 |
 |
 |
 |
 |
 |
 |
 |
 |
 |
 |
 |
 |
 |
 |
 |
 |
 |
 |
 |
 |
|
|
|
|
|
|
|
|
|
|
|
|
|
|
|
|
|
|
|
|
|
|
|
|
|
|
|
|
|
|
|
|
|
The Sawyer Watch Tool Co. was founded in July 1860 by Sylvanus Sawyer in Fitchburg, Mass. as a reorganisation of the New England Machine Co. The Company did not just make lathes, but a variety of equipment for use in watch and clock-making factories including a pinion cutting engine, and automatic leaf polisher for polishing the leaf or teeth of pinions and an automatic staff and pivot turning machine for turning staffs and pivots. At least two models of lathe are known to have been manufactured (shown below) both with a single round foot beneath the headstock: the No.2 for watchmakers and the No. 21/2 for larger work - the latter looking as though it qualified to be included in the "bench precision" class. Both were of the WW (Webster Whitcombe) type with a heavy, fat-topped bed with bevelled sides to locate the headstock, slide rest and tailstock. They incorporated the latest advances in high-speed spindle design with double-tapered bearings in hardened steel. They could be supplied with a range of useful accessories including screw-driven a cut-off (forming) slide that had what was, for the time - and possible all time - a unique feature, a toolpost able to be driven at right-angles to the slide by a crank-handle connected to a universally-jointed shaft turning what must have been rack-and-pinion gearing. Despite what must have been overwhelming evidence of the superiority of the hollow spindle lathe holding a draw-in split chuck (now called a collet) invented in 1857 or 1858 by Charles S. Moseley, in subsequent years several inventors attempted to improve on this system - but all to avail. While Mr Sawyer also used the hollow-spindle design, his patent included in it a work-holding device that could be adapted to secure other items on the end of the spindle - this being to improve on the method then in use of using wax to hold items on a small faceplate. Despite his claim that there was a reduction in the number of parts used when compared to an earlier patent of the same type (US 220291) by Kesselmeier - it appears to have been an interesting though unnecessarily complicated arrangement and appears never have been taken up by other makers. If it was ever used on Sawyer's own lathes is not known - so, if you have an example of this attachment on a Sawyer or other make of lathe, the writer would be very interested to hear from you..
|
|
|
|
|
|
|
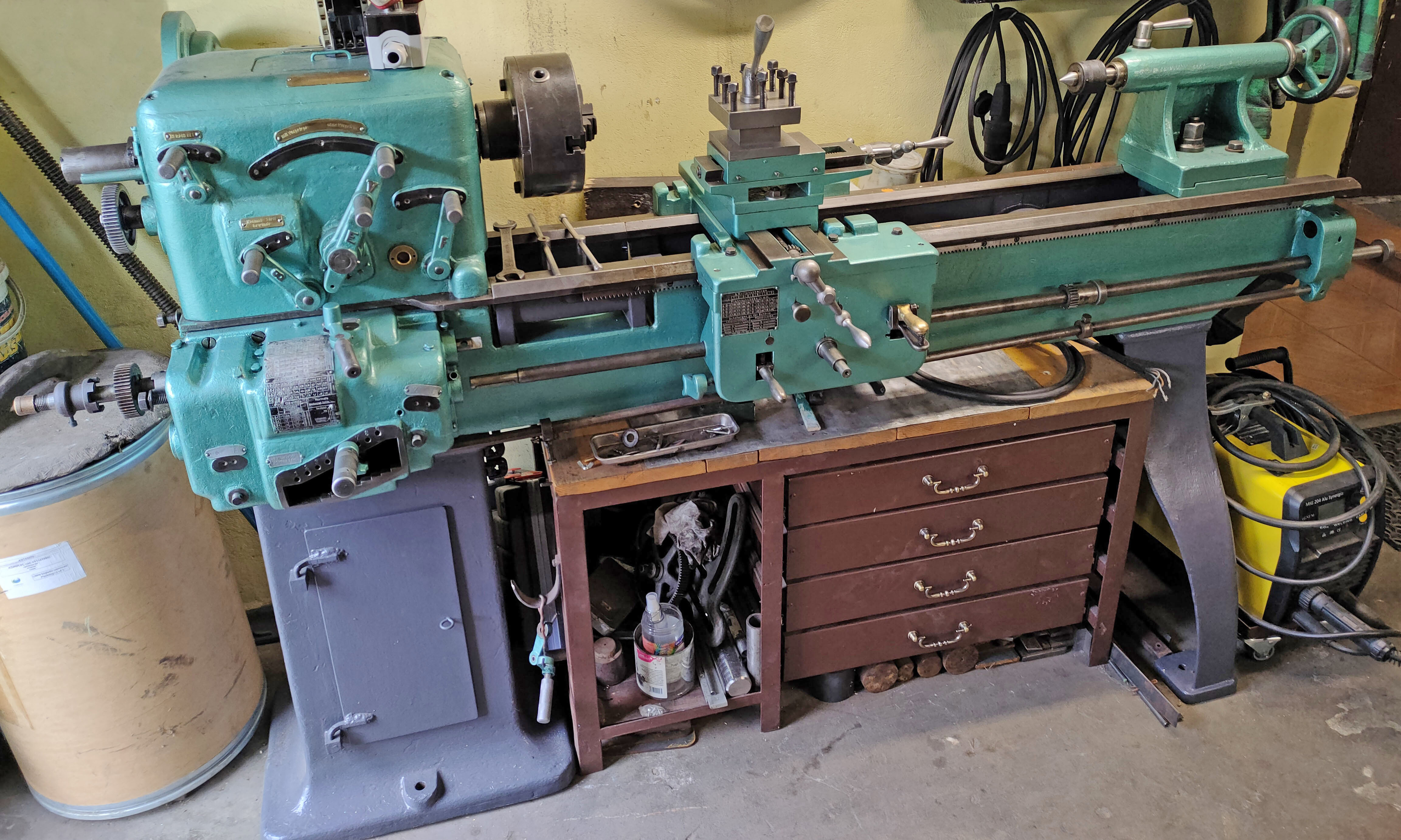 |
|
|
|
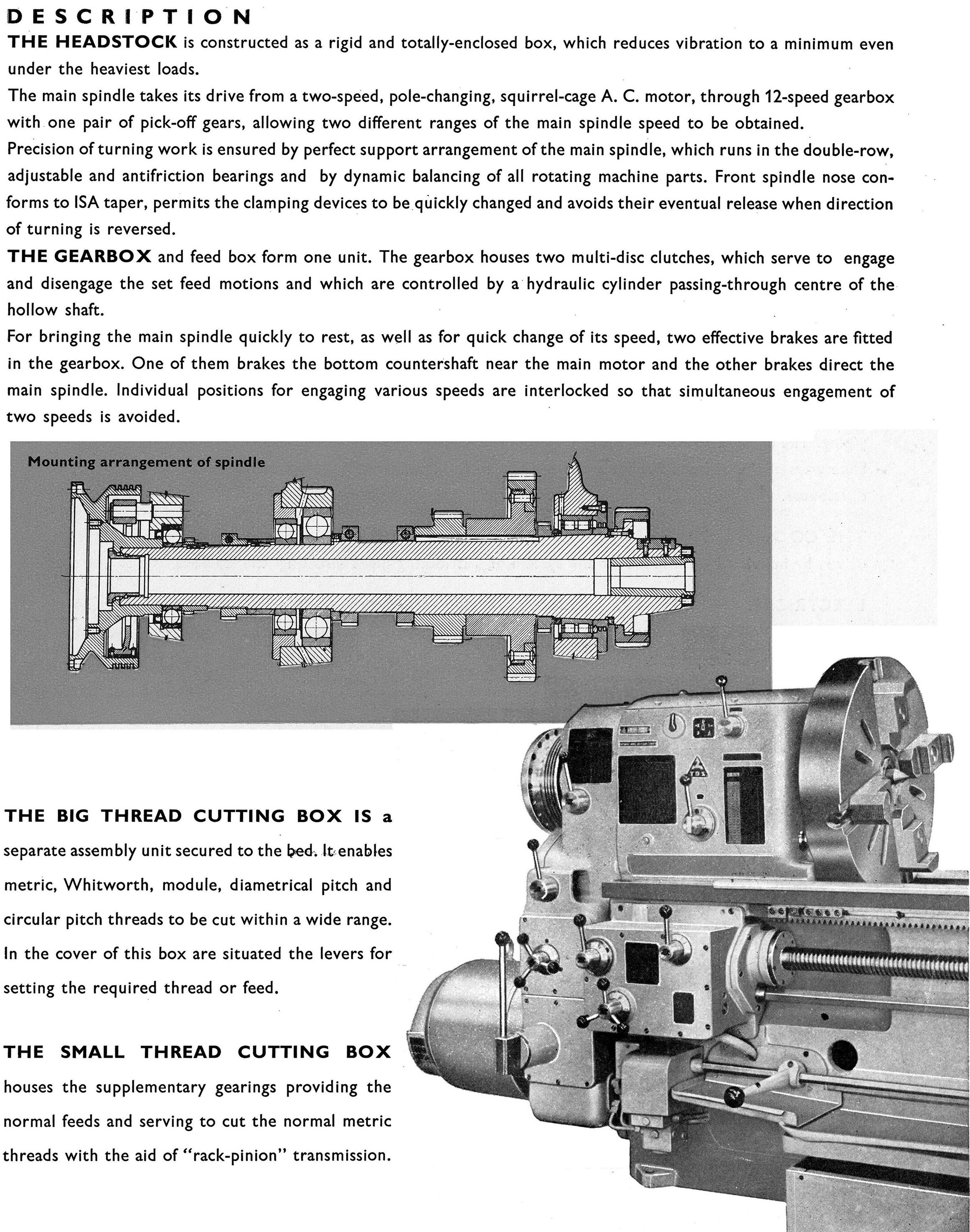 |
|
|
|
 |
|
|
|
|
|
|
|
|
 |
|
|
|
|
|
|
The Sawyer No.2 lathe for watchmakers fitted with screw-driven a cut-off (forming) slide that had what for the time (and possible all time) was a unique feature, a toolpost able to be driven at right-angles to the slide by a crank-handle connected to a universally-jointed shaft turning what must have been rack-and-pinion gearing.
|
|
|
|
|
|
|
 |
|
|
|
|
|
|
The Sawyer No. 21/2 for larger work--it's size and general appearance suggesting that it might qualify to be included in the "bench precision" class.
|
|
|
|
|
|
|
 |
|
|
|
|
The automatic leaf polisher is designed for polishing the leaf or teeth of pinions. It can he set to make so many strokes a tooth; it also can be set to polish so many teeth (or as many teeth as may be in the pinion), and not run by and polish one tooth the second time, which would cause an imperfection in the pinion. It rotates the pinion itself, that is, as soon as a tooth is polished, it turns the pinion around to the next tooth, and is arranged to plane the form on the polisher without removing it from the machine. It has all the necessary adjustments for its particular use.
|
|
|
|
|
|
|
|
 |
|
|
|
|
|
|
The automatic staff and pivot turning machine is designed for turning staffs and pivots, and is capable of doing a great amount of work. It can be adjusted to produce staffs and pivots in quantity of exact size. The machine will do the turning while the operator is preparing another piece of work to put in it, and the process is repeated. Every staff is turned upon dead centers, thereby insuring them to be perfectly true. It can be set to turn straight or taper, and to square up the shoulders, and has every adjust meat necessary to facilitate Its working, and produce accurate work at a very small cost..
|
|
|
|
|
|
|
|
 |
|
|
|
|
|
|
The pinion cutting engine, shown in the cut, is designed for cutting the teeth in small pinions. It has a revolving head with three spindles, each spindle running in a quill or shell, made from the finest steel, hardened, | and has double taper bearings. The spindle is also of hardened steel, ground lo fit the quill, has a fine combination of adjustments, and can be set with great accuracy. On the back end of each spindle is a gear. In revolving the head the driving need not be stopped, as the gear on the end of the spindle will connect with the driving gear while in motion, which facilitates the working of the machine and adds to its daily production.
|
|
|
|
|
|
|
|
|
|
|
|
|
|