 |
 |
 |
 |
 |
 |
 |
 |
 |
 |
 |
 |
 |
 |
 |
 |
 |
 |
 |
 |
 |
 |
 |
 |
 |
 |
 |
 |
 |
 |
 |
 |
 |
 |
 |
 |
 |
 |
 |
 |
 |
 |
 |
 |
 |
 |
 |
 |
|
|
|
|
|
|
|
|
|
|
|
|
|
|
|
|
|
|
|
|
|
|
|
|
|
|
|
|
|
|
|
|
|
|
|
|
|
|
|
|
|
|
|
|
|
|
|
|
|
|
|
|
|
|
|
|
|
|
|
|
|
Manufactured by the well-known American Cincinnati company, at one time the world's largest maker of milling machines with subsidiaries in many countries, the Cinedo general-purpose miller was built from 1961 until the late 1970s. It was not a stand-alone model, but one amongst a range of revised machines: the inexpensive Cinpak 45 with variable-speed drive, the Cinel 60 in plain horizontal and universal models and the Cinova 80 - a version built in plain, universal and vertical models in several different sizes. Closely resembling the earlier and well-known Cincinnati "Dial Type" millers - but with very much more angular lines and a revised control system - the Cinedo was available in plain horizontal, universal (with swing table) and vertical types with each available as four models - the 210-14, 310-14, 315-16, 415-16 and 420-16. These digit combinations can be found on all models (even special-order versions) but may be combined with other letter and digits. All sizes were of the same basic mechanical design but with tables and drive motors of different sizes; the prefix of the version number indicates table travel: 2 being for 28 inches, 3 for 34 inches, 4 for 42 inches and 5 for 50 inches The second two digits give the h.p. of the drive motor and the final two the table width in inches. Hence, as an example, the Type 315-16 had a 16-inch wide table with 34 inches of travel and a 15 h.p. motor. Design and controls Although comprehensively redesigned and updated, many important features and specifications of the Cinedo had been carried over unchanged from earlier Cincinnati models including the 100 to 1 ratio speed range; separate spindle and power-feed motors; very large dials to indicate the selected spindle speed and table feeds; hydraulic engagement of synchromesh-equipped gears to change speeds; a "Dynapoise" mass-balance overarm; 16 or 32 rates of table feed; pull out, quick-set micrometer dials; square-gibbed ways on the saddle-to-k nee mounting and fully automatic lubrication of the main moving parts. However, to lesson production costs, non of the former speed and feed-rate control systems were used: these had included the early and very effective method where the dials had indexed round (and paused between settings) as a control arm was depressed and the later push-button controls that removed the need to manipulate so many levers. To change speeds on the Cinedo the operator had to pull out a knob on the face of the speed-indicator disc, turn it left or right to "dial" the speed required and then release it - whereupon (as for decades previously on many Cincinnati millers) hydraulics shifted the gears into engagement. Changes of feed rate were similarly altered, with the dial mounted conveniently on the front face of the knee (as on late versions of the long-lived MI Type) and equipped with a crank handle, a half rotation of which, left or right, made a change to the next higher or lower setting. Electrical controls were simplified to a handy spindle stop/start push-button mounted on an adjustable pendant arm. Table movements were controlled, as on early Dial Types from the 1930s, by levers working in a correct directional sense: move a control to the left, the table moved left; move one upwards and the knee rose, etc. For an extra charge the controls could be duplicated at the rear (mounted on the left-hand face of the knee) - this being an especially useful (and safety-promoting) addition if large jobs were to be machined that would otherwise have involved the operator in walking from the front to the rear of machine and back again to change settings and observe the cut in progress. Knee, Tables and Feeds Like all Cincinnati general-purpose millers the Cinedo had a particularly massive and rugged knee. However, instead of the common V-ways on the column-to-knee and knee-to-saddle mountings used by many other manufacturers, Cincinnati chose to employ square ways fitted with three gib strips - an arrangement that was claimed to allow a very precise adjustment of each sliding surface. Table working surfaces were, in ascending size and relative to model numbers: 59.25", 65.25", 68.5" and 79.75" with cross-feed travel of 12 inches for the two smaller models and 16 inches for the larger. The knee vertical travel was, at 20 inches, the same across the entire range. All versions had table-feed motors of 3 h.p. and the customer could choose, at no extra cost, to specify 32 rates of longitudinal or cross-feed (both were identical) from either ½ to 60 inches per minute or ¼ to 30 inches per minute - with the vertical feed rate set, universally, at ½ of that for the longitudinal and cross. To aid smooth running of the slides under power the feed screws passed through ball races in their support brackets, with the longitudinal screw fitted with backlash eliminator" that permitted effective climb milling. All feeds were engaged through ball spline clutches, allowing the makers to claim improved accuracy in tripping when the automatic-disengage stops were used. Power rapids were fitted as standard and ran at 150 on longitudinal and cross and 75 vertically - both in inches per minute. Micrometer dials of a reasonable diameter were fitted (though one might have expected them to be larger) with a quick-adjusting function that allowed them to be pulled outwards against a light spring pressure, turned and reset. No locking screws or other securing parts were used that might have caused them to tilt over or alter their setting. A particularly useful fitting on the Cinedo (and other Cincinnati models from the mid 1940s onwards) was an automatic backlash eliminator on the longitudinal feed-screw for use during climb milling. The latter is a process where, instead of the workpiece being pushed against the rotation of the cutter (and so any backlash between feedscrew and nut automatically eliminated) the work is fed into the cutter in the opposite direction - producing a tendency for it to be violently "grabbed" in. During automatic table-cycle processes, where a cut was required in both directions, climb milling was essential and the Automatic Backlash Eliminator was devised to enable this to happen safely and effectively. The mechanism was ingenious, yet simple, and contained between taper-roller bearings in a single housing that held two separate feed nuts, each carrying teeth that meshed with its own rack. The two racks were arranged to sit each side of a spur gear which, when rotated, moved one forwards and the other backwards - so causing the nuts to rotate slightly in opposite directions. As the nuts turned, the effect was to eliminate backlash by making the pair grip the feedscrew firmly by seating each hard against opposite sides of the thread. With the unit engaged climb milling became as easy as conventional - and, in a production process, could double the effective work rate of the machine. Continued below:
|
|
|
|
|
|
|
|
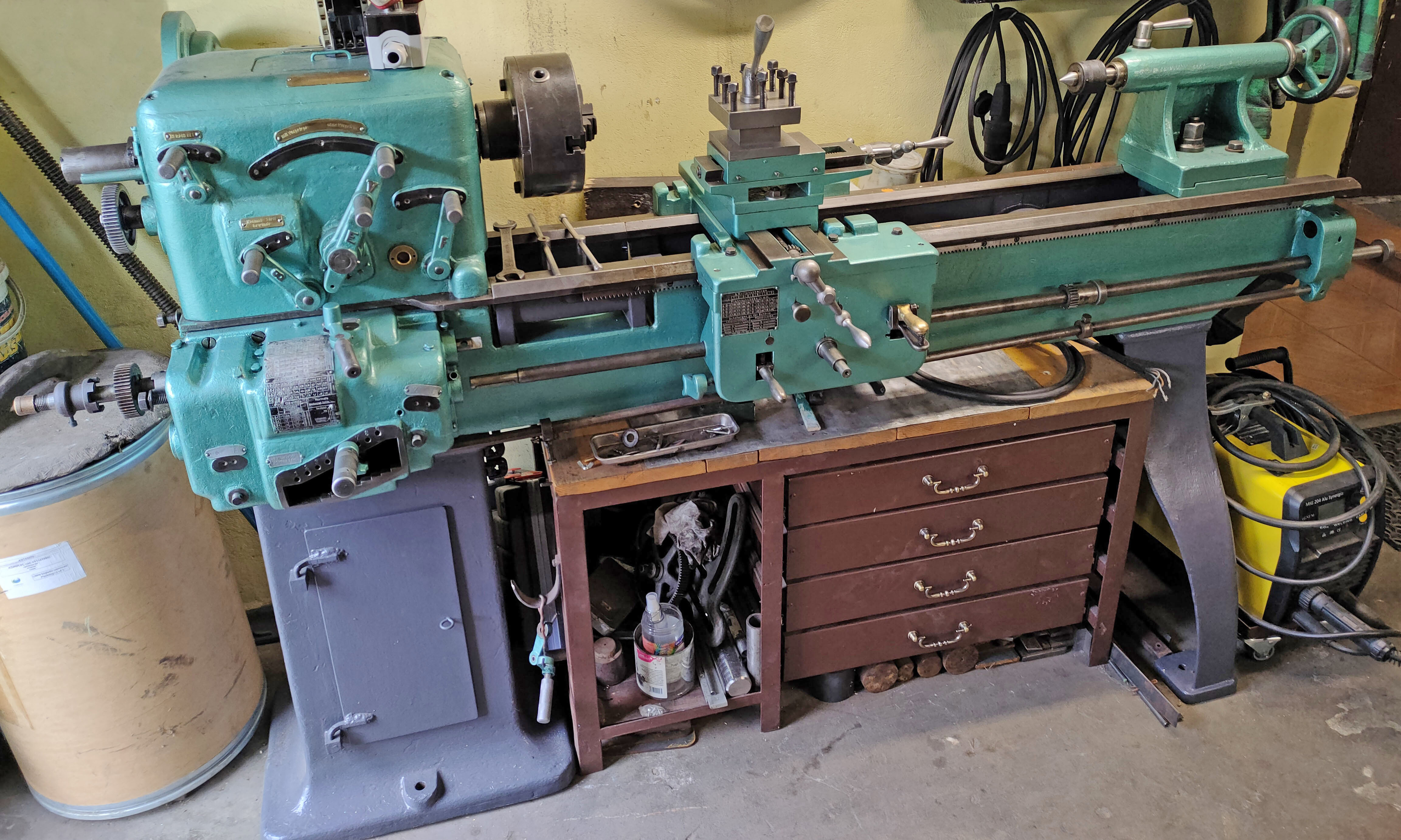 |
|
|
|
|
|
|
Cinedo vertical
Continued: Drive, Spindle and Overarm Mounted in the base of the column on a simple, vertically adjustable platform, the motor drove up to the spindle gearbox by V-belts. The two smaller machines both had 10 h.p. motors, the Model 315-16 a 15 h.p. and the 420-16 a 20 h.p. All versions (including the vertical) had 24 speeds with 18 to 1800 r.p.m. used on the two smaller versions and 16 to 1600 r.p.m. on the larger. Hardened and ground, in forged nickel-chrome steel, the main spindle ran in two high precision taper-roller bearings and one ball-type anti-friction bearing. On horizontal models the spindle diameter at the front bearing was 4 inches on 200 series machines and 4.375 inches on the 300 and 400. On vertical machines the same diameters were 3.75 inches on the 200 and 4.5 inches on the 300 and 400. To assist with high-speed milling when using carbide tools the spindle was equipped with a heavy flywheel assembly mounted on its outer end. All versions of the Cinedo were fitted with an "Arbor-loc" spindle nose, a Cincinnati design introduced as an optional-extra during the 1940s that had become a standard fitting on many of the company's general-purpose machines. Whilst provided outstanding rigidity, the assembly allowed an operator to change direct-fitting cutters, collets, adaptors and even long arbors in just a few seconds. Even if, for production purposes, using heavy-duty arbors and ganged cutters, a drawbar had to be used, this did not interfere with its simple operation. The unit worked by incorporating, on the spindle nose, a pair of adaptor half-nuts (held in place by spring clips) to accept a screw-on adaptor ring. A constant problem with any machine-tool used to the limits of its capacity and strength is vibration; and to help overcome some if its effects Cincinnati replaced the ordinary hollow-cast overarm with what they called a "Dynapoise" unit. This incorporated a mass-balance weight that was set at the factory during pre-delivery, final run-off testing, to give the smoothest possible cut at high rates of metal removal. On vertical models the totally enclosed, oil-flooded head had power feed fitted as standard, with a useful automatic release through a four-position turret stop with extra-long screws. If the feed was set to trip-out just before the required dimension, the final cut could be done by hand working to the built-in dial-test indicator. Once selected, the head feeds were controlled by the same crank handle on the front of the knee used for the control of the table feed rates. Sixteen rates were usually specified (though, as with table feeds, thirty-two could be ordered if required) that ranged from 1/4 to 30 (or 3/16 to 24) inches per minute and with a rapid-traverse rate of 70 inches per minute. Like the column and knee ways, those on the head were square, with rectangular gip strips to finely adjust each sliding surface Lubrication Unlike many previous Cincinnati millers that used a combination of automatic and manual lubrication (with oil fed to the knee and table ways by a hand-operated pump) on the Cinedo the entire system was automatic. A main reservoir was positioned inside the knee where, as soon as the main motor started, a mechanical pump both sprayed oil over the various mechanism inside and provided a supply under pressure to the table, column and saddle ways and to the moving parts of the feed mechanism. Continuing Cincinnati practice since the early 1940s, the heavily stressed knee elevation mechanism - it consisted of a one-piece, nitrided-steel screw, supported on taper roller bearings and running through an aluminium-bronze nut - was completely enclosed in a bath of EP oil. A separate header-tank positioned to one side (and level with the screw's top) fed oil down a pipe to fill the housing as the screw rose and fell. There was no lubrication responsibility on the part of the operator, other than to check the level of the main oil reservoir occasionally and apply an oil-can to a few of the hand controls. Accessories Both a number of useful accessories and adaptations to the specification were offered for the Cinedo, although nearly not as many as would have been available for a similar machine before the 1960s - the increasingly specialised nature of machining making the universally-adaptable miller increasingly irrelevant for production work. One especially useful addition for the Plain and Universal models was the "Independent Overhead Spindle" - a Ram-type" enclosed-motor, all-geared vertical head that could be left in place and used to support the standard drop-bracket used for horizontal milling. The unit was available in two forms, with 3 or 5 h.p. motors, each offered with a choice of four speed ranges, fixed at the time of ordering: 50-750; 75-1125; 100-1500 and 150 to 2250 r.p.m. Both fixed and sliding quill versions were listed, with former being double-jointed and able to be swivelled 360° both parallel and square to the axis of the table. Electrical control was through a swinging pendant. Automatic Table Cycle Offered on Cincinnati plain horizontal and vertical millers from the late 1950s onwards, the automatic table cycle control system was intended for production work. It enabled an operator to set up, using specially-shaped trip dogs in a just single T-slot on the table's front face, a sequence of simple but fully or semi-automatic operations that included all aspects of table control including movement direction, feeds and rapid traverses. Three additional controls could be added to the table cycle system, all built into the machine when new: Automatic Spindle Stop, Live Rapid Traverse and Automatic Knee Retraction. Whilst the Automatic Spindle Stop was just a simple (factory-installed) option to extend the usefulness of the automatic table cycle, Live Rapid Traverse was a more complex mechanism that provided an over-riding action built into the rapid-traverse mechanism. This, once selected, allowed the operator to set the position of the rapid feed trip dogs quickly and accurately by first mounting them in approximately the right place, starting an automatic cycle and then, when the cutting cycle engaged, using the rapid traverse lever to jog the workpiece close to the cutter. At this point the sequence was stopped, the dog set snugly against the cycle control lever and locked in place. The Automatic Knee Retraction system ensured complete safety during auto-cycle work by retracting the knee by 5/8" as the 'rapids' operated and returning it to the previous position immediately afterwards..
|
|
|
|
|
|
|
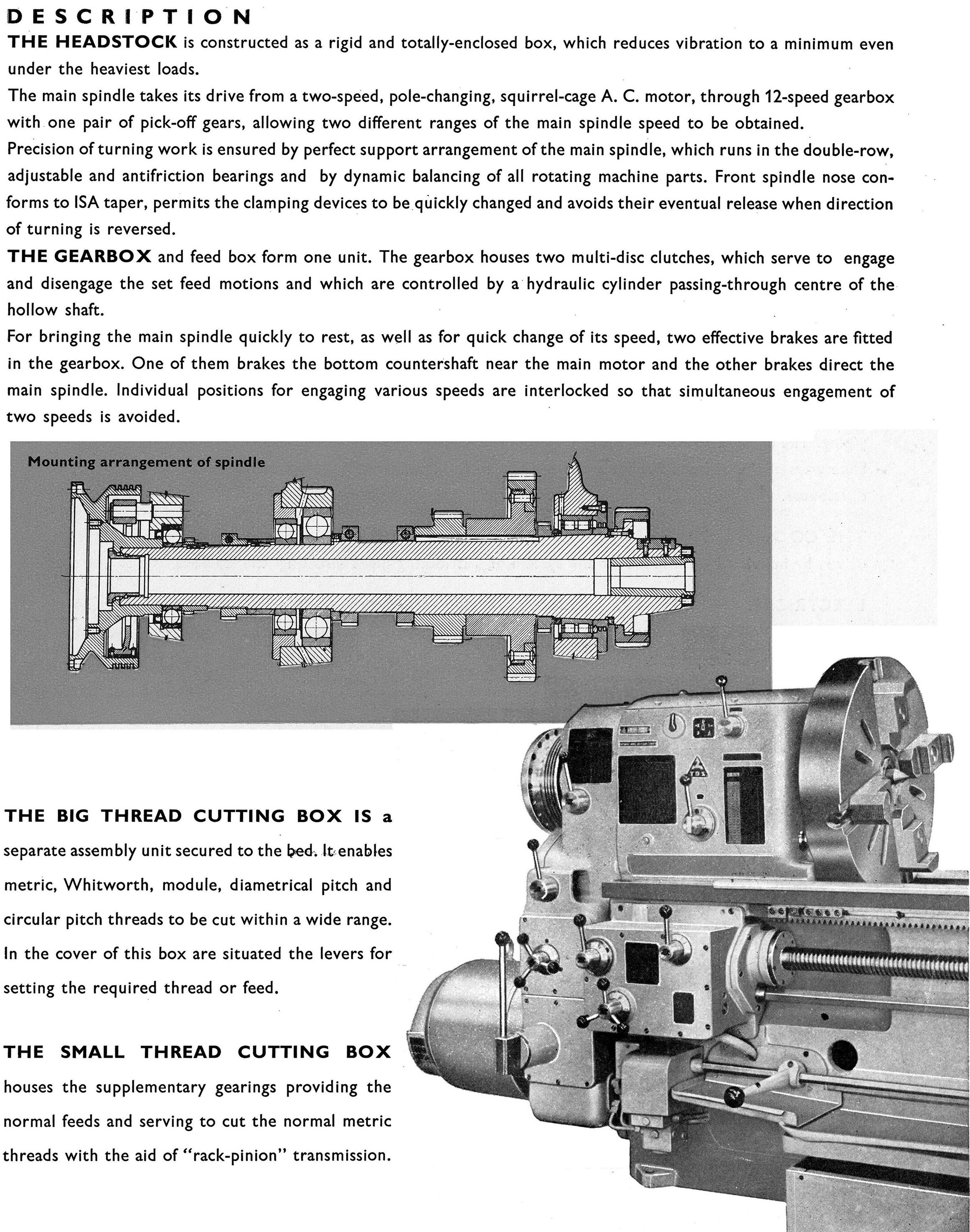 |
|
|
|
|
|
|
Cinedo Universal - with swing table and additional rear-mounted table controls
|
|
|
|
|
|
|
 |
|
|
|
|
|
|
Cinedo Plain Horizontal. Note the vertical telescopic coolant drain tube, a reversion to early Cincinnati practice
|
|
|
|
|
|
|
 |
|
|
|
|
|
|
Cinedo Milling machine - with the Automatic Table Cycle stops in place
|
|
|
|
|
|
|
 |
|
|
|
|
|
|
As on early Dial Type millers, on the Cinedo levers provided simple, foolproof directional-sense control of table movements
|
|
|
|
|
|
|
 |
|
|
|
|
|
|
A set of rear-mounted table-control levers, duplicating those on the front of the knee, was available at extra cost
|
|
|
|
|
|
|
 |
|
|
|
|
 |
|
|
|
|
|
|
Operator with hand on the table's longitudinal control lever
|
|
|
|
|
|
|
 |
|
|
|
|
|
|
The vertical head was fitted with lever-controlled power-feed and rapids as standard and a four-position, automatically disengaging turret stop with extra-long screws. If the power down-feed was set to release just before the required dimension, the final cut could be done by hand using the built-in dial-test indicator.
|
|
|
|
|
|
|
 |
|
|
|
|
|
|
Vertical head showing the twin oil-level windows
|
|
|
|
|
|
|
 |
|
|
|
|
|
|
To change speeds on the Cinedo the operator pulled out a knob on the face of the speed-indicator disc, turn it left or right to "dial" the speed required and then release it - whereupon (as for decades previously on many Cincinnati machines) hydraulics shifted the necessary gears into engagement.
|
|
|
|
|
|
|
 |
|
|
|
|
|
|
Section through the speed-change mechanism
|
|
|
|
|
|
|
 |
|
|
|
|
|
|
Changes of table feed rate were by a crank handle mounted conveniently on the front face of the knee (as on late versions of the long-lived MI millers) with a half rotation, left or right, making a change to the next higher or lower setting
|
|
|
|
|
|
|
 |
|
|
|
|
|
|
Micrometer dials of a reasonable diameter were fitted (though one might have expected them to be larger) with a quick-adjusting function that allowed them to be pulled outwards against a light spring pressure, turned and reset. No locking screws or other securing parts were used that might have caused them to tilt over or alter their setting.
|
|
|
|
|
|
|
 |
|
|
|
|
|
|
Automatic Backlash Eliminator. The mechanism was contained in a single housing and comprised two separate feed nuts, each carrying teeth that meshed with an individual rack. The racks were arranged to sit each side of a spur gear which, when rotated, moved one forwards and the other backwards - so causing the nuts to rotate slightly in opposite directions. As the nuts turned, the effect was to eliminate backlash by making the pair grip the feedscrew firmly by seating each hard against opposite sides of the thread.
|
|
|
|
|
|
|
 |
|
|
|
|
Like all Cincinnati general-purpose millers the Cinedo had a particularly massive and rugged knee. Instead of the common V-ways on the column-to-knee and knee-to-saddle mountings used by many other manufacturers, Cincinnati employed square ways fitted with a total of three gib strips that allowed a very precise adjustment of each sliding surface.
|
|
|
|
|
|
|
 |
|
|
|
|
|
|
Tight-fitting way wipers on the knee-to-column ways
|
|
|
|
|
|
|
 |
|
|
|
|
|
Hardened and ground in forged nickel-chrome steel the main spindle ran in two precision class taper-roller bearings and one ball-type anti-friction bearing. On horizontal models the spindle diameter at the front bearing was 4 inches on 200 series machines and 4.375 inches on the 300 and 400. On vertical machines the same diameters were 3.75 inches on the 200 and 4.5 inches on the 300 and 400
|
|
|
|
|
|
|
 |
|
|
|
|
|
|
A constant problem with any machine-tool used to the limits of its capacity and strength is vibration; and to help overcome some if its effects Cincinnati replaced the ordinary hollow-cast overarm with what they called a "Dynapoise" unit. This incorporated a mass-balance weight that was set at the factory during pre-delivery, final run-off testing, to give the smoothest possible cut at high rates of metal removal.
Pictures continue on Page 2
|
|
|
|