 |
 |
 |
 |
 |
 |
 |
 |
 |
 |
 |
 |
 |
 |
 |
 |
 |
 |
 |
 |
 |
 |
 |
 |
 |
 |
 |
 |
 |
 |
 |
|
|
|
|
|
|
|
|
|
|
email: tony@lathes.co.uk Home Machine Tool Archive Machine-tools Sale & Wanted Machine Tool Manuals Catalogues Belts Books Accessories
lathes.co.uk Gosmeta Lathes Gosmeta D110
A full-range Gosmeta catalogue is available
Manufactured by Gosmeta Industrie of Amsterdam in Holland - it is uncertain from which of their three factories they emerged: Gosselaar's N.V. in Holland, Gosmeta s.r.l. at Legnano in Italy or Gosmeta N.V. in Erembodegem, Belgium. Gosmeta made (and probably factored) a wide range of machine tools and associated products including centre, toolroom and capstan) lathes, milling machines, presses, guillotines, press brakes, plate benders, nibblers, lathe chucks and toolposts, dividing heads, rotary tables, bench, pillar and radial-arm drills, mechanical hacksaws and bandsaws, circular cut-ff Saws, carbide tool & twist drills grinders, vertical spindle grinders, horizontal borers, shapers and welders machines. If you have a Gosmeta machine tool of any type, and would like to supply photographs for the Archive, the writer would be pleased to hear from you. One unusual Gosmeta lathe found in 2020 was a Model D110; with a centre height of around 125 mm and a capacity between centres of perhaps 500 mm, this was a well-built, toolroom-class lathe of which few appear to survive; pictures here..
|
|
|
|
|
|
|
|
|
|
|
|
|
|
|
|
|
|
|
|
|
|
|
|
|
|
|
|
|
|
|
|
|
|
|
|
|
|
|
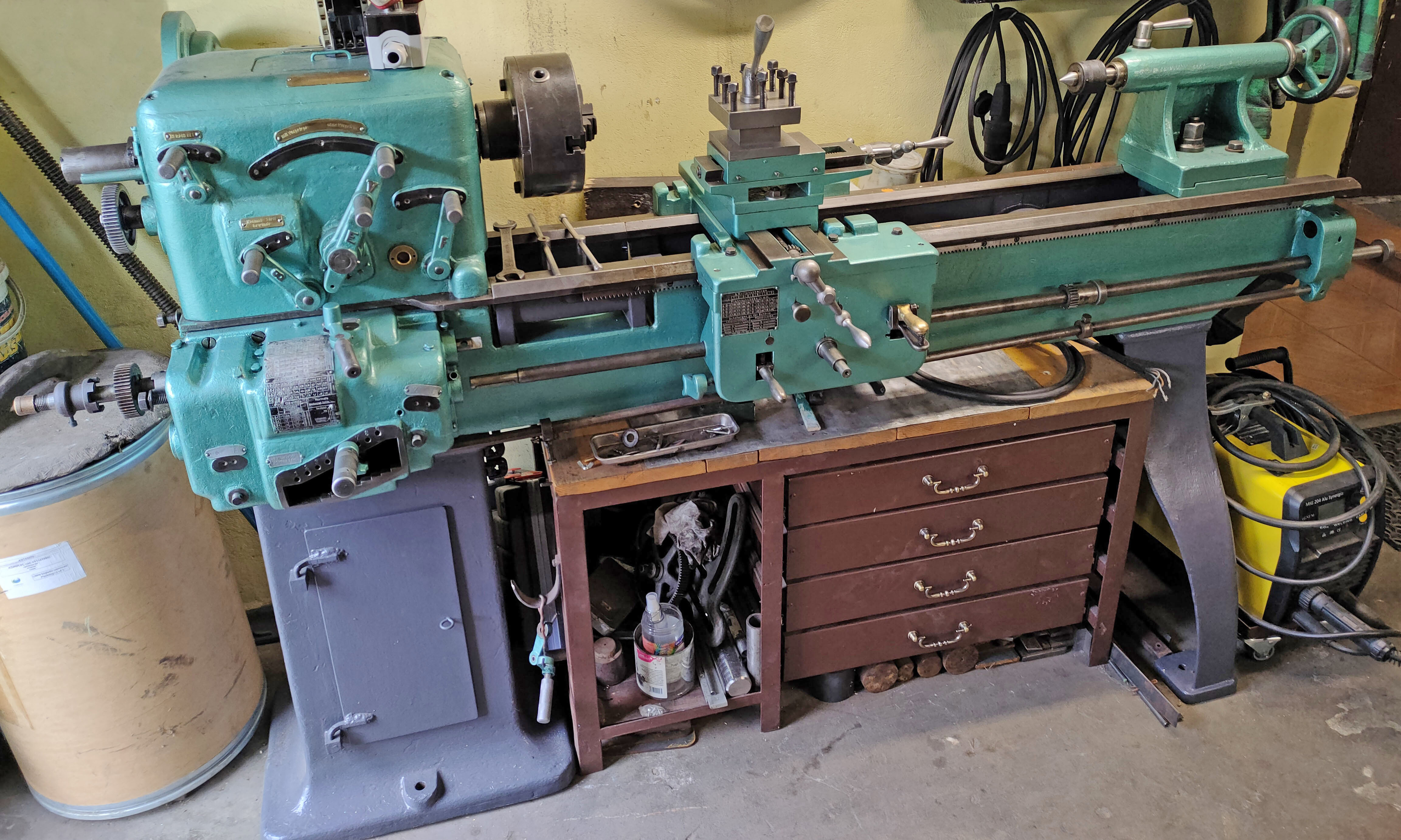 |
|
|
|
|
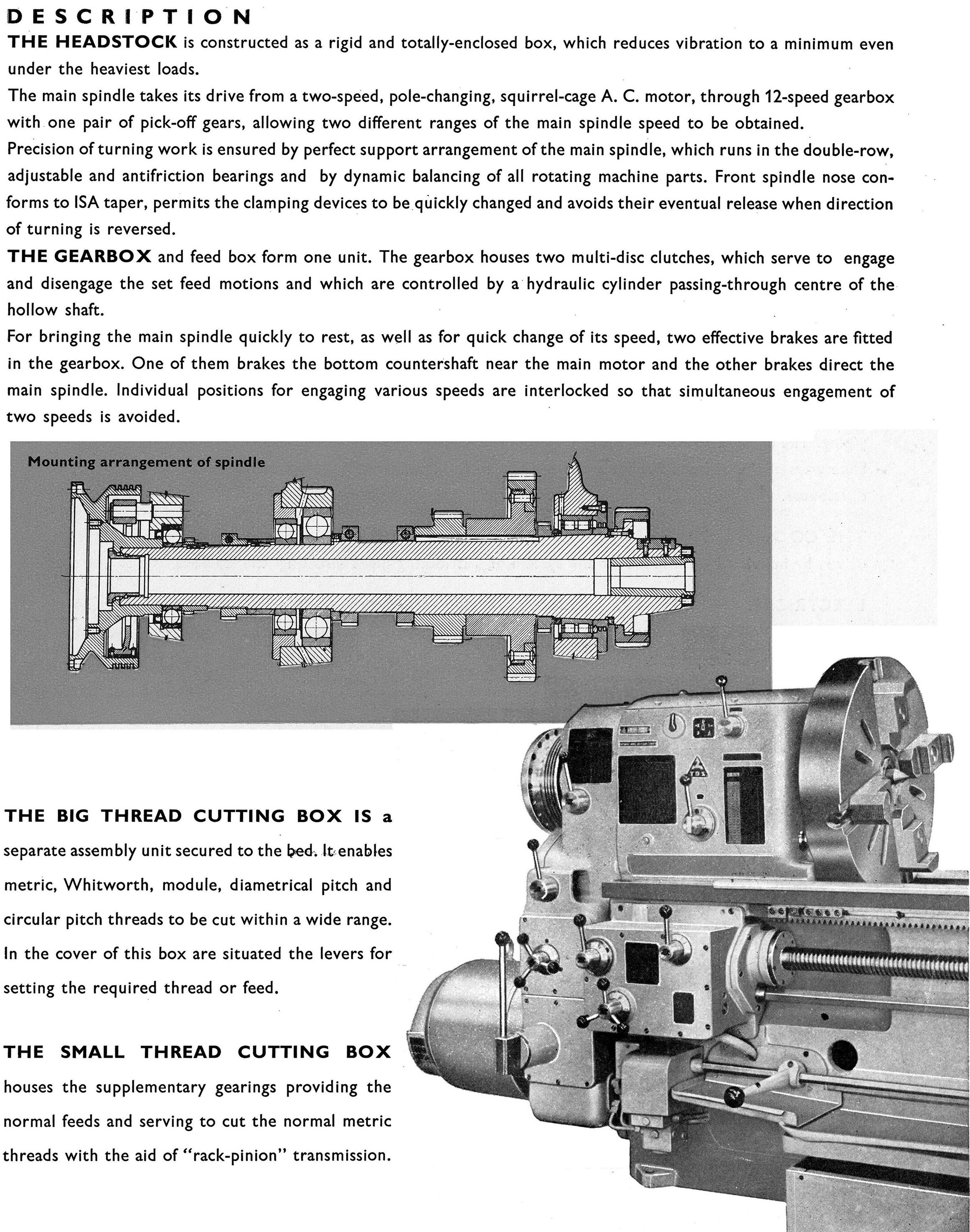 |
|
|
|
|
|
|
A late 1950s to early 1960s Gosmeta D-135 with a 140 mm centre height and admitting 810 mm between centres and mounted on the massive cast-iron base that appears to have been common across the Gosmeta range. This was strongly-built, general-purpose lathe with a straight, gapless-bed and fitted with a metric and Whitworth screwcutting and feeds gearbox. Power sliding and surfacing feeds were selected by a quadrant lever on the face of the oil-bath lubricated apron with, below it, the wind-in handwheel for engagement and disengagement of the feed. Screwcutting and feeds was by a conventional Norton-pattern quick change gearbox with selection of by the usual sliding tumbler mechanism. Drive came from a motor mounted in the headstock-end cast-iron plinth that drove a 4-speed gearbox; final drive to the headstock was by a belt that ran over a pulley running in its own bearings - the connection with the spindle being by a "peg" - the design relieving the spindle from all effects of belt pull. A lever on the face of the headstock engaged the high and low speed ranges, the eight in number spanning 59 to 1220 r.p.m. Running in a plain bronze bearing at the front, the rear of the screwed-nose spindle was supported in a taper roller race with end thrust taken by a ball race. Electrical control of the spindle stop, start and reverse was by the operation of push buttons and switches.
|
|
|
|
|
|
|
 |
|
|
|
|
|
|
Gosmeta D-160 and D-180 - the former with a centre height of 160 mm and the latter 180 mm. The D-160 was sold as a single model that admitted 1000 mm between centres while the D-180 could be had, optionally, with an additional 500 mm. Both lathes were of identical mechanical design - differing only in their centre height and motor power - and equipped with an enormously deep bed that had a permanent, open gap in which a diameter of 450 mm on the D-160 and 600 mm on the D-180 could be swung. The fully-enclosed, oil-bath lubricated screwcutting and feeds gearbox had all-lever control to alter the feed rates - there being no open slot to allow the ingress of dirt and swarf. Also sealed, the apron had positive, automatically pumped lubrication from a base reservoir with a supply also directed to the lathe's bed and cross slide ways. The headstock was very heavily built, fitted with hardened and ground gears held on splined shafts that ran in anti-friction bearing with lubrication by a pressure pump. Drive from the motor (2 h.p. on the D-160 and 3 h.p. on the D-180) passed through a double forward/reverse multi-plate clutch equipped with an automatic brake. Changes of spindle speed were made by the juxtaposition of two levers mounted on a common axis - the six speeds provided spanning (on both lathes) an identical 50 to 1200 r.p.m. Hardened and ground, the spindle ran in taper roller races and was equipped with a standard American long-nose taper in an L00 size. Electrical control of the spindle stop, start and reverse was by a third-rod system with two cooperating levers - one pivoting from the right-hand face of the apron, the other positioned just outboard of the screwcutting gearbox. Standard equipment was - for a European lathe - generous and included a lengthened cross slide that allowed the mounting of a rear toolpost, a full coolant system,. 4-jaw chuck, fixed steady, travelling steady, a 4-way indexing toolpost and a catchplate.
|
|
|
|
|
|
|
|
|
|
 |
|
|
|
|
|
|
D-200, D-220 and D-250 from the 1960s - three Gosmeta lathes that shared an identical mechanical design and differed only in their centre height and availability of capacity between centres - the former pair offered with a choice of either 1000 or 1500 mm and the D-250 with 1000, 1500 and 2000 mm. Built with the usual very deep bed common to all Gosmeta lathes, the D-220 had a detachable gap section that, when removed, allowed a diameter of 720 mm to be swung, the matching figure of the D-250 being 780 mm. Fully-enclosed, the oil-bath lubricated screwcutting and feeds gearbox had all-lever control to alter the feed rates - there being no open slot to allow the ingress of dirt and swarf. Also sealed, the apron had positive, automatically pumped lubrication from a base reservoir with a supply also directed to the lathe's bed and cross slide ways. Power feeds were each engaged by their own lever on the front face of the apron, these working through individual, safety overload clutches. Very heavily built, the headstock held hardened and ground gears sliding on multi-splined shafts that ran in anti-friction bearing with positive lubrication from a pressure pump. Drive from the base-mounted 5 h.p. motor was taken upwards by three V-belts tensioned by what could be a unique system: a jockey pulley mounted on a horizontal slideway - adjustable for position by a handwheel and screw - fastened to the top surface of the stand's left-hand face. Power passed through a double forward/reverse multi-plate clutch equipped with an automatic brake. Changes of spindle speed were made by the juxtaposition of two levers mounted on a common axis - the six speeds provided spanning (on both lathes) an identical 50 to 1200 r.p.m. Hardened and ground, the spindle ran in taper roller races and was equipped with a standard American long-nose taper in a size L1. Electrical control of the spindle stop, start and reverse was by a third-rod system with two cooperating levers - one pivoting from the right-hand face of the apron, the other positioned just outboard of the screwcutting gearbox. Standard equipment was - for a European lathe - relatively generous and included a lengthened cross slide that allowed the mounting of a rear toolpost, a full coolant system,. 4-jaw chuck, fixed steady, travelling steady, a 4-way indexing toolpost and a catchplate.
|
|
|
|
|
|
|
 |
|
|
|
|
|
|
|
|
|
A rebuilt and slightly different D-220 with alerted headstock speed-control levers together with an emergency stop button
|
|
|
|
|
|
|
|
|
 |
|
|
|
|
|
|
Gosmeta D-310A 310 mm x 1500 or 2000 mm lathe as sold during the 1960s Built with the usual very deep bed common to all Gosmeta lathes, the D-220 had a detachable gap section that, when removed, allowed a diameter of 920 mm to be swung. Fully-enclosed, the oil-bath lubricated screwcutting and feeds gearbox had all-lever control to alter the pitch and feed rates - there being no open slot to allow the ingress of dirt and swarf. Also sealed, the apron had positive, automatically pumped lubrication from a base reservoir with a supply also directed to the lathe's bed and cross slide ways. Feeds were selected by a push-pull knob and engaged by a positive in/out lever. Very heavily built, the headstock held hardened and ground gears sliding on splined shafts that ran in anti-friction bearing with lubrication from a pump. Drive from the 7.5 h.p. motor passed through a double forward/reverse multi-plate clutch equipped with an automatic brake. Changes of spindle speed were made by the juxtaposition of two levers mounted on a common axis - the ten speeds provided spanning 14 to 800 r.p.m. Hardened and ground, the spindle ran in taper roller races and was equipped with a standard American long-nose taper - thought to be a size L1. Electrical control of the spindle stop, start and reverse was by a third-rod system with two cooperating levers - one pivoting from the right-hand face of the apron, the other positioned just outboard of the screwcutting gearbox. Standard equipment was - for a European lathe - relatively generous and included a lengthened cross slide that allowed the mounting of a rear toolpost, a full coolant system,. 4-jaw chuck, fixed steady, travelling steady, a 4-way indexing toolpost and a catchplate.
|
|
|
|
|
|
|
 |
|
|
|
|
|
|
The rebguilt D-220 shown higher up the page in the process of being restored to working order
|
|
|
|
|
|
|
|
|
|
 |
|
|
|
|
 |
|
|
|
|
|
|
Drive from the base-mounted 5 h.p. motor was taken upwards by three V-belts tensioned by what could be a unique system: a jockey pulley mounted on a horizontal slideway - adjustable for position by a handwheel and screw - fastened to the top surface of the stand's left-hand face.
|
|
|
|
|
|
|
 |
|
|
|
|
|
|
Gosmeta D-200. Power feeds were each engaged by their own lever on the front face of the apron, these working through individual, safety overload clutches.
|
|
|
|
|
|
|
 |
|
|
|
|
|
|
Gosmeta D-310B - a long-bed version of the D-310A admitting either 3000 or 4000 mm between centres and fitted with a 10 h.p. motor and, because it was so heavy and the bed long, a tailstock moved along the bed by a crank handle that engaged with a rack shared by the carriage. However, the maker's literature shows lathes with a very much greater capacity, almost certainly in excess of 10 metres with their beds having additional central support.
|
|
|
|
|
|
|
 |
|
|
|
|
|
|
|
|
|
Gosmeta D-410 410 mm centre height and admitting 2000, 3000 or 4000 mm between centres. Constructed to the same standard as the smaller models in the Company's range, this lathe had a deep, straight along its bottom face and with a detachable gap section that allowed work up to 1300 mm in diameter to be turned. Fully-enclosed, the oil-bath lubricated screwcutting and feeds gearbox had all-lever control to alter the pitch and feed rates - there being no open slot to allow the ingress of dirt and swarf. Also sealed, the apron had positive, automatically pumped lubrication from a base reservoir with a supply also directed to the lathe's bed and cross slide ways. Feeds were selected by a push-pull knob and engaged by a positive in/out lever. Very heavily built, the headstock held hardened and ground gears sliding on splined shafts that ran in anti-friction bearing with lubrication from a pump. Drive from the 20 h.p. motor passed through a double forward/reverse multi-plate clutch equipped with an automatic brake. Changes of spindle speed were made by the juxtaposition of four lever, two on separate and the other pair on a common axis - the 12 speeds provided spanning 12 to 550 r.p.m. Hardened and ground, the spindle ran in taper roller races and was equipped with a standard American long-nose taper - thought to be a size L2. Electrical control of the spindle stop, start and reverse was by a third-rod system with two cooperating levers - one pivoting from the right-hand face of the apron, the other positioned just outboard of the screwcutting gearbox. As on many lathes of a similar size and length, the heavy tailstock moved along the bed by a crank handle that engaged with a rack shared by the carriage. Standard equipment was - for a European lathe - relatively generous and included a lengthened cross slide that allowed the mounting of a rear toolpost, a full coolant system,. 4-jaw chuck, fixed steady, travelling steady, a 4-way indexing toolpost and a catchplate.
|
|
|
|
|
|
|
|
|
|
|
|
|
|
|