 |
 |
 |
 |
 |
 |
 |
 |
 |
 |
 |
 |
 |
 |
 |
 |
 |
 |
 |
 |
 |
 |
 |
 |
 |
 |
 |
 |
 |
 |
 |
 |
 |
 |
 |
 |
 |
 |
 |
|
|
|
|
|
|
|
|
|
|
|
|
|
|
|
|
|
|
|
|
|
|
|
|
|
|
|
|
|
|
|
|
|
|
|
|
|
|
|
|
|
|
|
|
|
|
|
|
|
|
|
|
|
|
Founded in 1873, John Lang & Sons was based in Mary Street, Johnstone, near Glasgow. At first their operations, like many contemporary Companies in this once thriving industrial area, included a variety of products and services including the manufacture of gears (a specialism that was to last until their closure) shapers, horizontal borers, the design and making of one-off machines and lathes. However, it was not long before lathes were to dominate output and, subsequently, the Company became famous for their wide range of high-quality, well-designed and effective machines that were regarded by many as superior to those manufactured by Dean, Smith and Grace - and equal to those from the better German makers. Although lathes made up the bulk of entries in the Company's catalogue, other items continued to be made including automatic tooth-rounding machines; heavy-duty tailstock revolving centres; mandrel and bench straightening presses; centring, counter-boring and facing machines; small pumps for oil or water and a multi-plate friction clutch branded "Jehu". Lang were to remain an independent enterprise until taken over by Wickman in the 1960s, to become Wickman-Lang. Wickman were known for their automatic lathes and these had already been built at the Lang factory for some years before the take over. Both conventional and automatic types (the former in decreasing numbers) were built at the Lang factory until the John Brown Engineering Group, who owned Wickman, closed the factory in 1979. A small offshoot, Lang Power Chucks, managed to survived until the mid-1980s. Amongst the huge variety of regular production and one-off Lang lathes manufactured was the popular "Junior", a machine thought to have been introduced during the mid 1930s. Built to Lang's usual very high standards this almost entirely conventional machine was no tiny, inconsequential product - it was a "Junior" only in Lang's terms and would, for many other machine-tool makers, have been an advanced offering. The lathe was available with a choice of three centre heights: 6.5", 8.5" and 10" (165 mm, 215 mm 174 mm) with the two smaller versions also sold as boring and facing lathes with the option of a 6-tool indexing turret. Each version of the Junior was an individual, dedicated model with many unique parts and its own size of bed - and (as offered by many other makers) the same machine with an increased centre height. Bed widths were, respectively, 11.75" (298 mm), 14.75" (375 mm) and 17.75" 451 mm) with depths of 9" (228 mm), 10.25" (260 mm) and 11.5" (292 mm). Net weights for the two smaller machines were 21 cwt (1066 kg) and 35 cwt (1778 kg) while the largest was a very much more massive at 72 cwt (3658 kg). The two smaller models were each sold as standard with a bed 6-feet long while the largest, with a capacity more in keeping with its mass, measured 8 feet. As an option longer beds were available with that on the smallest version being 7-feet long, the middle size up to 9-feet long and with the largest (using a central support) available in foot increments up to a maximum of 16 feet. A gap was not offered, the design of the inverted V and flat ways that extended in front of and behind the headstock precluding this option. As a result the carriage, with its long projecting swarf guards fitted to the end of each saddle wing, had its cross slide mounted almost centrally and could bring the toolpost right up to the front face of the headstock. Equipped with the traditional Lang narrow front vertical way to guide the saddle (with adjustment by a tapered gip strip), the unhardened beds were, like all the Company's castings, produced in a close-grained iron (with a percentage of steel) that had been subjected to stringent metallurgical controls and poured in-house from a Lang designed and operated melting unit. Bed were braced between their walls with strong diagonal webs and supported two cast iron feet with a deep, pressed-steel chip and coolant-collection tray between them. Continued below:
|
|
|
|
|
|
|
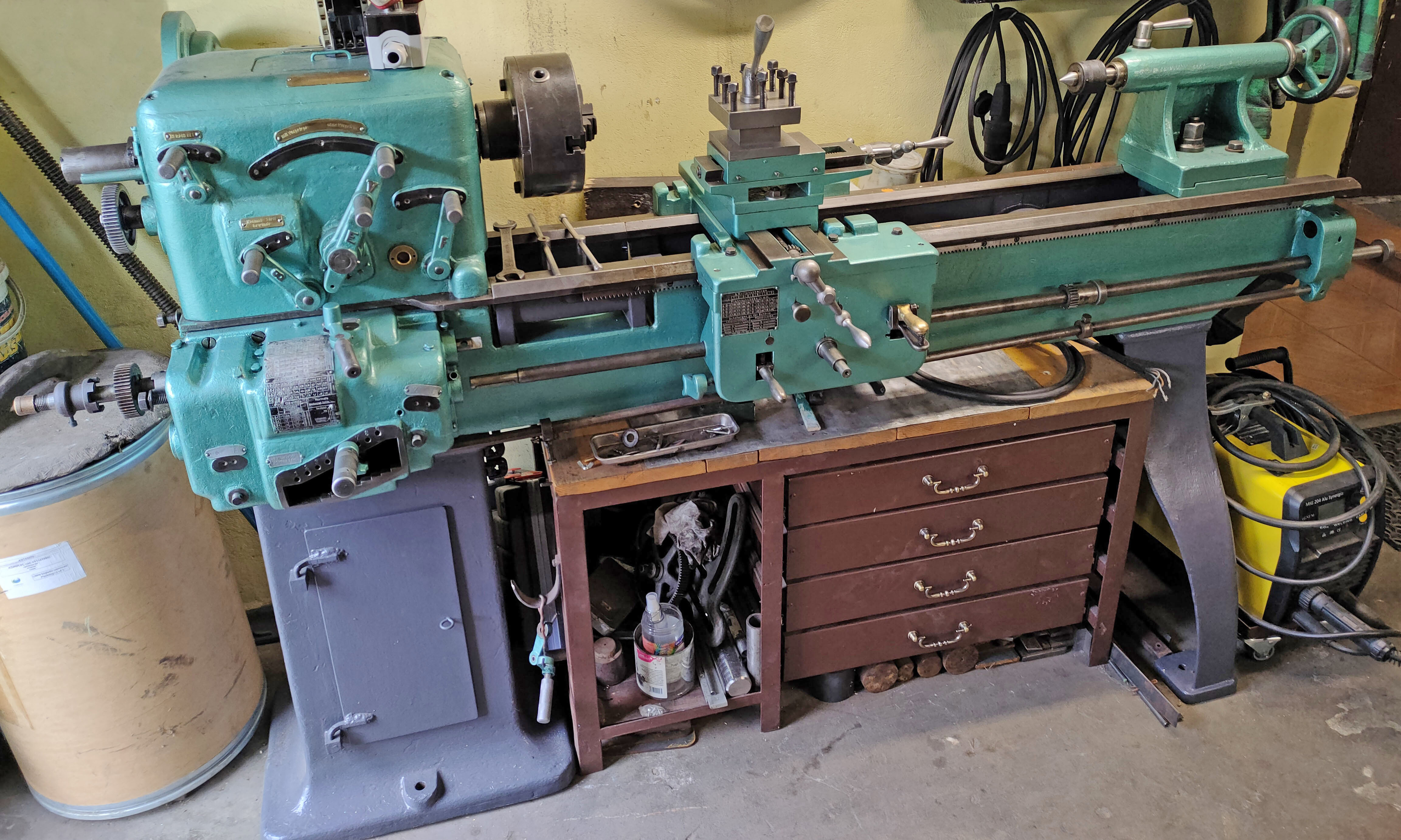 |
|
|
|
|
|
Lang Junior as a 6.5 -inch centre-height model
|
|
|
|
|
|
|
|
|
Continued: Heavily built, the 6-speed headstock was all-geared with drive on early models by a wide flat-belt or, on later machines, with the option of a multiple V-belt pulley. The former were intended to be driven at 500 to 600 r.p.m. - the power required varying from 2 to 5 h.p. for the smallest models and up to 10 h.p. for the largest. With the pulley widths for the three models being 2.75" (70 mm), 3.5" (89 mm) and 4.75" (121 mm). Later 6.5-inch and 8-inch models had the option of a built-on electric motor behind the headstock with drive by triple V-belts of "B" section. The 10-inch version with V-belt drive had its motor mounted on a separate floor-standing foot plinth behind the headstock-end foot. All types were equipped, on the pulley input shaft, with a multi-disc clutch of Lang manufacture that used alternate steel and bronze plates, running in oil, with actuation by three radial toggle levers. Control was by a long lever at the front of the bed placed so as to be within easy reach of the operator's normal working position. As the clutch lever moved to disengage the drive, a Ferodo-lined brake was brought automatically into operation to stop the spindle - an essentially fitting to prevent heavy jobs rotate uselessly for several minutes… Internal gears were in a nickel chrome, heat-treated steel with tooth profiles ground after the (distorting) heat treatment to ensure silent running. Sliding gears moved along ground, six-spline shafts supported in ball bearings while all parts were lubricated by a pressure pump that drew oil from a sump in the headstock base. On the two smaller models spindle speeds were changed by a pair of separate levers - while the largest model used three, with the pair nearer to the spindle nose being mounted concentrically. Rather unusually, the headstocks of the 6.5-inch and 8.5-inch models (but not the 10-inch) contained a pair of "pick-off" gears (shown in the illustration below) that, when swapped over, changed the overall speed range - these being shown on a speed plate fastened to the face of the headstock with one range in white digits and the other in red - these being 20 to 400 r.p.m. and 46 to 908 r.p.m. Like the bed, each model had its own size of headstock holding a ground-finished spindle made from a high-quality "Crucible" steel containing 0.5% carbon - this being melted in small batches using large clay containers (a process that died out in the 1950s). Spindle bores were 1.125" (29 mm); 1.625" (41 mm) and 2.125" 941 mm); diameter of the Lang quick-release spindle-nose fittings 5.75" (146 mm); 7" (178 mm) and 9.5" (241 mm) and the Morse taper sockets, 3MT, 4MT and 5MT. Bearings were of the anti-friction type with the front a Lang-patent, pre-loaded, spherical roller that took both radial and end thrust while that at the rear was an ordinary roller. In order to keep the selling price low, in place of a full screwcutting and feeds gearbox all versions of the Junior shared the same design of a much simpler, oil-bath unit equipped with all-steel, heat-treated gears running on ground splined shafts. Controlled by the juxtaposition of two levers on its front face and driving through a separate power shaft, six rates of feed were available from each setting of the changewheels - these being sliding from 12 to 144 inches per minute (2.1 to 18 mm) with the cross motion set to be half as fast. Using all the changewheels enabled a range of inch pitches from 4 to 42 t.p.i. Metric threading was also possible, the standard set of changewheels, carried on a guarded quadrant arm, including a suitable 127t transposing gear. To cut left-hand threads and to reverse the direction of the carriage and cross-feed travels, a small lever on the headstock (positioned between and just below the spindle-speed selector levers) was used to engage what amounted to a built-in tumble reverse mechanism to the changewheel drive. Although lubrication was by an oil-bath reservoir with either a sight-glass or dip stick to check the level, the operator was cautioned to check this daily and top up as required - a task that was bound to be overlooked in a busy workshops. Each lathe had an appropriate size and pitch of leadscrew, these being, in diameter and threads per inch from smallest to largest: 1.25" and 4 t.p.i., 1.5"; 4 t.p.i. and 1.75" and 2 t.p.i. A useful feature, included in the standard specification, was a permanently fitted thread-dial indicator built into the front left-hand wing of the saddle. Formed as one casting with an oil sump in its base, the apron had all its shafts supported at both ends with selection of power sliding or surfacing by a push-pull knob that slid a gear across to engage the desired drive - the mechanism, of course, being interlocked to prevent simultaneous engagement of both. Power was transmitted from the drive shaft by a key-driven wormwheel to a bronze wheel and then through a hardened-steel, multi-tooth clutch in nickel-chrome heat-treated steel that was controlled by a lever on the face of the apron. The lever, held in its engaged position on the two smaller models by a lock, was easily tripped even under heavy cutting loads by a slight sideways pressure aided by a spring. On the largest version the apron was of a different, more modern design as used on a number of later Lang lathes; still double-walled and with splash lubrication from a sump and the multi-tooth clutch, the controls were altered so that selection and engagement of feeds was by a single lever, moved across a short gate in the middle of the front face, with a reverse control pivoting from the bottom left-hand corner. Of conventional construction, the compound slide rest was fitted with tapered gib strips and zeroing micrometer dials of, for the era, reasonable size. Fitted as standard to the T-slot, 360°-swivel top slide was a clog-heel, single-clamp toolpost, though the option was also offered at extra cost of either an American-type lantern unit or an indexing 4-way type. Able to be set over for the turning of slight tapers, tailstocks each had a barrel diameter and travel suitably proportioned according to the model's work capacity at, respectively, 1.75" (44 mm) diameter and 3" (76 mm) travel; 2.5" (63 mm) and 4" (101 mm) and 3.25" (83 mm) and 4" (101 mm). On the 10-inch model, to help move the very heavy tailstock, a crank handle was fitted that worked through gearing connected to the carriage bed rack. Supplied with each new lathe was a double-pin catchplate; faceplate; 3-point fixed steady; 2-point travelling steady; chip tray; set of screwcutting changewheels and a set of spanners. Extras included the usual 3 and 4-jaw chucks; an indexing 4-position automatic stop for the longitudinal feed; taper turning; coolant equipment; 4-way and lantern toolposts; V-belt instead of a flat-belt headstock input pulley; turning tools and a reversing clutch for the spindle drive..
|
|
|
|
|
|
|
|
|
|
|
|
|
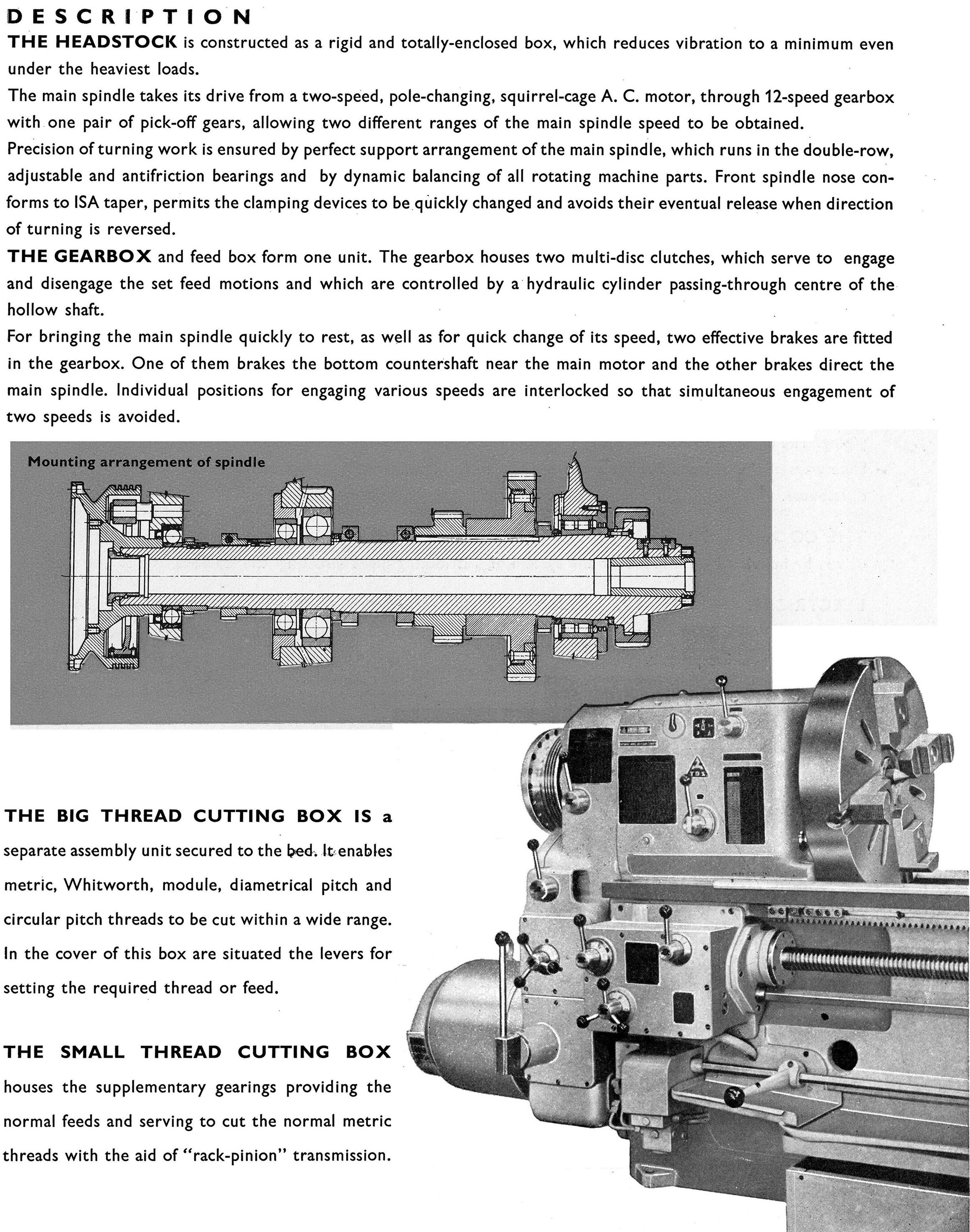 |
|
|
|
|
|
Lang Junior 8.5-inch centre height model equipped as a boring and facing lathe with a 6-station turret
|
|
|
|
|
|
|
 |
|
|
|
|
|
The very much more massive 72 cwt (3658 kg) 10-inch centre height Junior
|
|
|
|
|
|
|
|
|
|
|
|
 |
|
|
|
|
|
|
|
Headstock of the 6.5-inch and 8.5-inch centre height Junior models
|
|
|
|
|
|
|
|
|
|
|
 |
|
|
|
|
|
|
6.5-inch and 8.5-inch Junior headstock showing the pick-off gears that could be swapped over to give alternative speed ranges
|
|
|
|
|
|
|
|
|
|
|
 |
|
|
|
|
Headstock of the 10-inch centre height Junior - note the two concentrically mounted speed-change levers
|
|
|
|
|
|
|
|
|
 |
|
|
|
|
|
|
Interior of the Lang Junior 10-inch model headstock
|
|
|
|
|
|
|
 |
|
|
|
|
|
|
Spindle bearings were of the anti-friction type with the front a Lang-patent, pre-loaded, spherical roller that took both radial and end thrust while that at the rear was a plain roller.
|
|
|
|
|
|
|
|
|
|
|
|
 |
|
|
|
|
|
|
In order to keep the selling price low, in place of a full screwcutting and feeds gearbox all versions of the Junior shared the same design of a much simpler 6-speed, oil-bath unit equipped with all-steel, heat-treated gears running on ground splined shafts
|
|
|
|
|
|
|
 |
|
|
|
|
|
|
6-speed screwcutting and feeds gearbox as fitted to the 10-inch Lang Junior
|
|
|
|
|
|
|
 |
|
|
|
|
|
|
Formed as one casting with an oil sump in its base, the apron had all its shafts supported at both ends with selection of power sliding or surfacing by a push-pull knob that slid a gear across to engage the correct drive. Power was transmitted from the drive shaft by a key-driven wormwheel to a bronze wheel and then through a hardened-steel, multi-tooth clutch controlled by a lever on the face of the apron. The lever, held in its engaged position on the two smaller models by a lock, was easily tripped even under heavy cutting loads by a slight sideways pressure aided by a spring.
|
|
|
|
|
|
|
|
|
|
|
|
 |
|
|
|
|
|
|
On the 10-inch centre height Junior the apron was of a different, more modern design as used on a number of later Lang lathes; still double-walled and with splash lubrication from a sump the controls were altered so that selection and engagement of feeds was by a single lever, moved across a short gate in the middle of the front face, with a reverse control pivoting from the bottom left-hand corner.
|
|
|
|
|
|
|
 |
|
|
|
|
|
|
On the 10-inch centre height Junior the apron was of a different, more modern design as used on a number of later Lang lathes; still double-walled and with splash lubrication from a sump the controls were altered so that selection and engagement of feeds was by a single lever, moved across a short gate in the middle of the front face, with a reverse control pivoting from the bottom left-hand corner.
|
|
|
|
|
|
|
 |
|
|
|
|
|
|
Lang Junior boring & facing lathe - 6-station capstan attachment
|
|
|
|
|
|
|
|
|
|
|
|
 |
|
|
|
|
|
|
Motor mount and V-belt drive system on the Lang Junior 10-inch
|
|
|
|
|
|
|
 |
|
|
|
|
 |
|
|
|
|
|
|
|
|
|
|
|
|
|
|
|
 |
|
|
|
|
|
|
|
|
|
|
 |
|
|
|
|
|
|
American style lantern toolpost
|
|
|
|
|
|
|
 |
|
|
|
|
|
|
|
|
|
|
|
|
|
|
|
|
|
|