 |
 |
 |
 |
 |
 |
 |
 |
 |
 |
 |
 |
 |
 |
 |
 |
 |
 |
 |
 |
 |
 |
 |
 |
 |
 |
 |
 |
 |
 |
 |
|
|
|
|
|
|
|
|
|
|
|
|
|
|
|
|
|
|
|
|
|
|
|
|
|
|
|
|
|
|
|
|
|
|
|
|
|
|
|
|
|
|
|
|
|
Besides their No. 10 and No. 11 metal-turning lathes, Sypher manufactured a distinctly different range of wood-turning models. All appear to have been constructed around the same simple and economical design of bed consisting of two strips of steel angle joined at each end by a cast-iron foot assembly. The steel was planed flat on the top surface and milled down the centre line to provide an accurate location for the headstock and tailstock.
|
|
|
|
|
|
|
|
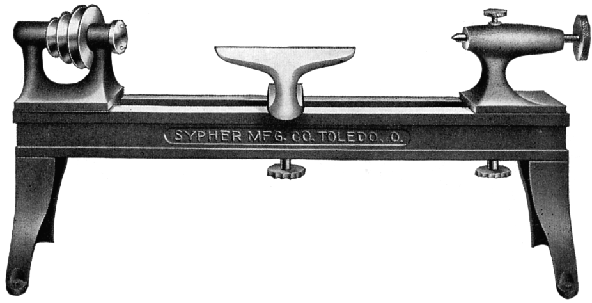 |
|
|
|
|
|
|
No. 1 and No 2 Lathe. These were tiny machines, with just 4-inches of swing (a centre height of 2 inches) and accepting 11 inches between centres (No. 1) and 17 inches (No. 2). Although it was a "proper" lathe, the makers advertised it as: "A Real Speed Lathe" - the term speed lathe being used in the USA to describe almost any machine with a simple headstock (or even just an electric motor) and some form of tool-rest assembly. The picture flatters the lathe's cosmetic finish: in reality it was comparatively crude, as one might expect of a lathe designed to sell at the bottom of the market. Note the simple T-rest, formed on one piece and non-adjustable for height
|
|
|
|
|
|
|
|
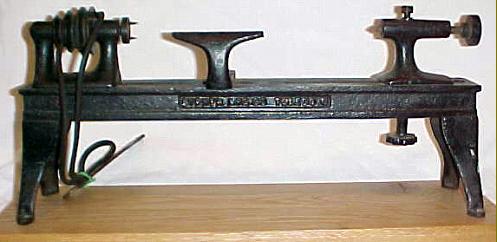 |
|
|
|
|
|
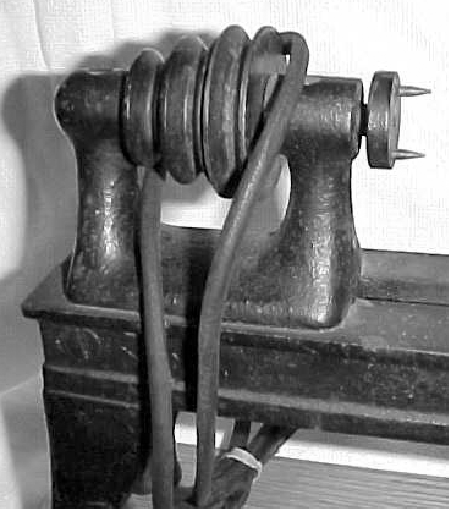 |
|
|
|
|
|
|
|
Headstock of the No. 1 and No. 2 lathe
|
|
|
|
|
|
|
|
|
|
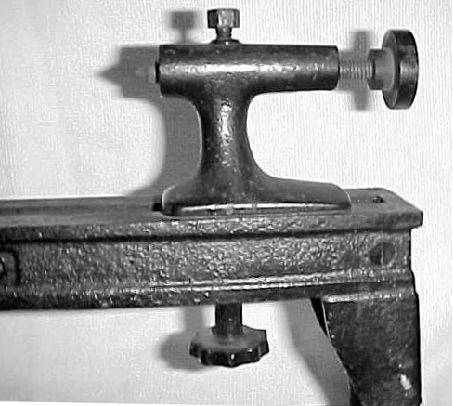 |
|
|
|
|
|
|
|
|
|
Tailstock of the No. 1 and No. 2 lathe
|
|
|
|
|
|
|
|
|
|
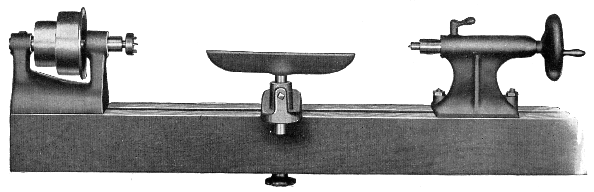 |
|
|
|
|
|
|
No. 15 Lathe This was a build-it-yourself concept with the manufacturer providing the headstock, tool rest and tailstock, leaving the customer to find two length of well-seasoned 2" x 4" hard wood which were mounted to
|
|
|
|
|
|
|
|
|
|
|
 |
|
|
|
|
|
|
The No. 19 lathe had a swing of 10 inches and a distance between the No. 1 Morse taper centres of 25 inches - however, the provision of Morse sockets was a $2 optional-extra, the centres were otherwise held in place by set screws. The bed was economically constructed from 1/4" thick steel angle which - and the makers made much of this - had been planed flat on the top; a slot, one-inch wide was milled down the centre to locate both headstock and tailstock. The headstock was bushed with brass, not an ideal material, but one which the makers pointed out could be replaced for just 25c. The fist use of a V-pulley for the headstock of a small lathe for amateur use (for which the makers offered a choice of a V or round belt) can be traced to 1929, the approximate date of this model.
|
|
|
|
|
|
|
|
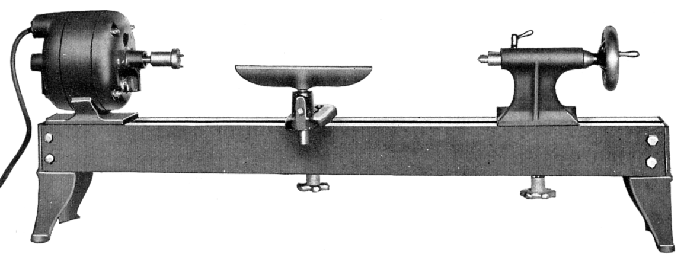 |
|
|
|
|
|
No. 25 Electric Bench Lathe 7.75" x 24" A cheap and sometimes effective way of producing a budget wood-turning lathe is to make the electric motor act the part of the headstock. If the motor is large, specially designed or adapted (or the work undertaken not too heavy) there is some real chance of success. However, in the case of the No. 25 Sypher lathe, with an ordinary 0.25 hp, 60 cycle, 1750 rpm motor bolted to a single, centrally-positioned cast-iron foot (and the number of speeds restricted to one) then the prospects cannot have been so bright for other than very simple, light work. The bed was constructed from two lengths of 3" x 1.5" channel-section steel bolted at each end to cast-iron feet. The tailstock was from the No. 10 and No. 11 lathe with a No. 1 Morse taper centre, automatically knocked out as the spindle was drawn back. This lathe is very similar to the "Peerless" - which was almost certainly made by Sypher - shown in the 1930 edition of the Sears, Roebuck Wood Working Machinery catalog.
|
|
|
|
|
|
|
|
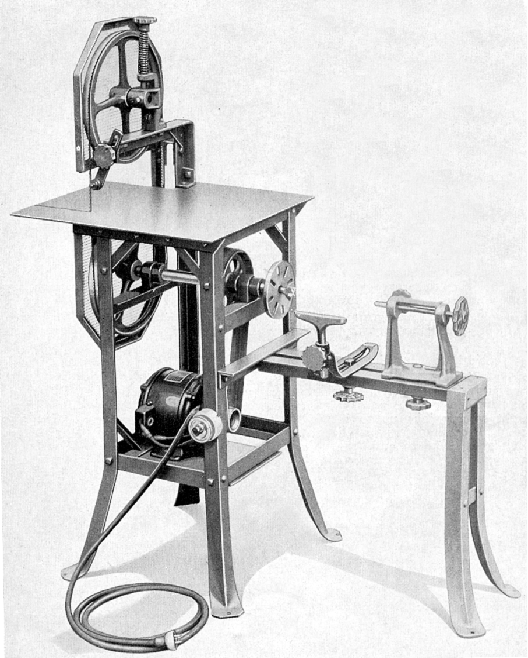 |
|
|
|
|
|
|
No. 46 Combination Band Saw and Lathe. With a swing of 5.5 inches and a capacity between centres of 28" this combination tool would have provided the amateur enthusiast of the 1920s and 1930s with a useful work tool. The chances that the cast-iron tailstock could have been brought into accurate alignment with the plumber-bearing mounted headstock spindle must have been slim at best. The price, in the early 1930s, was $45.
|
|
|
|
|
|
|
|
|
|
|
|
|
|
|
|
|
|
|