 |
 |
 |
 |
 |
 |
 |
 |
 |
 |
 |
 |
 |
 |
 |
 |
 |
 |
 |
 |
 |
 |
 |
 |
 |
 |
 |
 |
|
|
|
|
|
|
|
|
|
|
|
|
|
|
|
|
|
|
|
|
|
|
|
|
|
|
|
|
|
|
|
|
|
|
|
|
|
|
|
|
|
|
|
|
|
|
The Beginnings Born in 1892 (d.1973) Charlie "CB" DeVlieg was the ninth child of parents who had emigrated from Groningen, Holland. Having abandoned school at the age of 14, DeVlieg began his engineering career with a short spell as an apprentice machinist before becoming, first, a tool designer at the Ford Motor Company and then an assistant master mechanic at Dodge Brothers. By 1917 he was employed as a works manager at the machine-tool builders Kearney & Trecker, his experience there leading him to design a novel bed-type milling machine. In the mid 1920's he left K&T and offered his design to the Sundstrand Machine Tool Co. who, liking the idea, gave him a job and put into production the Rigidmil - its very name, of course, indicating its particular appeal. Having worked for three years at Sundstrand he left to start his own company, designing milling machines and arranging with a Michigan manufacturer, the Walcott Machine Co. (presumably the same company as the renamed Walcott Lathe Co.?) to build them - this concern, unfortunately, going out of business. Faced with a new challenge, in 1929 DeVlieg purchased his own factory and began manufacture on his own behalf, the Great Depression causing the venture to fail. However, together with his son Bud, he started a small engineering shop and - obviously well able to control costs - ran it successfully through the depression. Finally, in 1939, at the age of 47, he founded the DeVlieg Machine Co., the first product being the Vanemil, a machine capable of making aircraft-engine supercharger blades that was more efficient - by a factor of 15 - than the types used before. Vanemill serial numbers run from 1940 (No. 123) to 1944 (No. 152) indicating a possible production run of some twenty-nine units. During WWII, and inundated with orders, DeVlieg faced an unacceptably long wait of 18 months for two new horizontal boring machines. As a consequence, he set to and designed and built his own, this being so successful that - so the story goes - three were sold before he was able to retain one for his own use. This very first model - of which (like the Vanemil) it appears that no pictures survive - was developed to become the famous Jigmil, a machine that was so well made, so accurate and helped by clever, precise automatic positioning of head and table, that jobs could be done without the need for expensive work-holding jigs and fittings. What Charles DeVlieg had invented and developed was, in effect, the world's first "jigless borer". Quality Founded on a reputation for high-class workmanship, the use of quality materials and close attention to detail, it is perhaps slightly strange that DeVlieg restricted themselves to making just this one type - not for them, it seems, was there ever a temptation to make, in volume, any other sort of machine tool. However, it is reported that they did manufacturer e some other items including pull-broaching machines, a full line of cartridge-style boring heads, tool pre-setters and their well-known line of "Microbore" single-point boring, facing and turning tools (patented in 1946). By concentrating their main resources on improving the Jigmil, they were to manufacture it - over several decades - in a number of different sizes, to suit a wide variety of work, combining this with increasing the refinement (and complexity) of its control systems. Although eventually outclassed by CNC machining centres, many of these now venerable precision horizontal boring and milling machine are still in profitable use. After DeVlieg became Devlieg-Bullard, a further change of ownership resulted in a new company, Bourn-Koch, who now offer a range of models with computer control and up-to-date specifications. Although a Series "3A" Jigmil is listed as having been manufactured from 1941 (Serial No. 130) until 1944 (Serial No. 143) these may well have never been publicised, but instead sold "into the trade" for munitions work. It is believed that the first commercially available Jigmil, the 3B was sold in either 1944 or 1945, both years having serial numbers beginning with, or prefixed by, "145" and the first advertisement (featuring a 3B) traced to the 1946/7 edition of "Hitchcock's Industrial Reference". The 3B was then joined by the 4B - first listed in 1947/8 with Serial numbers starting with "170" - and then, in 1955 by the smaller 2B, the first recorded Serial number of this type starting with "215". However, by 1955 five Jigmil models were available: the standard 2B, 3B and 4B types and two special long-bed versions intended for tackling large, flat workpieces, these being the 3C with 72 inches of longitudinal travel and 4C with a choice of either 96 or 120 inches - though serial numbers for this type are unknown. The digit in the machine type designation referred to the spindle diameter in inches (save the 2B, whose spindle actually measured 2.5 inches) and a second number e.g. 3B-48 where 48 was the table's horizontal travel. Weights varied considerably - though all were massive - with even the smallest ever offered, the 2B, weighing 13,000 lbs (5.8 tons) and the heaviest, probably the 4B-120, 45,000 lbs (20 tons). In subsequent decades the original Type B was to be followed by, successively, the Types C, H, J, JMC, K, R, 4W, a number of CNC types and the DeVlieg/Okuma. Alfred Herbert Jigmils DeVlieg also had the Jigmil built under licence by the Alfred Herbert Company at their Lutterworth factory, near Leicester, in England; initially, just the 2B and 3B models were offered (catalogued respectively as the Herbert 2B and the 3H) followed by the H and J types and, when production ceased in the United States, manufacture of all versions was continued exclusively by Herbert. During the 1980s a partnership was entered with the OKUMA Company of Japan with new models - all 3-axis CNC types - listed in the sales catalogues as being by DeVlieg/Okuma. Continued below:
|
|
|
|
|
|
|
|
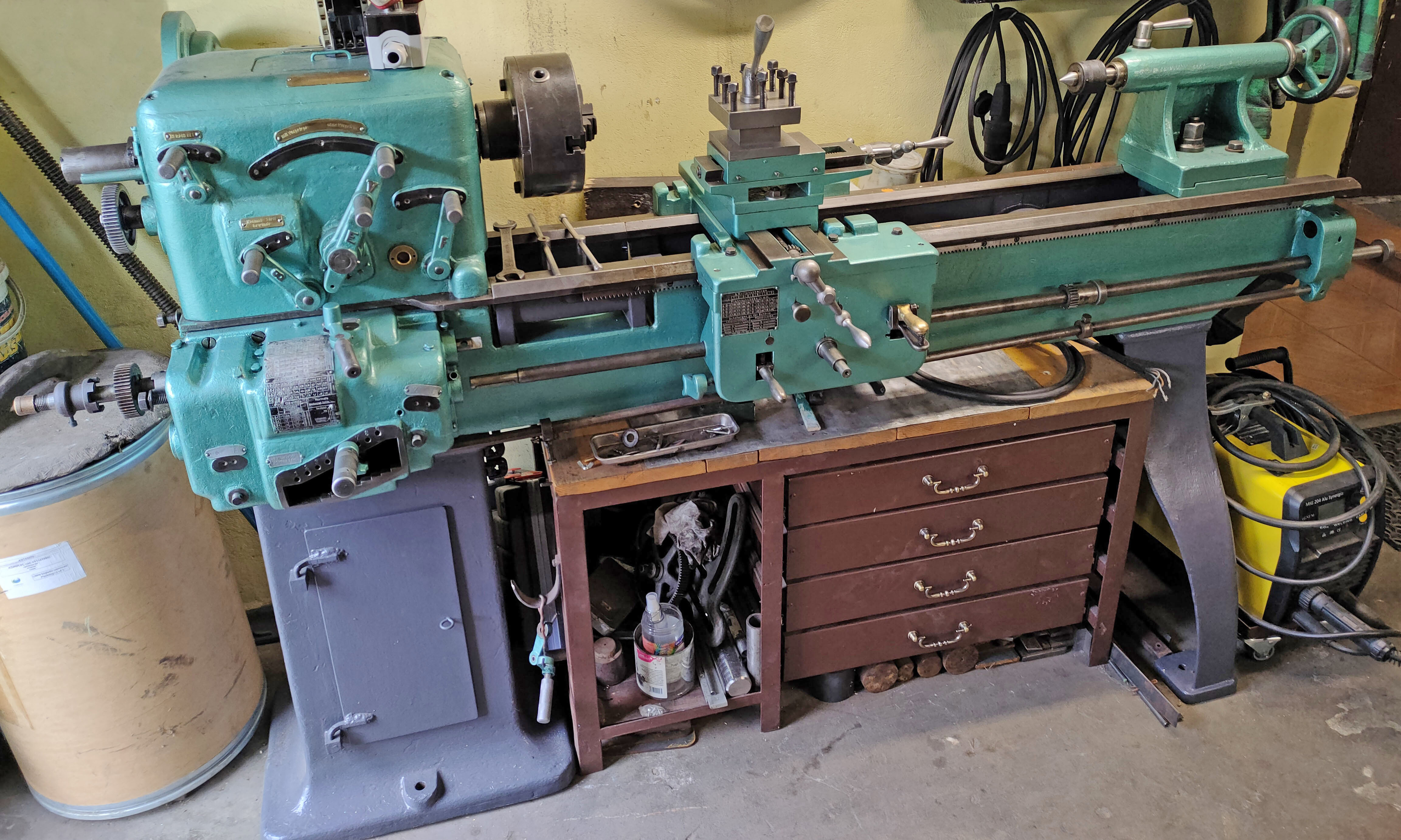 |
|
|
|
|
|
A typical DeVlieg Jihmil as sold during the mid 1950s - a Model 3B-48
|
|
|
|
|
|
|
|
|
Continued: Intended as a machine that could both bore holes with great precision and also function as a general-purpose milling machine, the makers claimed the accuracy of a Jigmil to be better than 0.0001" (one ten-thousandth of an inch). It was also stated that as, "automatic push-button operated hole spacing" in both horizontal and vertical planes was provided, no operator skill was required for "positioning and locking". However, the reality was more complicated, for the system had to be set up first, the exact method depending upon the year of production and the state of positioning technology (with DeVlieg offering training courses for operators, the publicity sheets had, perhaps, somewhat overstated the ease of use). Duplitrol Positioning System At first, DeVlieg supplied each new machine with their patented "Duplitrol" system - this involving the use of two "Duplitrol Bars", a set of "Duplitrol Blocks" being combined with the built-in automatic positioning of spindle head and table and a set of precision end-measuring rods and micrometer thimbles. Each Duplitrol Bar - one was mounted on the horizontal axis and the other on the vertical - consisted of a 3/4" square-section piece of mild steel into which it was necessary for the person setting the machine to drill a series of 1/4" diameter holes, each positioned so as to reflect the centre distance of the holes to be bored in the workpiece - though if this was beyond the capabilities of the factory, DeVlieg offered a bar layout and drilling service. The holes in the workpiece drawing were laid out using right-angle co-ordinates, those in the horizontal plane being labelled 1, 2, 3, 4, etc. and those in the vertical A, B, C, etc. - the Duplitrol bars being similarly marked. Once the initial settings had been made - and the machine started by using a button marked "Auto Position", the table or spindle head was moved using the rapid feed until a knurled-head stop pin, inserted in one of the holes, contacted the arm (or button) of the "positioning unit" (this having a built-in dial indicator that showed the operator (to a "tenth of a tho") how close to zero the final position was). The cycle was then completed by a "controlled oscillation" of the table or spindle head about the zero line - at successively slower rates of feed - until the final setting was nearly achieved, this being an automatic backward reverse of the feedscrew to release any end thrust, at which point the table - or head - could be clamped tight (with no upsetting of their final position) and the hole boring started. After this it was only necessary, after the first hole had been finished to shift one (or both) of the stop pins to the next position and the machine cycled automatically to bore the second hole - the process being repeated until the job was finished. Not only was this a great help when machining multiple holes in one component, but when smaller jobs could be mounted side by side on the table, the system functioned in exactly the same way machining one and then the next - a great time-saver and profit maker. When finished with, the two Duplitrol bars were stored so that the exact machining sequence could, if required, be repeated. If the job did not justify making special bars, or for a one-off production run, a set of hardened Duplitrol blocks could be used instead; the blocks - each drilled with a hole for the stop pin - were locked into the trough by a bolt and adjusted as necessary to set the hole spacing required. Once in place, the automatic system worked exactly as for the bars. A further alternative was also possible - usually employed for one-off jobs - the use of traditional, high-precision end-measuring rods, these being placed in the trough together with the necessary micrometer thimble and adjusted as required. Does the Duplitrol system work? A user reports buying a 3B-96 from Boeing Aircraft that had survived with all its Duplitrol systems intact - and obviously long unused. As the machine was also fitted with a modern DRO he was Curious to see how accurate the original system was and would it repeat-consistently (indeed, would it even still work?) he switched on the DRO and pressed the auto-positioning system button. Not only did the system function - despite relying upon common relays, microswitches and pneumatic timing relays - but repeated with dead accuracy to the zero digit. As heavy and as rigid as it was, the DeVlieg was not intended as a pure jig borer - nor was it priced as such - but as a machine for serious production work. For vertical jig-boring to the highest possible standards the Swiss Dixi and SIP models were long considered the finest available: the Dixi owner enjoying infinitely-variable spindle and table feeds - the latter hydraulically operated and absolutely smooth - while the SIP customer could choose from a wide range of models (many rugged enough for production use) built by a maker trusted to supply the International Bureau of Weights and Measures in Paris, the Bureau of Standards in Washington and the National Physical Laboratory in Teddington, England (and other important metrological institutions) with measuring equipment that replicated the "master metre" bar - and two witness bars - held in Paris. Continued below:
|
|
|
|
|
|
|
|
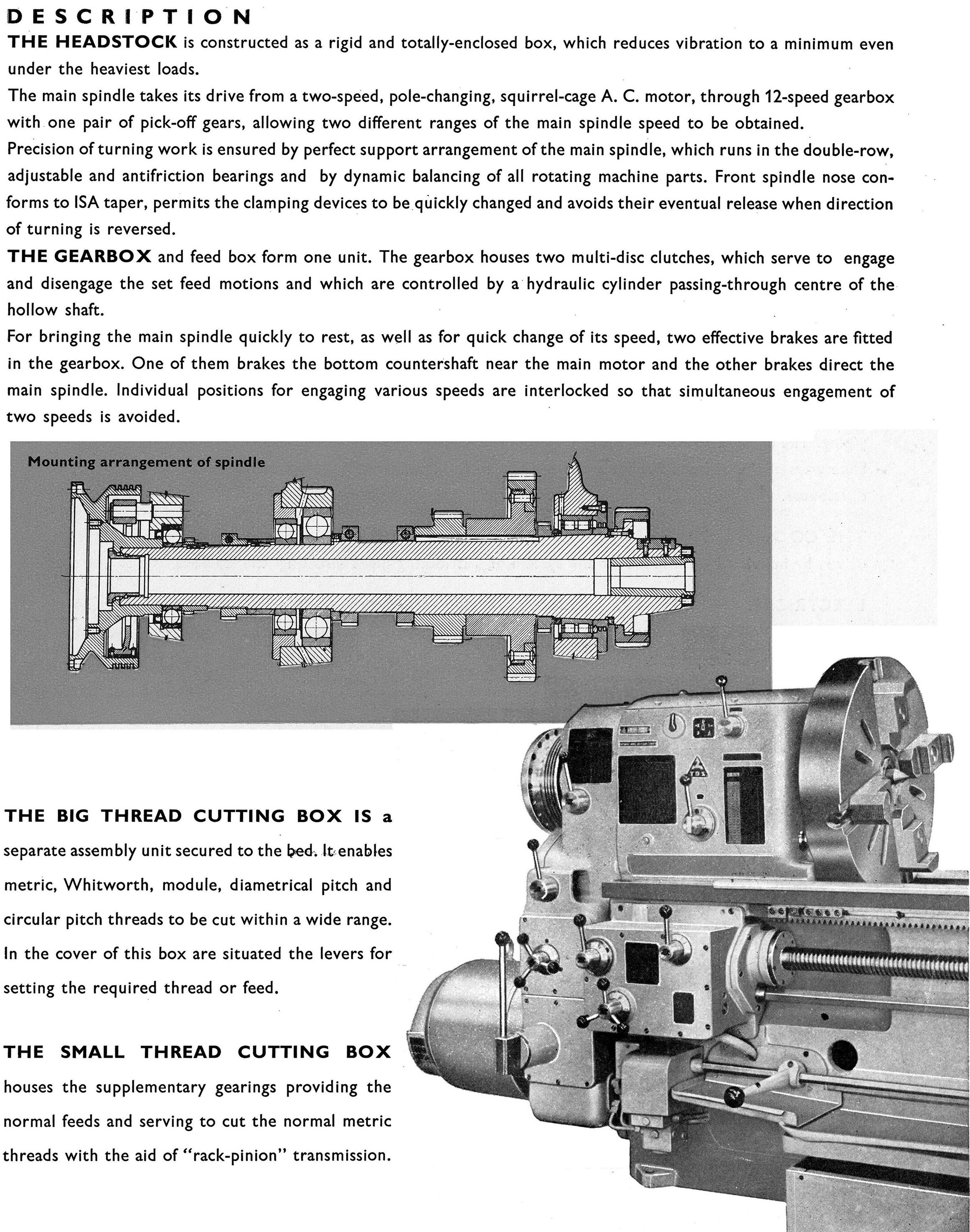 |
|
|
|
|
|
|
|
|
|
A read side view of the Mid-1950s 3B-48 Jigmil with control annotations. An experienced (and obviously satisfied) user comments: ...and running them, every control falls into your hand. Don't even have to think, just put your hand up and, oh yeah! There's the feed lever, under my thumb. Rapid retract for measuring, hit the button, part backs out, measure, hit the button, comes back within a tenth. Power drawbar. Power everything. Speeds and feeds up the wazoo.
|
|
|
|
|
|
|
|
|
|
|
|
|
|
Continued: Basic Construction and Function The Jigmil was constructed around two main castings: a massive base able to take heavy loads with, at the back, a column secured (on early 2B, 3B and 4B models) by nine heavy bolts and four large taper dowels. The design was such that, even at the extremes of its travel, the table - and consequently the workpiece - was always fully supported, there was no "sweet spot" in the centre as with many other ordinary milling machines. The top of the base was machined with narrow, V-shaped guides upon which slid, longitudinally on the X axis, a saddle - this in turn equipped with ways for the T-slotted worktable. The whole assembly was constructed to the highest possible standard of accuracy, an experience user commenting: "The foundation of the machine was a table with a finish that equalled any scraped AA-standard surface plate. The T-slots would have qualified for inspection work in location and were topped off with 90° cross slots that were not close to 90° - they were a dead 90. Hence, a Devlieg operator didn't need anything else but the table for the setting up jobs." The table had the facility of automatic retraction and exact repositioning by automatic, push-button control - the movement being for the purposes of tool changing and adjustment, checking dimensions and rotation of any indexing table in use. The setting of the retraction could be adjusted over a 12-inch range from the face of the spindle, a circular scale and micrometer dial being provided to make the required setting. The actual traverse cutting movement (Z axis) was provided by the long inward and outward movement, under power, of what would normally be called the "quill", but which DeVlieg termed the "spindle bar" - this emerging from a spindle assembly built into a head that was raised and lowered (Y axis) on ways machined into the right-hand face of the column. The end of the spindle bar did not have an outboard support, the rigidity of the Jigmil and relatively low the cutting forces in boring rendering one unnecessary. Did the arrangement work in practice? The comments of a user confirm that it did: "….if the job will fit on the table, you can get to it. Hang the spindle bar out to its maximum reach - into the bottom of a hole so deep you couldn't even see it. 5" cutter used: no chatter. Hold an accurate size ? - all day long. Jig boring? - all day long. Even the damn accessories are enjoyable to use." Slideways carrying the table and head were finished by hand scraping, the accuracy being to "within 0.0001" per foot on all alignments and paths of travel" - though the table edge and T slots were to within 0.00015" per foot. Longitudinal and vertical feeds were of the push-button controlled, power-operated kind only - no handwheel being fitted to either - and with the selection of feed direction by a single, interlocked lever that prevented both from being engaged at the same time. All power feeds incorporated rapids, these too being push-button controlled rather than "spring-lever" operated as on most other machines. To give an idea of the complexity involved in running a Jigmil, on the B Series models of the mid 1950s (excepting the 2B), up to nine 3-phase motors were fitted, these operating the spindle drive, table feed, table rapid traverse, retraction of saddle (platen), automatic tool locking and release, feed unit hydraulic pump, table stop adjustment, power saddle lock and the power lubrication system. From the Type J Jigmils onwards the main drive 3-phase AC motors were replaced by variable-speed DC types. Continued below:
|
|
|
|
|
|
|
|
|
|
|
|
|
|
|
 |
|
|
|
|
|
Mid-1950s 3B spindle-head controls
|
|
|
|
|
|
|
|
|
|
|
|
Continued: The Spindle Head A work of engineering art - and driven by smooth-running, constant-mesh helical gears - the spindle assembly had, from the start of production, always been of the very highest quality. Ground and hand-lapped to tolerances of 0.00005" or less, the "spindle bar" was forged from a very special, high-alloy steel and slid back and forth inside its containing sleeve on Nitralloy liners, the whole assembly turning in high-precision Timken taper-roller bearings. By the 1970s the liners had been replaced by ones in a diamond ground and honed ceramic, with a maximum clearance of just five microns, the bar moving on an oil film under compression. This development was, claimed the makers, virtually wear-free and able to maintain precise alignment of the bar even when at full extension. In addition, the spindle bearings had been changed to a self-compensating, Timken Hydra-rib taper-roller type whose floating outer races were held in position by hydraulic pressure - the design giving stiffness to the assembly while also allowing for expansion of the bar as it warmed in use. A form of thermal control was also fitted to remove heat generated when running at high speeds, this being in the form of a free-standing, pumped refrigeration unit that circulated cooled water around the bearing housings. The cooler was first offered as an option on the introduction of the H range in the USA and on Herbert-built 3H and 43H types, but eventually became part of the standard specification. When listed as an optional extra, the cooler was especially recommended for machines equipped with Datatrol NC controls - where spindle speeds could be as much as 50% faster. By the early 1950s changes of spindle speed had been much easier by the incorporation of a pre-selector system - though the original lever-change design appears to have been used for a little longer on the 2B. With the machine running, the operator could pre-select the next speed required on a dial and bring it into use by pressing a button - there being no need to stop the motor when running in forward or reverse direction. In addition, for setting and other purposes, a lever was provided to disengage the drive and allow the spindle to be turned by hand. All but the early models of the Jigmil had, as part of their regular equipment, a push-button-operated power-draw bar to retain and release tooling - a special fractional h.p. "torque" motor working through a gearbox and clutch being employed to ensure the uniform application of pressure. The mechanism worked at any position of the spindle bar and helped to ensure accurate duplication of boring depths and diameters to an accuracy of 0.0001". As with all power-equipped drawbar systems, the arrangement also removed the chances of damage to the spindle and its bearings by the heavy-handed and impatient use of hammers on drifting-out slots and tool-retaining wedges. Early models of the 3B had a No. 5 Morse taper in the end of their spindle bar, later ones switched to a the same N.M.T.M. fitting employed on all versions of the 4B - sizes being a No. 40 in the case of the 3B and a No. 50 for the 4B Continued below:
|
|
|
|
|
|
|
|
|
|
 |
|
|
|
|
|
|
|
|
|
|
|
|
|
|
|
Continued: Provided with a range of feed rates, by the early 1950s the spindle bar feed was now fitted, as standard, with an automatic trip by means of a vernier-equipped, depth-control dial that worked for just a single stroke - a handwheel and micrometer dial also being provided for the purposes of hand feed and manual setting (depth control on all early B Series machines had been by length rods and a dial indicator). For production work the bar feed could be fitted with an Automatic Depth Control Attachment mounted on the side of the head; the unit consisted of a rotating, turret-like assembly - the same length as the bar-feed travel - and equipped with 12 bars, each carrying a pair of adjustable stops blocks to set the start and finish of a cut, the blocks engaging with an arm - or button - protruding from a trip unit. Once in operation the attachment made a rapid advance of the tool to its pre-set position, rotated the tool, applied the cutting feed and stopped at the preset depth; there followed a short dwell period followed by a rapid return to the start position. To provide all the automatic positioning features of a Jigmil meant that, from the start of production, the fitting of a complex electro-mechanical control system. As the machine was developed , even more sophisticated, electrical-activated hydraulic gear-shifting mechanisms were incorporated and so, as troubles inevitably arose with the passing of years, endless fun was provided for electrical engineers charged with fault finding. It is also worth mentioning that DeVlieg are known to have incorporated, during production runs, many small changes to the control systems - so having the correct wiring diagram is essential. Interestingly, while the larger models were continuously developed, improved and made more complex, the basic 2B continued as the sole survivor of the original range being manufactured, unchanged, into the 1970s - the publicity material for October 1973 reporting that: "...the 2B-36 is designed for boring and milling small workpieces such as instrument cases, gear cases, jigs, fixtures and experimental parts…". In the same catalogue the H, J and newly-introduced K Series models were listed side by side, the latter pair with more powerful motors of the DC type, higher spindle speeds and the ability to be run under NC control - the K also having a greater width across the column. Continued below:
|
|
|
|
|
|
|
|
|
|
 |
|
 |
|
|
|
|
|
|
|
|
At first, DeVlieg supplied each new machine with their patented "Duplitrol" system - this involving the use of either "Duplitrol Blocks",(left picture) or a pair of "Duplitrol Blocks" (right picture) combined with the built-in automatic positioning of spindle head and table and a set of precision end-measuring rods and micrometer thimbles.
|
|
|
|
|
|
|
|
|
|
|
|
|
|
Continued: Accessories In addition to the expected milling-cutter holders, holder adapters, reducing sleeves, flood and air-mist coolant equipment, Tee-nuts and studs, work-holding and clamping sets and boring and facing heads, a variety of other accessories was available to extend the machine's capabilities and ease of use. Items listed over the decades included a range of the important super-precision, single-point carbide-tipped and micrometer-adjustable Microbore boring bars. Microbore cutters were originally intended by DeVlieg to improve and maintain the accuracy of a Jigmil while also speeding up final tool setting - the operator being able to "dial-in", using a vernier-equipped micrometer dial, any small adjustment required. One division on the main scale indicated a change of 0.001" on diameter, the vernier scale improving this to an accuracy of 0.0001". However, so useful were the Microbore cutters - they were available singly or in boxed sets - that their use quickly spread to other machine tools. As demand for them increased, and new more complex control systems were introduced throughout the machine-tool industry, the range of Microbore tooling was extended to include boring heads, a milling system, indexible carbide inserts and holders, tips made from high-speed steel, titanium carbide, ceramic and "Kendex throw-away" types, auto-retractable and dual-head versions and collets and collet chucks. DeVlieg even offered a service to manufacture Microbore cutters to a customer's particular specification, some of these including production types fitted with complex, multi-head cutters, each individually adjustable. To keep the Microbar tools in perfect order, DeVlieg offered two high-precision tool and cutter grinders, one manual, the other automatic: intended for use on Microbar units, they could maintain - to precise gage accuracy - the correct geometrical profiles of single-point tools with either conical or cylindrical relief at the radius of the nose. Also available was a set of four matched, hand-scraped, T-slotted angle plates - in various sizes to suit the different machines - and a number of very accurate, T-slotted, rectangular-form, rotating indexing tables, their intended use being to save time by allowing holes to be bored, milled, drilled, tapped, faced, backbored and countersunk into two, three or four sides of a job in precise alignment after just one initial setting - there being no need to employ special long boring bars or outer supports. At first just two indexing table were offered, both of the hand-turned type but fitted with quick-action, "easy-lift" mechanisms: the larger and very rigid Model E was sold in five sizes and bolted directly to the machine table, it was equipped with a floating ball-bearing assembly and could be ordered with indexing positions at either 90° or 180° intervals. The other table was the smaller Model M - made in three sizes - with its top rotating on a fixed base, four-position 90° indexing only and available, in later years, with the option of an air-lift mechanism (this lighter model was really intended for use on the small 2B Jigmil but was joined later by a larger version, the AM). These first tables were then joined by two power-operated versions, with settings at 90° and 360°, and then, with the development of NC and CNC controls, tables that could be indexed (under power of course) through 360,000 positions. Other useful items were also listed including: a matched set of hardened and ground locating and nesting blocks to locate workpieces on the machine and indexing tables, a high-speed boring attachment that provided a range of extra-fast spindle speeds - at a step-up ratio of 3.8 : 1 - for use on small diameters; accompanying the high-speed head was a special set of boring bars with taper shanks that allowed a boring range on diameter from 0.5" to 1.75". Held in a fitted hardwood case, the set included the necessary tools, two drill-chuck adapters, grinding blocks and wrenches. Tapping equipment was also listed - again held in fitted hardwood boxes - one consisting of five sizes of tapping head with spindles that allowed the tap to "float" freely and follow its own lead. An accurate and adjustable torque-limiting control was provided that prevented tap breakage if taps became dull, overloaded or bottomed out when working into blind holes. Is there room in your garage for a Jigmil 2B? In America, probably; in the UK, almost certainly not. If there was, could you operate it? Would you have fun trying? Would your neighbours complain? One can dream… Quotations from happy Jigmil users: - "I had the honor of working in the Devlieg department of a tool shop ….. our oldest machine was a 4B-60 with the Duplitrol positioning system. It was used daily without a digital readout for precision die work. We also had a 4K96, 4K60, and a 5K120. The 96 and 120 were eventually upgraded to AB controls. Of all the machines I have ever run in the shop, and that's a lot of different machines, the DeVliegs were the most fun and close in precision to our SIP boring mill, and holding .0005" over 6' was not a problem. "
- "If you like machining, you owe it to yourself to drive a Devlieg some day. If I were starting a job shop again, this would be one of the first machines I would look for. They make turret mills look like toys.."
- "For job-shop work, the damn things are just a joy. For production, compared to doing things with readouts, also a joy. You can set them up to auto-locate (sort of - they have highly accurate bars that go into v-grooves, like some other jig borers. You just hit the button, the machine rapid advances to the bar's location, backs up, re-advances slowly, unclamps the drive to eliminate pressure on the measuring device, clamps the table. Automatically. Built-in indicators to show you where it is. All it doesn't do is give you a little jolt in the ass to tell you it's ready."..
|
|
|
|
|
|
|
|
|
|
|
|
|
|
|
|
|
|
|