed by the American Cincinnati Company in the late 1930, this design allowed the ram to act as an overarm for horizontal milling - while also forming a mount that could be moved in and out when fitted with vertical and slotting heads. The extra cross travel so gained meant that the miller could tackle far larger work than one of conventional arrangement. Able to carry jobs up to 450 kg in weight, the FGS-25/32 featured automatic tool clamping as standard for both the 40 INT horizontal spindle and the 'ordinary' vertical head, hardened bed ways for all directions of travel, a centralised lubrication system that also fed oil to the slideways, and the facility to set up automatic work cycles. Equipped with 18 spindle speeds, the ram-head gearbox was driven by two V-belts from a 5.5 kW motor bolted to its top face. The horizontal spindle ran, at the front, in a grease-lubricated high-precision, double-row roller bearing with axial thrust taken by two angular-contact ball races; at the rear another high-precision roller bearing was used, this being lubricated by oil mist. Automatic tool clamping was built in, operated by a column of Belleville springs with release by compressing them with a hydraulically-operated piston rod. Two vertical heads were offered at extra cost: a 95 kg "Universal" double-swivel unit - the Type IUG-25 - with each axis able to be rotated through 360° and an "ordinary" vertical type, the robust 180 kg IVG-25 that could be inclined at 45° each way from vertical. Both heads had the same speed range that, as standard, ran from 45 to 2240 r.p.m. with the option - at increased cost - of a slightly faster range spanning 56 to 2800 r.p.m. The design of the "Universal" head precluded both the fitting of automatic tool clamping and quill feed - while the vertical standard head had both, the 60 mm of quill travel being under the control of both a sensitive, slow-feed handwheel and a lever for quick-action drilling. Electrical control was built into an adjustable pendant control panel with push buttons used for starting and stopping the spindle and spindle-head motion. Auxiliary functions were provided with push buttons and switches for engagement and disengagement of the knee drop, work-cycle interruption, engagement and disengagement of climb milling, clamping and release of the cutting tool and for the coolant centralised lubrication systems. 1000 x 320 mm, the table had four 18 mm wide T-slots on a spacing of 63 mm with travel longitudinally of 720, in traverse of 360 mm and vertically 420 mm. Powered by a 1.1 kW motor, the table feed box was built into the right-hand side of the knee and incorporated directional clutches and brakes for all three feed axes. 13 rates of feed were available (selected by a single lever) these spanning from 16 to 1000 mm per minutes both longitudinally and in traverse and from 5 to 315 mm per minute vertically. A rapid feed was provided as part of the standard specification, this being 2800 mm per minute longitudinally and in traverse - and 900 mm per minute vertically. Operation of rapids was by pressing a spring-loaded lever, releasing it stopped the drive. Accessories and options included a very wide range of cutter arbors, the two mentioned vertical heads; a vertical head with power down-feed; slotting and rack-milling attachments, a universal indexing head; powered and hand-turned rotary tables; ordinary, swivel-base, tilting and self-centring machine vices; collet chucks and collet sets; cutter guards; a variety of cutters. Specification options included machines calibrated in inches; recirculating ball screws for the longitudinal and cross feeds and millers prepared for severe climatic conditions and/or equipped with electrical systems for other than the standard 380-volt 50 Hz supply. Millers could also be built to other specifications - though upon consultation only. The FGS 25/32 weighed 2310 kg and required a floor space of 2.56 by 2.56 metres.
|
|
|
|
|
|
|
|
|
|
|
|
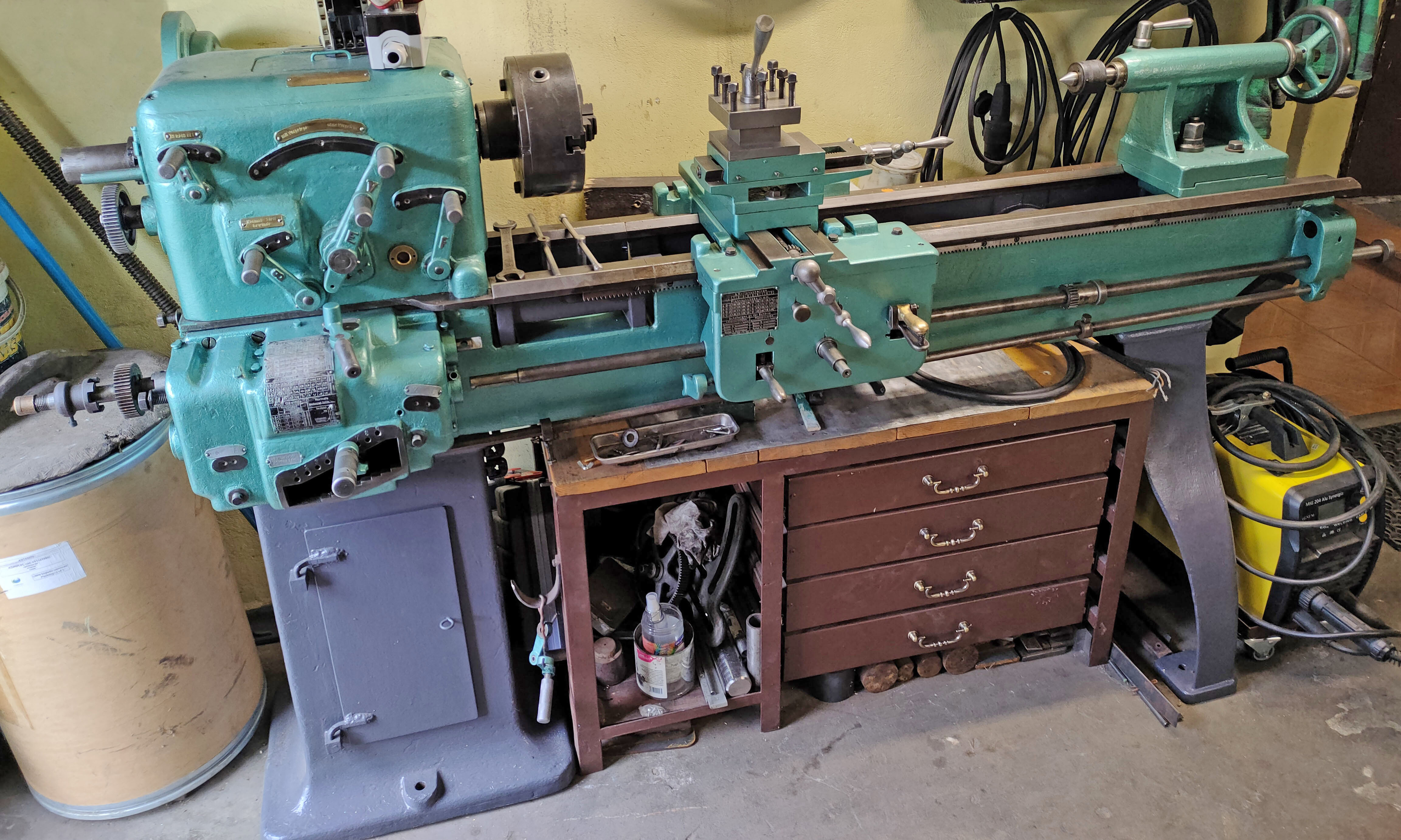 |
|
|
|
|
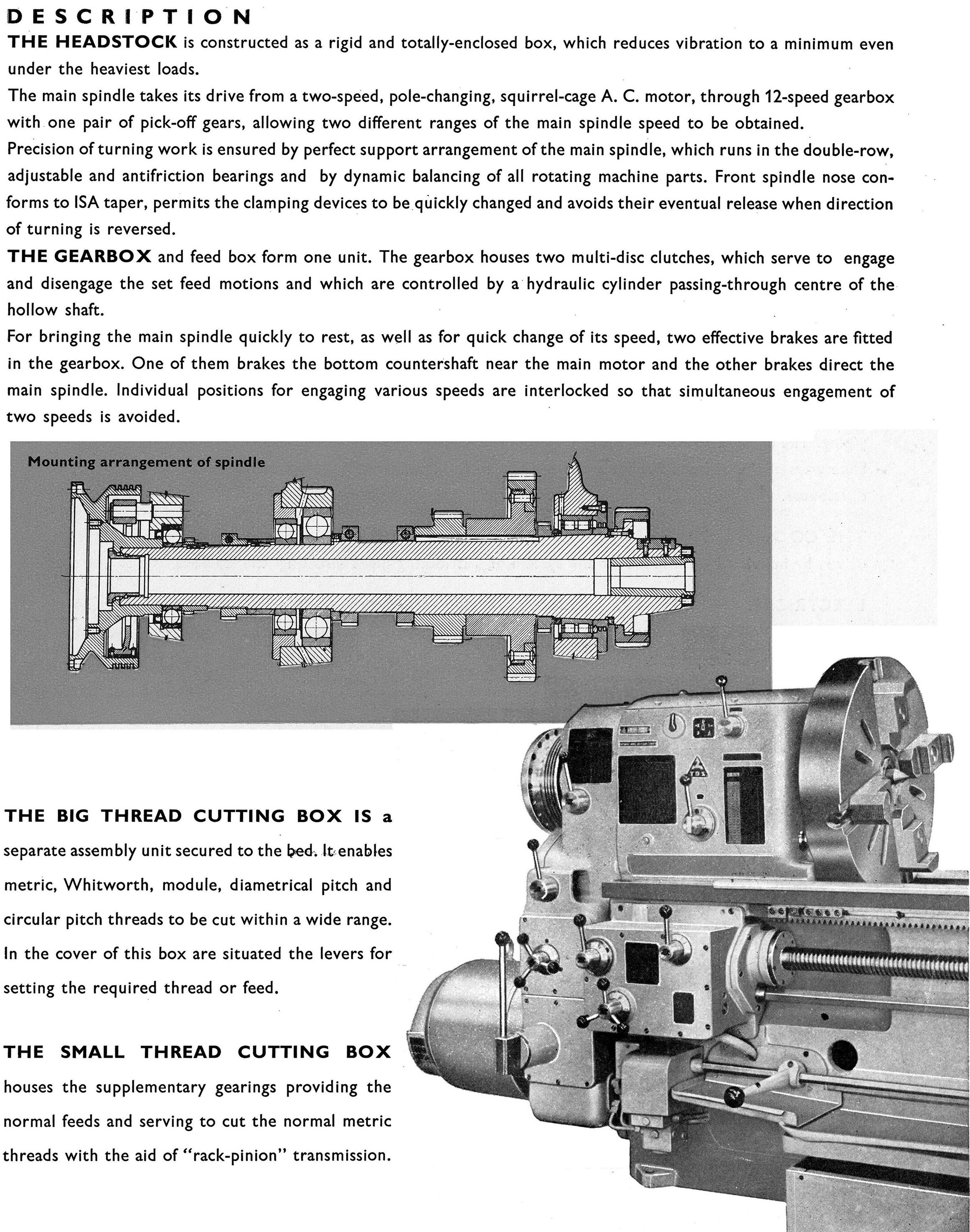 |
|
|
|
|
|
TOS FGS-25/32 miller fitted with the Universal vertical head Type IUG-25
|
|
|
|
|
|
|
|
|
|
|
|
 |
|
|
|
|
|
TOS FGS-25/32 miller in its horizontal form
|
|
|
|
|
|
|
 |
|
|
|
|
|
|
|
|
Spindle speeds were changed by three levers
|
|
|
|
|
|
|
|
|
 |
|
|
|
|
 |
|
|
|
|
|
Section through the end elevation of the gearbox-equipped ram head
|
|
|
|
|
|
|
|
|
|
|
|
 |
|
|
|
|
|
Section through the side elevation of the gearbox-equipped ram head
|
|
|
|
|
|
 |
|
|
|
|
|
Section through the spindle. The horizontal spindle ran, at the front, in a grease-lubricated high-precision, double-row roller bearing with axial thrust taken by two angular-contact ball races; at the rear another high-precision roller bearing was used, this being lubricated by oil mist. Tool clamping was built in, this being operated by a column of Belleville springs with release by compressing the springs with a hydraulically-operated piston rod.
|
|
|
|
|
|
|
 |
|
|
|
|
|
Front face of the ram head
|
|
|
|
|
|
|
|
|
|
|
|
 |
|
|
|
|
|
|
|
|
Overarm and drop-bracket supporting a long cutter arbor
|
|
|
|
|
|
|
|
|
 |
|
|
|
|
|
|
The "ordinary" vertical type, the robust 180 kg IVG-25, could be inclined at 45° each way from vertical. As standard, spindle speeds ran from 45 to 2240 r.p.m. with the option - at increased cost - of a slightly faster range spanning 56 to 2800 r.p.m. The 60 mm of quill travel was under the control of both a sensitive, slow-feed handwheel and a lever for quick-action drilling. Tool clamping was built in, this being operated by the same system used on the horizontal spindle with a column of Belleville springs whose release was by compressing them with a hydraulically-operated piston rod. The maker's appear to have listed a version of the head that incorporated power up and down feed, though its specification is not known.
|
|
|
|
|
|
|
 |
|
|
|
|
|
The vertical head Type IUG-25, a 95 kg "Universal" double-swivel unit with each axis able to be rotated through 360°. The standard speeds range ran from 45 to 2240 r.p.m. with the option - at increased cost - of a slightly faster range spanning 56 to 2800 r.p.m. The design of the "Universal" head precluded both the fitting of both the automatic tool clamping and quill feed fitted to the "standard" head.
|
|
|
|
|
|
|
|
|
|
|
|
 |
|
|
|
|
|
|
|
Slotting attachment 123 kg Type IOF-25. Able to be swivelled 45° each side of vertical, the unit had a maximum ram stroke of 80 mm, a minimum of 4 mm and a maximum stroke rate of 200 per minute. The maximum distance between the end of the ram and the table was 390 mm
|
|
|
|
|
|
|
|
|
|
|
 |
|
|
|
|
|
|
Knee assembly. Powered by a 1.1 kW motor, the table feed box was built into the right-hand side of the knee and incorporated directional clutches and brakes for all three feed axes. 13 rates of feed were available (selected by a single lever) these spanning from 16 to 1000 mm per minutes both longitudinally and in traverse and from 5 to 315 mm per minute vertically. A rapid feed was provided as part of the standard specification, this being 2800 mm per minute longitudinally and in traverse and 900 mm per minute vertically. Operation of rapids was by pressing a spring-loaded lever, releasing it stopped the drive.
|
|
|
|
|
|
|
 |
|
|
|
|
|
|
Electrical control was built into an adjustable pendant control panel with push buttons used for starting and stopping the spindle and spindle-head motion. Auxiliary functions were provided with push buttons and switches for engagement and disengagement of the knee drop, work-cycle interruption, engagement and disengagement of climb milling, clamping and release of the cutting tool and for the coolant centralised lubrication systems.
|
|
|
|
|
|
|
|
|
|
|
|
 |
|
|
|
|
|
Switchboard unit work-cycle switches
|
|
|
|
|
|
|
 |
|
|
|
|
|
|
Powered 320 mm diameter VMR rotary table - driven by a Carden shaft from an extension to the table's feed unit
|
|
|
|
|
|
|
 |
|
|
|
|
|
|
Hand-turned 320 mm diameter rotary table
|
|
|
|
|
|
|
 |
|
|
|
|
|
|
DU-250 Universal Dividing Head. This attachment had a 130 mm centre height and a spindle bore of 28 mm with a No. 4 Morse taper. Tailstock was also supplied. The unit was designed for direct and indirect simple and differential indexing and allowed the machining of spiral flutes and cams. Divisions were possible for all numbers from 2 to 60 and, at a given stepping, up to 720. With the differential indexing device in use, all divisions up to 400 were possible.
|
|
|
|
|
|
|
 |
|
|
|
|
|
|
Rack Milling attachment Type IDF-20/32. This accessory enabled not only the milling of racks, but also accurately-spaced holes and similar operations
|
|
|
|
|
|
|
|
|
|
|
|
|
|