 |
 |
 |
 |
 |
 |
 |
 |
 |
 |
 |
 |
 |
 |
 |
 |
 |
 |
 |
 |
 |
 |
 |
 |
 |
 |
 |
 |
 |
|
|
|
|
|
|
|
|
|
|
|
|
|
|
|
|
|
|
|
|
|
|
|
|
|
|
|
|
|
|
|
|
|
|
|
|
|
|
|
|
|
Founded in 1898 and based originally in Bienne, Switzerland, Hauser was eventually absorbed into the Societe Genevoise (SIP) group and today still form part of that now international and greatly expanded company. Today that organisation - now listed as resident in China - makes a variety high quality conventional and CNC controlled machine tools. Although Hauser always placed a strong emphasis on their jig boring and jig grinding models, they were also famous for the specialised equipment and tooling made for watch, clock and mechanical instrumentation industries. Hundreds of different machines were manufactured including a (seldom-found) precision bench lathe, miniature, high-precision specialist milling machines; optical checking equipment; profile projectors; measuring instruments; many types of automatic and semi-automatic pivot-polishing machines; hardness testers; rotary tables; workshop measuring microscopes, machines for forming and regrinding tungsten carbide and ceramic wheels; automatic recesses milling machines (for the production of watch plates) and universal facing and boring heads, etc. A number of automatic, continuous-production machine tools were also offered, all designed to deal exclusively with tiny parts. Examples of the latter included transfer and multi-spindle profile milling machines; transfer units for machining small components in metal strips; milling and drilling machines with three horizontal work spindles; drilling and tapping machines with multiple horizontal spindles; milling, drilling and boring machines to produce watchcases; 3-spindle vertical millers and multi-spindle drilling, tapping and milling machines. Many of these special Hauser models were as one-offs, in very limited numbers - or even built to a customer's design in order to solve a difficult production problem. As such, though attractive to look at, superbly made and eminently collectable, they are often difficult to adapt to general or home-workshop use. Simple designs of horizontal and vertical bench milling machines were produced in a bewildering variety of sizes and types - though again, most were really intended for production rather than one-off work - and with most featuring an unsupported cutter protruding from a lathe-like headstock assembly that limited their application to lighter rates of metal removal. On horizontal machines, the main body was usually of the type machined to accept a very heavy right-angle adaptor that allowed the head to be mounted vertically - though this required the setting up of a complicated drive system. However, as these machines were intended only for the relatively delicate work, very little power was needed and the drive was always by a round leather or fabric rope. Vertical millers were often based around a cast-iron base plate and main column formed as one piece, with a table moved by levers or screw feeds - or even a combination of both. Spindle heads were similar - and often interchangeable between horizontal and vertical models - with feed by lever against front and back (or up and down) stops with very fine-pitch, hardened screws and with cutters held by direct-fitting, draw-in collets. On vertical types, in order to provide as wide a range of movement and work capacity as possible, two slides were sometimes used: the head, for example, moving on an intermediate plate that its self could be adjusted for position by clamps against ways formed on the inner face of the main column. A common fitting was a simple 100 to 150 mm diameter, lever-turned rotary table (again with screw stops) capable of mounting a variety of fittings including watch-lathe type faceplates with delicate clamps, angle brackets, dividing attachments and vices. Jig borers should always be installed in a temperature-controlled room - often recommended to be at 21° - but as a precaution, to aid the stabilty and accuracy Hauser incorporated, on some models, a number of heating elements in the head assembly. An important note: to avoid damage it is vital that the drive variator used in the single column Hauser machines uses the correct lubricant - Monsanto Santotrac 50. See this page for more details Continued below:
|
|
|
|
|
|
|
|
|
|
|
|
|
|
|
|
|
|
Continued: Measuring Systems As the reason for a jig borer's existence is its the ability to position a workpiece with great precision, makers invested many years' work into producing high-quality, ultra-precise mechanical and mechanical optical measuring systems. Prior to the 1920s (and as used in earlier locating machines developed in Switzerland around 1910) the Swiss SIP Company had led the way by employing very accurate leadscrews with scales calibrated down to 0.0002" (0.005 mm) on the smallest models and 0.0005" (0.015 m) on the largest. However, only the Moore Jig Borer Company in the USA could produce, on a commercial basis, screws that were pitch perfect over the whole of their (maximum 20-inch) length and required no compensating correction mechanism. Hence, although of a very high standard, even the SIP screws required some method of automatically modifying their micrometer dial readings. The solution was to check, with great precision, how far turning the screw actually moved the table - and to do this it was necessary to measure the travel very accurately, in small increments. The obvious candidate for a reference standard was, naturally enough, one of SIP's own standard scales - a very high precision steel ruler of such accuracy that other length-measuring instruments could be calibrated from it (SIP were the leading suppliers of these to Government, engineering, scientific, and metrological institutes worldwide). The feed-screw was turned and the tester recorded the simultaneous readings from micrometer dial and standard scale - the latter being read through a microscope attached to the vertical spindle. The next step was to prepare a "curve of errors" that was reproduced, in an enlarged form, on a strip of hardened steel fixed permanently alongside the table (and other moving elements, if required). As a slide moved, a small lever followed the strip's profile and transferred its (tiny) movements, via a rod held in brackets, to another lever at the other end. Connected to the last lever was the vernier scale, positioned next to the rim of the feed-screw micrometer dial and free to move relative to it. Thus, for any position a corrected setting was automatically obtained - though great care in taking the vernier reading was, of course, essential. This ingenious (but simply engineered) system is believed to have been first employed by SIP in their jig borers during the 1920s and ensured that the accuracy of a complete machine was greater than that of its precision feed-screws. Following the introduction of the first SIP jig borer in 1919 (and their steady development during the 1920s) the Company decided that a standard scale should be built into the body of the machine and its graduations observed directly through an optical system with the results displayed on an illuminated screen. The first such model - a new Hydroptic type with a particularly smooth hydraulic table drive - was announced during 1934 and proved an enormous success with the standard scale method, combined with external rulers, micrometer drums and vernier scales, now able to provided toolrooms with the most accurate way yet of determining a position.
Hauser Screw-feed (non-optical) Jig Borers Although Hauser made (when they were in direct competition with the much larger SIP Company) at least two twin-column jig borers, the No. 4 and No. 5, they were far better known for their smaller, single-column types the Series Nos. 2 and 3. These could be supplied with table-position readings readings taken direct from the feed screws using conventional micrometer-dials and vernier scales or fitted as "optical models" - the standard scales used probably being sourced from SIP, then the world's leading maker of such items. In this respect the Hauser's optical types were comparable with the Models 1-H and 2P from SIP..
|
|
|
|
|
|
|
|
|
|
|
|
|
|
|
|
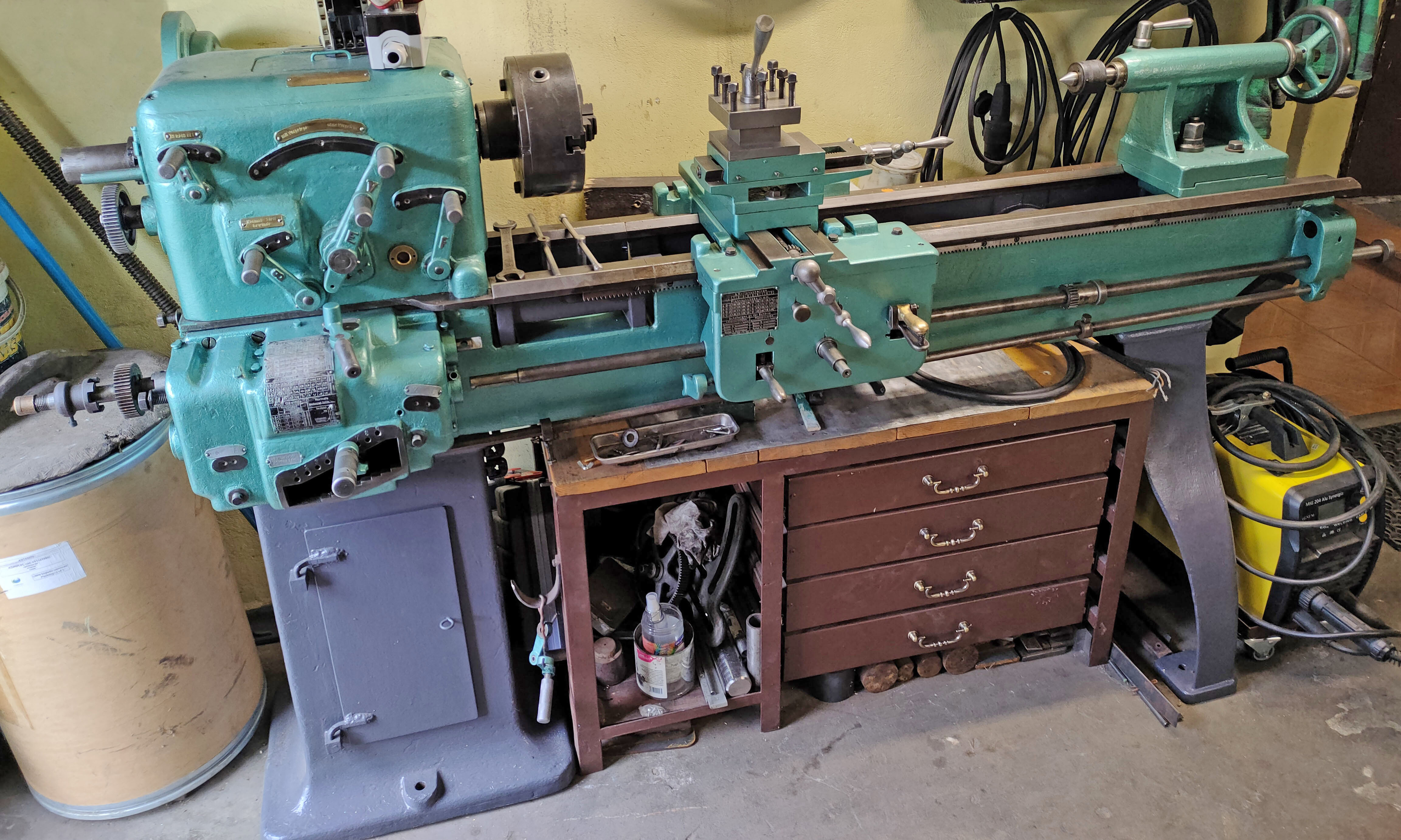 |
|
|
|
|
|
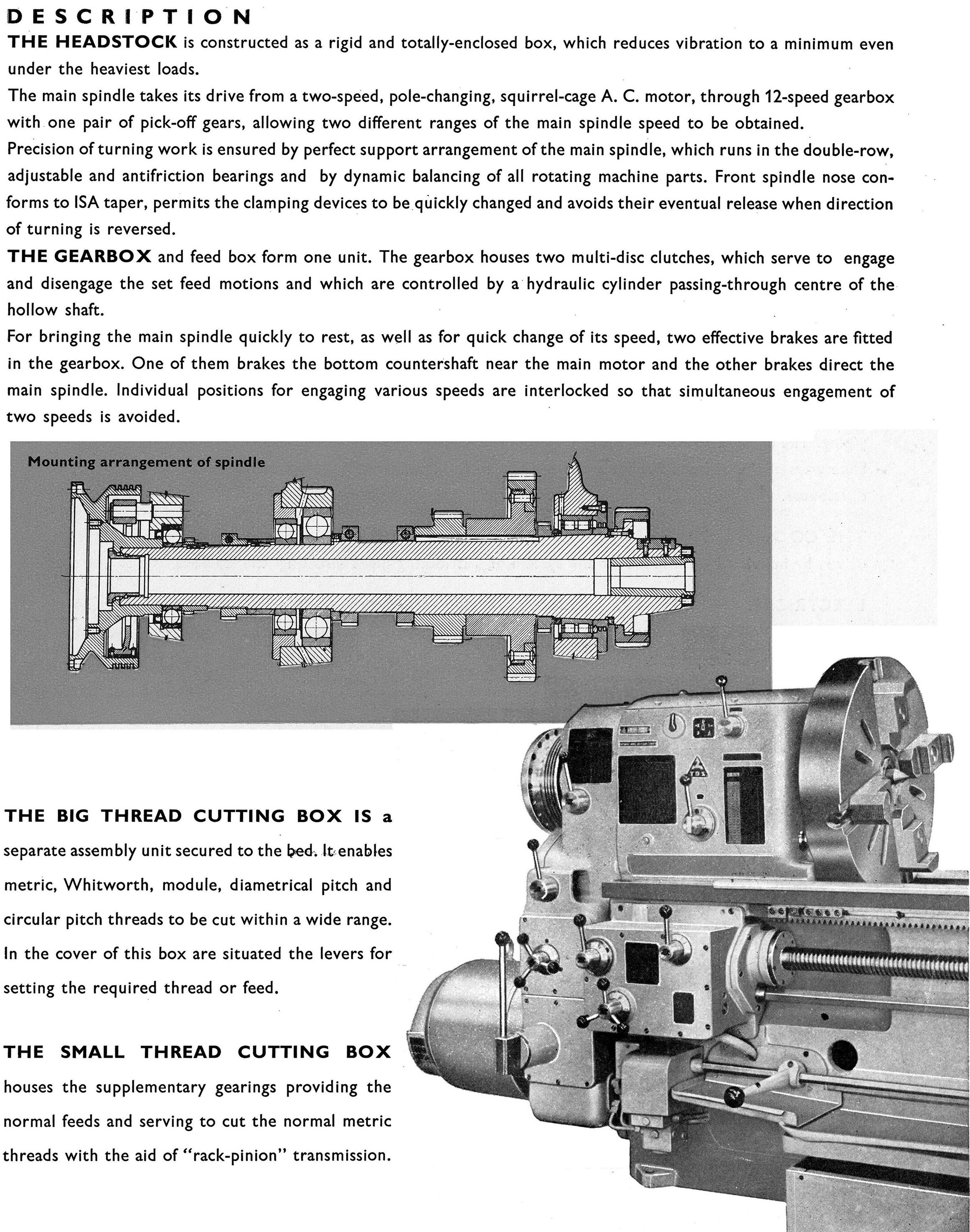 |
|
|
|
|
|
|
HAUSER 2BA Jig Borer -- circa late 1950s/1960s Whilst the No. 4 and No. 5 Hausers may not have enjoyed the popularity of similar SIP models, the smaller models were in great demand, with waiting times, in the 1950s and 1960s, stretching to over a year on some occasions. Of the pair, the No. 2BA was first to market with over 1000 sold before the introduction of No. 3. The No. 2 was eventually to be built in at least six versions - the direct-reading, screw-feed 2BA, 2A2 and 2A3, the optical-reading OP2 and two unusual combined jig boring and jig grinding machines: the mechanical dial-reading 2SB and optical 2SBO. All models of the No. 2 can be found in M.1 and Mk.2 form - the earlier having "round" styling typical of the kind used on machine tools until the late 1950s, and the later more modern, angular lines with the Hauser name picked out in large letters arranged vertically down each side of the stand's front face. Most popular of all, the 2-BA was versatile and adaptable, its larger table and longer head and spindle travels - together with a slightly better speed range than the other more specialised versions - giving it a clear advantage for run-of-the-mill toolroom work. With a working surface of 450 x 310 mm (17.75" x 12.25") the table had six T-slots and a longitudinal travel of 350 mm (14") and a cross-feed of 200 mm (8"). Carried on the back of the main body, the complete head assembly, together with the 0.75 h.p. spindle-drive motor and gearbox, could be elevated under power through a distance of 390 mm. Raised to its maximum height, a clearance of 570 mm (22.5") was created between spindle nose and table surface, a figure that allowed unusually large jobs to be accommodated that would otherwise have tied up larger and more expensive machines. To ensure complete safety, electrical switches were fitted that cut power if the limit of up or down travel was reached. To preserve their accuracy and maintain lubrication, the vertical ways were completely enclosed by bellows. Running in specially commissioned, high-precision roller bearings (that proved in service to have an unusually long life) the spindle had a generous 130 mm (5.125") of travel and was controlled by either a quick-action rack-and-pinion drive with a huge micrometer drum and a standard-fit 0.01 mm/0.001" dial indicator. Two rates of power up and down feed could be selected, 0.03 or 0.06 mm (0.0012" and 0.0024") per minute - the extreme slowness of which ensured a particularly fine surface finish. At the whim of the customer, the spindle nose could be equipped with either a No.1 or No. 2 Morse taper socket. Using a 0.75 h.p. 3-phase motor, spindle speeds were infinitely variable between 120 and 3000 r.p.m. - the result being an ability to drill holes smaller than 0.3 mm and bore them to a recommended maximum of 65 mm in diameter. Manufactured from special hardened, aged and ground steel, the table feed-screws were turned by large, smooth-faced handwheels - both positioned on the right-hand side of the machine and facing to the right. The final setting was achieved by knurled-edge knobs of a size comfortable to grip with the whole hand - and by which means the job could be perfectly positioned. In order to ensure an even greater degree of accuracy, this Hauser was fitted with the automatic screw-pitch correction mechanism described in the opening to the Hauser section above. Fitted to a very heavy cast-iron stand, left open at the front to accommodate a seated operator, the machine was of a considerable mass. At a glance, one might have estimated the weight at around 500 to 600 kg, but it actually tipped the scales at an astounding 985 kg (2175 lbs) - the result of a machine built without compromise to perform a specific job, regardless of cost..
|
|
|
|
|
|
|
|
|
|
|
|
|
|
 |
|
|
|
|
|
|
Hauser 2A3 Jig Borer -- circa late 1950s/1960s A lighter version of the 2BA, though with an identical mechanical layout, was the 2A3. This had a smaller 360 mm x 240 mm (14.5" x 9.5") table with its longitudinal travel reduced to 200 mm (8") in both directions and a head that could be elevated (under power) through 250 mm (9.75"). The reduced scale of the main components allowed the maker to guarantee an improvement in the "accuracy of the settings" from 0.003 mm to 0.002 mm (0.0001"). However, the maximum clearance between spindle nose and table was, at 350 mm (13.75") some 40% less than that for the 2BA limiting its work (deliberately) to smaller components. In addition, having only a No. 0 Morse taper in the spindle, the ability to engage in faster rates of metal removal was obviously limited; even so, despite these limitations, the makers claimed a drilling capacity in steel of 13 mm (0.5') and boring to a maximum diameter of 50 mm (2"). Spindle travel was just 70 mm (2.75") an amount adequate for very fine work. Powered by a flexible shaft from a separate drive unit, the bottom speed was just 25 r.p.m. faster than that of the 2BA, giving a range from 150 to 3000 r.p.m. Fitted on the end of the table was a slideway able to take a variety of fittings identical to those employed on the M1 Model - for example a spindle having only 40 mm travel (designed to take Type B 8 mm collets rather than a Morse taper) the speed range of which was infinitely variable between 250 to 2700 r.p.m. Mounted beneath the vertical slide, on the side face of the saddle, was a faceplate with three clamps - again an item borrowed from the M1. The net weight of the 2A3 was approximately 600 kg (1300 lbs). 2A3 photographs
|
|
|
|
|
|
|
|
 |
|
|
|
|
|
|
Hauser 2A2 Jig Borer - circa late 1950s/1960s Smallest and lightest of the 2 Series machines was the 2-A2. Built to tackle very small jobs it was, like the others, constructed on the same basic stand unit and had a mechanical and dimensional specification identical to that of 2A3 - save for differences concentrated in the head and drive assembly.
|
|
|
|
|
|
|
|
|
|
|
|
|
|
 |
|
|
|
|
|
|
Hauser 3BA Jig Borer - circa late 1950s/1960s Introduced late in the Company's history, Hauser's largest single-column screw-feed jig borer was the Type 3BA. Weighing only 100 kg more than the 2BA, this machine was, in effect almost the same in every respect - save for a larger 550 x 320 mm (22" x 12.5") table with travels of 400 mm (16") longitudinally and 250 mm (10") across. The head was able to be elevated through an additional 10 mm (0.375") to give 600 mm (23.5") of clearance between spindle nose and table - just 30 mm more than the 2BA. The head fitted was identical (though a No. 2 Morse taper was standard) with 130 mm (5.125") of spindle travel and the same 120 to 3000 r.p.m. speed range.
|
|
|
|
|
|
|
|
 |
|
|
|
|
|
|
Hauser M1 Jig Borer--shown with spindle microscope in place Based on a design dating back to the early 1900s - and believed to have been originally developed by the Swiss firm SIP - Société Genevoise d'Instruments de Physique - the smallest Hauser jib borer made after WW2 would originally have been called (as a SIP) a "pointing machine" and lacked any form of spindle drive. Originally marketed alongside an even smaller version, the Model 0, the M1 was intended for use in the watch, clock and precision instrument industries, instead of a horizontal table, the M1 was fitted with a vertical, T-slotted 250 x 150 mm (10" x 6") plate formed on the front of the machine's main body to which could be bolted various accessories; these included: an ordinary rectangular, a 250 x 150 mm T-slotted table; a 200 x 132 mm table with a glass insert used exclusively for measuring work (with episcopic illumination combined with the centring microscope or diascopic illumination with either a centring or double-image microscope); a 135 mm diameter rotary table that could read down to 5 seconds of arc; a large swivel support (for measuring screws and worm wheels etc.) and a 135 mm (5.25") diameter table fitted with three radial clamps in the manner of a faceplate from a watchmakers' lathe. The longitudinal table travel was 125 mm (5") with in and out movement limited to 100 mm by a slide that carried the vertical head. Control of table movements was by the usual hardened, aged and ground steel the table feed screws fitted with enormous micrometer drums that turned inside housings viewed through with glass covers. The drums read down to 0.01 mm (0.001") the verniers to 0.001 mm (0.0001" or 1/10,000th of an inch) with external rulers on each axis for coarse settings. The slideway on the end of the horizontal ram could take various fittings including a centring microscope, a double-image microscope and a quickly-detachable spindle housing able to be moved through 40 mm (1.5") of vertical travel under the control of a sensitive lever. Fitted to take Type B8 0.315" (8 mm) collets this spindle was driven by a Hauser-type, flexible shaft with the motor was mounted on a high structure above the spindle. Speeds, which were infinitely variable, ranged from 250 to 2700 r.p.m. Photographs of an M1 here
|
|
|
|
|
|
|
|
|
|
|
|
|
|