 |
 |
 |
 |
 |
 |
 |
 |
 |
 |
 |
 |
 |
 |
 |
 |
 |
 |
 |
 |
 |
 |
 |
 |
 |
 |
 |
 |
|
|
|
|
|
|
|
|
|
|
|
|
|
|
|
|
|
|
|
|
|
|
|
|
|
|
|
|
|
|
|
|
|
|
|
|
|
|
|
email: tony@lathes.co.uk Home Machine Tool Archive Machine-tools Sale & Wanted Machine Tool Manuals Catalogues Belts Books Accessories
lathes.co.uk "Autometric" Horizontal Jig Borer Autometric Machine Tool Co, Meyer, Kearney & Trecker
Catalogs for the Autometric are available
It is uncertain which Company first manufactured the "Autometric" horizontal jig borer. Two catalogs have been discovered which show that the first may have been by the aptly named "Autometric Machine Tool Co. of Ninth Street and Dwight Way, Berkeley, California and then by the "Meyer Mechanical Laboratory" of 1811 Sacramento Street, San Francisco - though the latter might just have been a distributor.. The Autometric jig was built initially in two models, the "A" and "B", with production appearing to have begun in 1940 or 1941 and with later models produced by the milling machine maker Kearney & Trecker. The K & T model differed in a several ways from the original and was to be made, eventually, in a variety of different forms and sizes - as was a vertical version. The American machine might have been inspired by the remarkable pre-WW2 German Koelsh-Beichle Combined Universal Die Milling Machine, this being patented in Germany and the United Kingdom during 1932 to 1935. In the UK the machine was copied, or badged, by Excel and on sale as early as 1931 with the German-made versions staying in production until the late 1960s - obviously filling an important if niche section of the machine-tool market. As the writer has copies of Autometriccatalogues in his collection sourced by a long-established machine tool dealer, there is a strong possibility that examples of the Autometric must have been sent to the UK during WW2 (though one has yet to emerge). They were definitely sent to Australia - one from the Small Arms Factory in Lithgow, New South Wales carries a badge proclaiming, "This Equipment is the Property of Ministry of Munitions Commonwealth of Australia" with the supplier's triangular badge reading, "Moore machinery of Los Angeles and San Francisco". Model A Of what must surely be a unique arrangement, the Autometric - the name was intended to suggest "self-measuring" - was arranged in the manner of a lathe with its bed and headstock made from a normalised casting and formed as one integral unit. Heavily ribbed on the inside to aid rigidity, it was further protected from distortion by being arranged to contact the floor on a three-point housing. Headstock The headstock did not, like a conventional jig borer, contain a cutting head; instead, it held a front-facing, 14-inch diameter rotary table which, in its central position, enabled work up to twenty-four inches in diameter to be held in its six T-slots. The head was held on a pair of vertical steel bars and was driven using a two-stage set-up using multi-step V-pulleys. The periphery of the table was engraved at 1/2° intervals and provided with a vernier scale that allowed settings to an accuracy of one minute of arc. Rotating in super-precision, pre-loaded, double-row roller bearings by SKF, the table could be both elevated through a range of ten inches and rotated either by hand through worm-and-wheel gearing or under power, four speeds being provided of 30, 78, 170 and 437 r.p.m. Bored through to clear 1.5", the central hole through the table was tapered (at least on early models) by 5/8" per foot. When the hand feed was engaged - by releasing a control on the machine's end face and lifting the handwheel - the drive to the motor was disengaged and so turning the wheel rotated both the wheel and its motor. Hence, as there was no interlock to prevent the motor from starting when the worm and wheel were engaged, the operator had to be especially careful on this point if the gearing was not to be wrecked. Bed Offset towards the front of the main casting in order to provide an open space for the operator, the bed ways consisted of two bars, hardened to Rockwell 62-63, ground, lapped and supplied with automatic lubrication. The cast-iron saddle, screw-driven by hand or power through a maximum travel of 16 inches, was fitted with hardened and ground steel bushes, frozen into their housings at 90°F below zero. Hand-feed was at the rate of one inch per revolution of the carriage-mounted handwheel and rate of power feed, from a 1/5th h.p. motor, infinitely variable from 0 to 3.5 inches per minute. With the feed motor switched on, engagement was by a small lift-and-lower lever positioned half-way down the front face of the headstock. The feed rate was varied by a small dial low down on the front face of the headstock - though on the K & T versions the control was moved to the end of the bed. It appears that the variable-speed gearbox was of the swash-plate type (a "ball variator") - interestingly, on the version used here (certainly on K & T models), turning the rate down to zero and then rotating the dial further, reversed the feed direction. In order to provide long-lasting accuracy, the holes in the main casting that accepted the bed bars and other fittings were bored using what the makers described as "align bore fixtures" - in other words, a form of jig - and were first machined with two roughing cuts and then the casting allowed to season and stabilise. After this process - which was for an unstated length of time - two further finishing cuts were made using a second set of boring bars, the accuracy achieved being 0.0004" in 30 inches. The mounting holes were not bored parallel but tapered 9°, the bed and other bars being locked in place by split, tapered bushes. It appears that there was no need for any form of adjustment to the bed or saddle ways - no gib strips or other fittings were used - and the consequent easy, stick-free (automatically lubricated) movements would certainly have helped the operator to achieve high-quality results. Continued below:
High-resolution pictures - may take time to open
|
|
|
|
|
|
|
|
|
|
|
|
|
|
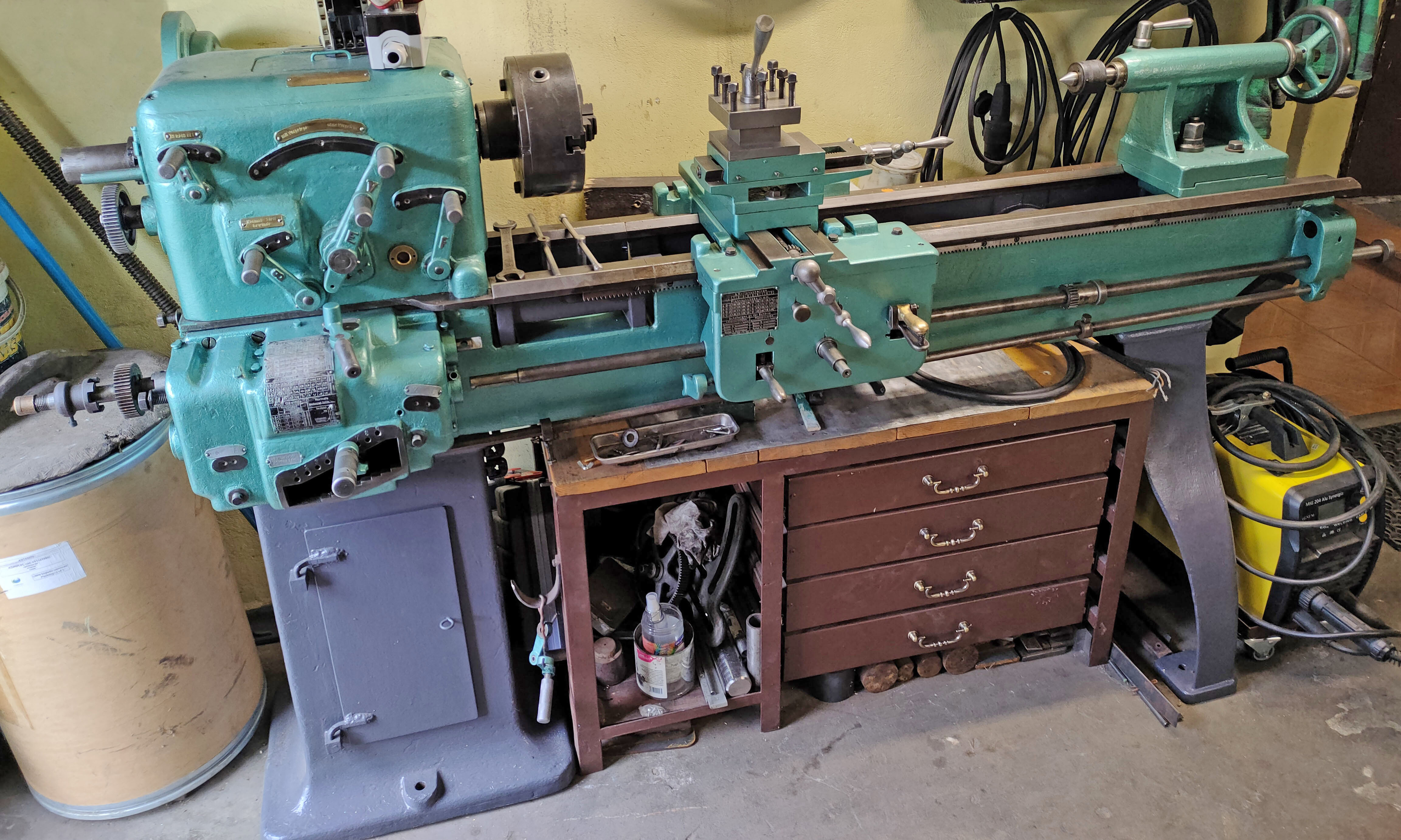 |
|
|
|
|
|
|
Continued: Boring Spindle Head Mounted on the saddle, and also running on two hardened and ground steel bars, was a 16-inch-travel cross slide (ribbed at the front, underside and rear for rigidity), that held a rotary table topped by a high-speed boring spindle held on ways along which it could be driven by a hand-operated screw-feed through five inches of travel - adjustment of fit being by a conventional gib strip with five closely-spaced adjustment screws. The rotary table was equipped with self-equalising clamps and allowed straight, angular and taper boring; the whole of the assembly was claimed by the makers to be, "..hand scraped to perfect fit and alignment". Using draw-in collets to hold cutters or micrometer-equipped boring heads, the spindle was driven by V-belt from a specially designed, small-frame, 1/3rd h.p. motor with a balanced armature - the normal electrical specification being 220 volts, 3-phase on 60 cycles. The simple electrical switchgear comprised three toggle-type on/off switches on the front face of the headstock labelled, left to right as: Rotary Table, Feed and Spindle. Ten spindle speeds in geometric progression were provided, those on the Model A running from 294 to 2350 r.p.m. and on the Model B from 100 to 2350 r.p.m. Radial loads were taken, as on the headstock rotary table, by super-precision, pre-loaded, double-row roller bearings by SKF, and end thrust by ball races. The result of the drive's arrangement - as there was no gear train involved - was claimed to be a particularly smooth-running assembly. Instead of being housed in a moveable quill, the spindle was fixed in its housing with the entire carriage moved to apply the cutting feed on the boring of straight holes - so ensuring that the cutting tool was always supported in the most rigid way possible. When boring at an angle, the carriage was locked, the rotary table set to the desired and the spindle driven forwards by its handwheel. However, when boring a tapered hole, or boring large holes, the spindle was locked and the rotary table on the "headstock" spun under power and the carriage feed applied by hand. Although all jig borers are built to the very highest standard of accuracy, to perform properly they need suitable positioning and measuring systems. A good example of this is to be found in Switzerland where the Geneva-based SIP company had been established in 1862 to produce scientific apparatus and precision measuring machines and instruments. After some confusion from the French-based International Bureau of Weights and Measures - who kept the "master metre" bar and two witness bars in their vaults, but seemed unable to provided subdivided replicas - SIP was called upon to produce working standards for the International Bureau, the Bureau of Standards in Washington and the National Physical Laboratory in Teddington, England as well as other important international metrological institutions. The result was a high-precision steel ruler - a standard scale - by which other length-measuring instruments could be calibrated. With this background SIP then moved into machine-tool production, their first effort being a watchmakers' "Pointing Machine" developed between 1910 and 1919 - a device that proved to be the immediate forerunner of the now ubiquitous jig borer. If you are interested in how these machines developed, a close reading of the introductory SIP page will provide some extra useful details. Continued below:
|
|
|
|
|
|
|
|
|
|
|
|
|
|
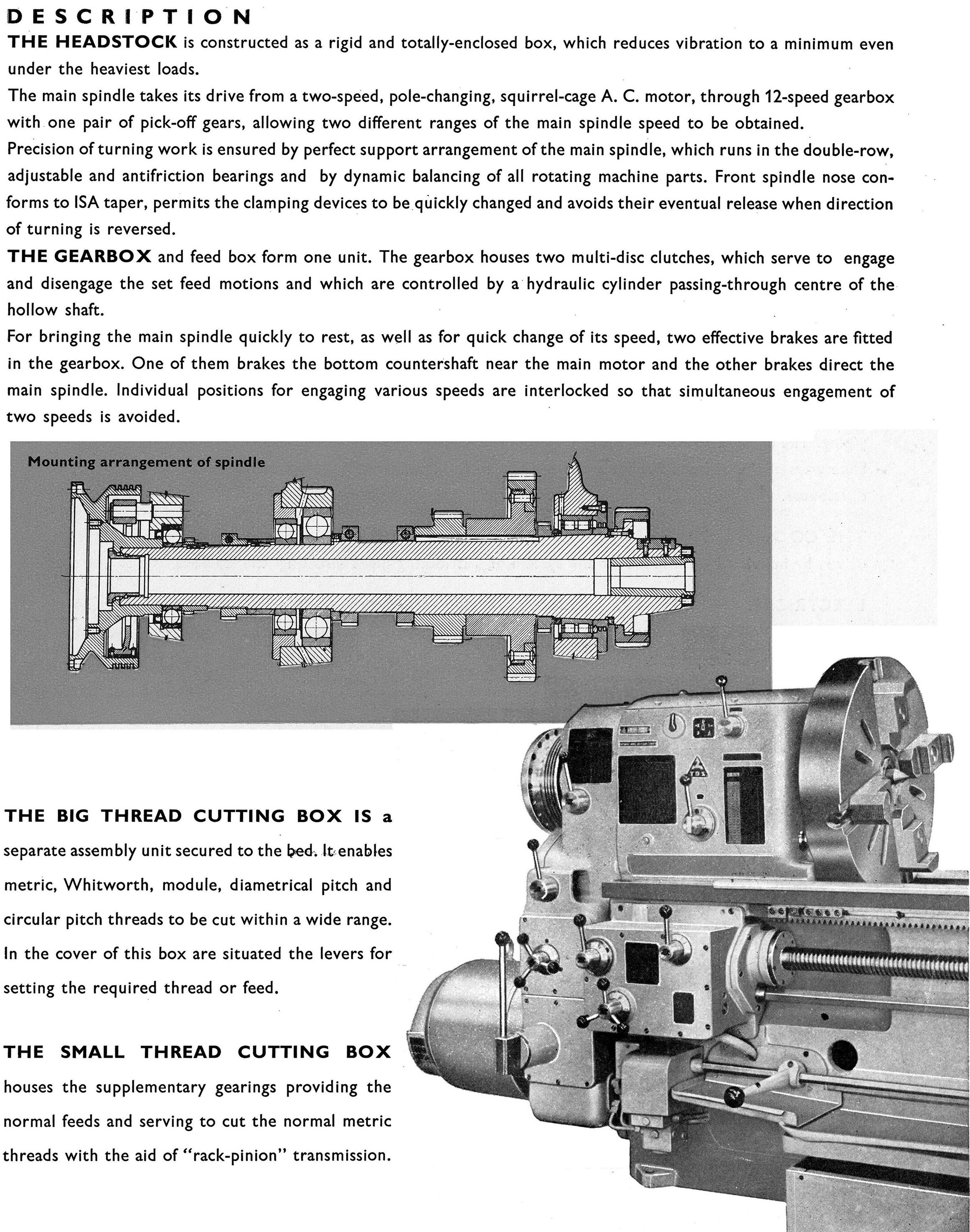 |
|
|
|
|
|
|
Continued: Setting and Measuring On the Autometric, the setting of a job was done with the aid of precision measuring screws fitted with huge, 6-inch diameter, vernier-equipped micrometer dials together with built-in digital mechanical "click" counters - these being used to make the initial settings to one-hundredth of an inch. Passing through long nuts in bronze, formed with a 10 t.p.i. Acme thread and made in tool steel, the measuring screws were hardened to 53-56 Rockwell C Scale, ground and finally finish lapped - the claimed accuracy being to a maximum error of 0.0001" (one ten-thousandth of an inch). On the 16-inch long cross-feed screw, the maximum lead error between any two points was better than 0.00025" and on the 10-inch long vertical lead screw 0.0002" - hence, any job that used the full range of travels could be spaced and bored to within a centre-to-centre accuracy of 0.00025" and smaller jobs to within 0.0001". As the screws were used only for measuring and not for power or hand feeds, the makers stated that, "Tests under operating conditions have shown that the original accuracy will be maintained for years of constant use" - the implied suggestion being that the tests had been run for years but, of course, in reality, this would have been the result of extrapolating whatever wear could be measured over a much shorter time scale. At the start of a job, the rotary table vernier, the vertical and cross measuring counters and micrometer dials were all set at zero - thus establishing baselines from which all other settings could be made, e.g. to make a measurement, the operator first watched the counters to make settings to one-hundredth of an inch, then the micrometer dials to bring the setting to within one-thousandth - and finally the vernier settings to achieve one ten-thousandth. Post-machining inspection (and in some cases initial setting), was simplified by a drop-on surface plate that fitted over the bedways in front of the rotary table. On the table could be placed such measuring and marking equipment as needed, for example, dial indicators, scribing blocks, and height gauges, etc. Meyer Autometric Jig Borer Model B Using the same main body casting, bed and cross slide ways, transmission system and measurement equipment as the Model A, the Model B differed only in having a rectangular table with three T-slots in place of the headstock-mounted rotary table and a fixed, non-swivelling boring spindle. As a result, the machine was, for some applications of even greater accuracy than the Model A - but of course, at the expense of versatility. Equipment and Accessories Supplied as part of the standard equipment with every new Meyer Autometric jig borer was a complete electrical installation; a light unit; a single 1/2" collet, collet adapter and a collet draw tube for the boring spindle; a surface plate (for the model B only to complement the rectangular, headstock-mounted T-slotted table); a bed guard and the necessary wrenches. Available at extra cost was a range of accessories that included: coolant equipment; a range of higher spindle speeds of up to 7000 r.p.m.;collets and collet-retaining draw-tubes; micrometer boring heads and boring bars for the boring spindle; a collet attachment for the rotary table spindle; spindle centering plugs; drill chucks; drill bit sets; various fixtures and work-holding devices and a table to hold the accessories. In addition, the makers offered to provide special spindle speed and feed ranges as well as design and manufacture any work-holding devices required for special jobs. Do you have a Meyer or Kearney & Trecker Autometric? If so, the writer would be pleased to hear from you.
|
|
|
|
|
|
|
|
 |
|
|
|
|
|
|
|
|
|
|
|
 |
|
|
|
|
|
|
Straight boring using a micrometer boring head
|
|
|
|
|
|
|
|
 |
|
|
|
|
|
|
Boring at an angle using a micrometer boring head
|
|
|
|
|
|
|
|
 |
|
|
|
|
|
|
Inspecting completed job using the drop-on surface plate and a dial test indicator
|
|
|
|
|
|
|
|
|
|
|
|
|
|
 |
|
|
|
|
|
|
Some of the accessories and work-holding devices available from the makers
|
|
|
|
|
|
|
|
 |
|
|
|
|
|
|
Using the same main body casting, bed and cross slide ways, transmission system and measurement equipment as the Model A, the Model B differed only in having a rectangular table with three T-slots in place of the headstock-mounted rotary table and a fixed, non-swivelling boring spindle. As a result, the machine was, for some applications of even greater accuracy than the Model A - but of course at the expense of versatility.
|
|
|
|
|
|
|
|
 |
|
|
|
|
|
|
|
|
|
|
|
 |
|
|
|
|
 |
|
|
|
|
|
 |
|
|
|
|
|
|
|
|
|
|
|
 |
|
|
|
|
|
|
|
|
Badges on the Meyer Autometric jig borer supplied to Australia during WW2
|
|
|
|
|
|
|
|
|
|
|
|
|
 |
|
|
|
|
|
|
|
|
The simple electrical switchgear comprised three toggle-type on/off switches labelled, left to right as: Rotary Table, Feed and Spindle. The control bottom right with the pin bar through it controlled the rate at which the carriage was driven along the bed.
|
|
|
|
|
|
|
|
|
|
|
|
|
|
|