 |
 |
 |
 |
 |
 |
 |
 |
 |
 |
 |
 |
 |
 |
 |
 |
 |
 |
 |
 |
 |
 |
 |
 |
 |
 |
 |
 |
 |
|
|
|
|
|
|
|
|
|
|
|
|
|
|
|
|
|
|
|
|
|
|
|
|
|
|
|
|
|
|
|
|
|
|
|
|
|
|
|
|
|
|
|
Manufactured by Oerlikon-Bührle, WMVD-Division, Birchstrasse 155, CH-8050 Zurich in Switzerland, the Oerlikon UB2 was designed as a versatile, high-precision milling and drilling machine that could be used as either a static or portable unit. Able to be ordered complete, or as separate components depending upon a customer's particular requirements, the beautifully made UB2 consisted of four elements: a cast-iron, T-slotted baseplate or stand; a large-diameter vertical column with a 4-bolt mounting flange; a "crosshead" casting that moved up and down the vertical column and, passing through the crosshead, a horizontal tube with a milling/drilling head on its end. As a close examination of its features and construction reveals, the designers exercised considerable ingenuity to make the UB2 as compact, strong, versatile and adaptable as possible - whilst sacrificing little in the way of rigidity. Secured to the baseplate by 4 bolts the vertical column could be set in any convenient position, even allowing the head to overhang the edge and so machine large or awkward components positioned to the side or above. All linear movements - up and down with a travel of 590 mm and in and out through 390 mm - were made quickly and easily by a removable hand crank working through worm and rack gearing. The head could be turned 360 degrees in all directions - achieved by swinging the crosshead around the vertical column (it was supported in ball bearings for ease of movement by hand) and manually rotating the horizontal column around its axis against a degree scale inscribed on the crosshead. Continued below:
|
|
|
|
|
|
|
|
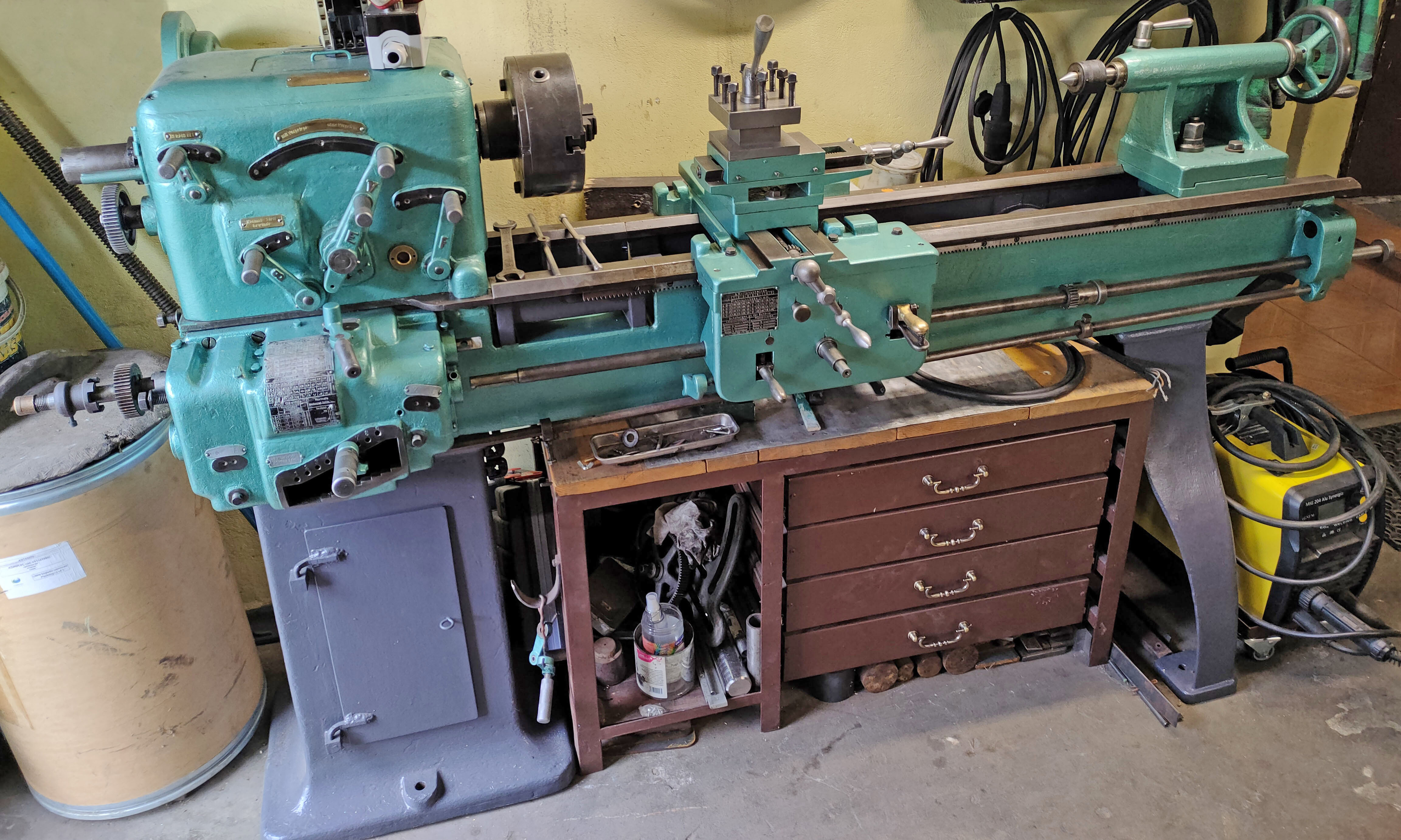 |
|
|
|
|
|
|
Continued: Because the elevation rack was captive within the crosshead, it had to rotate with it, and was secured at the top and bottom within captive rings. Each ring had a bevelled inside face against which the tapered end of the rack registered - an identical arrangement being used for many years on inexpensive Taiwanese mill/drill machines. This arrangement meant that, if the head was raised or lowered, there was no way to maintain lateral alignment - the head being loose to turn on the column. To solve the problem the makers provided a neat solution: a pair of hinged, quick-release clamps that could be fastened round the column and over the rack - so locking it in place and causing it to act as a vertical guide bar. Because the head would most commonly have been used vertically and horizontally to the left or right, the makers provided, via a lever, a stout indexing plunger to ensure that these positions could be quickly and accurately set. Locking levers were of the adjustable type, with the handles spring-loaded and able to be indexed to their most convenient operating position. A masterpiece of compact engineering, the drive system consisted of a 2-speed 1.2/1.5 h.p. 3-phase motor built into the rear end of the horizontal tube and connected (by a long shaft) to an oil-immersed 4-speed gearbox situated just behind the vertical head. By this means the rear of the machine was kept clear and its overall dimensions considerably reduced - there was no projecting motor, mounting plate, drive belts or guards to get in the way and the miller was thus able to be positioned more easily when attempting (in its portable role) to machine hard-to-reach jobs. A good spread of eight reversible speeds was provided in geometric progression: 25, 50, 80, 160, 400, 800, 1280 and 2560 r.p.m. Continued below:
|
|
|
|
|
|
|
|
|
|
|
|
|
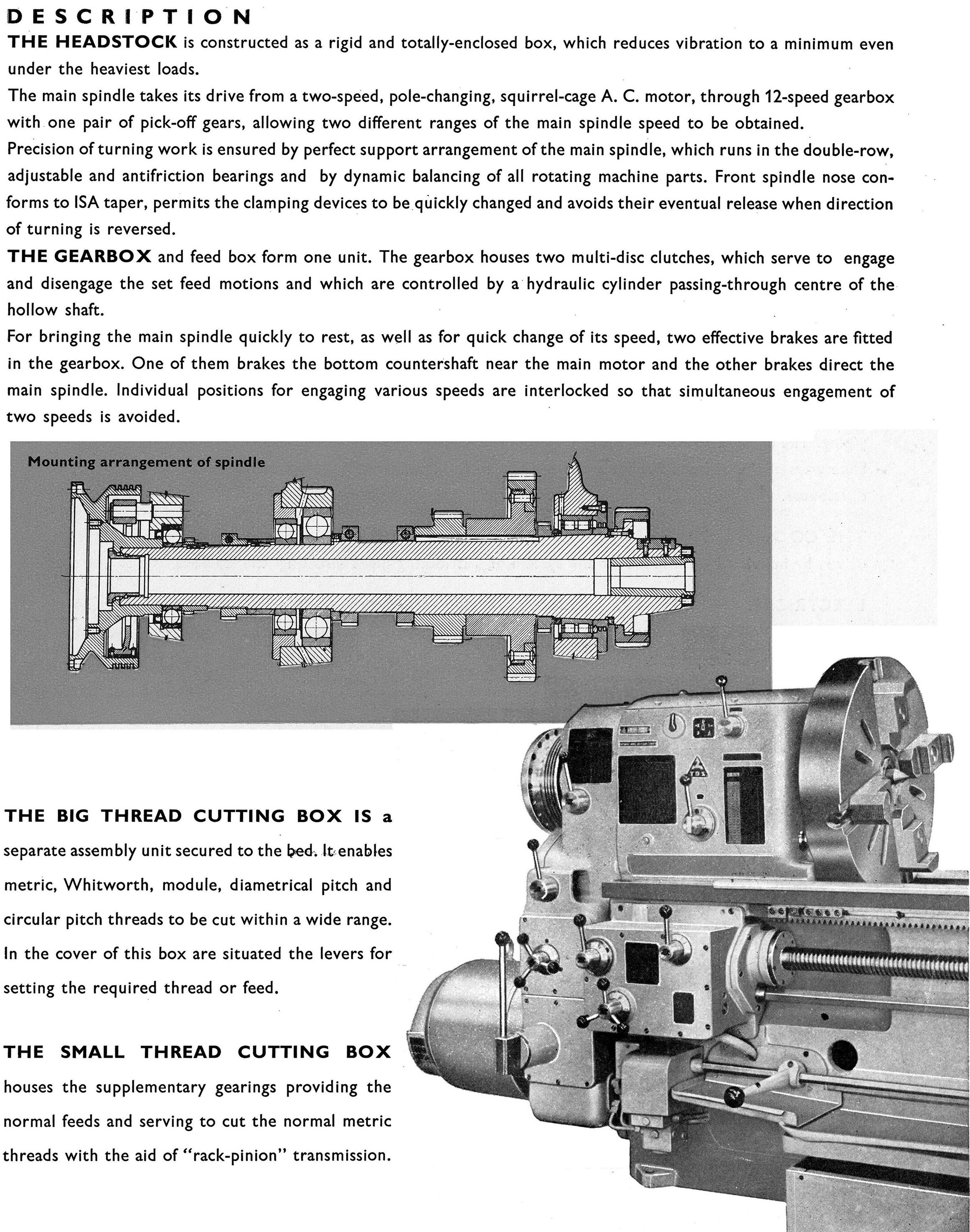 |
|
|
|
|
|
|
Cast-iron box stand with top and side-mounted T-slotted tables and the optional storage drawers
Continued: Running in a rigid assembly of an adjustable, double-row, high-precision roller bearing at the bottom (and a ball race at the top to allow for expansion) the chrome-molybdenum spindle had a flame-hardened, No. 3 Morse taper nose with an external thread to mount a collet chuck, boring-bar holder or other screwed fitting. Cutting tools with taper shanks could be drawn into and ejected from the spindle by a "clamping and release rod" whilst, to shorten tool-changing times, a quick-action ejector was fitted that automatically released the tool as the spindle retracted. The quill could be moved through its 150 mm of travel by either a quick-action lever with rack-and-pinion gearing or, very slowly, though a worm-and-wheel mechanism. Unfortunately, instead of being at the side, the handwheel for the fine feed was placed awkwardly, on the front face of the head and, to compound the error, was both rather small and lacked a handle - it had to be turned using finger cut-outs in the rim. In compensation, three rates of power down-feed were available - 0.06, 0.12 and 0.25 mm of feed per revolution of the spindle - engaged by a short lever and instantly stopped by pulling out a knob on the face of the head. Also available, as an optional extra, was a mechanism that provided an automatic disengagement of the drive to an accuracy of within 0.1 mm (0.004"). Continued below:
|
|
|
|
|
|
|
|
 |
|
|
|
|
|
|
Section though the horizontal tube and vertical head
Continued: Two stands were available: one constructed from welded steel that took the separate cast-iron T-slotted base plate (this unit was preferred if the machine was going to be used as a portable unit) and another one-piece, box-type in cast-iron. The latter unit had two 880 mm x 700 mm machined faces, one on top with five T-slots and another, vertically, on the left-hand side, with four. With the "portable" cast-iron base plate the machine weighed a considerable 600 kg (1320 lbs) a figure that rose, when mounted on the cast box stand, to 825 kg (1715 lbs). Also available for both stands, but at extra cost, was a storage unit - its three drawers running on rollers and so able to take a considerable weight of tooling and accessories. For milling and co-ordinate drilling work a very strong and heavy (110 kg/242 lbs) screw-feed compound slide was listed. This had a 520 mm x 280 mm table with three T-slots, 320 mm of longitudinal travel and 300 mm in traverse. In addition to the expected chucks, boring heads, cutter holders and Morse adaptor sleeves a number of useful accessories and options were offered including: a longer vertical column that gave 1030 mm of clearance beneath the spindle nose; a 170 mm thick raiser block to sit under the vertical column mounting flange; a spring-return attachment for the automatic retraction of the spindle (a special key was needed to tension the spring) and, only useable in conjunction with the spring-return accessory) the previously-mentioned an automatic release for the power down-feed. If any reader has a UB2, any experience of using one or an instruction book or , the writer would be interested to hear from them. More UB2 pictures here and here
|
|
|
|
|
|
|
|
|
|
|
|
|
|
 |
|
|
|
|
|
 |
|
|
|
|
|
 |
|
|
|
|
 |
|
|
|
|
|
 |
|
|
|
|
|
|
Drilling into an awkwardly positioned flange
|
|
|
|
|
|
|
|
 |
|
|
|
|
|
|
Drilling into a confined space
|
|
|
|
|
|
|
|
 |
|
|
|
|
|
|
In use as a mobile production unit on assembly work
|
|
|
|
|
|
|
|
|
|
|
|
|
|
 |
|
|
|
|
|
|
Machine-tool assembly - a radial-arm drill base being drilled to match its floor stand
|
|
|
|
|
|
|
|
 |
|
|
|
|
|
|
Extended column model in use
|
|
|
|
|
|
|
|
 |
|
|
|
|
|
|
|
|
|
|
|
 |
|
|
|
|
|
|
Oerlikon trepanning head - the Val-Cut - able to cut out rings and profiles up to 250 mm diameter and 30 mm deep in steel
|
|
|
|
|
|
|
|
 |
|
|
|
|
|
|
An example of the extreme angle to which the head could be set
|
|
|
|
|
|
|
|
|
|
|
|
|
|
|
|