 |
 |
 |
 |
 |
 |
 |
 |
 |
 |
 |
 |
 |
 |
 |
 |
 |
 |
 |
 |
 |
 |
 |
 |
 |
 |
 |
 |
 |
 |
 |
 |
 |
 |
 |
 |
 |
 |
 |
 |
 |
 |
 |
 |
 |
 |
 |
 |
 |
 |
 |
 |
 |
 |
 |
 |
 |
 |
 |
 |
 |
|
|
|
|
|
|
|
|
|
|
|
|
|
|
|
|
|
|
|
|
|
|
|
|
|
|
|
|
|
|
|
|
|
|
|
|
|
|
|
|
|
|
|
|
|
|
|
|
|
|
|
|
|
|
|
|
|
|
|
|
|
|
|
|
|
|
|
|
|
|
|
|
|
|
|
|
Manufactured by C.B.Ferrari s.a.s. di R.Bianchi & Co. at via Mazzini, 58, Mornago (Varese) in Italy during the 1960s and 1970s, the M1R and M2R Precision Universal Milling Machines were a particularly well-made and interesting variation on the classic design of the more common models by Deckel, Maho and Thiel - a type that has found favour worldwide. While the vertical, T-slotted face of the knee - together with the availability of various bolt-on tables - was the same, instead of the main column containing a speed-change gearbox, with gear drive to demountable heads sitting above, Ferrari used a rather less versatile self-contained ram assembly, with a motor flange mounted at the rear. In its layout and operation this head closely resembled the units offered by makers such as Cincinnati, Parkson, Arno and Riva, etc., to convert their horizontal milling machines into ram-type verticals. Made from a high-strength cast iron, the main castings were first rough machined then heat treated and allowed to weather for between six and twelve months before final machining. Slideways were ground and then hand scraped - with gib strips made from heat-treated and nitrided steel to ensure an easy, sliding fit and long life. Like Deckel, Ferrari took trouble to ensure that the table ways were completely protected by being enclosed in bellows, as well as fitted with oil scrapers. Of identical design, the M1R and M2R differed only in the size of the main vertical table and its travels: that on former having dimensions of 725 x 215 mm (28.5" x 8.5") a longitudinal travel of 325 mm (12.8") and a vertical of 400 mm (15.75"). The table on the M2R was usefully larger being 850 x 225 mm (33.5" x 9") with a longitudinal travel of 400 mm (15.7") - or optionally of 450 mm (17.7") - and a vertical of 450 mm (17.7"). Each had 3 T-slots and powered feeds were fitted to all axes and driven by separate 0.5 h.p. DC motors under potentiometer control to give rates that were infinitely variable from 0 to 1000 mm (40") per minute. Electromagnetic clutches were used to provide an instantaneous engagement and stop to the table drives - with push-buttons used to select rapid feeds at the rate of 1500 mm (60") per minute on the longitudinal and cross and at a conservative (and safer) 375 mm (15") per minute vertically. Continued below:
|
|
|
|
|
|
|
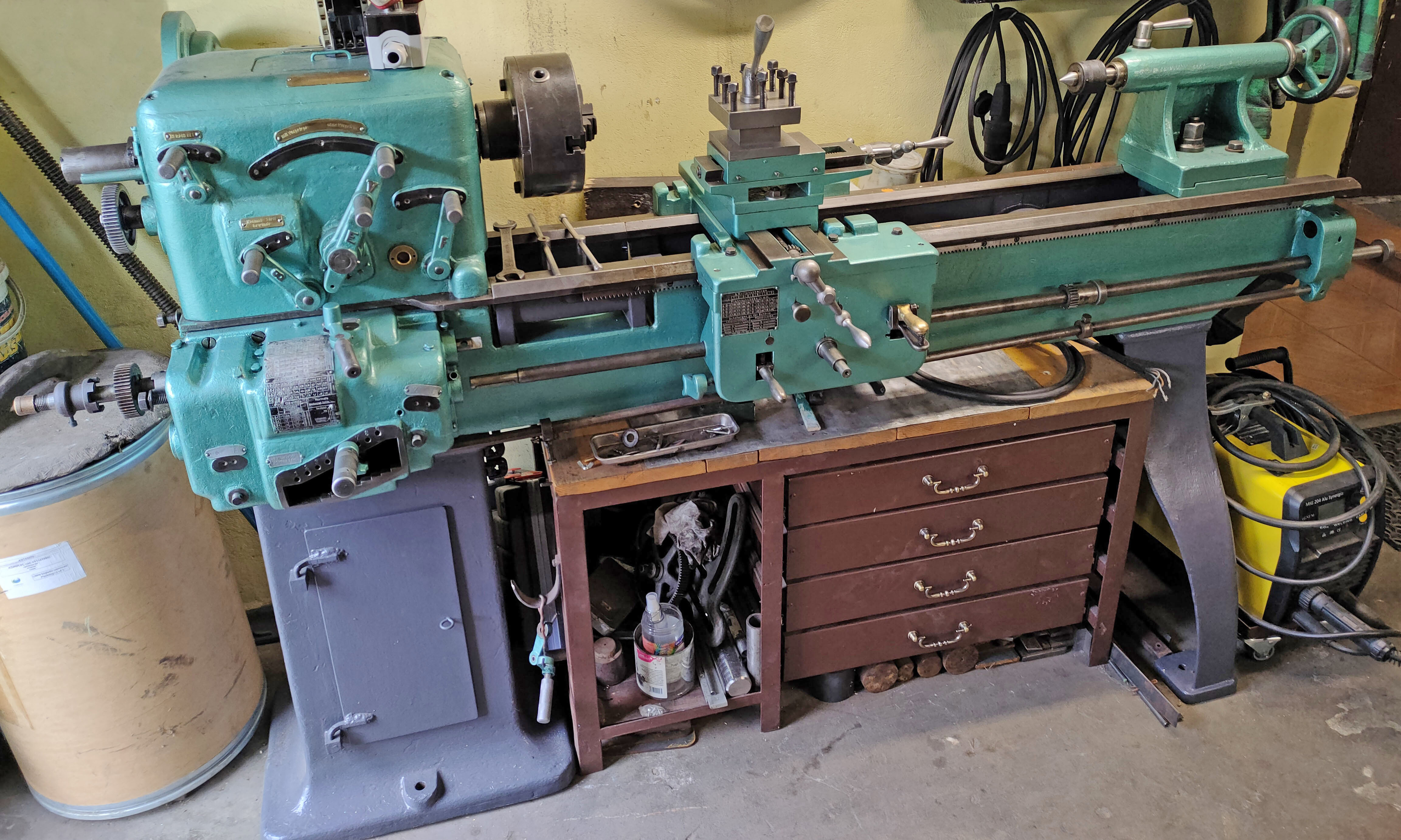 |
|
|
|
|
|
|
Ferrari M1R and M2R Universal precision Milling Machine
Continued: All feedscrews were in heat-treated, nickel-chrome steel with ground threads - and (most unusually) with a hard-chrome finish; the feed nuts on the horizontal and head screws were of the double type, adjustable to remove backlash while large, clearly engraved micrometer dials were given a non-glare, satin-chrome finish. Crisply engraved precision rulers were fitted to each axis, adjustable over a range sufficient to reset to a whole centimetre. The vertical screw, being heavily loaded, was run in an oil bath fed from a reservoir inside the column. With 450 mm of in and out travel, the standard head was fitted with a 4 h.p., 1500 r.p.m. motor and had 12 speeds from 60 to 1800 r.p.m. all gear-driven and controlled by just two levers on its right-hand face. Hardened, tempered and profile ground, the head gears ran on hardened and ground splined shafts turning in ball and roller bearings. Fitted with adjustable, precision taper roller bearings, the main spindle had an ISO 40 nose and 4 well-spaced tapped holes in its end flange to bolt on various types of head. As an option, another version of the head was available, the Type 2018. Easily recognisable by its backwards facing, large-frame, 3.5/4.2 h.p. 2-speed motor this had 24 speeds from 30 to 1800 r.p.m. - though one with higher rather than slower revolutions would have been more useful. Ensuring that the machine could be used to its full potential, a wide range of accessories was offered with three tables listed that could be carried on the vertical knee; these were: the 800 x 315 mm (31.5" x 12.5") Type 2010 Plain with 4 T-slots; the 700 x 315 mm (27.5" x 12.5") Type 2011 Universal Tilting that could be inclined 30° each side of its level position in three directions and the Type 2012 Auxiliary Box Table that was T-slotted on all 4 faces and with dimensions of 400 x 250 x 140 mm (15.8" x 10" x 5.5") Bolt-on attachments were available in several forms with the most basic, the Type 2009, being an overarm assembly with a drop bracket support on its outer end that allowed the machine to be used as a horizontal miller with a full-length horizontal cutter arbor. Four vertical heads were listed: the Type 2009 was a plain, heavy-duty type, with an ISO 40 spindle nose, no quill feed, fitted with an external, dynamically balanced flywheel and able to be inclined 90° each side of upright. As the head was driven at a 1:1 ratio, the 12 speeds were identical to the horizontal range - 60 to 1800 r.p.m. For drilling, boring and precision work the makers offered the Type 2040. This was identical in basic specification to the Plain Type 2009 (though the flywheel was omitted) and fitted with a simple, lever-operated quill that had a travel of 60 mm measured by vertical ruler engraved in mm. For complex angular work the Type 2041 Double-swivel Universal Head could be fitted. Able to be rotated through 360°, the spindle line was set just 40 mm from the face of the horizontal support and the 12 speeds spanned the usual 60 to 1800 r.p.m. All heads (and the tilting table) were provided with a degree-engraved, vernier-equipped scale that allowed angles to be set down to an accuracy of 5 minutes of arc. Continued below:
|
|
|
|
|
|
|
|
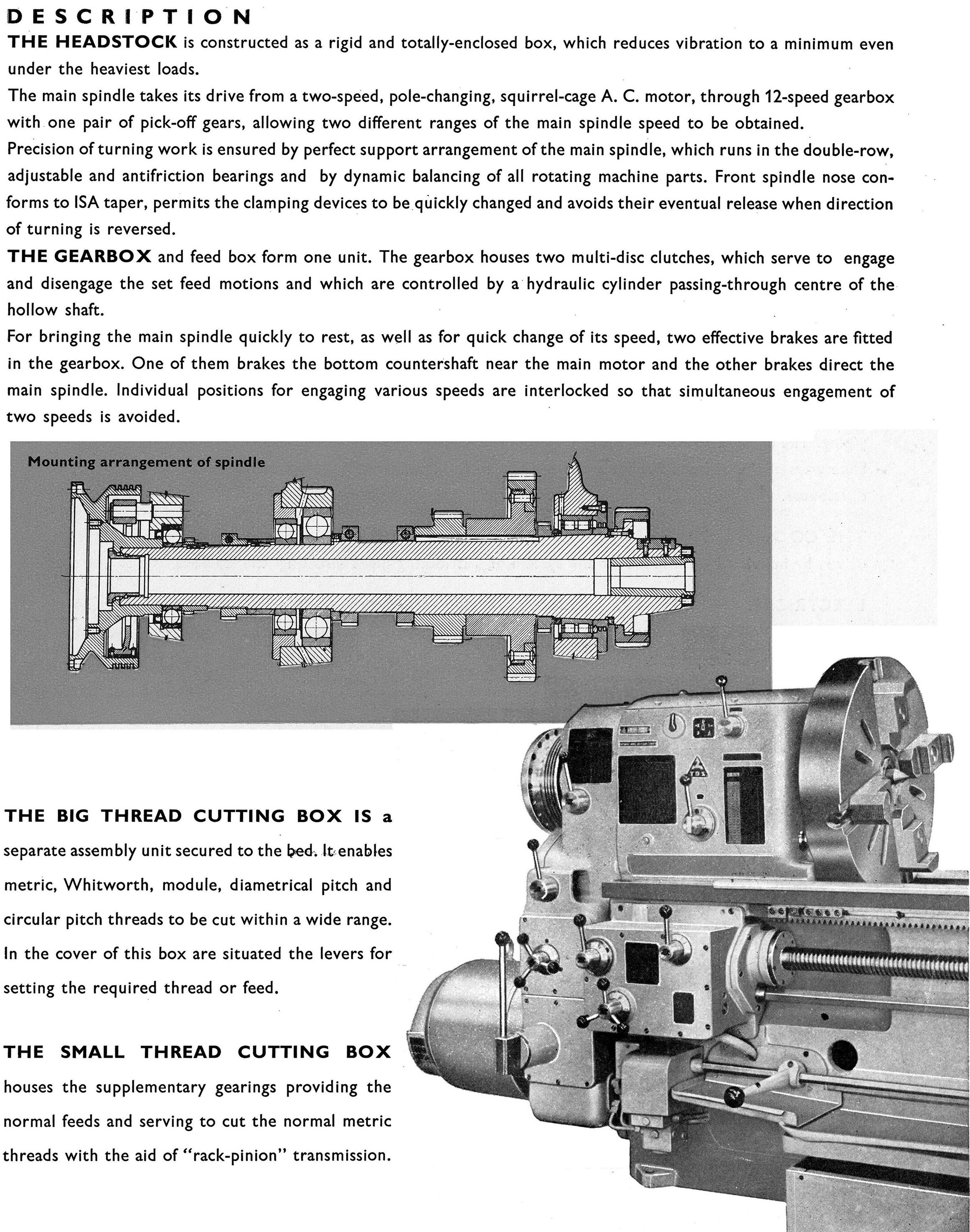 |
|
|
|
|
|
|
|
|
|
|
|
|
Continued: All the conventional heads were of robust construction, with their spindles running in taper roller bearings; however, the top speed of 1800 r.p.m. was rather low for the proper use of small cutters and, to compensate, Ferrari offered a Spindle Speed-multiplier that increased revolutions by a factor of five. Supplied in a fitted wooden box, the unit came with 5 collets able to hold cutters of: 3 to 4 mm, 5 to 6 mm, 7 to 8 mm, 9 to 10 mm and 11 to 12 mm. To compliment the Speed Multiplier, a Universal Head for Angles and Internal Surfaces Type 050401 was listed. This was driven by a small 0.18 h.p. motor and ran at speeds of 2000, 4000 and 6000 r.p.m. One very special fitting was the Type 2048 Cross Spindle Head. This turned the (60 to 1800 r.p.m.) drive through 90° to drive a small horizontal milling spindle (set across the face of the horizontal head) and could mount cutters up to 130 mm (5") in diameter and 100 mm (4") long. Other accessories included an Air-driven Grinding Head designed to run at 70,000 r.p.m. fro a 4 Kg/cm2 (60 p.s.i.) supply with an air consumption of 140 litres/min (5 c.f.m.); automatic, semi-automatic and universal boring and facing heads; the Type 050411 Semi-universal Dividing Head with Tailstock; the Type 050392 Simple Dividing Head with direct indexing; a precision boring spindle; mountings for dial indicators; a centring and setting microscope; a sine angle attachment with magnetic base; optical reading and setting equipment to measure table travel; tool and equipment cabinets and the expected range of machine vices (including a hydraulic version), table clamps, horizontal cutter and stub arbors, adaptors to mount Morse taper fittings, collet chucks in standard and quick-change fittings; drill chuck holders. Also offered was a special version of the miller, the type M2R-RQA - one of the first machines of this size and type to be offered with a fully integrated digital read-out system. *Proof of the type's success - the genus Precision Universal Milling Machine - is evident from the number of similar machines made in various countries including: Austria: Emco Model F3 Belgium: S.A.B.C.A. Model JRC-2 Czechoslovakia: TOS FN Models England: Alexander "Master Toolmaker" and the Ajax "00", an import of uncertain origin. Germany: Hahn & Kolb with their pre-WW2 Variomat model Wilhelm Grupp Universal- Fräsmaschine Type UF 20 N/120 Hermle Models UWF-700 and UWF-700-PH Leinen Super Precision Micro Mill Macmon Models M-100 & M-200 (though these were actually manufactured by Prvomajska); Maho (many models over several decades) Ruhla Rumag Models RW-416 and RW-416-VG SHW (Schwabische Huttenwerke) Models UF1, UF2 and UF3 Thiel Models 58, 158 and 159 Wemas Type WMS Italy: C.B.Ferrari Models M1R & M2R Bandini Model FA-1/CB and badged as Fragola (agents, who also sold a version of the Spanish Meteba). Japan: Riken Models RTM2 and RTM3 Poland: "Avia" and "Polamco" Models FNC25, FND-25 and FND-32 by Fabryka Obrabiarek Precyzyinych Russia: "Stankoimport 676" Spain: Metba Models MB-0, MB-1, MB-2, MB-3 and MB-4 Switzerland: Aciera Models F1, F2, F3, F4 and F5 Christen and Perrin Types U-O and U-1 (Perrin Frères SA, Moutier) Hispano-Suiza S.A. Model HSS-143 Luthy Mikron Models WF2/3S, WF3S, WF-3-DCM & WF-2/3-DCM Perrin Type U-1 Schaublin Model 13 and Model 22 The former Yugoslavia: Prvomajska (in Zagreb with Models ALG-100 and ALG200) Sinn Models MS2D & MS4D "Comet" Model X8130, imported to the UK in the 1970s by TI Comet. United States: Brown & Sharpe "Omniversal" Sloane & Chace in the USA produced a miniature bench version and at least five Chinese-built models have also been made, including one from the Beijing Instrument Machine Tool Works. A number of the "clones" merely followed the general Thiel/Maho/Deckel concept whilst others, like Bandini and Christen, borrowed heavily from Deckel and even had parts that were interchangeable. Should you come across any of these makes and models all will provide "The Deckel Experience" - though you must bear in mind that spares are unlikely to be available and, being complex, finely-made mechanisms, they can be difficult and expensive to repair..
|
|
|
|
|
|
|
|
 |
|
|
|
|
|
|
M2R: the 850 x 225 mm (33.5" x 9") vertical, knee-mounted table had three T-slots, a longitudinal travel of 400 mm (15.7") - or optionally of 450 mm (17.7") - and a vertical of 450 mm (17.7").
|
|
|
|
|
|
|
|
 |
|
|
|
|
|
 |
|
|
|
|
|
|
As an option, another version of the ram head was available, the Type 2018. Easily recognisable by its backwards facing, large-frame, 3.5/4.2 h.p. 2-speed motor this had 24 speeds from 30 to 1800 r.p.m. - though one with higher rather than slower revolutions would have been more useful.
|
|
|
|
|
|
|
|
 |
|
|
|
|
|
|
Optical reading and setting equipment to measure table travel;
|
|
|
|
|
|
|
|
 |
|
|
|
|
|
|
Ferrari Type M2R-RQA - one of the first machines of this size and type to be offered with a fully integrated digital read-out system..
|
|
|
|
|
|
|
|
 |
|
|
|
|
|
|
Arranged for horizontal milling with the Type 2009 bolt-on overarm extension
|
|
|
|
|
|
|
|
 |
|
|
 |
|
|
|
|
|
|
Head Type 2009. A plain, heavy-duty model with an ISO 40 spindle nose, no quill feed, fitted with an external, dynamically balanced flywheel and able to be inclined 90° each side of upright. As the head was driven at a 1:1 ratio, the 12 speeds were identical to the horizontal range - 60 to 1800 r.p.m.
|
|
|
|
|
|
|
|
Head Type 2040. Used for drilling, boring and precision work this was identical in basic specification to the Plain Type 2009 (though the flywheel was omitted) and fitted with a simple, lever-operated quill that had a travel of 60 mm measured by vertical ruler engraved in mm
|
|
|
|
|
|
|
|
 |
|
 |
|
|
|
|
|
|
|
|
|
Type 050401 Universal Head for Angles and Internal Surfaces was listed. Driven by a small 0.18 h.p. motor this ran at speeds of 2000, 4000 and 6000 r.p.m.
|
|
|
|
|
|
|
Type 2041 Double-swivel Universal Head. Able to be rotated through 360°, the spindle line was set just 40 mm from the face of the horizontal support with 12 speeds spanning 60 to 1800 r.p.m.
|
|
|
|
|
|
|
|
|
|
 |
|
|
|
|
|
|
|
|
|
|
|
|
One very special fitting was the Type 2048 Cross Spindle Head. This turned the (60 to 1800 r.p.m.) drive through 90° to drive a small horizontal milling spindle (set across the face of the horizontal head) and could mount cutters up to 130 mm (5") in diameter and 100 mm (4") long.
|
|
|
|
|
|
|
|
|
|
|
|
|
 |
|
 |
|
|
|
|
|
|
|
|
Air-driven Grinding Head designed to run at 70,000 r.p.m. fro a 4 Kg/cm2 (60 p.s.i.) supply with an air consumption of 140 litres/min (5 c.f.m.)
|
|
|
|
|
|
|
|
|
|
|
|
|
|
|
|
|
 |
|
|
|
|
|
|
|
|
Spindle Speed-multiplier. This unit increased revolutions by a factor of five and was supplied in a fitted wooden box. 5 collets were provided able to hold cutters of: 3 to 4 mm, 5 to 6 mm, 7 to 8 mm, 9 to 10 mm and 11 to 12 mm.
|
|
|
|
|
|
|
|
|
|
|
|
|
 |
|
|
|
|
|
|
Type 2010 Plain table 800 x 315 mm (31.5" x 12.5") with 4 T-slots
|
|
|
|
|
|
|
|
 |
|
|
|
|
|
|
Type 2011 Universal Tilting 700 x 315 mm (27.5" x 12.5") and able to be inclined 30° each side of its level position in three directions
|
|
|
|
|
|
|
|
 |
|
|
|
|
|
|
|
Type 2012 Auxiliary Box Table 400 x 250 x 140 mm (15.8" x 10" x 5.5") T-slotted on all 4 faces
|
|
|
|
|
|
|
|
|
|
|
|
|
 |
|
|
|
|
|
|
|
|
Rotary table with dividing plate
|
|
|
|
|
|
|
|
|
|
|
|
|
 |
|
|
|
|
|
|
Type 050411 Semi-universal Dividing Head with Tailstock
|
|
|
|
|
|
|
|
 |
|
|
|
|
|
|
|
|
|
|
|
|
|
|
|
|
|
|
|