 |
 |
 |
 |
 |
 |
 |
 |
 |
 |
 |
 |
 |
 |
 |
 |
 |
 |
 |
 |
 |
 |
 |
 |
 |
 |
 |
 |
 |
 |
 |
 |
 |
 |
 |
 |
 |
 |
 |
 |
 |
 |
 |
 |
 |
 |
 |
 |
 |
 |
 |
 |
 |
|
|
|
|
|
|
|
|
|
|
|
|
|
|
|
|
|
|
|
|
|
|
|
|
|
|
|
|
|
|
|
|
|
|
|
|
|
|
|
|
|
|
|
|
|
|
|
|
|
|
|
|
|
|
|
|
|
|
|
|
|
|
|
|
|
Imported from Germany by Løvener Mohn A.S., a Norwegian machine-tool dealer, the Matra shown below was purchased by the Drøbak (Polar) Research Station, a division of the University of Oslo. On the dealer's shield is stamped: Auftrag 54934 which, translated as Order No. 54934 could well be machine No. 9, week 49 of 1934 - or machine No. 54 of September, 1934. As the design of the lathe matches many produced during the period 1925 to 1940, either interpretation would seem to be a reasonable supposition. Although no ordinary lathes were advertised with the Matra name before WW2 (with exception of a special piston lathe*) they did offer, in catalogues from 1935, a range of re-branded lathes manufactured by Fischer, Dolze & Slotta and Alfred Eriksen of Hamburg. The restored lathe below may be by the latter company, the shapes of the half-closed headstock, tailstock, changewheel cover, tumble-reverse control and screwcutting chart all bearing a strong family resemblance to other lathes by them. Erickson were also one of the few companies to offer spindle bore as large as 46 mm Classed as a straightforward, entirely conventional general-purpose workshop lathe, the Matra was selling into a market where many similar examples were being offered by a number of competing German firms including Auerbach, Beling & Lűbke, Ehrlich, See (FSB), Gläss, Schuchardt & Schutte, Karger, Flesch & Stein, Robling and Weisser. Honestly-built, well-proportioned and neatly detailed - and with unusually comprehensive and tight fitting cast-iron guards over the various gears trains - the Matra had a very reasonable capacity for its size: a centre height of 180 mm and with a detachable gap piece that allowed a job 520 mm in diameter and around 180 mm thick to be turned on a faceplate. Whilst most similar British lathes of the time would have had a headstock spindle with a miserably small bore (barely adequate for most regular workshop jobs) on the Matra things were different: running in cap-type bronze bearings the spindle was a massive 64.2 mm in diameter with a 45.5 mm hole - so large that the maker had to provide a step-down 5 Morse to 2 Morse adaptor for regular between-centre work (Erickson, the probable builders, were one of the few companies to list a spindle bore as large as 46 mm on lathes of this centre height). The nose thread was odd: it measured 4 threads per 0.926 inch or 23.54 mm pitch - neither an exact 4 t.p.i. nor a 24 mm pitch. However, almost certainly the intention was 4 t.p.i., the use of a English Whitworth standard thread at that size still being standard practice in German engineering. The backgear reduction ration was set at 1 : 5.5 and a 3-step cone pulley provided, of a proper width, for flat-belt drive. Although originally supplied for drive by a simple remote countershaft, on the back of the bed a machined surface suggests that there would have been provision to mount an integral drive unit, possibly one of the clumsy interim types as shown in the picture of the heavier Matra lathe at the bottom of the page. Drive from headstock to leadscrew was through a tumble-reverse mechanism (well supported by being mounted inboard of the left-hand spindle bearings) and changewheels - of which a generous set of twenty-two was provided, including a 127t metric-translation wheel. The full set comprised: 127-125-120-110-100-95-90-80-70-60-60-55-50-45-40-35-32-30-25-23-22 and 20t. Continued below:
|
|
|
|
|
|
|
|
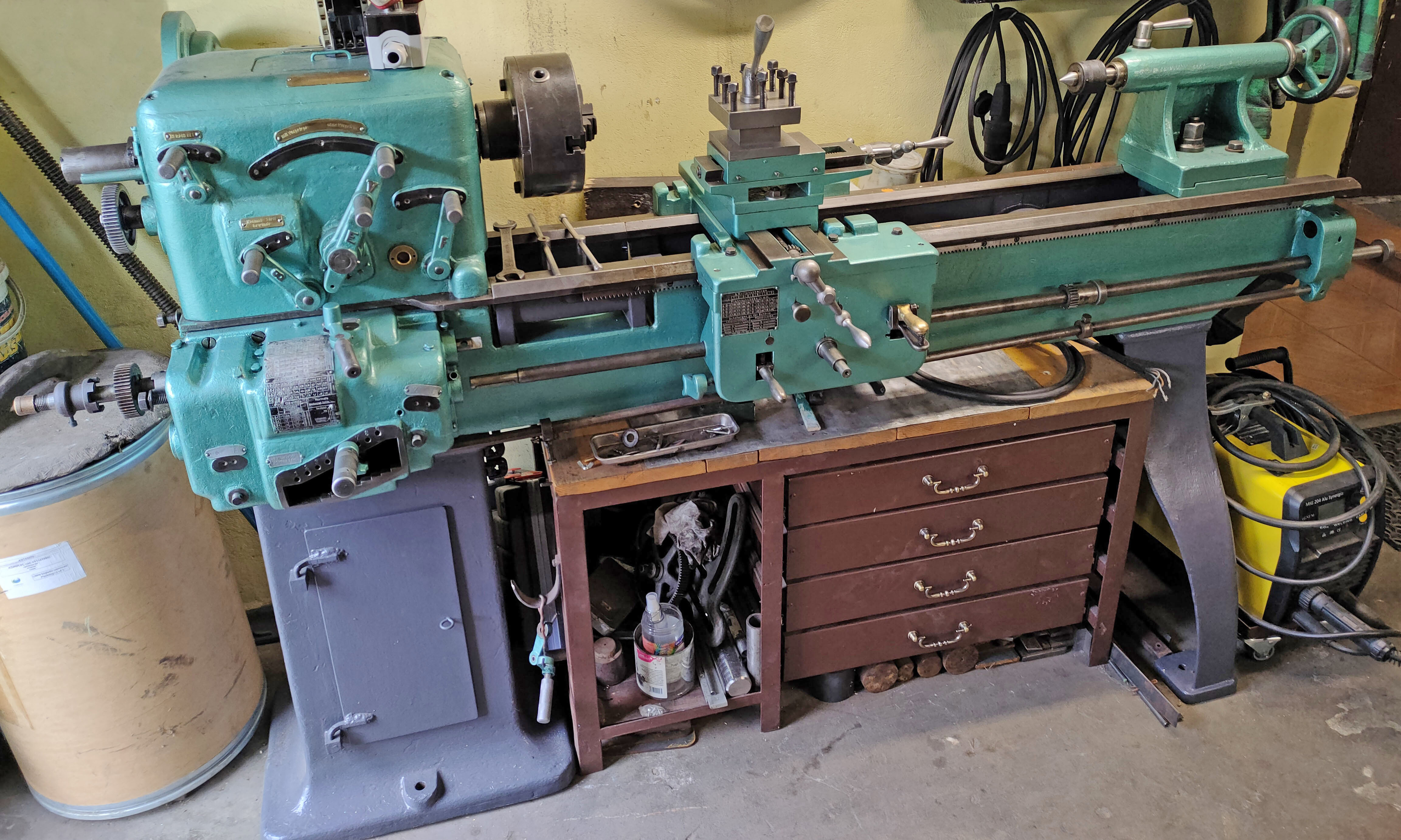 |
|
|
|
|
|
|
|
|
|
Early 1930s German-built Matra lathe. This was an honestly-built, well-proportioned and neatly detailed lathe with unusually comprehensive and tight fitting cast-iron guards over the various gears trains
Continued: Not for Matra the inadequate swing-open cover with no inner guard offered by many other makers: on their lathe the changewheels were completely contained in a proper cast-iron housing that could be locked closed with a screw. Continuing the Whitworth theme the 28 mm diameter leadscrew was threaded 8 t.p.i. and slotted, in the usual way, to provide a drive for the power cross feed - this being activated by pulling out a knob on the face of the apron to engage a pair of spur gears that were, in turn, driven by bevel gears - one of which was turned by key riding in a slot in the leadscrew. There appears to have been no way of instantly disengaging the feed, other than by pushing the knob in, a process that may have been hampered (especially if the cut was deep) by the mechanism "winding up". In addition to its simple (but effective) power-cross-feed mechanism, a further clue exist in the carriage assembly to show that this lathe was a steady development of a 1920s design: running on flat and V-ways, the saddle was relatively thin, with just two perfunctory cast-in braces and very deep front to back in order to carry an apron that was mounted well out from the bed. Not only was the leverage between leadscrew clasps nuts and bed greatly exaggerated by this design, but the apron was bolted to a section of the saddle that was remarkably thinned over its outer section. Although the full depth of the casting was maintained over the cross slide ways, this reduction of section at each side (and especially at the point where the transverse T-slots stopped short at the front) can have done little to enhance the rigidity of the assembly - or the usefulness of the saddle as a boring table. The carriage handwheel provided 54 mm of travel per revolution and could, for safety reasons, be pulled out to disengage the drive. Matra lathes of later years incorporated some noticeable improvements in the carriage area: the saddle was much heavier with a deep bracing section reaching down between the bed ways whilst the front was shortened and redesigned so that the apron could be fitted so that its inner section was underneath the front bed rail. A wind-in clutch engagement was also fitted to engage the power feeds - a safety mechanism that would have been appreciated by less experienced operators. Fitted with tapered gib strips secured by adjustment screws at both ends, the compound slide was a well-engineered assembly - with the cross slide having a V-way whose depth appears to have been noticeably greater than usual. Decent zeroing micrometer dials were fitted, with particularly clear engraved markings and large, knurled finger grips to change the setting. Driven by 16 mm diameter feed screws, with a split bronze nut that could be adjusted to remove backlash, the cross-slide had a travel of 210 mm and the top slide 140 mm. Fitted with a self-eject No. 2 Morse taper centre, the tailstock barrel was large enough for a No. 3 to be fitted. The tailstock barrel lock was especially powerful, having a long handle and a proper split-cylinder compression clamp. If you have a Matra machine tool of any kind the writer would be pleased to hear about them. *Marx & Traube GmbH in Frankfurt a. Main (Matra for short) specialised in tools and machines for car engine repairs. Before WW2 they offered valve-seat cutters, valve grinding machines, cylinder-boring and honing machines, hand-drills and a special piston lathe and piston grinding machine. The clever idea behind the last two devices was to machine worn-out bores to just the minimum amount required and then turn or grind a single size of "oversize" pistons to fit. However, this was an idea that did not catch on, repair shops preferring to buy oversize pistons in set sizes to which, of course, they could bore the cylinders to suit. After WW2 Matra offered, as an addition to their pre-war program, a special fine-boring machine able to machine connecting rods and motorcycle cylinders - and another for boring the main bearings in car cylinder blocks. All these specialised items were designed, and constructed, in-house by Matra. However, by the 1960s Matra were producing lathe and had also become machine-tool become resellers, offering big crankshaft grinding machines that closely resembled those manufactured by the Danish AMC Schou Company. An interesting Matra rebuild story: http://danny.mp.willems.googlepages.com/
|
|
|
|
|
|
|
|
|
|
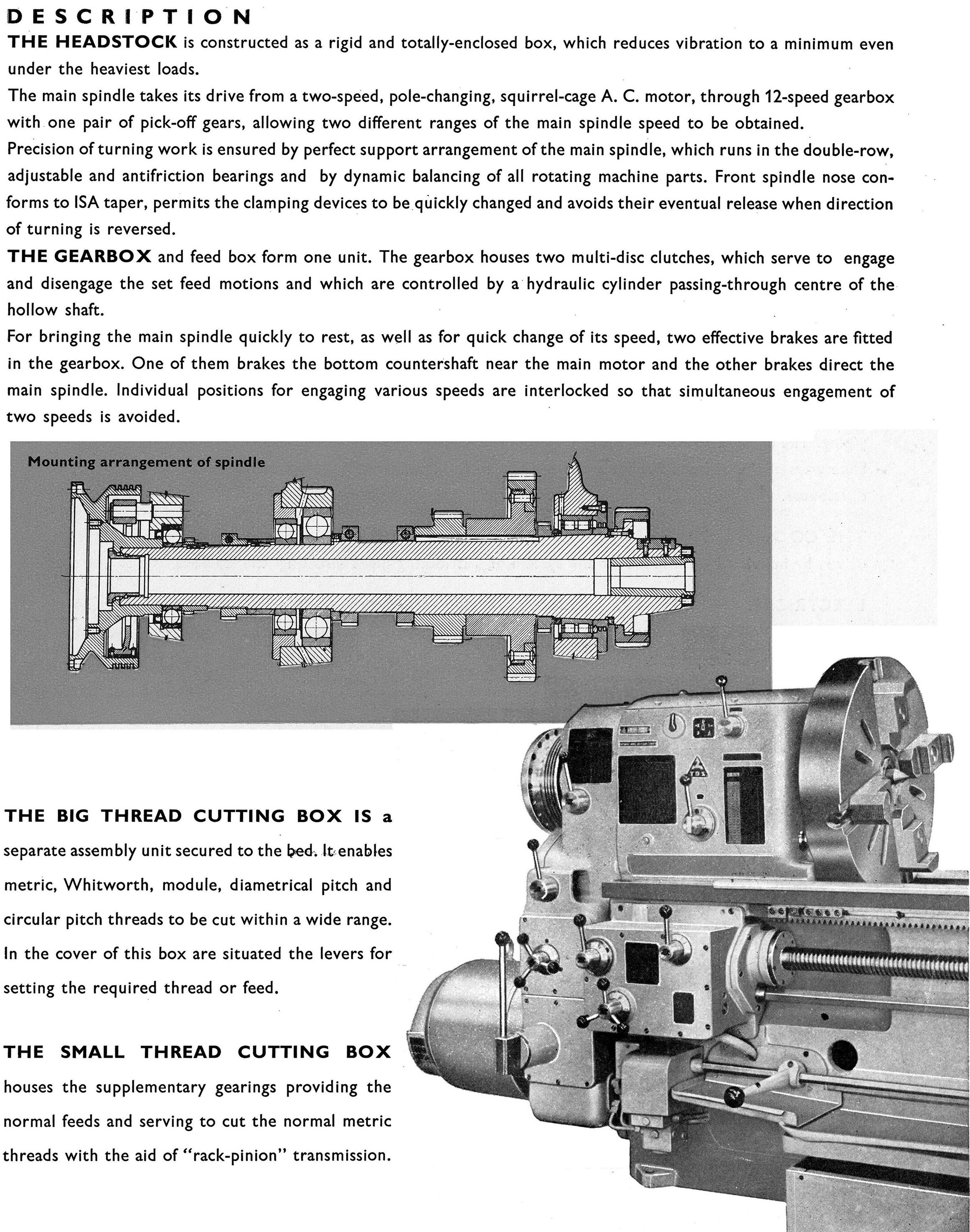 |
|
|
|
|
|
|
|
|
|
The Ericksen "Modena" lathe with a 46 mm bore spindle Although different in detail - though this is a more highly specified lathe, note the many the similarities to Matra version
|
|
|
|
|
|
|
|
|
|
|
|
|
|
|
|
 |
|
|
|
|
|
|
Well braced headstock with wide, 3-step flat belt drive
|
|
|
|
|
|
|
|
 |
|
|
|
|
|
|
Not for Matra the inadequate swing-open cover with no inner guard offered by many other makers: on their lathe the changewheels were completely contained in a proper cast-iron housing that could be locked closed with a screw. The hole in the headstock end standard leg) shows that at some stage the lathe would have been available with a treadle-powered flywheel drive.
|
|
|
|
|
|
|
|
 |
|
|
|
|
|
In addition to its comparatively crude power-feed mechanism, a further clue exist in the carriage assembly to show that this lathe was a steady development of a 1920s design: running on flat and V-ways, the saddle was a constant thickness front to back (no central bracing) and very deep front to back in order to carry an apron that was mounted well out from the bed.
|
|
|
|
|
|
|
|
|
|
|
|
|
|
 |
|
|
|
|
|
 |
|
|
|
|
|
|
The carriage handwheel provided 54 mm of travel per revolution and could, for safety reasons, be pulled out to disengage the drive.
|
|
|
|
|
|
|
|
 |
|
|
|
|
|
|
Fitted with tapered gib strips secured by adjustment screws at both ends, the compound slide was a well-engineered. The slides were driven by 16 mm feed screws, with a split bronze nut that could be adjusted to remove backlash
|
|
|
|
|
|
|
|
|
|
|
|
|
|
 |
|
|
|
|
|
|
The saddle was relatively thin, with just two perfunctory cast-in braces and very deep front to back in order to carry an apron that was mounted well out from the bed. Note the bevel gears to drive the power-cross-feed mechanism.
|
|
|
|
|
|
|
|
 |
|
|
|
|
|
|
Appropriate for a lathe used at the Norwegian Polar Research Institute, a box of turning tools marked Nansen was found with the lathe
|
|
|
|
|
|
|
|
 |
|
|
|
|
|
|
The tailstock had a No. 2 Morse taper - though there was sufficient diameter for a No. 3 to be fitted. Note the especially power barrel lock
|
|
|
|
|
|
|
|
 |
|
|
|
|
|
|
Metric and Imperial screwcutting chart
|
|
|
|
|
|
|
|
|
|
|
|
|
|
 |
|
|
|
|
|
|
Matra lathes of later years incorporated some noticeable improvements in the carriage area: the saddle was much heavier with a deep bracing section reaching down between the bed ways whilst the front was shortened and redesigned so that the apron could be fitted so that its inner section was underneath the front bed rail. A wind-in clutch engagement was also fitted to engage the power feeds - a safety mechanism that would have been appreciated by less experienced operators.
|
|
|
|
|
|
|
|
|
|
|
|
|
|
 |
|
|
|
|
|
|
Popular on some American lathes of the 1920s and early 1930s this interim type of self-contained drive system was cumbersome, expensive to make and not, with its comparatively short belt run, especially efficient. Note, in the background, the Matra valve grinder
|
|
|
|
|
|
|
|
 |
|
|
|
|
|
|
Matra D50 of the 1960s. 200 mm x 1150 mm
|
|
|
|
|
|
|
|
 |
|
|
|
|
|
|
|
|
|
Matra MDR-20 of the 1960s. 300, 350 or 400 mm x 1000 to 6000 mm
|
|
|
|
|
|
|
|
|
|
|
|
|
|
|
|
 |
|
|
|
|
|
|
|
|
|
|
|
 |
|
|
|
|
|
|
Matra MDR-22 and MDR-25. 220 or 250 mm x 1000, 1500 or 2000 mm
|
|
|
|
|
|
|
|
|
|
|
|
|
|
|
|