 |
 |
 |
 |
 |
 |
 |
 |
 |
 |
 |
 |
 |
 |
 |
 |
 |
 |
 |
 |
 |
 |
 |
 |
 |
 |
 |
 |
 |
 |
 |
 |
 |
 |
 |
 |
|
|
|
|
|
|
|
|
|
|
|
|
|
|
|
|
|
|
|
|
|
|
|
|
|
|
|
|
|
|
|
|
|
|
|
|
|
|
|
|
|
|
|
|
|
|
|
|
|
|
|
|
|
In Germany there were two machine-tool companies with the name Weisser: Johann Georg Weisser of St.Georgen in the Black Forest (also listed as J.G.Weisser Söhne and founded in 1856) and, the subject of this page, Eugen Weisser from Heilbronn. During the 1930s and 1940s, with fierce completion in the conventional lathe market, the German Eugen Weisser Company had, in addition to conventional lathes, cleverly made a name for themselves in the manufacture of machines dedicated to the production of piston, con-rod and other engine parts. They also specialised in high-speed production lathes that used gearless (belt-drive) headstocks that were particularly smooth running and able to produce a superior, mirror-like surface finish that required no further work before being built into a finished mechanism. While, at the time, a small capstan or automatic lathe was normally chosen for the mass production of smaller parts, these required expensive tooling and setting up by skilled workmen; if the job was for fewer than a run of 250 or so (especially if the parts were longer and larger) if was often cheaper and more convenient to used a modified centre (engine) lathe or, better still, a machine designed especially for such work - the interesting and unusual American Porter Cable/W.C.Lipe being an early and very successful, long-lived example. Introduced during the late 1940s and selling well by the early 1950s (with some customers ordering batches of up to fifty at a time), the 6.5" x 20" Weisser PZ-165 was a lathe of seemingly ordinary appearance yet capable of high-speed production using unskilled or semi-skilled labour while also doubling up a conventional (though non-screwcutting) centre lathe. Constructed as a sturdy box reinforced with straight and diagonal ribs, the bed was very deep and fitted with V and flat ways and cast-in chip chutes. It was carried on separate headstock and tailstock plinths, the former having the 4 or 5 h.p. double-squirrel cage motor flange mounted on the outside of its right-hand face. Designed for 200 switching actions per hours, at extra cost the standard motor could be replaced by one that allowed up to twice as many. Drive to the internally mounted, oil-bath gearbox was through what the makers described as an "elastic clutch" - a form of flexible coupling designed to smooth the drive. Controlled by two concentrically-mounted levers, the twelve speeds normally specified were: 120, 150, 190, 240, 300, 375, 475, 600, 750, 950 1200 and 1500 r.p.m. However, at extra cost both higher and lower ranges were available - the latter by altering the ratio of the headstock-mounted backgears. For the set of six higher speeds drive to the headstock spindle was, as might be expected, by three V-belts direct from the output clutch on the gearbox - and through backgear for the lower six. Continued below:
|
|
|
|
|
|
|
|
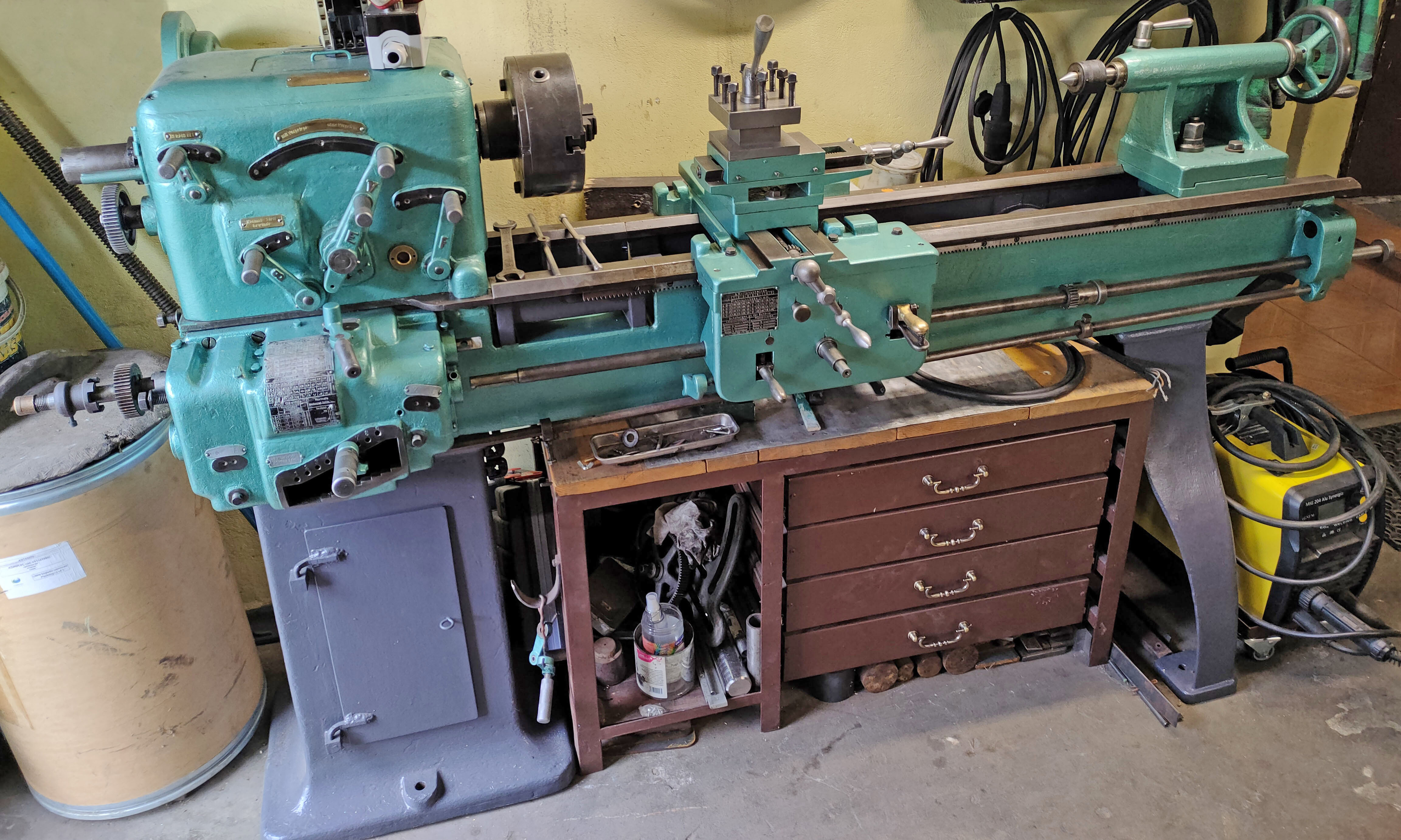 |
|
|
|
|
|
|
Weisser PZ-165 as made circa late 1940s and early 1950s
|
|
|
|
|
|
|
|
|
|
|
|
|
|
|
Continued: To ensure the smoothest possible running the headstock spindle, together with all its rotating parts was dynamically balanced. Hardened and ground (and precision lapped on the front journal), it was bored through 1.06", had a No. 4 Morse taper socket and a screwed spindle nose. The plain front bearing, fed from a circulation oil bath, had a parallel bore and tapered outside, by which means it could be drawn into the casting and the running clearance adjusted by closing down a slit along its length. As an extra-cost option the customer could specify a spindle whose front bearing consisted of two precision ball races - in which case the drive system was modified to give a speed range from 190 to 2400 r.p.m. The rear of the spindle was supported in ball bearings, with a pair of ball races to take the thrust. Interestingly (and happily for the maintenance department), the V-belts could be changed without dismantling the headstock (an arrangement also found on the Hardinge HLV-H lathe), slots being provided in the upper and lower sections of the headstock casting that allowed the belts to be hooked into place. Bolted to the bed immediately below the headstock was the splash-lubricated feeds' gearbox with all its gears hardened and ground and mounted on shafts running in ball races. The box, driven by three V-belts from a pulley overhung on the end of the headstock spindle, was claimed to provide an absolutely slip-free drive, even under the heaviest of cuts. Six rates of sliding and surfacing feeds were available, the former at 0.00157" to 0.01575" per revolution of the headstock spindle and the latter half as fast i.e. 0.00079" to 0.00787". Double-walled and sealed, the apron was reputed to be leak-proof and formed with an oil sump in its base with a pressure pump to take lubricant to the bed and cross-slide ways. Drive from the feeds' gearbox came via a slotted rod (there was no leadscrew) with a key driving the enclosed worm-and-wheel mechanism. All gears were, as might be expected, hardened and ground and supported, if running at higher speeds, on shafts running in ball races. An important feature of the lathe was the patented automatic-disengage mechanism that worked at the lightest touch, in both directions, on both carriage and cross slide. To hold the carriage stop (a micrometer type accurate to within 0.000394" (0.01 mm)) a separate rail was provided in front of the bed's front V-way, an arrangement that also allowed the fitting of special or custom-made high precision stops. As part of the standard specification, the long cross slide had two T-slots machined into its rear half that allowed the mounting of a second top slide - as well as connecting to the taper-turning attachment. Micrometer dials were engraved with crisp divisions, fitted with knurled rings and twin opposed pin-spanner ring nuts used to adjust out backlash between outer sections of the screw assembly and the dial components. As the inner, fixed section of the cross slide micrometer dial abutted against and rose above the face of the apron, as the slide was drawn backwards its movement was limited by contact with this part. If a simple extension section had been arranged to carry the end of a lengthened screw (as seen for example on the Myford Series 7 lathes) the slide's travel could have been usefully extended. Rather oddly, on early versions of the lathe, the 360° swivelling top slide had its feed-screw offset to the left of the centre line - an error corrected on later machines. The slide was held to the cross slide by two nuts in a circular T-slot and came equipped with a single toolpost, though others, including a rather fine indexing 4-way type with hardened clamping screws and internal workings, were available to special order. Entirely conventional, the tailstock had a 2.04" diameter spindle and a No. 4 Morse taper; it was locked to the bed by a lever-operated eccentric cross shaft with an additional clamping plate provided for really heavy work. Supplied as standard with each new machine were: a complete electrical installation, ready to run; two Morse centres; speed and feed tables; a drive plate with safety shielding; one micrometer stop for the carriage feed; a stop for the cross feed; chip tray; wrenches and an operator's handbook. A number of accessories were offered including: collet chucks to screw on to the spindle nose together with the usual range of round, square and hexagon collets; coolant equipment; a standard 6.3-inch 3-jaw chuck (interestingly of American manufacture, by Cushman); a special 6.3-inch 3-jaw chuck by Wescott with jaws that could be adjusted simultaneously for concentric turning or individually for eccentric work; a precision 6.3-inch 3-jaw chuck by Forkadt; a second top slide for to mount on the rear of the cross slide; multiple tool holders on a special base for use on the rear of the cross slide (as shown in the picture immediately below); a taper-turning attachment; an instrument housing with rev counter and ammeter to mount on the headstock; a rotating tailstock centre with precision ball bearings; a tailstock spindle with a precision rotating centre built in; a rotating carriage stop with several individually adjustable stops; DC instead of AC electrical equipment; fixed and travelling steadies; a machine lamp and a Kienzle speed indicator for the selection of the correct cutting rates..
|
|
|
|
|
|
|
|
|
|
|
|
|
|
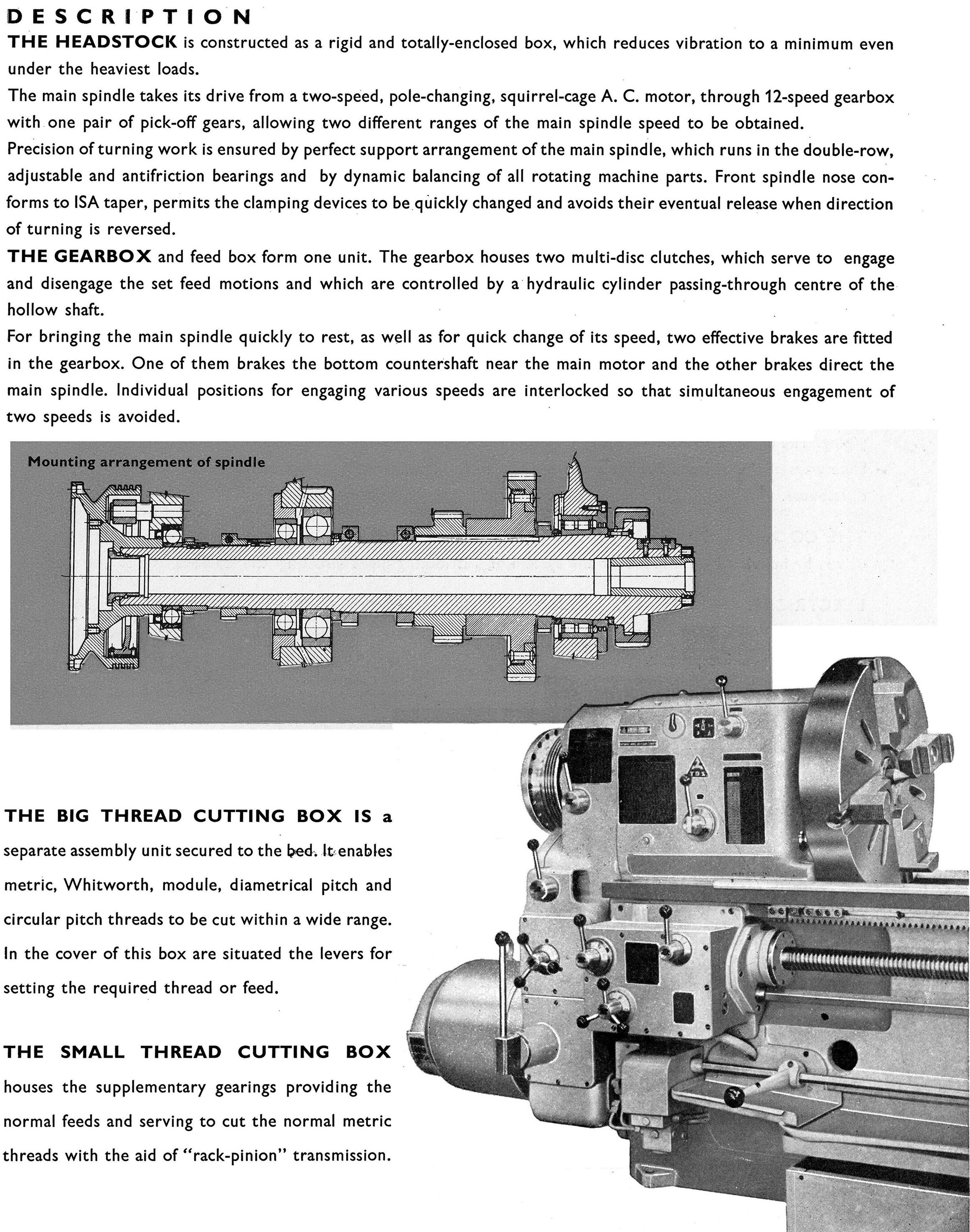 |
|
|
|
|
|
|
Weisser PZ-165 fitted multiple tool holders on a special base at the rear of the cross slide
|
|
|
|
|
|
|
|
 |
|
|
|
|
|
 |
|
|
|
|
|
|
Weisser PZ-165 fitted with two top slides and a taper-turning attachment
|
|
|
|
|
|
|
|
|
|
|
|
|
|
 |
|
|
|
|
|
|
As part of the standard specification, the long cross slide had two T-slots machined into its rear half that allowed the mounting of a second top slide - as well as connecting to the taper-turning attachment. Micrometer dials were engraved with crisp divisions, fitted with knurled rings and twin opposed pin-spanner ring nuts used to adjust out backlash between outer sections of the screw assembly and the dial components. As the inner, fixed section of the cross slide micrometer dial abutted against and rose above the face of the apron, as the slide was drawn backwards its movement was limited by contact with this part.
|
|
|
|
|
|
|
|
 |
|
|
|
|
|
|
Constructed as a sturdy box reinforced with straight ribs, the bed was very deep and fitted with V and flat ways and cast-in chip chutes.
|
|
|
|
|
|
|
|
 |
|
|
|
|
|
|
Section through headstock and spindle
|
|
|
|
|
|
|
|
|
|
|
|
|
|
 |
|
|
|
|
|
|
Double-walled and sealed, the apron was reputed to be leak-proof and formed with an oil sump in its base with a pressure pump to take lubricant to the bed and cross-slide ways. Drive from the feeds' gearbox came via a slotted rod (there was no leadscrew) with a key driving the enclosed worm-and-wheel mechanism. All gears were, as might be expected, hardened and ground and supported, if running at higher speeds, on shafts running in ball races.
|
|
|
|
|
|
|
|
 |
|
|
|
|
|
 |
|
|
|
|
|
|
Eugen Weisser Factory - probably in the late 1940s
|
|
|
|
|
|
|
|
|
|
|
|
|
|
 |
|
|
|
|
|
 |
|
|
|
|
|
|
|
|
|
A conventional geared-head screwcutting Eugen Weisser lathe from the 1950s
|
|
|
|
|
|
|
|
|
|
|
|
|
|
|
|
|