 |
 |
 |
 |
 |
 |
 |
 |
 |
 |
 |
 |
 |
 |
 |
 |
 |
 |
 |
 |
 |
 |
 |
 |
 |
 |
 |
 |
 |
 |
 |
 |
 |
 |
 |
 |
 |
 |
 |
 |
 |
 |
 |
 |
 |
 |
 |
 |
 |
 |
 |
 |
|
|
|
|
|
|
|
|
|
|
|
|
|
|
|
|
|
|
|
|
|
|
|
|
|
|
|
|
|
|
|
|
|
|
|
|
|
|
|
|
|
|
|
|
|
|
|
|
|
|
|
|
|
|
|
|
|
|
|
|
|
|
|
|
Dean Smith & Grace, founded in 1865, had a formidable reputation in the field of high-quality machine tools. More than once their products have been called the "Rolls-Royce" of lathes - being beautifully made, from superior materials, and to a carefully considered design that took account of both the operator's needs and the sometimes conflicting needs of his employer. These were machine tools with a long, accurate and productive life. Despite being reformed in their later years after various financial troubles, the manufacturing branch of the company no longer trades; the original company was conservative, paternalistic and set the highest possible standards in every field - from the sublime to the faintly ridiculous. Apprenticeships were rigorous and the boys encouraged to continue their studies once outside their "time"; a tight control was kept on metallurgy by the in-house foundry (which also took on larger jobs for other local firms); most of the cutting tools were made in-house and even hammers specially made, the heads shaped from aged rail tracks. The canteen cutlery was stamped "DSG" and the appearance of the work-force was also special - at one time their overalls (white starched) being made to measure for each man by the tailors Speak's of Keighley, a specialist firm who made a range of garments including. 'heavy-duty' trousers. The latter must have been particularly hard-wearing. a retired employee mentioning to the writer in 2015 that he was still able to fit into his made-to-measure pair, bought in 1965 for £5 (despite several knee-patches). DSG only made larger lathes, with, for example, their 1940s range beginning with the "13-inch" (6.75" actual centre height). However, even this comparative "baby" by DSG standards was still built with no compromises as to weight or specification; it was offered in two bed lengths, with between-centres capacities of 30 and 42 inches. The short-bed version, at 3920 lbs, weighed within a whisker of a figure some three times that of a Colchester Student - and was even 80% heavier than the latter maker's 15-inch Triumph model; Dean, Smith and Grace concerned themselves only with Very Serious Machinery. With its patented "Fastlock" nose, the headstock spindle of the 13-inch was bored to clear bar up to 1.5" in diameter and ran on either precision Timken taper roller or plain bearings - in the latter case the front bearing was 3.5 inches in diameter and 4 inches long - with a mid-point bearing to add stiffness. A 5 h.p. motor gave twelve speeds, through multi V-belts (a flat belt was optional), from either 16.8 to 750 rpm or 22.5 to 1000 rpm. The roller-bearing spindle model was available with just one speed range of 31 to 1400 rpm. Like all DSG lathes, the bed was protected from swarf by long (American) Hendey-like covers that extended from both the front and back edges of the saddle. Removing the covers allowed the lathe to swing an extra 2 inches over the saddle - but the effect on turning capacity by removing the bed guards is not recorded. Combined with a huge, 1.5-inch diameter leadscrew, the screwcutting gearbox generated forty-one different pitches from 2 to 64 t.p.i together with (via a separate power shaft) forty-one different sliding feeds of 20 to 640 cpi and forty-one surfacing feeds of 30 to 960 cpi. To cut the full threading range, and to extend it to inch pitches up to 1", it was necessary to bring into play one or more of the five extra changewheels and a "free-wheel" supplied with the lathe. Both headstock and tailstock accepted No. 3 Morse taper centres, the former with a sleeve adaptor. Supplied as standard with the lathe were: a 4-way toolpost, catchplate, 12-inch diameter faceplate, fixed steady with a 5-inch diameter capacity, a drill holder with a No. 4 Morse socket, suds tray, splashback and a set of spanners. Optional equipment included a larger 6-inch capacity fixed steady, coolant, a travelling steady, taper-turning attachment, extra changewheels to generate metric, diametral, module, B.A. or other threads, an automatic trip mechanism for the longitudinal carriage feed, a micrometer carriage stop and the usual range of 3 and 4-jaw chucks and collets..
|
|
|
|
|
|
|
|
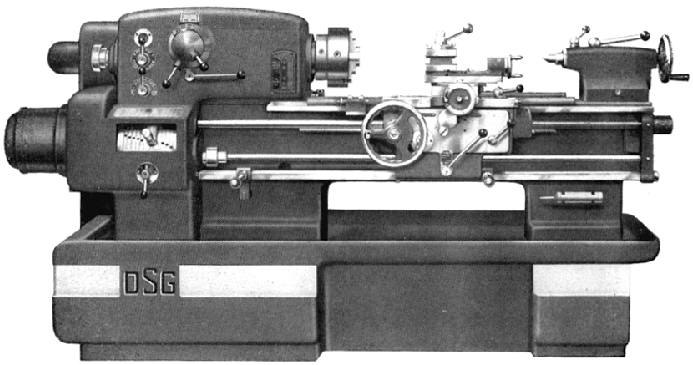 |
|
|
|
|
|
|
|
|
|
|
|
|
13" x 30" Dean Smith & Grace
The popular and long-lived 15" & 17" Dean Smith & Grace lathes (illustrated below) were substantially different to their smaller 13-inch brother, with apron and headstock controls of a distinctive design and with the option of a detachable-gap bed with a capacity of 25.5 inches in diameter by 7.25 inches wide. These models were available, initially, in just one bed length which allowed 36 inches to be admitted between centres. The makers models' names, "15-inch" and "17-inch" underplayed the machines' capacity, for each was capable of swinging one inch more over the bed if the long swarf guards, which extended well forward from the leading edge of the saddle, were removed Like the 13-inch lathe the three-bearing headstock spindle, with its patented "Fastlock" nose, could be ordered with either plain or roller bearings but, with a through capacity of 2.5-inches and plain bearings of 4.625 inches in diameter by 6 inches long, this was a much more massive structure. A 7.5 hp motor, driving via multi V-belts, gave eighteen forward and six reverse speeds - with the plain-bearing model capable of running from 7.8 to 720 rpm and the roller bearing version with a choice of either 9.8 to 900 rpm or 13.4 to 1230 rpm. When used with the three extra changewheels supplied with the lathe the screwcutting gearbox (driving through a 1.625-inch diameter leadscrew) was able to generate forty-nine pitches from 2 to 128 t.p.i. An extra six changewheels (supplied at extra cost) allowed inch pitches of up to 5" to be cut, together with metric threads from .5 mm to 130 mm. In addition, forty-nine sliding feeds of 14.5 to 920 cpi and 41 surfacing feeds of 29 to 1840 cpi. were provided by a separate power shaft, the direction of rotation of which could be reversed by a control lever mounted on the right-hand edge of the apron. Both headstock and tailstock accepted No. 4 Morse taper centres, the former with a sleeve adaptor. Supplied as standard with the lathe was a coarse-pitch screwcutting arrangement, feed reverse within the apron, 4-way toolpost, catchplate, 16-inch diameter faceplate, fixed steady with a 5-inch diameter capacity, No. 4 Morse centres, a drill holder with a No. 4 Morse socket, suds tray, splashback and a set of spanners. Optional equipment included a detachable-gap bed, coolant, larger 7-inch capacity fixed steady, a three-point travelling steady, 24 inch (15-inch swing) and 27 inch (17-inch swing) faceplates, taper-turning attachment, extra changewheels to generate metric, diametral, module, B.A. or other threads, an automatic trip mechanism for the longitudinal carriage feed, a micrometer carriage stop and the usual range of 3 and 4-jaw chucks, collets and steadies..
|
|
|
|
|
|
|
|
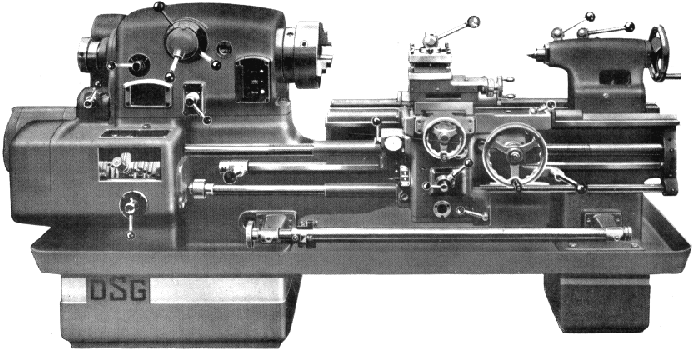 |
|
|
|
|
|
|
15" & 17" x 36" Dean Smith & Grace
|
|
|
|
|
|
|
|
|
|
|
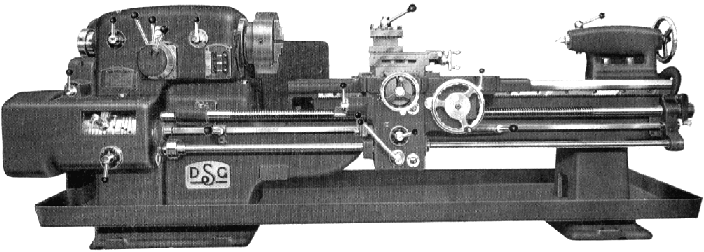 |
|
|
|
|
|
|
|
|
|
18 & 21-inch Dean Smith & Grace
Both very heavy machines, the 18" & 21" Dean Smith & Grace lathes were superbly made and capable of lasting for decades if well maintained. Both lathes were available with a standard between-centres capacity of 48 inches with either a straight bed, or one with a gap having the capacity to take a piece of material 32 inches in diameter by 10.25 inches thick. Long-bed models were also available to special order in which the capacity rose in increments of 12 inches - to a maximum of 240 inches. Again, as on the smaller lathes, the real swing was greater than that suggested by the model names. The "18-inch" version would turn 20" in diameter over the bed covers - whilst the "21-inch" managed to accommodate 22.5 inches. Like other DSG lathes of the period the headstock spindle could be ordered with either plain or roller bearings. The spindle and its three bearings - the front plain one was six inches in diameter and over six inches long - were of ample proportions - and bored through to pass a 3.5-inch diameter bar. A 12.5.5 hp 1440 rpm motor, driving through multi V-belts, gave eighteen forward and six reverse speeds, with the plain bearing model able to run from 5.3 to 420 rpm (or 7.5 to 600 rpm) and the roller bearing version (only) from 10 to 800 rpm. When used with the three extra changewheels supplied with the lathe, the screwcutting gearbox (driving a 2-inch diameter leadscrew) was able to generate forty-nine pitches from 1 to 64 t.p.i. An extra six changewheels (supplied at extra cost) allowed inch pitches up to 8" to be cut, together with metric threads from .5 mm to 200 mm. In addition, 49 sliding feeds of 12.5 to 800 cpi and forty-one surfacing feeds of 25 to 1600 cpi. were provided by a separate power shaft, the direction of rotation of which could be reversed by a control lever mounted on the right-hand edge of the apron. Both headstock and tailstock accepted No. 4 Morse taper centres, the former with a sleeve adaptor. Supplied as standard with the lathe were: a coarse-pitch screwcutting arrangement, feed reverse within the apron, 4-way toolpost, catchplate, 18-inch diameter faceplate for the 18-inch model, 22-inch faceplate for the 21-inch model, fixed steady with a 7-inch diameter capacity, No. 4 Morse centres, a drill holder with a No. 4 Morse socket, suds tray, splashback and a set of spanners. Optional equipment included a detachable-gap bed of any length (in 12-inch increments) up to 240 inches between centres, coolant, a larger 10-inch capacity fixed steady, a three-point travelling steady, larger faceplates of 30 inch diameter for the 15-inch swing lathe and 33 inch diameter for the 17-inch model, taper-turning attachment, six extra changewheels for inch and mm pitches, additional changewheels to generate metric, diametral, module, B.A. or other threads, an automatic trip mechanism for the longitudinal carriage feed, electric "quick power" traverse to the carriage, special tailstock with a built-in revolving centre, single pulley (flat belt) drive. from the motor, a micrometer carriage stop and the usual range of 3 and 4-jaw chucks, collets and steadies..
|
|
|
|
|
|
|
|
|
|
|
|
|
|
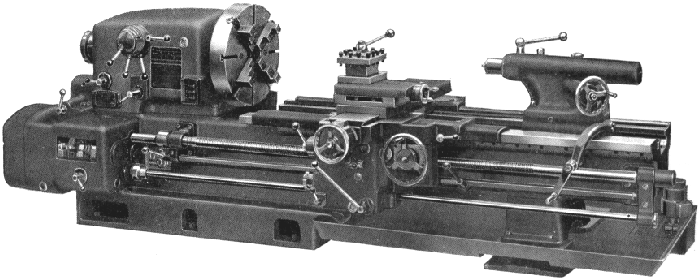 |
|
|
|
|
|
|
|
|
|
22 & 25-inch Dean Smith & Grace
Of generally similar layout to the 18 and 21-inch lathes, the 22" & 25" Dean Smith & Grace models had modifications designed to both take account of the greatly increased mass of the lathe and assist the operator in physically handling a much larger machine. More robust supports were provided beneath the headstock, a patent roller-bearing support was fitted to the saddle, a hydraulically operated self-adjusting clutch engaged the drive and a handle was provided to wind the heavy tailstock along the bed. Both lathes were available with the option of either a straight or a detachable-gap bed - with a capacity within the gap of 38 inches in diameter by 12.5 inches wide. The standard between-centres distance was 60 inches - but models could be ordered which had bed lengths which rose in increments of 12 inches to a maximum capacity of 240 inches. Again, as on other DSG lathes, the real swing was greater than that suggested by the model names. The "22-inch" version would turn 24 inches in diameter over the bed-protection bed covers and the "25-inch" model 26.5 inches. Even at this size the 4.125-inch bore headstock spindle could be specified with either plain or roller bearings. The spindle and its bearings (the plain ones were 6.75 inches in diameter and over seven inches long) were massively strong; an additional bearing in the middle of the spindle stiffened the whole headstock assembly. A 12.5 hp 1440 rpm motor, driving through multi V-belts, gave twenty-four forward and twelve reverse speeds, with both the plain and roller bearing models able to run from 5.4 to 420 rpm and, additionally, the roller bearing version from 7.6 to 600 rpm. The screwcutting gearbox, when used with the three extra changewheels supplied with the lathe, allowed the 2-inch diameter leadscrew to generate 49 different threads from 1 to 64 t.p.i. An extra six changewheels (supplied at extra cost) allowed inch pitches up to 8" to be cut, together with metric threads from .5 mm to 200 mm. In addition, 49 sliding feeds of 12.5 to 800 cpi and 41 surfacing feeds of 25 to 1600 cpi. were provided by a separate power shaft, the direction of rotation of which could be reversed by a control lever mounted on the right-hand edge of the apron. The headstock and tailstock both accepted No. 5 Morse taper centres, the former with a sleeve adaptor. Supplied as standard with the lathe were: a coarse-pitch screwcutting arrangement, feed reverse within the apron, 4-way toolpost, catchplate, 24-inch diameter faceplate, fixed steady with a 9-inch diameter capacity, No. 4 Morse centres, a drill holder with a No. 4 Morse socket, suds tray, shaft supports on the longer bed versions, rack feed to the tailstock sliding movement, a splashback and set of spanners. Optional equipment included a detachable-gap bed of any length (in 12-inch increments) up to 240 inches between centres, coolant, a larger 12-inch capacity fixed steady, a three-point travelling steady, larger faceplates of 36-inch diameter for the 22-inch swing lathe and 40-inch diameter for the 25-inch model, taper-turning attachment, six extra changewheels to generate inch and mm pitches, additional changewheels to produce metric, diametral, module, B.A. or other threads, an automatic trip mechanism for the longitudinal carriage feed, electric "quick power" traverse to the carriage with a three-speed feed box on the apron, special tailstock with a built-in revolving centre, single pulley (flat belt) drive from the motor, a micrometer carriage stop and the usual range of 3 and 4-jaw chucks and collets..
|
|
|
|
|
|
|
|
|
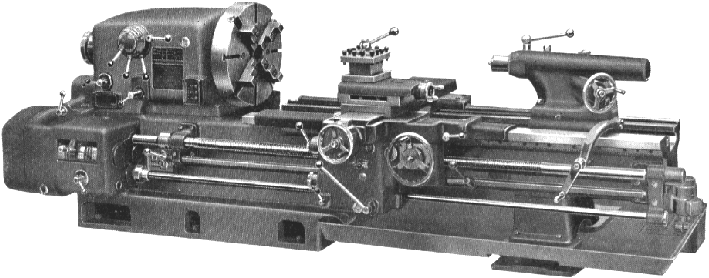 |
|
|
|
|
|
|
26 & 30-inch Dean Smith & Grace
Identical in general layout and specification to the 22 and 25-inch lathes the seven ton 26 and 30-inch DSG lathes offered greater capacity and a standard between centres length of 72 inches. Longer beds, with detachable gaps, admitting up to a maximum of 228 inches were available, in 12-inch increments. These were big machines (the 30-inch was dropped from the lists after a short production run) and their 20 hp motors could revolve massive 30-inch three-jaw chucks and 40 and 48-inch diameter faceplates. In view of the huge rotating masses involved the top speed was restricted to 420 rpm on the model with plain spindle bearings and 600 rpm on that equipped with the optional roller-bearing set up.
|
|
|
|
|
|
|
|
|
|
|
|
|
|
|
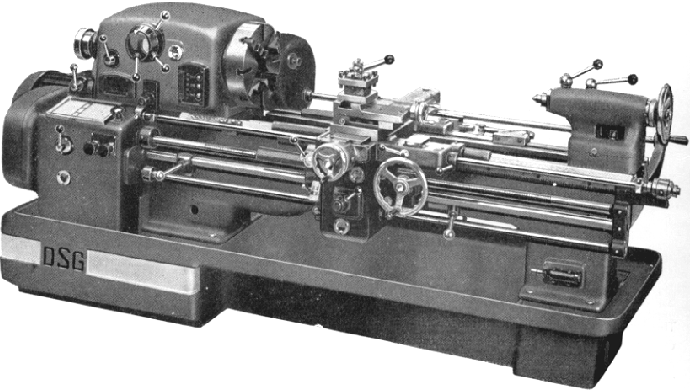 |
|
|
|
|
|
|
Dean, Smith & Grace 17T toolroom lathe
Weighing in at 2.5 tons the 17-inch (actual swing 18") DSG 17T Precision lathe was not a modified production lathe, but one specifically designed for toolroom use and built to tolerance and alignments of better than 0.0001". Even today a highly sought-after model, during the 1960s and 1970s they were assembled by a specialist fitter, Tommy Williams - who just loved the work and wanted no other. Fitted with a two-speed 7.5/3.75 hp motor, no fewer then thirty-six forward speeds and twelve reverse spindle speeds were available. Whilst early versions of the 17T had plain spindle bearing, later models were generally fitted with a set of the highest quality Timken taper roller bearings - though the option of a plain bearing headstock continued to be available. Some specials were also built, notably for Rolls Royce, where the headstock was a special, larger casting with a spindle that ran in taper-rollers but also a hand scraped, plain white-metal bearing in front of the front taper-roller bearings. The bearing could take the fitter Donald Booth several days to scrape in (using red lead not "blue" and maintenance engineers report that these lathes never require any headstock work. The bearing was to ensure that, when a test piece was put on a Taylor Hobson Talyrond (a machine to test surface finish and absolute roundness) no "bearing marks" were visible. The spindle and its three bearings (the front plain was 4.625 inches in diameter and five inches long) were of massive proportions - with the mandrel bored through to clear a 3.5-inch diameter bar. Two bed lengths were offered, the shorter admitting 36 inches between centres, the longer 48 inches. Supplied as standard with the lathe were: a coarse-pitch screwcutting arrangement (a handle on the right-hand side of the saddle allowed an instant reverse) coolant and piping, 4-way toolpost, catchplate, 16-inch diameter faceplate, fixed steady with a 5-inch diameter capacity, No. 4 Morse centres, a drill holder with a No. 4 Morse socket, suds tray, splash-back and a set of spanners. Optional equipment included a three-point travelling steady, a relieving and taper-turning attachment for the manufacture of cutters, a taper turning attachment (for tapering, not relieving), extra changewheels for inch, mm and other threads, an automatic trip mechanism for the longitudinal carriage feed, a micrometer carriage stop, single and quick-withdraw toolposts - and the usual range of 3 and 4-jaw chucks, collets and steadies..
|
|
|
|
|
|
|
|
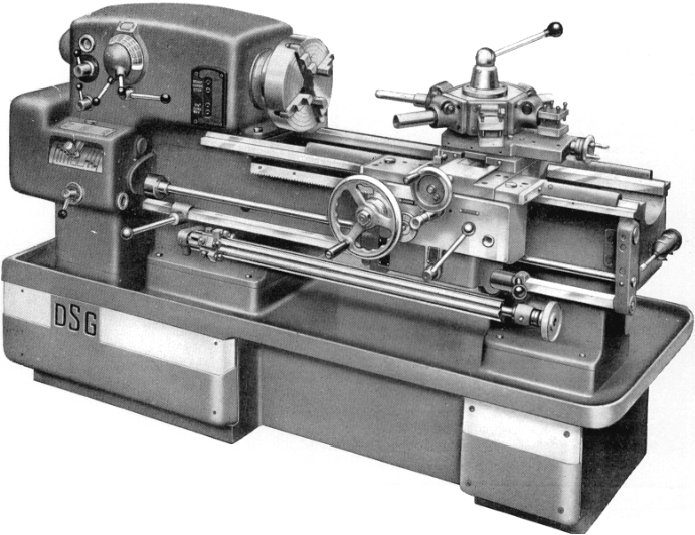 |
|
|
|
|
|
|
Type 13 SB 13-inch swing Surfacing and Boring Lathe with plain or roller bearing spindle.
|
|
|
|
|
|
|
|
|
|
|
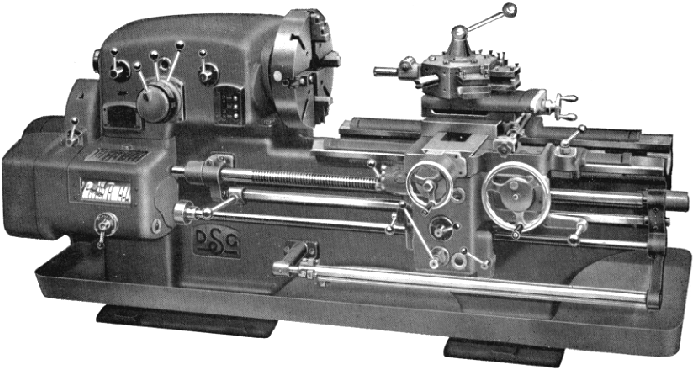 |
|
|
|
|
|
|
Type 20 & 24 SB 20 & 24-inch swing Surfacing and Boring Lathes with plain or roller bearing spindle.
|
|
|
|
|
|
|
|
|
|
|
|
|
|
|
|
|
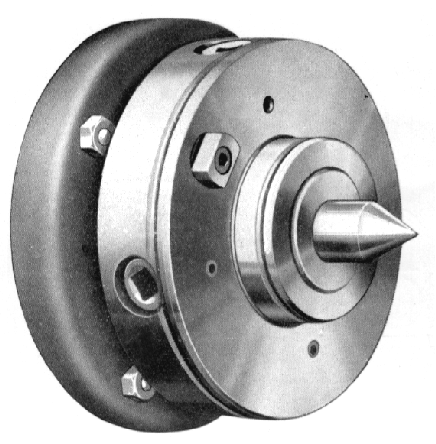 |
|
|
|
|
|
|
The Patent "Fastlock" spindle nose carried hardened cylindrical plungers which were controlled by cams and springs. The plungers projected into special backplates which could be fitted to chucks and backplates. A square key was used to rotate each plunger slightly - and so lock the chosen fitting securely in place. The system was fitted to the 13-inch, 15-inch, 17-inch and Type 20 SB lathes.
|
|
|
|
|
|
|
|
|
|
|
|
|
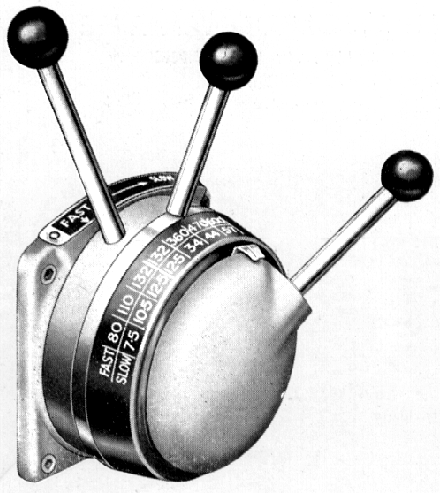 |
|
|
|
|
|
|
In a style later adopted by other makers, the DSG spindle-speed selector gathered all the controls onto one common shaft. The chosen speed was clearly indicated by a pointer against a Perspex-protected number - no colours to confuse the colour blind, and nothing to rub off.
|
|
|
|
|
|
|
|
|
|
|
|
|
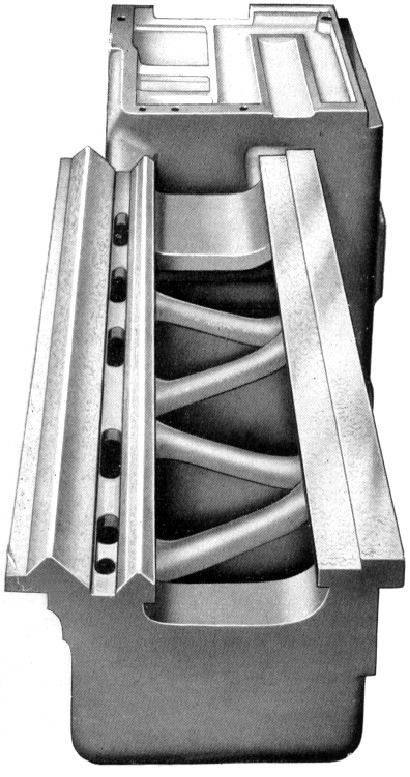 |
|
|
|
|
|
|
The bed was made from a semi-steel mixture with a Brinell hardness of approximately 200. Diagonal ribbing stiffened the ways, yet left plenty of clearance for the easy flow of chips through them. The front bed shear was formed into a lip which gave the leadscrew some protection form swarf.
|
|
|
|
|
|
|
|
|
|
|
|
|
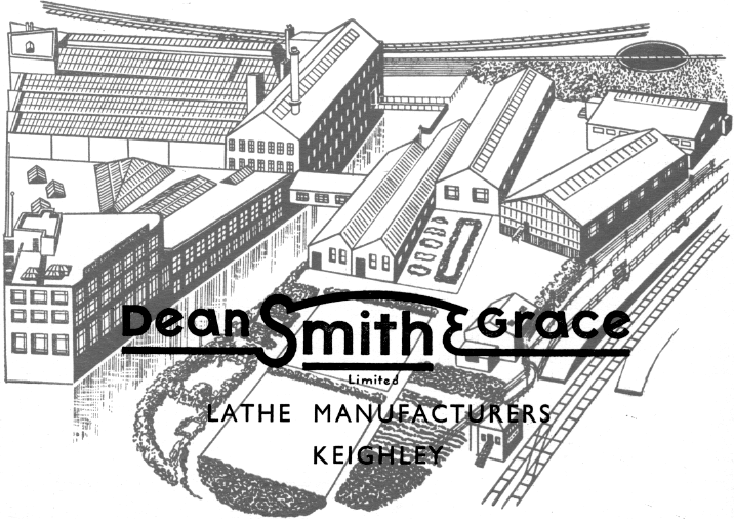 |
|
|
|
|
|
|
|
|
|
|
|
|
|
|
|
|
|
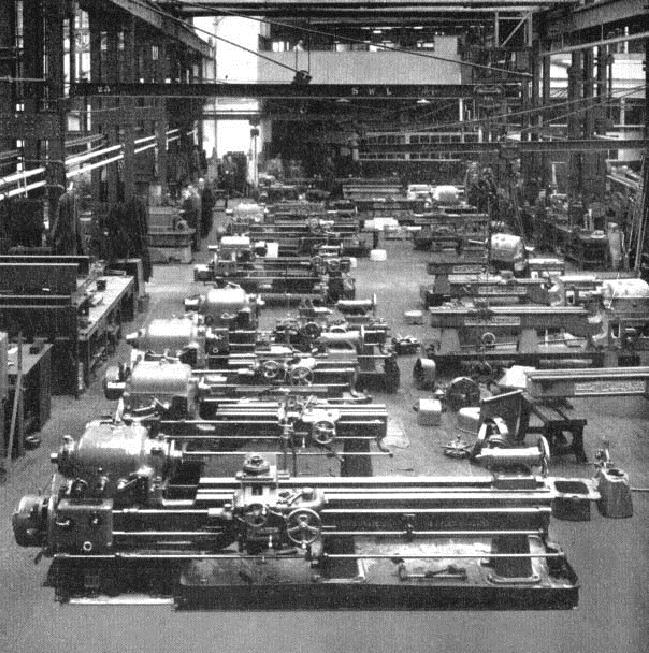 |
|
|
|
|
|
|
|
|
|
|
|
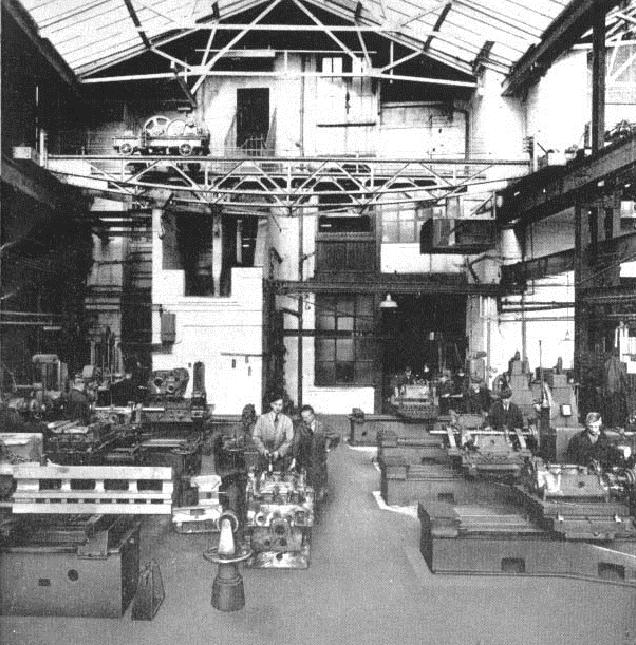 |
|
|
|
|
|
|
|
|
|
|
|
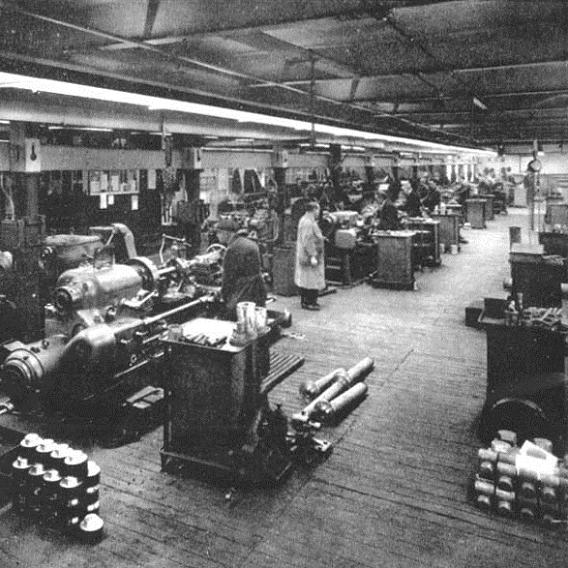 |
|
|
|
|
|
|
Medium Turning Department
|
|
|
|
|
|
|
|
|
|
|
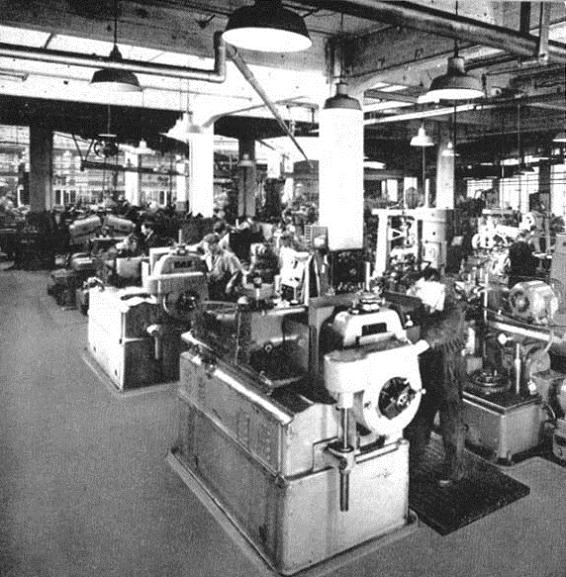 |
|
|
|
|
|
|
The gear-cutting Department
|
|
|
|
|
|
|
|
|
|
|
|
|
|
|
|
|
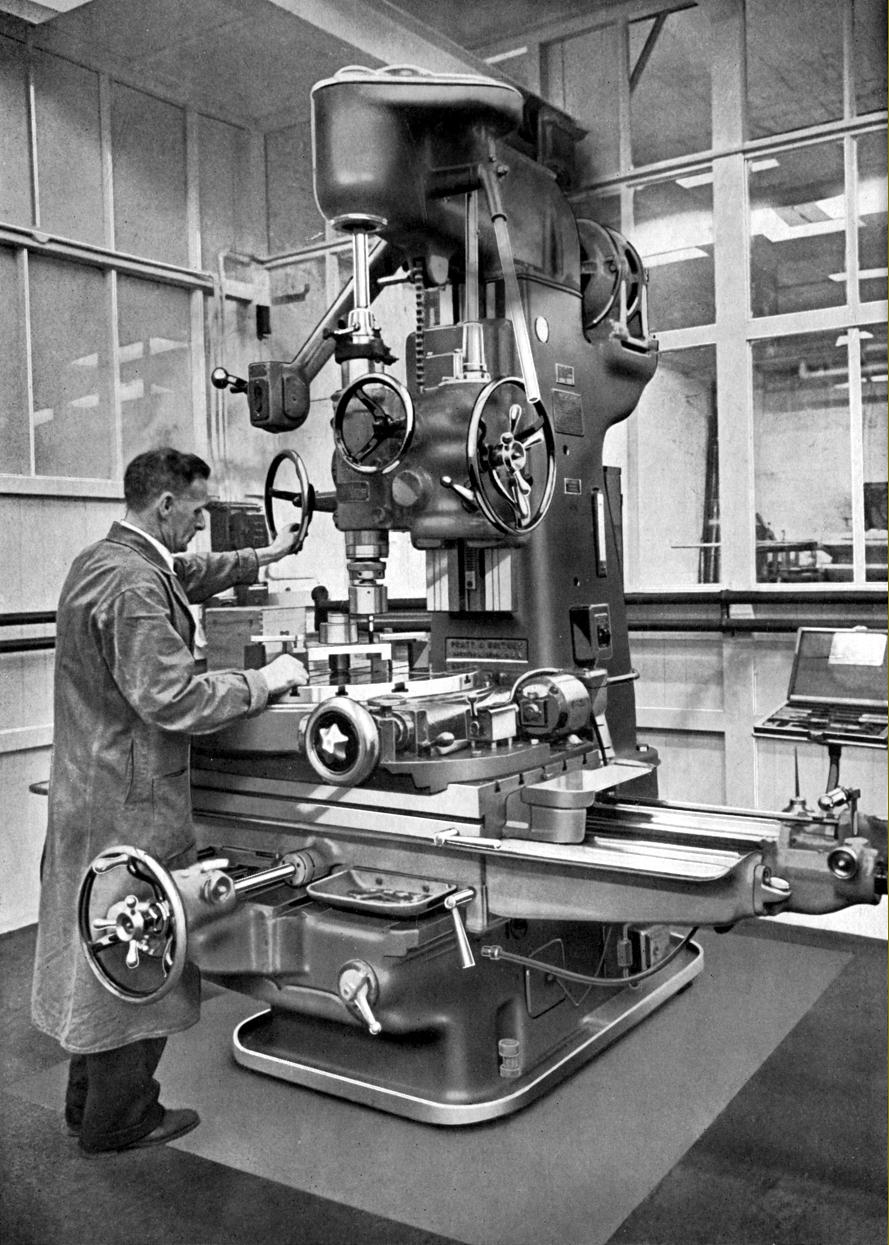 |
|
|
|
|
|
|
A special temperature-controlled section of the toolroom held a Pratt & Whitney jig borer
|
|
|
|
|
|
|
|
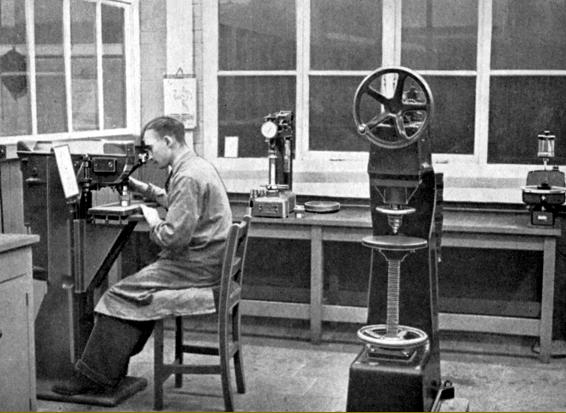 |
|
|
|
|
|
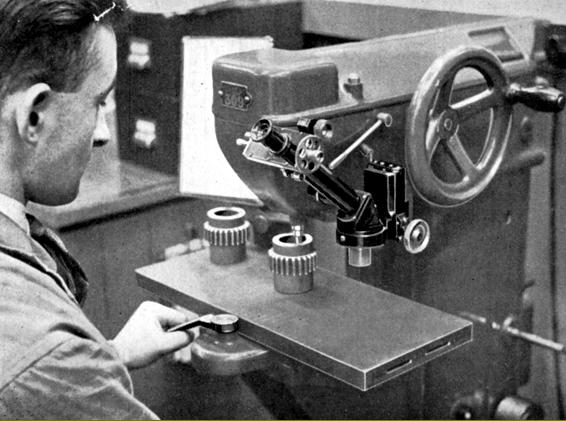 |
|
|
|
|
|
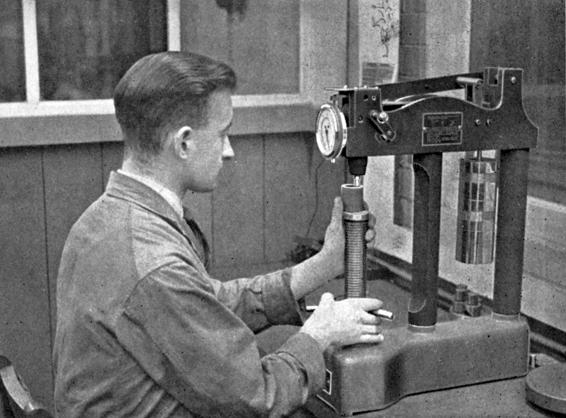 |
|
|
|
|
|
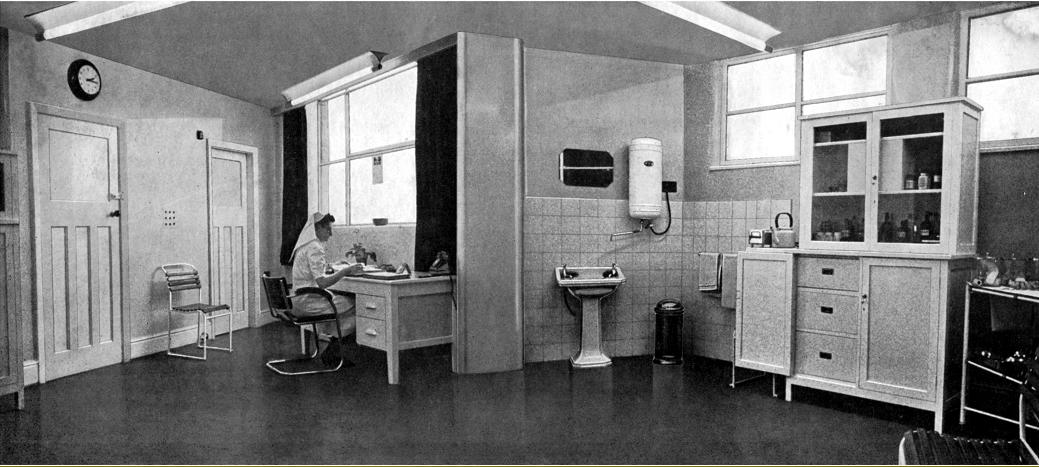 |
|
|
|
|
|
First Aid and nurse's station
|
|
|
|
|
|
|
|
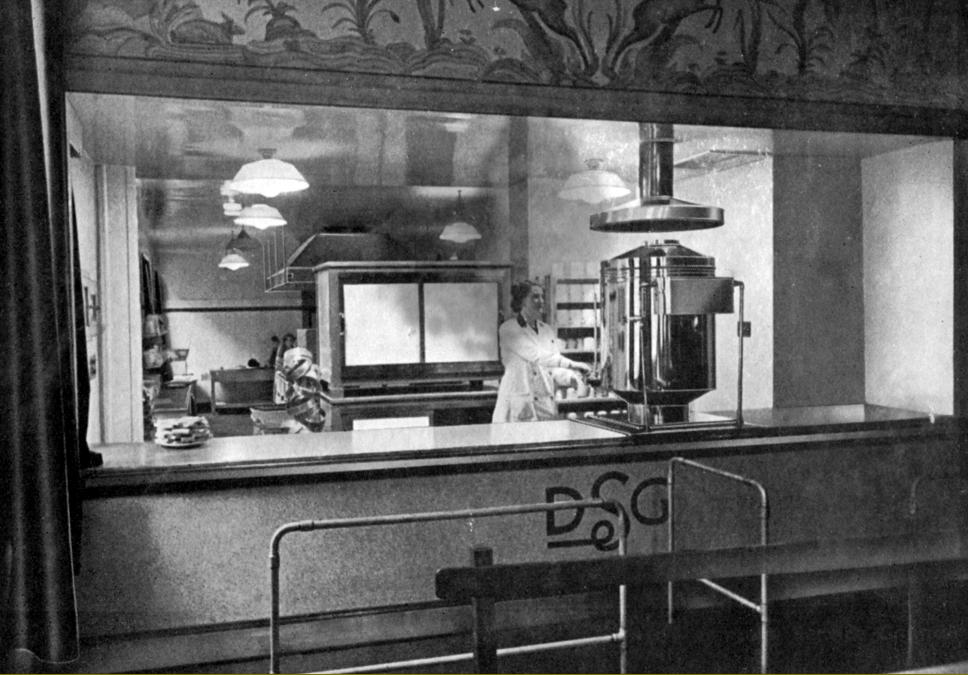 |
|
|
|
|
|
|
|
|
|
|
|
|
|
|
|
|
|
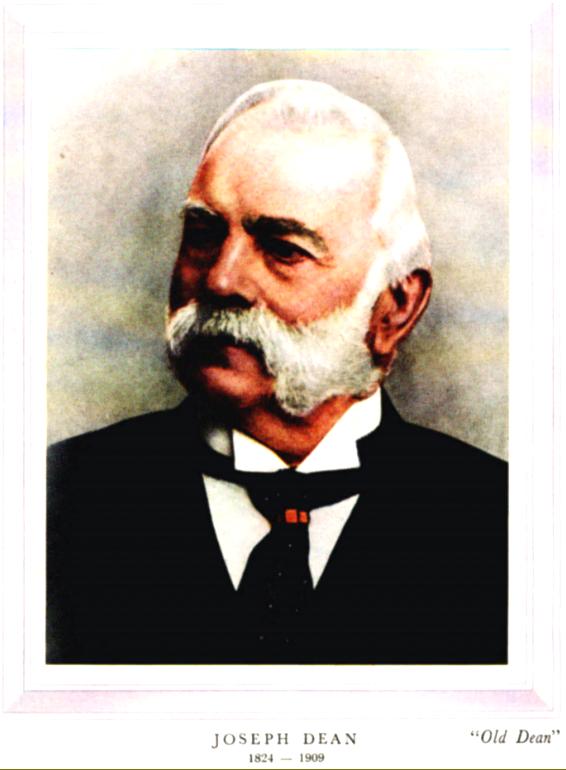 |
|
|
|
|
|
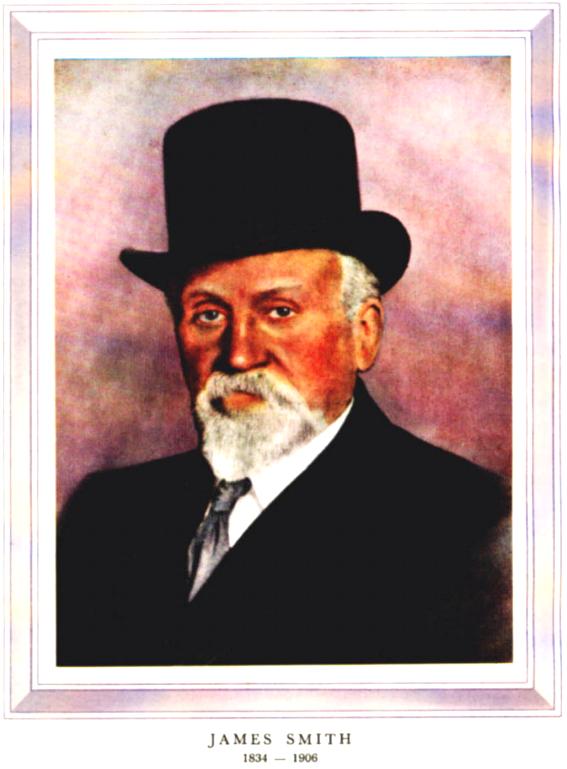 |
|
|
|
|
|
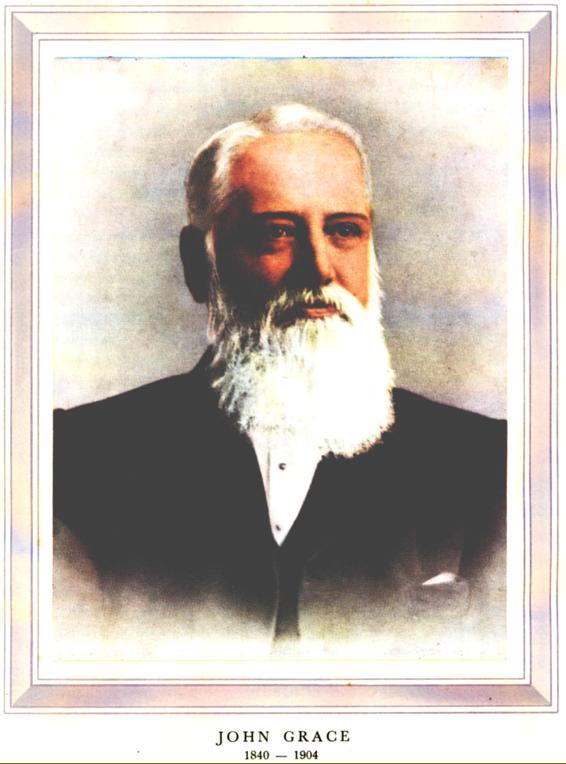 |
|
|
|
|
|
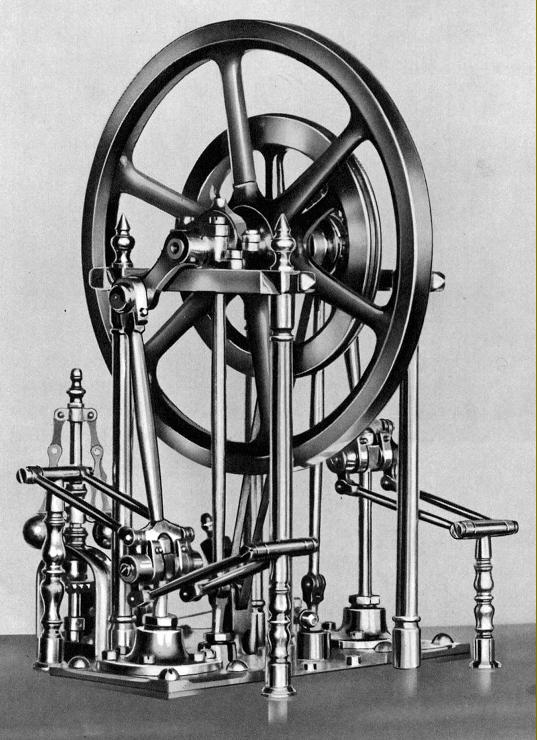 |
|
|
|
|
|
|
The first steam engine installed in the original Dean, Smith & Grace factory
|
|
|
|
|
|
|
|
|
|
|
|
|
|
|
|