 |
 |
 |
 |
 |
 |
 |
 |
 |
 |
 |
 |
 |
 |
 |
 |
 |
 |
 |
 |
 |
 |
 |
 |
 |
 |
 |
 |
 |
 |
 |
 |
 |
 |
 |
 |
 |
 |
 |
 |
 |
 |
 |
 |
 |
 |
 |
 |
 |
 |
 |
 |
 |
 |
 |
 |
 |
 |
 |
 |
 |
 |
 |
 |
 |
 |
|
|
|
|
|
|
|
|
|
|
|
|
|
|
|
|
|
|
|
|
|
|
|
|
|
|
|
|
|
|
|
|
|
|
|
|
|
|
|
|
|
|
|
|
|
|
|
|
|
|
|
|
|
|
|
|
|
|
|
|
|
|
|
|
|
|
|
|
|
|
|
|
|
|
|
|
|
|
|
Established in 1872, MDF (Maschinenfabrik Deutschland Aktiengesellschaft Dortmund) were famous for their very large machine tools including a wide range of centre (engine), facing, roll-turning, wheel type and burnishing lathes - all machines that were most impressive to watch in action. The large lathes were, while listed in general categories with recommended specifications, always custom-built to a buyer's exact requirements with bed types, lengths, saddle designs, spindle speeds and feed ranges specially arranged. Upon request the beds could be machined with the end (tailstock) section able to take either a retrofit bed extension (a plate covering the machined face being detachable for use as a planning guide for the new bed unit) or a later change to a "twin" lathe with left and right-hand facing headstocks. For turning large but slim workpieces, gaps were also available, these normally being closed up by bridging sections. By the late 1940s lathes were available with two, three or four bed ways as the Types: D-11, D-111 and D-1V all with a choice of centre heights: 20, 25, 32, 40, 50 and 63 inches and able to carry jobs weighing, respectively, 7, 12, 20, 30, 45 and 70 tons. From the model name it was possible to deduce the basic specification: e.g. the D-1V-100S was a Type D lathe with a 4-way bed (1V being, of course, Roman numerals) and a 100 mm centre height. Beds, cast from a close-grain iron, were of massive proportions with both longitudinal and traverse stiffening webs and usually mounted directly on the floor without supporting feet. Slideways were flat and very wide with narrow vertical edges used to guide the carriage. Continued below:
|
|
|
|
|
|
|
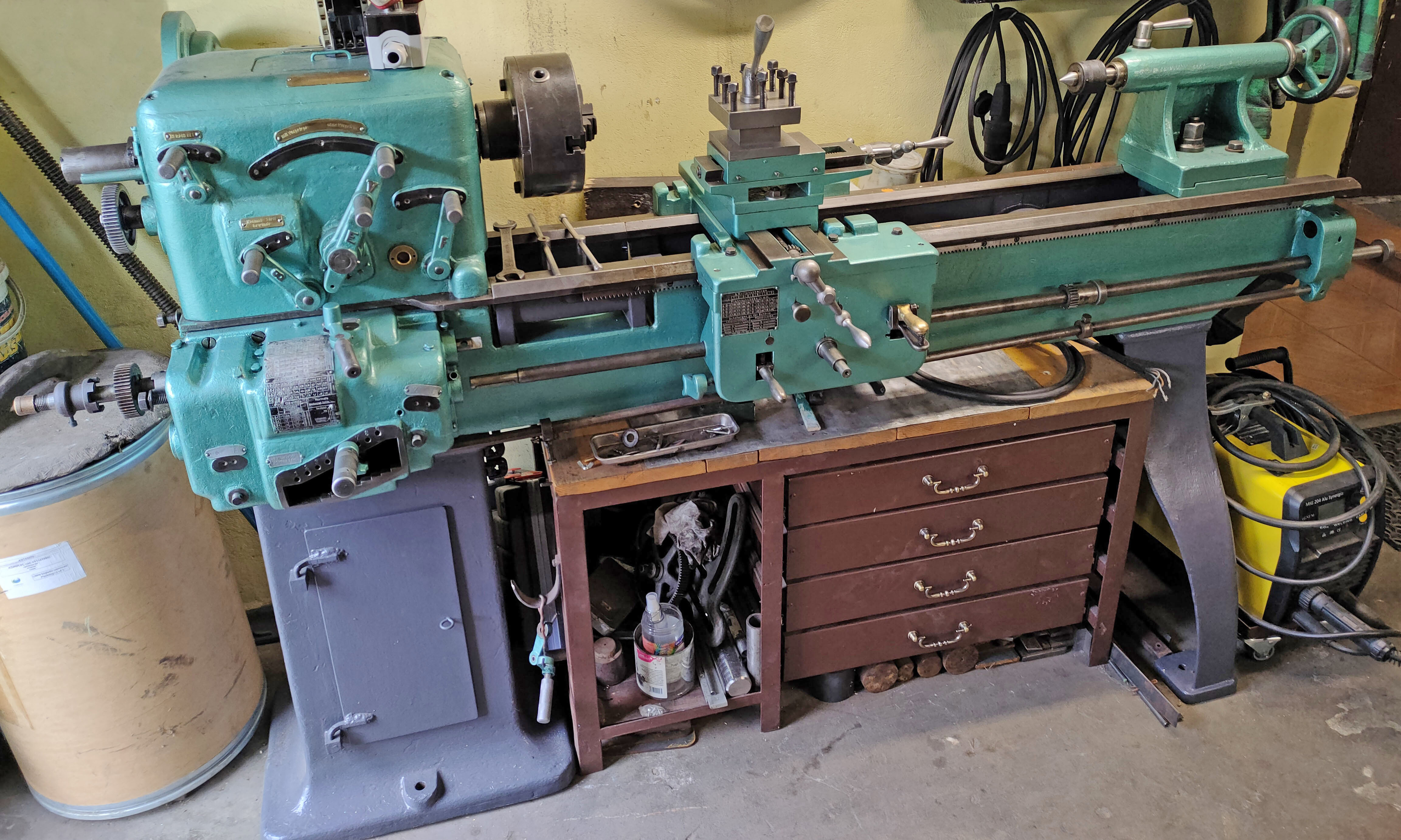 |
|
|
|
|
|
|
A smaller Deutschland Dortmund heavy lathe with a "2-way" bed: the Type D-11-40S with a 400 mm (16") centre height and fitted with screwcutting
Continued: Depending upon the bed length any reasonable number of independently driven carriages could be fitted with, on the Types D111 and D1V, the possibility of arranging facing both to front and rear and so able to slide past each other. On the D-11 bed the single carriage could carry an extended saddle with a second compound slide rest at the rear. However, if a customer's work involved unusual or awkwardly shaped jobs, the makers would design and manufacture special saddles, slides and tool holders to suit. As the mass of the carriages and their fittings was considerable, the amount of power required to get them moving (to overcome the static friction) was considerable; to reduce this, the sliding surfaces of the saddles were lined with a special very low-friction hard plastic, hand scraped to a perfect fit. The lubricant used was a mixture of graphite and oil and, after a time, this built up to reduce friction even further. Each carriage was a self-contained unit with the apron holding all the gears necessary for producing not only different rates of feed but also their direction. Power sliding and surfacing drive came from both by a headstock-driven splined power-shaft and also a flange-mounted motor inside the apron, the latter used to provide a rapid power traverse. Normally (and cleverly), the two feed mechanisms were connected by differential gearing to allow the quick feed to over-run the normal feed without having to disconnect or stop it so allowing the operator to speed up jobs where machined sections were some distance apart - the mechanism working either towards or away from the headstock. To allow control of both rapid and main motors from any position, each carriage was fitted with a set of push button. As an option, a screwcutting leadscrew could also be fitted, with both it and the power-shaft located below the outer edge of the bed's front way where they were protected from swarf. On long-bed models intermediate supports were required on both leadscrew and power shaft - these being in the form of either travelling or suspended bearings. The suspended type were moved by the saddle and, being fitted with latches and carried on dedicated ways, were automatically left behind at fixed points. The suspended bearings were clipped in place over the bed and installed by the operator where he thought fit - if he could be trusted…. Continued below:
|
|
|
|
|
|
|
|
|
|
|
|
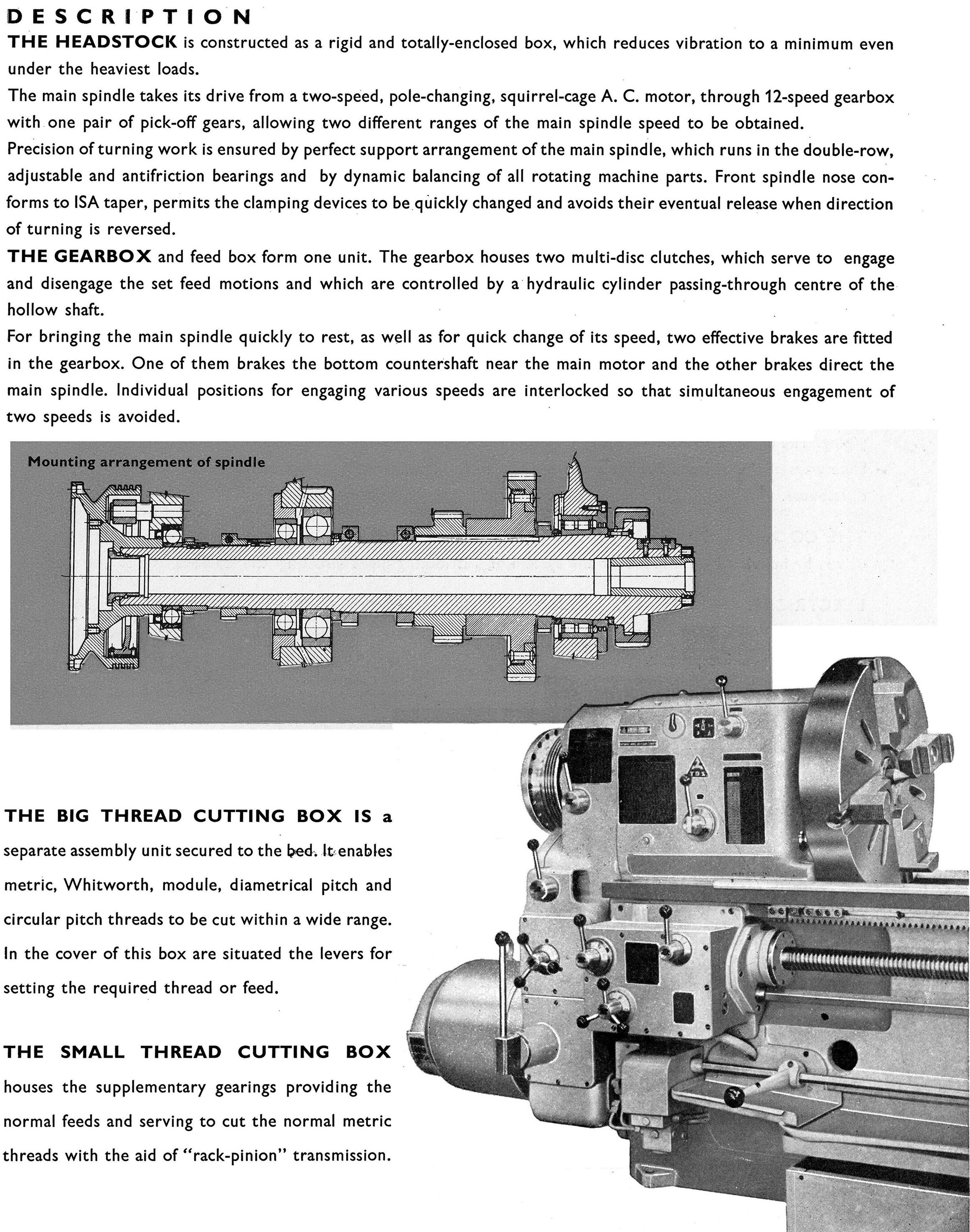 |
|
|
|
 |
|
|
|
|
Heavier: Type D-111 with a "3-way" bed
|
|
|
|
|
|
|
|
|
Heavy: Type D-11 with a "2-way" bed
|
|
|
|
|
|
|
 |
|
|
|
|
|
Heaviest: Type D-111V with a "4-way" bed Continued: Driven by conventional changewheels carried on a headstock-mounted quadrant, the leadscrew was grasped by massive split nuts with, to reverse it, a gear mechanism built into the headstock. Changewheels (screwcutting gearboxes were not offered) were available to generate inch, metric and module pitches in the usual way. Of massive proportions, the headstocks contained gears and shafts of forged steel with very the large gears (including that fastened to the rim of the larger faceplates) made from steel castings and with all but the largest hardened and ground. Speed selection was by hand-operated levers or wheels, the makers offering only a minority of models fitted with a complicated and hence potentially unreliable hydraulically-operated pre-selector system of the LeBlond "Servo-shift" type. The main spindle, made from a steel forging, ran in just two adjustable plain bearings - the makers deliberately rejecting the expected three-bearing design as they claimed this was a "mechanically undecided" system. All sliding gears within the headstock were on splined shafts (there were no keys to work loose) running in anti-friction bearings - though slow-speed shafts were run in plain. Lubrication was, naturally, well though out and of the recirculation type with an electrically-driven pump lifting lubricant from tank, through a filter to flood all bearings and gears. On most models the pump started before the main motor, thus allowing the operator to check, through multiple glass-covered inspection windows, that oil was flowing before the machine started. A long oil-distribution tube lay along the length of the headstock with a maze of pipes leading from it to direct oil to specific locations. Motors were mounted separately, either on a bracket bolted to the headstock end face of the lathe or floor mounted and connected to the headstock by a flexible coupling. As an option, where space was limited, the motor could be mounted on top of the headstock - but as this interfered with removing the top it was not recommended, unless unavoidable. The makers strongly encouraged the use of a variable-speed motor as this not only provided much finer and easier control of speeds (by push-buttons that could be located in almost any position and also easily duplicated) but reduced the number of times the operator would have to walk back to the headstock - a considerable stroll in the case of long-bed models - to change the gear settings. Fitted with an ordinary constant-speed motor all speed changes had to be made at the headstock (with selection of very low speeds required some juggling of the controls to get the gears to mesh) though push-button control of start, stop and reverse was also supplied for this type of installation and could be duplicated as necessary. To ensure that the selected speed was correct a rev counter was usually installed on the forward-face of the headstock together with an ammeter - the latter essential with the considerable power available - although an automatic cut-out did prevent inadvertent overloading. Tailstocks were made in upper and lower sections allowing them to be set over for the turning of slight tapers, were secured to the bed by heavy clamp plates and held against thrust forces by a pawl that engaged with a bed-mounted rack. Spindles were moved by hand, usually with a single handwheel that had two functions: the first shifted the spindle into position while the second, engaged by a lever, allowed the operator to apply sufficient force to hold the job in place. When employed for very heavy-duty work tailstocks could be equipped with a replacement spindle fitted with a permanently-mounted, T-slotted faceplate equipped with four adjustable clamping jaws. Although the normal tailstock spindle could be fitted with an ordinary rotating centre, the makers recommended instead the use of a spindle with the centre built in and turning on roller and thrust bearings, the latter being held against powerful springs to allow for workpiece expansion. On smaller lathes the tailstock were driven along the bed by hand-turned gearing while on larger the drive was electric, by a separate motor working through gearing and controlled by conveniently positioned push buttons..
|
|
|
|
|
|
|
 |
|
|
|
|
|
|
Deutschland Dortmund Type D-1V-100S with a "4-way" bed, a centre height of 1000 mm (40") equipped with two saddles on the front and one at the rear
|
|
|
|
|
|
|
|
|
|
|
|
 |
|
|
|
|
|
|
Deutschland Dortmund Type D-111-50L with a "3-way" bed, a centre h eight of 500 mm (20") and with one front and one rear saddle
|
|
|
|
|
|
|
 |
|
|
|
|
|
|
Type D-11-100L "2-way" bed lathe with a centre height of 1000 mm (40"). Note the rev. counter and ammeter installed in the forward-facing wall of the headstock
|
|
|
|
|
|
|
|
|
|
|
|
 |
|
|
|
|
 |
|
|
|
|
|
A very long-bed Deutschland Dortmund Type D-11 lathe with twin saddles
|
|
|
|
|
|
|
|
|
|
|
|
 |
|
|
|
|
|
In the middle: an extra heavy lathe Type D111-45SS lathe with a speed range from 10 to 300 r.p.m. Two fixed steadies are fitted of the type with roller jaws. To the left, just in view, are beds for the 3-wheel lathes.
|
|
|
|
|
|
|
 |
|
|
|
|
|
|
Typical Deutschland Dortmund headstock showing the long oil-distribution tube and the maze of pipes leading from it used to direct the flow of oil.
|
|
|
|
|
|
|
 |
|
|
|
|
|
|
Deutschland Dortmund Type D-1V-100L showing the front saddle and a tailstock fitted for very heavy-duty work with a special T-slotted faceplate with clamping jaws. On smaller lathes the tailstock were driven along the bed by hand-turned gearing on larger examples the drive was electric from a separate motor controlled by push buttons.
|
|
|
|
|
|
|
|
|
|
|
|
 |
|
|
|
|
Type D-11-40s. Ease of maintenance - the apron's front covers were quickly removed
|
|
|
|
|
|
|
 |
|
|
|
 |
|
|
|
|
|
|
Power shaft and leadscrew support: hand-positioned type
|
|
|
|
|
|
|
Power shaft and leadscrew support - automatic-disengage type
|
|
|
|
|
|
|
|
|
|
|
|
|
|
|
|
 |
|
|
|
|
|
|
Special compound slide rest with screwcutting attachment for short threading or taper-turning work With the supplied changewheels metric, inch, DP and MOD pitches could be cut
|
|
|
|
|
|
|
 |
|
|
|
|
|
|
Special accessory - a recessing toolpost for machining crank shafts
|
|
|
|
|
|
|
|
|
|
|
|
 |
|
|
|
|
|
|
Inside part of the Deutschland Dortmund factory with a section of the assembly shop in the foreground
|
|
|
|
|
|
|
 |
|
|
|
|
|
|
Deutschland Dortmund factory - middle bay, left-hand side: lathe assembly area for the D-Series lathes
|
|
|
|
|
|
|
|
|
|
|
|
 |
|
|
|
|
|
Deutschland Dortmund factory - middle bay right-hand side assembly of "wheel lathes" (two inward-facing headstocks), from front to back: two multi-purpose Type DRK-1V-160; two high-production car (railway) Type DRP-110; two slotting machines Type Stk-80 and three multi-purpose wheel lathes Type DRK-1V-110
|
|
|
|
|
|
|
 |
|
|
|
|
|
Left-hand lateral bay used for the assembly of sub units: to the right can be seen six headstocks intended for D-11-50S lathes and on the left two slotters (Type Stk-40 with a 400 mm stroke) and numbers of aprons, saddles, profiling tools posts, electric tracer units and piles of changewheels
|
|
|
|
|
|
|
|
|
|
|
|
 |
|
|
|
|
|
Centre (engine) lathes in various stages of manufacture:. In front lathe beds (the left one with a taper-turning unit,) and in the background seven lathes with headstocks mounted beds for wheel lathes
|
|
|
|
|
|
|
 |
|
|
|
|
|
Type D-11-50S with a carriage quick traverse feed motor built into the front left hand corner of its apron
|
|
|
|
|
|
|
 |
|
|
|
|
|
D-11-63L with hydraulic pre-selection of spindle speeds and equipped with fixed and travelling steadies
|
|
|
|
|
|
|
|
|
|
|
|
 |
|
|
|
|
|
|
Headstock and carriage No. 1 of the D-11-63L
|
|
|
|
|
|
|
 |
|
|
|
|
|
|
Tailstock end of the D-11-63L
|
|
|
|
|
|
|
|
|
|
|
|
 |
|
|
|
|
|
|
Opened headstock of the D-11-63L showing the hydraulically-operated pre-selector controls
|
|
|
|
|
|
|
 |
|
|
|
|
|
Carriage assembly with built-in electrically-operated tracer (copy) mechanism. On the right-hand side of the saddle are three brackets to hold the copy template and, hanging from the outer end of the top slide, the tracer stylus assembly
|
|
|
|
|
|
|
|
|
|
|
|
|
|
|
|