 |
 |
 |
 |
 |
 |
 |
 |
 |
 |
 |
 |
 |
 |
 |
 |
 |
 |
 |
 |
 |
 |
 |
 |
 |
 |
 |
 |
 |
 |
 |
 |
 |
 |
 |
 |
 |
 |
 |
 |
 |
 |
 |
 |
 |
 |
 |
 |
 |
 |
 |
 |
 |
 |
 |
 |
 |
 |
 |
|
|
|
|
|
|
|
|
|
|
|
|
|
|
|
|
|
|
|
|
|
|
|
|
|
|
|
|
|
|
|
|
|
|
|
|
|
|
|
|
|
|
|
|
|
|
|
|
|
|
|
|
|
|
|
|
|
|
|
|
|
|
|
|
|
|
|
|
|
|
|
|
Well regarded in the decades spanning the 19th and 20th centuries, the Flather Company was founded in 1875 by Edward W. Flather and his brothers William J. and Mark Jr. In its original form and based in Nashua, New Hampshire, the firm specialised in lathes, only later introducing planers and shapers - in which form, after incorporation in 1900, it continued as a going concern until the late 1920s. However, there was more than one Flather Company and one separate concern, the Flather Mfg. Co. (also of Nashua) was established by William's son - William himself leaving Flather & Co. in 1900 to join his offspring. As the main Company was already involved with larger lathes (their most famous being the unusual "circular gearbox" model an industrial-class engine lathe machine patented by Mr. Flather in April, 1895) the Flather Mfg. Co. must have decided to tackle the smaller end of the market. Their only known product to date was thus a little 7-inch swing (in reality with a 4-inch centre height) by 15 inches between-centres model - a machine now very rare indeed with just three so far discovered in the United States. Incorporating a number advanced features the lathe was featured in trade journals during 1919 (see at the bottom page) - though, of course, it may well have been in production for more than a year or two before that. No lightweight special for the amateur, this was a lathe that weighed, in bench form, 300 lbs, and with a specification and design details carefully thought out and every major component massively built. Looking remarkably like a scaled-down larger lathe, for its size and time this was indeed a good, solid job intended for serious professional use in a busy workshop. Enormously long and rigidly constructed, the headstock held a 3/4" bore carbon-steel spindle (with a relatively small 13/8" x 12 t.p.i. nose thread) running in parallel-bore bronze bearings retained by 2-bolt caps. The bearings were lubricated through simple but reliable twist-to-open "Winkley" oilers, a Detroit-manufactured item found in world-wide use on almost every conceivable type of mechanical device. Also constructed to a standard well beyond what might have been expected, the 3-step headstock pulley took a 1.25-inch wide belt and the 7 : 1 ratio 12 D.P. backgears were a full 1-inch wide - and obviously capable of sustained, hard use. Astoundingly for the class of machine, the headstock pulley had extended bosses on each end that ran in ball races - thus relieving the headstock spindle of the effects of belt pull. The bull-wheel had a handy spring-loaded, knurled-edge engagement pin that, with a pull and a twist, could be made to snap into and out of engagement with the cone pulley. Claimed spindle speeds in direct drive were high - the makers offering to gear the lathe so the top speed could be as fast as 2000 r.p.m. Interestingly, several aspects of the lathe were Dalton-like in their detail: the backgears and their arrangement; the particularly fine pitch (20 D.P.) changewheels (these even carrying the same form of casting number) and their (Dalton patent) method of retention by quickly-detachable threadless fasteners. These similarities might well have been the result of simple copying, some loose arrangement between the companies - or even the possibility of Dalton building a lathe for Flather to brand as their own. Unusually wide and with substantial V and flat ways, the bed had its underside parallel to the top (there was no fancy Victorian embellishment of curves) and two long cast-in feet at each end. The wide outside face of the front V-way was set at a much shallower angle than the shorter more upright inside face - a design feature employed by several makers in the 20th century, though without any agreement being reached as to its effectives in comparison with a conventional symmetrical V. With the ways arranged to continue for some distance past the front face of the headstock, the heavy saddle (complete with felt bed wipers) was able to be moved so that the cross slide (centrally positioned on the saddle) came right up to the spindle nose. Fitted with a large-section, full-length T slot running down the back of the bed, a taper-turning unit was offered as an extra - a useful feature in the days when such a lathe would have been called upon to perform a wide variety of tasks. To engage the unit, instead of the operator having to dismantle the cross-feed screw and nut, or employ a handy but expensive-to-produce telescopic screw and nut assembly, Flather used an ordinary screw (contained within the usual kind of housing) with the assembly held in place not by bolts or grub screws, but by a simple tab sliding in a vertical slot cut into the face of the saddle. The tab, secured by a hardened square-headed bolt, engaged with a cut-out in the underside of the cross-feed housing and held it in place. To engage the taper unit, was tab was slid downwards, so freeing the cross slide screw assembly and allowing it to move with the action of the slide. The arrangement also included a useful built-in threading stop and, because the feed screw was still attached to the cross slide, negated the need to use the top slide for feeding the cutting tool. Continued below:
|
|
|
|
|
|
|
|
|
|
|
|
|
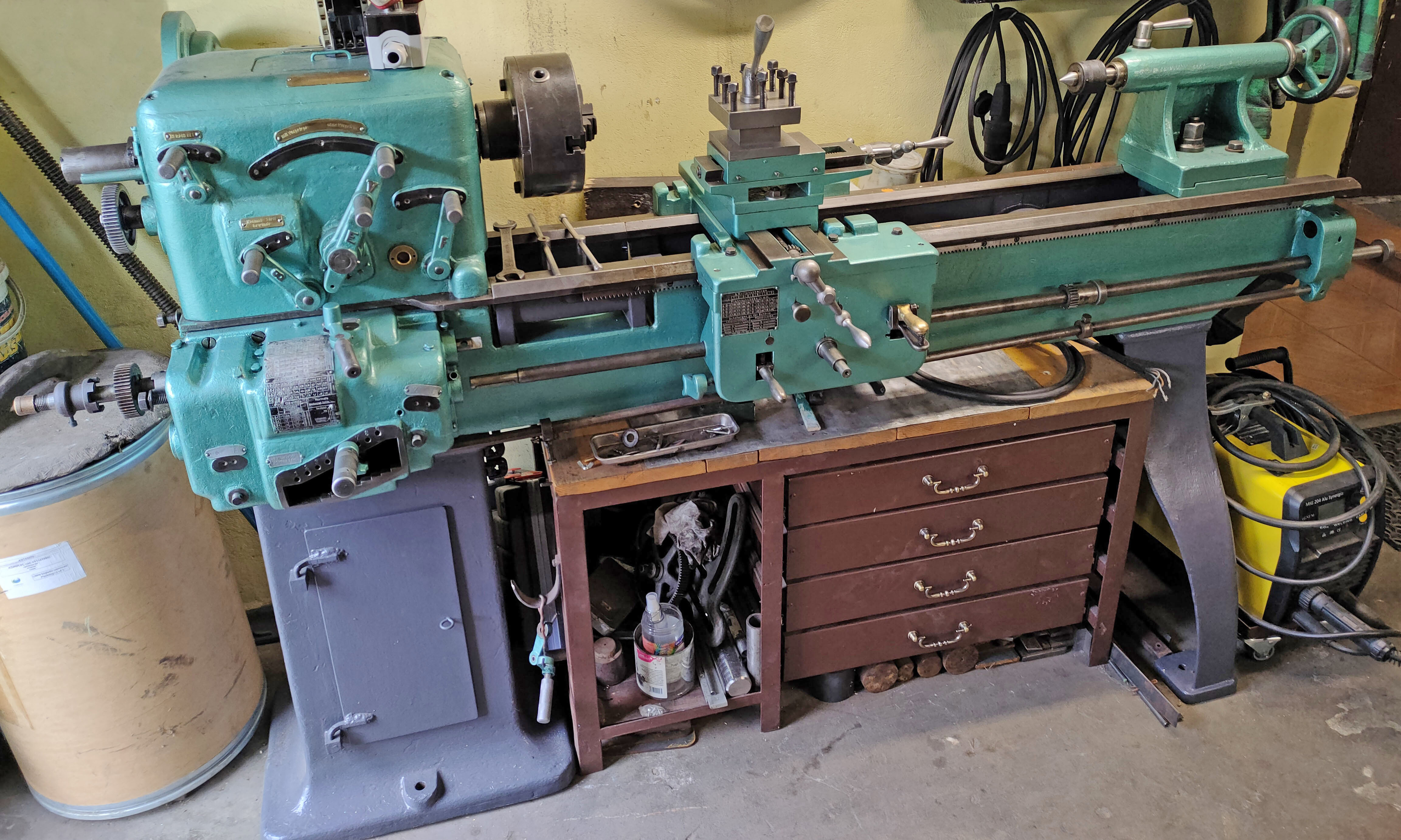 |
|
|
|
|
|
|
The solidly-built and now rare Flather 7-inch lathe circa 1919
|
|
|
|
|
|
|
|
|
Continued: Mounted on a rather short bracket - that would have prevented the assembly of a double-compound gear train for very fine feeds - the changewheels were driven through a tumble-reverse assembly. Instead of the expected square thread of relatively coarse pitch, the leadscrew had an Acme-form thread of an unusually fine, 10 t.p.i. pitch - this contemporary change from the use of "barley-sugar" leadscrews also being seen on machines produced by competing manufactures. The 13/16" diameter leadscrew carried a dog clutch at its headstock end coupled to a rod that automatically disengaged the longitudinal carriage feed; this wonderfully useful fitting allowed the operator to start a long cut and walk away - and, providing he remembered to set the stop and engage the mechanism, it would also have prevented any distraction (Martha Flint from the office was a favourite) from ruining a job. As an example of clever economy, the headstock-end leadscrew-bearing support bracket and dog clutch were formed as one bolt-on casting - with the upper surface being formed into a small tool tray. With reduction gearing between the carriage handwheel and bed-mounted rack, the Flather demonstrated yet another significant development in giving the operator better control of the cutting tool (no longer was an awkward-to-use, over-long crank handle fitted to a shaft with a gear connected directly to the rack). Of conventional design, the 5.5-inch travel cross slide and (1.5-inch travel) top slide both had small zeroing micrometer dials on their feed-screws - a considerable advance on most of the competition in this class. Fitted with a good-sized T-slot, the top slide took the usual form of quick-set, single-tool toolpost known in Europe as the American type. Locked by a cross-bed cam-lever with a permanently-fitted handle (no self-hiding spanners to waste time) the rugged-looking set-over tailstock used a generously-sized, slow-wearing 1/2" Acme-form thread to drive a 1 3/8" barrel with a No. 2 Morse taper socket. Unfortunately the barrel-locking arrangement was by that pitiful method - a slot in the casting closed down by a bolt. However, even here, things were better than might be expected and, to prevent too great a load being put on the casting the slot (made suitably long) was filled with a piece of metal that (economically) doubled as the barrel guide key. Inexplicably, there was no handle fitted to the tailstock handwheel, nor any knurling around its periphery to aid grip. With its "modern" features - sturdy build, backgear, screwcutting, geared-down hand carriage traverse, dog-clutch on leadscrew, tumble-reverse, guarded changewheels and fuss-free taper turning - even today this lathe would be a perfectly acceptable and useful machine. In order to appreciate what an advance in design and specification the little Flather 7-inch represented, an interesting comparison can be made with a model of similar capacity. the contemporary English Drummond 3.5-inch flat bed. If you have a Flather lathe of any description (especially this type, or the one with a "circular" screwcutting gearbox with multiple push-pull selectors) the writer would be very interested to hear from you..
|
|
|
|
|
|
|
|
|
|
|
|
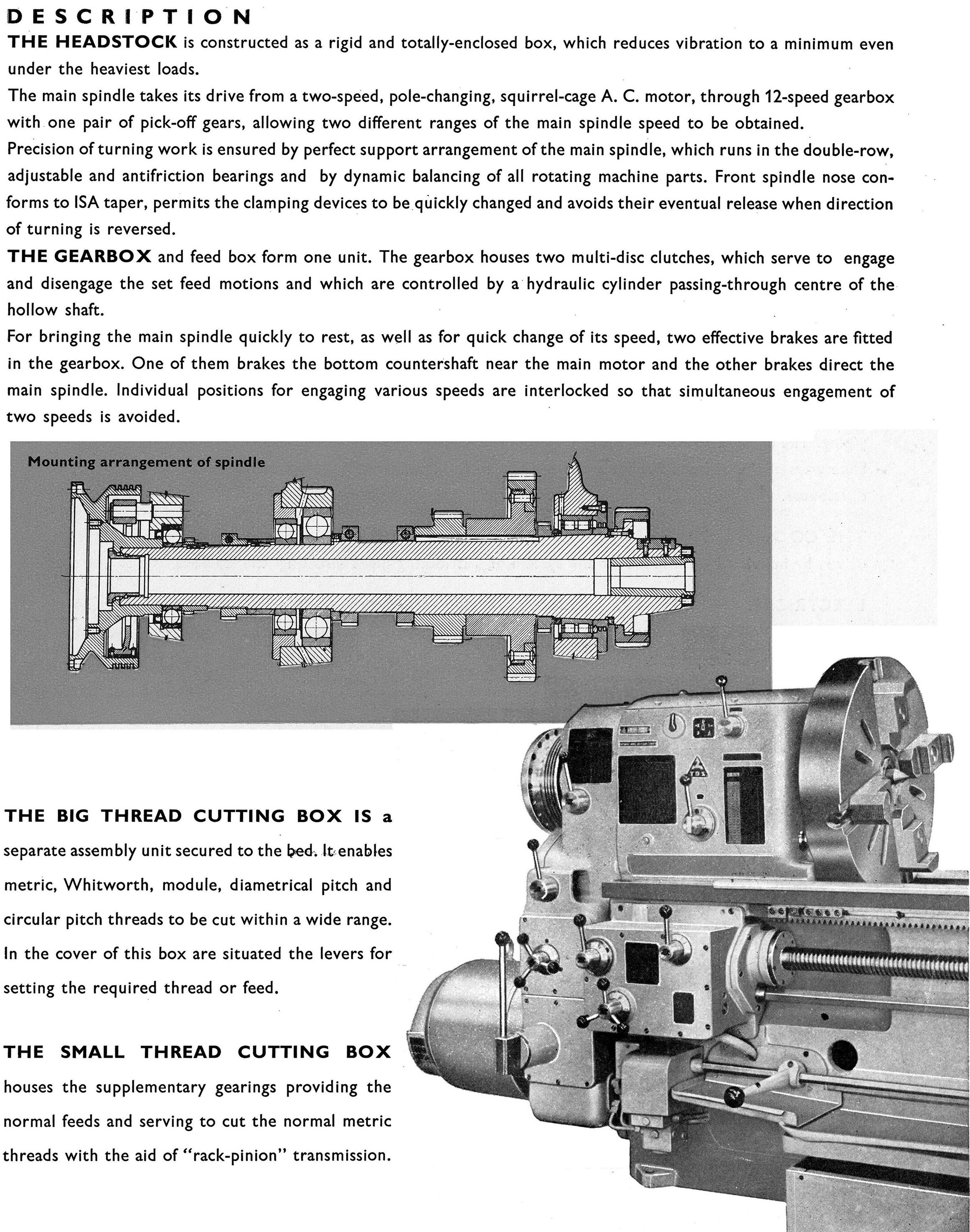 |
|
|
|
|
|
|
Judging by the large, full-length T slot running down the back of the bed, a taper-turning unit might well have been fitted as standard. The unit fitted to this lathe, whilst using the original mounting bracket, has a number of home-made components.
|
|
|
|
|
|
|
 |
|
|
|
|
|
|
The 12 D.P. backgears were a full 1-inch wide and obviously capable of sustained hard use. Also wider than usual for a lathe of this capacity, the headstock pulley took a belt 1.5-inches wide.
|
|
|
|
|
|
|
|
|
|
|
|
 |
|
|
|
|
|
|
For a small lathe the belt size was more than ample--as was the specification of the backgears
|
|
|
|
|
|
|
 |
|
|
|
|
|
|
The bull-wheel had a handy spring-loaded engagement pin that, with a pull and a twist, could be made to snap into and out of engagement with the cone pulley.
|
|
|
|
|
|
|
 |
|
|
|
|
|
|
The headstock was lubricated through simple but reliable "Winkley" oilers - a brand found in world-wide use on almost every conceivable type of mechanical device
|
|
|
|
|
|
|
|
|
|
|
|
 |
|
|
|
|
 |
|
|
|
|
|
|
To let the slide move when using taper turning, Flather used an ordinary screw (contained within the usual kind of housing) with the assembly being held in place by a simple tab sliding in a slot cut into the face of the saddle and engaging with a cut-out in the underside of the cross-feed holder.
|
|
|
|
|
|
|
 |
|
|
|
|
|
|
Small but readable micrometer dial on the cross-slide screw
|
|
|
|
|
|
|
|
|
|
|
|
 |
|
|
|
|
|
|
Too small and unreadable dial on the top slide - the graduations were just too close together
|
|
|
|
|
|
|
 |
|
|
|
|
 |
|
|
|
|
|
|
Of much finer pitch than usually fitted at the time (and of Acme form) the leadscrew carried a dog clutch at its headstock end coupled to a rod that automatically disengaged the longitudinal carriage feed
|
|
|
|
|
|
|
|
|
|
|
|
 |
|
|
|
|
|
|
A sign of times to come - changewheels safely enclosed within a cast-iron compartment
|
|
|
|
|
|
|
 |
|
|
|
|
|
|
|
|
|
Changewheels were held on studs that could be slackened and tightened from the front - so speeding up changes of feed rate or thread pitch
|
|
|
|
|
|
|
|
|
 |
|
|
|
|
|
|
|
|
|
As on early Sheldon lathes, changewheels were retained by quickly-detachable threadless fasteners
|
|
|
|
|
|
|
|
|
 |
|
|
|
|
|
|
Of conventional design, the cross and top slides both had small zeroing micrometer dials on their feed-screws - a considerable advance on most of the competition in this class. Fitted with a good-sized T-slot, the top slide took the usual form of quick-set, single-tool toolpost - known in Europe as the American type.
|
|
|
|
|
|
|
|
|
|
|
|
 |
|
|
|
|
|
|
Taper-turning unit: the original mounting bracket and (unusual circular) angle slide, but otherwise resurrected with home-made components
|
|
|
|
|
|
|
 |
|
|
|
|
|
|
Horrid close-down slot to lock the tailstock barrel - though at least the cut is long and the screw-abutment boss a reasonable size. The slot also holds the guide key for the barrel keyway
|
|
|
|
|
|
|
 |
|
|
|
|
|
|
|
|
|
 |
|
|
|
 |
|
|
|
|
|
|
|
|
 |
|
|
|
|
 |
|
|
|
|
 |
|
|
|
|
|
|
|
|
|
 |
|
|
|
|
 |
|
|
|
|
|
|
|
|
|
|
|