 |
 |
 |
 |
 |
 |
 |
 |
 |
 |
 |
 |
 |
 |
 |
 |
 |
 |
 |
 |
 |
 |
 |
 |
 |
 |
 |
 |
 |
 |
 |
 |
 |
|
|
|
|
|
|
|
|
|
|
|
|
|
|
|
|
|
|
|
|
|
|
|
|
|
|
|
|
|
|
|
|
|
|
|
|
|
|
|
|
|
|
|
|
|
|
|
Maho, now trading as DMG Moro making advanced CNC machines, was a German company, founded in 1920 by five mechanics in the Bavarian alpine village of Pfronten. Their original products were drafting instruments - hence their logo, a pair of dividers - and planimeters, pantographs and other high-precision mathematical instruments. Added to their range in the years before World War 2 were watchmaker's lathes, bench drilling and tapping machines and simple lever-operated milling machines intended for light production use. Although manufacture of precision machine tools began at their Pfronten-Steinach, Bayer.Allgäu factory during the WW2, it is likely that most of this work would have been sub-contracted from companies more established in the field - and it was not until 1950 that the Maho launched their first universal precision miller, the now-rare SK250. Designed along established Theil and Deckel-like lines (and eventually as copied by many other makers*) the SK had a ram head and a vertical T-slotted knee that was able to mount a variety of horizontal tables and other special fittings. This arrangement gave the machines a most useful versatility it being possible, for example, to mount the crankcase from a small engine on the vertical table and line-bore its main bearing. From the 1950s to the 1980s the company steadily developed this range of millers, but always remained faithful to the original design concept. Later, by the addition of NC and then CNC controls, their life was considerably extended and general performance immeasurable improved - one particularly successful model, the £50,000 MH600E of 1990, being the start of this accelerated process. In 1990, MAHO AG hade stablished a relationship with Thiel to become MAHO Seebach GmbH with their factory beginning production on the 3rd October, 1990. In 1992 there was a takeover of Thiel (FRG) production from Emstal - a town near Kassel - and in 1993 a further fusion of precision German machine-tool engineering when the Deckel Company (Munich) joined with the Maho Company of Pfronten to become Deckel-Maho. By 1994 Gildemeister AG (Bielefeld) had taken over Deckel-Maho and in 1995 manufacturing was moved from factories in Munich and Pfronten and concentrated in Seebach. The original 1950 Maho SK250 was followed by the MH Series, a range of very similar appearance and a design that was to be the basis of the company's success for the next three decades. The MH was made in three sizes: the rather similar MH600 and MH700 models and the very much more massive MH800 - all were made in early and late versions with the first being of typically 1940s and 1950s appearance with smooth, rounded castings and the later echoing design clues from the late 1960s to 1970s with angular styling. The very earliest versions can be recognised by an exposed electric motor mounted at floor level on an adjustable plate on the 600 and, on the 700, by a motor mounted inside the base of the column. Later versions of both machines had external, rear-mounted motors covered with a smooth, cast-aluminium cover and, instead of a simple model badge on the front of the knee, tended to carry a confusion of markings with the Maho name on either the right-hand face of the column, missing altogether, or combined with riveted-on badges proclaiming the name of the well-known export agents (who had premises in England) "Hahn & Klob" of Stuttgart. Continued below:
|
|
|
|
|
|
|
|
|
 |
|
|
|
|
|
|
|
|
|
1950 Maho SK250 precision universal milling machine
|
|
|
|
|
|
|
|
|
|
|
|
|
|
|
|
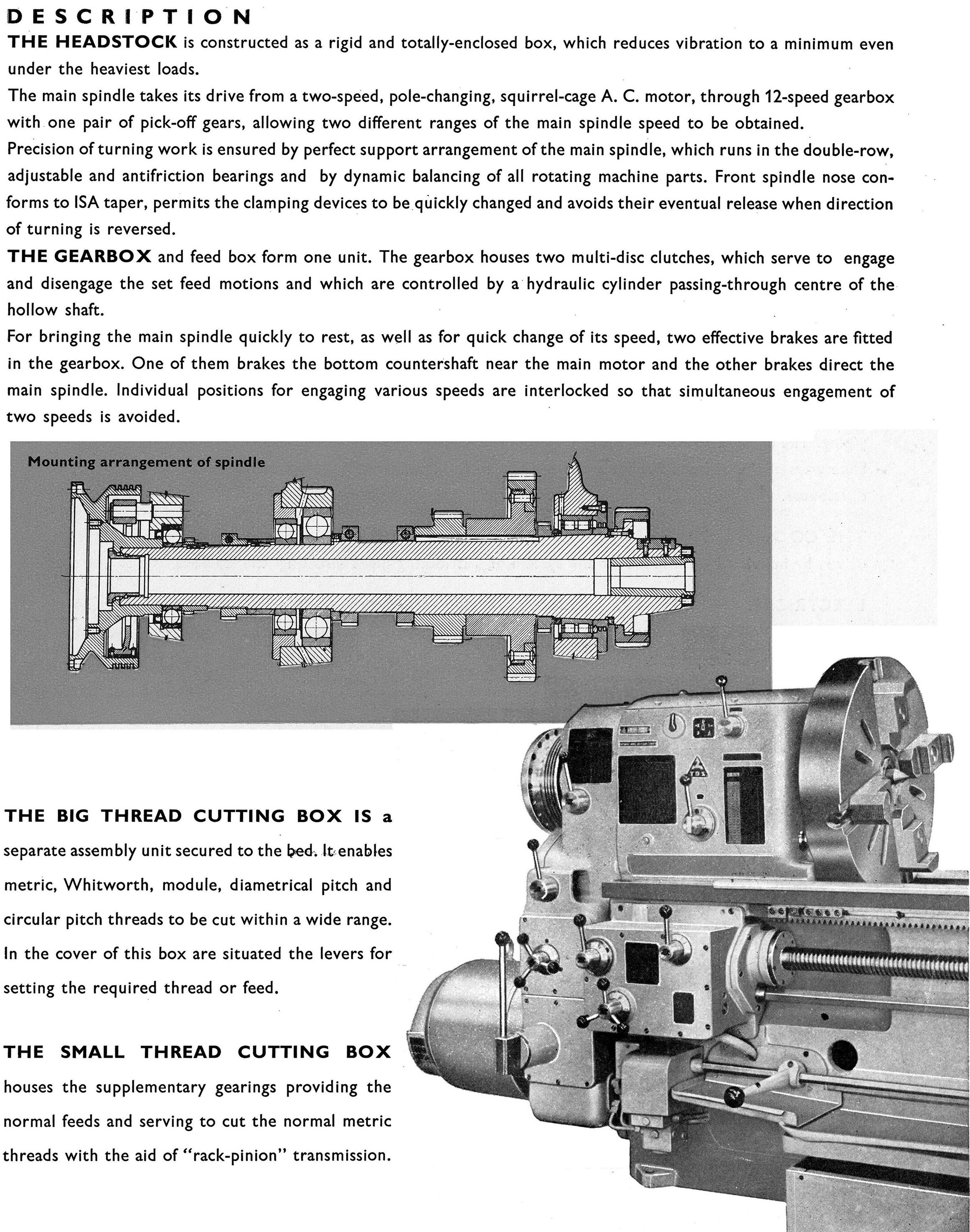 |
|
|
|
|
Early Maho 600 with exposed electric motor, a heavy-duty "Fixed Angular" horizontal table and the later type of standard vertical head with a domed front.
|
|
|
|
|
|
|
|
|
Continued: The design principles behind this type of miller centred around the use of a knee with a vertical T-slotted table, this able to mount a range of other tables - plain, plain tilting or plain swivelling and, most useful of all, one that could be tilted, inclined and swivelled. In addition, a variety of dividing heads, spiral-milling attachments and punch-milling accessories could also be fitted. The knee was arranged to be moved by hand or power longitudinally and vertically with the traverse (in-and-out) motion being provided by a head mounted in a slideway formed on top of the main column. Head travel was commonly controlled by a handwheel positioned in the top right-hand corner of the main column's right-hand face. Occasional, on larger models, the head could be moved under power as well, with the very largest versions (and not all companies making similar machines followed suit) always having this facility. Some versions, like the later Maho MH800 models, even grouped the complete spindle-drive mechanism within the head and so removed the need for a motor at the back of the column and a head-drive gearbox within it. The Mayo was made in three sizes: MH600, MH700 and MH800 - all available in early and late versions with the first being of typically 1940s and 1950s appearance with smooth, rounded castings and the later echoing design clues from the late 1960s with distinctly different and very angular lines. These notes concern only the earlier models, with data for the later being found in another chapter. The basic construction of the two smaller models was identical (the MH800 is described separately) with the top sliding housing contained a hardened and ground spindle (with a generously-large 4 Morse nose) fastened to the middle of which was a gear that engaged with (and slid along as the head position changed), a long column-mounted drive gear beneath it. The oil-splash lubricated drive gearbox, built into the top of the main column, held hardened gears (ground on their flanks), and provided 18 spindle speeds running from 65 to 1000 r.p.m in horizontal mode and 100 to 1560 r.p.m. in vertical. Motors became slightly more powerful as the years passed; on the MH600 the early 2-speed 1.2/1.9 kW motor (exposed at the back) being replaced by a 1.6/2.5 kW enclosed unit and on the MH700 the original 1.4/2.2 kW by a 1.8/2.6 kW model. With a 50 Hz supply all motors ran at 700 and 1400 r.p.m. or 850 and 1700 r.p.m on 60 Hz. Drive from motor to gearbox was by 3 V-belts, with spindle-speed changes made by electrical push-buttons and two levers protruding from the periphery of a common boss on the right-hand face of the column. Continued below:
|
|
|
|
|
|
|
|
 |
|
|
|
|
|
|
Earliest Maho 700 with the motor mounted inside the (ventilated) column base and a 'narrow-body' vertical head
|
|
|
|
|
|
|
|
|
|
|
|
|
|
|
Continued: Four different vertical "heads" were available: one just a long casting to hold the bracket required to support the end of a horizontal milling cutter arbour, a standard vertical, a high-speed vertical and a slotting. The standard vertical head for the 600 and 700 models was built in early and late versions, the former identifiable by its slender body and the latter by its barrel like, run-to-seed, middle-age spread. Unlike those makers who made a direct copy of the Deckel, on the Maho the heads were not mounted on top of the sliding housing, but instead fitted into it - each being equipped with a 280-mm long by 90-mm diameter boss made a close fit into a hardened and ground bore arranged above the horizontal spindle line. Inside the thick, rotating flange on the end of the head was a worn-and-wheel mechanism, operated by a micrometer-graduated handwheel, this allowing the head to be inclined to a precise angle (strangely, this useful - and for class of miller unique refinement - was referred to only obliquely in Maho publicity literature). Once set, the head angle was clamped by two bolts on the MH600 and four on the MH700. The standard and slotting heads were driven by a pinion on the end of a shaft that passed right through their mounting bosses, the gearing being arranged so as to increase the speed of the driven shaft in comparison with the driver. The standard vertical head could be swivelled through 360-degrees and was fitted with a short (70mm) travel quill operated by either a knurled-edge handwheel on the left, or a detachable lever or the right. Like the Deckel, the movement of the quill was by rack-and-pinion, an arrangement that gave a very coarse feed and limited the sensitivity that could be employed by the operator - a situation the writer found made worse when trying to use the ludicrously small handwheel. Even the spindle lock was awkward to use with a loose, square-headed spanner having to be found to turn a locknut that seemed stiff and unresponsive. Although the Maho vertical head ran faster than that on the original Deckel (and most of the other copies) it was still too slow to allow the use of really small diameter cutters - a type so often necessary in fine tool and die work. To address this shortcoming the makers offered a high-speed head, able to be swivelled 90-degrees either side of central and fitted with its own motor - on early models this was a 0.5 kW 3400 r.p.m. unit while later versions had one of the same power but running at 2800 r.p.m. In both cases, the resulting six spindle speeds were listed as identical, the range spanning 1900 to 6000 r.p.m. Unusually for a head intended to be used for fine, precision work by a skilled operator, there was no worm-driven fine feed, instead the same quick-action lever and handwheel used on the standard head was fitted, though with an additional 10 mm of quill travel. If only the Maho designers had examined other compact vertical millers available at the time - e.g. Bridgeport, Centec, Tom Senior, Cincinnati Toolmaster or Arboga, etc. - they would have seen that engineering both types of feed into one unit was not difficult. Both vertical heads had a maximum collet capacity of 17.5 mm and, while those on the MH600 were restricted to hand-feed only, the MH700 could be specified (providing the extra cost had been paid for "rapid" knee feeds) with automatic fine and rapid feeds to the head travel. Continued below:
|
|
|
|
|
|
|
|
 |
|
|
|
|
|
|
Later Maho MH700 with external, covered motor and slideways protected by bellows.
|
|
|
|
|
|
|
|
|
Continued: The knee on both machines could be operated by hand, or under power from an infinitely-variable drive that gave rates of feed from 7 to 250 mm per minute. Longitudinal and vertical feeds on the MH600 were 320 and 300 mm respectively and on the MH700 400 and 370 mm. As an extra the M700 could be fitted with "rapids" - a mechanism that allowed the knee to be moved back to a start position (both longitudinally) and vertically at 900 mm per minute. For bolting to the knee three different tables were available: plain, tilting and compound tilting. The most rigid, and best suited to heavy stock removal, was the plain type ("Fixed Angular" in the maker's terminology) of 600 mm x 210 mm with 4 T-slots on the MH600 and 700 mm x 295 mm with 5 T-slots on the MH700 (the dimensions all refer to the clamping area, not the overall size). The T-slots were of identical size (12-mm wide) and spacing (45-mm apart) on each model. More versatile than the fixed table (but less rigid) was the "Swivelling and Tilting Angular Table", a model that provided a good compromise between versatility and stiffness. The unit could be tilted 45-degrees either side of horizontal, swivelled 30 degrees on its vertical axis and had the bonus of a transverse feed (by screw) with 130 mm of movement. The table was sized to each model: 610 mm x 220 mm with 4 T-slots for the MH600 and 700 mm x 295 mm with 5 T slots on the MH700. The table that allowed the greatest functionality, but at the expense of being restricted to lighter cuts, was the "Swivelling Tilting and Inclinable" model. As its name suggested this could be moved in a manner identical to the Swivelling and Tilting table but also arranged to tilt in a fore and aft direction through 30-degrees either side of horizontal; however, its versatility was bought at the expense of having to leave off the transverse feed. Fitted with this table (and in combination with a suitable dividing attachment and vertical head) the miller was able to tackle an extensive range of complex machining. A Punch Milling Attachment was also listed - designed to allow the production of intricate shapes on milling cutters and punches - consisting of a chuck mounted on a finely-adjustable slide (itself carried by one of the dividing heads), a graduated glass plate with magnifying lens, a radius gauge, vernier callipers, a "Tesatest" gauge (reading to 0.01 mm), and a centering needle and centering feeler. The Spiral Milling Attachment, with its No. 4 Morse taper spindle driven by changewheels from a gear on the table-feed mechanism, was supplied complete with a tailstock, knee and set of changewheels that enabled it to be adapted for the manufacture of spirally-fluted milling cutters and reamers and also for the production of helical and worm gears and threads (under power) from 3 mm to 2000 mm pitch. With just hand feed the unit was limited to the spiral pitches from 3 to 16 mm. A single maker's Rotary Table was available: 340-mm in diameter it carried a No. 4 Morse taper hole in its centre and could be used for direct or indirect dividing. For the former a ring of 24 holes were provided and for the latter 3 indexing plates supplied as standard. Both the MH600 and MH700 stood just less than 1500-mm tall with a base casting slightly less than 600-mm wide. However, whilst base on the 600 (less the chip tray), was only 720 mm front to back on the 700 it was considerably deeper at 1164 mm. Although compact the millers were very heavily built: with motor and standard equipment the gross weight of the MH600 was 955 kg and the MH700 1265 kg..
|
|
|
|
|
|
|
|
|
|
|
|
|
|
 |
|
|
|
|
|
|
"Swivelling and Tilting Angular Table" fitted to the Model 700 - a good compromise between versatility and stiffness. The unit tilted 45-degrees either side of horizontal, swivelled 30 degrees on its vertical axis and had a 130-mm of transverse movement by a screw feed. *Proof of the type's success - the genus Precision Universal Milling Machine - is evident from the number of similar machines made in various countries including: Austria: Emco Model F3 Belgium: S.A.B.C.A. Model JRC-2 Czechoslovakia: TOS FN Models England: Alexander "Master Toolmaker" and the Ajax "00", an import of uncertain origin. Germany: Hahn & Kolb with their pre-WW2 Variomat model Wilhelm Grupp Universal- Fräsmaschine Type UF 20 N/120 Hermle Models UWF-700 and UWF-700-PH Leinen Super Precision Micro Mill Macmon Models M-100 & M-200 (though these were actually manufactured by Prvomajska); Maho (many models over several decades) Ruhla Rumag Models RW-416 and RW-416-VG SHW (Schwabische Huttenwerke) Models UF1, UF2 and UF3 Thiel Models 58, 158 and 159 Wemas Type WMS Italy: C.B.Ferrari Models M1R & M2R Bandini Model FA-1/CB and badged as Fragola (agents, who also sold a version of the Spanish Meteba). Japan: Riken Models RTM2 and RTM3 Poland: "Avia" and "Polamco" Models FNC25, FND-25 and FND-32 by Fabryka Obrabiarek Precyzyinych Russia: "Stankoimport 676" Spain: Metba Models MB-0, MB-1, MB-2, MB-3 and MB-4 Switzerland: Aciera Models F1, F2, F3, F4 and F5 Christen and Perrin Types U-O and U-1 (Perrin Frères SA, Moutier) Hispano-Suiza S.A. Model HSS-143 Luthy Mikron Models WF2/3S, WF3S, WF-3-DCM & WF-2/3-DCM Perrin Type U-1 Schaublin Model 13 and Model 22 The former Yugoslavia: Prvomajska (in Zagreb with Models ALG-100 and ALG200) Sinn Models MS2D & MS4D "Comet" Model X8130, imported to the UK in the 1970s by TI Comet. Sloane & Chace in the USA produced a miniature bench version and at least five Chinese-built models have also been made, including one from the Beijing Instrument Machine Tool Works. A number of the "clones" merely followed the general Thiel/Maho/Deckel concept whilst others, like Bandini and Christen, borrowed heavily from Deckel and even had parts that were interchangeable. Should you come across any of these makes and models all will provide "The Deckel Experience" - though you must bear in mind that spares are unlikely to be available and, being complex, finely-made mechanisms, they can be difficult and expensive to repair..
|
|
|
|
|
|
|
|
 |
|
|
|
|
|
|
Maho High-speed Vertical Head Although the Maho Standard Vertical Head ran faster than that on the original Deckel (and most of the other copies) it was still too slow to allow the use of the really small diameter cutters so often necessary in fine tool and die work. To address this shortcoming, the makers offered a high-speed head, able to be swivelled 90-degrees either side of central and fitted with its own motor - on early models this was a 0.5 kW 3400 r.p.m. unit while later versions had the same power but running at 2800 r.p.m. In both cases the resulting six spindle speeds were listed as identical, with a range spanning 1900 to 6000 r.p.m. Unusually for a head intended to be used for precision work by a skilled operator, there was no worm-driven fine feed, instead the same quick-action lever and handwheel used on the standard head was fitted - though with an additional 10 mm of quill travel.
|
|
|
|
|
|
|
|
 |
|
|
|
|
|
|
The earliest 'narrow body' vertical head
|
|
|
|
|
|
|
|
|
|
|
|
|
|
 |
|
|
|
|
|
The slotting attachment could be swivelled through 360 degrees, had a stroke variable from 0 to 80 mm and the 18 speeds gave stroke rates from 20 to 316 per minute.
|
|
|
|
|
|
|
|
|
|
|
 |
|
|
|
|
|
|
Maho 700 set up for stub milling
|
|
|
|
|
|
|
|
|
|
|
|
|
|
 |
|
|
|
|
|
 |
|
|
|
|
|
 |
|
|
|
|
|
|
|
|
|
|
|
 |
|
|
|
|
 |
|
|
|
|
|
 |
|
|
|
|
|
|
|
|
|
|
|
|
|